Комплексное исследование распределения материалов в рабочем пространстве печи перед ее задувкой
Характерной изюминкой работы замечательных доменных печей есть создание устойчивого газового потока по всему сечению, в особенности в центре, что во многом определяется рациональным режимом загрузки шихтовых материалов и оптимизацией распределения газового потока в печи. самые полные информацию о распределении материалов в печи смогут быть взяты лишь при изучении перед ее задувкой на протяжении загрузки шихты и уточнены в ходе ее раздувки и эксплуатации.
Получение данной информации для доменных печей громадного количества нужно в связи с резким повышением ее поперечных размеров и возрастающей роли газового распределения потока и оптимизации материалов по сечению печи. Одновременно с этим с ростом количества доменной печи осложняется проведение изучений распределения шихтовых материалов в рабочем пространстве классическими способами из-за необходимости отбора громадного количества материалов. Наряду с этим быстро возрастает трудоемкость операций, понижается оперативность и достоверность получения результатов экспериментов.
С целью проведения изучений распределения материалов на наибольшей доменной печи с целью повышения трудоемкости надёжности и уменьшения операций экспериментальных данных создали комплекс уникальных приемов с применением принципиально новых средств контроля в сочетании с классическими способами. При разработке исследовательского оборудования учитывали конструктивные и методические недоработки, характерные для устройств, использовавшихся ранее при изучении распределения материалов на колошнике перед задувкой доменных печей № 9 комбината “Кри-ворожсталь и № 6 HJIMK.
В частности, секторы емкости с бортами, искажающими распределение материалов при послойной загрузке лотковым распределителем, заменили на особые пробоотборники, складывающиеся из железной обечайки со штырями для ее закрепления, к которой крепится емкость из особо прочного эластичного материала. При установке таких пробоотборников на поверхность засыпи эластичный материал складывается, и пробоотборник делается фактически плоским.
Такие пробоотборники не искажают распределение материалов и разрешают отобрать пробы из сформировавшегося слоя материалов в любой точке сечения колошника. Наряду с этим вероятно уменьшение массы единичной пробы до минимальной величины (30-50 кг) при сохранении ее представительности и сокращении трудоемкости операций.
Толщину слоев рудных материалов и кокса измеряли посредством устройства, складывающегося из зонда с параллельно соединенными индуктивными катушками, намотанными на каркасы из ферромагнитного материала, и схемы измерения. Зонд возможно применять как для определения границ раздела слоев материалов с разной магнитной проницаемостью (к примеру, кокса и агломерата), так и распределения небольших частиц железорудных материалов, определяющих газопроницаемость и плотность шихты.
Индуктивные катушки с каркасами размещены на центральном стержне зонда и образуют незамкнутые магнитные цепи. Разрывы магнитных цепей, соответствующие размерам определяемых фракций материала, выведены посредством втулок конкретно к наружной поверхности головки зонда. Наружные поверхности втулок выполнены гофрированными.
Размеры гофрировки подобны величине разрывов магнитных цепей.
При вводе зонда в слое агломерата его куски замыкают разрывы магнитных цепей катушек. Степень замыкания разрывов магнитных цепей зависит от фракционного состава агломерата. С повышением содержания частиц небольшой фракции возрастает сопротивление переменному току, поскольку небольшой агломерат, заполняя пространство между ребрами разрывов и гофрировки магнитных цепей катушек, всецело их замыкает.
Неспециализированное сопротивление параллельно соединенных катушек переменному току измеряется универсальным мостом. Высокой чувствительности усфойства достигают за счет размещения разрывов катушек и параллельного соединения зонда их магнитных цепей на наружной поверхности головки зонда с возможностью яркого контакта с исследуемыми материалами.
При определении траектории схода материалов с лоткового распределителя, применили электроконтактные зонды, воображающие собой полые штанги, подвешенные с возможностью вертикального перемещения по стенке колошника. Зонды опускали в печь через открытые люки газоотводов.
В полости штанги расположены датчики, каковые взаимодействуют с микропереключателями при ударе кусков материала. Место встречи материалов со стенкой колошника фиксируется индикаторными лампочками на пульте дистанционного измерения, в один момент производится отсчет количества ударов счетчиками импульсов. Доуровня горизонтальных газоотборных зондов траекторию перемещения материалов определяли методом их ввода в рабочее пространство печи с побеленной поверхностью.
Использование средств контроля распределения материалов в печи, основанных на принципиально новых технических ответах, разрешило существенно повысить достоверность результатов изучения, взять более все данные при сокращении длительности исследовательских уменьшения и работ трудоемкости операций.
Характерной изюминкой исследования явилось получение одной и той же информации разными способами, что разрешило существенно повысить надежность взятых результатов. Изучение включало определение траектории ссыпания материалов с места и лоткового распределителя их встречи с цилиндрической стенкой колошника; изменение профиля засыпи материалов в печи; отбор материалов в печи по четырем взаимно перпендикулярным диаметром; определение толщины слоев кокса и агломерата в сегрегации и печи материалов по фракционному составу; контроль соосности газоотборных зондов й фактического размещения точек отбора проб газа; обработку экспериментальных данных, выдачу и разработку рекомендаций по рациональному распределению материалов в рабочем пространстве печи.
Изучение траекторий ссыпания материалов с лоткового распределителя и определение рабочих угловых положений лотка начали с пятой коксовой порции нулевой шихты, складывающейся из одного кокса, с углового положения, что согласно данным компании П. Вюрт соответствовало углу 38,0 Электроконтактные зонды опустили через нечетные газоотводы посредством спуско-подьемных барабанов, прикрепленных особыми устройствами к проушинам фланцев газоотводов. Опускание мерных реек произвели через четные газоотводы посредством канатов, закрепленных кроме этого за проушины фланцев газоотводов.
Газоотборные зонды с побеленной поверхностью вводили в рабочее пространство печи перед загрузкой исследуемой порции материалов. По окончании пересечения зонда пртоком шихты его извлекали из печи и измеряли нарушенный слой побелки.
В ходе проведения изучения установили, что угловые положения лотка, согласно данным компании П. Вюрт, не снабжают работу лоткового распределителя во всем их диапазоне. При угловых положениях лотка уже на положении (46°) верхняя граница потока материала была выше защитных плит колошника, исходя из этого произвели корректировку величины интервала шага и рабочего положений между ними.
Верхнее предельное положение лотка установили с углом наклона 44,6°, при котором верхняя граница потока материалов фактически сходится с верхней отметкой колошника. В рабочем режиме положения не употребляются и являются резервными на случай особенных режимов работы печи. На рис. 1 приведены траектории ссыпания агломерата при разных угловых положениях, полученные перед задувкой.
На одних и тех же угловых положениях лотка поток кокса если сравнивать с потоком агломерата пара смещен к оси печи. Комплекс изучений включал громадной объем работ на шихтоподаче и главном конвейере. Установили порядок формирования порции материалов при загрузке в весовые бункеры и выдаче на основной конвейер, и темперамент распределения фракционного состава материалов в порции на конвейере, сняли циклограммы работы механизмов БЗУ и шихтоподачи.
Изучения продемонстрировали, что шихта загружалась равномерно по окружности печи, профиль засыпи имел довольно горизонтальный участок вблизи кладки с четко выраженным углублением в центре печи. Глубина воронки составляла 2,7-3,0 м и ее вершина совершенно верно совпадала с осью печи. С целью выяснения возможности регулирования глубины воронки поверхности засыпи за рудными исследовательскими подачами загрузили компенсационные порции кокса на угловых положениях (откорректированных) 4-2 и 7-3.
При загрузке на угловых положениях 4-2 воронка всецело заполнилась коксом с образованием маленького конуса с вершиной, направленной вверх. При загрузке на угловых положениях 7-3 кокс размешался по большей части в промежуточном кольце.
Полученные результаты разрешили на базе показаний центрального зонда, в первый раз установленного в наборе загрузочного устройства, создать более идеальные программы загрузки шихтовых материалов с уменьшением глубицы воронки поверхности засыпи в осевой территории. В этом случае существенно уменьшается перемещение рудных материалов из промежуточной в осевую территорию и тем самым обеспечивается хорошая газопроницаемость столба материалов в центре печи и низкие рудные нагрузки, нужные для прогрева материалов в данной территории.
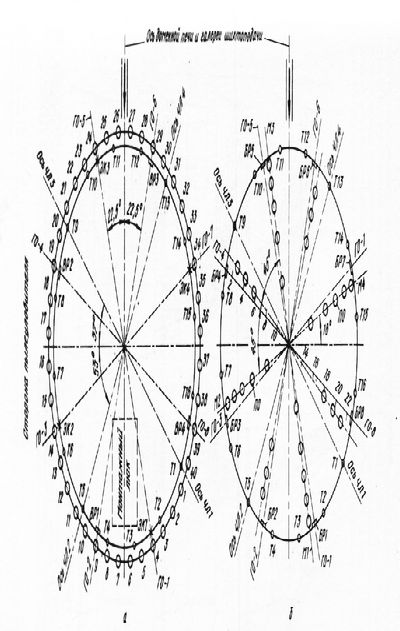
Рис.1. Размещение вертикальных электроконтактных зондов (ЭК1-ЭК4), мерных реек (ВР1-ВР4) для фиксации точек встречи потока материалов с цилиндрической стенкой колошника (а) и горизонтальных газоотборных зондов (М1-М4) для определения траектории схода материалов с лоткового распределителя, базисных реек (БР1-БР8) для замера профиля поверхности засыпи пробоотборников и материалов печи (ПО) для отбора проб материалов (б); ЧЛ1-ЧЛ4 – оси чугунных леток; Г01-Г08 – газоотводы; Т1-Т6 -периферийные термопары; 1-40 – номера воздушных фурм; 1-23 (по диаметру газоотводов) – точки измерения профиля мерными рейками и толщины слоев индукционными зондами
Рис. 2. Траектория перемещения порций агломерата (А, пунктирная линия) и кокса (К, целая) с лотка Л при разных углах наклона: 1 – электроконтактные зонды и вертикальные рейки; 2 – газоотборный зонд; 3 – место интенсивного нарушения слоя побелки (17-46 ° – угловые положения лотка)
Рис. 3. Профиль засыпи материалов в печи: А – агломерат; К – кокс; О – окатыши; Ш шлаковая щебенка; Г01-Г08 – газоотводы; цифры в скобках – угловые положения лотка; точки – эти замеров посредством индукционных зондов
Рис. 4. Сегрегация агломерата по фракционному составу: а – сторона пылеуловителя; б – воздухонагревателей (d и 3 – средний и эквивалентный диаметр кусков)
Изучение характера распределения фракционного состава агломерата на колошнике печи продемонстрировало, что сегрегация небольших и больших частиц четко выражена (рис. 4). Частицы небольшой фракции ( 5 мм) сосредоточены по большей части в промежуточном кольце, немного меньше ее в периферийной территории и предельное число – в центре печи.
Частицы большой фракции, наоборот, сосредоточены в осевой территории. Такое распределение агломерата по фракционному составу содействует формированию рационального газового потока. В отличие от агломерата какая-либо закономерность в распределении кокса по фракциям отсутствует. На основании результатов изучения с момента задувки печи установили программы загрузки шихтовых материалов, снабжающие умеренную подгрузку на периферии и хорошую газопроницаемость осевой территории.
Это разрешило организовать распределение материалов в печи и газовый поток с развитой осевой территорией, что содействовало прогреву столба шихты по всему сечению.