Механизация и автоматизация изготовления столярно-мебельных изделий
На киевской мебельной фабрике им. Боженко установлен конвейер для склеивания мебельных щитов из деловых отходов, приклеивания к хвойным заготовкам обкладок из древесины сборки и бука рамок. Перемещение конвейера пульсирующее, ритм его задается в зависимости от режима склейки конвейерными часами. остановка и Пуск автоматизированы, но смогут производиться кнопками «пуск» и «стоп» с рабочего места. Конвейер на половину собственной высоты опущен в котлован.
Сверху и с боков он защищен от внешнего воздуха кожухом из листовой стали. Это разрешает в конвейера создавать заданную температуру для сушки клеевых швов и регулировать воздухообмен. Обогрев клеевых швов производится находящимися в конвейера паровыми калориферами.
Пакеты набираются у конвейера на рабочем столе, а клей наносится на клеенамазы-вающем станке. Конструкция конвейера несложна, он высокопроизводителен и надежен в эксплуатации.
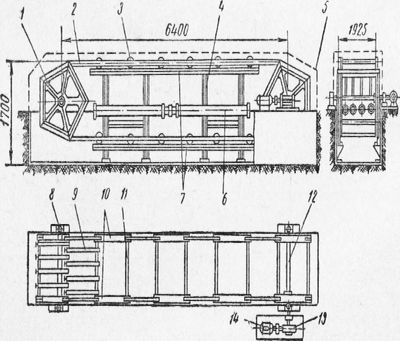
Рис. 1. Конвейер для склеивания мебельных рамок и щитов:
1 — звездочки, 2 — звенья пластинчатой цепи, 3 — ролики, 4 — сварная станина, 5 — кожух, 6 — паровые калориферы, 7 — направляющие, 8 — шариковые подшипники, 9 — зажимные струбцины, 10 — пластинчатые цепи, 11 — валики, 12 — вал, 13 — редуктор, 14 — электродвигатель
Для обработки щитовых буфета и дверок шкафа введена автоматическая линия. На автоматической линии производится обрезка щитов по ширине, фрезерование калевки на одной кромке, выбор для крепления пилястры на другой кромке, сверление гнёзд и отверстий под замок, пластинку замка, ключевину, обрезка щитов и болтик ручки в размер по длине. Автоматическая линия складывается из следующих главных частей: бункерного загрузочного устройства, пильно-фрезерного агрегата, стола для торцевания и сверления щитов, торцовочного агрегата, пятишпиндельного сверлильно-пульта управления и пазовального автомата с командным аппаратом.
Автоматическое управление линией осуществляется при помощи командного аппарата, складывающегося из вала, приводимого от привода подачи линии, и электрического контактора.
На валу имеются выключения и кулачки включения. Производится работа на автоматической линии в такой последовательности.
В бункерное загрузочное устройство загружают 18—20 щитов. На пульте управления включают все электродвигатели рабочих шпинделей. После этого включают электродвигатель подачи.
Толкатели выдвигают по одному щиту из бункера и передвигают их по столу пильно-фрезерного агрегата. Пилы обрезают щит по ширине. На одной кромке щита фрезеруется калевка, а на другой выбирается шпунт для крепления пилястры.
При предстоящем перемещении щита толкатели направляют его на сверлильно-торцовочный стол, где щит останавливается в определенном месте. Сейчас прижимные пневмоцилиндры прижимают щит к столу, сверлильно-пазовальный автомат сверлит все отверстия в щите, а пилы обрезают его по длине. При отходе выпивал в прошлое положение сбрасыватели, каковые находятся на кожухах выпивал, сбрасывают готовые дверки на ленточный транспортер, подающий их к шлифовальным станкам.
Раньше все эти операции выполнялись на отдельных станках семью обслуживающими их квалифицированными станочниками. Детали от станка к станку перевозились тележками, высокой точности обработки щитов не получалось и производительность труда была низкая. Внедрение автоматической линии дало большую экономию, сменная производительность линии равна 600 дверкам.
Во всех цехах первичной обработки деревообрабатывающих фирм, где установлены автоматические линии, используются разного типа автоподатчики и автоматические укладчики, каковые принимают готовые обработанные заготовки и укладывают их.
На столичном мебельно-сборочном комбинате № 1 используются вакуумные перекладчики. По конструкции они являются четыре вертикально подвешенные на направляющих рельсах трубы, на финишах которых имеются опрокинутые резиновые тарелки-приеосы. Когда тарелки-присосы прикасаются к изделию, на данный момент же машинально включается изделие и вакуумный аппарат хорошо прилипает к тарелкам, благодаря которым его возможно переносить и укладывать в предназначенное место.
Вакуум-перекладчик оптимален тем, что мягкие тарелки-присосы смогут переносить ровные полированные щиты без царапин и повреждений.
На комбинате при обработке боковых стенок платяных шкафов, поточная линия начинается рольгангом с вакуум-перекладчиком. К рольгангу электрокары с подъемными столами иногда подвозят штабеля щитов, каковые укладываются в кассеты, по 30 шт. в каждой. Для того чтобы количества достаточно для 20 мин. постоянной работы.
Когда на рольганг попадает кассета, на данный момент же включается автоматика. Резиновые тарелки-присосы вакуум-перекладчика забирают друг за другом щиты и подают их на второе транспортное устройство, расположенное под прямым углом к линии рольганга. Из этого щит перемещается к форматно-обрезному станку.
Рис. 2. Вакуумный перекладчик с резиновыми тарелками-присосами, работу которого осуществляет контроль фотоэлемент
Рис. 3. Автоматическая линия по обработке боковых стенок шкафа
Работа вакуум-перекладчика контролируется двумя фотоэлементами. Один фотоэлемент установлен на рольганге и его световой луч, направленный на кассету щитов, срочно дает сигнал на пульт управления, когда перекладчик берет последний нижний щит. Второй фотоэлемент осуществляет контроль правильность установки щита на транспортер форматно-обрезного станка.
В случае если непроизвольный перекладчик уложит щит с маленьким перекосом, световой луч воздействует на оператор и фотоэлемент будет об этом знать. В случае если же оператор вовремя не увидит предупредительного сигнала, фотоэлемент подаст распоряжение второму автоматическому устройству, которое остановит предстоящее перемещение изделия по транспортеру.
С форматно-обрезного станка, где щит опиливается по торцам и фрезеруются продольные кромки, рольганг подает щит к группе ленточно-шлифовальных станков. На первых двух шлифуется лицевая сторона щита. В то время, когда лицевая сторона боковой стены шкафа подготовлена для отделки, опять вступает в воздействие перекладчик — он переворачивает щит лицевой стороной вниз.
По окончании отшлифовки на второй группе ленточно-шлифовальных станков внутренней плоскости щита транспортирующие устройства перемещают изделие к вертикально-сверлильному и горизонтально -сверлильному станкам, где высверливаются 12 отверстий для крепления элементов шкафа. Готовые к отделке боковые стены шкафа снимаются с конвейера вакуум – перекладчиком и складываются в конце автоматической линии в кассеты, по 30 щитов в каждую. Из этого электрокары доставляют их на полуавтоматическую линию отделки.
Такие вакуум-пере-кладчики, заменяющие тяжелый физический труд подсобных рабочих, смогут быть применены везде, где имеются вакуум и компрессоры-установки.
Для сборки коробок и полуящиков платяных и бельевых шкафов, комодов, письменных столов, буфетов, другой мебели и сервантов используется станок СБЯ. Станина станка сварная, снабжена двумя жестко установленными чугунными ваймами (правой и левой), в каковые вкладываются детали коробки. На станке возможно собирать коробки и полуящики длиной 250—600 мм, шириной 250—600 мм, высотой 85—200 мм.
Станок СБЯ — двухпозиционный: в случае если на одной позиции создают сборку (склеивание) изделия, то на другой позиции одвременно с этим снимают ранее склеенный ящик и закладывают подробности очередного. Так, рабочий цикл сборки уменьшается, а производительность станка возрастает. Механизм управления станка складывается из рычага переключения цилиндров вайм, рычага переключения хода каретки с электродами и рычага для опускания данной каретки.
Клеевое соединение при сборке коробки подвергается давлению сжатого воздуха. Время выдержки клеевого соединения под давлением при склеивании мочевинными клеями тёплого отвердения марок М-4, М-60, МФС-1 и др. возможно регулировать, оно образовывает от 0,5 до 2 мин. Производится нагрев клеевого шва токами высокой частоты.
Рис. 4. Схема устройства станка СБЯ
Начинается сборка с закладки подробностей коробки в левую вайму и поворота рукоятки распределительного крана, направляющего сжатый воздушное пространство по каналу в правую полость двухстороннего цилиндра и в цилиндр. Под действием сжатого воздуха правый шток цилиндра отходит от правой ваймы, освобождая зажатый в нем ящик, а левый шток подходит к левой вайме и прижимает своим башмаком боковые стены снова заложенного в данной вайме коробки.
Сжатый воздушное пространство, пребывавший до этого в верхней полости цилиндра, выходит через золотник, а в левой полости цилиндра — через канал в выпускное отверстие распределительного крана. Когда левый башмак цилиндра сожмет движение поршня и боковые стенки в этом цилиндре закончится, давление сжатого воздуха в канале усилится и под действием появившегося давления откроется золотник. Через золотник сжатый воздушное пространство из канала попадает в верхнюю полость пневматического цилиндра.
Поршень цилиндра под действием сжатого воздуха, вытеснив воздушное пространство через канал в выпускное отверстие крана, начнет опускаться, а башмак сожмет заднюю и переднюю стены коробки в левой вайме. Так стены коробки в левой вайме сжимаются башмаками пневматических цилиндров.
Для сокращения выдержки клеевого шва его нагревают токами высокой частоты. Для этого рукоятку распределительного крана из нейтрального положения переводят в крайнее. Сейчас сжатый воздушное пространство проходит через регулятор скорости в канал, а через правую полость пустотелого цилиндра и через обратный клапан попадает под поршень цилиндра.
Поршень цилиндра поднимается и тянет за собой вверх каретку с четырьмя электродами, освобождая от них в правой вайме ранее собранный и склеенный ящик.
После этого каретку с электродами нужно передвинуть на позицию левой ваймы и опустить электроды на снова собранный в ней ящик для нагрева клеевого шва. Для этого рукоятку крана направляться переместить из одного крайнего положения в второе. Сейчас сжатый воздушное пространство последовательно проходит через обратный клапан регулятора скорости по каналу, а после этого через полый поршень — в левую часть цилиндра, где начинает двигать каретку с электродами влево до упора.
Дойдя до упора, каретка с электродами делается над левой ваймой, а рукоятку крана ставят в нейтральное положение и нажатием кнопки обратного клапана открывают выход для воздуха из цилиндра. После этого под действием собственного веса каретка с электродами опустится на коробку в вайме U замкнет контакты, соединяющие генератор ТВЧ с электродами, и начнется прогрев клеевых швов коробки.
На протяжении прогрева коробки в левой вайме из правой ваймы вынимают готовый ящик и на его место вставляются детали очередного коробки. По окончании склеивания и сборки на сборочном станке СБЯ ящик фрезеруют по высоте, шлифуют, после этого в нем выбирают паз и сверлят отверстия под замки.
Рис. 5. Схема устройства стапеля:
1 — основание, 2 — поворотная рама, 3 — верхняя опорная каретка, 4 — нижняя опорная каретка, 5 — пневмоцилиндры, 6 — пневмомешок, 7 и 8 — краны, 9 — стопор выдвижной, 10 — противовес, 11 — полуось, 12 и 13 — откидные кронштейны, 14 — колодки цилиндров, 15—колодки основания (опорные), 16 — колодки пневмомешков, 17 — колодки боковые (опорные), 18— гнездо для перегородки (откидное), 19 — электродвигатель привода, 20 — червячный редуктор, 21 — цепная передача, 22 — реверсивный кнопочник, 23 и 24 — рычажные концевые выключатели, 25 — штоковый выключатель, 26 — опорные ролики кареток, 27 — диск
Для сборки корпусной мебели на ленинградской мебельной фабрике № 3 внедрен в производство пневматический поворотный стапель. Сборка корпуса шкафа в стапеле производится из деталей и узлов с предварительно установленной фурнитурой. Так, к крайним дверкам, навешенным на бока при помощи рояльных петель, привернуты накладные замки и рояльные петли, к средней дверке привернуты ригельная планка, пятниковые петли и шпингалетные задвижки и т. д.
Сборочный стапель представляет собой коробчатую поворотную раму, сваренную из швеллера, опирающуюся на основание полуосями через шариковые подшипники. Для управления электромеханическим приводом поворота рамы стапеля на основании, с правой стороны установлен реверсивный кнопочник, имеющий кнопки «пуск вперед», «пуск назад» и «стоп». Для остановки поворотной рамы стапеля в положении, нужном для очередной технологической операции, на правой и левой сторонах основания установлены концевые выключатели рычажного типа, а на левой — еще и стержневой выключатель.
Рис. 6. Стапель:
а — в вертикальном положении, б — съем шкафа со стапеля
Так, рама стапеля совершает повороты в одну и Другую стороны, иногда останавливаясь посредством кон-Цевых выключателей в соответствии с технологическими операциями. Особой рычажной тележкой выводят шкаф из стапеля.
Сборка одного шкафа в стапеле продолжается 11—14 мин.
Использование стапеля улучшило условия и повысило производительность труда сборщиков, высвободило до 30% производственной площади по сравнению со сборкой на конвейере и существенно повысило культуру самого производства.
На автоматических линиях на перенастройку станков с одного размера на другой затрачивается от 90 до 190 мин. При применении совокупности программного управления время настройки уменьшается до 2—5 мин. Совокупность программного управления основана на цифровом способе задания программы, вычисленной в форме зашифрованных электрических сигналов.
Носителем программы являются перфорированная либо магнитная магнитные барабаны и лента, и устройство для считывания программных сигналов, каковые преобразуются в электрические импульсы, направленные в узел управления для управления и расшифровки механизмами автомата. Через команду узла управления узел аккуратных механизмов делает перемещение инструмента либо заготовки на определенные расстояния и возвращает их в исходное положение. Узел активного контроля машинально осуществляет контроль работу автомата.
Рис. 7. Схема автоматической линии с программным управлением настройкой станков:
1 — загрузочный бункер, 2 и 10 — транспортеры, 3, 9 н 12 — перекладчики, 4 — фуговальный станок СФ-4, 5 — приводные вальцы, 6 — торцово-базисный станок, 7 —четырехсторонний строгальный станок, 8 — контрольное устройство, 11 — шипорезный станок ПАРК-6, 13 — сверлильно-пазовальный станок СвПА, 14 — пульт управления
Автоматическая станочная линия УкрНИИМОД-2У с программным управлением настройкой станков предназначена для обработки брусковых подробностей из древесины и делает операции по созданию базисной поверхности на фуговальном и торцовочном станках, строжку с четырех сторон, контроль размеров и качества, торцовку двух финишей с одновременной зашиповкой, выборку гнезд либо сверление круглых отверстий. Протяженность обрабатываемых подробностей 400—1000 мм, ширина 20— 100 мм, толщина 15—100 мм.
Скорость подачи 6—8 м/мин, время настройки линии 2—5 мин. Контрольное устройство машинально определяет размер детали и качество обработки. Найденный брак удаляется с линии, годные подробности, остроганные в размер, подаются на модернизированный станок ПАРК-6, где в них выбираются шипы.
Порода древесины не воздействует на настройку работы и стабильность оборудования его на заданный размер. Перед обработкой заготовок на пульте управления задаются размеры настройки, включается ток, и через 2—5 мин. вся линия машинально настраивается.
Снабжение всех деревообрабатывающих станков с автоматической подачей совокупностями программного управления делает их еще более универсальными и применимыми кроме того в малосерийном производстве и в один момент решает вопрос комплексной автоматизации процессов изготовления изделий из древесины.
Перевод станков на программное управление обеспечит точность обработки подробностей, сократит время настройки и повысит производительность линий.