Очистка миниатюрных изделий
Виды загрязнений. Изюминкой очистки миниатюрных изделий являются их малые размеры, благодаря чего очистку создают при размещении изделий насыпью. Это событие затрудняет доступ моющего реагента сходу ко всей поверхности изделий.
Исходя из этого при очистке изделий им информируют вибрацию либо предусматривают перемешивание.
Малые размеры изделий накладывают ограничение на размеры ячеек и других конструктивных элементов поддонов, прочей оснастки и корзин, применяемой при очистке. Очистка миниатюрных изделий в ряде производств есть определяющим причиной, воздействующим на уровень качества производимой продукции. На данный момент имеется много разных растворителей, реагентов, составов для очистки. Использование того либо иного состава зависит от вида загрязнений, материала изделия, нужной степени чистоты и т. п.
Главными источниками загрязнений поверхностей миниатюрных изделий являются:
1) стружка, абразивные материалы, смазочно-охлаждающие жидкости, используемые при механической обработке изделий;
2) остатки технологических сред по окончании термической, хими-котермической обработки, отжига, сварки, пайки, склеивания и т. д.;
3) остатки щелочей, кислот, солей, промывочных составов по окончании травления, обезжиривания, электрополирования;
4) остатки и следы от упаковки, тары, режущего, монтажного и мерительного инструмента; рук, напальчников, перчаток операторов;
5) пыль, находящаяся в воздухе помещений, в которых создают изготовление и обработку изделий.
Загрязнение происходит фактически на всех этапах изготовления изделий: механической, термической, химической обработке, сварке, пайке, сборке.
В зависимости от химических особенностей виды загрязнений подразделяют:
а) механические — железная стружка, абразивные частицы от шлиф-порошков, доводочных паст, керамическая, посторонние частицы и стеклянная пыль, имеющие разную природу;
б) органические — смазки, канифоль, парафин, заливочные и клеевые композиции, ингибиторы коррозии;
в) загрязнения, химически связанные с поверхностью изделий — окисные, сульфидные и другие пленки, образующиеся на поверхности при термической и химико-термической обработке, и при хранении изделий.
В настоящих условиях на изделиях в один момент присутствуют загрязнения разных видов, исходя из этого процессы очистки должны включать последовательность последовательных операций, любая из которых предназначена для удаления одного либо нескольких видов загрязнений. При химической очистке направляться использовать вещества, продукты сотрудничества которых с поверхностью изделий легко удаляются при последующей обработке.
В ходе очистки изделий нужно осуществлять контроль чистоту технологических очистных сред: воды, растворителей, моющих составов и проводить выборочный контроль качества очистки изделий. Наряду с этим средства контроля должны обнаруживать малые поверхностные загрязнения. При транспортировании, хранении, исполнении последующих операций изготовления изделий нужно сохранять достигнутую степень очистки и исключать вероятные источники повторного загрязнения поверхностей изделий.
Обнаружение микрозагрязнений на изделиях. Микрозагрязнения на разных изделиях, площадках для неразъемных соединений, микроэлементах являются обстоятельством понижения соединений работы и надёжности изделий.
идентификация и Обнаружение микрозагрязнений есть нужным условием верного выбора способа очистки и моющих реагентов. Учитывая малые размеры изделий, для определения и обнаружения состава загрязнений рекомендуется использовать способы локального, микроспектрального, микрохимического, капельного и других видов микроанализа. Загрязнения смогут быть как органического, так и неорганического происхождения. К ним относятся: стружка, продукты износа, брызги припоев, остатки паяльных флюсов, клей, лаки, частицы полимерных материалов, ворс и т. д.
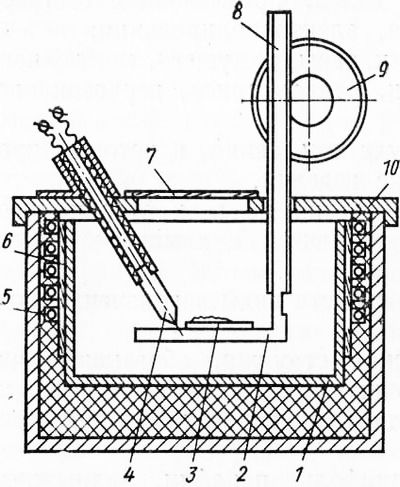
Рис. 1. Столик для нагревания микрообъектов
В зависимости от характера объекта для состава загрязнений и определения природы современными способами микроанализа достаточно микрозагрязнения массой 10“5 г. Для идентификации и обнаружения загрязнений применяют следующие выводы:
1) визуальный осмотр поверхности изделий посредством микроскопа при повышении в 25—50х;
2) осмотр под микроскопом в ультрафиолетовом свете; для этого микроскоп (к примеру, МБС-1) снабжают люминесцентным осветителем ОИ-18 и при наличии люминесценции, по возможности визуально, оценивают окраску свечения. Но данный способ не снабжает обнаружение загрязнений малых размеров;
3) осмотр изделия в поляризованном свете. Для этого микроскопы (МБС-1 либо МИН-9) снабжают дополнительными поляризационными фильтрами.
В большинстве случаев, осмотр, совершённый в соответствии с вышеуказанными способами, разрешает сделать предположение о характере загрязнений и избрать последующий способ анализа.
Взяли распространение следующие способы анализа.
Термический анализ. Наблюдение создают за трансформациями, происходящими в разбираемом изделии при нагревании. Наряду с этим замечают изменение внешнего вида загрязнений, определяют температуру их плавления и размягчения.
Разбираемое изделие помещают в нагревательный столик с температурой нагрева до 350 либо 500 °С.
В камеры помещена подставка, передвигаемая вверх и вниз посредством реечной передачи. Нагрев изделий и внутреннего пространства камеры либо образцов с разбираемыми микрозагрязнениями производится посредством нихромовой спирали, уложенной около камеры. Спираль.изолирована листовым асбестом.
Сверху камера закрыта крышкой, в которой предусмотрено слюдяное окно для наблюдения.
Нагрев осуществляют контроль посредством термопары либо термометра, расположенных в близи от разбираемого изделия. Наблюдение ведут под микроскопом МБС-1 через слюдяное окно. Вращением маховика получают наилучшего размещения объекта для осмотра.
Эмиссионный качественный микроспектральный анализ делают на спектрографе ИСП-22, собранном на базе искрового генератора ИГ-3. Источником возбуждения спектра есть высоковольтная импульсная искра. Электроды размещают на расстоянии 400 мм от щели спектрографа.
Положение электродов осуществляют контроль посредством оптической приставки.
Химический анализ сводится к наблюдению под микроскопом за поведением разбираемого объекта в условиях действия разных кислот, растворителей и щелочей.
Имеется и ряд других способов микроанализа загрязнений. Результаты анализа либо совокупность черт вещества, взятых указанными способами, разрешают выяснить материал некоторых микрозагрязнений.
Химические способы очистки. К химическим способам относятся обезжиривание, химическое и электрохимическое травление, электрополирование.
Обезжиривание используют для удаления с поверхности изде^ лий жиров растительного происхождения и животного, минеральных масел, консистентных смазок. Для обезжиривания используют органические растворители и щелочные моющие растворы с добавками поверхностно-активных веществ.
Обезжиривание в органических растворителях. Обезжиривание в органических растворителях используют для удаления с поверхностей изделий минеральных смазок и масел. В качестве обезжиривающих средств используют трихлорэтан, бензин «галоша», четыреххлористый углерод, хлорэтилен, фреон, ацетон, другие растворители и спирт.
В том случае, в то время, когда для обезжиривания применяют взрывоопасные и огнеопасные вещества, подачу их создают сжатым воздухом, а не механическими насосами. Нарис. 129,а продемонстрирована схема таковой установки.
Бензин (либо второй растворитель) заливают в резервуар из приемной ванны.
По окончании заполнения резервуара вентиль закрывают, а вентиль открывают. В резервуар подают сжатый воздушное пространство, давление которого осуществляют контроль посредством манометра. Под действием давления растворитель поступает в форсунки. От избыточного давления резервуар защищен клапаном.
Очищаемые подробности укладывают на противень. Струи бензина, истекающие под давлением из форсунок, направляются на очищаемые изделия, омывают их, и стекают в приемную ванну.
Обезжиривание создают кроме этого в тёплых либо кипящих растворителях, в нескольких ваннах с паровым обогревом. Ванны обезжиривания соединяют в один блок (рис. 2, б).
Для нагрева растворителя и обеспечения циркуляции в совокупности предусмотрены насос, напорный бак, трубопровод для наполнения ванн растворителем, подогреватели, через каковые пропускается пар, подаваемый по трубопроводу. Загрязненный растворитель по окончании применения направляется в отстойник.
Рис. 2. Установка для обезжиривания в органических растворителях
Высота перегородок между ваннами I, II, III запланирована на увеличение уровня растворителя от первой ванны к третьей. Такое размещение ванн исключает смешивание чистого растворителя с загрязненным из прошлых ванн, а неспешно вытесняет его в перегонный куб. В последней ванне изделия промывают в конденсате, поступающем из куба и образующемся при охлаждении паров растворителя посредством трубчатого холодильника 9, вмонтированного в установку над ваннами.
Охладителем есть вода, подаваемая по трубопроводу.
Недочёт хлорорганических растворителей пребывает в том, что по окончании промывки и обезжиривания на поверхности изделий остаются пленки из хлоридов металлов. Они кроме этого имеют довольно большую цена. Помимо этого, последовательность загрязнений: мыльные смазки, стеариновая, олеиновая и другие жирные кислоты, не хорошо удаляются органическими и хлорорганическими растворителями.
Обезжиривание в щелочах. Для обезжиривания используют щелочные растворы. Растительные и животные жиры под действием щелочи омыляются с образованием солей и глицерина жирных кислот. Отделение от поверхности загрязнений на базе минеральных масел достигается в следствии смачивания поверхности моющим раствором, эмульгирования частиц и диспергирования масла этих частиц в щелочном растворе.
В моющие составы не считая щелочи додают тринатрийфосфат, метасиликат, поверхностно-активные вещества. Последние, попадая в трещины и поры в слое загрязнений, адсорбируются на поверхности очищаемых изделий, ослабляя связь между загрязнением и материалом изделия. Образующиеся небольшие частицы загрязнений легче диспергируются в растворе.
Рис. 3. Схема установки для очистки травлением
Обезжиривание создают окунанием с одновременным встряхиванием изделий, помещенных в корзины, пульверизацией либо разбрызгиванием под давлением щелочного раствора. Интенсифицирующее воздействие на процессы очистки изделий в щелочных растворах оказывает введение ультразвуковых колебаний. Особенно действенно использование ультразвука при обезжиривании в щелочных растворах с добавками неионогенных поверхностно-активных веществ.
Взяло распространение электролитическое обезжиривание в щелочных растворах. Выделяемые при катодном либо анодном обезжиривании газы механически действуют на загрязняющую пленку, отрывают ее от поверхности изделия и, так, содействуют более стремительной и полной очистке. Электролитическое обезжиривание используют для очистки узкой вольфрамовой и молибденовой проволоки методом протягивания ее через раствор при одновременном действии током.
К примеру, скорость протяжки вольфрамовой проволоки, диаметром 0,05 мм при обезжир ивании ее в 20%-ном растворе едкого натра образовывает 3—4 м/мин; плотность подводимого тока 4—4,5 А/см2 при напряжении 5—10 В. Температура раствора 50—70 °С. С повышением диаметра проволоки направляться увеличивать плотность тока и уменьшать скорость протяжки.
Очистка химическим и электрохимическим травлением. Для очистки изделий от окалины и окисных плёнок по окончании сварки, заварки используют химическое и электрохимическое травление. Эти способы очистки применяют кроме этого по окончании механической обработки, холодной штамповки, прокатки для придания и одновременного удаления заусенцев поверхностям определенных особенностей.
Так, глубокое травление (матирование) увеличивает излучатель-ную свойство анодов, других изделий и экранов; усиливает сцепление поверхности с наносимыми покрытиями.
В качестве травильных растворов, электролитов применяют составы на базе соляной, серной, фосфорной, муравьиной и других кислот с добавками ингибиторов коррозии либо блеско-образователей.
Для получения чистых поверхностей изделий используют тройные составы. Эти смеси снабжают контролируемое травление изделий. Одним из таких составов есть состав из 80% перекиси водорода, 10% муравьиной кислоты и 10% воды. Режимы травления зависят от материала изделий.
Для изделий из меди время выдержки образовывает 1,5—2 мин; температура состава 60 °С; средняя толщина удаляемого слоя 0,002—0,003 мм.
Используют кроме этого тройные смеси, в которых вместо муравьиной кислоты применяют аммиак (к примеру, 75% воды, 20% аммиака и перекиси 5% водорода). Преимущество тройных смесей пребывает в том, что кроме получения качественной поверхности в них растворяются металлы, находящиеся ниже водорода в электрохимическом последовательности напряжений.
На рис. 3 приведена схема полуавтоматической установки для контролируемого травления изделий в разных тройных смесях с последующей промывкой в проточной деионизирован-ной воде и сушкой в струе очищенного азота, подогретого до 200 °С. Из резервуара, содержащего муравьиную кислоту, и резервуара, наполненного перекисью водорода, реактивы подаются в смеситель для подогрева и предварительного смешивания.
Для изготовление травильного состава по трубопроводу в смеситель подается деионизированная вода, прошедшая стерилизацию методом облучения ультрафиолетовой лампой, обработку смешанными смолами в ионообменной колонке, очистку посредством фильтра из мембранного фильтра и нержавеющей стали.
В циркуляции и системе приготовления деионизированной воды предусмотрены насос, отстойник, датчик для контроля сдельной электропроводности исходной воды. Травление, сушка и промывка изделий производится в одном и том же реакционном сосуде. Это делается чтобы исключить загрязнения изделий.
По окончании травления для промывки по заданному режиму в сосуд подается проточная деионизированная вода , пока промывная вода не будет иметь заданное удельное сопротивление. Затем изделия снова промываются деиони-зированной водой, имеющей большее удельное сопротивление. После этого направляться сушка в подогретом азоте, что подается по трубопроводу.
В установке предусмотрена вытяжная вентиляция III. Операции смешивания реагентов травильных смесей и заданные режимы обработки изделий выполняются машинально посредством программного устройства. Подача фильтрованной водопроводной воды производится по трубопроводу, а контроль ее удельной электропроводности посредством датчика 8. При применения в качестве реагентов аммиака, в установке предусмотрен для его подачи трубопровод.
По трубопроводу отработанные реагенты удаляются.
Очистка изделий по окончании доводки. По окончании доводки изделия шепетильно очищают от шлама, суспензий и остатков паст. Существует много приёмов и методов очистки.
Вот один из них, обширно применяемый в производстве.
Для очистки изделия помещают в эксикатор, заполненный на 2/3 количества спиртобензиновой смесью (бензин и — 50% этиловый спирт БР-1 — 50%). В течение 3—5 мин изделия иногда поворачивают чистым пинцетом и протирают их поверхности кистью. Операцию повторяют в другом эксикаторе с той же смесью.
После этого изделия протирают чистой хлопчатобумажной салфеткой. протирку и Промывку ведут до прекращения появления чёрных пятен на салфетке.
Промывку возможно вести в чистом бензине БР-1 либо в нагретом до 30—50 °С водном растворе тринатрийфосфата (концентрацией 30 г на 1 л воды) и эмульгатора ОП-7 (по 5 г на 1 л воды). По окончании очистки изделия просушивают в термостате при температуре 40—60 °С в течение 10—20 мин, а после этого помещают в сосуд с веретенным маслом и 10%-ной присадкой АКОР-1. Сосуд должен иметь притертую крышку, и в нем по окончании заполнения не должно быть воздушной подушки.
Бюкс, с очищенными изделиями устанавливают в эксикатор с индикаторным силикагелем, в котором изделия возможно хранить до 1,5—2 месяцев.
Изделия из неметаллических материалов (минералокерамики, ситалла, технических камней) очищают в той же последовательности с применением в качестве моющего средства 1—2%-ного водного раствора щавелевой кислоты либо разных моющих средств, приведенных в табл. 19.
Очистка изделий из кварца и стекла. Очистку изделий из кварца и стекла создают 6%-ным водным раствором перекиси водорода в течение 20—30 мин с последующей промывкой в деиони-зированной проточной воде. Очень действенна ультразвуковая очистка стеклянных изделий в изопропиловом спирте.
Керамические изделия очищают по окончании резки, других видов и шлифовки механической обработки. В большинстве случаев они бывают загрязнены остатками абразивов и смазочно-охлаждаемых материалов. Очистку создают в кипящем мыльном растворе (50— 60 г хозяйственного мыла на 1 л воды).
После этого направляться промывка в тёплой водопроводной и дистиллированной воде, обезвоживание в этиловом спирте либо ацетоне и сушка на воздухе при 100— 120 °С в течение 15—20 мин. самые загрязненные керамические изделия перед очисткой в мыльном растворе предварительно обезжиривают в тёплом трихлорэтилене.
Для удаления остатков органических загрязнений керамические изделия кипятят в 6—10%-ном растворе перекиси водорода. По окончании промывки в воде их сушат горячим воздухом и прокаливают в муфельных печах при температуре 1000 °С в течение 30—40 мин.
Термические способы очистки. Для удаления загрязнений с изделий взяли использование термические способы очистки: отжиг в очищенном, увлажненном водороде; окислительно-восстановительный отжиг; отжиг в вакууме и комбинированные приемы отжига в разных воздухах. Перед проведением термической очистки проводится тщательная очистка их от органических и солевых загрязнений химическими способами.
В случае если по окончании предварительной очистки химическими способами на поверхности изделий остаются органические загрязнения, то по окончании термической очистки наблюдаются чёрные пятна, удаление которых затруднено и в большинстве случаев требует применения повторной очистки с применением кислотных растворов. Это нарушает геометрические размеры изделий, а повторные отжиги ухудшают механические особенности материалов. Появление ярких пятен по поверхности изделий обусловливается нехорошей промывкой изделий.
Исходя из этого изделия, поступающие на отжиг, не должны иметь органических и солевых загрязнений. Хранить их следует в герметичной таре.
Очистка окислительно-восстановительным отжигом. Технологический процесс очистки железных изделий включает операции удаления остаточных органических загрязнений методом окисления в кипящей проточной деионизированной воде; сушку горячим (при температуре 120—150 °С) очищенным воздухом, окисление на воздухе (при температуре 400—650 °С), промывку в тёплом (при температуре 60—70 °С) щелочном растворе, повторную промывку в тёплой деионизированной воде, сушку в тёплом воздухе и восстановительный отжиг в водороде при температуре 500—1000 °С. При очистке изделий окислительным отжигом громаднейшую трудность воображает удаление остатков минеральных масел.
О качестве окисления изделий возможно делать выводы визуально по образованию узкого равномерного слоя окислов, прочно связанного с поверхностью изделия. Цвет окислов зависит от температуры их окисления. Недостатками при окислении изделия являются белесые пятна, отдельные чёрные точки.
Восстановительный отжиг обязан обеспечить полноту восстановления окис-ных пленок и получение нужных физико-механических особенностей изделий.
Очистку изделий способом окислительно-восстановительного отжига создают в установках с автоматической передачей кассет с изделиями с одной позиции на другую. Восстановительный отжиг в водороде осуществляется в печах. Исполнение всех операций производится по созданной программе.
Очистка методом отжига в воздухе водорода. Данный способ используется для восстановления окислов металлов, находящихся на поверхности изделий. В следствии происходит замещение газов (СО, С03, N2 и др.), содержащихся на поверхности железных изделий, на водород, что при последующем отжиге в вакууме легко удаляется из изделий.
При очистке методом отжига в водороде нужно, дабы время выдержки изделий в тёплой территории печи, скорость и чистота водорода его продувки снабжали восстановление окислов, а режимы отжига должны снабжать получение изделий с нужными механическими особенностями. Режим охлаждения изделий определяется температурной зависимостью растворимости газов в металлах.
Режимы отжига зависят от геометрических размеров изделий. Отжиг никелевой ленты толщиной 0,05—0,1 мм создают при температуре 700 ± 25 °С. Время нагрева 5—10 мин; охлаждения — 20—30 мин. Отжиг ленты толщиной 0,1—0,2 мм создают при температуре 750 ± 25° С.
Небольшие бронзовые изделия отжигают в водороде при температуре 650 ± 25° С, нагревая их до данной температуры в течение 10— 15 мин; охлаждение создают в течение 20—30 мин. Последующий отжиг в вакууме делают при температуре 650—• 750° С; время нагрева 20—30 мин, а охлаждения —.30—40 мин.
Для отжига изделий в водороде используют высокопроизводительные трубчатые толкательные печи. Для отжига узких проволочек применяют особые печи.
На уровень качества отжига громадное влияние оказывает способ и чистота водорода его продувки, степень герметичности печей, материал лодочек и муфеля.
Для очистки микропроводов из молибдена, их сплавов и вольфрама используют отжиг в увлажненном водороде. Используют кроме этого комбинированный отжиг изделий: в сухом водороде и в вакууме либо во мокром водороде, в сухом водороде и в вакууме.
Отжиг в вакууме. Используют для эвакуации газов из поверхностных слоев изделий. Этому виду отжига подвергают изделия, каковые нельзя отжигать в водороде. К примеру, изделия из титаного сплава, циркония, тория и др., так как они взаимодействуют с водородом с образованием гидридов. При отжиге в водороде у некоторых материалов ухудшаются их механические особенности.
Исходя из этого изделия из этих материалов отжигают в вакууме. Главными параметрами процесса есть величина разряжения и температура нагрева. Большая температура Т0 нагрева зависит от физических и химических особенностей материалов.
Фактически ее определяют из соотношения Т0 = 0,75ГПЛ, где Тпл — температура плавления металла.
Для удаления газов из паяных соединений температуру принимают равной Т0 = 0,75ТПЛ п, где Тпл п — температура плавления припоя. Отжиг в вакууме используется в комбинации с отжигом в водороде.
Отжиг изделий в вакууме производится в высокотемпературных печах с нагревателями сопротивления либо установках, в которых нагрев осуществляется токами высокой частоты. Время выдержки изделий при температуре отжига устанавливают умелым методом. При отжиге в вакууме нагрев обязан осуществляться медлительно и при увеличении температуры нельзя допускать резкого ухудшения вакуума чтобы не было окисления изделий.
По достижении устойчивого вакуума снова поднимают температуру до рабочей и создают отжиг, а после этого охлаждение.
Очистка изделий электрическим током. Очистку изделий от загрязнений во многих случаях создают методом применения электрического тока. Способ действен для удаления остатков органических загрязнений, пыли, ворсинок. Соляные загрязнения удаляются частично.
Существует пара разновидностей этого способа; очистка электрическими разрядами; действием тлеющего разряда при пониженном давлении газа; очистка струей ионизованного газа.
При действии электрических разрядов на металлы происходит их разрушение и эрозия под действием большой температуры загрязнений. Очистка этим приемом эргономична в условиях эксплуатации.
В случае если поверхность контактов миниатюрных изделий (к примеру, реле) загрязнена пленкой флюса, то ее очистку возможно создавать электрическим разрядом. Самый пригоден для этого случая емкостный разряд, поскольку он распространяется на громадную область очищаемого контакта. Это крайне важно, в случае если учесть, что в ходе работы точка контактирования может перемещаться по поверхности.
Рис. 4. Устройство для очистки тлеющим разрядом
Очистка сильноточным тлеющим разрядом. Способ очистки поверхности изделий сильноточным тлеющим разрядом в инертном газе основан на разрушении молекул загрязнений под действием ударов. хороших ионов, образующихся в тлеющем разряде. Наряду с этим в один момент происходит частичная эрозия и катодное распыление материала.
Газообразные продукты разложения загрязнений удаляются при откачке.
На рис. 4 приведена схема установки для очистки изделий тлеющим разрядом. Под стеклянным колпаком расположен алюминиевый экран, образующий внутреннее пространство. Изделия помещены в пространство между электродами.
Откачку воздуха создают через патрубок. Напряжение на электродах образовывает от 0,8 до 2 кВ, плотность тока — от 0,5 до 5 мА/см2. Напряжение на электроды подается через повышающий трансформатор.
Очистка изделий ионной бомбардировкой и тлеющим разрядом — завершающая операция по окончании удаления главного количества загрязнений химическими способами.