Способы формования
Формование стекла — главная и наиболее значимая по окончании стекловарения технологическая стадия производства изделий из стекла. Совокупность этих двух конкретно связанных процессов определяет тип стекольного производства, его технический уровень и экономическую эффективность.
Формование стекла сводится к превращению вязкого расплава (стекломассы) в жёсткое изделие заданной конфигурации в следствии приложения определенного силового действия к объекту формования и его твердения и постепенного охлаждения. Так, в ходе формования стекло в следствии его охлаждения переходит из состояния вязкой жидкости через пластическое в жёсткое хрупкое состояние, т. е. процесс формования связан с трансформацией вязкости в широком промежутке температур. Соответственно этому промежутку температур вязкость стекла в ходе формования изменяется от 102 до 1012 Па-с, причем именно на завершающем этапе формования происходит самоё значительное повышение вязкости.
Температурный движение вязкости, т. е. изменение вязкости с температурой для различных по составу стекол, значительно влияет на их текучесть, свойство к твердению и деформированию, следовательно, на целый процесс их формования. Различают две разновидности стекол — «маленькие» и «долгие».
Для «маленьких» стекол характерно резкое возрастание вязкости при охлаждении, т. е. для них характерен более маленький температурный промежуток, следовательно, они стремительнее теряют деформационную свойство (подвижность, текучесть, пластическое состояние) и скорее твердеют. «Долгие» стекла отличаются постепенным и умеренным ростом вязкости при охлаждении. Следовательно, сохраняют свойство к твердению и деформации более широком промежутке температур, т. е. более медлительно.
Следовательно, изменение вязкости стекла с температурой пределяет выбор того либо иного метода формования. Общий ход процесса формования возможно условно поделить на две стадии: фиксация и формообразование формы. На протяжении первой стадии пластичной стекломассе придают требуемую Лорму изделия.
На стадии фиксации формы форма изделия закрепляется в следствии твердения стекломассы, темперамент которого обусловлен способом и видом изделия его охлаждения.
Существует много способов формования стекла, каковые различают по характеру действия на стекломассу, виду создаваемых из стекла изделий и принципу сотрудничества стекломассы с формующими устройствами и органами. Самый распространены методы формования: выдувание, прессование, прессовыдувание, центробежное формование, вытягивание, прокатка, формование на подложке металла, моллирование, отливка, экструдирование. В производстве сортовой высокохудожественных изделий и посуды по большей части применяют выдувание, прессование, прессовыдувание и центробежное формование.
Выдувание — самый популярный метод циклического формования полых штучных изделий — осуществляется под влиянием равнодействующих растягивающих упрочнений, создаваемых во внутренней полости формуемого изделия сжатым воздухом (давлением 0,2…0,3 МПа). Производят изделия как вручную (ручное выдувание), так и механизированным методом.
Не обращая внимания на то, что ручное выдувание малопроизводительно и требует громадных физических упрочнений, данный метод незаменим при производстве высокохудожественных изделий сложной конфигурации из хрусталя. Главный инструмент при ручном выдувании— стеклодувная трубка.
Процесс выдувания складывается из следующих операций:
1) предварительно нагретую до температуры прилипания стеклодувную трубку опускают в стекломассу и набирают ее на трубку;
2) собранную на конец трубки стекломассу закатывают на железной плите либо в других приспособлениях (катальни-ках либо делоках) и из нее выдувают баночку (при наличии железной баночки либо наборной головки эта операция отсутствует) ;
3) на подготовленную баночку повторно набирают стекломассу числом, нужном для выработки изделия; порученный комплект раздувают в «пульку», которая по конфигурации приближается к готовому изделию;
4) выдувают изделие заданной конфигурации и размеров в формах.
Формы для ручного выдувания изготовляют преимуществен но из металла, время от времени из дерева, огнеупорных материалов и т. д.
Отличительная изюминка большинства изделий, выдувае мых на трубке, пребывает в том, что их верхняя часть (горло), будучи до конца формования соединена с трубкой и, пребывав на протяжении всего процесса вне формы, не получает требуемой конфигурации и в месте сочленения трубки с изделием в его верхней части образуется колпачок либо венчик. Так, полученное по окончании отделения от трубки изделие по существу есть еще полуфабрикатом и его край необходимо дополнительно обрабатывать (обрезкой, шлифованием, полированием либо отопкой).
Ручным выдуванием изделия производят бригадным способом. В большинстве случаев одна бригада, складывающаяся из 5…6 человек, изготовляет 850… 1000 изделий на ножке (либо 200 … 300 ваз для цветов). Внедрение в ручное производство средств малой механизации (к примеру, формование и пойла одновременное выдувание изделия фигурной ножки, применение цепных конвейеров) существенно повышает производительность труда.
При механизированном методе всевозможный ассортимент изделий выдувают сжатым воздухом на разных стеклофор-мующих агрегатах. Стеклоформующие агрегаты различаются принципом питания их стекломассой: капельным (полуавтоматы ВВ-2, автоматы АБ-6, АВ-6, ВВ-7, IS-6, S-10) и вакуумным (автоматы ВВ-6; ВС-24).
В стеклоформующих автомобилях изделия выдуваются в положении или дном вверх, или дном вниз. В большинстве случаев, в автомобилях с капельным едой выдувание в черновой форме производится дном вверх, после этого заготовка переворачивается и выдувание в чистовой форме заканчивается дном вниз. На автомобилях с вакуумным едой изделия выдуваются и в черновых, и в чистовых формах дном вниз.
Разглядим последовательность формования на примере выдувания чашек. По окончании вдавливания плунжера I происходит предварительное свободное выдувание II, вытягивание и поворот III. Последняя стадия IV — выдувание в форме при одновременном вращении трубки.
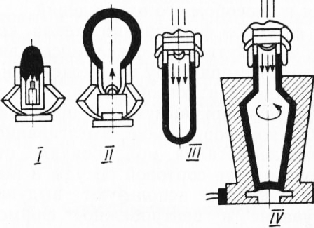
Рис. 1. Последовательность механизированного выдувания чашек на автоматах с вакуумным едой: 1 — комплект порции стекломассы по окончании вдавливания плунжера, 11 — предварительное свободное выдувание, III — вытягивание и поворот пульки, IV — выдувание изделия в форме при одновременном вращении трубки
Прессование — самый ветхий метод циклического формования штучных изделий.
Рис. 2. Последовательность операций прямого прессования стекломассы: I — подача капли стекломассы в чистовую форму (пресс-форму), II — прессование изделия пуансоном и формовым кольцом, III — выталкивание готового изделия из пресс-формы; 1 — чистовая пресс-форма, 2 —порция стекломассы, 3 — поддон-выталкиватель, 4 — пуансон, 5 — формовое кольцо, 6 — готовое изделие
Прессование не редкость прямое и косвенное (литьевое). В большинстве случаев, прямым прессованием производят изделия с развитой внутренней полостью. В этом случае применяют ручные (ПСП-2), полуавтоматические и автоматические (АПП-12, АРП-10) прессы.
Разглядим последовательность операции прямого прессования (рис. 2). В чистовую пресс-форму подается порция стекломассы в виде капли.
На нее опускается пуансон, охлаждаемый изнутри таким образом и водой формуется изделие, внешний контур которого ограничивается стенками пресс-формы, а внутренний — пуансоном. Дабы стекломасса не выдавлива-
лась из пресс-формы, на нее сверху накладывают и прижимают механизмом пресса формовое кольцо. По окончании небольшой вы держки (дабы изделие сходу не деформировалось) пуансон с формовым кольцом поднимают в исходное положение, а изделие по окончании охлаждения и затвердения удаляют из пресс-форму посредством поддона-выталкивателя 3. Прессование ведут в неразъемных либо раскрывных формах при изготовлении сложных асимметричных изделий.
Рис. 3. Последовательность формования изделия способом прессовыдувания: I— подача порции стекломассы в черновую форму, II — подвод пуансона к черновой форме, III — прессование горла изделия, IV — перенос заготовки из черновой в чистовую форму, V —выдувание изделия в чистовой форме; 1 — питатель, 2 — черновая форма, 3 — формовое кольцо, 4 — порция стекломассы, 5 — пуансон, 6 — пулька, 7 — дутьевая трубка, 8— чистовая форма, 9 — поддон
Недочёт этого метода в ограниченности применения, к примеру этим методом нельзя формовать изделия с узкими стенками (менее 2 мм), расширяющиеся книзу, с выступами либо углублениями сложной конфигурации на стенках. Помимо этого, поверхность изделий, приобретаемых этим методом, низкого качества (с кованностью, узкой матовостью) из-за твердения и резкого охлаждения стекломассы в контакте с поверхностью пресс-формы на протяжении формования.
Прессов ы дуван и е — метод формования изделий из вязкой стекломассы, в котором сочетается прессование пуансоном и выдувание. Этим методом производят, в большинстве случаев, ши-рокогорлые изделия.
Разглядим последовательность формования изделия методом прессовыдувания.
Существуют стеклоформующие автомобили (Гартфорд-28), в которых пулька в ходе формования остается неподвижной, а перемещаются черновая (отводится в сторону) и чистовая (поднимается к пульке снизу) формы.
Недочёт этого метода формования в технологии и сложности процесса, но данный метод обеспечива-вает правильное чёткое воспроизведение и регулирование толщины геометрических размеров формуемых изделий.
Цент робежно е формование основано на применении центробежной силы быстровращающейся формы. Этим методом формуют полые цилиндрические либо конические изделия разного назначения из стекол, тяжело поддающихся формованию (тугоплавких, «маленьких», кристаллизующихся).
Последовательность операций при формовании следующая. В форму подается совершенно верно отвешенная порция стекломассы, и форма начинает скоро вращаться. Создается центробежная сила, под влиянием которой стекломасса равномерно распределяется по внутренним стенкам формы, совершенно верно воспроизводя се конфигурацию.
Чем больше частота вращения, тем больше Центробежная сила и тем выше стекло поднимается в форме. Длительность формования 10… 15 с.
Изделия, отформованные этим методом, имеют ровную блестящую поверхность кроме того при сложной конфигурации. При Центробежном формовании по сравнению с другими методами уменьшается расход стекломассы благодаря тому, что не образуется формовочный колпачок. Помимо этого, данный метод легко поддаётся механизации, благодаря чему уменьшается количество Ручного труда и понижается себестоимость изделия.
Рис. 4. Последовательность формования изделия центробежным методом: I — ручной комплект стекломассы в форму для формования, II — начало подъема стекломассы в форме в момент включения вращения формы, III — окончательное формование изделия