Центробежное литье
Железные формы для центробежного литья именуют кокилями либо изложницами. Центробежный метод используют кроме этого для заливки в разовые формы, к примеру, титановых, медных, чугунных, металлических и вторых сплавов.
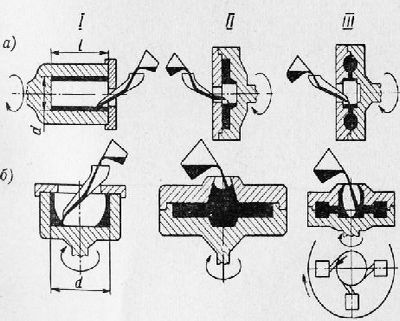
Рис. 1. Схемы центробежного литья
При литье в железную форму сплав заливают в подогрело вращающуюся форму. Он начинает вращаться под действием центробежных сил и затвердевает.
Вероятны три схемы центробежного литья.
При любой схеме ось вращения формы возможно горизонтальной, вертикальной, наклонной.
Первая схема — самый распространена. По данной схеме приобретают полые цилиндрические отливки без стержней.
На автомобилях с вертикальной осью приобретают маленькие тела вращения из-за разностенности по высоте отливки. Свободная поверхность — параболоид. Разностенность тем больше, чем выше отливка.
Вторую и третью схемы, при которых нет свободной поверхности, используют реже, в то время, когда центробежные силы применяют для увеличения плотности отливок либо улучшения заполнения тонкостенных отливок.
Особенности центробежного литья. Первая особенность. Распределившись под действием центробежных сил в виде полого цилиндра, металл охлаждается с двух сторон: с наружной — отдает тепло форме, со свободной поверхности — излучает в воздушное пространство.
В средних слоях металл остается самый горячим и, следовательно, имеет меньшую плотность.
Охлажденные на свободной поверхности частицы металла, как более тяжелые, имеющие громадную плотность под действием центробежных сил устремляются в радиальном направлении к стенкам формы и перемещаются в более тёплом и легком металле. Тёплый металл вытесняется на свободную поверхность из глубинных слоев тонущими частицами, каковые смогут быть жидкими, но более холодными.
Так при затвердевании металла во вращающейся форме в радиальном направлении непрерывно происходит конвекция. Свободная поверхность обогащается горячим металлом из глубинных слоев отливки, что предотвращает затвердевание на свободной поверхности. Затвердевание идет строго направленно.
Свободная поверхность может до последнего момента оставаться жидкой и питать отливку.
Гравитационный коэффициент показывает, во какое количество раз тяжелее делается сплав при его вращении.
Утяжеление частиц сплава есть второй, самой характерной изюминкой центробежного литья, содействующей получению плотных отливок.
В ходе питания отливки при затвердевании в неподвижной форме при простом литье перемещение маточного раствора по капиллярам происходит под действием сил земного притяжения, капиллярных сил и атмосферного давления. Эти силы довольно часто выясняются недостаточными и отливки получаются пористыми.
При центробежном литье к отмеченным силам добавляется в десятки раз громадная центробежная сила. Частицы жидкого металла перемещаются к периферии, утяжеленные в десятки раз, и заполняют непрерывно образующиеся при затвердевании межкристаллические вакуумы.
Центробежные силы создают условия не лишь строго направленного затвердевания отливки (первая особенность), но и многократно усиленного питания жидким металлом затвердевающего слоя. А это, как мы знаем, главные условия получения плотных беспористых отливок.
Третья особенность. Неметаллические и газовые включения при простом литье всплывают благодаря разности включений и плотностей металла. Они всплывают медлительно и мало возможно, дабы имели возможность всецело выделиться, поскольку на собственном дороги встречают затвердевающий сплав.
При центробежном литье свободная поверхность затвердевает последней, благодаря чему включения свободно выносятся на внутреннюю свободную поверхность. Отливки получаются с меньшим числом неметаллических включений.
Приведенные процессы, происходящие при кристаллизации отливки во вращающейся форме, свойственны для большинства сплавов. Более тёплая жидкость выходит на свободную поверхность вследствие того что она легче. Итог — последовательное затвердевание.
Но имеются исключения из этого неспециализированного правила, в то время, когда Центробежные силы смогут оказывать вредное воздействие.
Исключение первое. Жидкость неоднородная, к примеру, расплав свинцовой латуни является эмульсией . Во вращающейся форме свинец центробежными силами отбрасывается к периферии, а медь, как более легкая, вытесняется к свободной поверхности.
Ликвация может проявиться так очень сильно, что внутренняя часть отливки окажется бронзовой. Предотвратить это вредное явление возможно усилением охлаждения отливки снаружи и в один момент понижением до вероятного минимума скорости вращения формы — уменьшением К.
Исключение второе. Выпадающая жёсткая фаза легче жидкости, к примеру, заэвтектический силумин, содержащий больше 12% кремния. В начале затвердевания для того чтобы сплава выделяются кристаллы чистого кремния, каковые легче алюминия, и они центробежной силой оттесняются к свободной поверхности отливки, на которой образуется жёсткая корка.
Она образуется с двух сторон отливки. К концу затвердевания в средних слоях будут усадочные вакуумы.
В этом случае увеличение скорости вращения формы, т.е. повышение центробежной силы, будет содействовать лишь ухудшению качества отливки.
Центробежный метод литья по первой схеме разрешает применять вместо красок сыпучие, сухие, без связующих огнеупорные теплоизоляционные покрытия форм для регулирования снижения затвердевания температуры и интенсивности отливок контактного слоя формы.
Перед заливкой во вращающуюся форму, на всю ее длину вводят лоток с песком. Поворотом лотка на 90° песок высыпают; он центробежными силами распределяется по рабочей поверхности слоем равномерной толщины и является термическим сопротивлением.
Скорость вращения формы. Нужное число оборотов выбирают из условий:
1) получения отливки с верной геометрической формой, к примеру, цилиндрической, по первой схеме;
2) создания центробежных сил, нужных для оптимального процесса затвердевания отливки, т.е. получения плотных отливок.
Рис. 2. Схема получения чугунной трубы центробежным методом: а-исходное положение; б — заливка чугуна; в — окончание заливки; г — возвращение машины и извлечение отливки в исходное положение
Центробежным методом изготовляют большие отливки из легированных сталей для прокатки труб, втулки и венцы из антифрикционных сплавов, мелющие тела из белого чугуна, гильзы (автомобильных и тракторных двигателей) из легированного чугуна, напорные и сливные чугунные трубы, гребные винты (по Н-й схеме), подробности из жаропрочных и титановых сплавов (по 111-й схеме) и др. В качестве одного из примеров разглядим литье труб.
Литье труб. Метод получения труб в разовых формах вытесняется центробежным методом литья в металлические водоохлаждаемые формы. На рис.
121 приведены процесс получения и схема машины трубы. Электродвигатель через передачу вращает форму, помещенную в наполненный циркулирующей водой кожух 3. Машина может перемещаться при помощи катков. Заливочный желоб неподвижен. В мерный ковш заливают чугун.
Заливку начинают при крайнем правом положении автомобили (рис. 122, а), которая после этого перемещается влево (рис. 121, б), занимая к финишу заливки крайнее левое положение (рис.
121, в).
При возвращении автомобили в исходное положение особые клещи извлекают тёплую трубу, которую направляют в печь для термической обработки. Производительность автомобили 40-50 труб в час при внутреннем диаметре труб 200-300 мм.
Известна вторая схема автомобилей, отличающаяся тем, что перемещается заливочный желоб с ковшом, а машина не имеет возвратно-поступательного перемещения.
Чугунные трубы, изготовляемые в железных формах, имеют отбеленный на глубину до 3 мм хрупкий жёсткий наружный слой; остаточные термические напряжения в них могут быть около половины (и более) предела прочности металла, исходя из этого необходима термическая обработка труб.
При термической обработке — отжиге цементит распадается на перлит, графит и феррит и наровне с этим снимаются внутренние напряжения. Продолжительность отжига 40-60 мин.
Центробежным литьем приобретают отличные чугунные трубы, выдерживающие гидравлические опробования до 50 am. на данный момент для того чтобы кроме этого применяют полунепрерывный метод литья. Он пара экономичнее центробежного метода для больших труб диаметром более 400 мм.
—
При центробежной отливке металл заливают в форму, вращающуюся около вертикальной либо горизонтальной оси, в следствии чего жидкий металл оттесняется центробежной силой к стенкам формы, самый удаленным от центра.
Рис. 1. Форма для отливки прокатного валка
Металл, отлитый под давлением, имеет мелкозернистую структуру благодаря стремительного охлаждения в металлической форме, исходя из этого прочность подробностей, взятых отливкой под давлением, неизменно выше прочности подробностей, отлитых в песчаные формы.
Литье под давлением на данный момент активно используется в массовом производстве чтобы получить детали маленького веса из сплавов цветных металлов на базе меди, алюминия, цинка, магния, олова и свинца. Ведутся испытания по получению чугунных и металлических отливок под и т На рис. 2 приведена форма для литья под давлением. Неподвижная и подвижная частьформы составляют полость, соответствующую отливке.
Стержень помогает для образования отверстия. Жидкий металл поступает д форму под давлением через мундштук. Затвердевание отливки продолжается пара секунд, по окончании чего форма разнимается и готовая отливка выталкивается из формы толкателями.
Рис. 2. Форма для литья под давлением. давлением
Рис. 3. Поршневая машина с тёплой камерой для литья под давлением
В зависимости от положения отверстий стержни смогут размешаться как в неподвижной, так и в подвижной части формы.
Форма конструируется с таким расчетом, дабы при разъеме отливка задерживалась в подвижной части ее, в которой находятся толкатели.
Литье под давлением производится в автомобилях поршневых и компрессорных с тёплой и холодной камерой.
В поршневых автомобилях с тёплой камерой металл в форму подается под давлением поршня через мундштук. Расплавленный металл заливают в тигель, что подогревается посредством горелки 6. Из тигля в цилиндр 5 металл поступает через отверстие. Величина давления при литье колеблется от 20 до 70 кг/см2.
Поршневые автомобили с тёплой камерой используются для литья сплавов с низкой температурой плавления (свинцовых, оловянных и цинковых).
При литье более тугоплавких сплавов (бронзовых, алюминиевых) между поршнем и стенками цилиндра образуются настыли, вызывающие остановки автомобили. Для таких сплавов используются поршневые автомобили с холодной камерой, в которую заливается дозированное количество жидкого металла из отдельной печи, по окончании чего производится прессование.
Компрессорные автомобили используются, в основном, для литья под давлением алюминиевых сплавов. В них давление на металл производится сжатым воздухом. Расплавленный металл из ванны через отверстие вводится в черпак.
Для заполнения формы черпак поворачивается так, что отверстие выясняется закрытым пробкой, а мундштук входит в литник формы. Затем через отверстие черпака поступает сжатый воздушное пространство, что выталкивает металл в форму.