Изготовление промышленных отливок
Разные габаритные размеры, развес, сложность и конфигурация литых подробностей газовой турбины ГТ-12-3 обусловливают необходимость при разработке литейных технологических процессов строго личного подхода к каждой подробности.
самые крупногабаритные подробности, как, к примеру, верхняя и нижняя части улитки, формуются и планируют в горизонтальном положении, заливка же их производится в вертикальном положении.
форма по окончании скрепления и окончательной сборки болтами погружается на 3/4 собственной высоты в намерено приготовленную яму. Для предупреждения утечки металла при заливке яма около формы засыпается наполнительной смесью и шепетильно утрамбовывается пневматическими трамбовками.
форма имеет три литниковых стояка с воронками, через каковые производится заливка металла.
Средние по габаритным размерам и развесу отливки формуют, собирают и заливают в горизонтальном положении. Заливают формы через одноярусную, а время от времени двухъярусную литниковую совокупность с подводом металла в самые массивные сечения отливки, располагаемые под доходами.
самые низкие в положении при заливке подробности (менее 500 мм), к примеру, фланец улитки либо внешняя часть газовпуска, имеющие четко выраженную направленность затвердевания, заливают при помощи сифонной литниковой совокупности.
Используемая скорость подъема металла в форме должна быть большой и не должна нарушать хороший температурный градиент, что обусловливает уровень качества отливки.
Питание литых подробностей газовой турбины из стали аустенитного класса независимо от веса, габаритных размеров и др. осуществляется при помощи доходов закрытого типа.
В некоторых отливках по опыту НЗ им. Ленина используются стерженьки для не сильный саморегулирующегося давления, а в некоторых отливках воздушное давление от цеховой магистрали.
Металл в формы разливают из стопорных ковшей емкостью 3 и 10 т, в зависимости от ёмкости и веса отливки плавильного агрегата. Для обеспечения большой скорости заполнения форм металлом в любых ситуациях используют стопорные ковши с разливочными стаканчиками большого диаметра, равного 70 мм.
Внешняя часть газовпуска турбины низкого давления имеет удобную для литья форму, в которой предусмотрена «конструктивная» направленность затвердевания за счет сообщения ей конусности по всему сечению отливки. Нижняя часть отливки примерно в 2 раза уже верхней. Имеющийся круговой припуск на механическую обработку разрешает усилить направленность затвердевания металла, а при предстоящих технологических операциях значительно упрощает подготовку поверхности отливки для контроля качества ее за счет сокращения количества операций по снятию литейной корки.
Форму отливки изготовляют в парных опоках по неразъемной модели.
Наружная поверхность отливки выполняется в стержнях, внутренняя часть — конкретно в форме, облицованной хромомаг-незитовой смесью.
Питание отливок осуществляется при помощи двух доходов закрытого типа. Для улучшения питания в первый раз делается попытка-применять воздушное давление в доходах от цеховой магистрали.
Ввиду четко выраженной конструктивной направленности, отсутствия острых углов, переходов, приливов и др. и, основное, малого высоты отливки (412 мм) форма заливается при помощи сифонной литниковой совокупности с рассредоточенным подводом металла через четыре питателя.
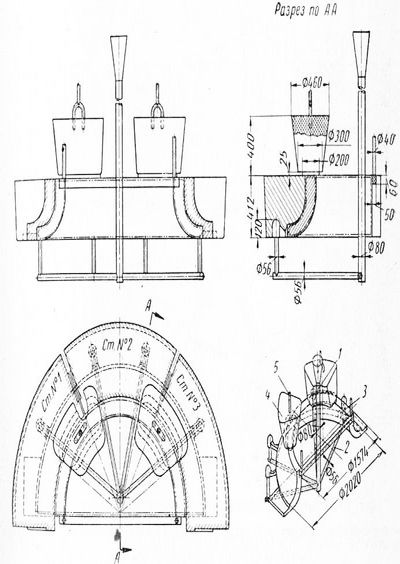
Рис. 1. Технологическая схема отливки внешней части газовпуска: 1 — литниковый стояк диаметром 80 мм; 2 — подводящий литниковый канал диаметром 56 мм; 3—питатель щелевой 40 X 80 мм; 4 — прибыль 600 X 200 X 400 мм; 5 —трубки для подвода воздушного давления в прибыль.
Контроль качества отливки по окончании неотёсанной механической обработки, и по окончании полирования и шлифования, керосиновой пробой, гамма-Дефектоскопйей, травлением и др. показывает плотный металл высокого качества и отсутствие пороков литейного происхождения.
Высокий уровень качества отливки второй половины внешней части газовпуска, изготовленной по такой же технологии, всецело подтверждает целесообразность ее применения.
Воздушное давление от цеховой магистрали в данной отливке выяснилось неэффективным, поскольку в верхних корках доходов в местах подвода воздуха найдены маленькие отверстия, свидетельствующие об утечке воздуха из полостей усадочных раковин.
Сифонный подвод металла благодаря малому хорошей технологичности и высоте отливки конструкции снабжает спокойное заполнение формы металлом и фактически не воздействует на ухудшение хорошего температурного градиента, предусматриваемого литейной и конструкцией разработкой.
Рис. 2. Технологическая схема отливки внутренней части газовпуска:
1 — литниковый стояк диаметром 80 мм; 2 — подводящий литниковый канал диаметром 80 мм; J — питатель щелевой 150 X 50 мм; 4 — питатель щелевой 180 X 50 мм; 5 — прибыль; 6 — трубки для подвода воздушного давления.
Внутренняя часть газовпуска турбины низкого давления формуется в парных опоках по неразъемной модели.
Литейная разработка подобна технологии повторной умелой отливки внутренней части газовпуска. Питание отливки осуществляется одной неспециализированной прибылью, перекрывающей всю верхнюю часть отливки.
Металл поступает в форму через двухъярусну’Ь литниковую совокупность со щелевыми питателями, подводящими металл в самые массивные части отливки — боковые фланцы.
Заливают формы из двухстопорного ковша емкостью 10 т через разливочные стаканчики диаметром по 70 мм. Литниковая совокупность имеет два стояка диаметром по 80 мм. Через щелевые питатели первого яруса на высоте 400 мм металл заполняет нижнюю часть формы.
По световому сигналу, установленному на высоте 500 мм, раскрывается металл и второй стопор до нижней кромки доходов поступает через первый и второй ярусы.
После этого первый ярус выключается и прибыль заполняется лишь через второй ярус.
Рис. 3. Технологическая схема отливки верхней и нижней половин передней части цилиндра большого давления: 1 — литниковый стояк диаметром 80 мм; 2 — подводящий литниковый канал диаметром 80 мм; 3 — распределительный литниковый канал диаметром 80 мм; 4 — питатель щелевой 120 X 20 мм; 5 — прибыль 280 X 420 X 500*.
На фланцах обеих половин отливок газовпуска по разъему наблюдались поверхностные разрозненные трещины глубиной до 25 мм и длиной до 200 мм.. При обработке они удаляются с припуском на механическую обработку.
Гамма-дефектоскопией было установлено полное отсутствие внутренних пороков в обеих отливках.
Передняя часть цилиндра большого давления (верхняя и нижняя половины, рис. 67) в отличие от внешней части газовпуска подвергается механической обработке лишь с внутренней стороны.
На внешней части подробности имеется кольцевое ребро толщиной 40 мм, идущее по всей цилиндрической части приблизительно посередине.
Условия для направленного затвердевания металла в форме создаются при помощи конусного припуска с внутренней стороны отливки, удаляемого потом при механической обработке.
Форма изготовляется в парных опоках по неразъемной модели.
Часть наружной поверхности отливки выполняется в стержнях; внутренняя поверхность — конкретно в форме.
Питание отливки осуществляется при помощи трех доходов закрытого типа.
По аналогии с внешней частью гайовпуска заливают формы через сифонную литниковую совокупность с рассредоточенным подводом металла при помощи четырех питателей.
Отмеченные мелом участки говорят о наличии на внутренней поверхности отливки двух незначительных по размеру пороков в виде надрыва и рыхлости глубиной около 3—5 мм. На наружной поверхности отливки литейные пороки отсутствуют. В целом уровень качества отливки соответствует предъявляемым требованиям и подтверждает целесообразность используемой разработке.
Подробность верхней половины передней части цилиндра отливалась по такой же технологии, что и нижняя добрая половина. Но наличие маленького горизонтального ребра (рис. 67, Р) с технологическим приливом выяснилось достаточным, дабы в месте его соединения с цилиндром появились сквозные трещины.
Образование указанных пороков разъясняется большим местным перегревом, что появился из-за наличия изогнутого прилива к ребру, расположенного весьма близко к цилиндрической части отливки, и затрудненной усадкой отливки из-за того же прилива к ребру. В первой отливке, у которой загиб ребра расположен на существенно большем расстоянии от цилиндрической части, указанные пороки отсутствуют.
Вторичная отливка верхней половины передней части цилиндра, выполненная специально для проверки этого предположения без загиба ребра, литейных пороков не имеет.
Задняя часть цилиндра большого давления формуется в парных опоках по неразъемной модели. Внешняя часть отливки выполняется конкретно в форме, внутренняя поверхность в стержнях. Питание отливки осуществляется при помощи трех доходов закрытого типа.
Доходы располагали симметрично по окружности. Ввиду большой высоты отливки (800 мм) используется двухъярусная литниковая совокупность. В первом ярусе литниковой совокупности металл подводится двумя щелевыми питателями размером 120 X 20 в нижнюю часть отливки.
Питатели второго яруса того же размера подводят металл в верхнюю, самая массивную часть отливки. Через третий питатель металл подводится в среднюю прибыль. Заливка металла в форму производилась из двух-стопорного ковша емкостью 10 т через разливочные стаканчики диаметром 70 мм любой.
По окончании неотёсанной зачистки наружной поверхности отливки и по окончании керосиновой пробы были обнаружены отдельные черновины величиной до 2 мм и участки с небольшой поверхностной пористостью. По окончании дополнительной зачистки вся чернота была удалена.
Рис. 4. Технологическая схема отливки верхней половины задней части цилиндра большого давления: 1 — литниковый стояк диаметром 80 мм; 2 — распределительный литниковый канал диамет-ром’ЯО мм; 3 — промежуточный литниковый канал диаметром 80 мм; 4 — питатель щелевой 120 X 20 мм; 5 — прибыль 320 X 480 X 500 мм.
Задняя часть цилиндра большого давления формуется в парных опоках по неразъемной модели. Внешняя часть отливки выполняется конкретно в форме, внутренняя поверхность в стержнях.
Отливка питается тремя доходами закрытого типа, симметрично расположенными по окружности. Ввиду большой высоты отливки (800 мм) используется комбинированная двухъярусная литниковая совокупность. Первый ярус литниковой совокупности представляет собой сифонный подвод металла через четыре щелевых питателя размером 120 X 20. По второму ярусу металл подводится через два щелевых питателя в верхнюю самая массивную часть отливки.
Через третий питатель металл подводится в среднюю прибыль. Заливка металла в форму производится из двухстопорного ковша емкостью 10 т.
Рис. 5. Технологическая схема отливки нижней половины задней части цилиндра большого давления: 1 — литниковый стояк диаметром 80 мм; 2 — подводящий литниковый канал диаметром 80 мм; 3 — распределительный литниковый канал диаметром 80 мм; 4 — питатель щелевой 120Х X 20 мм; 5 — прибыль 320 X 480 X 500 мм.
На внутренней поверхности отливки найдены небольшие трещины в виде сетки, каковые механической обработкой были полностью устранены.
Верхняя часть улитки цилиндра большого давления формуется и планирует в горизонтальном положении, а заливается форма в вертикальном, по окончании поворота ее на 90°.
Питание отливки осуществляется при помощи шести закрытых доходов, устанавливемых на фланцах.
В отличие от первой умелой отливки, в которой наблюдалось большое количество пороков в виде тёплых трещин и рыхлот, промышленная отливка верхней части улитки заливалась при намного более низкой температуре (1540°) при помощи двухъярусной литниковой совокупности.
Через первый ярус литниковой совокупности по аналогии с первой умелой отливкойметалл подводился в нижнюю боковую прибыль (шлакоуловитель), от которой через щелевой питатель, поступал в нижнюю часть формы. Через второй ярус литниковой совокупности металл подводился в самые массивные фланцы, на которых установлены прибыли, питающие всю отливку.
Рис. 6. Технологическая схема отливки верхней части улитки: 1 — литниковый стояк диаметром 80 мм; 2 — промежуточный литниковый канал диаметром! 80 мм; 3 — распределительный литниковый канал диаметром 80 мм; 4— питатель диаметром 56 мм; 5 — прибыль диаметром 450 мм, h = 500 мм; 6 — прибыль 750 X 500 ммг h =500 мм; 7 — прибыль 650 X 500 мм, h = 500 мм.
Результаты замеров в виде температурных кривых на данной же фигуре говорят о отсутствии направленности затвердевания металла отливки из-за подвода главной массы металла через первый (нижний) ярус литниковой совокупности.
Заливали металл из двухстопорного ковша емкостью 10 т.
На поверхности отливки наблюдалось большое количество литейных пороков в виде раковин, рыхлот и тёплых трещин, каковые по окончании зачистки и вырубки подвергались заварке и последующему контролю.
Рис. 7. Технологическая схема отливки нижней части улитки: 1 — литниковый стояк 1-го яруса диаметром 80 мм; 2 — литниковый стояк 2-го яруса диаметром 80 мм; 3 — литниковый стояк 3-го яруса диаметром 80 мм; 4 — распределительный литниковый канал 1-го яруса диаметром 80 мм; 5 — распределительный литниковый канал 2-го яруса диаметром 80 мм; 6 — распределительный литниковый канал 3-го яруса диаметром 80 мм; 7 — питатель щелевой 380 X 40 мм; 8 — питатель щелевой 420 X 140 мм; 9 — питатель щелевой 300 X 60 X 80 мм; 10 — питатель диаметром 40 мм; 11 — прибыль 850 X X 500 мм; h ‘ 600 мм; 12 — прибыль 890 X 465 мм, h = 600 мм; 13 — прибыль диаметром 430 мм, h = 600 мм.
Нижняя часть улитки большого давления по аналогии с верхней частью улитки формовалась в горизонтальном положении. Заливали форму в вертикальном положении по окончании поворота ее на 90°. Питание отливки осуществлялось при помощи шести закрытых доходов, установленных на фланцах.
Для заливки формы использовалась трехъярусная литниковая совокупность.
Через щелевой питатель первого яруса размером 380?40 металл подводится в самую нижнюю часть отливки.
Через щелевые питатели второго яруса металл поступал с двух сторон под фланцы и в средние по высоте части обоймы улитки. Через третий ярус литниковой совокупности самый горячий металл заполнял прибыли.
Показания термопар подтвердили наличие направленного затвердевания металла в форме, что говорит о целесообразности применения трехъярусной литниковой совокупности.
Заливали форму из двухстопорного ковша емкостью 10 т через разливочные стаканчики диаметром 70 мм любой по особенному режиму. Через первый ярус литниковой совокупности металл поступал в нижнюю часть отливки и создавал железную «подушку» толщиной около 500 мм.
Затем раскрывался заливка и второй стопор велась в один момент через два стопора в течение 20 сек., по окончании чего первый стопор закрывали, а металл поступаллишь через второй ярус до заполнения полостей доходов на уровне 200 мм над фланцем. Затем ковш передвигали без перерыва струи на воронку третьего яруса литниковой совокупности и заливка длилась до заполнения доходов металлом. Расстояние между второй и третьей воронками максимально уменьшалось, дабы свести к минимуму разбрызгивание металла при переходе с одной воронки на другую.
Контроль за подъемом уровня металла в форме осуществляется посредством электросветовой сигнализации.
Не обращая внимания на сложную конструкцию отливки, уровень качества ее было в полной мере удовлетворительное, имелось только незначительное количество поверхностных пороков в виде небольшой рыхлости.
Фланец нижней части улитки формовался в парных опоках по неразъемной модели. Внешняя часть отливки выполнялась в стержнях, внутренняя часть отливки —конкретно в форме.
Питание отливки осуществлялось при помощи трех доходов закрытого типа, установленных симметрично по окружности.
Ввиду маленькой высоты отливки (388 мм) использовался сифонный подвод металла через три щелевых питателя размером 120 X 20 мм любой.
За исключением двух участков небольшой пористости размером 20 х 20 мм, отливка пороков не имела.
Восемь обойм уплотнения складываются из шестнадцати половин, разных по весу и размеру. Часть обойм имеет круговой припуск на механическую обработку. Семь обойм отливались в вертикальном положении, а одна обойма для опыта в горизонтальном положении.
Для заливки обойм высотой около 500 мм использовалась сифонная литниковая совокупность, а для обойм выше 500 мм —двухъярусная литниковая совокупность.
Обойма заднего уплотнения диаметром 670 мм и высотой 340 мм подвергается со всех сторон механической обработке, исходя из этого нужная конусность для направленного затвердевания осуществляется за счет увеличенного припуска на механическую обработку.
Отливку формовали в парных опоках по неразъемной модели. Внешнюю часть отливки делали в стержнях, внутреннюю — конкретно в форме. Питание отливки осуществляли при помощи двух доходов закрытого типа.
Рис. 8. Технологическая схема отливки фланца нижней части улитки: 1 — литниковый стояк диаметром 80 мм; 2 — подводящий литниковый канал диаметром 56 мм; 3 — питатель щелевой 120 X 20 мм; 4 — прибыль 230 X 350 X 400 мм.
Ввиду малого высоты отливки (340 мм) подвод металла в форму производится сифоном, подобно подводу металла в переднюю часть цилиндра большого давления.
Обойма № 1 подвергалась механической обработке лишь с внутренней стороны, исходя из этого нужный уклон достигался при помощи повышения припуска на обработку лишь с внутренней стороны.
Подробность формовалась в парных опоках по неразъемной модели. Внешнюю часть отливки делали в стержнях, внутреннюю — конкретно в форме. Питание отливок осуществляли при помощи двух доходов закрытого типа.
Ввиду того, что высота отливок достигала 760 мм, заливали формы при помощи двухъярусной литниковой совокупности. Через четыре питателя первого яруса сечением 120 X 20 мм металл подводили в отливку снизу. Через два питателя второго яруса размером 220 X 20 металл поступал в подприбыльные территории отливки.
Рис. 9. Технологическая схема отливки обоймы заднего уплотнения диаметром 670 мм: 1 — литниковый стояк диаметром 80 мм; 2 — промежуточный литниковый канал диаметром 80 мм; 3 — распределительный литниковый канал диаметром 80 мм; 4 — питатель щелевой 120 X 20 мм; 5 — прибыль 200X320X 400 мм.
Рис. 10. Технологическая схема обоймы № 1: 1 — литниковый стояк диаметром 80 мм; 2 — промежуточный литниковый канал диаметром 80 мм; 3 — распределительный литниковый канал диаметром 80 мм\ 4 — питатель щелевой 120 X 20 мм; 5 — питатель щелевой 220 X 20 мм; 6 — прибыль 320 X 460 X 500 мм.
Обойму уплотнения (верхняя и нижняя половины) с круговым припуском на механическую обработку и высотой 745 мм изготовляли в вертикальном положении с сифонной заливкой по разработке, подобной технологии обоймы № 1 (рис. 10).
Обойму № 2 с круговым припуском на механическую обработку отливали в парных опоках по неразъемной модели. В отличие от всех остальных обойм, в порядке опыта, заливка и формовка производились в горизонтальном положении. Верхнюю часть отливки делали в стержне.
Питание отливки осуществлялось двумя доходами. Металл подводили в форму с двух сторон через два щелевых питателя.
Рис. 11. Технологическая схема отливки обоймы № 2:
1 — литниковый стояк диаметром 80 мм; 2 — промежуточный литниковый канал № 1 диаметром 80 мм; 3 — промежуточный литниковый канал № 2 диаметром 80 мм; 4 — питатель щелевой 220 X 30 мм; 5 — прибыль 220 X 490 X 300 мм; 6 — подводящий литниковый канал диаметром 80 мм.
Все остальные обоймы заднего и переднего уплотнения с круговым припуском на механическую обработку и высотой не более 500 мм отливали в вертикальном положении с сифонной заливкой по разработке, подобной технологии обоймы заднего уплотнения.