Электрохимическая размерная обработка миниатюрных изделий
Перспективным способом обработки конструктивных элементов малых размеров, основанном на ярком применении электроэнергии, есть электрохимическая размерная обработка.
Она основана на явлении анодного растворения металла в среде электролита под действием электрического тока. Наряду с этим плюс источника тока присоединен к обрабатываемому изделию, а минус— к инструменту. Процесс анодного растворения есть очень сложным и связан с массо- и теплопереносом.
Электрохимическую обработку используют для получения в высокопрочных сплавах и труднообрабатываемых металлах глубоких, наклонных отверстий, щелей, прорезей, пазов, полостей, имеющих сложную форму, и отверстий с громадным соотношением глубины к диаметру отверстия порядка 150—200; профилирования канавок, полирования узких пластин, заострения и заточки инструмента.
В качестве рабочей среды при электрохимической обработке применяют водные растворы нейтральных солей: хлористого натрия, азотнокислого натрия, хлористого калия, сернокислого натрия, и комбинации из этих солей. При применении для электрохимической обработки электролитов на базе нитрита натрия, что, как мы знаем, хороший пассиватор1, облегчаются условия борьбы с коррозией. Не считая указанных в качестве электролитов используют кроме этого водные растворы кислот.
Концентрация солей в электролите равна 5—15%, а кислоты не более 5—10%.
Производительность обработки характеризуется количеством снимаемого материала в единицу времени на один ампер подведенного тока. Так, при применении в качестве электролита раствора хлористого натрия производительность равна 2,2 мм3/мин-А, а при применении раствора азотнокислого натрия — 1,1 мм3/мин-А. В некоторых случаях за счет применения электролита, складывающегося из 3—4 компонентов, возможно существенно повысить съем материала и улучшить уровень качества обрабатываемой поверхности.
Учитывая, что все электролиты, применяемые для обработки, химически активны, с целью уменьшения их коррозионного действия как на само изделие, так и на оборудование принимаются особые меры по борьбе с коррозией.
Между электродом-инструментом и обрабатываемой поверхностью обязан выдерживаться межэлектродный торцовый и боковой зазоры, заполняемые электролитом. Величина торцового зазора пропорциональна рабочему напряжению и обратно пропорциональна скорости подачи инструмента. Торцовый зазор равен 0,01—0,075 мм.
Боковой зазор кроме этого изменяется в этих же пределах и зависит от электропроводности электролита, режимов электрода-процесса и конструкции инструмента анодного растворения.
При электрохимической обработке фактически отсутствует износ инструмента. Этим она выгодно отличается от механической и электроэрозионной обработки, износ инструмента при которых велик. Точность прошивания отверстий достигает 0,1—0,15 мм, а при профилировании полостей ±0,13 мм.
Прошивание полостей и отверстий. изготовление полостей и Прошивание отверстий создают на станках со следящими совокупностями и без них.
Электрохимическое прошивание отверстий (без применения следящих совокупностей) при постоянной подаче катода-инструмента происходит в ходе авторегулирования, т. е. в направлении перемещения катода-инструмента устанавливается такая плотность тока, при которой скорость анодного растворения материала делается равной подаче.
При электрохимическом прошивании отверстий малых размеров к электроду-инструменту предъявляют следующие требования: а) он обязан владеть достаточной жесткостью, чтобы не деформироваться и не вибрировать под действием сил, появляющихся в ходе обработки; б) рабочая часть электрода обязана содействовать ламинарному потоку электролита с мельчайшим перепадом «живых» сечений в зоне обработки; в) нерабочие поверхности электрода-инструмента должны быть надежно изолированы.
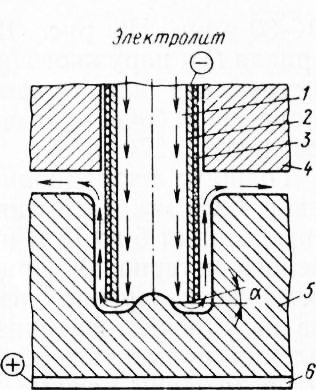
Рис. 1. Схема электрохимической обработки малых отверстий
Для получения отверстий применяют трубчатые электроды. Наличие внутреннего канала разрешает осуществлять прокачку электролита. Типовая схема обработки глубоких отверстий (диаметром 0,76 мм и глубиной 305 мм в турбинных лопатках) приведена на рис.
1. Поток электролита прокачивается под давлением через канал трубки-электрода, подключенной к отрицательному полюсу источника тока. Трубку изготавливают из химически стойкого материала (титана, нержавеющей стали) и покрывают электроизоляционным слоем. В качестве электрода-инструмента возможно с успехом применять медицинские иглы.
Покрытие должно быть нанесено ровным слоем, строго концентрично с диаметром трубки и иметь нужную механическую прочность. Благодаря применению заточки торцовой части электрода-инструмента под углом а= 10° постоянно совершенствуются условия прошивания. Толщины стены трубки и слоя изолирующего покрытия должны быть достаточны чтобы пропустить требуемое количество электролита, подводимый ток и обеспечить соответствующий боковой зазор.
Изделие 5 подключают к хорошему полюсу источника тока через контактную пластину. Для обеспечения направления перемещения электрода-инструмента предусматривается кондукторная втулка. В тех случаях, в то время, когда нужно обработать сходу пара отверстий, оси которых параллельны друг другу либо расположены под некоторым углом, нужно использование кондукторных втулок.
Одним из наиболее значимых факторов, воздействующих на возможность применения электрохимической обработки, ее экономичность, качество и точность приобретаемой поверхности, есть надежность диэлектрического покрытия инструмента. Для электрохимической обработки толщина диэлектрической пленки на нерабочей поверхности электрода должна быть 0,03—0,1 мм.
Покрытия должны владеть высокими электроизоляционными особенностями, иметь малую толщину, снабжать надежную адгезию с материалом электрода-инструмента, быть теплостойкими и технологичными. В качестве защитного покрытия при прошивании отверстий смогут быть использованы керамические эмали 17Т, 174Р, 405А и лаки на базе полиэтилфениленэтила и др. составы.
Для электроизоляции защиты и деталей приспособления его от коррозии применяют быстротвердеющий пластик — стирак-рил, что затвердевает при обычной температуре в течение 40—80 мин. На рис. 120 приведены соотношения внутреннего (кривая 1) и наружного (кривая 2) диаметров трубчатого электрода-инструмента для прошивания отверстий в никелевом сплаве.
Скорость рабочей подачи в этом случае 1,4 мм/мин при плотности тока 270 А/см2.
Толщина изоляционного покрытия на электроде-инструменте равна 0,05 мм. Используемый диапазон рабочих напряжений — в пределах от 5 до 15 В (в зависимости от электролита и обрабатываемого материала). При работе на верхнем пределе напряжения вероятно осаждение и испарение электролита побочных продуктов на рабочей поверхности электрода.
Для исключения для того чтобы явления используют обратную полярность в течение 0,3—0,4 с в течении каждых 8—20 с процесса обработки.
Использование в качестве электролитов при электрохимической обработке водных растворов кислот снабжает меньшее замусоривание межэлектродного зазора, поскольку продуктами растворения в этом случае являются не хлопьевидные гидроокислы металлов, а их ионы.
В ходе работы ввиду электролиза и испарения содержание кислот в водных растворах значительно уменьшается, благодаря чего электролит испытывает недостаток в периодической корректировке. Ответственным причиной, определяющим процесс электрохимической обработки, есть температура электролита. С ростом температуры размер отверстия возрастает, а при определенном значении начинается испарение электролита в межэлектродном зазоре, что ведет к резкому падению тока в рабочей территории и к маленькому замыканию.
При чрезмерном увеличении температуры вероятно повреждение диэлектрического покрытия.
Созданы полуавтоматические электрохимические установки для прошивания отверстий в разных изделиях. К примеру, для прошивания контровочных отверстий в гайках. Установка складывается из двух агрегатов: фактически блока и станка энергопитания. Она имеет три секции, воображающие собой отдельные рабочие позиции с свободным индивидуальным управлением и циклом работы.
Блок управления каждой позиции размещают в нижней части станины и подключают штепсельными разъемами.
Рабочее перемещение электрода-инструмента осуществляется снизу вверх. Это разрешает обеспечить вольный доступ в рабочую камеру. Инструмент закрепляют в силовой головке, имеющей электромеханический привод.
Наряду с этим обеспечивается получение трех -скоростей рабочего хода и столько же холостых ходов.
Блок энергопитания совмещает в себе бак с электролитом, источник питания и насосную установку. Бак снабжен коллектором, для слива осевших продуктов растворения, и холодильником. Выпрямитель по трехфазной однополупериодной схеме собран на силовых диодах ВКД-200. Мощность источника питания 2 кВт. Насос для подачи электролита шестеренчатого типа выполнен в антикоррозийном выполнении и снабжен устройством для автоматической выборки торцового зазора.
Производительность- установки 96 гаек в час.
Рис. 2. График зависимости диаметра трубки от диаметра отверстий
Рис. 3. Приспособление для прошивания отверстий
Для прошивания отверстий диаметром 0,8 мм и более в тонкостенных трубопроводах (толщина стены 0,3—0,5 мм) с подачей электрода-инструмента, равной скорости растворения материала, помогает электрохимическая установка УЭТ-1, рабочая головка которой выполнена в виде ручного пистолета. На корпусе закреплена головка со сферической рабочей поверхностью и с уплотняющим наконечником, электродвигатель подачи с винтом и редуктором, связанным со штоком, в котором закреплен электрод-инструмент, и реле давления. Для обеспечения подачи электролита помогает гидравлическая совокупность, складывающаяся из насоса, трубопроводов, двухпозиционного электромагнитного клапана, дросселя.
Для получения отверстий головку через уплотнительный наконечник прижимают к поверхности изделия. Между сферической поверхностью и изделием, заготовки образуется рабочая камера А, которая заполняется электролитом по трубопроводу от насосной установки. Электролит сливается из рабочей камеры в бак насосной установки по трубопроводам через дроссель и клапан, что помогает для установления нужного давления подпора в рабочей камере. На давление подпора настроено реле давления.
При подаче напряжения на катод-инструмент и включении электродвигателя подачи инструмент через уплотнение в отверстии головки приближается к обрабатываемому изделию и прошивает отверстие. В момент образования сквозного отверстия поток электролита меняет направление, устремляясь в появившееся отверстие. В рабочей камере А давление значительно уменьшается, и реле давления переключает клапан, закрывающий трубопровод и открывающий трубопровод, по которому электролит от насосной установки по трубопроводу подается в рабочую камеру и потом в появившееся отверстие, омывая электрод с наружной стороны.
При уменьшенном предварительном торцовом межэлектродном зазоре в начале процесса обработки происходит замыкание либо сильное искрение, что портит электрод и поверхность изделия-инструмент. Давление электролита выбирают таким, дабы обеспечить нужную скорость течения электролита в рабочей территории межэлектродного зазора. В большинстве случаев оно равняется 10 — 25 к Гс/см2.
В качестве электродов-инструментов используют трубки из нержавеющей стали либо медицинские иглы диаметром на 0,2 — 0,5 мм меньше диаметра прошиваемых отверстий. При обработке получается отверстие с маленьким уклоном. Прошивание ведется при токе 8—12 А, напряжении 12—16 В и скорости подачи электрода-инструмента 1—8 мм/мин.
В качестве электролита применяют 12—15%-ный раствор азотнокислого натрия.
Размеры отверстий, прошиваемых электрохимическим способом, лимитируются диаметром электрода, толщиной защитного слоя, боковым зазором и т. д. Воображает определенный интерес получение отверстий диаметром 0,05—0,3 мм, в то время, когда роль электрода-катода делает отрицательно заряженная струя электролита, вытекающего из диэлектрического (стеклянного) сопла с высокой скоростью. Струя на определенном отрезке сохраняет размеры и форму отверстия в сопле.
Для обеспечения нужного заряда в сопло введен проводник, что подключен к источнику постоянного тока. Изделие, в котором нужно взять отверстие, подключено к хорошему полюсу.
получение и Разрезание пазов. Рациональным есть использование электрохимического способа для разрезки труднообрабатываемых токопроводящих материалов, получения узких пазов, правильных прорезей, канавок и т. д.
Рис. 4. Безэлектродное прошивание отверстий
Но имеются и различия. В частности, отсутствуют термические действия в зоне обработки и не изнашивается электродная проволока, чем допускается повторное ее применение. При исполнении пазов и вырезании обеспечивается подача изделия, а не инструмента.
Между поверхностью реза и проволочным электродом обеспечивается межэлектродный зазор А. Величина зазора 0,07—0,12 мм.
Подвод электролита в зону обработки создают посредством сопла. В качестве электролита применяют водные растворы хлористого, азотнокислого натрия концентрацией 8—18%. Напряжение на электродах при исполнении в металлическом изделии прорези проволокой диаметром 0,2 — 0,25 мм образовывает 20 В. Ширина реза пара значительно уменьшается при снижении концентрации и увеличении подачи электролита.
В некоторых случаях для получения пазов, разрезания и щелей заготовок используют электрохимическую обработку дисковым электродом. Между изделием и диском обеспечивается межэлектродный зазор А, в который по трубке подается электролит. Диску сообщается вращение, и и подача в направлении заготовки.
Проволочный либо дисковый заготовки и электроды подключают к источнику постоянного тока. Наряду с этим полярность сохраняется прямой. Как и при размерной обработке отверстий, при исполнении узких пазов, щелей и вырезании по контуру имеет место скругление кромок. Радиус скругления пара значительно уменьшается при повышении подачи. Электрохимическая обработка более производительна, чем электроэрозионная.
Но электрохимический метод дает меньшую точность. Это ограничивает область его применения.
Рис. 5. Электрохимическое прорезание пазов
Рис. 6. Электрохимическое профилирование
Прорезание узких пазов, щелей и вырезку по контуру возможно создавать на электрохимическом станке для фасонного вырезания МА-4429. В качестве инструмента применяют латунную проволоку диаметром 0,1—0,3 мм. Наряду с этим ширина прорезаемых пазов и щелей образовывает соответственно 0,6—1 мм. Вместо проволоки используют кроме этого стержень диаметром 0,5 мм и более, что позволяет приобретать криволинейные пазы шириной 0,8 мм. Получение сложного контура реализовывают посредством копирной совокупности.
Поток электролита, проходящий через особое сопло, формирует около катода «рубаху», снабжающую стабильность процесса обработки. Скорость обработки может колебаться в зависимости от толщины изделия от 0,5 до 10 мм/мин. Шероховатость поверхности паза Ra ^ 2,5—0,63 мкм.
Точность при исполнении прямолинейных пазов 0,02 мм, а криволинейных —0,06 мм.
Профилирование. Часто необходимо в образовании на изделиях профилированных канавок, полостей, фигурных углублений. При электрохимическом профилировании канавок особенную трудность воображает обеспечение точности малого радиуса дна канавки (R = 0,1 + 0,05 мм) в сочетании с надлежащей геометрией по диаметру и углу.
Исполнение этих условий зависит от точности изготовления инструмента (диска-катода), размеры которого должны зеркально отображать профиль канавки с учетом величины межэлектродного зазора, и, помимо этого, от величины его радиальных и осевых биений.
Электрическая доводка диска-катода способом обратной полярности по эталонной канавке не снабжает получения радиуса R = 0,1 мм, поскольку острые кромки растворяются. В большинстве случаев при установке нового диска на шпиндель электрохимического станка он подвержен биению, которое тяжело устранить ввиду большой окружной скорости вращения диска. Для устранения этих недочётов используют следующий метод приспособления диска-и профилирования катода.
Приспособление основанием устанавливают (базисной частью типа «ласточкин хвост») на столе станка, фиксируют двумя винтами и закрепляют гайками и сменными болтами. Инструмент для профилирования диска размещают в гнезде державки, которую возможно регулировать в вертикальном положении, а за счет поворота кронштейна — ив горизонтальном положении. Для ускорения настройки кронштейн имеет нониус с делениями.
Профилирование создают следующим образом. Предварительно обработанный на токарном станке диск-электрод из нержавеющей стали либо титановых сплавов ОТ4, ОТ4-1, ВТ14 закрепляют в шпинделе электрохимического станка.
Крепление диска-катода на шпинделе станка продемонстрировано на рис. 124, в. Диск насаживают на бронзовое кольцо, которое через меднографитовые щетки соединено с отрицательным полюсом источника тока. Кольцо вместе с диском изолируют от шпинделя текстолитовой втулкой, запрессованной на шпинделе станка. При вращении шпинделя вместе с диском посредством спаренных резцов снимают припуск с углов диска.
Вращение шпинделя создают вручную.
Хороший полюс источника постоянного тока присоединяют к обрабатываемому диску, а отрицательный — через корпус и клемму к алмазным брускам. Так как алмазные зерна, находящиеся в алмазоносном слое брусков и выступающие из токопро-водящей связки, не выполняют ток, то они создают между электродами нужный зазор, непрерывно заполняемый электролитом. При прохождении тока через электролит происходит электрохимическое растворение, и материал с поверхности диска снимается, а продукты растворения удаляются электролитом и алмазными зёрнами.
Доводка характеризуется фактически малым силовым действием на обрабатываемую поверхность и отсутствием деформации инструмента. Низкое напряжение (2—5 В) снабжает течение процесса без дугообразования и бездефектную обработку.
Шероховатость поверхности диска по профилю не осуществляют контроль, поскольку на образующей диска не остается рисок, каковые при последующей электрохимической обработке смогут быть всецело перенесены на подробность.
Для получения острия на периферии диска-электрода технологический ток в конце обработки выключается на 5—15 с. Геометрию диска по всем параметрам без снятия его со станка проверить тяжело, исходя из этого доводку делают до получения на пробной подробности требуемых размеров. В окончательном виде размеры профиля диска зависят от состава электролита, электрических, гидравлических и механических режимов, и от марки обрабатываемого изделия. Профиль диска доводится всегда при обработке второй марки материала, поскольку для этого как правило требуется поменять режимы и состав электролита алмазной обработки.
Электролит, применяемый для доводки, складывается из 4—5% хлористого натрия (по весу), 4—5% калийной селитры; 1,3% бромистого калия, 0,5% сернокислого безводного натрия, другое — вода.
По окончании окончательной доводки профиля диска электролит очищают, поскольку в ходе последующего профилирования, канавок на изделиях может случиться электрический контакт электродов благодаря засорения межэлектродного зазора металлической пылью и стружкой. Для облегчения процесса очистки в первом отсеке главного бака имеется маленькой, легко вынимающийся бачок. Особенно шепетильно нужно очищать электролит при изготовления диска-катода из титановых сплавов, поскольку они владеют малым удельным весом и их частицы медленнее скапливаются на дне бачка.
Обрисованный метод доводки профиля диска-катода снабжает: требуемую точность и геометрию (наряду с этим радиус дна канавки возможно взять менее 0,1 мм, а овальность по внутреннему диаметру канавки —в пределах 0,02 мм); шероховатость поверхности канавки на титановых сплавах Ra’^ 1,25 мкм. Применив диск-катод иного профиля, возможно взять новый требуемый профиль канавки.
Рис. 7. Электрохимическое полирование фольги
Имеются попытки изготовления узкой проволоки диаметром 0,03—0,05 мм из труднообрабатываемых и малопластичных материалов: титана, молибдена и др. Процесс пребывает в протягивании большего диаметра проволоки (предварительно взятой простыми способами) с малым упрочнением через отверстие, в которое подается электролит. Обрабатываемая проволока является анодом, а волока либо дюза — катодом.
Полирование узких пластин. Для получения изделий из фольги тугоплавких сплавов толщиной в пара микрон и точностью до долей микрона используют электрохимическое размерное полирование. Так, к примеру, фольга из сплава вольфрам — рений марки ВР-27ВП имеет толщину 0,02 мм с допуском на толщину порядка 0,006 мм.
Исходя из этого для получения стабильной улучшения качества и толщины фольги ее поверхности используют электрохимическое полирование. Режимы полирования фольги толщиной до 0,005 мм из вышеуказанного сплава следующие: напряжение на электродах —6 В; удельное давление, снабжающее прижим Держателя фольги к сетке-притиру, образовывает 0,1 кГс/см2. В качестве электролита применяют 1%-ный водный раствор виннокислого натрия с добавкой окиси хрома числом 50 г/л.
Для электрохимического размерного полирования применяют устройство, схема которого продемонстрирована на рис. 7. Держатель фольги, складывающийся из упора, прокладки и обоймы посредством самоустанавливающегося центра 8 присоединен к хорошему полюсу источника постоянного тока. Отрицательный полюс этого источника присоединен к вращающейся планшайбе, образующей вместе с сеткой-притиром катод-инструмент. Через держатель производится подвод тока к полируемой фольге.
Трубка помогает для подачи электролита на поверхность катода-инструмента.
Сначала создают полирование держателя с применением прокладки уменьшенной высоты. Наряду с этим обоймы и торцы упора обрабатывают заподлицо, создавая поверхность, эквидистантную рабочей поверхности катода-инструмента и являющуюся технологической базой. После этого берут прокладку большей толщины.
Отличие в толщинах прокладок равна толщине заготовки фольги. Совершив замену прокладок, приобретают свободное пространство под торцом упора, куда и помещают заготовку фольги для доводки и полирования. При полировании заготовок фольги, окончательный размер которых более 0,005 мм, вместо железных прокладок возможно использовать резиновые.
Рис. 8. Устройство для заострения изделий и электрохимической заточки
Заточка. Явление интенсивного электрохимического растворения материала с острых кромок используют для заточки игл, электродов, наконечников и других острых предметов. Процесс основан на анодном растворении металлов в условиях неравномерного электрического поля.
В качестве электролита применяют водные растворы хлористого, сернокислого и азотнокислого натрия, нитрит натрия и др. солей, используемых при электрохимической обработке. При верно подобранных составе и режимах электролита уровень качества поверхности затачиваемых изделий удовлетворительное. В зависимости от его сечения и материала изделия процесс ведут на режимах: напряжение 8—15 В; плотность тока 4—7 А/см2.
Наряду с этим изделие всегда перемещают, осуществляя тем самым форму угла острия и регулировку заточки.
Для электрохимической заточки миниатюрных электродов помогает устройство, складывающееся из основания, на котором установлена ванна с электролитом и опущенным в него катодом. К основанию прикреплен штатив, соединенный со штангой посредством оси с рукояткой. Приспособление соединено со штангой при помощи хомутика.
В корпуса приспособления помещен электродвигатель, что при помощи закрепленного на его оси поводка соединен с валиком, передающим вращение затачиваемому электроду, укрепленному в цанге. В средней части валика при помощи регулировочных винтов и оси закреплена в заданном положении втулка с кольцевой канавкой на периферии.
В зависимости от требуемого угла заточки электрода регулируют угол наклона втулки, определяющий амплитуду вертикального перемещения электрода в ходе его перемещения. На конфигурацию затачиваемого электрода воздействует угол его наклона к зеркалу электролита. футляр 6 и Кожух 7 приспособления выполнены из диэлектрика.
Совместное возвратно-поступательное и вращательное перемещение затачиваемого электрода дает возможность приобрести по его окружности равномерную заточку. Наряду с этим достигается соосность острия с конической и цилиндрической частями электрода.
Получение отверстий в бриллиантах. Разновидностью электрохимического метода обработки есть обработка отверстий в фильерах и алмазных волоках, основанная на явлении Пельтье — выделении тепла в месте контакта двух разных проводников в зависимости от направления электрического тока.
Являясь диэлектриком, бриллиант не поддается электрохимической и электроэрозионной обработке хорошими способами, исходя из этого для разрушения его употребляется разложение электролита под действием электрического тока. В следствии разложения электролита выделяется кислород. Расположенный в близи от острозаточенного тугоплавкого (вольфрамового) электрода-инструмента бриллиант, помещенный в оправку, благодаря большой температуры и выделяющегося кислорода выгорает.
Рис. 9. Получение отверстий в бриллиантах
В качестве рабочей жидкости применяют 1—3%-ный водный раствор азотнокислого калия. Питание на электрод-кольцевой электрод и инструмент подается от сети переменного тока через регулировочный автотрансформатор. Напряжение на электродах 220 10% В; величина тока в цепи порядка 1—2 А. На рис. 9, б приведена принципиальная электрическая схема для обработки бриллианта.
Уровень рабочей жидкости поддерживается на 20—30 мм выше поверхности.
В ходе работы вольфрамовый электрод сгорает и изнашивается. Для прошивания лунки глубиной 0,1—0,15 мм нужно поменять пара электродов. Площадь кольцевого электрода должна быть многократно больше площади электрода-инструмента. При подаче кислорода в зону обработки разрушения алмаза и процесс выгорания интенсифицируется, и производительность обработки возрастает. Процесс образования отверстий долгий и длится 12—20 ч. Микротрещин на бриллианте в большинстве случаев не замечают.
Стойкость волок, обработанных обрисованным методом, выше многократно если сравнивать с волоками, обработанными механическим сверлением.
По окончании прожигания отверстий в бриллианте нужна доводка отверстия и последующая обработка механическим способом.