Размерная ультразвуковяа обработка миниатюрных изделий
Процесс ультразвуковой размерной обработки основывается на разрушении материала изделия при скалывающем и долбящем действии абразивных частиц под действием колеблющегося с ультразвуковой частотой инструмента, торец которого выполнен по форме требуемого конструктивного элемента.
Процесс ультразвуковой обработки осуществляется следующим образом. При подаче напряжения от ультразвукового генератора в обмотку магнитострикционного преобразователя он изменяет собственные размеры с частотой подводимого тока.
Амплитуда продольных колебаний магнитострикционного либо пьезокерамического преобразователя в среднем достигает 0,008—-0,015 мм. Для концентрации звуковой энергии на меньшей площади и одновременного повышения амплитуды колебаний инструмента в колебательной совокупности ультразвукового станка предусматривается концентратор. Инструмент крепят к нижнему финишу концентратора.
Амплитуда колебаний инструмента наряду с этим достигает 0,08 — 0,1 мм. Для обеспечения процесса ультразвуковой обработки инструментприжимают к обрабатываемой поверхности и под него подают абразивную суспензию. Острые края абразивных частиц 2, плотность которых достигает 40—100 тыс. см2 с громадной частотой повторения ударов (16—25 тыс. ударов в 1 с) приводят к интенсивному разрушению материала изделия.
В следствии скалывания и разрушения микроскопических количеств материала изделия на нем образуется негативное изображение инструмента. Свойство разрушаться под скалывающем действии абразивных зерен у разных материалов разная. Самый действен ультразвуковой способ при обработке изделий из стекла, кварца, кремния.
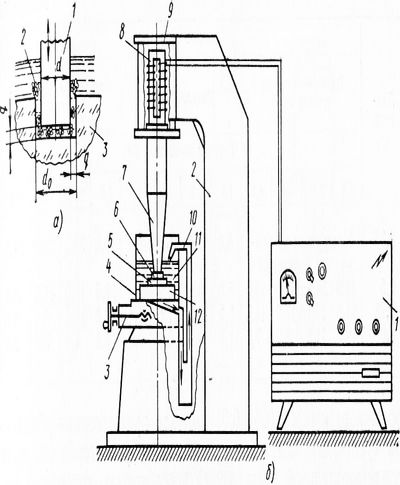
Рис. 1. Ультразвуковая размерная обработка
Производительность ультразвуковой обработки (либо количество материала, разрушаемого и удаляемого в единицу времени) зависит от частоты подводимых колебаний, упрочнения прижатия инструмента к изделию, глубины обработки, зернистости и типа абразива, инструмента и материала изделия.
В качестве рабочей среды применяют абразивную суспензию, складывающуюся из материалов, каковые жёстче материала обрабатываемых изделий. К ним относятся карбид кремния, карбид бора, корунд, борсиликокарбид, природный и синтетический алмазный порошок и др. Чаще всего для обработки изделий из стекла, других материалов и керамики используются карбид кремния и карбид бора.
Порошки из этих материалов владеют хорошей режущей свойством и имеют малую цена.
Для ультразвуковой обработки применяют, в большинстве случаев, порошки небольшой зернистости со средним размером зерна 0,01— 0,04 мм. Для точных и доводочных работ используются порошки размером 0,005—0,01 мм. Для изготовление абразивной суспензии значительно чаще используют воду, которая владеет удовлетворительной смачивающей свойством, высокой плотностью и хорошими охлаждающими особенностями, и минеральное либо рафинированное масло.
Абразивную суспензию приготовляют из расчета 45—55% по весу образовывает жидкость, а другое порошок.
На рис. 1, б приведена схема ультразвукового станка. Магни-тострикционная (либо пьезокерамическая) головка крепится к корпусу станка. Питание ее осуществляется от ультразвукового генератора.
На передней панели генератора выведены устройства, тумблеры, настройки и рукоятки управления на требуемую частоту. Колебательная совокупность станка складывается из магнитострик-ционного концентратора и преобразователя. Инструмент прижимается к поверхности обрабатываемого изделия, расположенного на подставке. Все это помещено в ванну с абразивной суспензией.
Для эвакуации продуктов подачи и обработки свежей суспензии предусмотрена совокупность ее регенарации и прокачки. Станок снабжен механизмами вертикальной и горизонтальной подач.
Инструмент. Материалом для инструмента помогают сплавы и металлы, имеющие меньшую твердость, чем обрабатываемая подробность, а следовательно, и меньший износ от абразивных частиц. Для инструмента применяют малоуглеродистые, инструментальные, нержавеющие стали, ее сплавы и медь, другие материалы и вольфрам.
Относительный износ инструментов из малоуглеродистых сталей 20, 35, стали 45 и У8, и нержавеющей стали аустенит-ного класса образовывает в среднем 3—4%.
Инструмент делают целым либо составным и крепят к колебательной совокупности ультразвукового станка посредством резьбового соединения. Для правильного крепления инструмента торцовую посадочную поверхность делают строго перпендикулярной оси инструмента и шепетильно обрабатывают. Размеры рабочей части инструмента выполняются с учетом разбивки отверстий.
Рис. 2. Инструмент для ультразвуковой обработки
Размеры рабочего профиля инструмента для обработки отверстий уменьшают на величину поправки, а размеры внутреннего контура полого инструмента при обработке подробностей по наружному контуру увеличивают на величину поправки.
Крепление рабочей части к державке составного инструмента значительно чаще создают пайкой. При обработке отверстий в минера-локерамике в качестве инструмента используют иглы из нержавеющей стали. Иглы вставляют в торцовое отверстие концентратора по скользящей посадке без пайки. Наряду с этим используют как целые, так и полые инструменты.
Наряду с этим утраты звуковой энергии в местах соединения инструмента с концентратором малы.
В качестве рабочих частей инструментов применяют калиброванную проволоку «серебрянку», и швейные иглы. Острие иглы предварительно шлифуют до требуемого размера, а после этого ее вставляют в обойму (верхней частью) и припаивают.
Для изготовления одиночного либо группового пустотелого инструмента используют калиброванные никелевые трубки либо медицинские иглы, имеющие наружный диаметр 0,15 мм и более.
Перспективным направлением есть использование вращающегося алмазно-абразивного инструмента. Тонкодисперсному порошку природных либо синтетических алмазов способом прессования и гальваностегии придается форма, являющаяся зеркальным отображением формы полости, которую нужно взять на изделии. Посредством цилиндрического штифта алмазную коронку припаивают к державке, которая в верхней части имеет резьбовое отверстие для крепления к звуковой совокупности станка.
В ходе работы инструменту информируют не только ультразвуковые колебания, но и придают вращательное перемещение около оси. Ультразвуковая обработка с применением для того чтобы инструмента есть более производительной если сравнивать с обработкой в среде абразивной суспензии.
Оборудование. Отечественной индустрией для ультразвуковой обработки выпускаются как особые, так и универсальные малогабаритные станки. На рис. 3, а приведена схема настольного ультразвукового станка МЭ-22, предназначенного для обработки алмазных волок, применяемых в производстве узкой прецизионной бронзовой, вольфрамовой, алюминиевой и других проволок.
Ультразвуковой станок помогает для того чтобы алмазных волок, и для исправления изношенных.
Рис. 3. Ультразвуковая обработка алмазных волок
Диаметры обрабатываемых и исправляемых отверстий равны 0,3 мм и более. Рабочая частота обработки — 22 кГц. Упрочнение подачи регулируемое и образовывает 20—200 г. Мощность питающего ультразвукового генератора —0,1 кВт.
Для точности обработки и повышения производительности шпинделю звуковой головки с вмонтированным в него ультразвуковым вибратором сообщается вращательное перемещение от электродвигателя постоянного тока. Вертикальное установочное перемещение головки создают посредством гайки и ходового винта. Ванночка, на дно которой устанавливают заготовку волоки, перемещается вертикально по направляющим качения, причем поджим заготовки к игле-инструменту производится соленоидом.
Пространство, образованное между двойными стенками ванночки, сообщается с полостью, затянутой упругой диафрагмой. Кулачок, приводимый в перемещение электродвигателем, иногда давит на диафрагму посредством рычага. Образующиеся наряду с этим пульсации давления иногда откачивают суспензию из ванночки и опять возвращают ее, осуществляя тем самым перемешивание.
Предусмотрено вертикальное ручное установочное перемещение ванночки посредством гайки и ходового винта, и установочное перемещение головки при правке инструмента.
Правку инструмента создают шлифовальным кругом, приводимым во вращение электродвигателем. Шлифовальная головка установлена на двойном суппорте, один из которых снабжает перемещение круга в зону правки инструмента, а второй — перемещение круга на протяжении образующей инструмента и установку траектории этого перемещения для заточки рабочего финиша инструмента под углы 12, 36 и 90°. Возвратно-поступательное перемещение круга создают вручную ручкой суппорта.
Глубина резания за любой двойной движение круга обусловливается перемещением шлифовальной головки по суппорту от дифференциального винта при застопоренной ходовой гайке. Для правки шлифовального круга применяют бриллиант, а для проверки измерения заточки амплитуды и качества инструмента его колебаний помогает микроскоп, установленный на направляющих. При повышении 35х и длине свободного отрезка 23 мм микроскоп снабжает отсчет с точностью до 0,02 мм.
В станине помещен электродвигатель с вентилятором, снабжающим воздушное охлаждение вибратора.
В станке применена двухполуволновая колебательная совокупность с магнитострикционным ультразвуковым вибратором из никеля, катеноидальным концентратором и опорным резонансным фланцем. Катеноидальный концентратор снабжает нужное усиление амплитуды колебаний прикрепленного посредством гайки сменного инструмента.
Помимо этого, он отличается достаточной поперечностной жесткостью и одновременно с этим благодаря собственной конфигурации не мешает создавать правку инструмента и абразивную заточку. Крепление опорным резонансным фланцем переменного сечения снабжает малые утраты ультразвуковой энергии. Отверстия во фланце помогают для прохода воздуха, охлаждающего вибратор.
Подвод подмагничивания и тока возбуждения к вибратору производится через щетки и контактные кольца.
Рис. 4. Головки ультразвуковых станков: а — магнитострикционная; б — пьезокерамическая; в — магнитострик-ционная повышенной точности
Все органы электроуправления и контроля сосредоточены на панели станка. Амперметр, измеряющий величину тока в соленоиде, помогает для определения силы прижима заготовки волоки к инструменту. Источником высокочастотного переменного тока, питающего вибратор, есть ультразвуковой ламповый генератор УМ2-01 с свободным возбуждением.
Заготовка волоки прижимается к инструменту с силой 60—80 Г. Обработку ведут в водной суспензии синтетического алмазного порошка АСМ14 — АСМ40 из расчета 0,7 карат алмазного порошка на 1 карат кристалла бриллианта. Возможно использован и естественный бриллиант, но синтетический дешевле в 1,8 раза. Концентрация алмазного порошка берется около 12% по массе для естественного бриллианта и 16—20% —для синтетического.
Не считая магнитострикционных преобразователей для целей обработки взяли распространение пьезокерамические преобразователи, в которых в качестве источника механических колебаний применяют пьезокерамику. Пластина из пьезокера-мики посажена на стержень корпуса и прижата через рабочую прокладку гайкой. К нижнему финишу корпуса прикреплен концентратор с инструментом. Преобразователь помещен в стакан, что крепят к нему посредством гайки.
Пьезокерами-ческие преобразователи несложнее в эксплуатации и имеют более большой к. п. д. При подаче тока высокой частоты пьезокерамика преобразует высокочастотные колебания в продольные механические колебания инструмента, под действием которых в присутствии абразива происходит обработка.
Для увеличения производительности, улучшения и точности качества обработки используют магнитострикционную головку, которая информирует рабочему инструменту попеременно продольные и поперечные колебания. Это достигается тем, что корпус головки снабжен вращающимся шпинделем, в котором укреплен магнитострикционный преобразователь, складывающийся из двух частей, питаемых от источника высокочастотного переменного тока.
Колебательная совокупность головки складывается из двух однообразных магнитострикционных преобразователей, трудящихся в режиме продольных колебаний. Преобразователи соединены с разрезным двухканальным концентратором, несущим зажим для инструмента. Концентратор прикреплен к стакану опорными фланцами , находящимися соответственно в пучности и в узле смещения. Стяжка снабжает жесткость концентратора. Стакан вращается в корпусе посредством электродвигателя через зубчатую передачу.
Обмотки магнитострикционных преобразователей питаются от двухфазного генератора, имеющего сдвиг фаз 180°. Обмотки смогут быть переведены на работу в однофазном режиме.
Кроме обрисованного выше станка для обработки круглых и профильных отверстий малых диаметров используют ультразвуковые станки ЛЭ-400, А.209.05 и др.
Ультразвуковой станок ЛЭ-400 рекомендован для обработки правильных отверстий диаметром от 0,2 мм и более конфигурации и различной формы, пазов, щелей, раскроя и разрезки заготовок из жёстких материалов.
Наличие ручной микрометрической подачи изделия к инструменту разрешает повысить чувствительность подачи, благодаря чему на станке возможно создавать обработку малых конструктивных элементов с высокой точностью. В случае если станок имеет магнитострикционный преобразователь, то он должен быть укомплектован лампово-транзисторным генератором УЗГ-0,2ЛТ мощностью 200 Вт; в случае если же он имеет пьезокерамический преобразователь, то полупроводниковым генератором мощностью 100 Вт. Последний имеет фиксированную частоту 22 кГц и не требует дополнительных регулировок.
Станок оснащают специальной оснасткой и набором приспособлений, расширяющей его технологические возможности. Для размерной обработки отверстий диаметром 0,5 мм и более используют настольный ультразвуковой станок УЗСН-З. Для обработки драгоценностей, цветных поделочных и технических камней применяют настольный ультразвуковой станок НУПС-1. Мощность его генератора 100 Вт.
Минимальный диаметр пришиваемых отверстий —0,2 мм.
Обработка отверстий. Часто необходимо получения одного либо нескольких отверстий в жёстких материалах. В некоторых случаях нужно взять до ста и более отверстий.
Изюминкой ультразвуковой обработки отверстий малых размеров в жёстких материалах есть большая возможность скола краев отверстия при выходе инструмента. Для предотвращения этого нежелательного явления перфорируемое изделие приклеивают к стеклянной пластине-подложке, и снижают давление на инструмент в момент его выхода.
В ходе ультразвуковой обработки отверстий ввиду поперечных колебаний инструмента наблюдаются завалы на входе отверстий. Ликвидируют их методом калибровки и шлифованием по плоскости. В зависимости от количества, размещения, размеров отверстий в изделиях используют соответствующую технологическую оснастку. Так, для получения одиночных отверстий используют инструмент с одним рабочим элементом.
Обработку отверстия наряду с этим ведут с применением накладного шаблона-кондуктора. Он имеет посадочную поверхность по наружному либо внутреннему контуру изделия. В шаблоне предусмотрено направляющее отверстие для прохода и ориентации инструмента.
Минимальную высоту направляющего отверстия принимают равной одному либо полутора диаметрам прошиваемого отверстия. Шаблоны изготавливают из легкообрабатываемых материалов.
Ультразвуковую обработку, к примеру, используют для прошивания 81 отверстия диаметром 0,8 мм в ситалловой плате толщиной 0,5—0,6 мм. Наряду с этим применяют многоэлементный (81 элемент) инструмент с запаянными калиброванными штырями.
Заготовку платы в разогретом состоянии приклеивают шеллаком к стеклянным подкладкам, размеры которых в плане пара превышают размеры платы, а базисные края последней на 0,5—• 1,0 мм поддерживаюткромки подкладки, что разрешает верно ориентировать подробность по упорам установочного приспособления. Приклеивание реализовывают чтобы исключить происхождение сколов при выходе инструмента из материала.
По окончании обработки стеклянную подкладку разогревают и отсоединяют изделие. Поверхность подкладки очищают от остатков клея и применяют повторно, приклеивая изделие к второй ее плоскости.
Посредством шаблона приспособление базируется относительно инструмента, а после этого крепится струбцинами к основанию пружинного столика, установленного на столе ультразвукового станка. Пружинный столик помогает для обеспечения стабильности и плавной подачи прижима. Он складывается из неподвижного корпуса, в обойме которого по шариковым направляющим перемещается основание. Перемещение осуществляется под действием спиральной пружины.
Для измерения величины перемещения стола предусмотрен индикатор. Столик снабжает плавную подачу обрабатываемой платы, с упрочнением около 50 г и его использование сокращает поломку изделий и инструмента.
Рис. 5. Пружинный СТОЛИК для плавной подачи при ультразвуковой обработке
Ультразвуковым инструментом есть ступенчатый концентратор, в торце которого выполняются отверстия в соответствии с размещением отверстий в плате. Из калиброванной металлической проволоки диаметром 0,8 мм нарезают штыри. отверстия концентратора и Концы штырей лудят оловом, а после этого паяют встык. По окончании пайки торцы штырей шлифуют; наряду с этим на штыри надевают кондуктор, предотвращающий их деформацию.
Вылет штырей около 6 мм.
Закрепив в приспособлении подкладку с платой, приспособление базируется довольно закрепленного на концентраторе инструмента. После этого приспособление крепят к основанию пружинного столика. До износа инструмента установочное приспособление не переналаживают и не снимают с пружинного столика, а И только заменяют обработанную плату (приклеенную на подкладку) новой, приготовленной для обработки.
Лишь по окончании замены либо перестановки инструмента создают переналадку установочного приспособления. В качестве абразива применяют порошок карбида бора, водную суспензию которого наносят кисточкой на поверхность платы. Подача абразивной суспензии насосом в этом случае неприемлема, поскольку наряду с этим портится полированная поверхность платы, загрязняется столик и приспособление.
Одновременно с этим при маленьких толщинах прошиваемых плат вполне небольших порций абразива, подаваемых в рабочую территорию кисточкой.
Перемещением головки станка инструмент опускают на поверхность платы , пока основание столика не переместилось на 5—10- мм. Затем головку станка фиксируют, а шкалу индикатора столика устанавливают в нулевое положение. После этого на ультразвуковой генератор подают напряжение.
Генератор выводят на оптимальную частоту и создают прошивку отверстий.
Глубина обработки обязана быть больше толщину платы на 0,2 — 0,3 мм, что контролируется по индикатору. Нужно при обработке каждой новой платы увеличивать глубину прошивания отверстий на 0,3—0,5 мм для того, чтобы по мере износа штырей обеспечить калибровку отверстий в плате неизношенной их частью. Это обеспечит более высокую точность прошивания отверстий (до +0,05 мм).
По окончании окончания обработки генератор выключают, основание столика опускают и снимают подкладку с платой, а в приспособление вставляют очередную плату. Время прошивания 81 отверстия в плате образовывает около 2 мин. Стойкость инструмента до переточки образовывает 8—10 изделий, а до полного износа —около 50 плат.
По окончании износа инструмента в концентратор впаивают новые штыри и его применяют для предстоящей обработки.
На данный момент создан технологический процесс ультразвукового прошивания в стекле глубоких отверстий малого диаметра с отношением длины к диаметру до 200 : 1.
Обработку отверстия создают в два-три этапа с последовательным введением все более долгих инструментов. Инструмент полый, покрытый небольшими кристаллами натуральных алмазов, обработанных и ориентированных так, дабы обеспечить оптимальное резание. Закрепление алмазов — гальваническое.
Станок имеет повышенную жесткость станины, увеличенную мощность звуковой приводных электродвигателей и головки, двухскоростную совокупность подачи. При прошивании отверстия диаметром 1,6 мм длиной 305 мм в стекле сначала создают прошивание отверстия длиной 13 мм, после этого вторым инструментом длиной 152 мм и, наконец, третьим инструментом до 305 мм.
Инструмент имеет частоту вращения 4500 об/мин при частоте ультразвуковых колебаний 20 кГц и амплитуде 0,03 мм. Охлаждение территории резания осуществляется равномерной струей воды, поступающей через центральную часть инструмента. Сочетание вращения инструмента и продольных его колебаний разрешает создавать обработку при малых осевых упрочнениях, что сокращает износ инструмента.
Подобным образом создают обработку отверстий менее 1 мм.
Для изготовления многоотверстных ферритовых пластин (МФП) запоминающих матриц на данный момент самый обширно используют два способа: а) литье под давлением с последующим отжигом; б) ультразвуковую обработку отожженных ферритовых заготовок посредством многоэлементных инструментов.
При изготовлении МФП способом литья приобретают отверстия не меньше 0,3—0,6 мм. Ультразвуковая же обработка дает возможность приобрести отверстия диаметром 0,17—0,18 мм при высокой точности шага.
Рис. 6. Ультразвуковая обработка многоотверстных ферритовых пластин
Крепление рабочих элементов к основанию инструмента создают припоем ПОС-61. Инструмент резьбовым хвостовиком крепят в концентраторе ультразвукового станка. Обработку ведут при следующих режимах:
Наряду с этим применяют абразив марки М10, М14 и карбид кремния. Одним инструментом последовательно прошивают пять заготовок. Глубина обработки отверстий первой заготовки образовывает 0,5 мм, а для второй и последующих заготовок (с учетом износа рабочих элементов) —Соответственно 0,55; 0,6; 0,65 и 0,7 мм. Форма отверстий, получающаяся в следствии ультразвуковой обработки, продемонстрирована на рис.
103, а. Коническая форма отверстий обусловливается износом рабочих элементов инструмента.
Разделение заготовки на пять готовых МФП размером 21 X 3 X 0,43 мм создают методом прорезки в ней плоским ультразвуковым инструментом узких пазов и последующего шлифования стороны, противоположной обработанной ультразвуком, до толщины 0,43 мм. Влияние износа глубины элемента обработки и рабочего инструмента на точность отверстия возможно установить при рассмотрении рис. 103, в. Для исключения влияния первого фактора на величину диаметра отверстия изношенная часть рабочего элемента инструмента обязана пребывать за пределами толщины готовой пластины.
применение глубины и Изменение обработки соответствующих абразивов (в частности, марки М7) разрешило уменьшить брак по отверстиям d1 примерно до 7%, а по отверстиям d2— до 6%. ужесточение допусков и Дальнейшее снижение брака на диаметр отверстия связано с проведением дополнительных технологических мероприятий (отделение больших фракций абразива для получения большей однородности его состава, использование абразива из синтетических алмазов, повышение стойкости рабочих элементов инструмента).
Примером действенной обработки громадного количества отверстий групповым инструментом есть получение 256 отверстий диаметром 0,25 мм, в ферритовой пластине. Ход отверстий 0,8 мм.
Обработка велась на ультразвуковом станке с применением группового инструмента, складывающегося из впаянных калиброванных штырей числом, равном числу отверстий. Время обработки составило 1 мин.
Обработку конструктивных элементов изделия создают на станке 4770 по накладному шаблону, благодаря которому ориентируют изделие относительно инструмента. Использование ультразвуковой обработки разрешило сократить процент брака и повысить точность изготовлений изделий.
вырезание и Раскрой изделий. Ультразвуковым методом создают вырезание миниатюрных изделий, раскрой материала, прорезание пазов и других конструктивных элементов малых размеров.
Рис. 7. Изделия, полученные ультразвуковой обработкой
Ультразвуковой раскрой материалов используют по большей части для вырезания заготовок из полупроводниковых материалов, технических камней, металло- и минералокерамики. Для получения одного реза используют одиночный инструмент ножевидной формы. Толщину б его рабочей части берут мельчайшей (0,1—0,8 мм) для того, чтобы свести к минимуму утраты материала.
Разрезаемую заготовку на столе ультразвукового станка ориентируют относительно инструмента так, дабы плоскость реза была параллельна ее базисной плоскости. Для выверки относительного размещения плоскости реза к базисной поверхности используют шаблоны либо плоскопараллельные плитки. Фиксацию заготовки на станке создают эластичными прижимами. Заготовки малых размеров приклеивают к стеклянным пластинам.
Для предотвращения сколов заготовку разрезают не на всю толщину, а оставляют перемычку. После этого заготовку переворачивают и приклеивают к пластине, а недорезанную перемычку сошлифо-вывают. Недочётом для того чтобы приема разрезания заготовок есть большой отход материала.
Для нарезания громадного количества пластин используются многолезвийный инструмент, складывающийся из рабочих инструментов — лезвий , засунутых в державку. Толщину лезвий берут минимальной. Требуемый ход t между лезвиями устанавливают посредством мерных прокладок. Для обеспечения равного вылета I для всех лезвий по окончании их пайки создают выравнивание методом приработки на электроэрозионном станке.
Использование для выравнивания шлифования для узких лезвий затруднительно ввиду возможности их деформаций и изгиба.
При резке многолезвийным инструментом заготовок из кварца, стекла, минералокерамики используют частоту 18—22 кГц и удельное давление инструмента 0,4—0,5 кГс. Резку кристалла кварца сечением 16 X 16 мм на пластины толщиной 0,4 мм инструментом, складывающимся из 20 лезвий, создают в течение 4 мин. Пластину толщиной 0,08 мм от кристалла германия отрезают однолезвий-ным инструментом в течение 5 мин.
Для изготовление абразивной суспензии при ультразвуковой резке заготовок из кварца, кремния, турмалина и других используют карбид бора с размером зерна 0,05—0,08 мм. При отрезке узких пластин из хрупких материалов однолезвийным инструментом имеют место случаи их разрушения, что разъясняется происхождением поперечной составляющей колебаний лезвия инструмента. Для устранения этого нужно рассчитывать колебательную совокупность так, дабы свести к минимуму величину данной составляющей.
Помимо этого, во многих случаях используют многолезвийный инструмент, при разрезании которым внутренние лезвия испытывают в меньшей степени влияние поперечной составляющей, чем крайние.
Для вырезания и раскроя миниатюрных заготовок и изделий используют специальный ультразвуковой вырезной полуавтомат 4770А. На станке вырезают диски диаметром от 1 мм и более, и создают раскрой на квадраты размером 1 X X 1 мм пластин кремния, германия и других жёстких материалов.
При раскрое и вырезании, как и при размерной обработке изделий из полупроводниковых и других хрупких материалов, принципиально важно верно выбрать величину упрочнения подачи инструмента, поскольку при чрезмерном давлении вероятно разрушение изделия либо большие сколы материала, причем на выходе инструмента упрочнение нужно снижать.
Величина упрочнения зависит от толщины обрабатываемой заготовки. Так, при толщине материала 0,1—0,15 мм все возможное упрочнение образовывает 0,4 кГ; при толщине 0,15—0,4 мм — 1,0 кГ и при 0,4—1,0 мм — 1,5 кГ.
раскрой и Разрезание узких заготовок из жёстких материалов, и получение узких пазов возможно создавать на особой установке — ультразвуковой ножовке. Принципиальная схема однолезвийной ультразвуковой ножовки приведена на рис. 105.
Она складывается из двух звуковых головок, к концентраторам которых припаяна металлическая лента (материал сталь У8А, 65Г, 60С). Ленту размещают над обрабатываемой заготовкой, которая приклеена к столу.
Установка смонтирована на ультразвуковом станке 4770 и снабжена двумя особыми приставками: а) складывающейся из двух звуковых головок, установленных на подвижной раме, которая может перемещаться в вертикальной плоскости по шариковым направляющим станка; на раме укреплены кроме этого приспособления для растяжения и зажима ленты; б) складывающейся из двигателя, подвижного рабочего стола с ванной и механизма горизонтального перемещения стола. Вертикальное перемещение режущей ленты и создание давления между заготовкой и лентой производится функциональными механизмами станка.
Рис. 8. Изделия, обрабатываемые ультразвуковым способом
Разработка резания следующая: между заготовкой и лентой создается давление; включается насос, подающий абразивную суспензию в зону реза; наряду с этим заготовке информируют возвратно-поступательное перемещение относительно ленты. После этого включают генератор ультразвуковых колебаний; под действием появившихся в ленте ультразвуковых колебаний частицы абразива ударяют по заготовке, в следствии чего происходит ее разрезание. Толщина ленты 0,15—0,35 мм.
Кроме раскроя и разрезания заготовок ультразвуковым способом создают обработку миниатюрных изделий по контуру. В случае если изделие довольно несложной формы, то обработку создают за одну операцию. Для получения изделий сложных форм используют многооперационную обработку.
За одну операцию создают вырезание пьезоэлементов из турмалина. Размеры их составляют 0,5 X 0,5 X 1 мм. Для вырезания микропьезоэлементов используют многолезвийный инструмент с толщиной лезвий 0,08 мм. В качестве абразива используют микропорошок карбида бора М28.
Время вырезания 25 заготовок на ультразвуковом станке УЗСН-З мощностью 0,4 кВт, составило 12 мин.
Изделия, имеющие разные конструктивные элементы малых размеров (фасонные полости, пазы, прорези), приобретают за пара операций методом последовательной обработки по элементам контура. Такая технологическая последовательность удлиняет цикл изготовления изделия, но упрощает конструкцию, форму инструмента и пара повышает его стойкость. Точность при многооперационной обработке за счет большего количества установов меньше, чем при однопозиционной обработке.
Обработка пазов и щелей в изделиях из труднообрабатываемых материалов.
Рис. 9. Схема однолезвий-ной ультразвуковой ножовки
Он имеет два конструктивных элемента размерами 0,3+0’04 и R 0,4 мм. Обработку этих элементов создают по окончании обработки изолятора по наружному контуру и центрального отверстия. Предварительно изделия приклеивают на стеклянную пластину. Инструментом для обработки паза 0,3+0’04 мм есть железная вставка диаметром 0,3 мм, закрепленная в концентраторе. Для верной установки изолятора относительно инструмента используют особую стойку с оправкой.
Штучное время на обработку одного паза на ультразвуковом станке УЗСН-З составило 30—40 с. Подобно создают обработку и внутреннего паза R 0,4 мм. При применении группового инструмента неспециализированное время обработки существенно уменьшается.
На поверхности пластины из кварцевого стекла нужно нанести паз глубиной и шириной 0,07 мм, выполненный по спирали Архимеда. Ход спирали А0А0 = 1 мм. Для обработки паза-спирали используют составной инструмент. В металлический концентратор, на торцовой поверхности которого выполнена спиральная канавка, засунута металлическая лента толщиной 0,07 мм, которой предварительно придана форма спирали.
Для верной установки стеклянной пластины-заготовки применен установочный шаблон, выверенный на соосность с концентратором-инструментом. Обработку создают на ультразвуковом станке ЛЭ-400.
Вопросы точности ультразвуковой обработки. При ультразвуковой обработке направляться учитывать вопросы точности, поскольку разрушающему действию абразивных зерен подвергается не только изделие, но и инструмент. Приобретаемое в изделии отверстие конической формы имеет размеры, пара громадные если сравнивать с размерами инструмента.
Боковой зазор между стенкой и инструментом взятого отверстия приблизительно равен диаметру зерна абразива, используемого при ультразвуковой обработке. Это появляется благодаря шпинделя и биения инструмента звуковой головки при вращении. Конусность отверстия растет с повышением диаметра инструмента в пределах 1,8—3,5° за счет возрастания времени действия зерен абразива на инструмент. Овальность отверстий находится в пределах ±0,01 мм.
Исходя из этого чтобы получить отверстия требуемых размеров во многих случаях прибегают к уменьшению размеров инструмента на величину разбивки. Величина уменьшения размеров инструмента может колебаться в пределах 0,07—0,1 мм в зависимости от размеров отверстия, зернистости абразива, формы инструмента и др.
Благодаря износа и разрушения инструмента под действием абразива, нарушающие точность воспроизводимого изображения, скругляются острые углы. Для частичного предотвращения этих нежелательных явлений прибегают к применению нескольких инструментов — для чернового прохода, а после этого для чистого, т. е. окончательного формирования отверстия. Наряду с этим практикой установлено, что любой новый инструмент должен быть на 0,02—0,03 мм больше прошлого для того, чтобы исключить появление ступеней в взятом изображении.
Шероховатость поверхности, приобретаемая в следствии ультразвуковой обработки, обусловливается размером зерен абразива, видом материала изделия. В зависимости от конкретных условий шероховатость торцовой поверхности изображения колеблется в пределах Ra ^ 2,5—1,25 мкм для уменьшения качества конусности и улучшения поверхности отверстий направляться использовать более небольшие абразивы, учитывая, но, что скорость обработки при применении мелкозернистого абразива заметно падает.
Учитывая, что к. п. д. ультразвукового генератора не превышает 0,4—0,6, а к. п. д. магнитострикционных преобразователей кроме этого низок, цена обработки ультразвуковым способом очень велика. Исходя из этого рассмотренный способ используют в тех случаях, в то время, когда изделие нереально как следует обработать вторыми способами.
Ультразвуковой способ действен при обработке изделий из стекла, керамики, фарфора, жёстких сплавов, полудрагоценных и драгоценных технических камней, ферритов, полупроводников для прошивания круглых и профильных отверстий диаметром не меньше 0,3—0,5 мм. При обработке меньших отверстий эффективность его существенно понижается благодаря необходимости нередкой заточки и правки инструмента.