Электрохимическое полирование
Электрохимическое полирование представляет собой процесс, обратный гальваническому осаждению металлов: обрабатываемую деталь помещают в качестве анода в ванну с электролитом и при заданном режиме (плотности тока, температуре и времени погружения) осуществляют съем металла. Процесс анодного растворения используют в операциях очистки поверхности металла, удаления заусенцев и грата, заострения, полирования.
Наибольший интерес представляет электрохимическое полирование. Такое полирование наиболее широко распространено в промышленности, но оно весьма трудоемко, плохо поддается механизации и автоматизации. Этим процессом определяются такие важнейшие критерии качества поверхностного слоя, как макро- и микрогеометрия, наклеп, микроструктура, остаточные напряжения.
В прямой зависимости от этих критериев находятся эксплуатационные свойства деталей машин и механизмов — усталостная прочность, отражательная, теплоизлучающая и теплопоглощающая способность, обтекаемость жидкостями и газами, коррозийная стойкость.
Полирование определяет также эстетику изделия.
Сущность процесса
Электрохимическое полирование основано на анодном растворении обрабатываемой поверхности при режимах, которые обеспечивают интенсивное растворение микровыступов шероховатой поверхности и замедленное растворение во впадинах. В результате неравномерной скорости растворения шероховатая поверхность сглаживается, и появляется заметный блеск.
Только в случае преимущественного растворения микровыступов на поверхности металла происходит полирование (сглаживание).
Преимущественное растворение микровыступов может происходить тогда, когда у поверхности металла в результате электролиза образуется пленка низкой электропроводности, состоящая из продуктов анодного растворения.
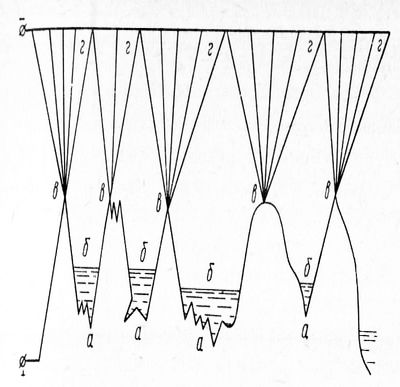
Рис. 1. Схема образования вязкой пленки:
а — впадины; б — вязкая пленка; в — выступы; г — силовые линии тока.
В этом случае толщина пленки, а следовательно, и электрическое сопротивление ее в микровпадинах будут больше, чем на выступах, что и приведет к более интенсивному растворению выступов.
Растворимость анодных продуктов в электролите, скорость диффузии их в электролит, состав и физико-химические свойства анодной пленки имеют существенное значение для процесса полирования. Поэтому этот процесс у различных материалов происходит неодинаково. У многих металлов и сплавов (медь, никель, алюминий, нержавеющие хромистые и хромоникелевые стали) сглаживание сопровождается появлением блеска на обработанной поверхности.
У некоторых сплавов (стали карбидного класса, бронзы, латуни) наблюдается блеск без заметного сглаживания шероховатостей. Ряд металлов и сплавов (олово, свинец, серый чугун, высококремнистые стали) вовсе не полируется. Вместо сглаживания образуется’ сильно травленая поверхность с толстыми темными пленками.
Существует несколько гипотез, по-разному объясняющих процесс электрохимического полирования, причем следует отметить, что ни одна из них не объясняет полностью все данные опыта. Наиболее вероятной и логически объясняющей сущность процесса является гипотеза вязкой пленки. Согласно этой гипотезе, электрохимическое полирование может происходить лишь при образовании на поверхности анода в процессе анодного растворения вязкой пленки.
Вязкая пленка состоит из продуктов анодного растворения, обладающих высоким электрическим сопротивлением. Покрывая тонким слоем шероховатую поверхность полируемого металла, эта пленка приобретает неодинаковую толщину на различных участках поверхности. На выступах толщина пленки и соответственно ей критическое сопротивление меньше, чем во впадинах.
Вследствие различного сопротивления пленки и способности электрического тока концентрироваться на остриях плотность тока на выступах будет больше, чем во впадинах. Поэтому скорость растворения вершин выступов будет больше скорости растворения дна впадин. В результате неравномерного распределения плотности тока и вследствие этого различной скорости растворения возникает сглаживание шероховатой поверхности.
Достоинства и недостатки электрохимического полирования
Электрохимическое полирование металлов имеет свои достоинства и недостатки. Главное достоинство метода — высокая производительность. Время полирования практически составляет не более 10 мин., причем габариты детали и форма ее не влияют на производительность. Возможна одновременная обработка такого количества деталей, какое помещается в ванне. Производительность процесса не зависит от твердости и вязкости обрабатываемого материала.
Электрохимическое полирование позволяет обрабатывать детали не только простых очертаний, но и сложного профиля, а также внутренние полости, трудно доступные или вовсе не доступные при механическом полировании.
Основное отличие электрохимически полированной поверхности от механически полированной — отсутствие на ней каких-либо следов деформации и структурных изменений. Это — естественное следствие сущности электрохимического процесса, который осуществляется не только без приложения каких бы то ни было механических усилий к обрабатываемой поверхности, но и вовсе без физического прикосновения к ней.
Больше того, электрохимическое полирование удаляет механически деформированный поверхностный слой металла и восстанавливает его истинное строение. В результате анодного растворения поверхность оказывается свободной от механических и термических изменений. Улучшается микрогеометрия; блеск поверхности оказывается больший, чем у механически полированной.
Электрохимическое полирование выявляет дефекты в металле (неметаллические включения, трещины, волосовины, неоднородность структуры).
Поверхности, электрохимически полированные, пассивируются и благодаря этому в 4—6 раз лучше сопротивляются коррозии; они обладают повышенными оптическими свойствами.
Процесс не требует применения полировальных станков, фетровых кругов, абразивных порошков, паст. Возможны автоматизация обработки и одновременное обслуживание нескольких ванн. Значительно облегчаются и оздоровляются условия труда.
Перечисленные достоинства характеризуют несомненное превосходство электрохимического метода над механическим. Однако на нынешней ступени развития этому методу присущи и серьезные недостатки, которые ограничивают применение электрохимического полирования.
Один из основных недостатков — незначительная эффективность сглаживания. Электрохимическим полированием можно улучшить чистоту поверхности на 1—2 класса, причем оно эффективно, если исходная шероховатость не грубее 4—5-го классов. Поэтому при необходимости достигнуть 12—13-го классов приходится механически подготовлять поверхности до 10—11-го классов.
Грубо обработанная поверхность (после точения, фрезерования, шлифования), подвергнутая электрохимическому полированию, почти сохраняет макрорельеф поверхности. Сглаживаются полностью лишь отдельные микровыступы и наблюдается закругление гребешков.
Попытки многих исследователей повысить эффективность сглаживания и, по существу, решить задачу электрохимического шлифования практически не привели к положительным результатам. Повышение эффективности сглаживания требует прежде всего применения высоких плотностей тока (более 100 а/см2), что, в свою очередь, приводит к растворению больших толщин металла (0,5—1 мм).
Необходимое время полирования обычно определяется опытным путем и находится, как правило, в пределах 8—10 мин. при полировании сталей. Увеличение производительности полирования сверх 10 мин. не только не ведет к улучшению качества поверхности, но часто, наоборот, ухудшает ее.
Сглаживание следов механической обработки происходит постепенно: после первых 3—4 мин. электрохимического полирования наблюдается уничтожение мелких рисок и появление гладких полированных площадок; после 10 мин. на поверхности остается рельеф грубых рисок, которые в дальнейшем полностью не исчезают, а лишь закругляются, образуя волнистую поверхность. Мы проводили исследования сглаживания при изменении времени полирования от 2 до 20 мин.
Увеличение времени полирования приводит к еще большему растворению металла. Кроме того, оно может вызвать в сплавах вытравливание отдельных структурных составляющих.
Данные этой таблицы показывают, что при возрастании времени полирования шероховатость поверхности улучшается. Однако, начиная с 10 мин. выдержки, улучшение это незначительно, и через 15 и 20 мин. сглаживание наших образцов (сталь У10 закаленная) происходило примерно с одинаковой эффективностью. К этому следует добавить, что значительная эффективность сглаживания сопровождается большим съемом металла.
В процессе полирования за 10 мин. растворяется слой металла толщиной 60—100 мк.
Это резко искажает форму и размеры деталей, подвергаемых полированию, и превосходит припуски, оставляемые обычно на полирование.
Кроме того, интенсивное растворение металла приводит к накоплению в электролите большого количества железа (Ре20з). При накоплении Fe203 в количестве 6% к весу электролита полирование становится невозможным.
Так, например, ванна емкостью 10 л при полировании деталей с поверхностью 0,5 дм2 способна практически работать 4—6 суток. Затем железо должно быть удалено из раствора или электролит следует заменить вновь приготовленным.
Однако еще задолго до полного насыщения электролита железом состав электролита в процессе эксплуатации изменяется. Контроль его производят ежедневно, определяя удельный вес, и соответственно корректируют. Убыль воды в результате испарения восполняют довольно частым добавлением горячей воды.
Помимо контроля удельного веса электролита необходимо периодически осуществлять анализ на содержание Сг03, Cr203, H2S04, Н3РО4 и Fe203 и корректировать состав электролита.
При накоплении в электролите 1,5% Сг20з производят под действием тока окисление трехвалентного хрома в шестивалентный, а после окисления электролит прогревают в течение часа при 90—110 °С.
Анализ и корректировка кислот и удаление железа из электролита являются еще более затруднительными операциями. Таким образом, сложность корректировки состава электролита и, в конечном счете, короткий срок службы электролита являются еще одним весьма существенным недостатком электрохимического полирования. Расчеты показывают, что в результате непродолжительного действия электролита и, следовательно, большого удельного расхода кислот электрохимическое полирование в ряде случаев оказывается экономически нерентабельным.
Рис. 2. Зависимость съема металла от времени полирования (углеродистые стали).
Оборудование для электрохимического полирования
Оборудование, предназначенное для осуществления процесса электрохимического полирования, весьма сходно по конструкции с оборудованием, имеющимся в цехах металлопокрытий для операции хромирования.
Основным оборудованием являются ванны, источники постоянного тока низкого напряжения и приборы для измерения и регулирования электрического режима.
Ванны.
Ванны должны быть снабжены электронагревателями, помещенными в защитных, химически стойких, оболочках внутри самой ванны, и водяной рубашкой. Применение двойного нагрева необходимо потому, что при приготовлении и проработке электролита приходится нагревать его до 110—120°С, а в процессе полирования необходимо поддерживать температуру 70—80 °С. Применение водяной рубашки исключает возможность перегрева электролита.
Кроме того, она используется для охлаждения проточной водой электролита, который часто перегревается в процессе полирования.
Внутренняя поверхность ванны должна быть облицована химически и температуростойким материалом. В качестве таких материалов для наиболее агрессивного сернофосфорнохромового электролита следует применять свинец, фторопласт-4 либо покрытия из суспензии фторопласта ЗМ или химически стойкой силикатной эмали марки ЛК-1.
В лабораторных условиях могут быть использованы жаростойкое стекло, фарфор, керамика.
Источником питания ванн обычно служат выпрямители селеновые марки ВСГ-ЗМ, купрокеный ВКГ-100 либо германиевый ВАГЗ-9/12-600. При необходимости возможна совместная работа нескольких выпрямителей.
Регулирование тока осуществляется по-разному, в зависимости от режима работы ванны и источника питания. В последнее время в промышленности применяется плавное бесступенчатое регулирование тока изменением напряжения в первичной обмотке трансформатора. Трансформатор смонтирован совместно с селеновым или германиевым выпрямителем.
Подробное описание оборудования и схем для регулирования электрического режима можно найти в специальной литературе.
Составы электролитов, их приготовление и корректирование
Для электрохимического полирования предложены сотни различных по составу электролитов.
Это свидетельствует прежде всего о том, что до сих пор не найден состав электролита, который бы удовлетворял следующим основным требованиям:
1) высокой сглаживающей способностью;
2) длительной работоспособностью;
3) способностью полирования многих металлов и сплавов;
4) безопасностью в эксплуатации.
В результате испытаний разных электролитов установлено, что наиболее универсальным в современной технике является электролит, основой которого служит фосфорная кислота с добавлением серной кислоты и хромового ангидрида (фосфорносернохромовый электролит). Всестороннее изучение указанного электролита показало, что в нем практически возможно полировать большое количество марок сталей — от углеродистых до высоколегированных, включая нержавеющие и инструментальные стали. В этом электролите также возможно полировать медь, алюминий и некоторые марки сплавов на их основе.
Рис. 3. Ванна для электрохимического полирования:
1 — корпус наружной ванны; 2 — корпус внутренней ванны; 3 — нагреватель.
Приготовление и корректирование электролита
Порядок приготовления электролита следующий: смешивают фосфорную кислоту уд. веса 1,54 и серную кислоту уд. веса 1,82.
В отдельном сосуде растворяют в воде хромовый ангидрид. После отстаивания сливают его в ванну полирования. Затем вливают в ванну расчетное количество ортофосфорной кислоты уд. веса 1,54, а затем серной уд. веса 1,82.
Полученную смесь прогревают при 140° С в течение примерно 1,5—2 час. до достижения уд. веса 1,73—1,74 (для полирования углеродистых сталей) и при 110—120 °С — до удельного веса 1,64 (для полирования нержавеющих сталей).
Опыт эксплуатации фосфорносернохромового электролита показывает, что работоспособность его во многом зависит от того, насколько поддерживается в процессе полирования соотношение соединений шестивалентного и трехвалентного хрома.
Если прикатодное пространство не изолировано от общего объема ванны, то в процессе полирования на катоде происходит восстановление хромовой кислоты, причем продукты восстановления повышают вязкость электролита, доводя его до непригодного состояния. Поэтому рекомендуется прикатодную зону изолировать пористой диафрагмой.
Диафрагма представляет собой узкий керамический пористый сосуд (прямоугольный или цилиндрический), в который помещается катод. Материалом для изготовления диафрагм служит смесь красной и шамотной глины (30% шамотной глины) и песка. В зависимости от габаритов катодов и ванны диафрагма формуется с возможно более тонкими стенками и обжигается при 1000— 1100 °С.
При пользовании диафрагмой срок службы электролита возрастает в 5—6 раз. Анодное окисление трехвалентного хрома при накоплении его свыше 2% ведут при анодной плотности тока 10—15 а/дм2, напряжении 10—12 в и температуре электролита 60 °С. Соотношение анода к катоду 1 : 10.
Материалом анодов и катодов служит свинец. После окисления электролит рекомендуют прогреть в течение часа при 90—110 °С.
Особенности электрохимического полирования
Исследование работы фосфорносернохромового электролита показывает, что все три кислоты оказывают взаимно благоприятное влияние. Увеличение содержания фосфорной кислоты позволяет понизить плотность тока и напряжение, тогда как увеличение содержания серной кислоты повышает пределы плотности тока. Изменяя концентрацию и соотношение кислот, возможно установить области полирования для заданной марки материала.
Рис. 4. Схема изоляции прикатодной зоны:
1 — электролит в ванне; 2 — диафрагма; 3 — электролит прикатодной зоны; 4 — катод; 5 — анод.
Рис. 5. Полирующая способность фосфорносернохромовых электролитов при полировании:
а — углеродистых и низколегированных сталей; б — нержавеющих хромистых сталей.
Полирование сталей. Фосфорносернохромо-вые электролиты обладают полирующей способностью в широких пределах концентраций: от 60 до 85% фосфорной кислоты и от 15 до 40% —серной кислоты. На рис.
26 приведены диаграммы, иллюстрирующие области полирующей способности электролита углеродистых и нержавеющих групп сталей. Электрохимическое полирование каждой группы сталей имеет свою особенность. При полировании углеродистых сталей, если необходимо максимально сгладить шероховатости и не требуется блеск, следует увеличить содержание воды в электролите до 30—35%, а хромовой кислоты — до 12—15%.
В этом случае при плотности тока 15—25 а/дм2 и температуре электролита 70 °С обрабатываемая поверхность приобретает серебристый цвет. Если необходимо сгладить шероховатость с получением блеска, то целесообразнее осуществить процесс в двух растворах: сгладить в электролите с большим содержанием воды и придать блеск в другом электролите с меньшим содержанием воды.
Рис. 6. Профилограммы шероховатости механически обработанных и электрохимически полированных поверхностей нержавеющей стали:
а — фрезерованная и электрохимически полированная после фрезерования; о — шлифованная и электрохимически полированная после шлифования.
Качество поверхности зависит от содержания углерода в стали и ее структуры. Наиболее легко полируются стали со структурой равномерно распределенного феррита и перлита. С увеличением содержания углерода в стали изменяется величина предельного тока, при котором наступает анодная пассивность.
Наименьший ток соответствует низкоуглеродистой стали (0,1%) с почти ферритной структурой; наибольший — среднеуглеродистой стали (0,45%) при соотношении феррита и перлита 1:1. При дальнейшем увеличении содержания углерода, когда структура становится более однородной и преобладает перлитная составляющая, предельный ток вновь снижается.
При полировании хромистых нержавеющих сталей в электролите при плотности тока 20—30 а/дм2 поверхность получается травленой и сглаживания не наблюдается. При плотности тока 40 а/дм2 наблюдается блеск без сглаживания. Наиболее эффективное сглаживание, сопровождаемое блеском, происходит при плотности тока в пределах 50—70 а/дм2.
Этой плотности соответствуют профилограммы шероховатости поверхностей различно обработанной нержавеющей стали марки 2X13.
Из профилограмм следует, что поверхность, шлифованную абразивным кругом зернистостью 12 до 7-го класса, возможно отполировать до 9-го класса. Фрезерованную поверхность с шероховатостью 6-го класса возможно отполировать до 9-го класса.
Следует заметить, что в ряде случаев волнистость поверхности не мешает улучшению ее эксплуатационных свойств. Так, например, исходная фрезерованная поверхность после электрохимического полирования, будучи волнистой, обладает повышенной усталостной прочностью, лучшим сопротивлением коррозии и полным отсутствием деформированного слоя.
Температура электролита
Значительное влияние на качество поверхности оказывает температура. При низких температурах (30— 40 °С) полирования не происходит, и поверхность оказывается травленой, матовой. С повышением температуры поверхность становится более блестящей, но травление сохраняется.
При температурном интервале 70—80°С получены лучшие результаты.
Для каждого электролита, режима полирования и полируемого сплава существуют пределы температур электролита, отвечающие лучшему качеству поверхности. При чрезмерном снижении температуры электролита против оптимальной повышается вязкость электролита и соответственно вязкость пленки на аноде, а также затрудняется диффузия продуктов анодного растворения. В результате замедляется процесс анодного растворения, полирующее действие электролита ослабляется или полностью прекращается и наблюдается травленая поверхность.
Чрезмерное повышение температуры ускоряет процесс анодного растворения, снижает вязкость электролита и пленки на аноде, облегчает диффузию и уменьшает омическое сопротивление электролита. С повышением температуры усиливается газообразование, на обрабатываемой поверхности появляются полосы и наблюдаются травленые участки.
Несоблюдение главным образом электрического и температурного режимов приводит к появлению различных дефектов при электрохимическом полировании.
Расстояние между электродами и их перемешивание
Расстояние между электродами оказывает заметное влияние на равномерность удаляемого слоя. Так, при расстоянии 20—40 мм происходит значительное растворение (от 0,2 до 0,6 мм). Увеличение расстояния до 150 мм не приводит к существенному улучшению равномерности съема.
Увеличение расстояния не позволяет использовать необходимый ток вследствие высокого удельного сопротивления электролита.
Перемешивание электролита ухудшает качество поверхности, покрывая ее темным налетом, причем эффективность сглаживания не возрастает.
Особенности полирования меди
Возможно полирование меди и некоторых ее сплавов (латуней) и в одной ортофосфорной кислоте уд. веса 1,5 (716 г/л Н3Р04). Однако добавление к ортофосфорной кислоте хромового ангидрида позволяет осуществлять процесс полирования в широких пределах плотности тока (20—70 а/дм2) и сократить время полирования до 1—3 мин. Катодами служат свинцовые пластины. Соотношение поверхностей анода и катода 1 : 3.
В процессе полирования меди, как и при полировании сталей, уменьшается содержание воды, кислоты и происходит восстановление Сг03 до Сг20з. Корректирование электролита осуществляется так же, как и при полировании сталей. Вода добавляется до необходимого удельного веса, а кислота — по данным химического анализа.
Сгг03 окисляется на аноде в Сг03.
Эффективность сглаживания электролита невелика. Поэтому подготовка механическим шлифованием должна заканчиваться на зернистости 5. Хорошо полируется без всякой предварительной подготовки листовой холоднокатаный материал. В этом случае должна быть проявлена забота о тщательном сохранении поверхности листа от царапин, забоин и других повреждений.
Следует иметь в виду, что раковины, поры и включения хорошо выявляются электрохимическим полированием. Скорость растворения меди при плотности тока 50 а/дм2 составляет 1 мк/мин, причем снижение удельного веса электролита с 1,5 до 1,3 ускоряет процесс растворения.
Особенности полирования алюминия
Характерная особенность полирования алюминия — интенсивное пассивирование полируемой поверхности и вследствие этого снижение плотности тока до очень малых плотностей (1—2 а/дм2) и повышение напряжения до 15—25 в. Эта особенность не должна смущать, хотя она наступает через 2—4 мин. после завешивания детали и несколько ухудшает блеск.
Если полирование осуществляется с целью получения высокой отражательной способности, рекомендуется в этом случае разрушать образующуюся окисную пленку кратковременным переключением тока с анода на катод (реверсированием) либо выключением тока на несколько секунд.
Резкое ухудшение качества полированной поверхности алюминия наступает в результате анодного растворения алюминия. При накоплении в электролите 30 г/л алюминия, по существу, прекращается работа ванны. Контроль и корректирование раствора осуществляют так же, как и в процессе полирования сталей.
Применение электрохимического полирования
Несмотря на существенные недостатки электрохимического полирования и все продолжающиеся исследования в данной области, этот процесс уже сейчас находит эффективное применение в некоторых производствах.
В то же время из-за отсутствия объективных данных и незнания особенностей электрохимического полирования часто возникают значительные затруднения или принимаются ошибочные решения в выборе этого метода.
Применение электрохимического полирования на нынешней стадии развития целесообразно прежде всего там, где затруднено или невозможно механическое полирование (недостаточные для механического полирования поверхности, недопустим нагрев или силовое воздействие, дефекты материала или механической обработки). Так, например, электрохимическому полированию подвергают различные детали арматуры.
Электрохимически полируют детали карбюратора (в частности, клапан подачи горючего из нержавеющей стали или фольги), тончайшую ленту, проволоку и трубы. Особый интерес представляет полирование труб длиной 6—8 м из нержавеющей стали Х18Н9Т. Механическая очистка внутренней поверхности длинных труб вызывает значительные трудности. Химическая очистка труб не решает задачи—она растравливает поверхность и не полностью очищает от окалины.
Электрохимическим полированием внутренняя поверхность становится более гладкой, блестящей, повышается коррозийная стойкость, уменьшается трение жидкости и газов о стенки, обеспечивается высокая производительность процесса.
При полировании длинных труб крупного диаметра (больше 100 мм) и других крупных полых деталей внутренняя полость используется в качестве ванны-электро-лизера. Катод в этом случае монтируется в центре трубы. Полирование ведется с протоком электролита через трубу.
Трудности полирования больших поверхностей труб заключаются в необходимости применения тока порядка 10 000 а. Столь большой ток вызывает чрезмерный разогрев электролита и выделение большого количества газов. К тому же трудно выполнима подводка большого тока, поэтому трубы крупных диаметров полируют на небольших участках, непрерывно подвигая катод вдоль трубы. Длина катода зависит от диаметра трубы. Например, для трубы диаметром 200 мм длина катода должна быть 170 мм.
Электролит циркулирует под давлением до 4 атм, скорость перемещения катода — до 8 м/мин.
В настоящее время разработано несколько конструкций установок для полирования внутренней и наружной поверхностей труб различных диаметров.
Электрохимическое полирование находит применение и в производстве режущего инструмента. Образующийся при шлифовании инструмента дефектный слой легко снимается электрохимическим полированием. В результате повышаются стойкость инструмента и защита от коррозии.
Например, электрохимическое полирование канавок сверл обеспечивает более легкий сход стружки при сверлении и меньший разогрев сверла.
Полирование сверл осуществляется партиями, а не по одному сверлу, как при механическом полировании. Объем ванны емкостью 150 л позволяет загружать одновременно до 30 сверл диаметром 10— 15 мм. Для быстрой загрузки сверл сконструированы приспособления — рамки.
Рис. 7. Полирование сверл:
а — механическое; б — электрохимическое.
Для полирования 1000 сверл диаметром 10 мм в среднем расход электролита составляет 8,7 кг. Соответственно расходуется ортофосфорной кислоты 5,4 кг, серной кислоты — 2,5 кг и хромового ангидрида — 0,8 кг.
Уже указывалось, что электрохимическое полирование удаляет поверхностный слой металла, а многие дефекты материала выступают наружу. Когда преследуют цель декоративной отделки деталей, это свойство является недостатком метода. В случаях необходимости контроля качества поверхности это — несомненное достоинство.
Высокая чувствительность электрохимического полирования к неоднородности состава все больше используется в практике металловедческих лабораторий для контроля качества сталей: выявления микро- и макроструктуры, трещин, флокенов, волосовин, неметаллических включений и других нарушений сплошности металла; определения карбидной неоднородности, склонности сплавов к интеркристаллитной коррозии; обнаружения деформированных участков, явлений термического отпуска тонкого поверхностного слоя. При подготовке шлифов для микроскопического исследования достоинства электрохимического полирования особенно заметны.
Поверхность шлифа, полированная электрохимически, освобождается от всех термических и механических изменений (наклепа), неизбежных при механических способах обработки. Она свободна также от каких-либо загрязнений полирующими веществами и пленок, в том числе и окисных, образовавшихся ранее. И хотя полированная поверхность анодно пассивированная, она остается чистой и активной.
Отсутствие на поверхности следов термических воздействий и деформаций и повышенная чистота полированной поверхности позволяют наблюдать истинную, неискаженную структуру исследуемого материала. Электрохимически полированная поверхность особенно удобна для рассмотрения при больших увеличениях. Здесь отчетливо выявляются тончайшие детали структуры, обычно искаженные при механической подготовке (первичное зерно, микроликвация).
Электрохимическое полирование в сочетании с химико-механическим методом ускоряет процесс приготовления шлифов.