Электрошлаковая сварка
Долгие изучения в Университете электросварки им. Е. О. Патона по вертикальной сварке под флюсом с принудительным формированием стали причиной созданию принципиально нового метода электросварки, взявшего наименование электрошлаковой сварки. Данный вид сварки плавлением тесно связан с дуговой сваркой под флюсом: процесс начинается, как дуговая сварка, и неспешно переходит в электрошлаковую, которая при нарушениях опять легко переходит в дуговую сварку.
И в том и другом случае сходны неспециализированная технологическая схема, флюсы, однообразны электроды, источники питания током. Но имеется и очень значительное, различие: при электрошлаковой сварке отсутствует дуговой разряд, что дает основание вычислять электрошлаковую сварку независимым методом электросварки.
Источником нагрева при электрошлаковой сварке есть тепло, выделяющееся при прохождении электрического тока через расплавленный шлак.
Схема электрошлаковой сварки, продемонстрированная на рис. 134, во многом сходится со схемой вертикальной дуговой сварки под флюсом с принудительным формированием. Главное отличие содержится в том, что при электрошлаковой сварке подбирают режим, скоро подавляющий дуговой разряд и переводящий процесс сварки в электрошлаковый.
В установившемся состоянии в пространстве между кромками свариваемых подробностей и шлако-удерживающими приспособлениями расположена ванна расплавленного шлака, в которую загружён плавящийся железный электрод. Ток, проходящий между основным металлом и электродом через расплавленный шлак, подогревает его и поддерживает в нем электропроводность и высокую температуру.
Температура шлаковой ванны обязана быть больше температуру плавления металла. Расплавленные главный и электродный металлы образуют ванну жидкого металла 5 под шлаковой ванной;
затвердевающий расплавленный металл образует сварной шов, соединяющий свариваемые кромки.
Электродная проволока непрерывно подается в ванну по мере плавления, а шлакоудерживающие приспособления, в большинстве случаев бронзовые ботинки, охлаждаемые водой, перемещаются вверх соответственно увеличению уровня железной ванны. Подвижные ботинки именуются ползунами. Не всегда нужны два ползуна, часто бывает достаточно одного, а при маленьких швах шлакоудерживающие приспособления смогут быть неподвижными и образующими кокиль для наплавленного металла.
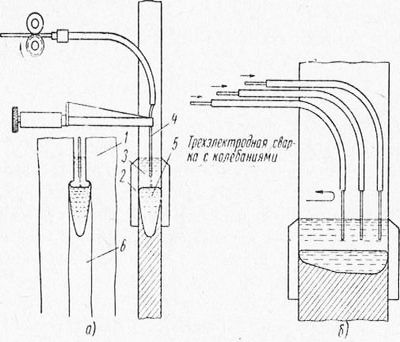
Рис. 1. Схема электрошлаковой сварки: а — одноэлектродной; б — трехэлектродной
Шлак, приобретаемый расплавлением флюса, иногда подаваемого в ванну, представляет собой расплавленный электролит, проводимость которого скоро растет с увеличением температуры. Охладившийся и затвердевший шлак фактически не проводит тока и есть изолятором.
Флюсы для электрошлаковой сварки должны отвечать дополнительным требованиям: иметь большую температуру кипения, различаться минимальным газообразованием при больших температурах, иметь низкие стабилизирующие особенности, не хорошо поддерживать горение дуги а также подавлять его, содействуя переходу дугового процесса в электрошлаковый.
Затрудняют горение дуги и содействуют установлению электрошлакового процесса повышение глубины шлаковой ванны, использование переменного тока. Уменьшение глубины шлаковой ванны повышает устойчивость дуги и переводит электрошлаковый процесс в дуговой. Исходя из этого электрошлаковая сварка начинается с дугового разряда, пока не образуется шлаковая ванна достаточной глубины.
Тепловыделение в шлаковой ванне происходит неравномерно: самый интенсивно на финише электрода и в маленьком прилегающем к нему количестве шлака. В данной самая активной территории отмечается большое падение напряжения; отделяются капли нагретого электродного металла, несущие большое количество тепла. Температуры в сварочной ванне скоро выравниваются интенсивными конвекционными потоками.
Установившийся электрошлаковый процесс в большинстве случаев идет нормально, с малым выделением газов и малым разбрызгиванием.
Расход флюса на образование узкой шлаковой корки под ползунами мал и образовывает не более 5% наплавленного металла, в 15—30 раз меньше, чем при простой сварке под флюсом. Понижается и расход электричества на 1 кг наплавленного металла, поскольку значительно уменьшается расход энергии на плавление флюса.
Вероятна сварка за один проход металла громадных толщин: одним неподвижным проволочным электродом возможно сваривать металл толщиной до 60 мм. При возвратно-поступательном перемещении электрода возможно сваривать металлы толщиной до 150 — 200 мм, а одновременная работа нескольких электродов разрешает сваривать фактически металлы сколь угодно громадных толщин за один проход; имеется опыт сварки металлов толщиной до 2000 мм.
Ввиду малого количества шлака и относительно не сильный его сотрудничества с металлом наплавленный металл легируют только электродной проволокой. Большие глубина железной ванны и длительность нахождения металла в жидком состоянии содействуют удалению неметаллических включений и пузырьков газа из металла. Конфигурация ванны сокращает возможность транскристаллизации и образования тёплых трещин.
Замедленные охлаждение и нагрев территории термического влияния ликвидируют явления закалки; охлаждения и скорость нагрева в различных точках территории влияния в 10—100 раз меньше, чем при дуговой сварке; многократно больше длительность нахождения металла при больших температурах — более 1000 °С, вызывающих рост зерна; ширина территории влияния больше многократно.
Наплавленный металл при электрошлаковой сварке, в противоположность простой сварке под флюсом, образуется в основном за счет расплавленного электродного металла; Часть главного металла легко может уменьниться до 10—20%.
Для электрошлаковой сварки требуются относительно маленькие удельные мощности. Электродная проволока в большинстве случаев используется диаметром 3 мм, сварочный ток на один электрод 00-900 а, рабочее напряжение 30—50 в, вылет электрода 100—500 мм. Громадный вылет электрода, нагреваемый сварочным током, и расплавленный шлак ускоряют плавление электрода практически в 2 раза если сравнивать с дуговой сваркой.
В следствии замедленного охлаждения и нагрева довольно часто отмечается крупнозернистая структура наплавленного зоны и металла термического влияния; для улучшения структуры по окончании сварки требуется нормализация изделия. Замедленное охлаждение в большинстве случаев дает пара пониженные значения прочности сварного соединения если сравнивать с дуговой сваркой.
Электрошлаковая сварка, в большинстве случаев, выполняется в вертикальном положении; сварка в наклонном положении, а тем более в нижнем еще не вышла из стадии лабораторных изучений.
Формы соединений, делаемых электрошлаковой сваркой, достаточно разнообразны; значительно чаще используется стыковое соединение, вероятны кроме этого тавровое и угловое соединения.
Сварка изделий какое количество-нибудь сложной формы затруднительна, освоены до тех пор пока швы постоянного сечения на всем протяжении, прямолинейные и кольцевые, лежащие в вертикальной плоскости. В прямолинейных швах нужны вспомогательные начальные, либо входные и выводные, либо конечные планки.
В начале сварки проходит некое время, пока устанавливается устойчивый электрошлаковый процесс. До этого момента участок шва получается неудовлетворительным, со большими непроварами. Данный участок нужно разместить на начальных планках. В конце шва скопляются неметаллические включения и образуется большая конечная усадочная раковина. Неудовлетворительный конечный участок шва нужно разместить на выводных планках.
По окончании планки удаляют кислородной резкой.
—
Электрошлаковая сварка — сварка плавлением, при которой для нагрева металла употребляется тепло, выделяющееся при прохождении электрического тока через расплавленный электропроводный шлак.
По ГОСТ 19521—74 электрошлаковая сварка классифицируется:– по виду электрода — проволочным электродом, пластинчатым электродом, плавящимся мундштуком; – количеству электродов с неспециализированным подводом сварочного тока — одно-, двух- и многоэлектродная; – наличию колебаний электрода — не раздумывая и с колебаниями.
основной металл и Электрод связаны электрически через расплавленный шлак. За счет тепла, выделяемого в шлаковой ванне при прохождении электрического тока, кромки и металл электрода главного металла оплавляются и стекают на дно расплава, образуя железную ванну. В начале процесса сварки возбуждается электрическая дуга, по окончании расплавления образования и флюса шлаковой ванны жидкий флюс заливает и гасит дуговой процесс и дугу переходит в электрошлаковый.
Свариваемые подробности собирают вертикально без скоса кромок, с зазором 20—40 мм. Для создания шва и удержания шлака и жидкого металла от вытекания используют особые формующие устройства — подвижные либо неподвижные бронзовые ползуны, охлаждаемые водой, либо остающиеся пластины. Кристаллизующийся в нижней части железной ванны расплавленный металл образует шов.
К главным параметрам электрошлаковой сварки относятся: скорость сварки, сварочный ток, скорость подачи электродов, напряжение сварки, толщина металла, приходящегося на один электрод, расстояние между электродами. Вспомогательные составляющие режима: зазор между кромками, глубина шлаковой ванны, состав флюса, скорость поперечных колебаний электрода, вылет электрода, сечение проволоки и др. При применении электродных проволок глубина шлаковой ванны в большинстве случаев 25—70 мм, скорость подачи проволоки 100—500 м/ч.
Рис. 2. Схема процесса электрошлаковой сварки
Сварку пластинчатым электродом используют для относительно маленьких швов высотой до 1,5 м. Вместо пластин возможно использовать расходуемые электроды, т. е. стержни круглого, квадратного и
вторых сечений. В этом случае существенно упрощается аппаратура для сварки.
Сварка плавящимся мундштуком как бы объединяет методы сварки проволочными и пластинчатыми электродами. В пластинчатом электроде делают пазы либо к нему приваривают трубки для подачи электродных проволок. При сварке пластина остается неподвижной и есть плавящимся мундштуком, по которому подается проволока.
Этим методом возможно сваривать швы сложного криволинейного профиля.
Электрошлаковую сварку осуществляет особыми электрошлаковыми аппаратами, каковые снабжают подачу в зону сварки электрода, поддержание устойчивого электрошлакового процесса и перемещение на протяжении шва по мере его образования.
Электрошлаковая сварка имеет преимущества и следующие особенности: – металл фактически любой толщины возможно сваривать за один проход, исходя из этого производительность сварки в 5—15 раз выше, чем при многослойной автоматической сварке под флюсом, наряду с этим (в большинстве случаев) не нужно разделки кромок; – вертикальное положение железной ванны, повышенная температура ее верхней части и большое время нахождения металла в расплавленном состоянии содействуют удалению газов и неметаллических включений из металла шва; – небольшой расход флюса, в большинстве случаев не более 5% от массы наплавленного металла.
Недочётом электрошлаковой сварки есть большой перегрев металла околошовной территории, что ведет к понижению пластических особенностей, исходя из этого требуется (в большинстве случаев) последующая высокотемпературная обработка для получения требуемых механических особенностей сварного соединения.
Электрошлаковую сварку используют для сварки сталей, алюминиевых и титановых сплавов толщиной более 25 мм. Главные виды сварных соединений, делаемых электрошлаковой сваркой, продемонстрированы на рис. 3.
Рис. 3. Главные виды сварных соединений, делаемых электрошлаковой сваркой: а, б — стыковые, в, д — тавровые, г — угловые, е — переменного сечения