Неметаллические покрытия
Неметаллические покрытия — это покрытия лаками, эмалями и красками.
В художественной индустрии, а также в архитектуре лакокрасочные покрытия используются частенько — они составляют приблизительно 50%- Так же как и другие виды покрытий, они защищают изделия от коррозии, изолируют железные изделия от окружающей среды и одновременно с этим являются декоративно-отделочными.
Преимуществом этого вида покрытий являются: простота исполнения, экономичность и достаточная стойкость.
Недочёты его — недолговечность и низкая художественная сокровище.
Лакокрасочные покрытия разделяются на две группы:
1) лаки — покрытия бесцветные либо слабо подсвеченные, прозрачные либо глухие;
2) краски — покрытия, отличающиеся от лаков присутствием красителей.
Лак является растворителем , в котором растворена смола.
В качестве растворителей раньше чаще всего использовались разные высыхающие масла растительного происхождения. Нанесенные на металл, они образуют узкий слой, что полимеризу-ется, т. е. загустевает и после этого затвердевает в виде узкой блестящей влагонепроницаемой пленки. Скорость подсыхания масел возрастает с увеличением температуры, действия света, и добавлением сиккативов (химическое соединение свинца, кальция, марганца, кобальта).
В качестве растворителей на данный момент используют бензин, бензол, спирты, эфиры, скипидар, ацетон. Многие из них ядовиты, к примеру серный эфир и метиловый спирт; другие огнеопасны, исходя из этого использовать их направляться ограниченно.
В качестве наполнителей в лаках используют разные смолы — вещества органического происхождения, имеющие некристаллическое строение. Они весьма разнообразны по свойствам и происхождению; при нагреве они размягчаются и расплавляются; прекрасно растворяются в растворителях и нерастворимы в воде.
Краски. В качестве растворителей для красок, предназначенных для окраски металлов, в большинстве случаев используют разные масла (масляные краски) либо нитросоединения типа ацетона, нитролака и др. Такие краски именуются эмалевыми.
Они скоро сохнут и образуют ровную сливающуюся поверхность.
На рис. 1 продемонстрирован рельеф из алюминия с применением холодной змали.
В качестве наполнителей в красках помогают красочные пигменты, каковые являются либо тонко растертые окислы и цветные соли разных металлов (окись хрома, кобальта и т. п.), либо натуральные пигменты.
Окраска может производиться кистями либо из особых приспособлений типа аэрографов — способом распыления. Наряду с этим для меньшей утраты краски работа в большинстве случаев производится в электростатическом поле, благодаря которому небольшие капельки краски притягиваются окрашиваемой поверхностью. Клеевые краски, разводимые на воде, для окраски металлов негодны.
Для качественной отделки художественных изделий, покрываемых разными покрытиями, нужно, дабы:
– лакокрасочные покрытия не содержали кислот, щелочей, каковые, растворяясь в воде, делаются электролитом и содействуют происхождению электрохимической коррозии;
– покрытия скоро высыхали и образовывали прочную непроницаемую для воды пленку;
– покрытия владели укрывистостью, т. е. легко наносились и разравнивались по поверхности изделия;
– изделие, а в качестве катодов помогают изделия, каковые покрывают этим металлом.
Исключение составляют хромирование, где аноды употребляют свинцовые, а время от времени и золочение, в то время, когда из экономических мыслей пользуются нерастворимыми (угольными, платиновыми либо металлическими) анодами. Аноды изготовляются из металлов высших марок, в которых количество посторонних примесей минимально.
Подготовка поверхности изделий под покрытия. Поверхность изделия перед покрытием должна быть совсем чистой — это снабжает обычное сцепление главного металла с осажденным, и хорошее уровень качества самого осаждаемого металла.
Для очищения поверхности используют три вида обработки, каковые дополняют друг друга: механическую, химическую и электрохимическую.
Механическая обработка. Эта обработка включает полирование и шлифование, в случае если нужно иметь ровную поверхность; помимо этого, используют пескоструйную обработку и крацевание для более либо менее матовой поверхности.
Но по окончании полирования и шлифования на изделии остаются другие загрязнители и жировые плёнки, а также остатки стеариновых и олеиновых окиси и кислот хрома, каковые наносятся на изделие в виде пасты на протяжении полирования.
Химическая обработка. Цель данной обработки — удаленнее поверхности изделия оксидных пленок методом травления, остатков флюса (буры) — методом отбеливания, загрязнений и жировых плёнок — методом обезжиривания.
При травлении используются сильные кислоты — серная, азотная, соляная либо их смеси. Их составы бывают разны. Самый распространены для медных сплавов и меди «отравы» следующего состава: 5 л азотной, 1 л серной кислоты и 50 г поваренной соли; смесь азотной и серной кислот в равных количествах с добавкой 5—10% поваренной соли; время от времени к ней додают еще сажу (она восстанавливает окислы азота).
Приготовление «отравы». В азотную кислоту додают маленькими порциями серную; данный раствор перемешивают и охлаждают, после этого в совсем остывший раствор вводят соль и сажу.
При отбеливании пользуются не сильный раствором серной кислоты— холодным либо горячим (для ускорения). При отбеливании удаляется в основном бура, если она осталась по окончании пайки, поскольку при травлении бура не удаляется.
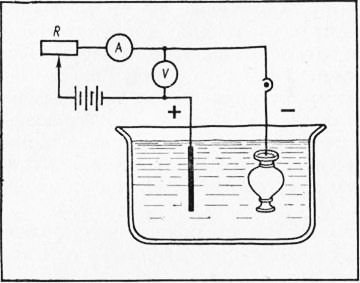
Рис. 1. Схема гальванической установки: R—реостат; А — амперметр; V вольтметр; + — анод; — — катод (изделие)
Приготовление отбела. Серную кислоту додают в необходимое количество воды, не нужно воду лить в серную кислоту, поскольку в другом случае кислота разбрызгивается и может обжечь трудящегося.
На 100 г воды додают 5—15 г серной кислоты.
Обезжиривание.
Данный процесс осуществляется последовательным применением следующих операций:
1) изделие промывают в бензине, ацетоне, дихлорэтане;
2) протирают при помощи щетки венской известью (тонко размолотый свежеобожженный известняк);
3) промывают в тёплых (95—100 °С) щелочах в течение 3— 10 мин (по окончании обезжиривания изделия шепетильно промывают в тёплой воде).
Раствор составляется так: 10—20 г едкого кали на литр тёплой воды.
Электрохимическая обработка. Электрохимическая обработка дает самая тщательную очистку самые загрязненных изделий. Она используется Для обезжиривания поверхностей.
Для этого изделия загружаются на катоде; анодом помогает лист нержавеющей стали; анод не растворяется.
При прохождении тока в растворе появляются ионы водорода. Они движутся по направлению к катоду и механически сбивают частицы жира с изделия. При прохождении водорода раствор перемешивается и тем ускоряется обезжиривание.
Помимо этого, под действием водорода жир частично омыляется в эмульсию (эмульгирование жиров).
Недочётами данной обработки есть то, что водород может поглощаться металлом и он получает хрупкость. Дабы предотвратить это явление, нужно на пара мин. переключать катод на анод, наряду с этим водород выходит из металла. Помимо этого, электролит имеет малую рассеивающую свойство, исходя из этого глубоко профилированные детали и изделия с отверстиями не смогут быть обезжирены этим методом.
Состав раствора для обезжиривания (на один литр воды): едкий натр—15—25 г, углекислый натрий — 15 г, тринатрийфосфат—15 г, жидкое стекло — 3 г (напряжение тока 6—9 В, плотность тока 3— Ю А/дм2). Процесс продолжается 3—5 мин (из них 2—4 мин на катоде и 0,5—1 мин на аноде). катода и Поверхности анода должны быть приблизительно равными по площади.
Для ее сплавов и обезжиривания меди используется холодная ванна, а для стали — нагретая до 90—95 °С.
Используются кроме этого и приемы гальванического травления. Они созданы в основном для тёмных металлов. При этих процессах исключается «водородная хрупкость», которой тяжело избежать при несложном (химическом) травлении.
В качестве электролита используются растворы серной кислоты, для анодов — свинец.
Помимо этого, для получения блестящих поверхностей используется электрополирование. На данный момент электрополирование находит широкое распространение и в некоторых областях оно вытесняет механическое полирование благодаря простоте работы и своей экономичности, к примеру в области ювелирного, галантерейного и посудного производства. Электрополирование придает изделию не только декоративный внешний вид, но и содействует устойчивости против коррозии.
Сущность этого процесса содержится в следующем. Изделие помещают в электролит в качестве анода. Поверхностные выступающие участки изделия растворяются, и неспециализированная поверхность сглаживается и получает глянец, поскольку в электролите поверхность изделия покрывается вязкой пленкой, владеющей низкой электропроводностью.
Эта пленка образуется из продуктов поверхностного растворения изделия и находится по поверхности неравномерно — в углублениях она более толстая, а на выступах уже. Это приводит к концентрации силовых линий на выступающих частях и их стремительное растворение.
В качестве электролитов используют смеси серной и ортофос-форной кислот в концентрациях и различных отношениях с маленькими добавками — от 3 до 20% хромового ангидрида. Процесс протекает при повышенных температурах (до 70—90°С) для полирования металлических изделий и при простой комнатной температуре (без подогрева) для изделий из ее сплавов и меди. Длительность процесса 2—15 мин.
Источники тока. Для гальваностегии пригоден лишь постоянный ток, т. е. ток, идущий в одном направлении. Источниками тока помогают генераторы постоянного тока, выпрямители (селеновые либо купроксные), аккумуляторная батареи, и элементы либо батареи.
Гальванические ванны для электролита. Для гальванических ванн употребляются сосуды из разных материалов в зависимости от состава растворов, для которых они предназначаются.
Размеры ванн зависят от размера покрываемых изделий.
Наряду с этим соблюдаются следующие условия:
1) расстояние между изделием и дном ванны не меньше 5— 10 см;
2) толщина слоя электролита над изделием не меньше 5 см;
3) расстояние от зеркала электролита до края ванны не меньше 10 см.
Обогрев ванн. Многие процессы гальваностегии, к примеру золочение, хромирование, требуют повышенной температуры. Существуют следующие методы подогрева электролита.
Электрические устройства с электроспиралями укрепляются на дно ванны либо опускаются конкретно в электролит. В этом случае спирали изолируются от электролита защитными кожухами. В зависимости от электролита кожухи изготовляются из стали для щелочных ванн либо из фарфора и фаянса для кислых ванн.
Парообогрев осуществляется при помощи трубопроводов и змеевиков, каковые укладываются на дно ванны, и по ним пропускают тёплый пар. Для щелочных ванн используют металлические трубы, для кислых — свинцовые.
Обогрев тёплой водой (ванны с водяной рубахой). Для этого ванны делаются с двойными стенками и между ними циркулирует тёплая вода. Данный метод весьма эргономичен, не требует нередкой очистки, легко регулируется.
Недочётом этого метода есть то, что он не разрешает поднять температуру в ванне выше 80 °С.
Перемешивание электролита. Для обычной работы ванны нужно, дабы концентрация электролита была везде однообразной. Но так как в ходе осаждения металла электролит около изделия получает меньшую концентрацию, его нужно перемешивать.
Существует пара способов перемешивания электролита.
Работа с анодом в руке. Это несложный прием, при-годый для серебрения и золочения. Передвигая анод в электролите, последний перемешивают, и осаждение металла происходит из разных участков ванны.
Поступательно-возвратное перемещение катода. Изделия подвешиваются к штангам, каковые соединены с эксцентриком, вращающимся от мотора. Наряду с этим изделие двигается на протяжении ванны вперед и назад, перемешивая электролит.
Перемешивание механическими мешалками, приводимыми в перемещение от мотора.
Продувание воздухом. По дну ванны прокладываются трубы с отверстиями; в трубы подается под давлением воздушное пространство. Проходя через электролит, воздушное пространство перемешивает его.
Перемешивание полуавтоматами и автоматами— особыми приспособлениями, каковые движут катод (изделие) на протяжении ванны. Перемешивание является следствием трения катода (изделия) об электролит. При перемешивании изделие проходит мимо многих анодов, повертываясь к ним разными сторонами.
Этим достигается громадная равномерность покрытия, чем в простых ваннах. Приспособления являются транспортёром , что передвигает катоды на протяжении долгой ванны либо нескольких ванн из одной в другую. Особый непроизвольный регулятор снабжает прерывистый движение транспортера при переходе из одной ванны в другую, его скорость — 0,2—2,5 м в 60 секунд.
Электролитические покрытия
В зависимости от условий, в которых будет пребывать изделие, подлежащее гальваническому покрытию, толщина наращенного слоя металла не редкость разна.
Имеются три группы условий работы:
а) твёрдые — это наружная воздух, загрязненная промышленными газами, испарением морской воды либо действием грязи, пыли;
б) средние — закрытые помещения, шнобель повышенной влажностью, неотапливаемые помещения либо воздух сельской местности, где отсутствуют вредные газы;
в) легкие — в сухих отапливаемых помещениях.
Меднение. Бронзовые покрытия для антикоррозионных и декоративных целей используют редко, поскольку на воздухе медь легко окисляется и теряет блеск и цвет. При действии сернистых соединений бронзовые покрытия скоро темнеют и чернеют; при действии углекислых и хлористых соединений они зеленеют.
Для защиты стали от коррозии в твёрдых условиях медь совсем не годится, поскольку при повреждении бронзового слоя омедненное железо ржавеет стремительнее, чем не омедненное.
Бронзовые покрытия в большинстве случаев используют при многослойных покрытиях декоративного характера — никелирование, хромирование, серебрение, золочение — как подслой. Использование бронзового подслоя разрешает приобретать лучшее сцепление между изделием и покрытием.
Меднение создают в цианистых либо кислых электролитах.
Меднение в цианистых электролитах имеет следующие преимущества:
1) медь осаждается конкретно на сталь, а в кислых ваннах на изделие осаждается так называемая контактная медь, имеющая весьма непрочное сцепление со сталью;
2) бронзово-цианистые ванны владеют хорошей рассеивающей свойством, а осадки из кислых ванн не хорошо покрывают углубления;
3) дают небольшой кристаллический плотный осадок меди.
Недочёты цианистых бронзовых ванн:
1) электролиты очень сильно ядовиты;
2) небольшой выход металла по току;
3) не допускают применения высоких плотностей тока;
4) малоустойчивы в работе.
Состав ванны (на 1 л воды) и режим работы:
цианистая медь — 106 г;
цианистый калий — 90 г;
углекислый натрий — 50—80 г.
Напряжение 3—6 В. Температура раствора 25—30 °С. Плотность тока для меднения цинка 0,7—0,8 А/дм2, меднения стали — 1 А/дм2 до 1,5 А/дм2.
Процесс меднения в цианистых ваннах протекает медлительно, исходя из этого целесообразно в этих ваннах приобретать узкие слои 5— 10 мкм, а окончательное наращение создавать в кислых ваннах.
Аноды используют из чистой меди, поскольку присутствие посторонних металлов — цинка, свинца и др. — портит ванну.
Толщина анодов от 3 до 10 мм; перед потреблением их отжигают и травят в азотной кислоте. Аноды оставляют в ванне неизменно. Расстояние между катодом изделием и (анодом) не меньше 100 мм.
Процесс идет прекрасно, в случае если поверхность анодов больше поверхности катода либо по крайней мере не меньше. В случае если ванна в порядке, то предмет начинает покрываться медью спустя 0,5—1 мин по окончании погружения и через 15—30 мин процесс возможно закончить.
В большинстве случаев через 10 мин предмет вынимают, крацуют и, промыв, после этого снова опускают в ванну. Перед опусканием в ванну первый раз предмет направляться обезжиривать, не смотря на то, что процесс идет и без обезжиривания, поскольку цианистый калий «съедает» жир, но ванна скоро портится от загрязнения. При обычной работе получаются ровные, плотные розовые осадки меди, а на катоде происходит спокойное, еле заметное газовыделение.
Неполадки в работе бронзово-цианистых ванн и их устранение.
1. Осадки получаются пористые, наряду с этим осаждение идет весьма медлительно. Это происходит, в случае если плотность тока через чур высокая либо содержание металла в ванне незначительно. направляться понизить плотность тока либо добавить в ванну цианистую медь.
2. Темно-красные пятнистые осадки на изделии и серые и зеленоватые налеты на анодах говорят о недостатке цианистого калия либо малую поверхность анодов; электролит около анодов наряду с этим делается голубым. направляться добавить цианистый калий, а аноды протравить в пятипроцентном растворе азотной кислоты и расширить их число.
3. На анодах появляется белый осадок — не достаточно цианистого калия и истощился электролит около анодов; требуется перемешать электролит и, в случае если белый осадок не провалится сквозь землю, добавить цианистый калий.
4. В случае если осаждение идет весьма медлительно, а аноды все время сохраняют цвет чистой меди (все время травятся), то направляться добавить цианистую медь (предварительно растворив ее в малом количестве электролита).
5. Осадок делается чёрным, зернистым либо вовсе ничего не осаждается — ванна содержит через чур много цианистого калия; направляться добавить цианистой меди маленькими порциями, предварительно растворив в маленьком количестве электролита (сухая не-намоченная соль не растворяется в электролите).
По окончании меднения предмет весьма шепетильно промывают в воде, поскольку любая капля электролита, оставшаяся в порах изделия, приводит к появлению пятна, которое весьма тяжело удаляется.
Сернокислые электролиты имеют следующие преимущества:
1) не ядовиты;
2) весьма несложны по составу;
3) дают большой выход по току;
4) устойчивы в работе;
5) разрешают трудиться на высоких плотностях тока. Недочёты:
Состав сернокислого электролита (на 1 л воды) и режим работы:
бронзовый купорос — 200—250 г; серная кислота 50—70 г.
Температура раствора без перемешивания — комнатная, с перемешиванием 30—40ЭС.
Плотность тока без перемешивания 1 — 2 А/дм2. Плотность тока с перемешиванием 3—5 А/дм2. Неполадки и их устранение.
1. Осадки неотёсанные, шероховатые, неравномерные — ванна загрязнена небольшими посторонними частицами (пылью). Нужно электролит профильтровать.
2. Чёрные рыхлые осадки, в особенности в углубленных местах, — недочёт серной кислоты. направляться добавить серной кислоты.
3. Бурное газовыделение, осадки рыхлые губчатые, пятнистые— недочёт бронзового купороса (либо избыток кислоты). Нужно добавить бронзового купороса, предварительно растворив его в маленьком количестве подогретого электролита.
Латунирование. Данный процесс используется как подслой (вместо меди) и как независимое покрытие.
Состав ванны (на 1 л воды) и режим работы: цианистая медь — 27 г; цианистый цинк — 9 г; цианистый натрий — 54 г.
Температура 20—40 °С, плотность тока 0,1—0,3 А/дм2, выход по току 60—80%. Аноды из бронзы.
Неполадки и их устранение.
1. Бледные осадки — излишки цинка либо громадна плотность тока. направляться добавить цианистой меди либо уменьшить силу тока.
2. Красные осадки — избыток меди. Нужно добавить в ванну цианистого цинка.
3. бурное газовыделение и Бледные осадки — избыток циана. направляться маленькими порциями додавать в ванну обе соли, предварительно растворив их в воде.
Никелирование. Никелевые защитно-декоративные покрытия используют весьма обширно как в технике, так и в художественных изделиях из металла благодаря следующим преимуществам: красивый вид; легко принимают полировку.
Толщина покрытия в зависимости от условий работы для изделия установлена следующая: а) при легких условиях (закрытое сухое, отапливаемое помещение) бронзовый подслой — 10 мкм, слой никеля 5 мкм; б) при средних условиях (на открытом воздухе) подслой меди 20 мкм, слой никеля — 10 мкм*. Самый прочно никелевое покрытие на меди либо латуни; на стали осажденный никель держится непрочно, исходя из этого используют многослойные покрытия, т. е. поверхность металлического изделия сперва омедняется, а после этого полируется и никелируется.
Состав электролита (на 1 л воды) и режим работы:
сернокислый никель—140 г;
сернокислый магний — 30 г;
сернокислый натрий — 50 г;
борная кислота — 20 г;
хлористый натрий — 5 г.
Температура электролита 20—30 °С; плотность тока 1 А/дм2. Скорость осаждения: слой толщиной в 1 мкм осаждается за 5 мин.
Главный химикат — это сернокислый никель, но из одной данной соли нельзя сделать ванну, поскольку такая ванна весьма не хорошо проводит ток. Для лучшей проводимости тока используют сернокислый магний и сернокислый натрий.
Для регулирования постоянной кислотности (ванна имеет тенденцию делаться щелочной) применяют борную кислоту.
Для защиты растворения и облегчения анодов их от пассивирования помогает хлористый натрий.
Неполадки в работе и их обстоятельства:
1. Предметы не никелируются: а) не сильный ток, б) ванна холодна (ниже 15°С); нужно усилить ток либо подогреть ванну.
2. Слой никеля чёрный с пятнами: а) ванна не хватает кислая — добавить борной кислоты (осадок отсвечивает желтым цветом); б) ванна через чур концентрированна — разбавить водой (на анодах зеленые кристаллы); в) ванна не хватает электропроводка — добавить сернокислого магния либо сернокислого натрия; г) ванна бедна металлом — добавить сернокислого никеля; д) обезжиривание и плохая подготовка — протереть изделие венской известью.
3. Отслаивание, хрупкость и растрескивание осадка: а) нехорошая подготовка; б) низкая температура ванны; в) ток через чур велик (подгар на углах и выступающих частях — серый цвет); г) громадна кислотность — нейтрализуется аммиаком.
Никелевые покрытия используют в основном для отделки изделий интерьерного характера; они заменяют серебрение. Никелевые покрытия весьма декоративны, они имеют серебряный цвет с теплым желтоватым оттенком (в отличие от хрома — холодный голубовато-сероватый оттенок). Их с успехом используют для ее сплавов и меди, стали и сейчас для алюминия.
Хромирование. Покрытие хромом занимает особенное место среди гальванических процессов. Нет ни одной отрасли техники, где бы не использовалось хромирование. Это обусловлено следующим:
1) высокой твердостью хромовых покрытий, превосходящей твердость закаленной стали;
2) прочностью и жаростойкостью против химической коррозии;
3) в художественных изделиях хромирование, не считая указанных обстоятельств, обусловливается и холодным и красивым блеском серо-голубым цветом хромового покрытия.
Практика покрытия хромом — самая сложная из всех гальванопокрытий, поскольку она имеет следующие изюминки:
1) весьма нехорошая рассеивающая свойство электролита, т. е. не хорошо покрывает углубление;
2) требуется высокая плотность тока — от 35 до 60 А/дм2 (в большинстве случаев для других покрытий плотность тока не превышает 4— 5 А/дм2);
3) вместо простых растворимых анодов используют нерастворимые свинцовые либо свинцово-сурьмяные, каковые при электролизе оказывают помощь проводить ток, а хром осаждается всецело из раствора.
Для декоративных покрытий используют в большинстве случаев хромирование (не толще 1 мкм) по бронзово-никелевому подслою: слой меди цианистой толщиной 3 мкм, слой меди кислой — 12 мкм, слой никеля — 10 мкм, всего 25 мкм.
Перед хромированием бронзово-никелевый подслой шепетильно полируют.
Состав ванны (на 1 л воды) и режим работы:
хромовый ангидрид 300—350 г;
серная кислота 3—3,5 г.
Температура хромирования 40 °С, плотность тока 15—20 А/дм2. Суммарная поверхность анодов должна быть меньше катодной вдвое.
Неполадки и их устранение.
1. Хром не осаждается в углубленных местах:
а) недостаточна плотность тока;
б) избыток серной кислоты.
Дабы расширить плотность тока в углубленных местах, дают толчок тока на одну 60 секунд, т. е. увеличивают плотность тока в несколько раз больше обычной, а после этого снижают ее до обычного размера.
2. Матовый либо пригорелый осадок, в особенности на выпуклых мес-стах:
а) громадна плотность тока;
б) запассивировались аноды;
в) изделия завешены под током без предварительного подогрева их в электролите.
Устранение недочётов:
а) расширить расстояние между катодом и анодом либо применить защитные катоды;
б) запассивиро-ванные аноды протравить в соляной кислоте и зачистить металлической щеткой;
в) перед включением тока подробности прогреть в электролите.
3. точки и Тёмные полосы на осадке либо чёрный осадок сплошь — недочёт серной кислоты.
4. Зернистые, вздутые, отслаивающиеся осадки — нехорошая подготовка изделий либо загрязненный электролит.
Серебрение. Серебрение используют в ювелирном деле, в производстве столовых устройств и т. п. Толщину серебряного покрытия берут разной — в зависимости от назначения: для столовых устройств 15—30 мкм; для галантереи и ювелирных изделий — 60— I00 мкм. Металлические изделия перед серебрением омедняют на толщину 30—50 мкм. Серебрение производится в бесцианистых ваннах следующего состава (на 1 л воды): серебро хлористое 6—8 г; желтая кровяная соль — 18 г; кальцинированная сода—18 г.
Плотность тока 0,1—0,3 А/дм2, температура 18—25 °С. Аноды используют либо из чистого серебра, либо угольные; наращение ведут два-три раза, в промежутках изделие обрабатывают мягкой латунной крацовочной щеткой со не сильный раствором поташа либо кваса (с необходимой тщательной промывкой по окончании крацо-вания в проточной воде).
Перед серебрением подробности полезно амальгамировать, т. е. покрывать ртутью (50 г азотнокислой ртути на 10 л воды).
Цвет осажденного серебра снежно-белый. Хранить и использовать электролит следует в темноте под крышкой либо при красном свете. В свежей только что составленной ванне осаждение идет без тока. Неполадки:
1. Отслаивание осадка — нехорошая подготовка.
2. Желтоватые либо розовые осадки — присутствие меди.
3. Чёрные, пятнистые осадки — загрязнение электролита, недочёт серебра.
Золочение. Золочение — это самый красивый и дорогой метод отделки художественных изделий из металла; используется по большей части в ювелирном деле. В прошлом золотили и большие изделия— посуду, бра, люстры, решетки и т. д.
Металлические изделия перед золочением покрывают медью толщиной 30—50 мкм. Толщина золотого слоя 2—5 мкм, редко 10— 20 мкм. Производится в бесцианистых ваннах.
Состав электролита (на 1 л воды) и режим работы:
хлорное золото—2—3 г; желтая кровяная соль—7,5 г; кальцинированная сода — 7,5 г.
Плотность тока 0,1—0,2 А/дм2; температура 60—80 °С. Аноды — чистое золото, платина, уголь (сталь). Для получения матовой либо полированной поверхности изделия его соответственно матуют либо полируют ручным полировником.
Интенсивность Цвета осадка зависит от плотности тока, которую комфортно регулировать громадным либо меньшим погружением анода в электролит.
Неполадки:
1. Бледные осадки:
а) недочёт в электролите золота;
б) низкая температура ванн;
в) малая плотность тока.
2. Красноватый цвет:
а) высокая концентрация золота в ванне;
б) высокая температура ванны;
в) наличие в ванне меди.
3. Зеленоватый оттенок: присутствие серебра в ванне.
Гальваническая отделка алюминия
По собственной химической природе его сплав и алюминий существенно отличаются от других металлов и сплавов, чаще всего используемых в индустрии (меди, латуни, латуни, стали, чугуна и др.). Благодаря этого гальванические приемы, пригодные для металлов и большинства сплавов, для алюминия не годятся.
На данный момент различают два типа гальванической художественной обработки алюминиевых изделий:
1) покрытие медью либо бронзой;
2) анодирование.
Гальваническое омеднение и латунирование алюминиевых художественных изделий.
Последовательность операций:
1. Изделие обезжиривают в растворителях — бензине, керосине, ацетоне.
2. Затем изделие травят в тёплом 8—10%-ном растворе едкого натра и промывают в тёплой, а после этого холодной проточной воде. При травлении на изделии появляется тёмный налет.
3. После этого изделие переносят в крепкую азотную кислоту.
4. По окончании обработки в кислоте изделие шепетильно промывают в холодной воде.
5. Подготовленное изделие переносят в кислую бронзовую ванну простого состава (на 1 л воды 250—300 г бронзового купороса и 20— 25 г серной кислоты) и, поместив на катод, дают напряжение 3—6 В. Процесс протекает при комнатной температуре.
Изделие в течение 2—3 мин покрывается ровным слоем меди. В данной ванне изделие находится до тех пор, пока не нарастет слой меди нужной толщины (в большинстве случаев около одних дней).
Покрытое медью изделие возможно оксидировать серной печенью в темно-коричневые и тёмные тона, напоминающие чугун, копченую медь и т. п.
Помимо этого, по бронзовому слою алюминиевые изделия возможно серебрить, никелировать, золотить и др.
Анодирование. Подготовка изделия для анодирования такая же, как и для омеднения.
Сущность процесса содержится в следующем. Изделие подвешивается в ванну на анод; катодами помогают свинцовые пластины. При прохождении тока поверхностная пленка изделия разрыхляется.
Состав ванны: 20%-ный раствор серной кислоты; температура 13—23°С; плотность тока 1 —1,5 А/дм2; напряжение 12—18 В.
По окончании промывки изделия в тёплой воде создают наполнение пленки либо окрашивание ее в растворах анилиновых красителей.
Рис. 2. Декоративные чашки из анодированного алюминия Живописец Л. X. Линакс
На данный момент анодирование используется весьма обширно; наряду с этим чем чище алюминий, тем прочнее пленка.
При анодировании операции выполняются в таковой последовательности: механическая обработка — шлифование, полирование; промывка в бензине; электрополирование; промывка в воде (два раза); разрыхление пленки на аноде в течение 30 мин; промывка в воде (два раза); наполнение пленки (окрашивание) в течение 2—5 мин; температура раствора 70°С; промывка в воде; уплотнение и закрепление пленки кипячением в дистиллированной воде 30 мин.
Приготовление красителя (анилинового): 1 г на 1 л воды. Раствор подготавливается следующим образом: в кипящую воду маленькими дозами додают раствор и краситель все время перемешивают; пену, появляющуюся на поверхности, снимают.