Изготовление профильных шаблонов
Профильные шаблоны изготовляют ручным либо механизированным методом. В первом случае практически все операции, начиная от заготовительных и заканчивая доводкой, делает высококвалифицированный слесарь-инструментальщик. Данный метод применяется при единичном изготовлении шаблонов.
Изготовление профильных шаблонов. Типовой технологический процесс исполнения профильных шаблонов ручным методом складывается из следующих операций: вырезки штучной заготовки; правки заготовок; шлифования боковых плоскостей; обработки двух базисных поверхностей шаблона под углом 90°; разметки, сборки заготовок в пачки; обработки профиля по разметке; опиливания по профилю с образованием пазов в местах сопряжения отдельных элементов профиля; термической обработки отдельных заготовок; окоича-тельного шлифования боковых поверхностей; сборки заготовок в пачке; шлифования всех элементов рабочего профиля; доводки всех элементов рабочего профиля; разборки пачки, притупления острых маркировки и кромок.
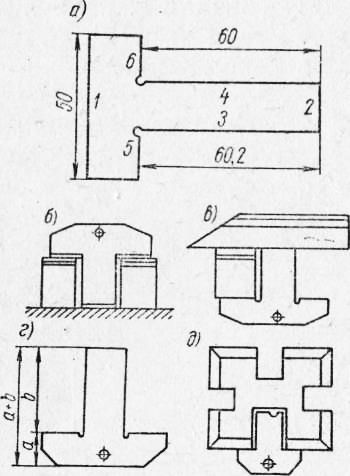
Рис. 1. Порядок доводки шаблона (а) и методы проверки шаблонов (б, в, г и д).
Как и при изготовлении скоб, одной из важных операций есть опиливание профиля шаблона. Особенно трудоемок процесс опиливания криволинейных поверхностей.
самый простым и рациональным методом опиливания криволинейных поверхностей есть обработка по копиру либо по готовой подробности. Но данный метод пригоден лишь при изготовлении громадного количества аналогичных шаблонов. Обширно распространено опиливание по разметке, но оно малопроизводительно и неточно.
Криволинейные выпуклые поверхности обрабатывают плоскими напильниками как на протяжении поверхности, так и поперек нее. При опиливании на протяжении поверхности напильником делают качательные перемещения в вертикальной плоскости, а при опиливании поперек поверхности напильник перемещают горизонтально и в один момент поворачивают около собственной оси. Выпуклую поверхность возможно взять методом запиливания последовательности площадок.
Неспешно увеличивая их число, приобретают криволинейную поверхность.
Вогнутые криволинейные поверхности обрабатывают круглыми и полукруглыми напильниками. Дабы на вогнутой поверхности не появилось огранки, напильнику кроме гбризонтального перемещения вперед придают еще и боковое перемещение. По мере обработки подробность перезажимают в тисках, дабы опиливаемый участок всегда был под напильником, а не сбоку.
При обработке криволинейных поверхностей наиболее сложным есть получение плавного перехода от кривой к прямой и от дуги к дуге. Разглядим процесс опиливания шаблона, в котором дуга окружности сопрягается с прямой (рис. 2).
Сначала обрабатывают криволинейную поверхность с наведением на ней продольных штрихов, а после этого — прямолинейную. Для этого шаблоны устанавливают в приспособлении так, дабы низшая точка криволинейной поверхности пребывала в одной плоскости с направляющей поверхностью. Установку осуществляют контроль лекальной линейкой (рис. 2,а).
Место, где должно случиться касание дуги прямой, необходимо отметить. Опиливая прямолинейный участок (поперечными перемещениями), нужно добиться для того чтобы положения, в то время, когда просвет между прямой и дугой совсем провалится сквозь землю (рис. 2,б и в). При верной обработке в месте их соприкосновения будет видна четкая граница между продольными штрихами на криволинейной поверхности и поперечными — на прямолинейной (рис.
2, е).
Чаще всего видящимися неточностями при опиливании являются: занижение прямой (рис. 2, д), врезание в дуговой участок (рис. 2,г), перекосы, в то время, когда штрихи сходятся наклонно (рис.
2,е).
Рис. 2. Приемы контроля и обработки шаблона.
Рис. 3. Приспособления для опиливания шаблонов.
Правильные криволинейные поверхности обрабатывают методом опиливания профиля по отдельным элементам. расположение и Геометрическую форму этих элементов осуществляют контроль универсальными инструментами.
Сложные и правильные профили шаблонов опиливают в приспособлениях, снабжающих правильную установку обрабатываемой подробности под разными углами к опиливаемой поверхности. Одно из таких приспособлений продемонстрировано на рис. 3.
В корпусе приспособления имеется вертикальный паз со сквозной прорезью, в котором перемещается планка, закрепляемая с задней стороны винтом. В верхней части планки имеется отверстие, куда вставляется цилиндрический калибр. К плоскости корпуса с громадным числом резьбовых отверстий крепится угольник с пазами, что разрешает регулировать его выверку и установку довольно верхней плоскости корпуса.
При опиливании шаблонов, имеющих участки в виде дуг полуокружностей, планку устанавливают по блоку мерительных плиток в положение, при котором центр ее отверстия будет пребывать от верхней плоскости корпуса приспособления на расстоянии, равном радиусу обрабатываемого участка. После этого шаблон технологическим отверстием надевают на калибр, засунутый в планку, и, поворачивая его около оси, обрабатывают дугу полуокружности его рабочей части.
Угольник помогает для припиливания прямолинейных и наклонных участков шаблонов и контршаблонов. Его устанавливают посредством концевых мер длины либо по угломеру под определенным углом к опиливаемой плоскости. Шаблон ставят на опорные поверхности угольника, прижимают к плоскости корпуса приспособления и в таком положении обрабатывают.
Для удобства опиливания вогнутых полуокружностей на верхней плоскости приспособления имеются два (либо более) призматических паза, расположенных строго перпендикулярно вертикальной опорной плоскости корпуса. Направленный по призматическому пазу круглый напильник в ходе опиливания удаляет с обрабатываемого участка шаблона часть металла, образуя в нем радиусное углубление, расположенное под углом 90° к его плоскости и торцам.
Не считая уголбника к корпусу приспособления возможно прикрепить синусную и опорную линейки и другие инструменты, содействующие более выверке и точной установке обрабатываемых подробностей.
При опиливании плоскостей, расположенных под прямым углом, громадную плоскость выбирают в качестве базисной, опиливают ее начисто, а уже после этого подгоняют к базисной вторую плоскость. Опиливание второй плоскости осуществляют контроль угольником, что прикладывают к базисной плоскости.
При обработке внутренних углов сперва опиливают наружные поверхности, каковые будут базами при разметке внутреннего угла и при контроле в ходе обработки.
При опиливании внутренних прямых углов шаблона используют угловые рамочные наметки, а при доводке и опиливании прямолинейных плоскостей — рамочные наметки с зажимными винтами. Плоскости Л и ? наметки должны быть шепетильно обработаны под прямым углом. Шаблон устанавливают в наметку и прижимают винтами к плоскости А так, дабы его разметочная риска строго совпадала с рабочей кромкой наметки.
После этого наметку закрепляют в тисках и опиливают шаблон.
Рис. 4. Наметки.
Важной операцией при изготовлении шаблонов есть припасовка — обоюдная пригонка друг к другу последовательности поверхностей, сопрягающихся без зазора при любых перекантовках (положениях). Припасовку обширно используют при обработке профильного шаблона, поскольку к нему постоянно делают контршаблон.
Шаблон есть проверочным инструментом, благодаря которому по способу световой щели осуществляют контроль профиль подробности, а контршаблон нужен для проверки шаблона, что в ходе контроля громадного количества подробностей изнашивается. Профили шаблона и контршаблона должны совершенно верно совпадать при любых положениях.
В зависимости от конфигурации профиля шаблона слесарь-инструментальщик сам решает, что изготовлять сначала — шаблон либо контршаблон. В тех случаях, в то время, когда профиль шаблона легко измерить универсальным инструментом, сначала делают шаблон, а по нему припасовывают контршаблон. При изготовлении радиусного шаблона легче сперва сделать контршаблон, а по нему припасовать шаблон.
Рис. 5. Шаблоны и контршаблоны.
При сложном профиле шаблон и контршаблон изготовляют посредством выработок, являющихся более несложными по форме шаблонами, каковые возможно измерить универсальным инструментом. В большинстве случаев сперва делают выработки, а позже профильные шаблоны, причем количество выработок зависит от сложности и точности профиля шаблона.
Изготовление резьбовых шаблонов. При установке и заточке резца на токарном станке и контроле резьбы активно применяются резьбовые шаблоны (рис. 6, а).
К ним предъявляются следующие требования: долгие боковые поверхности шаблона должны быть параллельны в пределах 0,01…0,02 мм; угол а должен быть расположен симметрично довольно боковых поверхностей; аз и углов осевые линии аг должны быть перпендикулярны, а осевая линия угла cti — параллельна боковым поверхностям.
Рис. 6. Резьбовой шаблон (а) и схема обработки шаблона по выработкам (б).
Как видим, изготовить резьбовой шаблон посредством универсальных измерительных инструментов нереально. К примеру, наружный угол шаблона а возможно было бы сделать по угломеру, но наряду с этим нет гарантии, что осевая линия угла будет параллельна боковым поверхностям шаблона. Следовательно, резьбовой шаблон нужно изготовлять по выработкам.
Предварительные операции выполняются по простой схеме технологического процесса, а окончательные (опиливание до термической обработки и доводка по окончании нее) — по выработкам.
Для изготовления резьбового шаблона требуются три выработки. Выработка предназначена для пригонки внутренних углов аг и аз так, дабы их осевые линии были перпендикулярны боковым поверхностям шаблона. По выработке сперва обрабатывают одну сторону угла, а после этого другую. Наружный угол а шаблона пригоняют от боковых поверхностей по выработке.
Для симметричного размещения угла а, довольно боковых поверхностей шаблона нужно пригнать его по выработке 3 сперва от одной поверхности, а после этого от второй. Такая обработка (пригонка) именуется контровкой угла довольно боковых поверхностей шаблона.
Так как выработки тяжело изготовить посредством универсального инструмента, их делают по контрвыработкам. Выработки и контрвыработки делают сырыми либо термически обработанными, в зависимости от количества шаблонов.
Посредством выработок шаблоны изготовляют как до термической обработки, так и по окончании нее. По окончании термической обработки шаблоны пригоняют по новым выработкам.
В тех случаях, в то время, когда шаблоны имеют сложный профиль низкой точности, их изготовляют по вычерченному профилю. На чистом странице цинка либо нержавеющей стали вычерчивают профиль шаблона в соответствии с чертежу. На заготовке шаблона профиль размечают и после этого фрезеруют, оставляя припуск на предстоящую слесарную обработку.
Сначала слесарь опиливает те участки шаблона, каковые возможно легко измерить универсальным инструментом, а после этого — остальные, пригоняя их по профилю к вычерченному на цинковом странице. Пригонку создают , пока профиль шаблона не сойдется с вычерченным.
Данный метод получения профильных шаблонов несложен и недорог, поскольку не нужно выработок, но точность обработки наряду с этим не выше ±0,07 мм.
Механизированные методы изготовления профильных шаблонов. Среди таких способов самым распространенным есть шлифование на прецизионных плоскошлифовальных станках с применением лекальных тисков, синусных линеек, других приспособлений и магнитных призм. Профильное шлифование снабжает высокую производительность труда и довольно высокую точность обработки.
К примеру, при чистовом шлифовании возможно взять линейные размеры с точностью до ±0,01 мм, а угловые — в пределах ±30”… ±2’ с высотой микронеровностей 0,000 5—0,001 мм.
При обработке шаблонов средней точности шлифование профиля окончательна операцией, а при изготовлении шаблонов более высокой точности шлифование предшествует доводке. Так как по окончании шлифования на доводку рабочих поверхностей остается равномерный припуск 0,01—0,02 мм, трудоемкость ее понижается.
Самый активно используются плоскошлифовальные станки с магнитной и горизонтальным шпинделем плитой, которая помогает для закрепления подробностей. Шлифование базисных поверхностей шаблонов, и прямолинейных участков профиля создают посредством лекальных тисков, наклонных участков профиля, расположенных под разными углами к базисным поверхностям, посредством магнитных призм, а угловых шаблонов — посредством синусного кубика.
Рис. 7. Приспособление для шлифования выпуклых цилиндрических поверхностей.
Обработка радиусных поверхностей шаблонов, и выпуклых и вогнутых Цилиндрических поверхностен осуществляется профилированным кругом.
Приспособление для шлифования выпуклых поверхностей громадного радиуса непрофилированным кругом продемонстрировано на рис. 7. На кубике расположен валик, что возможно прижат к кубику планкой. На левом финише валика находятся тиски, а на правом — рукоятка, благодаря которой возможно вращать валик, тиски и закрепленные в них шаблоны. Шлифование создают периферией круга.
Величина радиуса обрабатываемой поверхности зависит от величины подъема шлифовального круга над столом станка, и в большинстве случаев он равен 200 мм. Радиус контролируют индикатором либо линейкой, установленной на блоке концевых мер длины.
В рассмотренных случаях применения особых приспособлений для изготовления профильных шаблонов учитывается, что шлифовальный круг имеет цилиндрическую форму, а его образующая параллельна рабочей плоскости магнитной плиты. Следовательно, правка шлифовального круга не вызывает затруднений и производится посредством приспособления, установленного на магнитной плите станка.