Обработка металлов с применением электролитов и паст
Химически активные вещества, употребляемые при химико-механической обработке, на данный момент большей частью распространены в виде паст и растворов электролитов. При неотёсанных процессах (резании и шлифовании) используют электролиты, а при узких (полировании, притирке и доводке) — пасты.
Обработка посредством электролитов. Растворы электролитов являются очень активными химическими средами.
Обработка при помощи паст. Пасты, используемые в процессах доводки, полирования и притирки, отличаются рядом изюминок. Главная изюминка пребывает в том, что пасты химико-механического действия не режут металл, как это характерно абразивным пастам. Это свойство зависит от состава пасты п метода подготовки ее компонентов.
Главными компонентами, входящими в составах паст, являются окиси металлов (окись хрома, окись алюминия, железа и др.). Помимо этого, в пастах находятся стеарин, олеиновая кислота, керосин и силикагель. На данный момент наровне с доводочными пастами Национального оптического университета (ГОИ) известного состава используют пасты для обоюдной притирки сопряженных полирования и поверхностей.
Свойства окиси хрома. Окись хрома — один из лучших материалов для доводочно-полировочных работ. качество и Производительность процесса приобретаемой поверхности зависят от исходных материалов, из которых приобретают окись хрома, от режима термической обработки окиси ее фракционирования и хрома.
Из всех известных на данный момент исходных материалов чтобы получить окись хрома (хлористый хромил, бихроматы калия, натрия, аммония, хромовой кислоты, хромовых квасцов и др.) лишь хлористый хромил и бихромат калия, восстановленные до окиси хрома серой, снабжают нужные полирующие особенности.
Из пяти марок окиси хрома, производимых по ГОСТ 2912-58, пригодны для полировки и доводки лишь две марки — ОХ-Э и ОХ-В. Эти марки, так же как и окись хрома, полученная из бихромата калия, требуют предстоящей термической фракционирования и обработки.
Окись хрома, полученная из вторых солей (бихромата аммония, Громовых квасцов), не владеет полирующей свойством; восстановленная, к примеру, углем либо спиртом она в 3 раза менее производительна, чем восстановленная серой.
Громаднейшей полирующей свойством (40—45 мк) владеет паста из окиси хрома, прокаленной при температуре 1600° С в течение 8 час. Подъем температуры до 1600 °С продолжается 16—18 час., охлаждение с печью — в течение 8 час. Содержание катализатора — 5%.
Окись хрома по окончании для того чтобы режима термической обработки получается в виде небольших спекшихся агрегатов тёмного цвета размером до 3 мм. При растирании они тяжело распадаются на отдельные кристаллы.
Окись хрома для 15-микронной пасты подвергают нагреву до 1200 °С в течение 12 час. Длительность нагрева при конечной температуре (1200 °С)—6 час., охлаждение с печью — в течение 6—7 час.
Кроме окиси хрома большую роль играются входящие в состав паст стеариновая и олеиновая кислоты. Они помогают не только связывающим окись хрома материалом. Стеариновая и олеиновая кислоты адсорбируются на поверхностях обрабатываемой подробности и полировальника. Отличаясь громадной активностью, они способны вступать и в химические соединения с окислами металла (к примеру, при обработке сплавов на базе меди).
Установлено, что пасты с однообразным числом парафина и стеарина дают различную производительность (пасты на парафине на 15—20% менее производительны) . Использование в качестве связывающего вещества индустриального масла вместо олеиновой кислоты практически в 2 раза снижает производительность. Оптимальное весовое количество стеарина, которое достаточно ввести в состав пасты, образовывает 10%. На практике вводят в большинстве случаев 20—30%, а при применении очень жёстких материалов в качестве главных паст количество жирных кислот возможно увеличено до 65—70%.
Так, к примеру, пасты на базе бора и карбидов кремния при содержании 70% жирных кислот разрешают применить их для притирки медной арматуры. В этом случае не образуется неотёсанных схватывания и рисок поверхностей. На процесс обработки пастами воздействуют смачивающие жидкости (керосин, вода, скипидар, растворы солей и др.).
Керосин в сочетании со олеиновой кислотой и стеарином есть лучшей жидкостью, наряду с этим нужно использование керосина из грозненской нефти вязкостью 1,05.
Производительность достигает большого значения при смачивании полировальника маленьким числом керосина и нанесении равномерного узкого полусухого слоя пасты. При смачивании пара громадным числом керосина вязкость пленки значительно уменьшается, паста наносится толстым неравномерным слоем, а производительность понижается до 10 раз.
Наличие в составе паст силикагеля содействует улучшению адсорбционной свойстве. Износ достигает максимума на протяжении прилипания и скоро падает на протяжении проскальзывания трущихся поверхностей. Исходя из этого производительность зависит не только от состава пасты, но и от толщины нанесенного слоя.
Пасты химико-механического действия в один момент оказывают на металл механическое, химическое и адсорбционное воздействие.
Если сравнивать с абразивными порошками и абразивными пастами, а также высокой твердости, пасты химико-механи-ческого действия владеют высокой полирующей свойством. Вместе с тем для них очень характерна пониженная стойкость если сравнивать с абразивными материалами.
Паста ГОИ 45 мк снимает с закаленного примера за 440 м пути (практически до полной утраты полирующей свойстве) слой металла толщиной 220 мк, микропорошок М28 такой же слой снимает за 720 м пути, а М20 — за 840 м. Из этого следует, что паста ГОИ 45 мк имеет меньшую стойкость, чем микропорошки М28 и М20. Но для съема нужного припуска при помощи пасты пример обязан состояться в среднем в 2 раза меньший путь.
Подобные результаты взяты при сравнении стойкости пасты ГОИ 40 мк химико-механического действия с пастами на базе микропорошков абразивного действия (рис. 2,6). Как видно из приведенных в табл.7 данных, паста ГОИ 40 мк снимает за 1 м пути в среднем в 2 раза больше металла, чем абразивные пасты.
Еще заметнее выявляется высокая полирующая свойство пасты ГОИ 40 мк при механизированной доводке. В этом случае с закаленной пластины 10 X 30 мм возможно достигнут съем 40 мк приблизительно за 35 оборотов диска-полировальника диаметром 400 мм. Следовательно, за 350 оборотов диска эта паста обязана снять слой металла толщиной 0,4 мм.
На самом же деле этого не происходит. Фактически толщина снятого слоя получается многократно меньше. Разъясняется это тем, что пасты ГОИ, как указывалось, владеют низкой стойкостью — по окончании 7—10 проходов по одному и тому же слою пасты ее полирующая свойство полностью исчерпывается.
Если не возобновлять слоя пасты на полировальнике (вращающемся стеклянном диске), то за первые 45 сек. съем металла (к примеру, на алюминиевых сплавах) возрастает практически пропорционально времени обработки. После этого наступает стремительная утрата полирующей свойстве пасты, и съем металла значительно уменьшается, причем на полировальнике обнаруживается столь много продуктов износа, что делается неосуществимым продолжать процесс обработки , пока они не будут удалены.
Следовательно, при условиях, в то время, когда полирующий слой пасты будет иногда возобновляться, величина съема должна быть близка к расчетной. Испытания всецело подтвердили сообщённое. С целью этого сконструировано приспособление к доводочному диску, разрешившее сперва механизировать, а после этого и автоматизировать удаления нанесения и процессы паст продуктов износа.
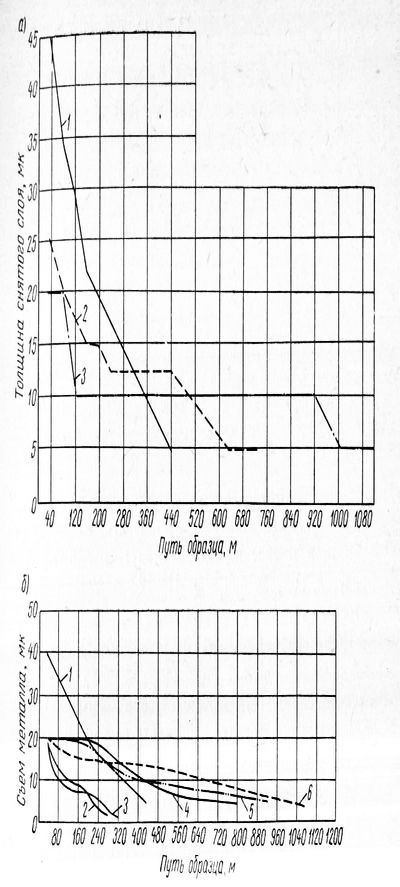
Рис. 1. Сравнительные эти стойкости:
а — пасты ГОИ и абразивных микропорошков: 1 — паста ГОИ 45 мк; 2 — абразивный микропорошок М28; 3— абразивный микропорошок М20; б — пасты ГОИ и абразивных: 1 — паста ГОИ 40 мк\ 2—6 — абразивные пасты.
В следствии опытов с применением приспособления установлено, что в случае если иногда возобновлять полирующий слой с учетом стремительной утраты полирующей свойстве паст, то в однообразных условиях величина съема металла, к примеру, с закаленной стали при доводке на чугунном полировальнике достигает приблизительно 0,4 мм, а с алюминия на стеклянном полировальнике— 1,0 мм в мин. Эта значительная технологическая изюминка пасты должна быть очень учтена при автоматизации задач процессов и решении механизации доводки.
автоматизация и Механизация процессов доводки пастами должна быть по большей части направлена на операции своевременного удаления и нанесения паст продуктов износа. При успешном ответе данной задачи делается вероятным снимать в течение нескольких мин. миллиметровые припуски, приобретая наряду с этим 11 — 12-й классы шероховатости.
Пониженная стойкость паст химико-механического действия и благодаря этого стремительная утрата их полирующей способности явились очень благоприятными особенностями при притирке и доводке сплавов на базе олова, алюминия и меди. Выполненное автором изучение износа трущихся поверхностей в присутствии паст ГОИ продемонстрировало, что в случае если между трущимися поверхностями (вкладыш и вал подшипника) покинуть слой пасты, то через 1000—1200 оборотов вала износ пасты заканчивается (наступает стабилизация износа).
Наблюдения за громадным числом турбинных подшипников (баббит), редукторных шестерен (сталь твердостью RC = 32—35), чугунных станин, вкладышей подшипников, тормозных золотников, арматуры (латунь, латунь), обработанных химико-механическим методом, кроме этого подтвердили отсутствие абразивного действия на подробностях, изготовленных из чугуна, бронзовых и алюминиевых сплавов.
В поверхностных слоях образцов, притертых неотёсанными и средними сортами паст ГОИ и шепетильно промытых, остатков пасты в виде зерен, талантливых повредить поверхность, не найдено.
Рис. 3. Производительность механизированной доводки пастами:
1 — электрон; 2 — дюралюминий.
Опробования говорят о том, что пасты не владеют режущими особенностями, свойственными абразивам, они не втираются в поверхность металла и не шаржируют его.
Полировальники. При химико-механической обработке не считая паст большую роль играются полировальники. От них зависит точность приобретаемой поверхности подробности.
Исходя из этого чтобы не было деформаций полировальник должен быть достаточно твёрдым и пребывать неизменно в хорошем рабочем состоянии, т. е. иметь правильную и ровную поверхность.
Главное требование, предъявляемое к полировальникам, это износостойкость под действием паст. Высокая износостойкость полировальника позволяет направить действие доводочного материала в основном на обрабатываемую поверхность, сохраняя, так, точность полировальника в ходе эксплуатации. С данной точки зрения заслуживает внимания чугун марки СЧ35-56, легированный комплексной добавкой хрома, молибдена и никеля.
Но эта марка чугуна требует долгих опробований.
Материал полировальника обязан различаться однородностью состава, твёрдости и структуры; он оказывает значительное влияние не только на точность приобретаемой поверхности, но и на производительность процесса.
По назначению все полировальники возможно поделить на две группы:
1) полировальники, используемые для правильной доводки; в эту группу входят чугунные, стеклянные и фибровые;
2) полировальники, используемые для полирования; ко мне относят эластичные полировальники из пробкового дерева, полимерных материалов и фетра — фторопласта и бутилметакрилата.
Чугунные полировальники самый пригодны для доводки сталей закаленных (твердостью RC = 56—60) и термоулучшенных.
Для изготовления чугунных полировальников широкое распространение взял серый перлитный чугун марки СЧ28-52 без пористости и твёрдых включений следующего состава: С (неспециализированный) —2,8—3,10%, а также С (связанный)—0,6—0,8%; Мп — 0,5— 0,7%’; Si —1,8-2,0%; S —0,1-0,12%; Р — 0,3-0,4%.
Структура чугуна должна быть с перлитной базой (90—95% перлита) и с равномерно распределенными выделениями графита в виде отдельных тонких пластин и гнёзд, малозавихренных и не переплетающихся между собой.
Необыкновенная роль в материале чугунного полировальника в собственности углероду. Неспециализированное содержание углерода влияет на износостойкость и темперамент выделения графита. Через чур малое содержание неспециализированного углерода ведет к образованию небольшого и эвтектического графита, повышенное содержание — большого графита.
Наличие этих видов графита неблагоприятно отражается на износостойкости чугуна. При изготовлении чугунных полировальников направляться учитывать раздельно содержание углерода — свободного и связанного. Нужно, дабы связанный углерод, входящий в состав перлита, был в громаднейшем количестве (0,6—0,8%).
Чем больше связанного углерода в чугуне, тем выше его твердость и износостойкость. Твердость по Бринеллю должна быть в пределах 200— 220 кг/мм2.
Термическая обработка. При отливке чугунных полировальников в следствии неравномерного охлаждения, и фазовых и структурных превращений появляются большие остаточные напряжения, каковые являются обстоятельством деформаций полировальников.
самый эффективным способом снятия остаточных напряжений в отливках есть отжиг (неестественное старение) по следующему режиму:
1. Загрузка в печь, нагретую не выше 100 °С (полировальники должны быть предварительно механически обработаны).
2. Нагрев до 450 °С со скоростью не более 60 °С в час.
3. Выдержка при 450 °С из расчета 25 мм/час по громаднейшей толщине.
4. Охлаждение со скоростью не более 20 °С в час до 80 °С.
5. Выгрузка полировальников из печи при 80 °С (не выше).
Чугунные полировальники по окончании отжига подвергают взаимной притирке и шлифованию.
В случае если по окончании шлифования неровность плоскости будет в пределах 0,02—0,03 мм на длине 0,5 м, то возможно создавать сразу же притирку пастой ГОИ 40 мк.
Притирку чугунных полировальников создают по схеме трех плит.
Стеклянные полировальники предназначены для обработки сплавов на базе алюминия и меди. Они должны быть изготовлены из оптического бесцветного стекла марок МКР-1 («Пирекс») и J1K6 («Легкий крон») (ГОСТ 3514-57). Эти сорта стекол отличаются высокой твердостью, химической устойчивостью и громаднейшей износостойкостью. Помимо этого, указанные марки владеют мельчайшим коэффициентом теплового расширения.
Последнее свойство особенно нужно при правильной доводке, в то время, когда температурные трансформации не должны приводить к формы стеклянного полировальника.
Износостойкость стеклянного полировальника под действием паст имеет огромное значение не только для сохранения точности полировальника в ходе его эксплуатации, но и для увеличения производительности процесса. Паста, изнашивая в основном обрабатываемую поверхность, конечно ведет к повышению съема металла, и к экономичному расходу пасты.
К преимуществам стекла относится не только высокое сопротивление износу под действием химических паст, вместе с тем однородность материала, антикоррозий-ность, возможность высокопроизводительной правки его свободным абразивом без шаржирования поверхности. Полировальники из стекла в течении многих лет удачно используют при обработке алюминиевых и бронзовых сплавов. Преимущества их содействуют увеличению качества доведенных поверхностей и неспециализированной культуре производства.