Пайка режущего инструмента с пластинками из твердых сплавов
Высокочастотная пайка инструмента имеет последовательность значительных преимуществ перед печной пайкой в очковых пламенных печах, пайкой газовой пайкой и горелкой на контактных сварочных автомобилях. При высокочастотной пайке имеются все условия чтобы получить высокое качество паяного инструмента с пластинками из жёстких сплавов, что и есть главным ее преимуществом. К этому направляться еще добавить, что по удобству ведения процесса пайки, производительности и стоимости ни один метод пайки инструмента кроме этого неимеетвозможности с ней соперничать.
Высокие требования, предъявляемые к режущему инструменту, заставляют большое количество трудиться над разработкой пайки, поскольку нереально иметь отличный инструмент без прочного паяного шва. Какого именно бы качества не была пластинка из жёсткого сплава, в случае если нет уверенности, что она надежно припаяна, нельзя рассчитывать, что инструмент будет прекрасно трудиться.
В то время, когда на протяжении работы ломается резец с пластинкой из жёсткого сплава, и пластинка скалывается и отлетает, значительно чаще обстоятельством поломки есть нехорошая пайка.
Пайка инструмента возможно неудовлетворительной благодаря многих обстоятельств; главные из них — нехорошая подгонка пластинок к корпусу и подготовка инструмента к пайке, неподходящие температура и режим нагрева, неудачная конструкция индуктора, через чур долгий процесс нагрева, наличие громадных внутренних напряжений из-за негативных условий охлаждения.
Уровень качества пайки инструмента в значительной мере зависит от работ по подготовке. Выборка паза в корпусе инструмента производится по форме пластинки методом фрезерования. Пластинка обязана прекрасно прилегать к сопрягающимся с ней плоскостям. завалов и Неровностей на плоскости корпуса инструмента, соприкасающейся с пластинкой, направляться избегать, поскольку они понижают прочность шва.
Заусенцы по окончании фрезерования необходимо зачищать. В зависимости от назначения инструмента пазы под пластинки изготовляются открытые и закрытые; первые имеют место у одно-лезвийного инструмента, по большей части резцов, вторые— у многолезвийного: сверл, фрез, разверток.
Ввиду того, что кое-какие инструменты сразу после пайки подвергаются закалке, направляться избегать острых углов, вызывающих появление трещин на протяжении охлаждения.
Корпусы инструментов должны поступать на пайку чистыми. оптимальнее , если они проходят обезжиривание в моечных автомобилях с последующей просушкой. Пластинки должны быть зачищены наждачной бумагой либо очищены на пескоструйном аппарате.
Те пластинки, каковые имеют коробление и не хорошо прилегают к корпусам, направляться отправлять на доводку.
В большинстве случаев, перед пайкой не нужно создавать особого обезжиривания твердосплавных пластинок, но, в случае если в этом появляется необходимость, они обезжириваются в бензине либо каком-либо втором растворителе. Прекрасно обезжиривает нитро-пастворитель РДВ.
Как мы знаем, что чем уже слой припоя в спаиваемом шве, тем прочнее шов. Но при пайке режущего инструмента, трудящегося в тяжелых температурных условиях, либо, к примеру, при пайке твердосплавных резцов, корпуса которых закаливаются в масле по окончании припайки пластинок, возможно замечать, что большее количество трещин появляется на тех экземплярах, у которых шов спая уже и пайка которых, казалось бы, должна быть прочнее.
В чем же обстоятельство происхождения трещин?
Оказывается, обстоятельство происхождения трещин в этом случае кроется не в перегреве, не в нехорошем качестве материала пластинки и не в нехорошей пайке, а в том, что появившиеся благодаря резкого охлаждения внутренние напряжения так громадны, что материал пластинки не выдерживает и растрескивается. Внутренние напряжения появляются потому, что материал корпуса пластинки и материал инструмента имеют очень сильно отличающиеся друг от друга коэффициенты линейного расширения. Время от времени коэффициент линейного расширения материала пластинки многократно меньше, чем материала корпуса.
Наличие между корпусом инструмента и твердосплавной пластинкой компенсационной прокладки из пластичного материала существенно сокращает внутренние напряжения. Материалом прокладки может служить пермаллой, и малоуглеродистое железо и никель в виде фольги либо небольшой сетки. Толщина компенсационных прокладок для небольших резцов образовывает 0,2—0,3 мм, для больших 0,8—1,5 мм. Прокладки перед пайкой подлежат очистке и обезжириванию.
Компенсационные прокладки направляться прокладывать по всем плоскостям прилегания твердосплавной пластинки к корпусу.
Одним из. мероприятий, снижающих внутренние напряжения в инструменте, трудящемся в тяжелых термических условиях, возможно кроме этого переход на пайку более легкоплавкими припоями.
Для предотвращения смещения при пайке пластинок, заложенных в закрытый паз, их направляться зафиксировато в нем кернением, штифтами либо клиньями. Заклинивание производится в тех случаях, в то время, когда пластинки сидят в пазах через чур вольно. штифты и Клинья изготовляются из мягкой стали.
В некоторых случаях, в то время, когда кернение не снабжает достаточно надежной фиксации пластинок, а заклинивание их сложно, для фиксации при пайке применяют шнуровой асбест, которым обвязывают многолезвийный инструмент с заложенными в пазы пластинками. Значительно чаще этим пользуются при пайке твердосплавных специальных фрез и свёрл.
В случае если при пайке в соляной ванне возможно привязывать пластинки металлической проволокой, то при высокочастотной пайке это делать не нужно, поскольку при нагреве проволока перегревается и перегорает еще задолго до расплавления припоя, благодаря наведения токов в ее замкнутых накоротко витках, и исходя из этого обеспечить фиксацию пластинки неимеетвозможности.
В отдельных случаях комфортно фиксировать твердосплавную пластинку на державке инструмента методом временной приварки к ней газовой либо точечной сваркой особой металлической технологической пластинки, которая может поддерживать либо закреплять твердосплавную пластинку на протяжении пайки в нужном положении.
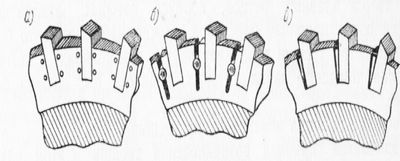
Рис. 1. Фиксация твердосплавных пластинок при изготовлении фрез: а — кернением; б— штифтами; в — клиньями
Рис. 2. Примеры фиксации твердосплавных пластинок на режущем инструменте с открытым пазом при помощи приваренных технологических пластинок: а — технологическая пластинка, временно приваренная к державке для облегчения пайки отрезных резцов; б — приваренные пластинки в виде полос прижимают твердосплавные пластинки к корпусу инструмента на протяжении пайки
Это делается, к примеру, при изготовлении отрезных резцов (рис. 2).
Для облегчения фиксации при пайке цилиндрических подробностей однообразного диаметра, к примеру, при необходимости удлинить сверла, целесообразно применять технологические соединительные муфты с прорезями либо отверстиями для подачи припоя и флюса. Плотная подгонка соединительной муфты разрешает создавать пайку без фиксирующего приспособления. Соединение финишей сверл в муфты выполняется встык, в косой стык либо часть сверла перед пайкой закрывают мокрым асбестом.
Технологические муфты, как и временно привариваемые фиксирующие пластинки, по окончании пайки удаляются последующей механической обработкой.
На собранный инструмент с пластинками, заложенными в закрытые пазы, флюс оптимальнеенаносить до помещения инструмента в индуктор методом опускания его в кипящий раствор, которым значительно чаще есть бура. Флюс наряду с этим попадает в небольшие зазоры, снабжая хорошее смачивание поверхности шва на протяжении пайки.
Подготовленный к пайке инструмент по окончании порции и нанесения припоя флюса вносят в индуктор. При пайке резцов припой в виде фольги либо стружки закладывается под припаиваемую пластинку и мало на нее; при пайке фрез, зенкеров и свёрл он находится большей частью в виде проволоки над спаиваемым швом.
Рис. 3. Удлинение сверл методом пайки с соединительной муфтой (прорезь в муфте предназначена для подачи припоя и флюса)
Рис. 4. Метод нанесения припоя в виде проволоки на многолезвийный инструмент с закрытым пазом: 1— корпус инструмента; 2 — твердосплавная пластинка; 3 — припой в виде проволоки
При пайке крупногабаритных резцов, требующих долгого времени прогрева, а также в тех случаях, в то время, когда припой не был подвергнут травлению перед пайкой, целесообразно при пайке класть припой на твердосплавную пластинку. Это обеспечат лучшую пайку благодаря тому, что все окислы, имевшиеся и появившиеся при пайке, будучи более легкими, чем припой, останутся наверху, не попадут в шов и исходя из этого не смогут отрицательно оказать влияние на его прочность.
При верном размещении паяемого инструмента в индукторе нагрев корпуса инструмента пара опережает нагрев пластинки, но к моменту расплавления припоя они имеют практически однообразную температуру. При пайке резцов это имеет место тогда, в то время, когда зазор между индуктором и пластинкой в 2—3 раза больше, чем между индуктором и корпусом инструмента.
Через чур мелких зазоров между индуктором и инструментом делать не нужно, в особенности при громадных мощностях, поскольку наряду с этим тяжело избежать местных перегревов и неравномерности нагрева, могущих являться причиной происхождения трещин на пластинках. Очаги местного перегрева смогут появиться из-за переходных сопротивлений между пластинкой, державкой и припоем при циркуляции и большой скорости нагрева индуктированных токов перпендикулярно плоскости пайки инструмента.
Процесс пайки резцов при высокочастотном нагреве осуществляется намного проще, нежели многолезвийного инструмента. В большинстве случаев, резцы паяются ручным методом в многоместном индукторе, в то время, когда в одном индукторе находятся сходу пара резцов с различной степенью нагрева. После достижения требуемой температуры нагрева ранее заложенным в индуктор резцом и расплавления припоя, что в жидкотекучем состоянии начинает интенсивно двигаться под действием сил элекромагнит-ного поля, резец вынимают из индуктора, поправляют и прижимают к нему пластинку, по окончании чего процесс пайки можно считать законченным.
Время от времени имеет место неверный подход к процессу высокочастотной пайки инструмента. Он содержится в том, что главные условия поверхностного нагрева под закалку механически переносят на процесс пайки. Наряду с этим стараются паять подробности на громадных мощностях, пробуя целый процесс провести в течение секунд либо долей секунды, стремятся к увеличению производительности за счет сокращения времени нагрева.
Таковой подход к пайке пагубно отражается на качестве режущего инструмента, в особенности резцов, приводя к браку из-за трещин на твердосплавных пластинках. Это происходит вследствие того что при работе на громадных удельных мощностях неизбежен неравномерный поверхностный нагрев неоднородного материала с местным перегревом пластинок при отставании нагрева державки.
Неблагоприятно отражается кроме этого на качестве резцов прогрев державки на малую глубину под пластинкой, вызывающий, по-видимому, резкое охлаждение пла-тинки по окончании отключения нагрева и благодаря этого высокие °нутренние напряжения, приводящие к поломкам и трещинам. В отличных показателей получаются при глубинном прогреве финиша корпуса резца с находящейся на нем пластинкой, при времени нагрева, разрешающем теплу попадать вглубь за счет теплопроводности металла. Таковой нагрев, не смотря на то, что и требует пара большего расхода энергии, но существенно усиливает уровень качества инструмента.
Режим пайки самый верно определять, исходя из нагреваемого количества и времени нагрева.
Рис. 5. Размещение резцов в индукторах двух конструкций: а — резцы в индукторе, снабжающем благоприятные условия нагрева для пайки; б — резцы в индукторе, не снабжающем благоприятных условий нагрева для пайки
От габаритов той части резца, которая находится в индукторе, зависит требуемая необходимое время и мощность пайки. По умелым данным время нагрева под пайку резцов может быть около 0,5—1,5 мин. на 1 шт., что соответствует средним скоростям нагрева 40—10 °С/сек. При таких малых скоростях нагрева понижается возможность происхождения трещин на пластинках резцов.
Исходя из этого высокой производительности при пайке режущего инструмента направляться достигать в основном не за счет сокращения времени нагрева, а методом применения многоместных приспособлений и индукторов, разрешающих паять в один момент пара резцов при самоё полном минимальных затратах и использовании генератора на подготовительное время. По окончании пайки резцы направляться класть на асбестовый страницу штабелями либо в тёплый песок для замедления их охлаждения.
Если производится пайка резцов с пластинками из быстрорежущей стали, нагрев ведется до более больших температур. В большинстве случаев припой наряду с этим выбирается с таким расчетом, дабы пайка происходила при температурах закалки быстрорежущей стали той марки, из которой сДелаНа пластинКЗ( ? тем дабы сразу после пайки подвергнуть ее охлаждению в струе сжатого воздуха либо в масле. При пайке таких резцов допускается после достижения температуры пайки прижатие пластинки вручную либо при помощи пресса, причем направляться учитывать, что пластинка в нагретом состоянии легко может смяться а также разрушиться.
Паять фрезы сложнее, чем резцы, поскольку наряду с этим требуется взять хорошее затекание припоя в шов на громадном его протяжении, что достигается либо одновременным нагревом всех пластинок, либо нагревом отдельными участками. Индукторы для пайки фрез изображены на рис. 10.
Индукторы с параллельными витками удобны для пайки твердосплавных фрез при медленном их вращении на особой оправке либо асбестовом диске.
При применении кольцевого индуктора, в которого концентрически помещается фреза, виток большего диаметра помогает для пластинок и нагрева фрезы снаружи, а виток меньшего диаметра — для подогрева корпуса фрезы снизу (рис. 32). Ввиду того, что корпус более массивен, чем пластинки и требует большего количества энергии, фреза находится на близком расстоянии от нижнего витка меньшего диаметра, чем и обеспечивается интенсивный прогрев корпуса до нужной температуры.
Пайка аналогичных подробностей без подогревающего витка очень тяжела, поскольку теплоотсос в массивный корпус фрезы затрудняет нагрев пластинок до требуемой температуры, в особенности в случае если пластинки изготовлены из быстрорежущей стали и паяются высокотемпературным припоем.
Пайка дисковой фрезы при последовательном нагреве отдельных ее частей с твердосплавными пластинками, проходящими при медленном вращении фрезы между двумя параллельно включенными прямоугольными витками индуктора (один из витков возможно перевернутым на 180°), разрешает следить за температурой нагрева отдельных участков и регулировать ее, изменяя скорость вращения фрезы. Таковой метод во многих случаях эргономичнее, чем нагрев фрезы концентрическим кольцевым индуктором, поскольку в последнем случае все припаиваемые пластинки достигают большой температуры практически в один момент, что не исключает возможности взять непропай из-за недогрева в одном месте, при перегреве — в другом.
Рис. 6. Пайка дисковой фрезы в круглом индукторе: 1 — индуктор; 2 — фреза; 3 — асбестовый лист
При таком нагреве по мере расплавления припоя фрезу неспешно поворачивают до тех пор, пока не будут припаяны все пластинки.
Рис. 7. Пайка дисковой фрезы в проходном индукторе: 1 — индуктор; 2 — фреза; 3 — асбестовый лист
По окончании напайки инструмент, не требующий последующего отпуска, направляется на очистку в пескоструйном аппарате, по окончании чего поступает на контроль., Уровень качества пайки инструмента с пластинками из жёсткого сплава проверяется внешним осмотром. Наличие черновин в паяном шве говорит о нехорошем качестве пайки. Особенно шепетильно направляться контролировать на наличие трещин инструмент, что по окончании пайки подвергается закалке.
Найти трещины возможно промывкой инструмента в керосине с последующей обдувкой песком. Трещины четко вырисовываются на очищенной поверхности, поскольку керосин выступает в местах трещин. Их возможно найти кроме этого внимательным осмотром в лупу.
Инструмент с пластинками из быстрорежущей стали, прошедший по окончании пайки пескоструйную очистку и дополнительную термообработку, подвергается контролю по наличию трещин и качеству пайки и, также, контролю, при необходимости, на твердость.
Производительность при высокочастотной пайке резцов существенно выше, чем при вторых методах пайки и может быть около, при наличии многопозиционного индуктора, одной-двух тысяч штук в смену.
Рис. 8. Пайка дисковой фрезы в петлевом индукторе: 1 — индуктор; 2 — фреза; 3 — приспособление