Пайка с общим нагревом
Пайка с неспециализированным нагревом осуществляется одним из следующих главных способов: погружением в жидкую среду, разогретую до соответствующей температуры; в печах с определенной газовой средой; в вакууме. Более активно используется пайка в электрических печах самых назначений и разнообразных конструкций.
Громаднейшее использование нагрев в печах находит при пайке высокотемпературными припоями — медью, бронзовыми сплавами, серебряными, никелевыми и др., но он может удачно использоваться и при пайке легкоплавкими припоями, и при пайке его сплавов и алюминия. Нагрев в печах владеет рядом преимуществ в сравнении с другими способами:
— равномерность нагрева, возможность контроля температуры и точного регулирования и времени выдержки;
— автоматизации процесса и сравнительная лёгкость механизации;
— высокая экономичность при условии постоянной работы; возможность обеспечения стабильного качества паяных соединений.
Особенно экономически выгодно и технически целесообразно использовать нагрев в печах при массовой пайке небольших подробностей (наряду с этим во многих случаях пайка совмещается с термической обработкой) и при пайке изделий сложных форм с солидным числом труднодоступных соединений.
Большой нагрев, снабжаемый печью по большей части определяется типом применяемых нагревателей. В печах с температурой нагрева до 1100 °С в большинстве случаев используются железные нагревательные элементы из жаростойких и жаропрочных сплавов; кое-какие особые сплавы снабжают нагрев до 1200 °С.
Но достигнуть более больших температур нагрева посредством таких нагревателей фактически не удается кроме того при применении защитной атмосферы в связи с относительно низкой температурой плавления этих сплавов. Использование керамических (силитовых и карборундовых) нагревателей снабжает нагрев до температуры 1300 °С.
Температуру нагрева до 1600 — 2500 °С дают нагреватели из вольфрама и — тугоплавких металлов молибдена. Но наряду с этим нужна защита нагревателя, поскольку указанные материалы при нагреве на воздухе скоро окисляются и разрушаются.
Сейчас созданы и используются высокотемпературные нагреватели из дисилицида молибдена (MoSi2) для температур до 1600 °С при нагреве на воздухе. Создан кроме этого новый тип нагревателя, воображающий собой молибденовый стержень, покрытый слоем дисилицида жаростойкой эмали и бора и выдерживающий на воздухе 1900 °С в течение 15 час.
Нагрев подробностей в печах под пайку возможно создавать в разных средах:
— в простой воздушной воздухе;
— в восстановительной воздухе;
— в защитной воздухе инертного газа;
— в вакууме.
Нагрев в печах с воздухом используется по большей части при низких температурах. Пайка в печах на воздухе при больших температурах ведет к сильному окислению изделий. Последующая очистка их от остатков и окалины флюсов есть очень трудоемкой операцией.
При пайке в восстановительной среде подробностей из конструкционных сталей и некоторых вторых материалов нет необходимости использовать флюсы, что существенно упрощает разработку всего процесса. Исходя из этого пайка в восстановительной среде есть прогрессивным методом и активно используется в индустрии. Такая пайка дает соединения с большой прочностью, предохраняет соединяемые подробности от обезуглероживания и окисления и снабжает высокую производительность.
В качестве восстановительной атмосферы в большинстве случаев используют газовые смеси и чистый водород, которые содержат водород либо окись углерода. Восстановительные особенности таких газовых смесей определяются концентрацией этих составляющих, и степенью очистки от паров воды, углекислого газа и кислорода.
При выборе газовой среды нужно руководствоваться следующими мыслями:
1. Восстановительные особенности газовой среды должны быть тем-болыне, чем химически прочнее окисел, покрывающий припой и основной металл.
2. С повышением содержания водорода в газовой среде возрастает ее взрывоопасность. Громаднейшей взрывоопасностью владеет чистый водород, намного менее страшен диссоциированный аммиак и, наконец, фактически надёжен продукт частичного сжигания диссоциированного аммиака.
В случаях, в то время, когда использование достаточно высокоактивной газовой среды нереально либо не нужно для данного паяемого припоя и металла, возможно сочетать газовую среду с применением флюса.
Серьёзной чёртом газовой среды, обусловливающей ее восстановительную свойство, есть содержание в ней жидкости. Содержание жидкости в большинстве случаев характеризуется точкой росы, т. е. температурой, при которой эта газовая среда оказывается насыщенной паром. Чем суше газ, тем ниже температура точки росы, тем более пригодна эта среда для целей пайки.
Пайка в газовых восстановительных средах производится в особых печах с подачей рабочего газа конкретно в рабочее пространство. Подобные печи довольно часто снабжаются конвейером для постоянного либо периодического перемещения паяемых подробностей.
На рис. 1 продемонстрирована схема печи конвейерного типа КП-60 для пайки в восстановительной среде. Печь имеет две охлаждения — и камеры нагрева. В камере нагрева имеются две самостоятельно нагреваемые территории: одна с температурой 800 — 850 °С, а вторая с температурой 1125 — 1150 °С. Протяженность рабочей камеры 3150 мм. Печь герметизирована, за исключением щели для прохода ленты транспортера, где предусмотрена завеса горящим газом.
Камера охлаждения выполнена из пяти отдельных секций. Рабочей частью конвейера есть лента шириной 300 мм из жаростойкой проволоки, сплетенной в виде сетки. Производительность таковой печи образовывает 40 кг/ч паяемых изделий. Большие размеры изделий 400X350 мм.
Для изделий с большим сечением 200X350 мм нашли использование печи типа ОКБ-147 с шагающим подом. Большая температура таковой печи также 1150 ° С и производительность до 60 кг/ч. При отсутствии таких печей пайка выполняется в особых герметически закрывающихся контейнерах с нагревом до заданной температуры в простых печах.
Контейнеры используются кроме этого для пайки металлов, покрытых пленкой трудновосстановимых окислов, поскольку в них легче избежать загрязнения газа влагой и воздухом.
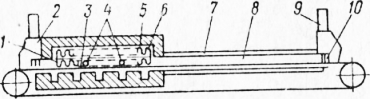
Рис. 1. Схема электрической конвейерной печи для пайки в восстановительной среде: 1 — территория пайки, 2 — загрузочный тамбур, 3 — сетка конвейера, 4 — отверстия для подачи газа, 5 — сводовые нагреватели, 6 — боковые нагреватели, 7 — корпус территории охлаждения, 8 — территория охлаждения, 9 — разгрузочный тамбур, 10 — асбестовые занавески
Трехфтористый бор довольно часто употребляется как добавка к газовой среде при пайке в воздухе инертных газов, делая наряду с этим роль газообразного флюса. В этом случае трехфтористый бор в смеси с защитным газом подается в контейнер в течение всего периода нагрева, выдержки при пайке и охлаждения до заданной температуры.
К числу прогрессивных способов пайки направляться отнести пайку в вакууме. Преимущества ее заключаются в сравнительной простоте управления процессом, в возможности получения отличных соединений на многих труднопаяемых сплавах и металлах и в высокой универсальности. Данный метод может снабжать достаточно высокую скорость (особенно при пайке маленьких изделий) и безопасность процесса.
На данный момент создан последовательность скоростных вакуумных установок.
Суть применения вакуума при пайке содержится в достигаемом наряду с этим резком понижении парциального давления кислорода и других активных газов, что разрешает полностью избежать окисления припоя и основного металла, а во многих случаях привести к разрушению имеющихся окислов. К тому же направляться учитывать, что при пайке в вакууме высокотемпературными припоями имеет место испарение окислов из главного металла, что кроме этого содействует получению качественных паяных соединений.
При пайке в вакууме направляться избегать применения сплавов, содержащих металлы с высокой упругостью паров (к примеру, кадмий, цинк), каковые при больших температурах будут интенсивно испаряться.
В зависимости от типа паяемых материалов создается вакуум с разной степенью разрежения, для чего употребляется соответствующее вакуумное оборудование. Ключевую роль в таких вакуумных совокупностях играется верный выбор вакуумных насосов.
При пайке сплавов и металлов, на поверхности которых образуются прочные окислы, требуется соответственно понижение остаточного давления до 10-4 — 10-5 мм рт. ст. Это требует применения более сложной аппаратуры, и в вакуумную совокупность последовательно с ротационными дополнительно вводятся пароструйные диффузионные насосы.
Для таких насосов употребляются масла, владеющие давлением насыщенных паров порядка ICh6 мм рт. ст., к примеру, масло марки Д-1А, обширно используемое в отечественной вакуумной технике. Диффузионный насос к совокупности подключается через особый вакуумный затвор, составляя с ним единый вакуумный агрегат.
Механические насосы ВН-461М, РВН-20, ВН-2Г и вакуумные агрегаты ВА-01-1 и ВА-05-1 употребляются в относительно маленьких установках (лабораторного типа либо небольших производственных). Насосы типа ВН-1МГ и агрегаты ВА-5-4 и ВА-8-4 применяются в больших лабораторных и средних производственных установках.
Для достаточно стремительной и экономичной откачки нужно верно подбирать размеры трубопровода и производительность насосов вакуумной совокупности.
Понижение парциального давления кислорода в окружающей воздухе достигается кроме этого при пайке в инертном газе — в большинстве случаев аргоне. В случае если сравнить по парциальному давлению кислорода воздух аргона, содержащего 0,005 % кислорода, и вакуум, то окажется, что соответствующее парциальное давление кислорода получается в вакууме при остаточном давлении приблизительно 2- 10-1 мм рт. .ст. Для получения более чистой среды нужна дополнительная очистка аргона от кислорода, азота, и осушка от жидкости.
Совокупности подачи и очистки аргона при пайке подобны совокупностям, использующимся при сварке. направляться иметь в виду, что довольно часто, кроме того в тех случаях, в то время, когда пайка ведется в воздухе инертного газа, в рабочем пространстве перед заполнением аргоном предварительно создается вакуум. Это разрешает многократно сократить расход газа, поскольку всецело исключается операция продувки аргоном для удаления воздуха из территории пайки.
Вследствие этого все современные достаточно большие установки для пайки в аргоне снабжаются вакуумными совокупностями и смогут кроме этого употребляться при необходимости для пайки в вакууме. установки и Такие печи стали называться вакуумно-компрессионных.
Изюминкой конструкции этих печей есть «холодный», во-доохлаждаемый герметичный кожух, принимающий внешнее давление при создании в печи вакуума и внутреннее избыточное давление при впуске в печь аргона.
На данный момент в индустрии употребляются особые установки для того чтобы типа, предназначенные для пайки изделий из разных материалов (высоколегированных и нержавеющих сталей, жаропрочных и титановых сплавов и др.), имеющие герметические камеры с территориями охлаждения и нагрева. Установки оборудованы механизмами для вращения либо продольного перемещения изделий в камеры. Большая температура нагрева в них достигает 1200 °С.
Существуют кроме этого установки для пайки относительно крупногабаритных изделий.
Как и при пайки в восстановительной среде, пайка в аргоне и вакууме может производиться как в особых печах, так и в контейнерах. При пайке в контейнерах воздушное пространство удаляется конкретно продувкой защитным газом либо предварительным вакуумированием.
Расход защитного газа при продувке, и чистота приобретаемой воздухи зависят от последовательности событий. При продувке нужно верно применять соотношение плотностей защитного газа и воздуха, что особенно принципиально важно при пайке изделий громадных сложных форм и размеров. К примеру, при продувке более тяжелым, чем воздушное пространство, аргоном рационально вводить его в нижнюю часть очищаемого количества, заставляя вытеснять воздушное пространство вверх.
По окончании вытеснения воздуха в контейнере остается большое количество адсорбированной и связанной жидкости, являющейся активным окислителем. количество и Время газа, потребное для удаления ее, смогут быть существенно уменьшены при верном сочетании нагрева и продувки контейнера. Так, продувка контейнера при комнатной температуре и последующий постоянный нагрев его в ходе пайки нерациональны.
При таком варианте в начале процесса нагрева контейнера отмечается увеличение содержания жидкости из-за десорбции и разложения гидратов; в будущем концентрация ее понижается, но к этому времени изделие успевает нагреться до температуры, при которой вероятно его окисление. Замедлением нагрева возможно уменьшить окисление, но это приведет к резкому повышению расхода газа.
Более рациональным есть исключение продувки при комнатной температуре и использование ступенчатого нагрева с выдержкой при температуре немного ниже температуры начала заметного окисления (фактически, ниже 200 — 300 °С). Это значительно сокращает расход защитного газа и повышает уровень качества защиты, что особенно принципиально важно при пайке материалов с повышенной активностью. Еще более высокие результаты достигаются при предварительном вакуумировании, но это связано с усложнением и удорожанием установки ее обслуживания.
Во многих случаях прекрасные результаты дает метод пайки погружением. Известны три разновидности этого метода:
1) пайка с погружением в соляную ванну;
2) пайка с погружением во флюсовую ванну;
3) пайка с погружением в расплавленный припой.
Во всех этих случаях паяемые подробности нагреваются расплавом ванны, нагретым до температуры пайки. Наряду с этим не только достигается равномерность нагрева и высокая скорость, но и предохраняются подробности от окисления.
Соляной ванной считается такая, в которой расплав нейтрален по отношению к окислам, покрывающим металл, и к самому металлу. Верно приготовленный солевой расплав всецело защищает металл от сотрудничества с окружающей воздухом, что при надлежащей предварительной подготовке подробностей разрешает паять кое-какие материалы, как к примеру нержавеющие стали, без флюсов. Солевой расплав защищает паяемые подробности от действия окружающей атмосферы не только в ходе пайки, но и при охлаждении, благодаря наличию узкой соляной корки, образующейся на поверхности подробностей.
Минимальная рабочая температура ванны, в большинстве случаев, обязана не меньше чем на 100° С быть больше температуру плавления расплава.
Перед пайкой в некоторых случаях подробности предварительно подогревают на воздухе до температуры 300 — 400 °С с целью уменьшения охлаждения ванны при погружении в нее подробностей.
Припой при пайке погружением в соляную либо флюсовую ванну заблаговременно укладывается в места соединений в виде проволоки, фольги, порошка, пасты.
Узлы из активных материалов удачно паяются погружением в соляные ванны в особых тонкостенных контейнерах.
На рис. 2 продемонстрирована схема групповой пайки узлов из титаного сплава погружением тонкостенного контейнера. Наряду с этим достигаются стремительный, равномерный высокое качество и нагрев изделий пайки.
Рис. 2. Схема групповой пайки в соляных ваннах с погружением особого контейнера: 1 — трубки для газа, 2 — крышка, 3 — песочный затвор, 4 — внутренний кожух, 5 — наружный кожух
Для пайки используются простые соляные ванны, т. е. тигельные с внешним электрическим обогревом (для температур до 850 °С) и электродные (для температур до 1300 °С).
Ванны для его сплавов и пайки алюминия погружением во флюс должны иметь тигель из химически стойких материалов (керамики, его сплавов и никеля), так как многие материалы очень сильно разъедаются используемыми флюсами.
Изделия сложной формы с громадным числом труднодоступных мест целесообразно паять погружением в расплавленный припой. Как пример таковой пайки возможно привести пайку соединений в радиоизделиях с печатными схемами. Подлежащую пайке печатную схему (плату) последовательно погружают на маленькую глубину во флюсовую ванну, в ванну с припоем и в промывочную ванну. Усовершенствованием этого процесса есть пайка волной расплавленного припоя.
Схема для того чтобы процесса продемонстрирована на рис. 50. Пайка погружением отличается высокой стабильностью и производительностью качества соединений и возможно обширно механизирована.
Рис. 3. Схема пайки волной припоя: 1 — ванна с припоем, 2 — паяемая подробность. 3 — крыльчатка, 4 — сопло
Рис. 4. Схема пайки сотовой панели с нагревом кварцевыми лампами: 1 — кварцевые лампы, 2 — сотовый заполнитель. 3 — обшивка панели, 4 — мягкий контейнер, А н Б — блоки кварцевых ламп
Не считая отмеченных выше способов пайки, в индустрии крайне редко удачно используется и ряд других. Так, к примеру, в Соединенных Штатах при изготовлении сотовых слоистых панелей для самолетов использование на практике начинает обнаружить пайка с нагревом кварцевыми лампами. Наряду с этим методе собранная панель помещается в контейнер, что герметически заваривается, после этого вакуумируется и заполняется аргоном.
Подготовленный контейнер с панелью устанавливается в приспособление между двумя блоками кварцевых ламп. Большая мощность, выделяемая лампами, образовывает около 200 вт/см2 паяемой панели. По окончании окончания цикла нагрева блоки кварцевых ламп отводят от панели, и приспособление с контейнером перемещают на позицию охлаждения.
С целью предотвращения коробления и ускорения процесса панель охлаждается между двумя водоохлаждаемыми плитами.
Целый цикл таковой пайки при температуре 950 °С в зависимости от толшины общей толщины и обшивки панели продолжается от 5 до 15 мин вместо 3 — 12 час при пайке в печах. Это достигается благодаря тому, что кварцевые лампы разрешают концентрировать высокую тепловую мощность конкретно на нагреваемом изделии. Пайка с применением в качестве источников нагрева кварцевых ламп начинает обнаружить использование при изготовлении многих вторых изделий.