Шлифование миниатюрных изделий
Особенности шлифования миниатюрных изделий. Характерная изюминка разработки миниатюрных изделий есть применение в качестве окончательной обработки шлифования, полирования, доводки. К этим изделиям относятся оси, валики, керны, иглы, штифты и т. п. изделия диаметром от 1 мм и менее, и малоразмерный режущий инструмент: сверла, развертки, метчики, пуансоны.
Материалом для их изготовления помогают высокоуглеродистые и легированные стали, жёсткие сплавы, минералокерамика и технические камни. В большинстве случаев, изделия должны быть обработаны по наружному либо внутреннему диаметру с высокой точностью (впредь до ±0,001 мм) и шероховатостью, соответствующей Ra 0,32—0,040 мкм.
Своеобразной изюминкой доводки и шлифования миниатюрных изделий есть обеспечение малых подач шлифовального круга, опасность происхождения местных напряжений, вызывающих деформацию, искривление, разрушение и изгиб изделия. Вследствие этого, при составлении технологических процессов шлифования нужно обеспечить уменьшение напряжений, появляющихся при их обработке. Помимо этого, при шлифовании миниатюрных изделий отмечается понижение их твердости, исходя из этого для инструмента и ответственных изделий предусматривается вторичная термообработка по окончании шлифования.
Шлифование цилиндрических изделий производится на кругло-, плоскошлифовальных и бесцентрово-шлифовальных станках.
Шлифование на круглошлифовальных станках. При шлифовании на круглошлифовальном станке изделие, имеющее ровную либо ступенчатую форму, зажимают в центрах, имея возможность вращаться. Вращение изделие приобретает через хомутик.
Шлифовальный круг крепят на шпинделе станка. Недочёт этого метода — необходимость в переустановке изделия для шлифования финиша, за что хомутик вращает изделие, и отсутствие возможности проскальзывания изделия довольно шлифовального круга при превышении упрочнения шлифования.
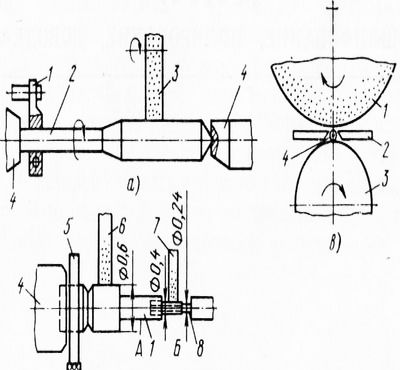
Рис. 1. Шлифование на кругло- и плоскошлифовальных станках
Для исключения прижогов, являющихся главной причиной брака ввиду малых размеров обрабатываемых изделий, передачу вращения к обрабатываемому изделию вместо твёрдого хомутика реализовывают посредством фрикционной пары методом установки резиновых дисков.
На рис. 1, б приведена схема обработки составного изделия ступенчатой формы с передачей перемещения резиновым диском. Изделие складывается из утолщенной металлической (диаметром 0,6 мм) и твердосплавной (диаметром 0,4 мм) частей. Изделие с одной стороны поддерживается смазанным твердосплавным люнетом, а с другой — узкой твердосплавной оправкой.
На крайнюю ступень изделия со стороны люнета надета переходная втулка с кольцом, контактирующим с приводным резиновым диском. Вращение резиновому диску сообщается эластичным шлангом. Наружный диаметр переходной втулки выполняется таким, дабы она входила в люнет с минимально вероятным для вращения зазором.
Обрабатываемое изделие легко снимается и снова устанавливается без нарушения точности базирования. Это разрешает делать шлифование в две установки. При одной установке электрокорундовым кругом 6 шлифуются ступени металлической части изделия, а при второй установке — алмазным кругом обрабатывается твердосплавная вставка.
Шлифование производится с охлаждением.
Неспециализированным недочётом обработки миниатюрных изделий на круглошлифовальных станках есть возможность большого прогиба изделия от силового действия шлифовального круга.
Ровные изделия возможно шлифовать на простом плоскошлифовальном станке. Изделие приводится во вращение резиновым диском и удерживается от выпадания направляющими ножами. Резиновый диск вместе с приводным устройством и направляющими ножами смонтированы в особом приспособлении, установленном на столе плоскошлифовального станка.
В ходе обработки стол с приспособлением перемещается под шлифовальным кругом.
Для шлифования цилиндрических изделий (пуансонов, заготовок малоразмерного инструмента) используют особые малогабаритные станки. На рис. 2, а продемонстрирован разрез узла шпинделя станка. В стойке укреплен полый шпиндель, в правый финиш которого засунута цанга с обрабатываемым изделием.
Вращение изделия осуществляется от электродвигателя (на рисунке не продемонстрирован) посредством клиноременной передачи. Шкив привода насажен на конец шпинделя. Зажим пуансона и цанги создают пружиной и гайкой через совокупность 10—11 рычагов.
Подача изделий из магазина в цангу осуществляется по каналу полого питателя. Толкатель помогает для проталкивания изделий в зону обработки. На рис. 2, б приведена схема узла шлифовальной головки станка. Шлифовальный круг, насаженный на шпиндель головки, приобретает вращение от электродвигателя через клиноременную передачу.
отвод и Подвод шлифовального круга создают поворотом рычага около оси.
Для шлифования твердосплавных изделий целесообразно использование алмазных кругов диаметром менее 20 мм и толщиной до 0,5 мм. Процесс изготовления таких кругов сводится к прокатке смесей железных и синтетических алмазных порошков. На особом оборудовании из смеси железных и синтетических алмазных порошков предварительно прокатывается заготовка в виде пластины требуемой толщины. В пластине алмазные зерна равномерно распределены по всему количеству.
Прокатка смесей порошков, снабжая стабильность свойств и высокую производительность процессов алмазной заготовки, разрешает кроме этого приобретать высокую точность по толщине пластины. Круги требуемых размеров и посадочные отверстия вырезают из заготовки на электроискровых станках, разрешающих изготовлять круги диаметром от 4 до 20 мм.
По окончании вырезки круги обрабатывают по наружному диаметру на круглошлифовальных станках для выведения торцевого и получения и радиального биения требуемого профиля. Для правки применяют круги КЗ зернистостью 16—25 твердостью CMl—СМ2.
Для придания алмазному кругу из синтетических алмазов нужного профиля возможно применять способ пластической деформации. Для этого круг нагревают до 400 °С и профилируют особыми металлическими роликами. Алмазные круги кроме этого изготавливают методом шаржирования.
Наряду с этим алмазные зерна раскладываются и вдавливаются в железный корпус, выполненный из пластичного материала, к примеру алюминия.
Рис. 2. Узлы станка для полирования и шлифования цилиндрических изделий: а — шпинделя; б — шлифовальной головки
Рис. 3. Шлифование на бесцентрово-шлифовальных станках
Шлифование на бесцентрово-шлифовальных станках. При шлифовании на бесцентрово-шлифовальном станке с ведущим кругом и опорным ножом изделие помещается между шлифовальным и ведущим кругами. Вращение изделие приобретает от ведущего круга. В ходе шлифования оно в меньшей степени подвергается изгибу, чем при обработке на кругло-шлифовальном станке. При шлифовании изделий диаметром менее 0,5 мм передача вращения от ведущего круга к изделию ухудшается ввиду малых размеров.
Для обеспечения стабильности частоты вращения изделия используют схему с двумя ведущими дисками. Наряду с этим один ведущий диск располагают ниже обрабатываемого изделия, а второй — над ним. Шлифуемое изделие прижимается кругом к неподвижной опоре. Диском сообщаются довольно малые скорости.
Эта схема возможно применена при обработке маленьких изделий.
Шлифование ровных миниатюрных изделий, имеющих внутреннее отверстие, производится на оправке. Внутреннее отверстие должно быть обработано совсем. Оправку перед установкой изделия смазывают. На протяжении шлифования оправка неподвижна, а вращение придается шлифуемому изделию посредством контактирующего с ней вращающегося резинового диска, что, со своей стороны, приобретает перемещение через торсионный валик. При установке и снятии обрабатываемого изделия резиновый диск отводится.
Поперечную подачу шлифовального круга создают до упора. Шлифование ведут с охлаждением.
Рис. 4. Схема шлифования на бесцентрово-шлифовальном полуавтомате
При бесцентровом шлифовании ось вращения изделия не занимает постоянного положения. Изделие при обработке может опираться собственной наружной и внутренней поверхностью. В случае если опорная поверхность сходится с поверхностью, подлежащей шлифованию, то ось вращения смещается на протяжении обработки, исходя из этого при бесцентровом шлифовании поверхности время от времени не являются строго круглыми.
Для бесцентрового шлифования изделий из закаленных углеродистых сталей У10А, У12А используют рабочие шлифовальные круги зернистостью 10—16, твердостью СМ2, СТ1К на керамической связке; ведущие круги зернистостью 10—16, твердостью Т1 на вулканитовой связке. Для шлифования изделий из жёстких сплавов используют алмазные круги. Шлифование на станках создают способом врезания либо на проход.
Способом врезания шлифуют цилиндрические изделия с буртами, выступами, и конические, сферические и другие фасонные изделия. Конические изделия возможно шлифовать с продольной подачей до упора. При первом методе изделие, установленное на нож между шлифовальным и ведущим кругами, приобретает вращение и осевую подачу от ведущего круга.
При втором методе осевая подача отсутствует, а шлифовальный круг приобретает поперечную подачу.
Станки для бесцентрового шлифования складываются из типовых узлов: бабки привода шлифовального круга, опоры для обрабатываемого привода и изделия вращения ее, смонтированного на станине станка. На станках с ведущим кругом он есть приводом и опорой для обрабатываемого изделия. Опорный нож есть второй опорой для изделия.
В бесцентрово-шлифовальных станках для шлифования изделий диаметром до 0,1 мм предусмотрено два диска и одна неподвижная опора. Созданы особые бесцентрово-шлифо-вальные станки для шлифовки прецизионных изделий. Одним из таких станков есть станок С-89, служащий для шлифования заготовок цилиндрических сверл диаметром 0,1—2 мм. Узлы станка приобретают перемещение от встроенного в станине электродвигателя.
Частота вращения главного шпинделя 6 тыс. об/мин; частота вращения ведущего круга 200, 400 и 600 об/мин. Точность обработки 0,01 мм.
В бесцентрово-шлифовальном станке 63 рабочих и ведущих круга вращаются в одном направлении, но с разными скоростями. Для движения шлифуемой заготовки на протяжении оси, т. е. для сообщения ей продольной подачи, ведущий круг устанавливают под маленьким углом по отношению к рабочему кругу.
На данный момент промышленность серийно производит бесцентрово-шлифовальный полуавтомат высокой точности ЗД180, служащий для обработки изделий минимальным диаметром 0,2 мм и 1 мм при врезном шлифовании. Шлифовальный и ведущий круги крепят на унифицированные шпиндели (рис. 69).
Обрабатываемое изделие устанавливают на опору.
За границей производят бесцентрово-шлифовальные станки, на которых создают шлифование цилиндрических изделий с наружным диаметром 0,25 мм и более. Достигаемый допуск равен ±0,005 мм. Шлифование реализовывают на проход. Производительность — одно изделие в 1 с. В связи с малыми размерами обрабатываемых изделий станок снабжен увеличительной лупой с подсветом. Изделия для обработки помещают в направляющий загрузочный V-образный лоток.
Оператор вручную проталкивает их в зону обработки. Пребывав между кругами, изделия опираются на особый нож и дополнительно удерживаются от выпадания верхней плитой. Это нужно ввиду их массы и малых размеров. Верхняя плита закреплена на шарнире, что облегчает ее отведение в сторону в ходе переналаживания станка и при необходимости визуально следить за процессом шлифования.
Готовые изделия отводятся со станка по узкой трубке.
Шлифование плоских узких изделий. Для шлифования узких пластин из хрупких материалов (мембран, конденсаторных пластин и т. д.) применяют следующий технологический прием; на прошлифованную опорную плиту накладывают узкую железную, к примеру латунную, сетку с ячейками 0,07—0,08 мм. Поверх сетки наносят слой клея, владеющего хорошей адгезией к материалу пластин, а после этого укладывают сами пластины.
По окончании отверждения клея опорную плиту с пластинами устанавливают на магнитную плиту плоско-шлифовального станка и создают шлифование. В ходе обработки толщину пластин осуществляют контроль, измеряя расстояния между их обрабатываемыми базовой поверхностью и поверхностями опорной плиты. По окончании обработки клей удаляют посредством растворителя.