Технологический процесс изготовления пластмассовых изделий
Таблетирование. При переработке пластических весов компрессионным прессованием громадное значение покупают правильная дозировка прессматериала, загружаемого в прессформу, уменьшение утрат на грат, удобство загрузки прессформы и т. д. С данной точки зрения громадные преимущества дает таблетирование материала, заключающееся в его механическом спрессовывании в жёсткие пилюли самой разнообразной формы.
Количество порошкообразного либо гранулированного прессматериала намного больше количества прессуемого изделия. Для фенопластов и аминопластов данный количество достигает 2,5-3-количеств изделия, а для во-локнитов — 7-10 количеств изделия. Это вынуждает делать в компрессионных прессформах загрузочные камеры громадных размеров.
Таблетирование порошкообразных материалов дает следующие преимущества:
1) значительно уменьшается количество исходного материала (для фенопластов приблизительно 1,0 г/см3), а следовательно, и размеры загрузочных камер пресс-форм;
2) отпадает операция взвешивания материала перед загрузкой в прессформу, поскольку пилюли имеют определенный вес;
3) ускоряется загрузка прессформы;
4) обеспечивается более правильная дозировка материала и уменьшаются утраты на грат и при взвешивании;
5) благодаря уменьшению включения воздуха (если сравнивать с порошкообразным материалом) ускоряется отверждение изделий и уменьшается цикл прессования;
6) постоянно совершенствуются условия предварительного подогрева, поскольку прогрев пилюль осуществляется при более большой температуре (170 — 190 °С — для пилюль, 100-120 °С — для порошка).
В большинстве случаев пилюли имеют форму цилиндров разной высоты, но в отдельных случаях им возможно придавать форму, близкую к форме готового изделия. Так, в случае если изделия имеют арматуру либо отверстия, то пилюлям придают особую форму, снабжающую их укладывание в формующую полость прессформы. При прессовании высоких полых конических либо цилиндрических подробностей рекомендуется использовать пилюли кольцеобразной формы.
Не все материалы в однообразной степени поддаются таблетирова-нию. отличных показателей получаются при таблетировании гранулированного прессматериала, имеющего однообразную величину зерен, снабжающую требуемые вес и объём с минимальным включением воздуха. Пилюли из порошкообразного материала имеют меньшую плотность.
Еще более затруднительно таблетирование материалов типа волокита и текстолита. Благодаря малой сыпучести этих материалов приобретаемые пилюли имеют неодинаковый вес и для спрессовывания требуют повышенных давлений.
Таблетирование возможно холодным (в необогреваемых пресс-формах) и горячим. Удельное давление при холодном таблетировании колеблется от 400 до 1800 кг/см2 (табл. 28).
При большем давлении прочность пилюль возрастает, но удлиняется процесс прессования, поскольку необходимо больше времени для перехода прессматериала в пластическое состояние.
Таблица 1
Уменьшение времени выдержки в прессформе при предварительном подогреве новолачных порошков
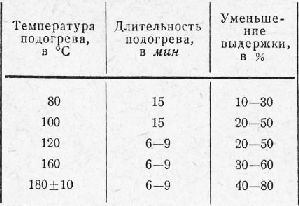
Таблетирование фасонных пилюль, по форме родных к готовому изделию, возможно создавать в обогреваемых формах. При тёплом таблетировании форма нагревается до температуры 80-120 °С; наряду с этим спрессовываемый материал, пребывав в форме 3-8 сек, лишь легко оплавляется по поверхности, не изменяя собственных физических особенностей. Горячее таблетирование содействует уменьшению содержания летучих в материале пилюли, увеличению ее удельного веса и прочности.
Предварительный подогрев. Предварительный подогрев есть одним из наиболее значимых этапов неспециализированного процесса прессования пластических весов. Различают два вида подогрева: низкий и глубочайший. Низкий подогрев используется для всех видов порошкообразного и гранулированного прессматериала.
Глубокому подогреву подвергаются таб-летированные прессматериалы.
Предварительный глубочайший подогрев позволяет равномерно прогреть пилюли по всей их толщине до температуры, равной температуре прессования. Благодаря этого пилюли, загружаемые в формующую полость компрессионной прессформы либо тигель литьевой формы, при приложении давления пуансона сразу же раздавливаются. Материал пилюли, переходя в пластифицированное состояние, растекается по формующей полости и скоро отверждается.
Применением предварительного подогрева достигается:
1) сокращение времени выдержки изделия в прессформе на 50-00%;
2) понижение удельных давлений прессования на 20-60%;
3) увеличение текучести материала на 25-50%;
4) уменьшение износа прессформы;
5) увеличение физико-механических и диэлектрических особенностей отпрессованных изделий.
Таблица 2
Прессование новолачных порошков с подогревом и без подогрева
Таблица 3
Изменение физико-механических особенностей изделий из новолачных порошков при высоком подогреве
Предварительный подогрев может производиться:
1) для пилюль из новолачных материалов толщиной 10-15 мм — в электротермостатах при температуре 160-180 °С; длительность — 6-9 мин. Подогрев резольных материалов производится при температуре 100-120° С; длительность — 6-9 мин. Недочёт подогрева в электротермостатах — неравномерный прогрев массы прессматериала: температура в пилюли либо навески материала не редкость ниже, чем на поверхности;
2) токами высокой частоты, что есть самоё эффективным, потому, что идет не методом передачи тепла, а происходит сходу по всей толщине материала. Материалы типа К-18-2 и К-21-22 в течение 30- 40 сек нагреваются до 140-160° С. Скорость и температуру подогрева токами высокой частоты нужно увязывать с длительностью одного цикла прессования и со скоростью переноса пилюли в прессформу.
Практика продемонстрировала, что материал, подогреваемый в течение 45-60 сек до температуры прессования, должен быть перенесен в прессформу и запресоован за 10- 30 сек, в противном случае его отверждение случится до начала прессования. таблетки и Порошкообразный материал, загружаемые в литьевые прессформы, нагреваются до температуры на 15-30° С ниже температуры прессования. Дополнительное тепло материал приобретает при прохождении литников прессформы;
3) контактный подогрев — между двумя обогреваемыми плитами; температура верхней плиты 115±5° С, температура нижней 105±5°С. Продолжительность выдержки зависит от толщины и диаметра пилюль и может быть около 30 мин и более. Производительность зависит от количества каналов в плитах.
Шеетиканальный контактный подогреватель (размеры плит 280?290?90 мм) за 9-10 мин способен подогреть 200- 250 г. пилюль диаметром 30 мм до температуры 85-95 °С.
литьё и Прессование пластмасс. Технологический процесс литья и прессования пластмасс складывается из следующих этапов: подготовка материала к прессованию, подготовка прессформы, фактически поделочные операции и прессование.
Подготовка материала включает в себя отвешивание либо отмеривание дозы материала, нужной для прессования, изготовление пилюль, и предварительный подогрев. При изготовлении изделий на литьевых автомобилях дозирование материала, поступающего в цилиндр автомобили, производится машинально перед инжекцией.
В подготовку прессформы входят: очистка прессформы, установка арматуры (при ее наличии) в формующую полость и загрузка пресс-материалом.
Процесс компрессионного прессования содержится в ярком формовании изделия, в период которого смогут быть сделаны подпрессовки, в раскрывании прессформы и удалении из нее отпрессованных изделий. При литьевом прессовании подпрессовки не производятся.
Режим преосоващш определяется следующими элементами:
1) температурой прессформы в период прессования;
2) удельным давлением пуансона (на 1 см2 горизонтальной проекции загрузочной камеры);
3) выдержкой под давлением, длительность которой зависит от толщины стенок изделия, сорта прессматериала, предварительного подогрева и температуры прессования материала.
Необходимым элементом режима переработки пластических материалов компрессионным и литьём и литьевым прессованием под давлением есть контроль температуры нагрева обогревательных плит пресса, прессформы либо материального цилиндра литьевой автомобили.
Контроль температуры производится раздельно для верхней и для нижней частей прессформы, поскольку разные веса пуансона и матрицы владеют неодинаковой теплоотдачей в внешнюю среду. Наличие разности температур нагрева пуансона и матрицы ведет к тому, что отпрессованное изделие остается в более холодной части прессформы.
Для контроля температуры употребляются датчики автоматических терморегуляторов либо в крайнем случае термометры, вставляемые в отверстия, сделанные в плитах пресса либо прессформы. Автоматические терморегуляторы поддерживают постоянство заданной температуры нагрева обеих частей прессформы либо материального цилиндра литьевой автомобили с точностью ±3 °С. Именно поэтому устраняется возможность перегрева либо недогрева, пятен, пузырей, недоливов, недо-прессовок и т. п.
На данный момент все машины и гидравлические прессы для литья под давлением оборудованы стационарными электрическими пультами автоматического управления.
При наличии электрического пульта управления гидравлический пресс может трудиться в двух режимах: автоматическом и наладочном. Наладочный режим употребляется лишь при установке прессформы и наладке пресса.
На автоматическом режиме выполняются следующие операции прессования: – предварительное смыкание прессформы под низким давлением; замедленное смыкание прессформы; – окончательное смыкание прессформы под большим давлением; подпрессовки до смыкания прессформы под низким давлением; предварительная выдержка прессформы в сомкнутом состоянии под большим давлением; – подпрессовки по окончании смыкания прессформы под низким давлением; выдержка изделия под давлением и разъем пресса на нужную высоту; – выталкивание и подъём выталкивателя отпрессованных изделий; включение подачи сжатого воздуха для удаления вытолкнутых изделий и очистки прессформы от остатков прессматериала; – опускание выталкивающего плунжера в исходное положение. В пультах вмонтировано устройство, сигнализирующее об окончании выдержки изделия под давлением, а кроме этого о неисправности соленоидов, управляющих гидравлическими клапанами.
Нарушение режима прессования ведет к браку изделий кроме того при в полной мере исправной прессформе и доброкачественном материале. В практике бывают случаи, в то время, когда из одной прессформы при прессовании пресс-материалов одной марки, но различных партий получаются разные по размерам подробности. Для получения аналогичных по размерам подробностей нужно шепетильно смотреть за режимом прессования и не допускать применения прессматериалов с разным содержанием жидкости и летучих.
Для увеличения механических особенностей отпрессованных уменьшения и изделий коробления для некоторых марок термореактивных материалов используется нормализация, проводимая в термостатах.
Дополнительно направляться подчернуть, что усадка фторопласта-4 зависит от степени сжатия материала при холодном прессовании. Практические опробования продемонстрировали, что большая степень сжатия достигается при удельных давлениях, равных 100-150 кг/см2; наряду с этим уменьшение размеров обожженного изделия в направлении перемещения пуансона равняется 1,4%, а в направлении, перпендикулярном перемещению пуансона, усадка достигает 6-8%. С увеличением удельного давления сжатия материала усадка по высоте изделия возрастает, а по диаметру либо длине и ширине пара значительно уменьшается.
Таблица 4
Режимы нормализации изделий, отпрессованных из реактопластов
Таблица 5
Особенности литья под давлением некоторых типов термопластов
Виды брака при компрессионном и литьевом прессовании реакто-пластов и при литье под давлением термопластов, а кроме этого обстоятельства его происхождения приведены в табл. 6.
Таблица 6
Виды брака при прессовании реактопластов и при литье под давлением причины и термопластов его происхождения