Антикоррозионная защита конструкций
Неспециализированные сведения. Главный способ антикоррозионной защиты металлических конструкций на фабриках-изготовителях — нанесение лакокрасочных материалов пневматическим либо безвоздушным распылением, струйным обливом, распылением в электростатическом поле, окунанием, кистью. Антикоррозионную защиту металлических животноводческих линий комплексов и конструкций электропередачи наносят кроме этого горячим цинкованием либо алюминированием, габаритных металлических резервуаров — напылением цинка.
На фабриках-изготовителях солидную часть изделий для защиты на период транспортирования, монтажа и хранения грунтуют одним слоем глифтал.евой грунтовки ГФ-021 по подготовленной поверхности. На монтажных площадках на поверхность конструкций наносят два слоя пентафталевой эмали ПФ-133 либо ПФ-115. Планируется окрашивание и грунтование конструкций перенести всецело на фабрики-изготовители.
Технологический процесс нанесения покрытий включает следующие операции: грунтования конструкций, сушки грунтовочного слоя, нанесения требуемого количества слоев покровных лакокрасочных материалов (эмаль, краска либо лак), сушки каждого слоя.
Широкое распространение находит новая быстросохнущая эмаль ПФ-1189, ..Дцставляющая собой суспензию наполнителей и пигментов в растворе алкидной смолы ЭПФ-40. Ее наносят в два слоя на поверхность металлоконструкций, очищенную от отслаивающейся ржавчины и окалины. Двухслойное покрытие данной эмали заменяет классическое трехслойное.
Наряду с этим срок работы его возрастает в 2 раза больше если сравнивать с покрытием одного слоя ГФ-021 либо двух слоев эмали ПФ-133 либо ПФ-115.
Время практического подсыхания эмали ПФ-1189 при температуре 7,5…8,5°С и влажности 74…92% образовывает 2 ч. Время сушки до степени, разрешающей создавать транспортирование конструкций,— 30…40 мин. По окончании нанесения первого слоя покрытие сушат в течение 10… 15 мин.
Эмаль используют в наборе с сиккативом НФ-1 и алюминиевой пудрой, до рабочей вязкости эмаль разбавляют сольвентом, ксилолом либо смесью ксилола с уайт-спиритом в соотношении 1 : 1. на 100 мае. ч. эмали ПФ-1189 додают 3 мае. ч. алюминиевой пудры и 5 мае. ч. сиккатива.
Кроме перечисленных лакокрасочных материалов для грунтования и окраски применяют металлический сурик по олифе оксоль, масляную краску МА-011, лаки БТ-517 и 63-4-81, грунтовку ФЛ-ОЗК.
Грунтовки ГФ-021 и ФЛ-ОЗК, эмали ПФ-133 и ПФ-115 возможно наносить пневматическим и безвоздушным распылением, струйным обливом, в электростатическом поле, окунанием, кистью; эмаль ПФ-1189 — пневматическим и кистью и безвоздушным распылением, металлический сурик на олифе оксоль — кистью и пневматическим распылением.
Главные технологические характеристики лакорасочных материалов — рабочая вязкость, время подсыхания, толщина одного слоя.
Рабочая вязкость — время истечения в секундах определенного количества жидкости через калиброванное отверстие вискозиметра. Для доведения лакокрасочных материалов до рабочей вязкости применяют смесь уайт-спирита с ксилолом либо сольвентом (1 : 1). Вязкость лакокрасочных материалов в зависимости от метода нанесения должна быть следующей, с: грунтовок ГФ-021, ФЛ-ОЗК при пневматическом распылении—16…24, при безвоздушном — 18…25, в электростатическом поле—17…20, струйным обливом — 17…20, кистью—12…30, окунанием—16…20; эмали ПФ-1189 при пневматическом распылении — 18…20, при безвоздушном распылении — 22…25, кистью — 35…40.
Толщина одного слоя грунтовки ГФ-021 должна быть 17 мкм, ФЛ-ОЗК— 19 мкм, металлического сурика на олифе оксоль и лака БТ-517—20 мкм, эмалей ПФ-133 и ПФ-115 —23 мкм, эмали 63-4-81 и лака ПФ-1189— 25 мкм, краски МА-011 — 28 мкм.
Длительность сушки при температуре 18…23°С поверхности, огрунтованной грунтовкой ГФ-021—28 ч, ФЛ-ОЗК и металлическим суриком на олифе оксоль — 24 ч.
Пневматическое распыление лакокрасочных материалов. При пневматическом распылении лакокрасочный материал температурой 18…23 °С сжатым воздухом преобразовывается в узкую дисперсную массу, которая наносится на поверхность.
Установка для пневматического распыления складывается из ручного краскораспылителя, соединенного шлангами со запасным оборудованием, которое снабжает подачу в краскораспылитель сжатого воздуха, очищенного от жидкости, лакокрасочного материала и масла.
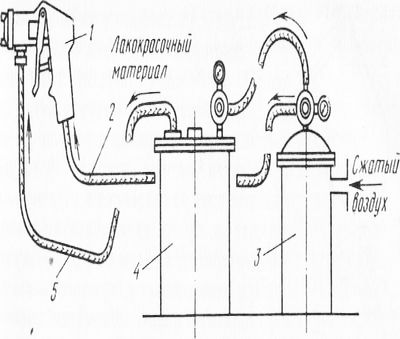
Рис. 1. Установки для пневматического распыления: 1 — краскораспылитель, 2 — шланг для подачи сжатого воздуха, 3 — маслоотделитель, 4 — красконагнетательный бак, 5 — шланг для лакокрасочного материала
Питание краскораспылителей сжатым воздухом возможно централизованным — от общей заводской сети либо при единичных работах — от личного компрессора. И в том и другом случае перед краскораспылителем устанавливают масловодоотделитель для очистки воздуха от загрязнений. Лакокрасочный материал может подаваться в краскораспылитель по шлангу 5 под давлением сжатого воздуха из красконагнетательного бака, установленного на рабочем месте.
При окраске конструкций на поточных линиях лакокрасочный материал подается совокупностью централизованной подачи.
Окрашивают конструкции пневматическими краскораспылителями в кабинах либо камерах, оборудованных вентиляционно-вытяжной совокупностью которая снабжает интенсивное удаление воздуха, загрязненного парами растворителя и красочной пылью, и его очистку.
При окрашивании железных конструкций значительно чаще применяют краскораспылители КРП-3 и СО-71А (Б). Корпус краскораспылителя представляет собой фасонную подробность, изготовленную из пластмассы. Нижняя часть корпуса выполнена в виде рукоять имеет удобную для обхвата рукой форму. В передней части корпуса находится ниппель краски, в задней — ниппель воздуха.
Подача краски в воздушную головку регулируется регулятором иглы. Воздушное пространство подается через воздушный клапан по окончании нажатия на курок.
Краскораспылитель включают в таковой последовательности. Раскрывается воздушный клапан пусковым курком, отводящим посредством муфты шток, что, преодолевая давление пружины, воздействует на шарик и открывает отверстие в седле для прохода воздуха в распределительную головку. После этого с некоторым опозданием отводится назад игла, освобождая отверстие сопла для выхода лакокрасочного материала. Этим достигается подача материала в воздушный поток.
При снятии упрочнения с пускового курка указанные отверстия закрываются в обратном порядке: сперва заканчивается подача лакокрасочного материала, а после этого сжатого воздуха.
При применении верхнего красконалив-ного стакана лакокрасочный материал подается к краскораспылителю через верхний штудер, а при работе от красконагнетательного бака через нижний штуцер. Наряду с этим один из штуцеров, верхний либо нижний, должен быть заглушён.
Красконагнетательный бак с перемеши-зающим устройством представляет собой герметически закрытый сосуд с крышкой, на которой монтируется арматура бака. Редуктор на баке помогает для понижения давления воздуха на краску. Часть воздуха от редуктора направляется прямо к краскораспылителю, вторая (со сниженным давлением) поступает в бак и вытесняет краску через трубку с фильтром в кран по шлангам к краскораспылителю.
Для безопасности работ установлен предохранительный клапан, что срабатывает при достижении давления 0,45 МПа.
Перемешивающее устройство представляет собой пневматическую турбинку для передачи вращательного перемещения мешалке. Шланги для подачи краски от красконагнетательного бака к краскораспылителю изготовляют из резинотканевого рукава диаметром 9 и 12 мм.
Способом пневматического распыления грунтуют около 70% изготовляемых металлоконструкций. Данный способ производителен, разрешает применять разные лакокрасочные материалы, применим для окраски поверхностей сложности и различной конфигурации. Уровень качества покрытия, нанесенного этим способом, высокое.
Недочёты этого способа — большие утраты на туманообра-зование и, как следствие, громадный расход лакокрасочных материалов, необходимость вентиляции и очистки воздуха, и применения личных средств защиты.
Способ безвоздушного распыления лакокрасочных материалов. Если сравнивать с пневматическим безвоздушное распыление имеет большие преимущества: меньшее туманообразование, лучшие санитарно-гигиенические условия труда рабочих, более низкий расход лакокрасочных материалов, более высокую производительность труда.
Рис. 2. Краскораспылитель типа СО-71А: 1 — головка, 2 — корпус, 3 — съемный наливной стакан, 4 — игла, 5 — регулятор иглы, 6, 10 — ниппели, 7 — трубка воздуха, 8 — воздушный клапан, 9 — курок
Сущность способа безводушного распыления содержится в том, что краска, находящаяся в гидросистеме установки, под давлением 8… 12 МПа при выходе из сопла краскораспылителя раздробляется до туманообразного состояния. Наряду с этим падение давления при выходе краски из сопла приводит к мгновенному испарению части растворителей, добавленных в краску, сопровождающееся большим повышением количества выходящего лакокрасочного материала.
Благодаря этого формируется мелкодисперсный факел краски, имеющий четкие границы и практически однообразную плотность по всему сечению. Туманообразование вне границ факела очень незначительно.
Главными факторами, воздействующими на формирование факела, являются давление в гидросистеме, вязкость краски, состав растворителей, качество изготовления и диаметр отверстия сопла.
Самый распространена установка «Радуга-0,63П», предназначенная для окрашивания изделий способом безвоздушного распыления под давлением 20 МПа. Все элементы установки смонтированы на каркасе.
Краскораспылитель типа КРБ-1 установки включают нажатием пускового крючка. Лакокрасочный материал под большим давлением проходит фильтр, встроенный в ручку. Он представляет собой полый цилиндр с продольными прорезями.
Наружная поверхность цилиндра имеет резьбу, по виткам которой намотана металлическая пружинная проволока. Лакокра сочный материал, проходя че рез зазоры, образованные со седними витками проволоки фильтруется чтобы не было засорения отверстия сопла.
Рис. 3. Установка безвоздушного распыления «Радуга-О.бЗП»: 1 — насос НПО,63-200, 2 — краскораспылитель КРБ-1, 3— шланг большого давления ШВД-200 , 4—всасывающий шланг с фильтром, 5 — патрубок, 6 — каркас-подставка, 7 — подача сжатого воздуха
Рис. 4. Краскораспылитель большого давления КРБ-1: 1 — распыляющее устройство, 2 — корпус, 3 — фильтр узкой очистки, 4 — поворотное устройство, 5 — пусковой крючок, 6 — предохранительное устройство
Предохранительное устройство 6 предназначено не только для предотвращения открывания запорного клапана при случайном нажатии на крючок 5, вместе с тем и Для фиксации крючка в рабочем положении, которая может пригодиться, к примеру, при окрашивании громадных поверхностей либо промывки совокупности. Распыляющее устройство имеет сопло с коническим либо цилиндрическим каналом. Сопло изготовляют из металлокерамики, карбида вольфрама и других износостойких материалов.
Шланг большого давления соединяется с краскораспылителем через поворотное устройство для свободного поворота краскораспылителя относительно шланга без трансформации его положения.
Обширно используют кроме этого агрегаты большого давления 2600Н для безвоздушного распыления материалов с условной вязкостью до 200 с (по ВЗ-4), с крупностью жёстких частиц до 0,08 мм и агрегат 7000Н — соответственно до 300 с и до 0,14 мм. Давление нагнетания в агрегат 2600Н — 23,5 МПа, 7000Н — 24 МПа, дальность подачи маловязких материалов по шлангам соответственно 40 и 90 м. Все элементы окрасочных агрегатов смонтированы на двухколесных тележках со съемными рукоятками и трудятся от электросети.
Вращение вала электродвигателя агрегата 2600Н посредством эксцентрика преобразуется в возвратно-поступательное перемещение поршня. Поршень через гидравлическую жидкость — масло, находящуюся в полости гидропередачи, сообщает перемещение мембране насоса.
В ходе возвратно-поступательного перемещения мембраны происходит всасывание лакокрасочного материала из расходной емкости через фильтр по всасывающему шлангу, потом через всасывающий и нагнетательный клапаны в шланг большого давления и распылитель с фильтром. Давление распыления изменяется регулятором давления насоса методом перепуска части масла из полости поршня в полость гидропередачи.
Рис. 4. Схема окрасочного 2600 Н: 1 — эксцентрик, 2 — гидропередача, 3 — электродвигатель 4 — маслофильтрующая пробка, 5 — поршень с пружиной, 6 — зазор для циркуляции масла, 7, 8, 9 — всасывающий, нагнетательный и перепускной клапаны, 10 — фильтр всасывающей совокупности, 11 — лакокрасочный материал, 12 — шланг, 13 — распылитель с фильтром, 14 — регулятор давления, 15 — мембрана, 16 — масло
При работе нужно располагать краскораспылители перпендикулярно окрашиваемой поверхности и на постоянном расстоянии от нее; передвигать распылитель с постоянной скоростью, наносить лакокрасочные материалы последовательным наложением параллельных полос, не проходя два раза по одному месту; смотреть за верным соотношением лакокрасочных материалов и подачи воздуха в распылитель, имея в виду, что в случае дефицита воздуха из распылителя выбрасываются большие брызги материала, а в случае дефицита материала образуются резкие толчки и пульсирующие струи; готовые рабочие составы по окончании доведения до рабочей консистенции должны быть процежены через сито с 3200…4000 отверстиями на 1 см2; шланги и краскораспылители закреплять за малярами и по окончании каждой смены шепетильно промывать в уайт-спирите или других растворителях.
Нужно иметь в виду, что утраты лакокрасочных материалов зависят не только от конфигурации конструкции, но и от расстояния распылителя до окрашиваемой поверхности (с повышением расстояния утраты материалов растут); от давления сжатого воздуха (с повышением давления при расстоянии 200…300 мм утраты материалов возрастают, а при расстоянии 100…200 мм — уменьшаются).
самая прогрессивной есть установка для бескамерной окраски металлических конструкций (рис. 180) с большими габаритами 13,8X3,6X3,3 м.
Установка имеет тележку с местным отсосом, на раме которой расположены три поддона и стеллажная решетка. Между кромками поддонов имеются щели, сообщающиеся с двумя вентиляционными патрубками, каковые закругленными финишами входят в канал гидрозатвора. Над каналом расположен короб воздуховода, опирающийся на трубчатые стойки, а в короба расположены трубы с распылительными форсунками для воды.
Короб воздуховода соединяется с гидрофильтром, имеющим два воздуходувных агрегата. Гидрофильтр представляет собой вертикальную шахту в виде металлического каркаса, обшитого металлическим страницей. В шахты расположены четыре полуцилиндра, образующие промывной канал, ванна-лоток для подачи воды и два водоотбойных щитка.
Подают окрашиваемые изделия на козелки посредством мостовых кранов.
Лакокрасочные материалы наносятся на поверхность изделий установками безвоздушного распыления 7000Н. Остатки лакокрасочных материалов, не покрывшие поверхность изделия, оседают на поддонах, а пары и аэрозоль растворителя отсасываются через щели поддона, проходят по вентиляционным патрубкам, коробу воздуховода и, очищаясь в гидрофильтре 6, выбрасываются в воздух.
По мере окрашивания тележка с местным отсосом, расположенная под стеллажной решеткой, подается в зону окраски и перемещается вместе с маляром. Руководят ходом тележки тумблером, смонтированным на краскораспылителе. Тумблер имеет три положения: «Вперед», «Назад» и «Стоп».
Кроме аэрозоля и паров местного отсоса растворителей из рабочей территории на высоте до двух метров над стеллажной решеткой располагают приточно-вытяжную вентиляцию.
Рис. 5. Установка для бескамерной окраски: 1 — тележка с местным отсосом, 2 — поддон, 3 — окрашиваемая конструкция, 4 стеллажная решетка, 5 — козелки, 6 — гидрофильтр, 7 — воздуходувной агрегат, 8 — распылительные форсунки воды, 9 — трубчатые стойки, 10 — канал гидрозатвора, 11 — вентиляционные патрубки, 12 — воздуховод, 13 — всасывающая щель местного отсоса
Рис. 6. Поточная линия бескамерной окраски: 1 — транспортная совокупность, 2 — мобильный портал, 3 — сушильная камера, 4 — рециркуляционный вентилятор, 5 — гидрофильтр, 6 —установка для бескамерной окраски. 7 — тележка с вентиляционным отсосом, 8 — тележка-поддон, 9 — механизм поперечного перемещения тележек-поддонов
Годовая производительность установки для бескамерной окраски при однослойном покрытии — 30 тыс. т металлоконструкций.
На базе установки для бескамерной окраски внедрена в эксплуатацию новая поточная линия, которая имеет транспортную совокупность, мобильный портал, установку для бескамерной окраски, сушильную камеру и гидрофильтр. Транспортная совокупность включает в себя тележки-поддоны на рельсовых дорогах, механизмы поперечного перемещения тележек-поддонов с механизмами разворота колес. Мобильный портал, опирающийся на две приводные тележки, имеет верхнюю площадку для маляра, монорельс с электроталью грузоподъемностью 2 т, два осевых вентилятора с душирующими патрубками.
Температура сушки в зависимости от лакокрасочного материала 60…90 °С при длительности сушки 80 мин.
Мобильный портал рекомендован для транспортирования тележек-поддонов посредством соединительных штанг, для раскладки, пакетирования и кантования небольших изделий электроталью, охлаждения изделий обдувкой вентиляторами, увеличения паров удаления растворителя и эффективности аэрозолей при окраске высоких изделий методом обдувки их вентилятором.
Годовая производительность линии при нанесении двухслойного покрытия 20…30 тыс. т металлических конструкций.
Самый обширно используемый способ нанесения лакокрасочных материалов способом распыления на металлические конструкции разной конфигурации позволяет механизировать и автоматизировать процесс окраски, взять покрытия хорошего качества.
Способ окраски изделий в электростатическом поле. При таком способе окрашивания исключается утраты лакокрасочных материалов, каковые достигают 50% при способе распыления. На данный момент в электростатическом поле окрашивают цилиндрические стержни длиной 3 м для пространственных решетчатых конструкций, элементы рамных конструкций коробчатого сечения, осваивают окрашивание стропильных ферм из гнутосварных профилей прямоугольного сечения.
Перед окраской эмалью ПФ-133 поверхность металлических конструкций подвергают дробеметной очистке до второй степени (ГОСТ 9.402—80), обезжириванию уайт-спиритом. Для грунтования используют грунтовку ГФ-021, растворитель сольвент с добавкой поверхностно-активного вещества (ПАВ) 3 либо СВ-102 числом 8,8% от массы сухого остатка грунтовки.
Для грунтования и окрашивания используют электростатические распылители ЭР-1ЭР и М-7 с закрытым электроприводом, заключенным в бакелитовую трубку. На верхнем финише трубки находится корпус с коническими шестернями внутри, приводящими во вращение горизонтальный шпиндель от электродвигателя. На шпинделе (частота вращения 1200 мин-1) закрепляют параболические чаши диаметром 50… 150 мм.
Краска подается в центр распыляющей чаши и под действием центробежной силы равномерно сбрасывается с ее кромки в виде небольших капель.
Окраска в электростатическом поле — прогрессивный способ нанесения лакокрасочных материалов на поверхность изделия. Высокое напряжение постоянного тока (до 100 кВ) между заземленным окрашиваемым распылителем и изделием формирует электростатическое поле. Частицы лакокрасочного материала, имеющие отрицательный заряд и движущиеся по силовым линиям поля с ко-ронирующего электрода распылителя к окрашиваемому изделию, заряженному положительно, оседают на его поверхности.
Частицы лакокрасочного материала, не осевшие на поверхности изделия, остаются в электростатическом поле и оседают на боковых и задней поверхностях изделия.
По окончании окрашивания и грунтования конструкции сушат в конвекционных либо терморадиационных сушильных камерах.
При окрашивании время от времени смогут появиться недостатки — в зоне примыканий раскосов, фасонок и других подробностей. Ликвидируют недостатки окраской безвоздушным распылением.
Коэффициент применения лакокрасочного материала — 90%. При окрашивании изделий этим способом значительно улучшается уровень качества покрытия.
Способ струйного облива. Данный способ используют по большей части для грунтования панельных переплетов.
Сущность способа содержится в том, что металлоконструкции, окрашенные лакокрасочными материалами посредством сопл, установленных по контуру конструкции, помещают в камеру с воздухом, содержащей определенное количество паров растворителей. Выдержка в парах растворителей нанесенного слоя лакокрасочных материалов разрешает замедлить процесс улетучивания из него растворителя в начальный момент формирования покрытия, что позволяет избыточному количеству лакокрасочного материала стечь с изделия, а оставшемуся — равномерно распределиться по поверхности.
Способ струйного облива возможно использовать для окрашивания и грунтования металлоконструкций на автоматизированных окрасочных линиях. Наряду с этим металлоконструкции не должны иметь глубоких карманов, внутренних полостей, затрудняющих стекание излишка лакокрасочных материалов. Крайне важно, дабы металлоконструкции были подвешены на конвейере в положение, снабжающее наилучшее стекание. Способ струйного облива негоден для нанесения быстросохнущих материалов.
Температуру лакокрасочных материалов при обливе нужно поддерживать в пределах 20…25 °С, время облива 1…2 мин, обильность облива 10…18 л/(мин • м2).
При антикоррозионных работах делают требования техники производственной санитарии и безопасности в соответствии с «нормами и Правилами техники безопасности, промышленной санитарии и пожарной безопасности для окрасочных цехов».
Лица, не достигшие 18 лет, к окрасочным работам не допускаются. Лица, не прошедшие предварительного медицинского освидетельствования, и имеющие противопоказания по состоянию организма, к работе с лакокрасочными материалами и растворителям и .не допускаются.
Готбвить рабочие составы из лакокрасочных материалов и разбавлять их растворителями нужно в краскозаготовительном отделении. Перемешивать и разбавлять материалы следует в железных ведрах, бачках либо резервуарах, снабженных приводными мешалками. Ведра и бачки должны иметь хорошо закрывающиеся крышки.
На рабочие места материал доставляют в хорошо закрытой небьющейся таре.
При громадных количествах лакокрасочных работ материалы поставляют централизованно и подают к месту работ по трубам. Пролитые на пол растворители и лакокрасочные материалы направляться срочно убрать, пол в этом месте засыпать песком. У рабочих мест возможно хранить лакокрасочные материалы в количестве, не превышающем сменной потребности.
Прием и одежды и хранение пищи в окрасочном цехе, складе и краскозаготовительном отделении лакокрасочных материалов запрещается.
Работы с применением открытого огня (сварочные и газорезательные работы) допускается делать не ближе 15 м от открытых проемов окрасочных и сушильных камер.
При пневматическом способе распыления лакокрасочных материалов нужно строго выполнять режим окраски чтобы не было повышения туманообразования и расхода лакокрасочных материалов. Рабочее давление сжатого воздуха на распыление не должно быть больше 0,5 МПа.
Чистить окрасочное и сушильное оборудование направляться инструментом из’цветного металла, не дающего искр. Сопла в зоне об-лива установки струйного облива нужно чистить при отключенном конвейере, но включенной вентиляции. В зону облива трудящийся обязан входить в респираторе.
При работе в помещении пневмораспылителями с лакокрасочными материалами, содержащими летучие растворители, рабочие должны быть снабжены очками и респираторами. К растворителям, выделяющим вредные пары, относятся: ацетон, уайт-спирит, бензол, скипидар, метиловый и этиловый спирты, толуол, ксилол.
Наносить защитные слои возможно лишь по окончании закрепления конструкций и надёжной установки в положении, исключающем самопроизвольный сдвиг либо поворот конструкций. Запрещается грунтовать конструкции, подвешенные на стропах и не установленные на стеллажи.
Рабочая одежда не должна иметь свисающих либо развевающихся финишей и должна быть наглухо застегнутой; свисающие финиши косынок, платков должны быть подобраны, манжеты рукавов — хорошо охватывать руки около кистей.
Для смазывания рук по окончании работы все рабочие должны быть снабжены пастами ПМ-I, «Ялот», биологическими перчатками. Пользоваться растворителями для мытья рук запрещается.
Нанесение цинкового покрытия. Способ тёплого цинкования содержится в погружении железных конструкций либо проката в расплавленный металл по окончании соответствующей подготовки поверхности. Между металлом покрытия и основным металлом образуется слой промежуточного сплава.
Относительная толщина этого слоя, так же как и толщина всего покрытия, колеблется в широких пределах и зависит от длительности нахождения изделия в ванне, состава ванны, температуры расплавленного металла либо сплава, скорости извлечения и конструктивной формы конструкции из ванны. Процесс отличается высокой производительностью и простотой технологии.
Ограничения в применении тёплого цинкования связаны с габаритами ванн (глубина вертикальных ванн до семи метров, размеры зеркала ванны до 2?2 м), короблением при нагреве сварных элементов тонкостенных конструкций и замкнутого сечения, невозможностью получения равномерного покрытия в сварных нахлесточных соединениях, если не обеспечен зазор между элементами не меньше 1,5 мм.
Металлизация изделий. К этому способу антикоррозионной защиты конструкций относится напыление цинка, заключающееся в распылении расплавленного цинка (и металла алюминия) на очищенную поверхность проката либо конструкции.
Структура покрытия имеет форму отдельных пластинчатых наслоений, а прочность сцепления покрытия с поверхностью изделия зависит от величины распыляемых частиц металла, скорости их полета, степени деформации частиц при соприкосновении с покрываемым металлом, его шероховатости и температуры поверхности. Покрытие при малых толщинах пористое, а получение толстых слоев (150…200 мкм) связано с громадной длительностью процесса.
Металлизационные покрытия наносят как на заводе — на технологических линиях в камерах, так и на монтажных площадках — на воздухе.
Разновидность металлизации покрытий — анодирование алюминиевых конструкций. Алюминий в простых атмосферных условиях мгновенно оксидируется, покрываясь защитной оксидной пленкой, мешающей предстоящему проникновению кислорода, в следствии чего алюминий получает коррозионную стойкость. Намного меньшую коррозионную стойкость имеют алюминиевые сплавы, в связи с чем их защищают от коррозии следующими методами: плакированием, анодным либо химическим оксидированием, глянцеванием и полированием, окраской лаками.
Анодное оксидирование (анодирование) — главной метод защиты алюминиевых сплавов от коррозии — пребывает в покрытии конструкции неестественным слоем жёсткой окиси алюминия (анодной пленкой). Анодная пленка владеет большой твёрдостью и прочностью, превышающей твердость инструментальной стали, высокой жаростойкостью и хорошими изоляционными особенностями, хорошим сцеплением и большой пористостью с металлом, благодаря чему есть хорошей базой для лакокрасочных покрытий.
Анодное оксидирование создают в ванных с водными растворами серной либо хромовой кислоты. С внутренней стороны ванны на стенах либо на дне укладывают свинцовые страницы, являющиеся катодами. Подробность, опущенная в ванну с раствором и соединенная с хорошим полюсом источника, есть анодом.
Для окрашивания подробностей в красный, светло синий, зеленый, тёмный и другие цвета в ванну наливают соответствующие красители.
По окончании оксидирования подробности промывают в холодной и тёплой воде для удаления остатков кислоты, уплотнения пленки тёплой водой за счет уменьшения объема пор и увеличения плёнки при нагревании, а после этого сушат до полного подсыхания.