Доводка и полирование миниатюрных изделий
При механической доводке изделий микропорошками вероятно взять точность формы, взаимного расположения и размеров поверхностей до 1-го класса точности; шероховатость поверхностей, Ra 0,040 мкм стабильные по качеству поверхности с минимальными деформациями без трещин, сколов, выкрашиваний; существенно улучшить эксплуатационные особенности изделий.
полирование и Доводку миниатюрных изделий создают вручную, на особых приспособлениях, установках, кругло-и плоскодоводочных станках. Производительность механизированной доводки в 3—5 раз выше если сравнивать с ручной.
полирование и Доводку цилиндрических изделий создают как продемонстрировано на рис. 1. При обработке на плоскодоводочных станках изделия помещают между верхней и нижней плитами — притирами, каковые совершают сложное перемещение. В рабочий промежуток между плитами подается доводочная алмазная, абразивная паста либо суспензия. Давление на изделия обеспечивается весом плит либо методом установки дополнительных грузов.
При доводке и полировании на круглодово-дочных станках кроме алмазной и абразивной паст употребляется твердосплавной диск. Изделие, зажатое в цанге, укладывают на люнет. При вращении изделия и твердосплавного диска происходит полирование и доводка последнего.
Производительность доводочных операций, качество и точность доводки в значительной мере зависят от верной подготовки их поверхностей на предшествующих доводке операциях. При доводке изделий на двухдисковых плоскодоводочных станках нужно ограничивать разновысотность обрабатываемых поверхностей изделий. Разброс размеров плоских и цилиндрических поверхностей в один момент обрабатываемых изделий не должен быть больше У4—V5 величины припуска под доводку.
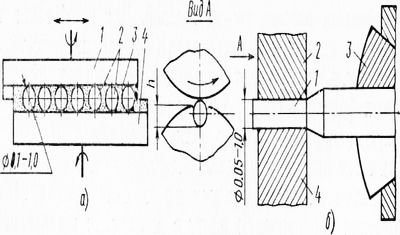
Рис. 1. полирование и Доводка цилиндрических изделий
При групповой односторонней доводке разновысотность обрабатываемых поверхностей изделий от установочной базисной поверхности при креплении в многоместных приспособлениях кроме этого не должна быть больше х/4—V5 величины припуска под доводку (в пределах 0,005—0,01 мм), что возможно фактически обеспечено на операциях шлифования. Припуски под доводку в зависимости от требований и размеров, предъявляемых к изделиям, целесообразно назначать в пределах 0,005—0,01 мм. Причем при односторонней и двусторонней плоской доводке рекомендуется назначать припуск в пределах от 0,04 до 0,08 мм, а при круглой доводке в пределах от 0,005 до 0,04 мм.
С целью достижения высокой производительности доводочных операций изделия на предшествующих доводке операциях направляться обрабатывать с шероховатостью, не более чем на два класса превышающей шероховатость поверхности изделия по чертежу, при условии обеспечения заданных требований по точности геометрической взаимного расположения и формы поверхностей.
На цилиндрических поверхностях изделий сложной формы должны быть предусмотрены канавки для выхода притиров. Изделия не должны иметь на поверхности трещин, вырывов, рисок. Сколы и выкрашивания на углах и гранях изделий из больших материалов не должны быть больше 0,02—0,04 мм.
Выбор микропорошков. Доводку миниатюрных изделий реализовывают микропорошками из синтетических либо природных алмазов, эльбора, карбида кремния зеленого — КЗ, карбида бора — КБ, монокорунда — МОНО, электрокорунда белого — ЭБ, хромистого — ЭХ, титанистого — ЭТ и др.
Доводку ведут:
а) пастами либо суспензиями при периодической их подаче на поверхность доводочного диска, притира либо изделия;
б) суспензиями — при их постоянной капельной подаче в зону обработки; в) предварительно шаржированными в поверхность доводочного диска либо притира зернами микропорошков.
Механическую доводку с постоянной подачей абразивной суспензии целесообразно использовать на предварительных доводочных операциях, и при доводке изделий, шероховатость поверхности которых Ra ^ 0,32—0,080 мкм. Пасты направляться использовать при механической и ручной доводке изделий со снятием в течение маленького времени главного припуска на начальных стадиях доводки. Наряду с этим на последних стадиях доводки обеспечивается точность до 0,001—0,003 мм и шероховатость поверхности, Ra 0,160-ь7?г 0,1 мкм.
Доводку зернами микропорошков, шаржированными в рабочую поверхность инструмента, используют на окончательных доводочных операциях, снабжая высокую точность изделий до 0,0003—0,0005 мм и шероховатость поверхности Rz ^ 0,1 мкм. Выбор микропорошков для полирования и доводки производится в зависимости от физико-механических особенностей материала изделия, качества и состояния обработки поверхности, требований и метода доводки, предъявляемых к доводочной операции.
Предварительную абразивную доводку закаленных металлических изделий притирами либо дисками из жёстких материалов (чугуна, стали) создают пастами и суспензиями из карбида кремния зеленого, карбида бора, электрокорунда обычного, белого, хромистого, и монокорунда. Причем предварительную доводку изделий из жёстких (HRC 48—62) хромистых сталей направляться осуществлять более производительными микропорошками из карбида кремния зеленого и карбида бора.
Получистовую доводку изделий из углеродистых сталей, сплавов и цветных металлов со съемом малых припусков ведут пастами либо суспензиями из электрокорунда титанистого либо белого, монокорунда, окиси алюминия (по окончании прокалки при температуре 1400—1500 °С).
полирование изделий и Окончательную доводку из мягких сталей, сплавов и цветных металлов чтобы не было шаржирования зернами обрабатываемой поверхности реализовывают абразивами пониженной твердости — окисью алюминия, окисью хрома, крокусом, глиноземами (по окончании прокалки при 1200—1300 °С). Для прецизионной окончательной доводки металлических изделий, предварительно шаржированных притирами и чугунными дисками, используют мелкозернистые порошки монокорунда, белого и титанистого электрокорунда и окиси алюминия (по окончании прокалки при температуре 1300—1400 °С).
Доводку изделий из металлокерамических жёстких сплавов, минералокерамики, ситаллов, технических камней создают алмазными микропорошками. Твердосплавные изделия направляться предварительно доводить алмазными суспензиями с постоянной (капельной) подачей их на рабочую поверхность доводочного диска. Предварительно и совсем — суспензиями и пастами с их периодической подачей.
Совсем — алмазным порошком, шаржированным в рабочую поверхность доводочного диска.
Доводку изделий из хрупких неметаллических материалов (минералокерамики, ситаллов, технических камней) возможно создавать суспензиями и алмазными пастами с периодической подачей их на поверхность доводочного диска либо притира из чугуна (предварительно) и мягких материалов — бронзы, меди, текстолита, органического стекла (совсем). Предварительную и окончательную доводку закаленных изделий из жёстких хромистых сталей на чугунных дисках либо притирах целесообразно вести микропорошками из эльбора и синтетических алмазов в составе суспензий и паст.
При алмазной доводке изделий из сталей, твердостью HRC 60—62 режущая свойство алмазных суспензий и паст АСМ5 в 2—8 раз выше абразивных на базе карбидов кремния, бора, электрокорундов. Причем обработка в этом случае сопровождается меньшими деформациями поверхностных слоев изделий, чем при абразивной доводке.
Поводку изделий из мягких сталей, цветных металлов и спла-оВ (HRC 25—45) делают микропорошками из эльбора либо аямазов на мягких (бронзовых, латунных) дисках либо притирах, снабжающих удержание зёрен и хорошее шаржирование в рабочей поверхности дисков в ходе доводки. Доводка изделий из мягких сталей, сплавов и цветных металлов суспензиями и алмазными пастами на чугунных дисках характеризуется понижением качества и производительности обработки в следствии частиц и шаржирования зёрен в обрабатываемую поверхность изделий.
полирование изделий и Окончательную доводку из сталей, сплавов и цветных металлов мелкозернистыми микропорошками из алмазов и эльбора в составе паст с их периодической подачей целесообразно создавать на дисках либо притирами из мягких полимерных материалов: текстолита, винипласта, органического стекла. Зернистость микропорошков из алмазов, эльбора и простых абразивов выбирают в зависимости от назначения доводочных требований и операций, предъявляемых к изделию.
Предварительную доводку металлических изделий реализовывают крупнозернистыми порошками из эльбора и простых абразивов М28—М40. Получистовую доводку ведут микропорошками зернистостью Ml0—М20, а окончательную мелкозернистыми — МЗ, М5, М7. Во многих случаях при необходимости исполнения очень узких полировальных и доводочных работ возможно использовать субмикронные порошки МО,7; МО,5; М0,3; имеющих размер главной массы зерен соответственно 0,0007; 0,0005 и 0,0003 мм.
При работе алмазными микропорошками повышение зернистости алмазов самый благоприятно при доводке твердосплавных изделий, поскольку более большие зерна стремительнее и лучше шаржируются в диск, а в закрепленном состоянии стойкость зерен быстро возрастает. Доводку твердосплавных изделий целесообразно создавать микропорошками в составе алмазных паст либо суспензий не больше АСМ20—АСМ28, а предварительно шаржированными в диск бриллиантами до АСМ28—АСМ40.
При применения алмазной доводки металлических изделий по окончании закрепления в поверхности чугунного доводочного диска либо притира зерна интенсивно изнашиваются и абразивная свойство алмазов с повышением зернистости от АСМ14 до АСМ40 возрастает незначительно. При доводке металлических изделий использовать алмазные микропорошки больше АСМ20 не рекомендуется.
Для понижения либо исключения попадания частиц бриллианта либо эльбора на поверхность изделий, в особенности из сталей, сплавов и цветных металлов, доводку пастами создают до полной утраты абразивной свойстве зерен, используют доводку предварительно шаржированными бриллиантами и эльбором, реализовывают последовательно доводку с переходом от больших микропорошков к небольшим с применением на завершающих стадиях дисков либо притиров из мягких и полимерных материалов, прекрасно удерживающих зерна и содействующих получению ровных, зеркальных поверхностей.
Концентрацию микропорошков в суспензиях и пастах выбирают в зависимости от его зернистости и вида абразива. С повышением концентрации зерен период их стойкости и величина суммарного съема материала возрастают; при чрезмерном повышении концентрации быстро возрастает расход микропорошков и понижается их режущая свойство.
При применения микропорошков из алмазов и эльбора в составе суспензий и паст с их периодической подачей повышение концентрации более 5—15% не нужно. В условиях доводки простыми абразивами (КЗ, КБ, ЭБ, ЭХ, ЭТ, МОНО) в составе паст с их периодической подачей концентрация микропорошка возрастает до 15—30%, а во многих случаях — до 45—50%. При доводке абразивными суспензиями с их постоянной подачей концентрация абразива в большинстве случаев образовывает 5—10%.
При применении алмазных суспензий с их постоянной (капельной) подачей с повышением концентрации до 3,5—5% отмечается рост съема материала. Мельчайший расход алмазов отмечается при доводке суспензиями с малой концентрацией алмазов в пределах 0,5—1%.
Способы подачи абразива. Выбор метода подачи абразива на инструмент определяет темперамент действия зерен на поверхность инструмента и изделия, работоспособность зерен, качество и производительность подвергнутых доводке поверхностей.
При доводке мазеобразными алмазными и абразивными пастами последние целесообразно подавать на шепетильно подготовленную рабочую поверхность инструмента лишь перед операцией. Пасту подают по окончании утраты абразивной свойстве ранее нанесенных в составе пасты зерен и тщательной очистки поверхности доводочного диска либо притира от остатков и шлама пасты.
период работы и Цикл пасты ее обновления определяется особенностями материала и зёрен изделия, зернистостью используемого абразива, конфигурацией обрабатываемой поверхности, соотношением площади обрабатываемой поверхности и инструмента, режимными и другими параметрами процесса.
Пасту на поверхность доводочного диска либо притира наносят в определенном количестве, зависящем от зернистости бриллианта либо абразива, вязкости неабразивной составляющей массы. В ходе доводки по мере скопления шлама для разжижения образующегося вязкого слоя и создания устойчивого слоя смазки рабочей поверхности доводочного диска, притира либо изделия подают рабочую жидкость. Подавать ее следует в определенном количестве, применяя дозирующие устройства с регулируемой подачей жидкости.
В табл. 12 приведены нормы паст разной зернистости, наносимые на поверхность доводочного диска, и нормы подачи рабочей жидкости. При применении способа предварительного шаржирования равномерно распределенные по поверхности доводочного диска в составе паст алмазные и абразивные зерна шаржируются в рабочую поверхность инструмента и прочно ею удерживаются в ходе доводки.
Шаржируют пасты способом накатывания посредством особого роликового приспособления. Шаржирование алмазных паст перемещающимися плоскими дисками либо плитами приводит к дроблению зерен в начале процесса шаржирования и ведет к понижению режущих особенностей зерен по окончании закрепления в диске. Шаржирование абразивов взаимно перемещающимися плоскими чугунными дисками (либо плитами) ведут при скорости относительного перемещения 8—10 м/мин, давление 0,15—0,18 кг/см2 в течение 2—4 мин.
При доводке алмазными суспензиями с малой концентрацией алмазов (0,15— 1 %) суспензию самый экономично подавать капельным методом числом 100—120 мг/мин при соотношении инструмента и площадей изделий в пределах 0,03—0,05. Для подачи применяют особые дозирующие смесители и устройства, устанавливаемые на станках.
Высокий уровень качества доводки возможно обеспечено при условиях, исключающих случайное смешивание паст разной зернистости, поскольку это может привести к повреждению’поверхности изделия большими зернами либо частицами и образованию задиров и глубоких рисок на обрабатываемых поверхностях. При переходе от более крупнозернистых микропорошков к небольшим, изделия нужно шепетильно очистить от суспензий и остатков паст, а доводку вести на дисках (притирах), соответствующих зернистости суспензий и паст и имеющих соответствующую маркировку.
полирование и Доводка цилиндрических изделий. Для доводки ровных осей, валиков, роликов, игл и других цилиндрических изделий малых диаметров с целью получения 1—2-го классов шероховатости и точности поверхности 0,16—0,04 мкм, помогает установка. Доводку изделий реализовывают за счет совмещения вращательного и возвратно-поступательного перемещения верхнего и нижнего притиров.
Изделия укладывают в пазы сепаратора 5, выполненного из органического стекла. Вращательное перемещение нижнему притиру сообщается от электродвигателя через червячный редуктор, а возвратно-поступательное от редуктора через ременную передачу сообщается механизму и водилу, соединенному с верхним притиром. Скорость вращения нижнего притира — 47 об/мин; верхнего — 75 двойных ходов в 60 секунд. Давление на изделия обеспечивается массой притира.
Для его подъема помогает стойка с подъемным приспособлением. Время доводки партии числом 24 изделий в среднем образовывает 5—б мин.
Для полирования и доводки до шероховатости Ra 0,04 мкм цилиндрических валиков,цапф, осей, малоразмерных сверл, разверток, метчиков рабочих частей калибровочных пуансонов и других изделий диаметром 0,05 мм и более с длиной полируемых участков до 8 мм помогает станок С-8а. Полирование и доводку создают твердосплавными дисками, рабочие поверхности заправлены по профилю доводимого участка изделия.
На станине смонтированы шпиндельная бабка, люнетная стойка и суппорт с качающимся рычагом. На правом финише качающегося рычага крепится шпиндель с полировальным диском. На левом финише рычага крепится груз — противовес.
Для настройки станка суппорт вместе с диском и рычагом может перемещаться в осевом и радиальном направлениях. Шпиндельная бабка, предназначенная для закрепления полируемой подробности в неподвижном центре, при настройке может перемещаться в осевом направлении. Вращение подробности производится от электродвигателя через шкив, поводок и ролики.
На полируемое изделие наряду с этим надевается хомутик. Для закрепления подробностей при помощи цанги имеется сменная шпиндельная бабка. Качающийся рычаг возможно наклонен в горизонтальной плоскости под углом до 10° для полирования конусных поверхностей.
В станке предусмотрен упор, что ограничивает опускание полировального диска.
Люнет, служащий опорой для полируемой цапфы, изготовляют из жёсткого сплава. По мере износа одной канавки люнет поворачивают и под полируемый элемент подробности устанавливают в другую канавку. Канавки наносят и доводят алмазными кругами либо вторым алмазным инструментом. При вводе изделия в канавку люнета нужно исключить провисание и изгиб.
Установку люнета по высоте создают микрометрическим винтом. Для обеспечения верной формы доводимого изделия нужно люнет систематически промывать в бензине либо керосине. Размер паза в люнете делают равным диаметру изделия плюс 0,01 — 0,03 мм, а глубину паза h = 0,8d.
Рис. 3. Круглодоводочный станок С-8а
Для полирования изделие одним финишем крепят в передней бабке станка, а вторым оно опирается на люнетный держатель. Для осуществления полирования твердосплавной диск накладывают на обрабатываемый участок. После этого изделию и диску информируют вращение в одном либо различных направлениях. Частота вращения диска равна 860 либо 1150 об/мин.
В случае если диаметр диска равен 75 мм, то его окружная скорость при этих параметрах равна соответственно 200 и 270 м/мин.
изделие и Шпиндель имеют частоту вращения 3500 об/мин. Благодаря малых диаметров полируемых изделий их окружная скорость не превышает 2—10 м/мин, т. е. многократно меньше окружной скорости диска, в связи с чем результативная скорость при полировании от трансформации направления вращения изделия изменяется незначительно.
Главным показателем производительности станка есть минутный съем материала, зависящий от диаметра, длины полируемого величины и участка припуска. Полировальный инструмент (твердосплавной диск) складывается из твердосплавного кольца и шайбы, которое либо припаивают к шайбе либо привертывают винтами посредством фланца.
На цилиндрической н торцовой поверхностях кольца наносят небольшие риски, наклонные под углом 10—20° к оси диска, каковые в ходе полирования соскабливают неровности с обрабатываемой поверхности. В качестве материала для дисков применяют жёсткие сплавы: В Кб, ВК8, ВКЮ и др.
В зависимости от требуемой шероховатости приобретаемой поверхности используют диски с большой, средней и небольшой заточкой, снабжающей соответственно шероховатость Ra 0,160— 0,040 мкм. Тип заточки определяется зернистостью алмазного инструмента, применяемого для правки и заточки диска.
полирование и Доводка плоских узких изделий. полирование и Доводка узких плоских изделий (мембран, прокладок, пьезокварцевых пластин высокочастотных кварцевых резонаторов и т. д.) толщиной менее 0,05 мм воображает серьёзные технологические трудности. Довольно часто нужно создавать полирование с обеих сторон узких изделий.
Для полирования таких изделий используют устройство для одновременного двустороннего полирования. Полируемые изделия устанавливают в отверстиях кассеты, движущейся между выполненными из отполированных материалов рабочими поверхностями двух кольцевых плит. Приспособление создано на базе доводочного станка.
Минимальная достигнутая толщина пластин при обработке с применением неподвижных плит — 0,08 мм, с применением вращающихся плит — 0,035 мм при допуске на толщину 0,0001 мм и плоскопараллельности не ниже 0,0002— 0,0005 мм.
При двусторонней доводке узких изделий в устройствах, складывающихся из двух притиров и размещенной между ними кассеты с обрабатываемыми изделиями, кассета не разгружена от сил, каковые появляются в ходе обработки в направлении плоскости кассеты. Это ведет к повышенному износу кассеты и не разрешает создавать обработку изделий уже 0,05 мм.
Для исключения обеспечения возможности и этого явления обработки изделий толщиной до 0,025 мм используют устройство, в котором верхний притир и кассета приводятся в перемещение эксцентриками, расположенными в одном радиальном направлен нии от оси вращения вала. Причем смещение эксцентрика, приводящего в перемещение кассету, в два раза меньше смещения эксцентрика, приводящего в перемещение верхний притир.
Устройство складывается из неподвижного нижнего кольцевого притира, кассеты, помещенной в держателе, верхнего кольцевого притира. Кассета имеет отверстия, в каковые закладывают обрабатываемые пластины. верхний притир и Держатель приводят в перемещение эксцентриками шпинделя. Смещение е эксцентрика в два раза превышает смещение эксцентрика. Последний связан с держателем через подшипник. Эксцентрик связан с верхним кольцевым притиром через обойму и подшипник.
Держатель опирается на неподвижное горизонтальное кольцо, установленное на трех регулировочных винтах.
Рис. 4. Устройство для полирования узких пластин
При вращении шпинделя кассета и верхний кольцевой притир приводятся эксцентриками во вращательное и поступательное перемещение. Наряду с этим верхний притир и кассета движутся неизменно в одном направлении, но скорость притира в два раза превышает скорость кассеты. Исходя из этого относительно кассеты верхний и нижний притиры движутся в противоположных направлениях с равными скоростями, что разгружает кассету от сил, действующих в направлении ее плоскости.