Формовочные материалы и смеси
Формовочные материалы. Формовочные материалы, используемые для того чтобы изготовить литейные форм и стержни, делятся на следующие группы: пески, связующие, противопригарные, высокоогнеупорные, особые и подсобные.
Цески (кварцевые, глинистые) появились в следствии разрушения горных пород (гранита, базолита и др.); они складываются из зерен минерала кварца (Si02) размером 0,06—1,6 мм с примесью других минералов и глины (окислы железа, полевые шпаты). Кварц владеет громадной высокой огнеупорностью и твёрдостью (температура плавления 1713 °С).
Кварцевые пески содержат до 2% глины и незначительное количество посторонних примесей, глинистые содержат глины до 50%. Глинистые пески по содержанию глины разделяются на худые (2—10%), полужирные (10—20%), жирные (20—30%) и весьма жирные (30—50% глины).
Связующие материалы: формовочная глина, жидкое стекло, сульфитная барда, разные крепители, этилсиликат, пульвербакелит и др.
Формовочная глина владеет высокой огнеупорностью (температура плавления 1750—1787 °С) и складывается из весьма небольших (0,001 мм) минеральных частиц, каковые при сотрудничестве с водой образуют клейкие растворы.
Жидкое стекло, сульфитная барда, крепители вводят в смеси, другие составы и противопригарные краски для придания им прочности.
Противопригарные материалы (графит, пылевидный кварц, тальк, каменный уголь и др.), и приготовляемые из них литейные краски, пасты-натирки наносят на поверхность стержней и форм с целью предупреждения пригара формовочных материалов к поверхности отливок. пылевидный кварц и Графит -используют как припыл и при приготовлении натирок и красок. Каменный уголь добавляется в состав формовочных смесей.
Высокоогнеупорные материалы (шамот, хромистый железняк, циркон, магнезит, асбест и др.) используют при изготовлении стержней и литейных форм для весьма больших и массивных отливок из легированных (нержавеющих, жаропрочных и т. д.) сталей, и многократно применяемых форм.
Особые материалы — чугунная дробь, каустическая сода, формалин, древесные опилки, торф и др. Чугунную дробь используют при изготовлении отливок особым способом литья как наполнитель. Древесные опилки, торф и др. вводят в смеси для податливости и повышения газопроницаемости высушиваемых стержней и форм.
Подсобные материалы — модельные пудры, разделительные жидкости, клей и др. разделительные жидкости и Модельные пудры используют при изготовлении стержней и форм чтобы при извлечении модели из формы, и стержня из стержневого коробки не повредить их поверхность. Клей используется при сборке форм и стержней для склеивания половинок.
Фундаментальные особенности формовочных материалов: теплопроводность, теплоемкость, газопроницаемость, прочность, текучесть и др.
Формовочные смеси. На данный момент в литейных цехах используют много разнообразных формовочных смесей. Выбор состава смесей обусловливается характером (весом, размерами, формой, родом сплава) изготовляемых отливок, и видом используемых форм (сырые, сухие, поверхностно подсушенные, химически твердеющие).
В зависимости от назначения смеси разделяются на облицовочные, наполнительные и единые.
Облицовочная смесь имеет наиболее высокий уровень качества и употребляется для покрытия рабочей поверхности формы, конкретно соприкасающейся с расплавленным металлом. Толщина слоя облицовочной смеси зависит от характера и рода отливки (15—50 мм).
Наполнительная смесь насыпается поверх облицовочной, владеет меньшей газопроницаемостью и прочностью и дешевле. Приготавливается наполнительная смесь методом переработки бывшей в потреблении формовочной смеси с добавлением (3—5%) свежих глины (и материалов песка).
Единая смесь образовывает целый количество формы и используется при машинной формовке, на автоматах в условиях массового производства небольших и тонкостенных отливок. От наполнительной смеси она отличается громадным содержанием свежих материалов и лучшими физико-механическими особенностями.
Стержневые смеси. свойства и Состав стержневых смесей обусловливаются в основном классом изготавливаемых стержней.
Важные стержни первого класса изготавливаются из стержневых смесей, состоящих полностью из кварцевого песка с добавлением крепителей. Большие стержни изготавливают из более недорогих стержневых смесей, в них частенько входит бывшая в потреблении смесь (20—35%), а связующим есть формовочная глина, сульфитная барда, а в качестве органической добавки — древесные опилки.
Стержневые смеси должны владеть теми же особенностями, что и формовочные. Но учитывая, что большинство стержня (не считая знаков) подвергается действию большой температуры и давлению заливаемого металла в форму, их делают с более большим показателями прочности, газопроницаемости, податливости и огне упорности.
В состав стержневых смесей значительно чаще входит чистый кварцевый песок от 70 до 100%;, огнеупорная глина либо бентонит и разного рода крепители. Такие смеси владеют высокой газопроницаемостью до 120, прочностью до 0,55 в сыром состоянии и до 12 кг/см2 в сухом. За последние годы широкое использование для того чтобы взяли жидкие самотвердеющие смеси, владеющие хорошими технологическими особенностями.
Регенерация отработанных смесей. Регенерации подвергаются отработанные смеси, накапливающиеся в обрубно-очистном отделении (от выбивки стержней, от очистных автомобилей), просыпи, собираемые с пола формовочного и стержневого отделений, сушильных камер и др. Такая смесь содержит в себе большое количество пыли, золы от сгоревших угля и опилок, куски форм и стержней, разные железные и неметаллические включения, и до 60—80% зерен песка, пригодных к предстоящему применению.
Для извлечения зерен песка из данной смеси ее подвергают переработке: разминанию комьев, магнитной сепарации, просеиванию и обеспыливанию.
—
Получение отличных отливок в значительной мере зависит от качества формовочных смесей и материалов, из которых изготовлены формы и стержни.
Формовочные материалы разделяют на главные — пески, глины и вспомогательные, к каким относятся связующие, используемые для изготовление стержневых смесей, противопригарные материалы (каменный уголь, графит, краски, хромистый железняк, циркон и др.), и клей, замазки, припылы и т. п.
Формовочные пески
Формовочные пески поставляются в естественном и обогащенном состояниях. По ГОСТ 2138—74, пески в зависимости от содержания глинистой составляющей (так именуются зерна с величиной в поперечнике менее 0,022 мм), вредных примесей и кремнезёма делятся на классы, а в зависимости от величины зерен главной фракции — на группы.
Для определения группы песка его необходимо просеять через обычный комплект сит и узнать, на каких трех смежных ситах осталась солиднейшая сумма остатков (в массовых единицах), именуемых главной фракцией. Зная, на каких ситах находится главная фракция песка, его возможно отнести к группе, которая определяется средним номером сита.
Формовочные глины
Формовочные глины, используемые в литейном производстве в качестве минеральных связующих в формовочных и стержневых смесях, классифицируются по минералогическому составу, по пределу прочности во мокром и сухом состояниях, по содержанию вредных примесей и по некоторым вторым особенностям.
По минералогическому составу формовочные глины делятся на виды, по пределу прочности при сжатии во мокром состоянии — на группы, в сухом — на подгруппы. В зависимости от содержания вредных примесей формовочные глины делятся на группы.
Основное различие между формовочными глинами содержится в том, что они имеют различные кристаллические решетки, в связи с чем на поверхности смогут появиться водные пленки различной толщины. Мельчайшее количество воды может удержаться на поверхности каолинитовых зерен, а громаднейшее — на поверхности монтмориллонитовых зерен. Из этого направляться, что монтмориллони-товые (бентонитовые) глины целесообразно применять при формовке по сырому.
Использование этих глин разрешает в 2—3 раза снизить содержание глинистой добавки в смесях, повысить их газопроницаемость, во многих случаях заменить формовку по сухому формовкой по сырому, улучшить поверхность отливок и т. д. При формовке по сухому возможно применять глины любого вида.
При приготовлении формовочных и стержневых смесей все составные части, за исключением воды и жидких связующих, загружают в смесители в размолотом либо сыпучем виде. Так как процесс получения глиняного порошка связан с обильным пылевыде-лением, то при изготовлении чугунных отливок по сырому вместо него используют глиняные либо глиняно-угольные суспензии.
3. Связующие материалы
Стержневые смеси, в которых связующим есть формовочная глина, в большинстве случаев, не снабжают таких качеств стержней, как прочность, газопроницаемость, выбиваемость. Благодаря этого глину приходится заменять материалами, владеющими высокой связующей свойством и придающими стержням большую прочность при сохранении хорошей выбиваемости и газопроницаемости.
Связующие материалы подразделяются на органические и неорганические и на три класса:
А — органические неводные, Б — органические водные и В — неорганические водные.
Класс А объединяет связующие, каковые владеют связующей свойством и не требуют добавления воды. Они не растворяются в воде, не смешиваются с ней и не смачиваются ею (масла, олифы, пеки, битумы, канифоль). В класс- Б входят связующие, растворяющиеся в воде, по окончании чего они покупают свойство связывать песок (декстрин, сульфитно-спиртовые бражка и барда).
К классу В относятся все неорганические связующие (формовочная глина, цемент, жидкое стекло), каковые, так же как и связующие материалы класса Б, оказывают собственный воздействие лишь по окончании добавления к ним воды.
Для удобства пользования связующие каждого класса разбиты на три группы. В каждую из трех групп входят связующие, владеющие приблизительно однообразными физико-механическими и технологическими особенностями. Главным показателем отнесения связующего к той либо другой группе есть прочность (временное сопротивление разрыву, в кгс/см2, пробного примера в сухом состоянии), приходящаяся на 1% связующего материала, введенного в состав смеси.
Оценка связующих производится по технологической пробе в лабораторных условиях. Из взятой смеси со связующим изготовляют образцы для опробования прочности на сжатие всырую и на разрыв всухую, и на газопроницаемость. Сушка образцов производится в соответствии с техническими условиями на данное связующее.
Как правило связующими являются побочные продукты, приобретаемые прн переработке нефти, горючих сланцев, древесины, хлопкового масла и др.
4. Противопригарные и другие вспомогательные материалы
В следствии химического и механического сотрудничества формы либо стержня с жидким сплавом, недостаточной огнеупорности и увеличенной пористости смесей, и большой температуры заливки на отливках образуется пригар. Для борьбы с ним используют особые противопригарные материалы.
Каменный уголь. При формовке по сырому в состав смеси вводят добавки каменного угля в измельченном состоянии следующего состава, в %: летучие вещества — не меньше 30, сера — не более 2 и зола — не более 11, влага — не более 12. Каменный уголь возможно заменен эстонским сланцем в виде порошка.
При нагревании формы жидким сплавом частицы угольной или сланцевой пыли выделяют летучие вещества и сгорают с образованием окиси углерода, наряду с этим между формой и сплавом образуется газовая прослойка, которая исключает возможность смачивания зерен песка сплавом и образования пригара.
Пылевидный кварц. Различают два вида этого материала: естественный и неестественный. Громаднейшее использование имеет неестественный пылевидный кварц, что приобретают методом размола кварцевого песка.
Пылевидный кварц применяют при производстве металлических отливок в качестве добавки в облицовочные смеси. Это сокращает пористость рабочего слоя формы либо стержня, в следствии чего значительно уменьшается механический пригар.
При введении пылевидного кварца в состав краски для стержня и покрытия формы на поверхностях образуется высокоогнеупорный слой, защищающий их от влияния большой температуры заливаемого сплава.
Циркон. При обогащении титаноцирконовых руд приобретают материал, именуемый цирконом. Промышленность производит цир-коновый концентрат для изготовление облицовочных формовочных и стержневых смесей и цирконовый порошок для красок.
Циркон — высокоогнеупорный материал (температура его плавления 2190 °С), он не вступает в химическое соединение с железом и легирующими элементами и есть хорошим противопригарным материалом.
Для стержней и облицовки форм рекомендуется следующий состав, в %:
цирконовый песок—100 и сверх 100% формовочная глина — 2; сульфитно-спиртовая барда — 2—3.
Хромистый железняк. Продукт помола хромитовой руды — хромистый железняк характеризуется большой огнеупорностью-Температура его плавления около 1850° С. Отсутствие сродства с окислами железа и постоянство количества при нагревании снабжают получение высококачественных отливок .
Используют облицовочные формовочные и стержневые смеси следующего состава, в : хромистый железняк (просеивается через сито с ячейками 1,5?1,5 мм) —100 и сверх 100 сульфитно-спиртовая барда — 2—3.
Физико-механические особенности смеси: прочность на сжатие в сыром состоянии — 0,5—0,7 кгс/мм2; влажность — 5—6%.
Толщина облицовочного слоя должна быть 10—30 мм, а подслоя из песчано-глинистой смеси — 40—60 мм. Другой количество опоки заполняется простой наполнительной смесью, а стержни — стержневой опилочной смесью.
Графит. Обширно используемый в чугунолитейном производстве графит есть высокоогнеупорным материалом. Различают графит кристаллический — в виде серебристых чешуек и скрытокри-сталлический (аморфный) — в виде тёмного порошка.
краски и Припылы. При формовке по сырому поверхности форм покрывают разными припылами (серебристым графитом, сланцем, цементом и др.). Для улучшения поверхностной прочности формы наровне с припылом используют опрыскивание поверхностей сульфитно-спиртовой бардой (плотностью 1,1) либо патокой (плотностью 1,28).
Для стержней и покрытия форм по сухому применяют натирки и краски. В состав их входят противопригарные материалы (аморфный графит, пылевидный кварц, тальк, молотый кокс и др.) и связующие вещества (бентонитовая глина, сульфитная барда, патока и Др.) Для предохранения красок от брожения в них вводят формалин.
Натирочные пасты, замазка и клей. Натирочные пасты используют в тех случаях, в то время, когда образуемые стержнями полости в будущем не подвергаются механической обработке и требуют громадной точности чистоты и размеров поверхности. Для очень важных стержней для чугунных отливок применяют пасты следующего состава: серебристый графит — 1 часть; аморфный графит — 1 часть; сульфитно-спиртовая барда -— до получения однородной пасты в виде густой сметаны.
Стержневые клеи помогают для ремонта и склеивания стержней. Сульфитный клей складывается из 5 частей сульфитно-спиртовой барды, 5 частей формовочной частей и 2 глины воды. Клей наносят ровным слоем на склеиваемые поверхности половинок стержней.
При спаривании больших и средних стержней швы заделывают особыми замазками, в состав которых входят, в %:
небольшой кварцевый песок — 60, формовочная глина — 25 и чёрный графит — 15.
5. Фундаментальные особенности формовочных смесей и материалов
смеси и Формовочные материалы, из которых изготовляют стержни и литейные формы, должны владеть определенными особенностями, снабжающими получение отличных форм, отливок и стержней.
Влажность воздействует на все свойства формовочных смесей и в основном на газопроницаемость, текучесть и прочность. Пониженная влажность повышает осыпаемость смеси и затрудняет формовку, а повышенная снижает прочность всырую, увеличивает прилипаемость смеси к модели и снижает газопроницаемость, благодаря чего появляется опасность образования вскипа отливки.
Газопроницаемость — крайне важное свойство формовочных смесей и материалов. Низкая газопроницаемость смесей возможно обстоятельством образования газовых раковин в отливках. Газопроницаемость зависит от формы зерен, однородности зерновых составляющих смеси, от содержания в ней ряда и глинистых веществ вторых обстоятельств.
Для увеличения газопроницаемости небольшого песка его нужно смешивать с 50—60% большого песка.
Прочность. Недостаточная прочность формовочных смесей ведет к деформации стержней и форм, искажению отливок, приводит к распорам и обвалы. Прочность зависит от влажности смеси, количества глинистой составляющей, степени уплотнения и зернистости песка.
Она регулируется дозировкой глины.
Прочность формовочных смесей в сухом состоянии возрастает с повышением в них влаги и содержания глины. Более большая прочность возможно достигнута при применении особых связующих материалов.
Прочность стержневых смесей зависит от количества и вида используемого связующего и обязана пребывать в определенных пределах.
Твердость характеризует равномерность и степень уплотнения формовочных смесей. Переуплотнение, так же как и недостаточное уплотнение смеси, приводит к дефектам отливок: распоры, вскип, газовые и земляные раковины, пригар и др.
Определение этих и других особенностей формовочных смесей и материалов производится в цеховых лабораториях.
6. Формовочные смеси
В литейном производстве громаднейшее использование имеют песчано-глинистые смеси, каковые классифицируются по методу формовки и по роду сплава, заливаемого в формы.
Смеси разделяются на единые облицовочные и наполнительные. Единой именуют смесь, применяемую для набивки всей формы (по большей части при машинной формовке). Облицовочными смесями оформляют лишь ту часть формы, которая соприкасается с жидким сплавом.
Наполнительную смесь наносят на слой облицовочной, ею заполняют и другую часть формы.
По состоянию формы перед заливкой различают смеси для формовки по сырому и по сухому. По роду сплава, заливаемого в формы, различают формовочные смеси для чугунных, металлических и цветных отливок.
Состав смеси для чугунного литья зависит от массы отливки, технологии изготовления и толщины стенок формы.
Для металлических отливок формовочные смеси должны иметь более газопроницаемость и высокую огнеупорность, чем смеси для чугунного литья.
Для форм цветных отливок смогут использоваться смеси со намного более низкой огнеупорностью, чем у смесей для чугунного и металлического литья.
Для увеличения чистоты поверхности отливок из сплавов на бронзовой базе в состав формовочной смеси вводят глинистые пески класса П. Фтористая присадка, вводимая в формовочную смесь при литье из магниевых сплавов, позволяет избежать окисления сплава в ходе затвердевания и заливки отливки. Она возможно заменена борной кислотой либо серным цветом.
7. Быстроотверждающиеся, химически отверждающиеся и самоотверждающиеся пластичные и жидкие смеси
Наровне с простыми песчано-глинистыми взяли распространение созданные у нас формовочные смеси с особенными особенностями.
Быстроотверждающиеся смеси.
Связующим материалом в них кроме этого есть жидкое стекло. Но процесс отверждения осуществляется не за счет продувки углекислым газом, а под действием добавки смесь отвердителя — шлака феррохромового производства. Живучесть пластичной смеси в большинстве случаев равна 20— 25 мин, исходя из этого ее приготовляют в два этапа: главную жидко-стекольную смесь изготовляют в смесеприготовительном отделении, а ввод в нее шлака, просеянного через сито с ячейками 0,5 мм, создают конкретно на участке формовки с перемешиванием в шнековом смесителе.
Облицовочную смесь наносят на модель слоем толщиной 50 мм и более, в зависимости от толщины и габаритов стены отливки. Другой количество опоки заполняют оборотной смесью. Длительность выдержки больших форм — не меньше 1 ч. По окончании извлечения модели форму окрашивают самовысыхающей огнеупорной или простой водной краской.
В последнем случае используют поверхностную подсушку.
Жидкие самоотверждающиеся смеси (ЖСС) отличаются от пластичных тем, что в их состав вводятся поверхностно-активные вещества (ПАВ), каковые при перемешивании смеси образуют на границах зерен пену. Пузырьки данной пены снижают силы трения между зернами песка, что придает смеси жидкоподвижность (текучесть). В качестве поверхностно-активного вещества значительно чаще применяют детергент коммунистический рафинированный (ДС-РАС).
ЖСС используют при изготовлении больших стержней и отливок, причем в отличие от всех смесей их «заливают«» в стержневые ящики и опоки. Время сохранения смесью текучести в большинстве случаев образовывает 9—10 мин, за который она должна быть использована. Установка для изготовление ЖСС размещается конкретно на формовочных либо стержневых участках.
Производительность установок —до 30 т/ч.
8. Стержневые смеси
9. Разработка изготовление формовочных стержневых смесей
Технологический процесс изготовление формовочных и стержневых смесей складывается из трех этапов: подготовки свежих материа-н» подготовки отработанных изготовления и смесей смесей.
Подготовка свежих материалов содержится в их сушке, просеивании и дроблении.
глины и Сушка песка производится в барабанных сушилах производительностью от 3,2 до 29,2 т/ч для песка и 0,9—8 т/ч для глины, а также в установках для охлаждения и сушки песка в кипящем’слое производительностью 3—10 т/ч.
Для дробления и сухой комьев глины и измельчения песка, угля, комьев отработанной смеси, сухих бракованных стержней используют размалывающие бегуны, валковые дробилки, шаровые мельницы мокрого измельчения угля.
Просеивание формовочных материалов перед потреблением реализовывают в мобильных землесеялках, а также в вибрационных и полигональных ситах производительностью от 5 до 125 т/ч и через плоские сита производительностью 50 т/ч.
Подотовка отработанной смеси содержится в магнитной сепарации ее для извлечения железных включений. Смеси, используемые при пескометной формовке, подвергаются двойной сепарации.
Приготовление смесей. Технологический процесс изготовление формовочных смесей складывается из дозирования сухих составляющих и загрузки их в бегуны в следующей последовательности: оборотная смесь+песок+глина в порошке либо в виде эмульсии – каменный уголь (для чугунных отливок, формуемых по сырому) либо опилки (для формовки по сухому); по окончании предварительного перемешивания добавляются жидкие компоненты.
Для смешивания составляющих используют бегуны периодического действия с вертикально вращающимися катками либо центробежные с горизонтально вращающимися катками.
В литейных цехах серийного и массового производства создаются центральные смесеприготовительные отделения, оснащенные высокопроизводительным современным оборудованием и разветвленной транспортной совокупностью. В некоторых из них комплексно механизировано и автоматизировано управление всеми операциями по приготовлению смесей.
10. Регенерация отработанных формовочных и стержневых смесей
Широкое внедрение в литейном производстве особых смесей, приготовляемых из свежих кварцевых песков, и ежегодный прирост производства отливок ведет к систематическому увеличению расхода кварцевых песков, природные ресурсы которых небезграничны. В целях сокращения расхода их нужно частично заменять регенерированными (восстановленными) песками из отработанных смесей, на данный момент вывозимых в отвал.
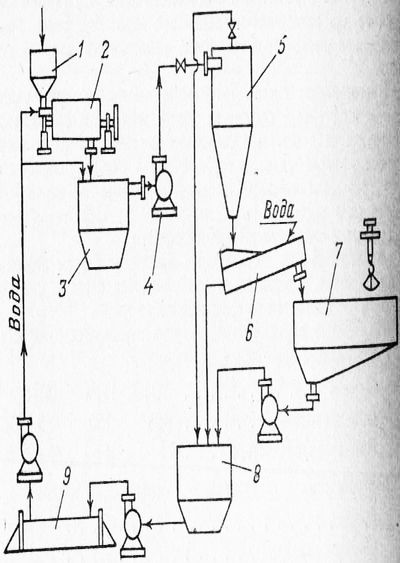
Рис. 1. Установка для регенерации отработанных смесей.
Пятилетний стаж работы установки продемонстрировал, что приобретаемый регенерат есть полноценным заменителем свежего кварцевого песка и возможно использован для изготовление формовочных и стержневых смесей.