Изготовление керамических форм
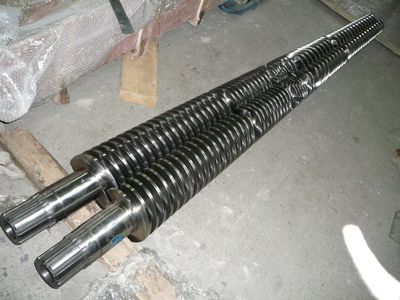
Как уже было указано, для изготовления форм по постоянным моделям применяют жидкоподвижную формовочную смесь. Для ее изготовления можно использовать те же огнеупорные материалы, что и для изготовления форм по выплавляемым моделям. К этим материалам предъявляются те же требования по огнеупорности, тепловому расширению и химической нейтральности по отношению к заливаемому металлу.
В последнее время применяют также синтетические (плавленые и дробленые) огнеупорные материалы, например циркон, муллит, оксиь циркония AZ-5 (48% AlaOs 15% Si02, 0,1% Fe203, 0,2% ТЮ2, 35% Zr02, 1,4% RaO, 0,3% остальные элементы) и хромовую руду. Чаще используют циркон или его смеси с молохитом (цирконовый и молохитовый пески).
В качестве жидкого связующего (по способу Шоу) применяют с самого начала гидролизованный алкоксиполисилоксан. Реже используют другие связующие, например водный раствор силиката натрия с катализатором — частично дегидратизированным сульфатом кальция или соединения титана —тетрабетахлор-этоксид титана с катализатором —дихтаноламином. Наилучшим и широко применяемым связующим остается гидролизованный этоксиполисилоксан.
Для Уникаст-процесса помимо этил-силикатов применяют также гидрозоль кремнезема и фосфатные связующие. Катализатором этилсиликатных связующих и гидрозолей кремнезема служат вещества с рН7 (амины, основные карбонаты магния, кислый карбонат натрия и т. п.).
Суспензии приготовляют смешиванием огнеупорного материала и жидкого связующего. Гелеобразующие катализаторы вводят в смесь непосредственно перед заливкой суспензии в модельную оснастку.
Изготовление форм по Шоу-процессу механизировано. Формы изготовляют запрессовыванием (впрыскиванием) суспензии в модельную оснастку. Чтобы обеспечить высокое качество форм и избежать дефектов при их изготовлении, применяют два типа суспензий.
Однако суспензия состоит из гидролизован-ного раствора этилсиликата и огнеупорного твердого наполнителя с соответствующей зернистостью; другая содержит полярный органический растворитель, тот же огнеупорный материал и геле-образующий агент. Обе суспензии смешивают непосредственно перед загрузкой в специальную машину типа шприц-машины.
Так, например, согласно французскому патенту [14] одна суспензия содержит циркон и гидролизованный этилсиликат 40, другая — циркон, спирт (изопропанол) и водный раствор аммониевого карбоната в качестве катализатора. Обе суспензии смешивают в шаровой мельнице.
При механизированном изготовлении форм по Шоу-процессу поступают следующим образом: обе суспензии приготовляют в двух самостоятельных смесителях. По мере необходимости обе суспензии смешивают и передают или к ручному формовочному станку, или на автомат для изготовления форм и смесь суспензий впрыскивают в формы. Если форма имеет исключительно сложную форму, то перед отверждением суспензию в форме вакуумируют, чтобы удалить из нее газовые включения.
После отверждения суспензии форма снимается с модели на специальном пневмо-гидравлическом устройстве. Из формы выделяют пары спирта, которые поджигают. Наружная поверхность формы быстро нагревается и окончательно отверждается.
Интенсивная сушка от теплоты сгорающих паров спирта приводит к растрескиванию всей формы. Сетка трещин очень тонкая. При этом не происходит деформации и усадки форм.
Внутри форма может иметь большие трещины, которые не только не являются пороками, а, наоборот, повышают газопроницаемость формы.
Способ быстрого удаления спирта из поверхностных слоев формы защищен рядом патентов. Например, в английском патенте для быстрого удаления спирта из формы рекомендуется использовать нагрев инфракрасными лучами. Сетка мелких трещин, которыми покрыты наружные слои формы, способствует получению крупных отливок с качественной поверхностью и без трещин..
Форма с микротрещинами очень податлива и во время затвердевания отливки не препятствует усадке металла, и в отливке не возникают большие напряжения. Для выжигания спирта из мелких форм применяют горелки, а большие формы обжигают в печи. После охлаждения формы подготовляют к заливке.
При Шоу-процессе используют четыре типа форм: цельно-керамические (моноформы), облицованные (двухслойные формы), оболочковые и оболочковые облицованные формы.
Цельнокерамические формы, изготовление которых уже было ранее описано, используют только для мелких отливок. Применение таких форм для крупных отливок сдерживается большим расходом дорогостоящих формовочных материалов.
Облицованные формы используют для экономии дорогостоящих формовочных материалов. Тонкий облицовочный слой, непосредственно соприкасающийся с металлом, изготовляют из высококачественных огнеупоров со связующими — гидролизо-ванным раствором этилсиликата. Основную (большую по массе) часть формы составляет наполнительная смесь шамота и жидкого стекла, отверждаемого углекислым газом.
Изготовление облицованных форм механизировано. На встряхивающем столе на промежуточной модели уплотняется шамотная смесь на жидком стекле. Полученная форма транспортируется на позицию продувки углекислым газом, где она отверждается за 15 с. Затем пневмогидравлическим устройством извлекается форма, с модельной оснастки снимается промежуточная модель, и форма вновь устанавливается на модельную оснастку.
Так как промежуточная модель больше основной модели, то между ней и формой образуется зазор. В образовавшийся зазор запрессовывается из шприц-машины суспензия. Для изготовления облицованных керамических форм расход формовочных материалов в 10 раз меньше, чем при изготовлении цельнокерамических форм.
Оболочковые формы изготовляют из суспензии, которую заливают или впрыскивают в зазор между собственно моделью и промежуточной моделью, размер которого определяет толщину оболочки. Такие оболочки можно применять для отливок массой не более 9 кг.
Облицованные оболочковые формы получают запрессовкой или заливкой формовочной массой в зазор между опорным слоем и собственной моделью. Такие формы используют для изготовления большого числа одинаковых отливок. Опорный слой, который только приблизительно повторяет форму отливки, изготовляют из чугуна или из другого дешевого материала.
Механизация изготовления форм, удешевление форм за счет введения регенерации формовочной массы расширили возможности этого способа. Его используют для получения не только литых штампов, но и многих других отливок: формообразующих деталей для прессования пластмасс, металлических форм и пресс-форм для литья под давлением, отливок авиационной, автомобильной и электротехнической промышленности, деталей режущего инструмента.
Способ Уникаст отличается от Шоу-процесса операцией отверждения формы. При Шоу-процессе гелеобразование связующего резко прекращают дегидратационным нагревом формы (поджигают пары спирта, выделяющиеся из формы). В Уникаст-процессе гелеобразование связующего ведут медленно, скорость его регулируется химическим взаимодействием между связующим и раствором гелеобразования. Для этого формы с тонкими стенками обрызгивают раствором гелеобразователя.
Для массивных стенок требуется более активная химическая проработка, и поэтому такие формы погружают в раствор гелеобразователя.
Торможение процессов отверждения формы, т. е. мягкое нарастание прочности предупреждает образование грубых трещин в керамике и обеспечивает хорошую поверхностную прочность (малоосыпаемая форма). Процессы, ведущие к гелеобразо-ванию, продолжаются и в сформировавшемся геле. Это было доказано вискозиметрическими исследованиями изменения консистенции и фотометрическими замерами прозрачности.
Конденсационные процессы связаны с увеличением объема как в золях, так и в гелях, и их можно исследовать дилатометоически. Форму можно сушить обычным способом, например, при 260 °С в сушиле.
Процесс запатентован фирмой Unicast Development Corporation (Нью-Йорк) (точный состав стабилизирующего раствора не опубликован). В Уникаст-процессе используется гелеобразующий катализатор, который обеспечивает затвердевание формы за 2—4 мин.
При изготовлении исключительно точных (с качественной поверхностью) внутренних полостей, пазов и отверстий применяют песчаные формы, в которые вставляют стержни, изготовленные Уникаст-процессом.
Этим способом можно получать отливки массой от 28 до 7000 кг. Верхнего предела по массе отливок практически не существует. По литературным данным, в 1960 г. в Японии фирма Toyo-KoGyo изготовила Шоу-процессом матрицу массой 2823 кг.
Минимальная толщина стенок малых размеров у отливок из стали, серого и высокопрочного чугуна 1,6 мм. Шероховатость поверхности в пределах 2—3 мкм.
Допуск на длину 75 мм в среднем ±0,03 мм/см, на длину от 75 до 150 мм в среднем ±0,05 мм/см. У крупных и массивных отливок (массой 226—362 кг) достигается точность ±0,1 мм/см. Эти данные приводит фирма Awnet-Shaw в своем проспекте.
Они соответствуют допускам на размеры, достигаемым способом литья по выплавляемым моделям на отливках точных геометрических форм.
На отливках с профилированными участками достигаемые отклонения, измеренные на равных длинах, но в разных местах отливок, отличаются друг от друга; это является следствием общей деформации отливки. Так, например, согласно данным работы [24] на отливке «пуансон» на длине 811 мм были определены отклонения в пределах от 0 до 1 мм; в других частях отливок на длине от 800 до 850 мм отклонения колебались от 0.0 до ±0,5 мм. На отливках «матрица» 121 J на длине 1180 мм отклонения составили +0,4 до 1,5 мм; на длине 2067 мм отклонение + 1,2 мм, а на длине 860 мм отклонение +0,6 мм.
Из опыта завода ZPS, г. Готвальдов (ЧССР) размерные отклонения колебались на литых формах для прессования резиновой обуви в следующих пределах: на длине 350 мм от —0,2 до —1,0 мм; на другой части отливки были отклонения от +0,2 до +1,7 мм, а на длине 358 мм, также в другой части отливки, отклонения составили от —0,2 до —0,5 мм. Отливка была выполнена по постоянной модели в облицованной форме.
Модельная масса состояла из цирконового порошка (Zirkosil 200) и молохитового песка (30/80); в качестве жидкого связующего использовали ги-дролизованный этилсиликат (NT40), в качестве гелеобразующего катализатора — циклогексиламин. Наполнительная смесь состояла из жидкого стекла и искусственного корунда Вк 36; отвер-дитель —углекислый газ.
Данные литературных источников о способе Уникаст различны. В проспекте фирмы Unicast Development Corporation сообщается, что точность при этом способе такая же, как при литье по выплавляемым моделям.
Описанный способ изготовления облицованных форм из двух смесей по постоянной модели достаточно экономичен, обеспечивает короткий интервал гелеобразования, сокращение общего производственного цикла и отсутствие осаждения грубых частиц огнеупорного материала из суспензии. Такой же результат достигается при использовании более медленно действующих гелеоб-разующих реактивов, таких, как основной карбонат магния, и при комбинации двух типов огнеупорного материала в формовочной смеси — мелких частиц с наибольшей удельной плотностью и крупных частиц с наименьшей удельной плотностью.
Литьем в керамические формы по постоянной модели можно изготовлять отливки практически из всех металлов и сплавов (корррозионно-стойких сталей, инструментальных и высокоуглеродистых сталей, серого и белого чугунов, медных, магниевых и алюминиевых сплавов, урана и металлов с высокой реакционной способностью).