Концевые меры длины, калибры и шаблоны
Наровне с многомерными измерительными инструментами (штангенциркули, Микрометры и др.), которыми измеряют любой размер в пределах крайних делений шкалы инструмента, используют так именуемые одномерные инструменты для проверки только одного определенного размера, взаимного расположения и форм поверхностей подробностей. К ним относятся калибры, щупы и шаблоны.
Калибры — бесшкальные измерительные инструменты, предназначенные для проверки определенных размеров обрабатываемых подробностей. При помощи калибров возможно установить пределы внутренних диаметров и отклонения наружных, длины и высоты подробностей, расстояния между центрами отверстий и т. д. Калибры определяют не числовое значение измеряемых размеров, а годность подробности, т. е. правильность ее настоящих размеров, ограниченных предельными отклонениями. Калибры разделяются на обычные и предельные.
К обычным калибрам относятся такие калибры, у которых измерительный размер равен заданному номинальному размеру подробности. Номинальными размерами предельных калибров являются предельные размеры контролируемой подробности, следовательно, разность размеров проходного и непроходного предельного калибров равна допуску подробности, контролируемой данным калибром.
В современном машиностроении, в большинстве случаев, размер назначается с двумя предельными отклонениями, и исходя из этого диагностику размеров подробностей создают не обычными, а предельными калибрами. Годность контролируемой подробности предельными калибрами определяется характером сопряжения калибра с измеряемыми поверхностями подробности: проходная сторона калибра обязана проходить через контролируемую подробность, а непроходная сторона — не проходит через эту подробность. Измерительное упрочнение, при котором калибр для контроля ровных поверхностей подробностей обязан проходить сопрягаемую поверхность, должно равняться собственному весу калибра, но не меньше 100 г. Температура калибра и детали должна быть однообразной (смогут различаться на 2-3 °С).
Способы проверки калибров для отверстии и валов установлены инструкцией Комитета стандартов № 71-58.
По технологическому назначению различаются:
1) рабочие калибры, предназначенные для контроля подробностей конкретно в ходе их изготовления;
2) калибры для проверки подробностей контролерами отдела технического контроля (ОТК);
3) приемные калибры, употребляемые клиентом для контроля изделий;
4) контрольные калибры (либо контркалибры), используемые для приёмных и проверки рабочих калибров.
Различия этих калибров состоят только в их размерах по отношению к полю допуска контролируемого размера подробности.
При маркировке калибров установлены следующие условные обозначения;
Р-ПР — рабочий калибр, проходная сторона;
Р-НЕ — рабочий калибр, непроходная сторона;
П-ПР — приемный калибр, проходная сторона;
П-НЕ — приемный калибр, непроходная сторона;
К-ПР — контрольный калибр для проходной стороны новых рабочих калибров;
К-НЕ — контрольный калибр для непроходной стороны;
К-И — контрольный калибр для проверки износа проходной стороны рабочих скоб;
К-П — контрольный калибр для перевода частично изношенных рабочих проходных калибров в приемные.
Кроме условного обозначения калибра на нем маркируются обозначение посадки и номинальный размер и класса точности изделия, для которого предназначается этот калибр, числовые размеры предельных отклонений этого изделия (в мм) и товарный символ предприятия-изготовителя. К примеру: в случае если на калибре-пробке имеется маркировка П-ПР 60А3, это указывает, что этот проходной приемный калибр рекомендован для контроля отверстий диаметром 60 мм с полем допуска на А3.
Маркировка Р-ПР 080 Ш3 свидетельствует, что это рабочий проходной калибр для проверки вала диаметром 80 мм широкоходовой посадки 3-го класса точности.
Различают калибры для контроля ровных цилиндрических поверхностей (валов и отверстий), ровных конических поверхностей, линейных размеров, резьб, шли-цевых сопряжений, профильных контуров и для контроля размещения поверхностей.
Для контроля диаметров отверстий используют калибры-пробки с полной и неполной цилиндрической поверхностью, и нутромеры сферические, воображающие собой стержни со сферическими поверхностями. Номинальным, размером проходной стороны калибра-пробки ПР есть мельчайший предельный размер отверстия, а непроходной стороны НЕ — громаднейший предельный размер отверстия.
При контроле проходная сторона ПР пробки обязана проходить в отверстие под легким упрочнением, а непроходная сторона НЕ не должна входить в отверстие. Проходную часть пробки делают дольше непроходной стороны.
Так, для отверстия 30+0’023 одна сторона пробки (удлиненная, рис. 1, а) будет иметь номинальный размер 30 мм и именоваться проходной ПР, а вторая сторона пробки (укороченная) будет иметь номинальный размер громаднейшего отверстия, т. е. 30,023 мм. Эта сторона пробки именуется непроходной и обозначается НЕ, она может входить лишь в подробность, имеющую завышенный размер отверстия.
Такие подробности бракуются.
Пробки предельные двусторонние с цилиндрическими вставками имеют пределы контролируемых размеров от 0,1 до 3 мм (рис. 33,6). В рукоятку этих пробок, имеющих накатку, устанавливают с двух сторон цилиндрические вставки и закрепляют карбинольным клеем.
Пробки со вставками с конусным хвостовиком (рис. 33, в) бывают односторонние и двусторонние, проходные и непроходные. Пределы контролируемых размеров этих пробок от 1 до 50 мм.
В средней части двусторонние пробки имеют поперечное отверстие, через которое возможно удалить клином одну из вставок.
Пробки односторонние со вставками, имеющими конусный хвостовик (рис. 1,г), выпускаются с пределами измерения от 6 до 50 мм. Проходная и непроходная части расположены друг за другом и поделены между собой узкой проточкой.
Пробки с насадками (рис. 1, д) изготовляются двусторонние, проходные и непроходные. Рукоятки у этих пробок имеют с двух сторон цапфы, на каковые надевают насадки и крепят их винтом.
Выпускаются пробки с насадками для контроля размеров от 30 до 100 мм.
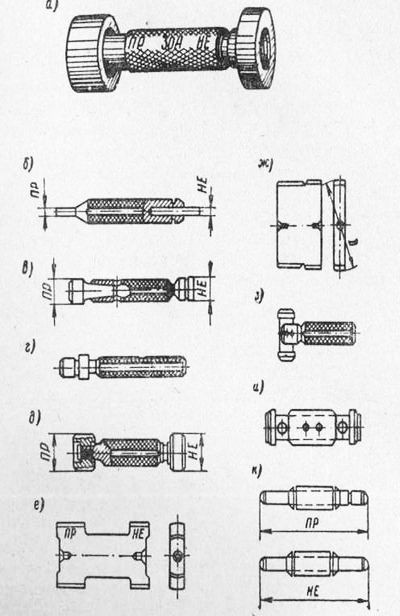
Рис. 1. Калибры-пробки для проверки диаметров отверстий.
Пробки листовые двусторонние (рис. 1, е) изготовляются для контроля размеров от 18 до 100 мм, а пробки листовые односторонние (рис. 1,ж)—для размеров от 50 до 360 мм.
Материалом для таких пробок помогает листовая сталь толщиной 6—12 мм.
Пробки неполные с рукоятками (рис. 1,з) бывают проходные и непроходные для контроля размеров от 50 до 150 мм. Пробки неполные с накладками (рис. 2, и) производят проходными и непроходными с размерами от 150 до 360 мм. Измерительная часть этих пробок прикрепляется к рукоятке винтами или карбинольным клеем.
Измерительные части изготовляют раздельно для проходного и непроходного размеров.
Рис. 2. Калибры-скобы для проверки диаметров валов
Для проверки диаметров вала применяют калибры – скобы разных конструкций (рис. 2). Независимо от конструкций скоба должна иметь проходную и непроходную измерительные поверхности.
Проходная часть ПР обязана вольно обнаружить на вал, поскольку она изготовляется по громаднейшему предельному размеру. Непроходная часть НЕ выполняется по мельчайшему предельному размеру вала, исходя из этого она на вал не находит.
Скобы листовые двусторонние (рис. 2,а) изготовляют для контроля размеров от 1 до 50 мм. Скобы листовые прямоугольные односторонние (рис.
2,б) используют для контроля размеров от 1 до 70 мм, а скобы листовые круглые односторонние (рис. 2, е) — для размеров от 1 до 180 мм. ‘
У двусторонних скоб проходная и непроходная части расположены на противоположных сторонах скобы, а у односторонних скоб—на одной стороне и разделяются канавкой. Длину непроходной части делают меньше, чем у проходной.
Производят кроме этого скобы, штампованные горячим методом: двусторонние для контроля размеров от 3 до 170 мм, односторонние для размеров от 3 до 50 мм и с ручками — для размеров от 50 до 170 мм. Штампованные скобы имеют ребра жесткости и более широкие измерительные губки, что повышает их срок и жёсткость эксплуатации. Скобы литые производят со вставными губками односторонние для контроля размеров от 100 до 325 мм.
Для облегчения веса в них делают отверстия.
Скобы регулируемые устроены так, что их возможно переналаживать на другой размер либо же восстанавливать по мере износа рабочие размеры. Так возрастает срок эксплуатации инструмента.
Для проверки настоящего размера скоб используют контрольные калибры. Для пределов измерения от 1 до 18 мм производят пробки контрольные со вставками, имеющими конусный хвостовик, для размеров от 18 до 100 мм — шайбы полные и для размеров от 100 до 325 мм — шайбы неполные. размеры и Конструкция ровных калибров-пробок диаметром от 1 до 360 мм приведены в ГОСТах 14807-69 и 14827-69.
Технические требования на ровные нерегулируемые калибры для контроля цилиндрических отверстий диаметром от 0,1 до 360 мм и валов диаметром от 1 до 360 мм указаны в ГОСТе 2015-69, а на скобы ровные регулируемые для контроля валов диаметром до 340 мм —в ГОСТе 2216-68.
Для проверки конических поверхностей подробностей используют конусные калибры, обычные и предельные. Их делают с контрольными рисками и уступами. Проверка конических поверхностей производится по осевому перемещению калибра довольно контролируемой подробности. В ходе проверки замечают, находится ли торец подробности в пределах уступа либо рисок (рис.
35,а, б, в, г).
Диагностику внутренней резьбы создают предельными резьбовыми пробками, а наружной — нерегулируемыми (твёрдыми) и регулируемыми предельными резьбовыми кольцами, и резьбовыми скобами. Проверка содержится в свинчивании резьбового калибра с контролируемой подробностью. Так, проходная резьбовая пробка обязана вольно ввинчиваться в гайку, а проходное резьбовое кольцо должно вольно навинчиваться на болт.
Рис. 3. Калибры для проверки конических поверхностей (а, б. в, г) и резьбы (д, е, ж)
Непроходные части резьбовых калибров не должны ввинчиваться в гайку либо навинчиваться на болт.
Проходная сторона калибра-пробки имеет долгую полный профиль и резьбовую часть резьбы, а непроходная— укороченную (3—3,5 витка) и ровную цилиндрическую направляющую (рис. 3, д).
Для проверки наружных резьб применяют твёрдые и регулируемые кольца. Проходные кольца выполняются с резьбой полного профиля по всей высоте кольца, а у непроходных резьба укороченного профиля в пределах 2—2,5 витка (рис. 3,е, ж).
Наружные резьбы проверяются кроме этого скобами разных конструкций.
Шаблоны. Для проверки контуров подробностей сложного профиля обширно применяют профильные калибры (шаблоны) (рис. 3,а). Профильный шаблон представляет собой как бы элемент сопрягаемой подробности. Проверка производится методом прикладывания шаблона к контролируемому контуру подробности. Результаты проверки определяются на глаз (визуально) по величине просвета либо по совмещению шаблона и контуров детали.
При проверке глухих мест, где нереально воспользоваться способом просвета, пользуются способом проверки на краску. Форма шаблона повторяет форму подробности, из этого понятно индивидуальный характер и большое разнообразие производства таких инструментов. Шаблонами осуществляют контроль профили зубьев шестеренок, профили кулачков муфт и кулачковых валиков, гнезда сальниковых уплотнений, радиусы закруглений подробностей, профили матриц и пуансонов штампов, углы заточки режущего инструмента и т. п. Шаблоны изготовляют из узкой листовой либо полосовой стали толщиной от 1,5 до 3 мм.
Не считая особых шаблонов (личного назначения) в производстве применяют еще и нормализованные шаблоны — радиусные и резьбовые.
Радиусные шаблоны являются металлические пластинки с выпуклыми и вогнутыми по радиусу финишами и предназначены для определения радиусов закруглений (галтелей) на разных подробностях. Они комплектуются в три комплекта: с радиусом выпуклых и вогнутых поверхностей от 1 до 25 мм. В комплекте № 1 девять выпуклых и девять вогнутых шаблонов с радиусами: 1; 1,2; 1,6; 2; 2,5; 3; 4; 5 и 6 мм.
В комплекте № 2 шесть шаблонов вогнутых и шесть шаблонов выпуклых с радиусами: 8; 10; 12; 16; 20 и 25 мм. В комплекте № 3 по двенадцать выпуклых и вогнутых шаблонов с радиусами: 7; 8; 9; 10; 11; 12; 14; 16; 18; 20; 22 и 25 мм.
Шаблоны в комплектах находятся в-порядке нарастания измерительного радиуса. Толщина пластин во всех комплектах 0,6 мм, а ширина в комплекте № 1 — 12 мм, а в комплектах № 2 и 3 — 20 мм. Проверка
Рис. 4. Примеры проверки подробностей посредством шаблонов, щупов и резьбомеров: а, б—профиля; в, г—шага резьбы; д, е—зазора.
радиуса закругления подробности производится прикладыванием шаблона к контролируемому элементу и определением отклонения на просвет.
Резьбовые шаблоны являются наборомузких металлических пластинок толщиной 1 мм с нанесенными на них правильными профилями стандартных резьб. Они используются в условиях ремонта механизмов и автомобилей, при экспериментальной работе, и при сортировке изделий с резьбой с целью основных элементов и определения типа резьбы.
Шаблоны комплектуются в два’комплекта: для метрической резьбы с углом профиля 60° и для дюймовой’ резьбы с углом профиля 55°. Комплект № 1 для определения шага метрической резьбы складывается из 20 резьбовых пластин с шагом: 0,4; 0,45; 0,5; 0,6; 0,7; 0,75; 0,8; 1,0; 1,25; 1,5; 1,75; 2,0; 2,5; 3,0; 3,5; 4,0; 4,5; 5,0; 5,5 и 6 мм.
Комплект № 2 для определения шага дюймовой и трубной резьб складывается из 17 резьбовых шаблонов с числом ниток на один дюйм: 28; 24; 20; 19; 18; 16; 14; 12; 11; 10; 9; 8; 7; 6; 5. На каждой пластине указаны величина шага либо количество ниток на 1”, а на обойме обозначена резьба — метрическая (60°) либо дюймовая (55°), т. е. М60° либо Д55°. Из комплекта резьбовых шаблонов нужно выбрать тот, что наилучшим образом сопрягается с профилем измеряемой резьбы.
При наложении резьбового шаблона на резьбу направляться применять как возможно большее количество витков с целью увеличения точности измерения (рис. 36,в, г). Зная шаг резьбы и наружный диаметр либо количество ниток на 1”, возможно по справочнику выяснить номинальный размер и наименование резьбы.
Щупы используют для определения величины зазора между сопрягаемыми поверхностями. Они являются наборомузких металлических пластин с параллельными измерительными поверхностями (рис. 36, д). Щупы разной толщины собраны на неспециализированной оси между двумя более толстыми пластинками, делающими роль футляра. Щупы производят 1-го и 2-го классов точности с толщиной пластин от 0,02 до 1 мм. Щупы длиной 100 мм изготовляют отдельными пластинами и наборами, а щупы длиной 200 мм — отдельными пластинами.
Комплектуются четыре комплекта. В комплекте № 1 девять щупов с толщиной: 0,02; 0,03; 0,04; 0,05; 0,06; 0,07; 0,08; 0,09; 0,1 мм. В комплекте № 2 17 щупов с толщиной: 0,02; 0,03; 0,04; 0,05; 0,06; 0,07; 0,08; 0,09; 0,1; 0,15; 0,2; 0,25; 0,3; 0,35; 0,4; 0,45; 0,5 мм. В комплекте № з десять щупов: 0,55; 0,6; 0,65; 0,7; 0,75; 0,8; 0,85; 0,9; 0,95; 1,0 мм.
В комплекте № 4 десять пластин с толщиной: 0,1; 0,2; 0,3; 0,4; 0,5; 0,6; 0,7; 0,8; 0,9; 1 мм.
Рис. 5. Плоскопараллельные концевые мерные плитки (а, б, в. г) и принадлежности к ним (д); примеры применения плиток (е, ж).
При измерении зазоров пластинки комплекта одну за второй с опаской проталкивают в щель между сопрягаемыми подробностями , пока одна из них хорошо не войдет в измеряемый зазор. Толщина щупа укажет величину измеряемого зазора. Во многих случаях пластинки комплекта складывают одну с другой в разных комбинациях для получения нужных размеров.
Пользоваться щупами, в особенности узкими, необходимо крайне осторожно, поскольку они смогут согнуться.
Плоскопараллельные концевые меры длины, сокращенно именуемые плитками, активно используются в машиностроении для правильных измерений. С их помощью создают проверку и градуировку измерительных устройств, инструментов и наладку оборудования, измеряют подробности, создают разметку и т. п.
Плитки являются прямоугольные металлические бруски двух размеров в сечении: 30X9 — для проверки размеров до 10 мм и 35X9 для проверки размеров более чем 10 мм. Характерным свойством плиток есть притираемость их друг к другу измерительными поверхностями.
Свойство притираемости пребывает в том, что совершенно верно обработанные и доведенные измерительные поверхности двух плиток при их соприкосновении под маленьким упрочнением, создаваемым руками, с одновременным зигзагообразным перемещением на протяжении долгого ребра до совмещения плоскостей обеих мер прочно сцепляются между собой. Плитки считаются верно притертыми одна к второй, в случае если посредством маленького упрочнения их не удается разъединить.
К двум притертым плиткам так же притирают третью, четвертую и т. д., составляя так называемый блок требуемого размера, пользуясь которым возможно создавать измерения с точностью до тысячных долей миллиметра. По точности изготовления концевые меры длины (в соответствии с ГОСТу 9038-59) делятся на четыре класса: 0, 1, 2 и 3-й. Самым правильным есть класс 0-й.
Для каждого класса точности установлены допускаемые параллельности плоскостей и отклонения размеров.
Плитки выпускаются размерами от 0,1 до 2000 мм и комплектуются в 15 разных комплектах от 4 плиток в комплекте до 116. ГОСТ 9038-59 предусматривает выпуск плоскопараллельных концевых мер 15 разных комплектов:
В эти комплекты входят плитки, отличающиеся одна от второй соответствующей отличием (градацией) в размерах: 0,001; 0,01; 0,1; 0,5; 1; 10; 25; 50; 100 и 1000 мм.
самоё широкое использование имеет комплект мер, складывающийся из 87 плиток; в данный комплект входят следующие меры:
С целью уменьшения износа плиток к некоторым па-борам прилагаются особые защитные плитки, каковые ставятся по финишам блока.
На данный момент фабрики «Красный» и «Калибр инструментальщик» производят 8 комплектов концевых мер из жёсткого сплава (по ГОСТу 13581-68) с числом плиток в комплекте от 4 до 112. Завод «Красный инструментальщик» комплекты мер из жёсткого сплава производит и по техническим условиям ТУ 2-054-616-68 с градацией через 0,0001 мм, размером от 2 до 2,001 мм (11 плиток).
Для более широкого применения концевых мер к ним прилагают комплекты принадлежностей (по ГОСТу 4119-66). В набор комплекта входят державки, установленные на основании, в каковые возможно помещать боковики и блоки плиток (плоские, радиусные, чертильные и центровые). Боковики притираются к блоку и фиксируются винтом, что позволяет по окончании установки в державке приобретать цельный инструмент, применяемый для правильных измерений: контроля точности показаний микрометра; для измерения диаметра отверстий, других работ и разметки.
При составлении блока концевых мер нужно стремиться применять вероятно меньшее количество плиток. Для этого направляться руководствоваться таковой последовательностью при выборе плиток. Первой берется плитка, содержащая один либо два последних символа пробного значения нужного размера. Следовательно, остаток будет воображать целое число миллиметров с меньшим числом дробных знаков.
Так же выбираются последующие плитки. Пускай требуется, к примеру, подобрать блок плиток, составляющих размер 39,375 мм. Первой берем плитку 1,005 мм (оставшийся размер будет 39,375— —1,005 = 38,37 мм). Второй — плитку 1,37, остаток образовывает: 38,37—1,37 = 37,0 мм.
Третью плитку берем 7 мм, четвёртая и остаток плитка — 30 мм.
Так, блок размером 39,375 мм составлен из четырех плиток: 1,005; 1,37; 7 и 30 мм.
Обращаться с концевыми мерными плитками направляться крайне осторожно и бережно, дабы не повредить их измерительных поверхностей. Перед пользованием плитки нужно промывать авиационным бензином и шепетильно протирать чистой мягкой тканью. По окончании работы с плитками они должны быть кроме этого промыты бензином, смазаны вазелином и уложены в соответствующие гнезда футляра.