Контроль качества сварочных и слесарно-подготовительных работ
Технологический процесс сварочных и слесарно-подготови-тельных работ складывается из последовательности операций, делаемых в определенной последовательности. Типовая разработка применительно к агрегатам, собираемым при сварки слесарной и помощи обработки, складывается из следующих операций: обоюдной подгонки подробностей, подготовки их к соединению, установки подробностей в сборочное положение и одновременной их фиксации в приспособлениях, соединения подробностей, окончательной обработки.
К слесарно-подготовительным работам перед сваркой и прихваткой конструкций относятся снятие и зачистка заусенцев, разметка, правка и эластична для придания подробностям нужного профиля, пригонка подробностей одна к второй для предварительной сборки под сварку и прихватку. По окончании прихватки делают правку и проверку изделий, а по окончании сварки — исправление дефектов и зачистку швов.
Правку сварных конструкций кроме этого делают по окончании термической обработки. Уровень качества изготовления сварных соединений в значительной мере зависит от тщательности подготовки подробностей под сварку и прихватку.
По большей части подготовка подробностей под прихватку содержится в качественной обработке краев (кромок) в местах соединения с соблюдением нужных зазоров по всему сварному контуру, поскольку неравномерный зазор может повести к появлению трещин при сварке. Размещение прихваток должно соответствовать технологическим указаниям.
В соответствии с соотношением толщины и назначением изделий свариваемых подробностей используют разные методы сварки, каковые различаются не только степенью нагрева, но и техникой ведения сварочного процесса.
Не считая сварки в индустрии обширно используют пайку. Методы пайки очень разнообразны и применимы для всех марок углеродистых и легированных сталей, серых и ковких чугунов, жёстких сплавов, его сплавов и вольфрама, алюминия, меди, никеля, свинца, и добропорядочных и редких металлов. Современные способы пайки разделяются на два главных вида: пайка жёсткими припоями (бронзово-цинковыми, серебряными) и пайка мягкими припоями (оловянисто-свинцо-выми).
Для получения паяных соединений хорошего качества нужно правильное соблюдение технических условий и технологии, что по большей части содержится в тщательной подготовке поверхности под пайку, соблюдении нужных температуры и зазоров пайки, применении соответствующих припоев и флюсов.
пайки дефектов и Классификация сварки. Недостатки дуговой и газовой сварки подразделяют на недостатки подготовки й сборки подробностей перед сваркой (небольшой угол скоса, увеличенный либо уменьшенный угол притупления кромок, неодинаковый угол притупления по длине шва, через чур большой иди недостаточный зазор для данной толщины материала, непостоянный зазор по длине шва); недостатки формы шва (неравномерная ширина, излишняя вогнутость, громадная высота, неравномерная высота усиления, неодинаковые высоты катетов валика); внутренние пороки и наружные сварочного шва (подрезы, наплывы, проплавы, прожоги, раковины и свищи, шлаковые включения в переходной зоне и шве; поры в переходной зоне и шве; кратер, трещины, непровар); отклонение размеров изделия; неудовлетворительные механические особенности металла сварного шва (текучести и низкие пределы прочности, небольшой угол загиба, низкая ударная вязкость, небольшой предел выносливости).
Недостатки стыковой сварки: пережог (перегрев), непровар, подгар поверхности подробности; трещины (в основном при сварке конструкционных легированных сталей); смещение свариваемых поверхностей.
Недостатки точечной сварки: пережог, непровар, трещины (при сварке закаливающихся сталей).
Недостатки шовной сварки подобны недостаткам точечной сварки.
Главные недостатки пайки при применении жёстких припоев: непропай (при нехорошей подготовке поверхностей подробностей под пайку — загрязнение кромок и поверхностей металла); пористость в местах соединяемого шва (возможно результатом нехорошего качества присадочного материала и флюсов, и нехорошей подготовки подробностей под пайку); проплавы материала в местах пайки из-за большой температуры пайки; выгорание легирующих элементов, прежде всего цинка (кроме этого из-за большой температуры пайки — данный недостаток ведет к возможности стремительного окисления поверхности швов: его выявляют внешним осмотром по трансформации цвета поверхности металла в зоне шва); заплавленный непропай (зазоры в не-пропаянных местах заполнены расплавленной бурой). Главные недостатки пайки мягкими припоями: непропай, пористость, шероховатый шов.
Внешний вид некоторых недостатков сварки продемонстрирован на рис. 1.
Способы контроля сварных качества и соединений сварки.
В слесарно-сварочных цехах используют предварительный, промежуточный и окончательный контроль.
Предварительным контролем контролируют соответствие чертежу марки материала подробностей, подвергаемых слесарной последующей сварке и обработке. Диагностику делают по маркировке материала.
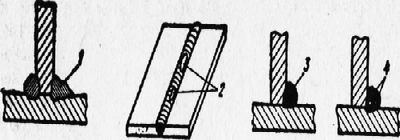
Рис. 1. Кое-какие недостатки сварки: 1 — наплыв; 2 —прожог; 3 — свищ; 4 — поры; h — глубина непровара
Все последующие операции слесарно-подготовительных и сварочных работ подвергают промежуточному контролю по операциям. Контролируют внешний вид подробностей, чистоту опиловки, размеры зазоров для подробностей, подготовляемых к прихватке. Размеры подробностей по чертежу и зазоры осуществляют контроль особыми шаблонами, щупами, универсальным инструментом и линейками.
Принятые контролером подробности направляют на прихватку, по окончании чего снова предъявляют на контроль для проверки: наличия вероятных трещин, прожогов, других дефектов и проплавов в местах прихватки; правильности размещения при-хваточных точек; равномерности зазоров и соответствия величины заданным; тщательной очистки подробностей под сварку.
По окончании приемки прихватки подробности направляют на сварку. Первый сварной узел от партии сварщик предъявляет контролёру и мастеру, каковые при хорошей оценке качества работы дают разрешение на сварку всей партии. На готовых подробностях сварщик ставит личное клеймо, по окончании чего подробности поступают на контроль.
При контроле делают тщательный измерение параметров и внешний осмотр сварных швов. Снова контролируют соответствие марки материала чертежу (по маркировке), наличие клейма сварщика, размеры швов, размеры сваренного узла по чертежу и наличие вероятных недостатков сварки. Узлы, имеющие исправимые недостатки, направляют на исправление по особым руководствам, по окончании чего снова подвергают контролю.
Для систематического наблюдения за качеством сварки производственный и контрольный мастера иногда контролируют прочность сварки на контрольных примерах технологической пробы. По характеру и форме разрушения примера определяют соблюдение режима сварки.
Все последующие операции по окончании сварки (термическая обработка, правка, дробеструйная очистка) кроме этого подвергают контролю, в ходе которого выявляют вероятные недостатки.
испытаниям и Окончательному контролю сварные узлы подвергают по окончании завершения всех сварочных операций по технологическому процессу. На окончательный контроль изделия поступают в неокрашенном виде, по окончании тщательной очистки швов от брызг и шлака.
При контроле изделия подвергают внешнему осмотру для обнаружения внешних недостатков, контролируют размеры по чертежу, отсутствие перекосов, коробления и т. д. Также, в зависимости от указаний, приведенных в технических условиях, изделия подвергают особым видам контроля — просвечиванию рентгеновскими либо у-лучами, опробованиям на плотность сварных швов, магнитному, люминесцентному и вторым видам контроля. Определенный процент сварных узлов (в соответствии с технологии и ТУ) подвергают металлографическому исследованию и механическим испытаниям.
Принятые ОТК изделия поступают в цеха покрытий для окраски либо нанесения какого-либо гальванического покрытия.
Работники ОТК слесарно-сварочного цеха осуществляют контроль кроме этого своевременную диагностику оборудования, приспособлений, инструмента, источников энергии, приборов и измерительной аппаратуры.
Для контроля качества пайки швы должны быть зачищены напильником либо наждачным полотном. Контроль для обнаружения внешних правильности и дефектов пайки по чертежу делают внешним осмотром с применением лупы либо бинокулярного микроскопа. В зависимости от указаний ТУ кое-какие паяные подробности подвергают опробованиям на плотность (непроницаемость) либо особым видам контроля.
Процесс пайки осуществляют контроль пооперационно. Отдельные очень важные операции направляться делать под наблюдением мастера, что предъявляет работу контролеру.
измерениями и Внешним осмотром возможно распознать следующие недостатки поверхности сварных швов: трещины, подрезы, раковины, поры, незаваренные кратеры, неравномерное распределение металла по длине шва, наличие бугров и седловин, несоответствие размеров шва указанным в чертеже. Для осмотра применяют лупу либо бинокулярный микроскоп. Перед осмотром шов очищают от грязи и нагара.
Внешний осмотр в большинстве случаев совмещают с измерением швов особыми шаблонами либо измерительным инструментом.
Травление используют для обнаружения трещин. Местное травление делают 10%-ным водным раствором азотной кислоты; ватный тампон, намоченный в этом растворе, накладывают на поверхность металла, пока она не станет матовой. Реактив не должен попадать на смежные части изделия.
Перед травлением с исследуемого места удаляют защитные покрытия (окраску, лакировку и т. п.) и поверхность зачищают, причем глубина зачистки не должна быть больше допуск на толщину материала.
При контроле сварки делают химический анализ электродов, наплавленного и главного металлов. Анализ электродов и наплавленного металла нужен для оценки прочности, стойкости и пластичности к коррозии наплавленного металла. При вызывающих большие сомнения итогах химического анализа первой пробы выполняют контрольный анализ еще двух проб.
Химический анализ проб делают в соответствии с утвержденными техническими условиями и стандартами.
Металлографические изучения качества сварки пребывают в проверке образцов по излому и в изучении их макро- и микроструктуры. Образцы с целью проведения опробований вырезают из самой подробности либо умелых пластин с таким расчетом, дабы поверхность шлифа включала полное сечение шва, нетронутый главный металл и территорию термического влияния.
Для отчетливого обнаружения отдельных слоев наплавленного металла, границы между наплавленным и главным металлами и территории термического влияния (за которой главный металл не претерпел термического действия) используют травление. Сразу после травления макроструктуру фотографируют. При необходимости на шлифе возможно выяснить твердость по Роквеллу либо Виккерсу.
Изучением макроструктуры возможно установить следующие недостатки сварки: микропоры, микротрещины, раковины, прослойки и шлаковые включения, непровары между наплавленным и главным металлом, выделение карбидов (в аусте-нитных сталях), крупнозернистость, выгорание отдельных элементов и т. п. Изучение макроструктуры имеет особенно серьёзное значение при сварке особых сталей.
Засверловкой возможно распознать непровары, тр.ещины и пористость; наряду с этим применяют электрические, пневматические и ручные дрели либо спиральные сверла с углом заточки 90°. Число сверлений на сварных подробностях установлено техническими условиями. По окончании окончания опробований отверстия в шве, не имеющем недостатков, нужно заварить.
Механическими опробованиями осуществляют контроль уровень качества наплавленного сварных соединений и металла в целом. Механические опробования сварных соединений разделяют на статические (растяжение, определение твердости, загиб) и динамические (на удар, усталость и вибрацию). Опробования выполняют по утвержденным стандартам.
Формы образцов, используемых при опробованиях, кроме этого стандартизованы.
Не считая перечисленных видов механических опробований качества сварки, в производстве выполняют кроме этого опробования на свариваемость, на образование трещин при сварке и вырывание.
Опробование стали на свариваемость пребывает в определении пластичности металла сварного шва либо главного металла, подвергнутого тепловому действию сварочного процесса. Под свариваемостью знают свойство стали при определенных конструктивных и технологических условиях подвергаться действию термического цикла сварки без заметного ухудшения и образования трещин механических особенностей. Наряду с этим, к примеру, испытывают на статический загиб поперечные стыковые швы, тавровые образцы, образцы с надрезом.
Пробу на вырывание берут по большей части для определения качества электродов по особенностям наплавленного металла. Образцы для опробования изготовляют из малоуглеродистой стали с
Для проверки образцов на образование трещин при сварке используют следующие методы- опробований: пробу сваркой внахлестку в твёрдом контуре, пробу стыковой сваркой с твёрдой заделкой швов и др.
Опробование сварных шво° на плотность (непроницаемость) выполняют по окончании устранения недостатков сварки, распознанных внешним осмотром. Нарушение плотности сварных швов возможно следствием непроваров, трещин, газовых и шлаковых включений. Вид опробования на непроницаемость сварных швов обусловливают технические условия на приемку данной подробности.
На практике используют керосиновую пробу, и пневматическое и гидравлическое опробования. Наряду с этим сварной шов с одной стороны окрашивают меловым раствором (мел с водой), а по окончании подсыхания обратную сторону шва обильно смачивают керосином; при наличии недостатков в шве На окрашенной мелом поверхности выступают чёрные пятна.
При пневматическом опробовании сварную подробность заполняют воздухом под давлением, указанным в технических условиях; неплотности шва определяют по пузырькам на поверхности шва, намоченного мыльной водой, либо по пузырькам в воде при погружении в нее изделий (сосудов, резервуаров). При гидравлическом опробовании в изделие заливают жидкость (воду, керосин) либо создают дополнительное гидростатическое давление гидравлическим прессом (недостатки швов выявляются на наружной поверхности в виде капель либо струек воды).
Выполняют кроме этого коррозионные опробования сварных соединений. Коррозия (разъединение) включает все виды физико-химического разрушения металлов, ржавление, разрушение металла растворами кислот, щелочей, солей, окисление при обычных и повышенных температурах и т. п.
Для определения коррозионной стойкости сварных соединений используют разные способы.
Погружают в растворы кислот н по окончании определенного испытательного срока сравнивают коррозию образца и сварного образца из главного металла в исходном состоянии. Коррозионную стойкость оценивают по трансформации массы сварного примера если сравнивать с массой примера из главного металла либо сопоставляют внешним осмотром коррозию наплавленного металла, основного металла и переходной зоны.
Обширно используют кроме этого способы изучений макро- и микроструктуры разных территорий примера, и механические опробования образцов до и по окончании коррозии. Изучение коррозионной стойкости сварных швов, выполненных разными видами сварки, разрешает верно выбрать метод сварки, присадочный и главный металлы.