Контроль поверхностной закалки по макрошлифам
Для травления макрошлифов в практике высокочастотной закалки значительно чаще используются следующие два метода:
1. Травление бронзовой хлорно-аммонийной солью.
Данный реактив четко выявляет глубину закаленного слоя, и макроструктуру исходного материала, к примеру, размещение волокон прокатки. Химическая формула его: CuCl2-2NH4C1-2Н20. Приготовляют реактив, растворяя в воде кристаллы соли до появления интенсивной синей окраски. Рекомендуется на 1 л воды брать около 100 г соли.
Нужно приготовлять реактив перед самым потреблением, а соль сохранять в сухом месте.
Шлифованную на станке и обезжиренную поверхность металла смачивают водой, а после этого раствором соли и выдерживают до появления шероховатого осадка меди. Данный осадок нужно с опаской удалить, протирая шлиф ватой в струе воды. На поверхности металла закаленный слой получает чёрную окраску, а исходный, незакаленный материал темнеет незначительно.
Процесс травления заканчивается высушиванием фильтровальной бумагой либо теплым воздухом. Для долгого сохранения макрошлиф покрывают бесцветным лаком, к примеру, цапоном.
Для получения четкого макрошлифа требуется смачивать реактивом всю поверхность в один момент. Для этого шлиф направляться либо окунуть в раствор, налитый в плоский сосуд, либо бережно лить раствор на шлиф, помещенный над стоком. При громадных габаритах исследуемой подробности это воображает громадные трудности, поскольку требуется либо особая ванна либо помещение с цементным полом, снабженным^сливом.
При травлении легированных сталей либо чугунных изделий удаление меди воображает некое затруднение. Медь реактива так прочно пристает к поверхности, что несложным протиранием ватой удалить ее нереально. Тогда медь смывают не сильный раствором аммиака либо азотной кислоты.
2. Травление 25-процентным либо 10-процентным водным раствором азотной кислоты.
Не смотря на то, что использование азотной кислоты воедно для трудящихся и требует необходимого наличия вытяжной вентиляции, но благодаря простоте получения результатов на чугунах и легированных сталях, и удобству изготовления макрошлифов подробностей больших габаритов в производстве рекомендуется применять этот реактив.
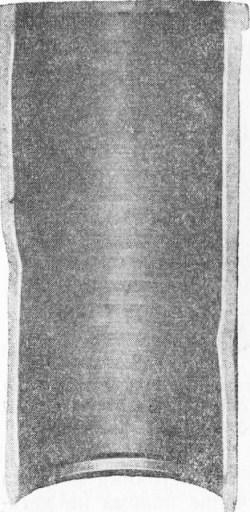
Рис. 1. Излом чугунной гильзы блока цилиндров. Закаленный слой выглядит более ярким.
Макрошлиф, приготовленный посредством одного из рассмотренных реактивов, разрешает распознать, как распределяется по сечению закаленный слой, соответствует ли его глубина заданным условиям. Действительно, эти сведения получаются приближенными, поскольку чёрные участки на макрошлифе соответствуют твердости HR(, = 30 и выше, т. е. на макрошлифе протравливается мартенситный слой вместе с переходной территорией. Исходя из этого довольно часто говорят о «глубине слоя по макро».
В тех случаях, в то время, когда нужно выяснить подлинную глубину слоя по мартенситу, нельзя пользоваться «глубиной слоя по макро», а необходимо отыскать ее по кривой твердости либо микроструктуре. Граница протравленного слоя на макрошлифе не всегда получается резкой. Расплывчатость границы возможно замечать при нагреве подробности на глубину, превышающую прокаливаемость данной марки стали.
Довольно часто за тёмной границей на макрошлифе протравливается узкая белая полоса, более яркая, чем исходная структура. Эта полоса характеризует территорию отпуска, что видится на предварительно улучшенной 1 стали, имеющей твердость, повышенную по сравнению со сталью отожженной. В случае если подробность из таковой стали подвергнуть высокочастотной закалке, то сходу за переходным слоем будет размешаться территория, нагреваемая до температур, превышающих температуру отпуска при улучшении.
В данной территории случится падение твёрдости и дальнейший отпуск до значения, близкого к твердости отожженной стали, выражающиеся на кривой твердости характерным «провалом».
Изготовление макрошлифа есть хорошим средством для проверки конструкции индуктора. В ходе создания конструкции (трансформации ее элементов) создают закалку подробностей и делают последовательность макрошлифов, по которым делают выводы о правильности внесенных конструктивных трансформаций. Но на окончательном этапе при разработке термического и электрического режима, и при контроле подробностей массового производства сведения, приобретаемые благодаря макрошлифу, уже недостаточны, и нужно переходить к более правильному способу — микроисследованию.
По макрошлифу возможно ориентировочно выяснить места перегревов, каковые при травлении становятся более тёмными. Макрошлиф оказывает помощь снимать кривую твердости, поскольку на нем виден район, где твердость направляться измерять особенно детально.
Рис. 2. Макрошлифы разных подробностей:
Измерение твердости на поверхности возможно создавать на твердомере с алмазным конусом (РВ — типа Роквелла), на твердомере с алмазной пирамидой (НВ — типа Вик-керса) и на склероскопе. Время от времени появляется необходимость осуществлять контроль твердость на внутренней закаленной поверхности полых подробностей. Само собой разумеется, измерение возможно осуществить простым твердомером на обломке уничтоженной для данной цели подробности.
Но, применив особое приспособление к тому же твердомеру, возможно ввести алмазный конус вовнутрь подробности и измерить ее твердость без разрушения.
Рис. 3. Макрошлифы прокатных валков:
Измерение твердости на поверхности при высокочастотной закалке облегчается отсутствием окалины.
В большинстве случаев замеряют твердость по одной либо нескольким линиям. В цилиндрических подробностях такими линиями помогают окружность и образующая;
В связи с тем, что при поверхностной закалке довольно часто закалена не вся поверхность, воображает интерес распределение твердости по данной поверхности, в особенности по краям закаленной территории. К примеру, при замере твердости по образующей на закаленных подробностях, подвергнутых самоотпуску, время от времени возможно найти заметное повышение твердости на поверхности у краев закаленного участка.
Разброс твердости по образующей либо окружности может сигнализировать о нарушении формы индуктора, об трансформации условий охлаждения, к примеру, в связи с засорением отверстий для закалочной воды, о неточно установленном зазоре между индуктором и закаливаемой подробностью.
Пара иные задачи ставятся при изучении распределения твердости по глубине закаленного слоя.
Как мы знаем, что долговечность и прочность подробностей по окончании высокочастотной закалки в основном зависят от этого распределения.
Исходя из этого таковой контроль твердости получает первостепенную важность, в особенности при наладке процесса закалки.
В связи с тем, что при высокочастотном нагреве закаленный слой имеет в большинстве случаев относительно малую толщину, измерение твердости в разных точках его сечения требует соблюдения определенных правил.
Так, при измерении твердости при помощи прибора Роквелла нельзя определять твердость в точках, удаленных менее чем на 1 мм от кромки. Если не соблюсти этого, то в замерах получается неточность благодаря выдавливания металла в сторону. Наряду с этим может случиться откол кромки, что время от времени ведет к повреждению алмазного конуса прибора.
Рис. 4. Макрошлиф с отпечатками, оставшимися от измерения твердости на приборе Роквелла. Расстояние между соседними отпечатками равняется 1,0 мм, твердость же выяснена через каждые 0,5 мм, благодаря размещению отпечатков по спирали.
В тех случаях, в то время, когда глубина слоя мала если сравнивать с величиной отпечатка алмазного конуса, а нужно взять большое количество точек измерения, рекомендуется создавать их не по радиусу подробности, а по спирали. Это диктуется тем, что отпечатки должны отстоять друг от друга на расстоянии не меньше диаметра отпечатка. В другом случае показания прибора смогут не соответствовать действительности.
Учитывая особенности таких измерений, возможно советовать для них прибор Виккерса, как более надежный и дающий меньшие отпечатки.
В некоторых случаях при измерении твердости по глубине полезно использовать прибор микротвердости ПМТ-3. Он разрешает определять твердость отдельных зерен металла. С его помощью возможно легко измерить твердость железной базы чугуна, закаленной на мартенсит.
В случае если измерения твердости закаленного чугуна создавать на вторых устройствах, то результаты получаются заниженными, поскольку наличие включений графита разрешает измерять лишь среднюю твердость.
Рис. 5. Микроструктура с отпечатками, оставшимися от измерения микротвердости прибором ПМТ-3: а — переходная территория закаленной подробности из стали марки 45; участки феррита (/) имеют меньшую твердость, чем мартенсит (2); б — закаленный слой подробности из серого чугуна; на нетравленном макрошлифе четко виден отпечаток между включениями графита.
При снятии кривых твердости в обязательном порядке необходимо доходить до незакаленной территории подробности, дабы иметь возможность делать выводы и о твердости исходного материала.
Посредством кривых твердости смогут быть распознаны особенности и дефекты закалки.
Напоследок направляться упомянуть еще об одном методе получения кривой твердости. Метод данный содержится в том, что подробность без разрезки подвергают послойному сошлифованию с поверхности и по окончании снятия каждого слоя создают измерение твердости на поверхности. В большинстве случаев за один прием сошлифовывают приблизительно 0,2 мм.
Не считая неудобства многократного шлифования, недочётом этого метода есть искажение показаний прибора в конце измерения, в то время, когда большинство слоя окажется сошлифованной. Сейчас узкий и жёсткий слой, пребывав на мягкой подушке незакаленного металла, проминается.
Увидим, что время от времени твердость, измеренная на поверхности, возрастает на 2—3 единицы по окончании сошлифования узкого слоя закаленного металла. В некоторых случаях обстоятельством этого есть перегрев поверхности, замечаемый значительно чаще при применении через чур высоких частот для получения громадных глубин закалки, в других случаях это явление разъясняется обезуглероживанием поверхности в ходе предшествующей термообработки подробности.
Рис. 6. Твердость структуры с 50% мартенсита: 1 — углеродистая сталь; 2 – среднелегирован-ная сталь.
Рис. 7. Распределение твердости по глубине закаленного слоя для подробности из стали марки 45: а – глубина закаленного слоя; б — переходная территория.
Рис. 8. Обнаружение некоторых недостатков в закаленном слое посредством кривых твердости: а — неудачное распределение твердости по глубине, обычное для довольно долгого нагрева, в то время, когда темперамент последнего приближается к поверхностному; б — перегрев на поверхности
Контроль по микроструктуре. Микроструктурный анализ есть самые детальным, но требует большой затраты труд и времени. Производится анализ на основании просмотра микрошлифа на металлографическом микроскопе.
в отличие от простой закалки, при высокочастотном методе закалки в поле зрения микроскопа довольно часто в один момент оказываются две либо кроме того три структуры: исходная, переходного слоя и закаленного слоя.
Изучение исходной структуры.
Рис. 9. Микроструктура подробности, характерная для высокочастотной закалки при условии узкой переходной территории. В поле зрения микроскопа видны в один момент структуры: закаленного слоя (а), переходной территории (б) и исходного материала (в) XI50.
Так как уровень качества закаленного слоя в сильной степени зависит от состояния и характера исходной структуры, то ее нужно принимать к сведенью при каждом микроанализе. Довольно часто как раз в ней возможно определить причину брака либо недоброкачественности закаленного слоя. Большую роль играются величина зерна исходной структуры и темперамент распределения отдельных структурных составляющих.
К примеру, при закалке среднеуглеродистых сталей утолщенные неотёсанные участки феррита приводят к сильной неравномерности в мартенсите; большое зерно ведет к игольчатости мартенсита и т. д. самая желательной при высокочастотной закалке есть исходная структура в виде сорбита либо мелкопластинчатого перлита.
Изучение структуры закаленного слоя. Обнаружение микроструктуры закаленного слоя разрешает самый совершенно верно и обстоятельно проконтролировать термический и электрический режимы закалки. Для высокочастотной закалки характерно безыгольчатое либо весьма мелкоигольчатое строение мартенсита.
В легированных сталях при высокочастотной закалке игольчатость проявляется лишь при больших перегревах.
Событием, затрудняющим контроль качества закаленного слоя по микроструктуре, есть отсутствие общепринятых и утвержденных шкал.
Так, определение степени игольчатости мартенсита либо его равномерности по составу и протравимости оказывается субъективным и может привести к разногласиям в оценке этих черт.
Затронутый вопрос получает особенную важность при высокочастотном способе закалки, характеризующемся высокой скоростью нагрева, в то время, когда структуры получаются пара хорошими и большое количество разнообразнее, чем при простом методе закалки.
Вследствие этого в НИИ ТВЧ создана восьмибалльная шкала микроструктур мартенсита для среднеуглеродистой стали, закаленной при высокочастотном нагреве.
Балл 1 характеризует структуру крупноигольчатого мартенсита, приобретаемого при перегревах. Такая структура, разумеется, недопустима при высокочастотной закалке.
Балл 2 соответствует структуре среднеигольчатого мартенсита, которую возможно допустить лишь в личных случаях, к примеру, в подробностях со сложной поверхностью, да и то только на участках, не являющихся важными при работе подробности.
Балл 3 представляет собой обычную микроструктуру средне-игольчатого мартенсита и относится к допустимым.
Баллы 4 и 5 относятся к структурам мелкоигольчатого мартенсита. Такая структура есть самая характерной для поверхностной высокочастотной закалки подробностей из среднеуглеродистой стали.
Балл 6 — безыгольчатый мартенсит, характерен для закалки при больших скоростях нагрева в основном небольших подробностей. Наряду с этим в закаленном слое большей частью присутствуют небольшие участки троостита; об этом свидетельствует и приведенная фотография. Однако, закалку на такую структуру можно считать в полной мере удовлетворительной, поскольку ни на твердости, ни на механической прочности подробностей эти недостатки не сказываются.
Баллы 7 к 8 характеризуют допустимую неравномерность мартенсита при стремительных нагревах под закалку стали, имеющей в исходной структуре быстро дифференцированные участки перлита и феррита. Так балл 7 воображает собою структуру мелкоигольчатого мартенсита с неравномерной концентрацией по углероду, не успевающей выравняться при стремительном нагреве. Эта неравномерность выражается в чередовании ярких и чёрных участков.
В структуре, соответствующей баллу 8, распознана троостйтная она образуется в местах бывших ферритных участков. Но Ясность по окончании закалки в этом случае остается равномерной идоста-Т чно высокой. Наряду с этим направляться не забывать, что чем неотёсаннее исходная Т°о\гктура, тем тяжелее добиться мартенсита равномерного состава при высокочастотном нагреве.
При разработке разработки высокочастотной закалки какой-либо подробности, наровне со рвением взять структуру в пределах баллов 4—6, нужно учитывать специфику подробности в каждом отдельном случае. Иными словами, время от времени направляться устанавливать особые допустимые баллы, руководствуясь прилагаемой шкалой.
Так, к примеру, при закалке подробности со сложной поверхностью время от времени нереально добиться во всех точках закаленного слоя аналогичной структуры. Тогда нужно оговаривать в технологических картах, в каких местах подробности, какой вид структуры допустим в пределах баллов 2—8.
При больших скоростях нагрева, довольно часто нужных при закалке тонкостенных подробностей на малую глубину слоя, и при неотёсанной исходной структуре направляться ориентироваться на баллы 4—8.
Видятся и таких ситуации, в то время, когда при наличии исходной структуры в применении скоростей и состоянии отжига нагрева порядка 1000—3000° в сек. по большому счету нереально взять в закаленном слое качественную структуру мартенсита без участков феррита. Примером для того чтобы явления может служить закалка шестерен среднего модуля по новому способу на двух частотах 1. В этом случае нужно создавать предварительную термическую обработку, к примеру, улучшение либо нормализацию, каковые измельчают либо уничтожают участки феррита.
Созданная шкала возможно применена и к оценке структуры мартенсита малолегированных конструкционных сталей, лишь с более твёрдыми требованиями к качеству приобретаемого закаленного слоя.
Контроль микроструктуры закаленного слоя возможно создавать на поверхности подробности без ее разрезки. Для данной цели микрошлиф изготовляют конкретно на поверхности, полируя маленькую лыску. В тех случаях, в то время, когда подробность имеет громадные габариты, микрошлиф разглядывают при помощи переносного микроскопа.
Но большей частью микроструктуру исследуют на шлифах, приготовленных по сечению подробности; лишь таким методом возможно взять исчерпывающую картину результатов закалки.
На микрошлифе возможно совершенно верно установить глубину закаленного слоя независимо от определения (либо в дополнение к нему), совершённого на основании кривой твердости. Наряду с этим глубиной закаленного слоя вычисляют расстояние от закаленной кромки до структуры, содержащей приблизительно 50% мартенсита в смеси с составляющими, характеризующими неполную закалку.
Рис. 10. Шкала микроструктур мартенсита при высоко
По микрошлифу возможно проверить наличие полной закалки в соответствующих местах подробности. Макрошлиф данной возможности не дает так как на нем протравливаются участки и с неполной закалкой
Так, к примеру, макрошлиф подробности с галтелью может создать чувство закалки всего обвода галтели, в это же время как микроструктура найдёт недалеко от галтели лишь неполную закалку (рис. 11). Таковой недостаток узнать особенно принципиально важно, потому, что неполная закалка галтели может вместо упрочнения подробности позвать ее разупрочнение.
Рис. 11. Некачественная закалка недалеко от галтели.
Микроструктура показывает неполную закалку, не смотря на то, что на макрошлифе закаленный слой идет по обводу.
Вторым примером может служить случай, в то время, когда на поперечном макрошлифе каленого кулачка распределительного валика распознан однотонный закаленный слой, идущий по контуру, а при изучении микрошлифа на носике обнаруживаются участки феррита, свидетельствующие о недогреве. В следствии при эксплуатации подробности на этих местах смогут оказаться задиры поверхности.
В случае если при изучении микроструктуры в закаленном слое обнаруживается неполная закалка, то кроме того в том случае, когдаполучен-ная твердость соответствует требованиям технических условий, это говорит о неправильно совершённой термообработке, поскольку неполная закалка, как мы знаем, не снабжает упрочнения подробности. Найти таковой брак возможно лишь при помощи микроанализа, что позволяет вовремя прокорректировать режим обработки.
Изучение структуры переходной территории. Переходной именуют территорию, простирающуюся между структурой и закалённым слоем исходного материала. структура и Ширина переходной территории воздействуют на распределение внутренних напряжений, а следовательно, и на прочность. Ширину переходной территории, так же как и закаленного слоя, возможно выяснить не только по кривой твердости, но и при помощи микроструктурного анализа.
Определение границы между переходной зоной и закалённым слоем было разъяснено выше, а финишем переходной территории нужно считать структуру исходного материала, не претерпевшую никаких трансформаций.
Переходная территория характеризуется структурой, характерной неполной закалке. Так, в переходной территории подробности из стали марки 45 присутствуют зерна мартенсита, феррита и троостита. Наличие громадного количества троостита в большинстве случаев говорит о недостаточной резкости охлаждения.
Громадная ширина переходной территории говорит об довольно долгом нагреве, к чему приходится прибегать, в то время, когда необходимо взять громадную глубину закаленного слоя при через чур высокой частоте тока, не соответствующей размерам данной подробности. В этом случае употребляется фактор теплопроводности. Это же явление может иметь место и при неправильно подобранном электрическом режиме, в то время, когда в подробность подается через чур малая мощность.
При установлении режимов и контроле серийных подробностей направляться обращать внимание на соотношение толщины закаленного слоя и ширины переходной территории, учитывая, что это соотношение определяет внутренние напряжения в подробности.
Контроль деформаций. При контроле качества закалки в серийном производстве и особенно при разработке режима громадную роль играется определение размеров деформаций, появляющихся в ходе закалки.
На характере деформаций и на их величине, так же как и в других случаях, сказываются изюминке высокочастотного нагрева. Потому, что закалке подвергается лишь слой маленькой толщины и, следовательно, структурные превращения и нагрев происходят в малом количестве металла, величина деформации может оказаться меньшей, чем при сквозной закалке. Но, в случае если закалке подвергается лишь некий участок подробности, то время от времени появляются деформации своеобразного характера.
Примером есть закалка шеек коленчатого вала, при которой получается разворот щек, не характерный простой закалке, приводящий в следствии к трансформации неспециализированной длины вала.
Величина деформации, равная разности размеров подробности до и по окончании закалки, определяется посредством простых измерительных инструментов: индикаторов, калибров, индикаторных устройств для измерения внутренних диаметров. В редких случаях, в то время, когда требуется точность измерения до микронов, используют оптиметры. Такие измерения легко осуществимы ввиду отсутствия окалины по окончании высокочастотной закалки.