Корпусные детали остова станка
Конфигурация главных корпусных деталей остова станка и его подвижных рабочих органов выявляется в ходе разработки неспециализированной компоновки станка. Предстоящей задачей проектирования есть выбор формы поперечных сечений этих подробностей, снабжающей нужную прочность, устойчивость и жёсткость совокупности при минимальном весе, и выбор формы направляющих, по которым перемещаются элементы подвижных рабочих органов.
Вес корпусных подробностей образовывает около 80—85% веса станка в целом; совершенство конструкции этих подробностей оказывает громадное влияние на металлоемкость станка.
Потому, что большая часть корпусных подробностей, за исключением тумб, оснований, плит и некоторых коробчатых подробностей, снабжено направляющими, то представляется целесообразным разглядеть прежде всего характерные формы направляющих прямолинейного перемещения.
Направляющие
Конструкция направляющих обязана снабжать нужную точность перемещения рабочего органа по прямолинейной либо круговой траектории и долгое сохранение данной точности.
Нужная точность перемещения достигается, как это указывалось выше, благодаря соответствующей геометрической точности направляющих, применению направляющих таковой формы, которая исключает возможность свободы перемещения рабочего органа под действием составляющих сил резания, и высокой жесткости направляющих, предотвращающей большие перемещения благодаря упругих деформаций.
Свобода перемещения рабочего органа как правило ограничивается особыми устройствами для устранения зазоров, появляющихся между контактирующими поверхностями направляющих как в ходе изготовления, так и при износе.
С целью долгого сохранения точности направляющим должны быть приданы размеры, снабжающие их работу при давлениях, не превышающих допустимые, а для изготовления направляющих необходимо применять износостойкие материалы. Профиль направляющих должен быть выбран с учетом влияния износа на точность перемещения.
В современных станках используются направляющие скольжения, и качения. При применении направляющих качения понижаются тяговые упрочнения, возможно повышена точность перемещения. Но возможности применения направляющих качения ограничены, поскольку при громадных нагрузках на направляющих появляются большие контактные давления.
Конструкции направляющих качения и скольжения очень многообразны.
Направляющие скольжения. самая простую форму имеют плоские направляющие. Рабочий орган опирается на плоскости направляющих. Перемещение рабочего органа в вертикальном направлении ограничивается планками, в горизонтальном — плоскостями. Для устранения зазоров в вертикальной плоскости производится пришабривание планок.
Для устранения зазора в горизонтальной плоскости помогает регулируемая планка, которая поджимается винтами. Пришабривание планок я регулирование планки посредством солидного числа винтов есть трудоемкой операцией. Рассмотренная конструкция регулировочной планки с винтами не снабжает получения высокой жесткости при повороте направляющих в горизонтальной плоскости.
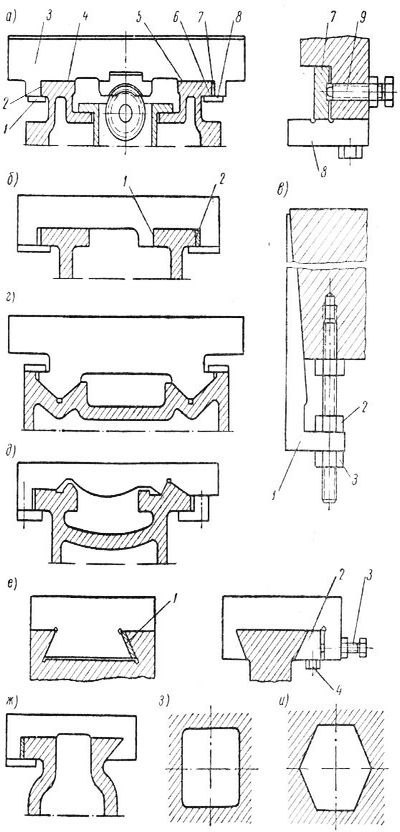
Рис. 1. Направляющие скольжения.
При маленькой длине направляющих подвижного рабочего органа вместо планки возможно использован клин с уклоном 1 : 50. Перемещением клина в осевом направлении посредством гаек обеспечивается узкая регулировка зазора, вместе с тем существенно увеличивается жесткость направляющих. При большей длине подвижных направляющих регулировочные клинья смогут быть установлены на двух противоположных финишах направляющих.
Для устранения зазора в вертикальном направлении на главных планках смогут быть установлены дополнительные планки, регулируемые так же, как планка, либо регулируемые клинья подобные по конструкции клину, продемонстрированному на рис. 1, в. Введение дополнительных регулируемых элементов ведет к снижению жёсткости и усложнению конструкции.
Модификация плоских направляющих, продемонстрированная на рис. 1, б, отличается тем, что перемещение в горизонтальной плоскости ограничивается плоскостями узкой направляющей, использование которой содействует увеличению точности.
В отдельных случаях, в то время, когда вес подвижных рабочих органов снабжает надежное замыкание направляющих и силц, появляющиеся в ходе работы станка, не приводят к подвижного рабочего органа в вертикальном направлении, плоские направляющие смогут быть выполнены без планок.
Поверхность плоских направляющих возможно сделана сколь угодно большой в соответствии с величиной принимаемых нагрузок, чем обусловливается использование плоских направляющих в тяжелых станках. Обработка плоских направляющих не воображает затруднений. Недочётом их есть трудность устранения зазоров.
Плоскими направляющими снабжаются станины тяжелых токарных станков, продольнофрезерных станков, траверсы, стойки, консоли.
Использование призматических горизонтальных корытообразныхили выпуклых направляющих исключает появление зазора в горизонтальной плоскости как при начальной сборке, так и в ходе износа, что есть их значительным преимуществом. Корытообразные призматические направляющие прекрасно удерживают смазку, что имеет значение при высокой скорости перемещения, в частности для направляющих столов продольнострогальных, шлифовальных станков.
Трудоемкость обработки призматических направляющих намного больше трудоемкости обработки плоских направляющих. Особенной трудоемкостью отличаются парные призматические направляющие. Для упрощения обработки используют комбинированные направляющие, складывающиеся из одной призматической и одной либо двух плоских.
В тяжелых продольнострогальных и продольнофрезерных станках используется комбинация из корытообразной и плоской направляющих, в токарных станках средних размеров и в расточных — из выпуклой призматической и плоской направляющих. Угол профиля призматических направляющих выбирается с учетом соотношения сил, действующих в горизонтальном и вертикальном направлениях, так, дабы равнодействующая сил не имела возможности привести к стола по наклонной поверхности направляющей.
При выпуклых призматических направляющих создаются благоприятные условия для удаления стружки, при корытообразных — удаление стружки затруднено.
Призматические направляющие владеют высокой жесткостью при повороте в плоскости размещения направляющих.
Большое распространение находят в станках направляющие в форме ласточкина хвоста, каковые отличаются простотой и компактностью регулировки. Для устранения зазора как в вертикальном, так и в горизонтальном направлениях достаточно одной планки. Планка регулируется так же, как планка,- продемонстрированная на рис.
1, а. Вместо планки возможно использован клин, подобный клину, продемонстрированному на рис. 1, в. Планка регулируется винтами и закрепляется винтами. Последний вариант конструкции имеет высокую жесткость.
По большому счету жесткость направляющих в tjxpMe ласточкина хвоста ниже жесткости рассмотренных ранее конструкций, но благодаря малых габаритов по высоте эта форма направляющих активно используется для движения кареток суппортов, столов консольнофрезерных станков и других рабочих органов.
Во многих случаях используются комбинированные направляющие, в которых сочетаются элементы направляющих в форме ласточкина хвоста и плоских направляющих. Такие направляющие имеют большее число регулирующих элементов, чем простые в форме ласточкина хвоста, и отличаются пара более высокой жесткостью. Комбинированными направляющими снабжаются разного рода траверсы.
Во многих случаях в станках используются круглые направляющие, имеющие форму цилиндрической поверхности. Такие направляющие употребляются для вертикального перемещения траверсы радиальносвер-лильного станка, для движения шпиндельных гильз сверлильных и фрезерных станков, скалок расточных станков, скалок задних бабок токарных станков. В некоторых моделях токарных полуавтоматов и автоматов круглые направляющие используются для движения суппортов.
В отдельных случаях для движения ползунов, имеющих относительно маленькое поперечное сечение, при громадной длине хода употребляются многогранные (четырех-, шестигранные) замкнутые направляющие. В частности, шестигранные направляющие имеют ползуны суппортов больших карусельных станков.
Как правило направляющие выполняются за одно целое С литыми корпусными подробностями. В целях увеличения долговечности направляющие выполняются накладными, из материалов, имеющих более высокую износостойкость.
Подробности, делаемые заодно с направляющими, отливаются из чугуна: более большие подробности (станины, стойки) — из чугуна СЧ 21-40, модифицированного чугуна, сопряженные с ними подробности — из чугуна СЧ 15-36. Направляющие подробностей, отлитых из чугуна, для увеличения износостойкости подвергаются поверхностной закалке.
Накладные направляющие в виде накладных планок либо призм, каковые прикрепляются на винтах к соответствующим поверхностям литых подробностей, изготовляются из конструкционной углеродистой стали, подвергающейся закалке (HRC 50—52), либо из цементируемых углеродистых сталей 15,20 (HRC 55—60). В отдельных случаях накладные направляющие изготовляются из легированных сталей 40Х, ШХ15.
В последнии месяцы взяли распространение, в особенности в тяжелых станках, накладные направляющие из текстолита и других синтетических материалов, и цветных сплавов. Накладные направляющие из текстолита или прикрепляются на винтах, или приклеиваются. Направляющие из цветных металлов (ЦАМ, латунь, баббит) выполняются в виде накладных планок либо получаются методом наплавки.
Накладные планки устанавливаются на маленьких направляющих. Использование накладных направляющих из указанных материалов исключает появление заедания, повышает износостойкость, что имеет особенное значение для тяжелых станков, где подобные направляющие и находят основное использование.
Смазка подается через отверстия, раскрывающиеся на поверхности направляющих. По длине направляющих размещается последовательность отверстий, соединяющихся между собой каналами либо трубопроводами, в каковые масло подается от насоса смазочной совокупности. Направляющие рабочих органов, перемещающиеся со большими скоростями, смазываются непрерывно направляющие рабочих органов, совершающих перемещение с малой скоростью, смазываются иногда.
В последнем случае смазочный насос приводится либо вручную, либо от вала того либо иного иногда включаемого привода.
самые благоприятные условия смазки направляющих рабочих органов, совершающих перемещение подачи, получаются при наличии закрытых поперечных канавок на направляющих подвижного рабочего органа. В случае если смазка подводится через отверстия, раскрывающиеся в канавки подвижного рабочего органа, то канавки должны быть изолированы одна от второй. В случае если смазка подводится через отверстия в неподвижных направляющих, то поперечные канавки подвижного рабочего органа соединяются между собой продольной канавкой, расположенной у края направляющих.
Расчет направляющих ведется или по громаднейшим, или по средним удельным давлениям. При скоростях, характерных для перемещения подачи, у чугунных направляющих станков средних размеров допускаемые громаднейшие давления не превышают 25—30 кГ/см2, а у тяжелых станков — 10—15 кГ/см2. Допускаемые средние удельные давления в два раза ниже.
При определении средних удельных давлений возможно воспользоваться значениями реакций, взятыми при определении тяговых упрочнений, и отыскать среднее давление, как частное от деления величины реакций на площадь направляющих. В более важных случаях нужно использовать уточненные способы расчета.
При разработке конструкции направляющих, в особенности прецизионных станков, нужно предусматривать защиту их от стружки, железной и абразивной пыли. Для удаления стружки на торцах подвижных салазок, перемещающихся по направляющим, устанавливается фетровая подушка, которая прижимается щитком. Но в фетровую подушку внедряются небольшие частицы стружки, железная пыль, каковые изнашивают направляющие станины.
По опыту станкостроительного завода им. Я. М. Свердлова, прекрасно зарекомендовали себя латунные съемники стружки, каковые прижимаются к направляющим под действием сегментной пружины.
Сварные, штампованные либо литые щитки, устанавливаемые на торце подвижных салазок, смогут быть использованы при относительно маленькой длине хода и наличии свободного места для движения щитка. Подобные щитки устанавливаются на торцах столов шлифовальных станков, на салазках некоторых моделей револьверных станков. В случае дефицита места щитки в некоторых случаях выполняются телескопическими.
Рис. 2. Защита направляющих.
Одним из средств защиты являются железные шторки, каковые, будучи связаны с подвижным рабочим органом, сматываются с барабана, снабженного спиральной пружиной.
Рис. 3. Направляющие качения.
На шлифовальных станках, где исключается повреждение защитного устройства стружкой, смогут быть использованы защитные гармошки, изготовляемые из ткани либо кожзаменителей.
Направляющие качения. В качестве тел качения в направляющих качения употребляются шарики, иглы, ролики. Подробности, плоскости которых контактируют с телами качения, смогут быть выполнены металлическими термически обработанными либо чугунными.
В качестве материала для металлических подробностей используется цементируемая сталь 20Х, для чугунных — чугун СЧ 21-40.
В шариковых направляющих подробности связаны с неподвижным основанием, а подробность — с подвижным рабочим органом. Шарики находятся в сепараторах. Одна из подробностей употребляется для регулирования зазора в направляющих либо для предварительного натяга.
В представленной на рис. 3, а конструкции регулирование осуществляется методом смещения планки винтами, по окончании чего планка закрепляется винтами. Планка возможно кроме этого выполнена в форме клина.
Для защиты направляющих рабочий орган снабжен выступами, каковые входят в пазы планок и образуют лабиринтное уплотнение.
В направляющих, продемонстрированных на рис. 3, б, использованы в качестве тел качения иглы, каковые находятся в пазах сепараторов, а в направляющих, представленных на рис. 3, в, — ролики.
Рассмотренные формы направляющих качения смогут быть использованы при относительно маленьком отношении длины хода к длине направляющих, поскольку при громадной длине хода тела качения, перемещаясь вместе с сепаратором, выходят за пределы направляющих и протяженность контакта тел качения с направляющими уменьшается.
При громадной длине хода используются направляющие, в которых обеспечивается перемещение тел качения по замкнутой траектории. При применении в качестве тел качения шариков последние направляются козырьками, расположенными на торцах подвижного рабочего органа, во внутренние каналы подвижного рабочего органа, пройдя по которым, они снова возвращаются в рабочую территорию. Для роликов используются сепараторы в форме цепей, каковые охватывают две звездочки, расположенные на неподвижных направляющих, что ведет к усложнению конструкции и увеличению габаритов направляющих.
При маленьких нагрузках направляющие скольжения катятся по двум-трем подшипникам качения, расположенным на осях в неподвижном основании. Для обеспечения верного положения роликов их оси делаются эксцентричными, чем обеспечивается нужная регулировка.
Расчет направляющих качения ведется по контактным напряжениям. Для определения громаднейших контактных напряжений определяют на базе уравнений статики эпюры распределения давлений на направляющих. Так как направляющие качения используются при относительно маленьких нагрузках, то в большинстве случаев ответ данной задачи не воображает трудностей, поскольку при указанных условиях не появляются большие опрокидывающие моменты и главную роль играются нагрузки от веса подвижных элементов.
Тяговые упрочнения при применении и указанных условиях направляющих качения кроме этого имеют маленькую величину, и их влиянием на распределение нагрузок возможно пренебречь. Выстроив эпюры распределения давлений на направляющих, находят громаднейшее давление на единицу длины направляющих — ртах.
Во фланцах находятся кроме этого отверстия для фундаментных болтов. При наличии внутренних фланцев гайки размещаются в особых карманах.
Рис. 4. Установка на фундамент плит, оснований, станин.
При маленькой удельной нагрузке для крепления посредством фундаментных болтов употребляются лапы. Отверстия для фундаментных болтов смогут имгть кроме этого продолговатую форму пазов.
Во многих случаях рядом с отверстием для фундаментного болта находится резьбовое отверстие для регулировочного болта. Посредством регулировочных болтов, опирающихся на железные плиты, производится выверка станка при установке. При отсутствии регулировочных болтов выверка осуществляется посредством клиньев, каковые помещаются между опорной поверхностью и поверхностью фундамента.
Тяжелые и прецизионные станки в большинстве случаев устанавливаются на регулируемых башмаках. При регулировании клин перемещается по основанию посредством гаек.
Кое-какие разновидности фундаментных болтов представлены на рис. 4, з, и и к. Фундаментные болты с анкерными плитами используются при установке тяжелых станков.
Для движения станков в ходе установки по контуру опорной поверхности делается последовательность пазов для ломика.
Легкие и средние станки смогут устанавливаться на неспециализированной цементной плите цеха. По окончании установки под станки подливается бетон. Станины этих станков должны иметь достаточную жесткость не учитывая их совместной работы с фундаментом.
Тяжелые станки устанавливаются на особых фундаментах, воображающих собой во многих случаях сложные инженерные сооружения с громадной глубиной залегания. Нужная жесткость обеспечивается при совместной работе станины с фундаментом. При громадной длине станины бетон по окончании установки подливается лишь под привод и в зону размещения портала.
Другая часть станины чтобы не было громадных температурных деформаций и деформаций от проседания фундамента устанавливается на башмаках и притягивается фундаментными болтами.
Легкие прецизионные станки громадной жесткости устанавливаются на регулируемых опорах, расположенных в трех точках. При солидной длине станины число регулируемых опор возрастает. При установки прецизионных станков на неспециализированной плите между станком и плитой прокладываются изоляционные прокладки.
Очень прецизионные станки устанавливаются на особых фундаментах, изолированных от вибраций, передаваемых извне, для чего под фундамент закладывается слой шлака, песка либо подводятся упругие элементы — металлические пружины, особые ботинки.
Плиты. Как элементы остова станка плиты употребляются в консольнофрезерных, вертикально- и радиальносверлильных, поперечно-строгальных станках. Плиты этих станков имеют сходную конфигурацию и являются верхнюю и нижнюю стены, связанные между собой совокупностью ребер. Как пример на рис.
5 приведен чертеж плиты радиальносверлильного станка. Так как плиты радиальносверлильных станков помогают для закрепления обрабатываемых различного рода и деталей приспособлений, то они снабжаются Т-образными пазами для крепежных болтов.
В плитах консольнофрезерных станков находятся резервуары для смазочно-охлаждающей жидкости.
Плиты расточных колонок, каковые помогают для закрепления больших подробностей и имеют громадную поверхность, в большинстве случаев выполняются сборными из отдельных секций.
Плиты рассчитываются как пластины, расположенные на упругом основании.
станины и Основания. Конструктивные формы оснований отличаются от конструктивных форм станин, опирающихся конкретно на поверхность фундамента, по большей части, отсутствием направляющих, что разрешает не рассматривать намерено конструкцию оснований.
Станины, опирающиеся конкретно на фундамент, смогут быть названы станинами-основаниями. Формы станин-оснований очень многообразны и зависят от общей компоновки станка, исходя из этого возможно указать лишь на кое-какие самые характерные разновидности: продольные станины-основания больших токарных, продольнофрезерных, продольнострогальных, двухстоечных координатнорасточных,горизонталь-норасточных станков, расточных колонок; маленькие станины бес-консольнофрезерных, координатнорасточных с двухкоординатным перемещением стола, зубофрезерных станков; Т-образные станины разных шлифовальных станков.
В станинах-основаниях находятся те либо иные механизмы приводов, резервуары для смазочно-охлаждающей жидкости, резервуары для масла, во многих случаях шкафы для электроаппаратуры. Особенности конструкции, вызванные размещением указанных устройств, являются чисто личными.
Характерные формы станин-оснований представлены на рис. 6. Для обеспечения соответствующей жесткости станины — основания снабжаются нужным числом продольных стенок и продольных и поперечных ребер. Окнам, имеющимся в стенках станин, рекомендуется придавать круговую форму.
Пара своеобразную форму имеют станины-основания больших токарных станков, снабжаемые сквозными шахтами, через каковые стружка проваливается в коридор, расположенный в фундаменте.
Рис. 5. Плита.
Станины, опирающиеся на тумбы либо основания, по большей части используются, как указывалось выше, в револьверных станках и токарных. Характерные формы станин токарных станков представлены на рис. 7. Станина с П-образными поперечными ребрами имеет пара меньшую жесткость, но несложнее в производстве, чем станина с диагональными Т-образными ребрами. Представленная на рис.
7, а, б ив форма станин токарных станков обусловлена необходимостью свободного отвода стружки через окна, расположенные между ребрами. Но незамкнутая форма сечения станины ведет к большому понижению ее жесткости, исходя из этого на некоторых моделях токарных станков отказываются от хороших форм сечения с целью увеличения жесткости. Сечение, представленное на рис.
7, г, при котором отвод стружки осуществляется через окна боковой стены, разрешает повысить жесткость в 4 раза по сравнению со станиной, имеющей П-образные ребра. Но условия для отвода стружки при данной форме станины ухудшаются. Потому, что роль станины в общей жесткости токарного станка относительно мала и упругие перемещения, обусловленные деформациями станины, составляют около 15% от общей величины перемещения, то жесткость не есть решающим причиной при выборе формы станины токарного станка.
Рис. 6. Станины-основания.
Станины рассчитываются на жесткость, наряду с этим определяется величина относительного смещения обрабатываемой подробности и режущего инструмента, появляющегося благодаря деформаций станины.
Рис. 7. Станины токарных станков.
При расчете станины рассматриваются как балки постоянной жесткости. Станины продольнофрезерных, продольнострогальных и других станков для обработки плоскостей рассчитываются на изгиб в вертикальной плоскости. Станины токарных станков расчитываются на изгиб в поперечном направлении и на кручение.
Подобно рассчитываются станины расточных станков.
Влияние фундамента учитывается коэффициентом увеличения жесткости.
Деформации станины, в большинстве случаев, не оказывают значительного влияния на трансформацию относительного положения режущего инструмента и обрабатываемой подробности, чем понижается актуальность расчета станин на жесткость.
К числу станин относятся кроме этого станины с круговыми направляющими. Специфика конструкции этих станин определяется их круглой формой. Конструктивные изюминки аналогичных станин самый ярко выражены у карусельных станков.
Стойки и порталы. Стойки являются конструктивными элементами остова разных типов станков: консольных, бесконсольных и продольнофрезерных, зубофрезерных, сверлильных, горизонтально- и координатнорасточных, карусельных, плоскошлифовальных и др. Конфигурация стоек в вертикальном направлении изображена на фигурах, иллюстрирующих формы неспециализированной компоновки разных типов станков.
Стойки или устанавливаются на основании нижней опорной поверхностью, или прилегают к основанию нижней частью боковой поверхности. Стойки соединяются с основанием болтами. Отверстия для болтов находятся во фланцах либо карманах, подобных карманам для фундаментных болтов.
Стойки двухстоечных станков (продольнострогальных, продольнофрезерных, карусельных, координатнорасточных), прикрепленные к основанию и связанные между собой поперечной балкой, образуют портал.
Рис. 8. Станина карусельного станка.
Стойки трудятся на изгиб в двух взаимно перпендикулярных направлениях и на кручение около вертикальной оси. Для жесткости стоек громадное значение имеет форма поперечного сечения. Особенно громадны деформации стоек при закручивании при появления искажения контура поперечного сечения.
Для устранения искажения контура поперечного сечения стойки снабжаются поперечными перегородками либо поперечными ребрами жесткости. В отдельных случаях введением поперечных перегородок удается поднять жесткость стоек на порядок. Расстояние между поперечными перегородками должно быть равняется приблизительно 2/3 длины линии контакта сопряженной подробности, передающей крутящий момент стойке.
Окна в поперечных перегородках, имеющие площадь, не превышающую 0,2—0,3 неспециализированной площади поперечного сечения, не вызывают значительного понижения жесткости стойки. Влияние окон на жесткость в значительной степени зависит от формы окна. Минимальное понижение жесткости приводят к треугольной и круглой формы.
Поперечные ребра, расположенные по контуру стойки, кроме этого содействуют увеличению крутильной жесткости стойки. Кроме того при маленькой высоте поперечных ребер, равной 0,05—0,1 соответствующего размера стойки в поперечном сечении, жесткость увеличивается приблизительно на 40%.
Продольные ребра содействуют увеличению жесткости при изгибе. Но жесткость увеличивается относительно мало — на 10—20%.
Окна, расположенные в стенках, быстро снижают жесткость стоек, в особенности окна, расположенные в узкой стенке.
В тех случаях, в то время, когда в стойки находятся те либо иные механизмы, как это имеет место, к примеру в консольнофрезерных станках, где в стойке размещается привод главного перемещения, конструкция стойки в значительной степени определяется условиями размещения механизмов.
Рис. 9. Сечения стоек.
Так как размещение противовеса в стойке ведет к повышению размера окон в перегородках и понижению жесткости, то в некоторых случаях противовесы выносят наружу, придавая им соответствующую форму.
На рис. 9 представлен последовательность характерных сечений стоек. Формы сечения изменяются в зависимости от размеров и типа станка: к примеру, стойки горизонтальнорасточных станков меньших размеров не имеют вертикальных перегородок, а стойки некоторых моделей двухстоечных станков снабжаются вертикальными перегородками. Отношение размеров поперечного сечения стоек одностоечных станков, стойки которых трудятся на кручение, рекомендуется принимать родным к 1 : 1, продольнострогальных и продольнофрезерных 1:2 — 1:3, карусельных 1 : 3—1 : 4.
Соединение стоек двухстоечных станков поперечной балкой возможно выполнено в разных формах. Формы, представленные на рис. 10, а и б отличаются от формы, продемонстрированной на рис.
10, б, более высокой жесткостью. Выбор одной из этих двух форм соединения в значительной степени обусловливается технологическими мыслями. С технологической точки зрения самый простой есть форма, приведенная на рис. 10, а.
Коробчатые подробности. Коробчатые подробности по большей части помогают для размещения в них разного рода механизмов: валов и шестеренок коробок подач и скоростей, отдельных групп передач кинематической цепи, шпиндельных узлов. Коробчатые подробности смогут являться как элементами остова станка, так и элементами подвижных рабочих органов.
Так, шпиндельная бабка токарного станка есть элементом остова станка, а шпиндельные бабки продольнофрезерных, расточных, радиаль-направляться и других станков — подвижными рабочими органами. Коробчатые подробности обоих видов имеют однообразную конструкцию, наряду с этим подвижные коробчатые подробности или конкретно снабжаются направляющими, или находятся на салазках.
Рис. 10. Схемы порталов.
Потому, что в коробчатых подробностях находятся механизмы, то стены коробчатых подробностей должны быть снабжены бобышками для размещения подшипников валов. Подшипники размещаются как в главных, так и в промежуточных стенках коробчатой подробности.
Для монтажа механизмов должен быть обеспечен доступ во внутреннюю полость коробчатой подробности. Доступ обеспечивается через одну из открытых стенок подробности, которая может закрываться откиднои крышкой либо крышкой установленной на винтах. Во многих случаях полость коробчатой подробности остается открытой.
Рис. 11. Коробчатые подробности.
При неразъемных корпусах подробности, монтируемые на валу, в ходе монтажа приходится удерживать на весу, поочередно одевая их на вал, пропускаемый через отверстия в стенках корпуса. При большем весе монтируемых подробностей процесс сборки делается затруднительным. Исходя из этого коробчатые подробности больших станков следует сделать разъемными, не обращая внимания на то, что наряду с этим усложняется технологический процесс обработки.
Коробчатые подробности прикрепляются к опорным поверхностям оснований станин, стоек. Наряду с этим корпус коробчатой подробности может размешаться с внешней стороны либо входить вовнутрь корпуса. Отверстия для крепежных болтов находятся во фланцах, лапах либо карманах, подобных карманам фундаментных болтов.
При установке шпиндельных бабок нужна строгая координация положения оси шпинделя довольно направляющих, которая достигается или методом создания у коробчатой подробности запасных базирующих поверхностей, контактирующих с направляющими станины, или методом введения регулировочных элементов.. Вспомогательные поверхности имеются на коробчатых подробностях, представленных на рис.
12, а и б. У первой — запасной поверхность контактирует с боковой поверхностью направляющей, у второй — с призматической. При отсутствии запасных базирующих поверхностей коробчатая подробность устанавливается в требующееся положение посредством болтов. Для регулирования положения подробности в вертикальной плоскости употребляются резьбовые втулки, каковые опираются на поверхность станины.
Рис. 12. Установка шпиндельных бабок.
Коробчатые подробности изготовляются из чугуна марки СЧ 15-32 либо свариваются из металлических страниц.
Под действием нагрузок, приложенных к валам, происходит деформация стенок, в которых расположены подшипники. Как показывают изучения, величина деформаций по большей части определяется толщиной этих стенок. Жесткость возможно повышена при введении ребер, связывающих бобышки с гранями коробки.
Подвижные стойки, порталы, траверсы. Подвижные стойки отличаются от неподвижных лишь наличием на нижнем основании направляющих, перемещающихся по направляющим станины. Подвижные стойки имеются у расточных колонок, у радиальносверлильных станков некоторых моделей.
Подвижные порталы образуются двумя подвижными стойками, связанными поперечной балкой. Подвижные порталы имеются у карусельных станков громадных размеров.
Траверсы, перемещающиеся по направляющим стоек одностоечных и двухстоечных станков в вертикальном направлении, имеют горизонтальные направляющие для движения суппортов либо шпиндельных бабок.
Рис. 13. Траверса.
Траверсы двухстоечных продольнофрезерных, продольнострогальных, карусельных и координатнорасточных станков имеют характерную конструкцию, изображенную на рис. 13. Траверса коробчатого сечения перемещается по направляющим двух стоек.
Траверса удерживается на направляющих планками. Для устранения зазоров помогают клинья. Перемещение траверсы осуществляется посредством вертикальных винтов, расположенных в стойках, и гаек, прикрепленных к траверсе.
В требующемся положении траверса закрепляется четырьмя прижимными планками.
Механизм зажима приобретает перемещение от свободного электродвигателя. Червячная шестерня с гайкой, расположенной в ступицы, перемещает штангу, имеющую резьбовую часть. На финишах штанги нарезаны зубчатые рейки, каковые зацепляются с шестернями, сидящими на двух валиках. На эксцентричных шейках валиков расположены шариковые подшипники. При повороте валиков 8 подшипники перемещают штоки, каковые поворачивают прижимные планки.
Под гайки прижимных планок подложены сферические шайбы. Регулирование силы прижима каждой из планок осуществляется посредством гаек. Электродвигатель выключается посредством конечного выключателя.
В нише траверсы находятся валы и ходовые винты.
Траверсы трудятся на изгиб в двух взаимно перпендикулярных направлениях и на кручение. Благодаря большому расстоянию между опорами, которое у больших карусельных станков достигает 15—18 м, в траверсе смогут появиться громадные напряжения, чем обусловливается необходимость ее проверки на прочность. Деформации траверсы особенно сказываются на смещении инструмента в вертикальном направлении.
Недостаточная жесткость траверсы может оказаться одним из важных факторов, содействующих происхождению вибраций.
Размеры поперечного сечения траверсы рекомендуется принимать родными к 1 : 1.
Траверсы одностоечных станков имеют форму, близкую к форме равного сопротивления. Подобную же форму имеют траверсы радиально-сверлильных станков, перемещающиеся по цилиндрической направляющей поверхности колонны. Для закрепления в требующемся положении траверса, имеющая надрез, стягивается.
Колонны радиальносверлильных станков, а во многих случаях и стойки как рядиальносверлильных станков, так и расточных колонок, делаются поворотными. Внешняя колонна поворачивается около внутренней колонны. В требующемся положении колонна закрепляется стяжным хомутом, складывающимся из двух половин, связанных шарниром.
Для зажима употребляются механизмы с свободными приводами.
Конструктивное оформление элементов корпусных подробностей. Конструкция корпусных литых подробностей обязана удовлетворять неспециализированным требованиям: простота стержней и изготовления моделей, простота формовки, получение отливки без литейных пороков и высоких остаточных напряжений, удобство очистки литья.
G целью увеличения жесткости корпусные подробности в зоне сопряжения с направляющими и бобышками делают с двойными стенками. Чаще бобышки усиливают дополнительными ребрами.
Бобышки в большинстве случаев находятся в корпуса, а внешние торцы бобышек — в одной плоскости, что снабжает удобство механической обработки.
Очень большие станины, плиты выполняются составными. Станины в большинстве случаев разделяются на секции по длине. Формы плит секций и соединения станин представлены на рис. 15, в и г.
Наровне с литыми в станкостроении используются и сварные корпусные подробности. Сварные конструкции находят преимущественное использование
в мелкосерийном и личном производстве. Сварные станины в большинстве случаев имеют меньший вес если сравнивать с литыми, поскольку благодаря более высокому модулю упругости стали однообразная жесткость возможно взята при меньшем сечении стенок. При малой толщине страниц, из которых изготовляется сварная подробность (3—6 мм), нужная жесткость достигается за счет ввариваемых рёбер и перегородок.
Трудоемкость изготовления сварных подробностей из узких страниц благодаря наличию рёбер и перегородок выше, чем трудоемкость изготовления подобных подробностей из толстых страниц толщиной 10—12 мм.
Рис. 14. траверса и Колонна радиальносверлильного станка.
Рис. 15. Конструктивное оформление элементов корпусных подробностей.
направляться подчернуть, что все советы, относящиеся к конструктивному оформлению корпусных подробностей и их направляющих, изложенные в данной главе, всецело относятся кроме этого и к корпусным подробностям подвижных рабочих органов.