Механическая обработка чистовых заготовок
По окончании обработки на продольно-фрезерных и торцовочном станках заготовка приобретает точные размеры и правильную форму по длине и сечению и преобразовывается из черновой в чистовую. Потом чистовая заготовка проходит еще одну технологическую стадию механической обработки и преобразовывается в готовую подробность.
Механическая обработка чистовых заготовок включает следующие операции: нарезание шипов и проушин, выборку отверстий и гнёзд, профилирование (фрезерование) и зачистку поверхностей (циклевание и шлифование).
Порядок исполнения операций следующий. В большинстве случаев первая операция — нарезание шипов и проушин, поскольку наряду с этим создаются новые установочные и сборочные базы, нужные для правильного исполнения операций по выборке отверстий и гнёзд, по сборке подробностей в сборочные изделия и единицы.
Следующие две операции — фрезерование и выборку продолговатых гнезд —возможно поменять местами. В случае если продолговатые гнезда выбирают на цепнодолбежном станке, то эта операция обязана предшествовать фрезерованию, а вдруг на сверлильно-пазовальном, то ее делают по окончании фрезерования. Разъясняется это тем, что при выборке гнезд на цепнодолбежном станке часто появляются сколы у края гнезда в месте выхода из заготовки фрезерной цепочки.
При предстоящем фрезеровании данный недостаток возможно ликвидирован.
Четвертая операция — высверливание круглых отверстий и, наконец, пятая — окончательная зачистка поверхностей.
Нарезание шипов и проушин. проушины и Шипы делятся на рамные и ящичные. проушины и Рамные шипы нарезают в брусках, соединяемых в рамки, ящичные — в щитах и дощечках, соединяемых в коробки.
оборудование и Технология для нарезания рамных и ящичных шипов разные.
Общее для этих видов шипов — высокая точность обработки, поскольку боковые поверхности их заплечики и шипов являются сборочной базой. Этими поверхностями определяется положение поперечных брусков в рамке по отношению к продольным брускам и положение задника и головки коробки к боковым сторонам.
Особенно правильным должно быть расстояние между заплечиками противоположных шипов бруска либо щитка. Базирование заготовок при нарезании шипов особенно принципиально важно и сложно, поскольку требуется полная определенность положения заготовки в момент ее обработки.
Рамные шипы нарезают на односторонних либо двусторонних рамных шипорезных станках и на фрезерном станке с кареткой.
В качестве режущего инструмента во всех шипорезных станках применяют круглые фрезы и плоские пилы.
На шипорезных станках за один проход подробности производится последовательно три операции: торцовка подробностей круглой пилой; образование проушины проушечным диском, закрепленным на вертикальном шпинделе; образование боковых его заплечиков и граней шипа двумя торцовыми подсечными фрезами, закрепленными соответственно на двух вертикальных шпинделях. Всего в одностороннем станке последовательно установлено четыре режущих инструмента.
На рис. 2 продемонстрирован односторонний шипорезный станок с кареткой, перемещаемой вручную. Станок имеет четыре рабочих органа: пильный вал, два шпинделя для подсечных торцовых фрез и шпиндель с проушечными дисками.
пильный вал и Шпиндели являются в один момент валами встроенных электродвигателей.
Заготовки укладывают на каретку прикасаясь к упорной линейке. При зарезании шипа с первого финиша заготовки торцы заготовок ориентируют по неподвижному упору, а при зарезании со второго финиша — по откидному упору. Заготовки зажимают посредством эксцентрикового зажима.
Подача заготовок на рабочие органы, расположенные последовательно приятель за втором, осуществляется кареткой по направляющей.
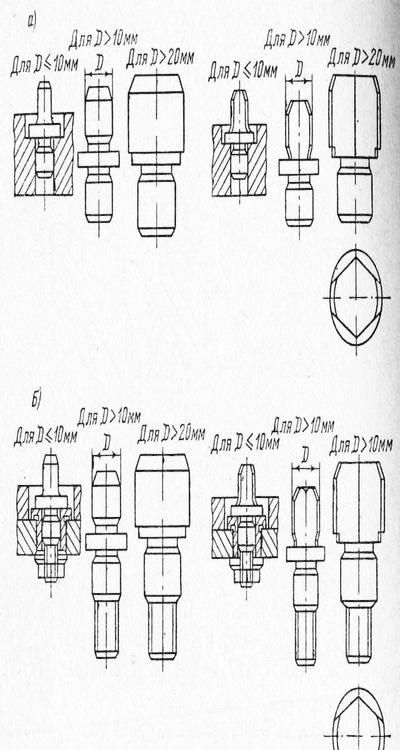
Рис. 1. Технологическая схема образования шипов на рамном шипорезном станке
Рис. 2. Односторонний шипорезный станок: 1 — каретка, 2 — упорная линейка, 3 — неподвижный упор, 4 — откидной упор 5 – зажим, 6 — выпивала, 7 — электродвигатель торцовой фрезы, 8 — маховичок перемещения суппорта торцовой фрезы по высоте, 9 — станина, 10 — нижняя торцовая фреза, 11 — проушечный диск, 12 — электродвигатель проушечного диска, 13 — направляющая каретки, 14 — маховичок механизма установки суппорта с проушечным диском по высоте, 15 — панель настройки
Рис. 3. Схемы организации рабочих мест у станков: а — одностороннего шипорезного, б — двустороннего шипорезного, в — одношпиндельного сверлильного, г — сверлильно-пазовального, д — цепнодолбежного
Конструкцией станка предусмотрена возможность перемещения суппортов рабочих органов в горизонтальной и вертикальной плоскостях, что разрешает делать рамные шипы разных размеров.
Более идеальные односторонние шипорезные станки (к примеру, Ш016-4) снабжены гидравлическими приводами зажима и подачи каретки обрабатываемых заготовок.
На одностороннем шипорезном станке трудится, в большинстве случаев, один станочник и лишь при обработке громадных заготовок — двое рабочих. Схема организации рабочего места у одностороннего шипорезного станка продемонстрирована на рис. 128, а.
Приемы нарезания рамных шипов на односторонних шипорезных станках сходны с приемами торцовки заготовок на торцовочных станках с кареткой. Для зажима заготовок в каретке используют винтовые, эксцентриковые либо быстродействующие пневматические прижимы.
Шипы либо проушины на одностороннем шипорезном станке возможно нарезать по одному из следующих вариантов: – все заготовки партии обрабатывают с одного финиша с установкой их в каретке без упора; после этого устанавливают упор, ограничивающий правильную длину будущей подробности, и обрабатывают все заготовки со второго финиша; – поочередная обработка заготовок с обоих финишей с применением откидного упора; первый финиш обрабатываютбез упора, второй — по упору.
Более производительным есть второй вариант, поскольку в этом случае станочник берет заготовку в руки один раз.
На двусторонних шипорезных рамных станках заготовку обрабатывают с обоих финишей за один проход, поскольку режущие инструменты установлены с двух сторон. Имеется пара моделей таких станков (ШД10-8 и ШД16-8), но по конструкции они однообразны и отличаются лишь возможностью обработки подробностей, разных по длине, толщине, и размерам приобретаемого проушины и шипа.
Двусторонний шипорезный станок обслуживается двумя рабочими (рис. 3, б). Производительность двустороннего станка в 3… 5 раз выше производительности одностороннего.
Нарезать шипы возможно и на фрезерном станке с кареткой (рис. 4). Пачку совершенно верно оторцованных заготовок кладут на каретку торцами прикасаясь к направляющей линейке и хорошо зажимают прижимом 5. Каретка с пачкой заготовок подается на режущий инструмент.
Режущим инструментом возможно торцовая фреза либо проушечный диск.
По окончании нарезания шипов на одном финише заготовок их поворачивают на 180°, повторяют приемы базирования, подачи и прижима заготовок. Точность размера шипа по длине зависит от точности торцовки.
Рис. 4. Нарезание шипов на фрезерном станке: 1 — фреза, 2 — ограждение фрезы, 3 — направляющая линейка, 4 — подпорный брусок, 5 — прижим, 6 — каретка
Чаще всего видящийся недостаток при нарезании шипов — скалывание шипа у последней заготовки в закладке-пачке. Для предупреждения скола на каретку на протяжении направляющей линейки в первых рядах заготовок помещают подпорный брусок, что представляет собой ранее обработанную подробность. Брусок направляться делать из древесины жёсткой породы.
Прямые ящичные шипы возможно нарезать на односторонних и двусторонних ящичных шипорезных станках, и на фрезерном станке.
Принцип работы станков для нарезания прямых ящичных шипов содержится в следующем. На горизонтальный шпиндель насаживают двух-резцовые фрезы с калиброванными прокладками-кольцами между ними. Протяженность передней режущей кромки фрезы определяет ширину проушины, а расстояние между фрезами (высота прокладки) — толщину шипа.
Дощечки-заготовки, уложенные пачкой на рабочий стол, подаются вертикально по направлению касательной к окружности резания инструмента.
На рис. 6 продемонстрирован односторонний ящичный шипорезный станок ШПК-40. На станине станка в подшипниках смонтирован горизонтальный шпиндель с фрезами. Шпиндель приводится во вращение от электродвигателя клиноременной передачей. Станина имеет вертикальные направляющие для движения стола. Нижняя часть стола жестко соединена со штоком гидроцилиндра, которым стол перемещается вверх и вниз довольно фрезерного шпинделя.
На столе укреплена подвижная линейка и две стойки с гидравлическими прижимами мембранного типа, каковые смогут перемещаться в горизонтальной и вертикальной плоскости и поворачиваться около оси. Привод фрезерного шпинделя сблокирован с верхним ограждением.
Рис. 5. Формирование прямых ящичных шипов: а — комплект фрез с прокладками, б — нарезание шипов: 1 — Фрезы, 2 — прокладки, 3 — заготовки
Рис. 6. Односторонний ящичный шипорезный станок ШПК-40: 1 — шкаф с пусковой аппаратурой, 2 — электродвигатель. 3 — органы управления гидроприводом, 4 — подшипники шпинделя, 5 — гидроприжимы, 6 — клиноременная передача, 7 — щиты-заготовки, 8 — стол, 9 — шланг, 10 — гидродилиндр подъема стола
На станке ШГТК-40 возможно кроме этого нарезать клиновые шипы. Станок обслуживает один рабочий. Порядок работы на станке следующий. Рабочий берет пачку дощечек либо щитков, укладывает их на стол, базируя пластями на столе, кромками прижимая к линейке и торцами к упору. Включает гидропривод прижимов, после этого подачи стола и привод шпинделя. По окончании зашиповки стол опускается и освобождаются прижимы.
Станочник переворачивает пачку дощечек на 180° и приступает к обработке второго финиша.
По окончании зашиповки всей партии дощечек при одной настройке станка приступают к зашиповке партии сопрягаемых дощечек. Для этого нужно передвинуть на протяжении шпинделя упорную линейку на толщину шипа либо ширину проушины, поскольку на одной сопрягаемой дощечке шип начинается конкретно от кромки, а на другой — на расстоянии от кромки, равном ширине проушины. Поступающие в зашиповку дощечки либо щитки должны быть совершенно верно оторцованы и не иметь кривизны и крыловатости.
В другом случае окажется брак.
Организация рабочего места у одностороннего ящичного шипорезного станка такая же, как у одностороннего рамного шипорезного станка.
На двусторонних ящичных шипорезных станках шипы нарезаются в один момент с двух финишей заготовок с торцовкой заготовок в размер. Исходя из этого на станке установлены две круглые пилы и две фрезерные наборные головки. Заготовки на режущие головки подаются по одной либо пачкой цепями с упорами из магазина, что загружается вручную.
Торцуются заготовки при их перемещении на цепях.
Для зашиповки заготовки останавливают наоборот фрезерных головок, каковые иногда перемещаются по вертикали по направляющим станины. Двусторонний ящичный шипорезный станок обслуживают двое рабочих.
Для изготовления на щитах и дощечках полупотайных ящичных шипов «ласточкин хвост» и соответствующих проушин используют шипорезные станки ШЛХ-3, в которых устанавливается в один момент до 25 фрезерных головок.
Фрезерование. Фрезерованием именуется обработка материала вращающимися резцами при его поступательном перемещении. Обработка подробностей на фуговальных, рейсмусовых и четырехсторонних продольно-фрезерных станках по существу кроме этого есть фрезерованием, но в практике под фрезерованием принято осознавать обработку криволинейных деталей и прямых с выборкой фальцев, пазов, гребней, калевок и проч.
В зависимости от вида делаемых работ используют одно-, двух- либо многошпиндельные станки с верхним либо нижним размещением шпинделей, легко фрезерные либо копировально-фре-зерные станки.
Базисной моделью есть фрезерный станок среднего типа фС-1. Шпиндель станка смонтирован на мобильном суппорте, что может поменять собственный положение по высоте. На столе имеются поперечные прорези, в которых установлены направляющие линейки. Регулируется положение шпинделя и суппорта по высоте маховичком. Шпиндель соединен с электродвигателем плоскоременной передачей. Для натяжения ремня помогает маховичок.
Отсос стружки производится приемником эксгаустерной установки.
Для разных видов обработки деталей на фрезерных станках применяют особые приспособления: упорные кольца, цулаги, шаблоны, линейки и упоры.
Для фрезерования прямолинейных кромок используют одношпин-дельные фрезерные станки с нижним размещением шпинделя. Вероятны следующие вилы фрезерования прямолинейных кромок: плоское — выверка ровных кромок под плоскость и профильное, которое возможно сквозным (на всей протяженности заготовки) и несквозным (на части длины заготовки) .
Работа ведется по направляющим линейкам. передняя и Задняя линейка линейка соединены скобой, которая огибает режущий инструмент.
При плоском и профильном сквозном фрезеровании задняя линейка собственной плоскостью обязана совпадать с касательной к окружности резания фрезы, переднюю устанавливают параллельно задней со смещением в сторону фрезы на величину сострагиваемого слоя h.
При профильном несквозном фрезеровании обе линейки устанавливают в одной вертикальной плоскости без смещения. На столе либо на направляющих линейках ставят ограничительные упоры, каковые определяют длину фрезерования. Заготовку кладут на стол станка, прижимая задним финишем к упору. Перемещением «от себя» подают заготовку на фрезу , пока она собственной кромкой не прижмется к линейке.
После этого продвигают заготовку на протяжении линеек до упора. Обработанную заготовку снимают со станка.
Рис. 7. Фрезерный станок ФС-1: 1 — станина, 2 — суппорт, 3 — маховичок подъема суппорта, 4— стол, 5 — направляющие линейки, 6 — кронштейн с откидным подшипником, 7 — приемник, 8 — маховичок для натяжения ремня
Фрезерование криволинейных кромок возможно плоским и профильным, сквозным (по всему контуру заготовки) и несквозным (на части длины контура). При фрезеровании криволинейных кромок на фрезерных станках пользуются особыми приспособлениями — цу-упорными кольцами и лагами.
Цулага является шаблоном , направляющая кромка которого имеет криволинейную форму, соответствующую форме будущей подробности. С противоположной стороны от направляющей кромки на шаблоне установлена линейка 2. Заготовка базируется на цулаге, линейке и упоре, прижимается сверху прижимом. На плите стола либо на шпинделе закреплено упорное кольцо, диаметр которого неизменно меньше диаметра окружности резания на величину толщины снимаемого слоя при фрезеровании.
Высота кольца должна быть не больше толщины основания шаблона либо высоты направляющей кромки шаблона. В качестве упорного кольца, усиливаемого на шпинделе, применяют шариковые подшипники. Цулагу с зажатой заготовкой надвигают на вращающуюся фрезу, все время прижимая направляющую кромку шаблона к упорному кольцу.
Фреза обработает кромку заготовки по контору шаблона.
Рис. 8. Направляющие линейки фрезерного станка: 1— стол станка, 2 —задняя линейка, 3— скоба, 4 — передняя линейка, 5 — заготовка
Рис. 9. Схема несквозного профильного фрезерования: 1 — задняя линейка, 2 — фреза, 3 — передняя линейка, 4, 7 — упоры, 5 — положение заготовки до обработки, 6 — положение заготовки по окончании обработки
Рис. 10. Приспособление для фрезерования криволинейных кромок: 1 — шаблон-цулага, 2 — линейка шаблона, 3 — прижим, 4 — упор, 5 — заготовка, 6 — направляющая кромка шаблона, 7 — фреза, 8 — упорное кольцо
По конструкции цулаги смогут быть различные в зависимости от размеров и формы обрабатываемых заготовок и от характера обработки. Цулаги изготовляются на столярно-мебель-ных фирмах. Точность обработки подробностей фрезерованием по большей части определяется точностью изготовления цулаг.
Обработка сборочных единиц и щитов по наружному контуру практически не отличается от фрезерования криволинейных брусковых заготовок, наряду с этим кроме этого используют цулаги и упорные кольца.
Торцовое фрезерование. Выборка несложных и фигурных полостей, пазов, канавок и гнёзд в щитах и заготовках осуществляется на копировально-фрезерных станках с верхним размещением шпинделя. В качестве режущего инструмента используют концевые торцовые фрезы.
В столе станка по одной оси со шпинделем установлен копировальный палец. Заготовку кладут на копир-шаблон, что имеет конфигурацию будущей подробности, и зажимают. Внутреннюю кромку копира-шаблона обводят по копировальному пальцу.
Опушенная сверху на заготовку фреза повторяет конфигурацию копир-шаблона.
Недостатки при фрезеровании. При фрезеровании заготовок по кривой на отдельных участках из-за наклона волокон вероятны сколы, в особенности на финишах заготовок. Для уменьшения этого недостатка пользуются двухшпиндельными фрезерными станками, шпиндели которых вращаются в различные стороны. Пользуясь то одним, то вторым шпинделем, любой участок кривой обрабатывают в удачном направлении.
Скорость подачи заготовок нужно согласовывать с условиями фрезерования отдельных участков.
Волнистость на обрабатываемой поверхности получается по причине того, что либо заготовка неплотно прижимается к направляющей линейке, либо во фрезеровании участвуют не все зубья фрезы. Не-прострожка прямолинейных подробностей не редкость )!з-за непрямолинейности фрезеруемых кромок либо из-за неправильной установки линеек. В криволинейных подробностях непрострожка возможно из-за неплотного прилегания заготовок к базисным поверхностям цулаги и упорному кольцу.
Техника безопасности при работе на фрезерных станках. Режущий инструмент на фрезерных станках в обязательном порядке ограждают корпусом с патрубками для выброса стружки. С передней стороны корпуса делают открытый проем, что перекрывают щитком, укрепленным на качающемся рычаге. При нажиме обрабатываемой подробности на скос щитка последний поднимается и дает доступ к режущему инструменту.
Совокупность щиток — рычаг уравновешена пружиной-противовесом, возвращающей щиток в исходное положение по окончании прохода подробности. Ограждение сблокировано с пусковой совокупностью для надёжной смены режущего инструмента, ремонта и обслуживания станка. Станки оборудованы электрическим устройством для стремительного торможения электродвигателя привода шпинделя.
Трудиться на станке возможно лишь при исправном ограждении и действующей электроблокировке.
При фрезеровании по линейке заготовку нужно прижимать к линейке и столу прижимными устройствами. В остальных случаях при ручной подаче заготовку необходимо подавать на режущий инструмент посредством колодок, толкателей либо шаблонов. Категорически запрещается при криволинейном фрезеровании подавать заготовку против слоя, поскольку в этом случае вероятен выброс заготовки.
Сверление круглых отверстий. Высверливать круглые отверстия, сквозные и несквозные (гнезда) возможно на разных сверлильных станках с горизонтальным и вертикальным размещением рабочих шпинделей. Сверлильные станки смогут быть одно- и многошпиндельные.
Громаднейшее распространение взяли одношпиндель-ные вертикальные станки с ручной и автоматической подачей.
Режущий инструмент для гнёзд и сверления отверстий — торцовые фрезы и специальные свёрла. Диаметр сверла либо фрезы определяет размер будущего отверстия. Помимо этого, для сверления отверстий смогут употребляться агрегатные силовые головки.
Заготовки, подлежащие сверлению, должны быть предварительно совершенно верно оторцованы.
На рис. 11 продемонстрирован сверлильный станок СВА-2. На чугунном основании установлена вертикальная колонка, на консоли которой укреплены шпиндельная электродвигатель привода и вертикальная головка шпинделя. Подача шпинделя вниз может осуществляться от ножной педали, от руки рычагом либо машинально от отдельного привода, расположенного внизу и складывающегося из электродвигателя и двухскоростной коробки передач. В верхнее исходное положение шпиндель возвращается особой пружиной.
На колонке укреплен стол станка. Он может поменять положение по высоте, поворачиваться около горизонтальной оси на 90° и перемещаться продольно. Станок снабжен подвижным ограждением сверла.
Громаднейший диаметр сверления 40, глубина 100 мм; частота вращения шпинделя 3000 и 6000 об/мин; скорость подачи шпинделя 6 м/мин.
Рис. 11. Сверлильный одно-шпиндельный станок СВА-2: 1 — педаль, 2 — колонка, 3 — маховичок передвижения стола, 4 — стол, 5 — прижим, 6 — шпиндельная головка, 7 — рычаг подачи шпинделя, 8 — электродвигатель, привода шпинделя, 9 — маховичок подъема стола
Станок обслуживает один рабочий.
Для одновременного сверления нескольких отверстий в рамках и щитах используют многошпиндельные сверлильные станки, либо присадочные.
Рис. 12. Сверлильно-пазовальный станок СВПГ-2: 1 — педаль, 2 — маховичок механизма установки стола по высоте, 3 — гидрораспределитель, 4 — кронштейн, 5 — стол, 6 — упорный угольник, 7 — гидроприжимы, 8 — патрон
Рис. 13. Форма приобретаемого гнезда на сверлильно-пазовальном (а) и цепнодолбежном (б) станках
Рис. 14. Порядок выборки гнезда, на сверлильно-пазовальном станке с ручной подачей концевой и спиральным сверлом фрезой
Сверление нескольких отверстий одного диаметра вероятно и на одношпиндельном станке. В этом случае используют приспособление, именуемое кондуктором. Кондуктор является шаблономиз листового железа либо другого материала, на котором отверстия расположены так, как они должны быть в заготовке.
Шаблон накладывают на заготовку сверху и прижимают. Сверло направляют через отверстия шаблона. За одну установку сверлят все отверстия в заготовке, меняют лишь позицию кондуктора относительно сверла.
Точность гнёзд и расположения отверстий на подробности зависит по большей части от закрепления заготовки и точности базирования на станке. Точность диаметра отверстий определяется точностью диаметра и выбором сверла его центровки.
Выборка продолговатых отверстий и гнёзд. отверстия и Продолговатые гнёзда в заготовках возможно взять на сверлильно-пазовальном и цепнодолбежном станках посредством спиральных сверл либо концевых фрез. Концевые фрезы более производительны; чистота боковых поверхностей гнезд выше.
Выбираемые на сверлильно-пазовальном станке гнезда в плане имеют форму прямоугольника с закругленными торцовыми поверхностями.
Порядок выборки гнезда на сверлильно-пазовальном станке с ручной подачей при работе спиральным сверлом схематично продемонстрирован на рис. 14. Сперва высверливают отверстия I и II по финишам гнезда, после этого последовательно отверстия III, IV, V и VI.
Затем, не поднимая сверла, расчищают все Гнездо.
При работе концевой фрезой приемы те же. Фрезу сперва углубляют на одном финише гнезда I, поднимают, после этого углубляют в противоположном финише гнезда II и, не вынимая фрезы, медлительно передвигают ее к первому финишу. За один прием возможно вы-фрезеровать гнездо глубиной не более двух диаметров фрезы.
самоё совершенным есть горизонтальный сверлильно-пазовальный станок СВПГ-2 с автоматической подачей. На станине горизонтально посредством шарнирной опоры закреплен электродвигатель с удлиненным валом, что помогает одновременно и шпинделем. В патроне закреплена концевая фреза.
В вертикальных направляющих станины на суппорте подвижно крепится стол, что может поменять положение по высоте и передвигаться по горизонтальным направляющим в сторону шпинделя и обратно. Заготовка прижимается на столе двумя гидроприжимами к упорному угольнику. Заготовка зажимается машинально в начале перемещения стола к фрезе.
Шпиндель, в котором крепится концевая фреза, не считая вращательного совершает еще колебательное перемещение в горизонтальной плоскости, исходя из этого на станке возможно высверливать продолговатое отверстие-паз глубиной до 80 и длиной до 125 мм. Величина амплитуды колебания шпинделя регулируется в зависимости от длины обрабатываемого паза. Колебательное перемещение шпиндель приобретает от гидродвигателя через кривошипно-шатунный механизм.
На станке трудится один станочник.
На рис. 16 продемонстрирован цепнодолбежный станок ДЦА-3. Режущий инструмент в цепнодолбежном станке — фрезерная цепочка, скользящая по направляющей линейке, приводится в перемещение звездочкой, закрепленной на электродвигателе.
Станок имеет цельнолитую чугунную станину коробчатой формы. В верхней части станины по направляющим перемещается вертикальный суппорт 6, на котором установлен электродвигатель с режущей головкой. Режущая головка складывается из фрезерной цепочки, направляющей линейки с роликом и приводной звездочки на валу электродвигателя.
На станине под режущей головкой закреплен рабочий стол 3, что может перемещаться в продольном и поперечном направлениях и устанавливаться под углом к горизонтальной плоскости. Обрабатываемая заготовка на столе закрепляется быстродействующим зажимом. Рабочее и холостое перемещения суппорта по вертикали осуществляются гидравлическим приводом, конструкция которого предусматривает автоматическую работу суппорта режущей головки по твёрдым ограничительным упорам.
Режущая головка опускается на такую глубину, которая выяснена нижним упором, по окончании чего машинально возвращается в верхнее исходное положение до верхнего упора. Режущая цепочка закрыта ограждением, которое есть в один момент приемником стружки и возможно через патрубок подсоединено к эксгаустерной сети.
Форма приобретаемого на цепнодолбежном станке гнезда в плане прямоугольная, углы дна закруглены, исходя из этого глубина гнезда делается с запасом если сравнивать с длиной сопрягаемого шипа. Мельчайшие размеры гнёзд определяются мельчайшими размерами фрезерных цепочек и их направляющих линеек.
При выборке долгого гнезда приемы работы цепочкой сходны с приемами работы концевой фрезой. Сперва опускают цепочку с одного финиша гнезда, поднимают ее, после этого опускают с другого конца гнезда. Позже надвигают цепочку в направлении первого углубления, фрезеруя промежуток.
направляться знать, что цепочка обязана трудиться восходящей ветвью.
В случае если в заготовке требуется выбрать одно гнездо либо отверстие, в качестве приспособления применяют один концевой упор. При необходимости выборки двух однообразных гнезд, расположенных в одну линию, возможно работу выполнить с одним упором за две установки и с двумя упорами за одну установку. В первом случае упор устанавливается и выбирается первое гнездо у всей партии заготовок, после этого упор переставляют в новое положение и выбирают второе гнездо.
При работе с двумя упорами работа протекает следующим образом. Упоры устанавливают с обоих финишей заготовки с таким расчетом, дабы правое гнездо выбиралось при крайнем левом положении заготовки у левого упора (/ позиция), а левое гнездо — при крайнем правом положении заготовки у правого упора (// позиция).
Рис. 15. Цепнодолбежный станок ДЦА-3: 1 — педаль, 2 — механизм передвижения стола в продольном направлении, 3 — ст*ол, 4 — маховичок зажима, 5 — маховичок «механизма натяжения цепочки, 6 — суппорт рабочего органа, 7 — ограничитель перемещения стола в продольном направлении, 8 — гидрораспределитель
На цепнодолбежных станках вероятен недостаток обработки — скол края гнезда при выходе цепочки из древесины. Скол возможно не допустить, в случае если на заготовке закрепить подпорный брусок. Недочётом цепнодолбежного станка есть кроме этого да и то, что нельзя получить гнезда размером по периметру меньше 40X6 мм.
Рис. 16. Выборка в заготовке двух гнезд на цепнодолбежном станке
Рис. 17. Нож для машинного циклевания (а) и ручная цикля (б)
Точность обработки гнезд на сверлильно-пазовальном и цепнодолбежном станках приблизительно однообразная. Допускаемые отклонения по ширине гнезда и расстоянию между кромками гнезда и детали 0,4 … 1 мм.
На станке ДЦА-3 возможно обрабатывать заготовки шириной до 160, толщиной до 200 мм. Громаднейшие размеры выбираемого паза-гнезда: ширина 25, протяженность 430, глубина 160 мм.
Станок обслуживает один станочник. Схема организации рабочего места у станка ДЦА-3 продемонстрирована на рис. 128, д.
Производительность цепнодолбежного станка определяется так же, как сверлильного.
Зачистка поверхностей. Заготовки по окончании обработки на фрезерных, сверлильных и цепнодолбежных станках смогут иметь волнистость, местные выколы, задиры и заусенцы на ребрах заготовок и на краях отверстий и гнёзд, вмятины, другие дефекты и ворсистость, каковые не допускаются в изделии. Неровности и недостатки ликвидируют циклеванием и шлифованием.
Циклюют лишь поверхности и твёрдые породы древесины, предназначенные под отличную отделку полированием.
Циклевание — это строгание поверхности древесины намерено заточенным ножом — циклей. Циклевание возможно создавать на циклевальных станках и вручную.
На рис. 18 продемонстрирована схема устройства циклевального станка. Нож устанавливают лезвием вверх в особой коробке. Лезвие должно выступать над поверхностью стола на 0,1…0,15 мм.
При прохождении заготовки 2 через станок с нижней поверхности снимается слой толщиной 0,025… 0,15 мм.
Рис. 18. Схема устройства циклевального станка: 1 — cтол, 2 — заготовка, 3 — подающие вальцы, 4 — циклевальный нож
При ручном циклевании заготовка базируется на верстаке обрабатываемой поверхностью вверх. Степень заглубления цикли в древесину зависит от прилагаемого рабочим твёрдости и усилия обрабатываемой древесины. Исходя из этого точность ручного циклевания ниже машинного.
Совсем поверхности зачищают шлифованием. Инструментом для шлифования помогает шлифовальная шкурка, складывающаяся из бумажной либо тканевой базы, на которую наклеены небольшие абразивные зерна из стекла, кремния, гранита или других материалов повышенной твердости.
Шлифуют древесину на протяжении волокон либо под маленьким углом. При поперечном шлифовании на древесине остаются царапины, портящие внешний вид изделия. Исходя из этого рамки, к примеру, направляться шлифовать по диагонали, дабы все бруски шлифовались под углом к направлению волокон.
Шероховатость шлифованной поверхности по большей части зависит от зернистости используемой шкурки. Чем. больше зерна шкурки, тем более неотёсанной получается поверхность. Шкурки с небольшими зернами дают более чистую поверхность, но они менее производительны. Исходя из этого рекомендуется шлифование проводить в два-три этапа.
Затевать нужно более неотёсанной шкуркой для стремительного уничтожения следов прошлой обработки и завершать мелкозернистой для получения требуемой шероховатости поверхности.
Шлифовальная шкурка закрепляется на держателях разных форм, совершающих рабочее перемещение. В зависимости от формы держателя различают ленточные, дисковые и цилиндровые шлифовальные станки.
Ленточные шлифовальные станки в качестве инструмента имеют нескончаемую шлифовальную ленту, натянутую на два шкива. Станки применяют для шлифования плоских и криволинейных поверхностей. Они бывают с горизонтальным и вертикальным размещением ленты; чаще используют первые.
Рис. 19. Шлифовальный ленточный станок ШлПС-5П: 1, 7 — направляющие для утюжка и перемещения стола, 2 — рычаг, 3, 5 —шкивы, 4 — шлифовальная лента, 6 — рукоятка, 8 — стол, 9 — утюжок, 10— винтовой механизм
Шлифование на ленточных станках осуществляется свободной лентой без прижима и лентой с контактным прижимом (утюжком).
На рис. 19 продемонстрирован шлифовальный ленточный станок ШлПС-5П. Станина выполнена в виде двух колонок, на которых смонтированы шкивы. Один из них приводной, укреплен конкретно на валу электродвигателя. На шкивах натянута шлифовальная лента. На колонках станины имеется два суппорта, по направляющим которых перемещается вручную на роликовых опорах рабочий стол. Поднимается и опускается стол механизмом. Обрабатываемый щит базируют на столе посредством упоров.
На цилиндрической направляющей, установленной между колонками параллельно ленте, подвижно крепится кронштейн с утюжком, перемещаемым вручную. На станке возможно обрабатывать сборочных единиц и поверхности щитов шириной до 850, длиной до 2000 и высотой до 400 мм. Скорость перемещения шлифовальной ленты 25 м/с, ширина ленты 160 мм. Станок обслуживает один станочник.
Схема организации рабочего места продемонстрирована на рис. 145, а.
В дисковых шлифовальных станках шлифовальная шкурка надевается на плоскую поверхность чугунного диска, что может иметь вертикальное либо горизонтальное размещение. Обрабатываемые подробности прижимаются к шкурке вручную либо прижимами. Дисковые станки предназначены в основном для чернового шлифования, снятия провесов в собранных рамках, шлифования небольших подробностей по торцовым и продольным поверхностям.
Цилиндровые шлифовальные станки используют для шлифования плоских плит и щитов, и для снятия провесов у собранных рамок. Держателем шкурки являются цилиндры-барабаны. Громаднейшее распространение взяли трехцилиндровые станки, у которых шлифовальные цилиндры вращаются поразному: первый и третий навстречу подаче, а второй по ходу ее. Не считая вращательного второй и третий цилиндры имеют осевое перемещение, приблизительно 150 двойных ходов в 60 секунд при величине хода 10 мм.
Трехцилиндровые станки бывают с вальцовой и гусеничной подачей.
Рис. 20. Схема организации рабочих мест у шлифовальных станков: а — ленточного, б — дискового с бобиной, в — трехцилиндрового
На рис. 146 продемонстрирован трехцилиндровый шлифовальный станок ШлЗЦ12-2. На станине станка уложена горизонтальная плита — стол, на котором смонтирован гусеничный механизм подачи. Стол может поменять собственный положение по высоте. Над столом находятся шлифовальные цилиндры, имеющие личные электродвигатели. Между цилиндрами находятся прижимные вальцы.
За третьим цилиндром укреплен барабан со щеткой для очистки шлифуемой поверхности от пыли. Шлифовальная шкурка навивается на цилиндры по спирали. На станке возможно обрабатывать рамки и щиты следующих размеров: ширина до 1250, толщина до 130, протяженность от 460 мм.
Скорость подачи до 15 м/мин.
Трехцилиндровый шлифовальный станок обслуживают двое рабочих.
При работе на шлифовальных станках нужно выполнять неспециализированные правила техники безопасности. Помимо этого, трудиться на этих станках возможно лишь при наличии охотно действующей экс-гаустерной установки для отсасывания пыли.