Наплавка твердых сплавов
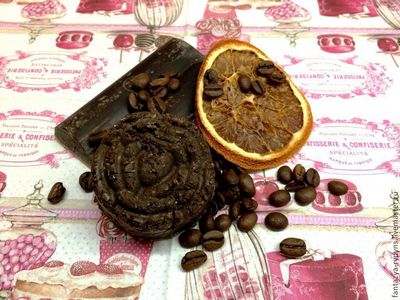
В современной технике приобретают широкое распространение и скоро совершенствуются жёсткие сплавы. Развитие техники применения жёстких сплавов идет по двум направлениям: с одной стороны, совершенствуются и постоянно совершенствуются составы жёстких сплавов и разработка их производства; иначе, совершенствуется техника нанесения жёстких сплавов на изделия, в основном техника их наплавки.
Жёсткие сплавы характеризуются в первую очередь большой твердостью, приблизительно HRC 55—94. Они сохраняют собственную твердость при нагревании до больших температур, в большинстве случаев, не поддаются отпуску и не смогут быть смягчены термической обработкой, исходя из этого механическая обработка жёстких сплавов очень трудоемка и может производиться только абразивами, в связи с чем при наплавке жёстких сплавов необходимо уделять особенное внимание сведению до минимума последующей механической обработки.
Жёсткие сплавы при высокой твердости, конечно, владеют малой пластичностью и отличаются хрупкостью, исходя из этого достаточно не хорошо сопротивляются ударным нагрузкам. Хрупкость жёстких сплавов сохраняется и при больших температурах, благодаря чего они склонны к образованию трещин при наплавке; на это направляться обращать особенное внимание.
Жёсткие сплавы возможно поделить на следующие четыре группы: 1) литые сплавы, либо стеллиты; 2) порошкообразные либо зернообразные продукты; 3) керамические либо спеченные сплавы; 4) плавленые карбиды. Базой всех жёстких сплавов являются прочные карбиды металлов, не разлагающиеся и не растворяющиеся при больших температурах. Особенно серьёзны для жёстких сплавов карбиды вольфрама, титана, хрома, частично марганца.
Карбиды металлов через чур хрупки и довольно часто тугоплавки, исходя из этого для образования жёсткого сплава зерна карбидов связываются подходящим металлом; в качестве связки употребляется железо, никель, кобальт.
Литые сплавы смогут быть поделены на настоящие стеллиты и более недорогие сплавы-заменители. К настоящим стеллитам относится, к примеру, коммунистический жёсткий сплав В-ЗК. Настоящие стеллиты являются в основном хрома и карбиды вольфрама, сцементированные железом и кобальтом-
Благодаря кобальта и высокого содержания вольфрама литые жёсткие сплавы типа настоящих стеллитов достаточно дороги и дефицитны.
Практика многих лет продемонстрировала, что литые сплавы-заменители являются намного более недорогими и как правило трудятся в полной мере прекрасно, исходя из этого, как не которые содержат кобальта и вольфрама, они сейчас очень активно используются в отечественной индустрии. Примером для того чтобы сплава есть изобретенный в 1929 г. отечественный сплав сормайт, наименование которого происходит от заглавия Сормовского завода, где в первый раз было освоено производство этого сплава. Сормайт представляет собой железохромистый сплав с маленькой добавкой никеля и не содержит кобальта и вольфрама.
Литые сплавы относительно легкоплавки, температура их плавления немного ниже температуры плавления сталей и образовывает около 1300—1350 °С. Выпускаются они в большинстве случаев в виде литых прутков либо стержней длиной 300—400 мм, диаметром 5—8 мм. Литые сплавы владеют средней твердостью HRC 70—80 и используются в основном для наплавки рабочих поверхностей, подвергающихся большому износу, к примеру, штампов, матриц и пуансонов, калибров, шаблонов, подробностей автомобилей и механизмов, трудящихся на трение, и т. п. Сплавы владеют высокой износоустойчивостью, сохраняющейся до температур 600-700 °С — начала красного каления.
Наплавка жёстких сплавов ведется, в большинстве случаев, в два, а время от времени и в три слоя. При наложении первого слоя наплавка является сплавомжёсткого сплава с расплавленным главным металлом, благодаря чего таковой сплав владеет пониженными износоустойчивостью и твёрдостью и не снабжает получения механических особенностей чистого жёсткого сплава.
Исходя из этого первый наплавленный слой в большинстве случаев не может служить рабочей поверхностью, а^ есть только подкладкой для нанесения второго слоя, что будет воображать собой практически чистый жёсткий сплав и владеть нужными механическими особенностями. В некоторых особенно важных случаях прибегают к наплавке третьего слоя, представляющего собой фактически уже чистый переплавленный жёсткий сплав.
Для получения экономичной наплавки жёсткого сплава необходимо стремиться к мельчайшему расплавлению главного металла на минимальную глубину; одновременно с этим главной металл должен быть расплавлен по всей поверхности нанлавки, в противном случае неизбежны непровары, каковые смогут вызвать растрескивание и отслаивание жёсткого слоя при работе наплавленной подробности.
Процесс газовой наплавки литого сплава ведут следующим образом. Для уменьшения напряжений, появляющихся в наплавленном слое, и возможности образования в нем трещин наплавляемую подробность предварительно подогревают до начала красного каления. После этого поверхность металла с опаской доводят нагреванием горелкой до начала поверхностного оплавления, т. е. до так именуемого потения металла, в то время, когда на его поверхности выступают отдельные жидкие капельки.
Тогда в пламя горелки вводят финиш прутка жёсткого сплава и натирают им поверхность подробности, размазывая жёсткий сплав по поверхности, т. е. как бы облуживая подробность жёстким сплавом. При достаточной квалификации сварщика эта операция гарантирует прочное сцепление с главным металлом наплавляемого жёсткого сплава при минимальном его расходе. На взятую так подкладку наплавляют жёсткий сплав с минимальным вероятным расплавлением ниже лежащего слоя.
Вероятна кроме этого и дуговая наплавка литых жёстких сплавов, для чего на прутки сплава наносят обмазку, не содержащую актив-пых окислителей, к примеру из мрамора, плавикового шпата и т. д., по типу обмазок УОНИ-13. Для дуговой наплавки используют кроме этого особые электроды со стержнем из простой низкоуглеродистой проволоки с толстой обмазкой, не содержащей активных окислителей, в которую вводят много ферромарганца и феррохрома.
Подобные недорогие электроды дают удовлетворительную наплавку в тех случаях, в то время, когда не предъявляется высоких требований к твердости и износостойкости наплавленного слоя. Помимо этого, используют трубчатые электроды, складывающиеся из металлической тонкостенной трубки, набитой порошкообразным жёстким сплавом либо материалом, образующим жёсткий сплав при расплавлении, а снаружи покрытой электродной обмазкой, улучшающей горение дуги и создающей шлаковую защиту. Удачно используется дуговая наплавка в инертных газах и плазменная наплавка.
Порошкообразные либо зернообразные сплавы являются не сплавы, а порошкообразную смесь, шихту либо материал для того чтобы и преобразовываются в жёсткий сплав только на поверхности наплавляемой подробности в ходе наплавки. Они самый недороги в наплавке и изготовлении и исходя из этого активно используются в индустрии. По внешнему виду эти продукты являются грубозернистый порошок либо крупинки тёмного цвета, состоящие, из зерен величиной 1—3 мм.
Различают два вида порошкообразных продуктов для наплавки: вольфрамовые и не которые содержат вольфрама. Вольфрамовый продукт является смесьюпорошкообразного технического вольфрама либо высоко процентного ферровольфрама с науглероживающими материалами. Отечественный сплав этого типа носит название «вокар».
Изготовляются подобные сплавы следующим образом: порошкообразный технический вольфрам либо высокопроцентный ферровольфрам смешивают с этими материалами, как сажа, молотый кокс и т. п.; взятую смесь замешивают в густую пасту на смоле либо на сахарной патоке. Из смеси прессуют брикеты и легко обжигают их до удаления летучих веществ. По окончании обжига брикеты размалывают и просеивают.
Готовый продукт имеет форму тёмных хрупких крупинок величиной 1—3 мм. Характерным показателем вольфрамовых продуктов есть их большой насыпной вес.
В Советском Альянсе изобретен порошкообразный сплав, не содержащий вольфрама и потому очень недорогой. Сплав носит название «сталинит»; он очень обширно распространен в отечественной индустрии. Долгая практика продемонстрировала, что, не обращая внимания на отсутствие вольфрама, сталинит владеет высокими механическими показателями, во многих случаях удовлетворяющими техническим требованиям.
Помимо этого, благодаря низкой температуре плавления (1300—1350 °С) сталинит имеет значительное преимущество перед вольфрамовым продуктом, что расплавляется только при температуре около 2700 °С. Низкая температура плавления сталинита облегчает наплавку и повышает производительность этого процесса.
Базой сталинита есть смесь порошкообразных недорогих ферросплавов, ферромарганца и феррохрома. Процесс изготовления сталинита такой же, как и вольфрамовых продуктов. Сталинит содержит 16—20% Сг и 13—17% Мп.
Твердость наплавки для вокара HRC 80-82, для сталинита HRC 76—78.
Наплавка сталинита производится угольной дугой по методу Бенардоса. Газовая горелка непригодна для наплавки, поскольку газовое пламя сдувает порошок с места наплавки. Подробность, подлежащую наплавке, подогревают до начала красного каления, носле чего на поверхность подробности насыпают сталинит равномерным слоем толщиной 2—3 мм. Для получения верных граней и краёв наплавки используют ограничители и специальные шаблоны из красной меди, графита либо угля.
На насыпанном слое зажигают Угольную дугу постоянного тока обычной полярности при силе тока 150—200 а. Наплавку ведут непрерывно, без обрывов дуги, и по возможности без повторного расплавления наплавленного слоя.
Ввиду достаточно большого расплавления главного металла угольной дугой первый слой наплавки не снабжает нужных особенностей и владеет недостаточной твердостью, исходя из этого наплавку сталинита ведут в два, а время от времени и в три слоя. По окончании наплавки слоя, не давая ему остыть, на него насыпают новый слой сталинита и создают наплавку, а после этого — замедленное охлаждение чтобы не было образования трещин в наплавленном слое, для чего тёплую подробность помещают в золу, сухой песок, хлопья асбеста, слюды и т. п. По окончании окончания наплавки рекомендуется наплавленную подробность отжечь при температуре около 900° С в течение 2—3 ч. Отжиг приводит к распадению остаточного аустенита, образующегося при наплавке, с выпадением добавочных карбидов и увеличением твердости наплавки на две-три единицы по Роквеллу; в один момент устраняются внутренние напряжения. За отжигом направляться замедленное равномерное охлаждение подробности.
Ввиду дешевизны продукта, и высокой производительности и простоты процесса наплавки сталинит очень активно используется в отечественной индустрии для самых разнообразных наплавочных работ. Сталинитом наплавляют части всевозможных автомобилей и механизмов, подвергающиеся стремительному износу в работе,— штампы, рабочие части автомобилей для горных пород и обработки грунтов (землечерпалок, экскаваторов), зубки врубовых автомобилей и т. п. Нанлавку вокара создают подобно наплавке сталинита.
Керамические, либо спеченные жёсткие сплавы — наиболее значимый вид жёстких сплавов, владеющих высокой твердостью, HRC 86—90, имеют ответственное значение для обработки металлов резанием, в основном для оснащения металлорежущего инструмента. Керамические сплавы изготовляют на особых фабриках. Базой их, придающей им высокую твердость, являются карбиды вольфрама, других элементов и титана.
Карбиды, изготовляемые в особых электрических печах, подвергаются очень узкому размолу, до небольшого порошка. Порошкообразный карбид цементируется железным кобальтом либо никелем, владеющим большой пластичностью, исходя из этого керамические сплавы менее хрупки, чем другие виды жёстких сплавов, лучше выносят ударную нагрузку и дают стойкое острие лезвия металлорежущего инструмента, удачно обрабатывающее самые жёсткие сорта металлов и сохраняющее стойкость при нагреве до светло-красного каления.
Количество связки, т. е. кобальта либо никеля, в разных марках образовывает 3—15%, другое карбид. В Советском Альянсе самый известен керамический жёсткий сплав победит, представ-чяющий собой карбид вольфрама, сцементированный кобальтом. Д тя изготовления металлокерамических сплавов узкий порошок карбида шепетильно смешивают с узким порошком кобальта либо никеля в надлежащей пропорции.
Из взятой смеси прессуют пластинки hi другие изделия. Спрессованные изделия подвергают предварительному обжигу, по окончании чего эти изделия приобретают некую прочность, но еще легко поддаются механической обработке — доводке, которой придают изделиям окончательные размеры; второй окончательный обжиг придает изделиям большую твёрдость и механическую прочность. По окончании окончательного обжига металлокерамические сплавы смогут обрабатываться только абразивами высших сортов и не поддаются никакой термообработке.
Керамические сплавы чувствительны к высокому перегреву. При нагреве до через чур большой температуры начинает плавиться кобальтовая либо никелевая связка, связь между зернами карбида ослабляется, в массу сплава попадает кислород воздуха, что создаёт окисление металла. В следствии сплав теряет механическую прочность, трескается и рассыпается при работе.
Сплав, сломанный благодаря перегрева, нельзя исправить последующей • обработкой, что делает неосуществимой приварку пластинок к державке металлорежущего инструмента. При температуре, нужной для расплавления сплава либо как минимум для расплавления стали державки, пластинка керамического сплава портится и теряет прочность.
Пластинки керамических сплавов припаивают к державке медью при температуре (температуре плавления меди 1083° С), надёжной для прочности керамического сплава, не ухудшающей его структуры. Хорошие результаты дает пайка медью в воздухе водорода. Припайка пластинок керамических сплавов может производиться кроме этого на электрических контактах сварочных автомобилей.
Плавленые карбиды владеют наивысшей твердостью, до HRC 92—94, но одновременно и большой хрупкостью. По составу эти сплавы являются чистый сплавленный карбид вольфрама, время от времени с добавками вторых веществ. Сплавы отличаются большой температурой плавления (—3000° С); выпускаются в форме кусков с острыми гранями.
Основная область их применения — горная индустрия, где они помогают для оснащения буровых долот и другого бурового инструмента, в особенности для жёстких горных пород.
Куски сплава ввариваются в углубления на поверхности изделия так, дабы режущая грань кусочка сплава пара выступала над поверхностью главного металла. Пространство между кусочками сплава заполняют наплавкой литого либо порошкообразного сплава. При работе инструмента промежуточный жёсткий сплав изнашивается стремительнее, и режущая грань кусочков плавленых карбидов, выступая над поверхностью инструмента, режет горную породу.
Для наплавки этих сплавов удачно употребляется индукционный наг гул. Сплав помещают на поверхность металлического инструмента, высокочастотный индуктор расплавляет поверхность стали и вплавляет в нее зерна сплава.