Операции по изменению свойств металла
К операциям по трансформации особенностей металла готовых изделий либо их частей для лучшего применения в производстве относятся:
— упрочнение поверхности изделий методом цементации либо электронаплавки графита и твёрдых сплавов;
— увеличение твердости рабочих частей режущих отдельных деталей и инструментов методом их отпуска и закалки;
— мягкости металла и повышение вязкости методом его нормализации и отжига.
Цементацией именуется насыщение углеродом поверхности изделий из стали с низким содержанием углерода (до 0,2%) для увеличения их прочности и твёрдости.
Цементация используется для обработки инструментов, тех деталей и штампов, каковые по собственному назначению должны иметь жёсткую наружную поверхность. Жёсткая поверхность позволяет подробностям лучше сопротивляться износу при трении, а сохраняющаяся мягкая сердцевина — выдерживать нагрузку от ударов (не раскалываться).
Цементация основана на появляющемся у стали и железа при нагреве до 850—900° свойстве растворять углерод и поглощать его в пределах поверхностного слоя. При насыщении углеродом поверхность выработанного из железа либо стали изделия делается более жёсткой.
При производстве цементации та часть поверхности изделия, которая не подвергается цементации, должна быть покрыта предохранительным слоем (к примеру глины). Подготовленное для цементации изделие помещают в большинстве случаев в металлический коробку и засыпают обрабатываемую поверхность так называемыми карбюризаторами. На дно коробки хорошо укладывают слой карбюризатора в 20—30 мм, на него кладут изделие и поверх укладывают второй слой карбюризатора толщиной 10—20 мм.
Такая укладка именуется «пакетом». Самый распространенными карбюризаторами являются смеси древесного угля (70 частей) и соды (30 частей) либо древесного угля (50 частей), каменного угля •(20 частей) и сажи (3 части).
Ящик с обрабатываемым карбюризаторами и изделием устанавливается на горне. По окончании того как температура в горне достигнет нужной высоты (до 900°), ящик выдерживается некое время на горне, в зависимости от желаемой глубины цементированного слоя, а после этого охлаждается. Для прогрева пакета в большинстве случаев требуется приблизительно 1,5—2 часа на каждые 100 мм высоты либо ширины пакета.
Температуру нагрева осуществляют контроль особыми устройствами — пирометрами либо кладут вместе с пакетами металлические коробки с кальцинированной содой либо с солями калия либо бария либо фтористого натрия. Каждое из этих веществ имеет различную температуру плавления (в общем от 850 до 990°). Одну коробку берут с солью, имеющей точку плавления, близкую к температуре цементации, другую — с солью с точкой плавления, превышающую предельную температуру для цементации.
Первая соль при достижении нужной температуры будет в расплавленном состоянии, вторая — в жёстком. По трансформациям состояния второй соли возможно делать выводы о наличии перегрева. Вся операция занимает от 4 до 8 часов.
Для стремительной цементации в большинстве случаев используют желтую кровяную соль. Порошок данной соли насыпается на раскаленную Поверхность изделия, температура поднимается до 700—800°, по окончании чего обрабатываемое изделие охлаждается в воде.
По окончании цементации изделие подвергают закалке при отпуску 760—780° и температуре при температуре 160—180° (см. ниже). Обработка подробностей, предназначенных для цементации, производится с припуском.
При термической обработке металлов нужно оберегать кожу от брызг и, независимо от этого, смазывать руки и лицо мазями, защищающими от ожогов и изъязвлений. Дабы предотвратить расплескивание электролита, направляться наливать его не более чем на 75% емкости ванн.
Решающую роль в технике безопасности играется прекрасно устроенная вентиляция как неспециализированная (всего помещения), так и особая (отсосные приспособления у установок и ванн). При работе с вредными смесями направляться, помимо этого надевать фартук, перчатки, сапоги из резины и соответствующий респиратор либо особый шлем.
Для допуска к термохимической обработке металлов нужно сдать соответствующий техминимум.
Термохимическая обработка инструментов и поверхностей деталей с целью их упрочнения требует особых площадей для установки горнов либо печей, большой траты времени на нагревание и возможно применена не для всех марок стали. Исходя из этого на данный момент в отечественной индустрии приобретает распространение электроискровой метод упрочнения поверхностей, что не имеет перечисленных недочётов.
Электроискровое упрочнение производится на установках и специальных станках и вручную при помощи маленьких (весом до 200 г) устройств, именуемых вибраторами.
Для покрытия поверхности изделия употребляется вставляемая в прибор пластинка жёсткого сплава (титановые сплавы Т15К6, Т30К4) либо графита (ЭГ2).
Эта пластинка представляет собой один из двух используемых в большинстве случаев в электроискровой установке электродов — анод.
Графитовые электроды используются для упрочнения чистовых инструментов, поскольку они снабжают лучшую чистоту поверхности упрочненного слоя, чем жёсткие сплавы.
Схема электроискрового упрочнения пара отличается от схем при электроискровом резании металла (сверлении и резке). Процесс обработки проходит в воздухе и не требует особых растворов (рабочих жидкостей).
Упрочняющий электрод (жёсткий сплав, графит) есть анодом установки либо вибратора, а обрабатываемое изделие катодом.
Электроды иногда в следствии вибрации размыкаются’и замыкаются (при питании установки либо прибора постоянным током). Появляется искра, которая переносит частицу анода на поверхность обрабатываемого изделия.
В большинстве случаев вибраторы складываются из подвижной части — якоря 2 с электрододержателем 1, упрочняющим неподвижной катушкой и электродом 4 с сердечником, которая включается в сеть (конкретно либо через понижающий трансформатор).
Обработка изделия вибратором производится следующим образом:
— очищенное от ржавчины и загрязнений и легко натертое маслом изделие помещается в тиски либо второе зажимное приспособление;
— включается предварительно проверенный и установленный на нужный режим (по ёмкости и току) вибратор со засунутой в него пластинкой жёсткого сплава либо графита; – держа вибратор в руке, приводят его упрочняющий электрод в соприкосновение с поверхностью изделия до происхождения искры; перемещают электрод по упрочняемой поверхности справа на протяжении нее, а позже поперек — до тех пор пока желтые искры не сменятся ярко-голубыми.
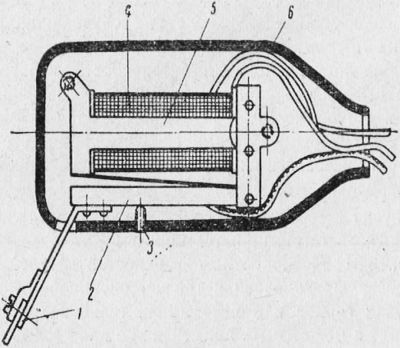
Рис. 1. Вибратор завода «Электросила»: 1 — электрододержатель с упрочняющим электродом, 2—якорь, 3 — винт для регулирования вибрации, 4 — катушка, 5 — магнитопровод, 6 — пластмассовый корпус вибратора
При упрочнении рабочей части режущего инструмента направляться избегать замыкания упрочняющего электрода с лезвием. По окончании завершения работы и по окончании выключения вибратора нужно разрядить конденсаторы прибора, прикоснувшись им к обрабатываемой подробности.
На протяжении работы с приборами и электроискровыми установками нужно пользоваться защитными очками и резиновыми перчатками. К работе смогут допускаться лица, предварительно сдавшие особый техминимум.
Использование электроискрового метода для упрочнения металла быстро повышает производительность труда. Производительность вибратора снабжает обработку 2 см2 поверхности з одну 60 секунд при толщине слоя покрытия 60—80 микрон. Электронаплавка жёсткого сплава на рабочую часть режущего инструмента занимает 0,5—1,5 мин. Электроискровое покрытие отличается хорошей схватываемостью с металлом изделия.
Режущий инструмент, покрытый электроискровым методом, получает прочность в 2—4 раза выше начальной.
Закалка содержится в нагревании стали до красного каления (к примеру углеродистой стали до 700—800°), в выдержке ее при данной температуре для прогрева и стремительном после этого охлаждении в струе воздуха, воде, масле либо каком-либо втором охлаждающем веществе.
Время выдержки для прогрева зависит от размеров закаливаемого изделия и образовывает приблизительно по 30 сек. на 1 мм диаметра для цилиндрических подробностей, 45 сек. на 1 мм для изделий мин и квадратного 1 сечения. на 1 мм для пластин.
Цель закалки стали — придание ей высокой твердости. Закалка производится в горнах, печах, расплавленных солях, свинце.
При охлаждении нагретого изделия в жидкости нужно двигать его, дабы уничтожить этим образующуюся около зака ливаемого предмета газовую либо паровую рубаху.
В случае если закаливается лишь часть изделия, то ее опускают в охлажденную жидкость на нужную глубину и перемещают изделие вверх и вниз, поскольку в противном случае на уровне погружения может появиться трещина.
Нужная высота температуры нагрева определяется особой аппаратурой (пирометрами). При наличии опыта определение высоты температуры производится на основании последовательной смены цвета закаливаемого изделия по окончании того, как температура поднимается выше 500 °С.
Так как под действием закалки сталь приобретает высокую твердость и делается хрупкой, то, дабы уменьшить хрупкость закаленной стали, ее «отпускают», другими словами создают операцию отпуска.
Отпуск содержится в повторном нагревании по окончании закалки изделий из углеродистой стали до 200—300° С, а из быстрорежущей до 560—600° С, с последующим охлаждением, как и при закалке. Цель отпуска — уничтожение хрупкости закаленной стали.
Температуру отпуска для углеродистых сталей возможно приближенно определять по цветам «побежалости», появляющимся на чистой поверхности закаленного металлического изделия при его нагревании до температуры 330°.
При появлении цвета побежалости, отвечающего заданной температуре отпуска, изделие охлаждают.
При термической обработке довольно часто совмещают отпуск и закалку. В этом случае, не позволяя охладиться закаливаемому изделию ниже температуры, достаточной для отдыха закаленной части (200—600°, смотря по марке стали), вынимают его из охлаждающей жидкости и скоро зачищают часть его поверхности шкуркой либо трением о камень либо песок. После этого следят за возникновением цветов побежалости на зачищенном месте и, если судить по цвету побежалости, совсем охлаждают изделие.
Возможно в зависимости от событий поступать и без того: охладить закаливаемый предмет всецело и снова нагреть до нужной при отпуске температуры. При таком методе отпуска внутренняя часть закаливаемого изделия получается более жёсткой.
Ото/сиг пребывает в нагревании стали до мрачно- либо светло-красного цвета с последующим медленным охлаждением вместе с печью либо в раскаленном песке, золе и других веществах, слабо проводящих тепло. Отжиг помогает для уничтожения избыточной твердости металла. Сталь по окончании отжига делается мягче и легче обрабатывается режушим инструментом.
Температура при отжиге зависит от состава отжигаемой стали (от 750 до 860°). Чем больше находится в стали углерода, тем ниже должна быть температура отпуска и тем медленнее необходимо ее нагревать и охлаждать.
В случае если требуется, дабы сталь в изделии имела повышенное сопротивление разрыву и легко обрабатывалась режущим инструментом, ее подвергают нагреву до красного каления, но пара более высокому (на 25—50°), чем для отжига. Такая обработка именуется нормализацией стали.
Сейчас в производстве все шире внедряется термическая обработка изделий (закалка, отпуск, нормализация и отжиг) при помощи электрических индукционных токов высокой частоты (т. в. ч.). Эти токи, имея высокую концентрацию, дают высокие температуры, причем время для нагревания очень незначительно. Громадное удобство применения токов высокой частоты содержится в простоте нужных для этого устройств.
При закалке токами высокой частоты обрабатываемую подробность помещают в особое приспособление (воображающее собой индукционную катушку в виде навитой бронзовой проволоки), к которому подводятся токи высокой частоты. В следствии действия токов поверхность подробности скоро и очень сильно нагревается. По окончании нагревания подробность охлаждают, помещая в особую среду (раствор либо воду).
На рис. 2 продемонстрировано приспособление для применения токов высокой частоты, именуемое индуктором.
При работе с токами высокой частоты нужно предварительно пройти особый техминимум.
Рис. 2. Виды индукторов для закалки подробностей т. в. ч.