Отливки из высоколегированных сталей
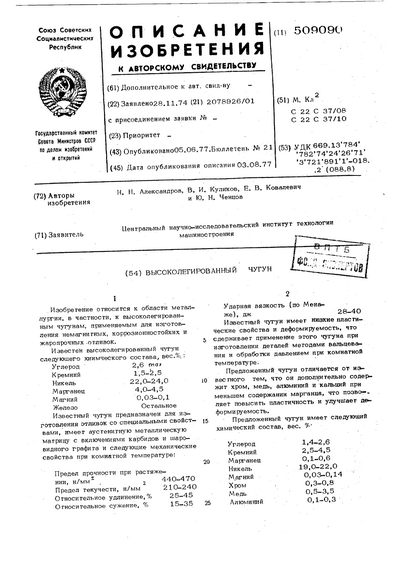
Отливки из высокомарганцовистой стали 110П3Л. Среди высоколегированных сталей, используемых для изготовления фасон-пых отливок, сталь 110П3Л взяла громаднейшее распространение; по структуре она относится к аустенитному классу. Устойчивая аустенитная структура образуется в Fe-Mn-C сплавах, содержащих 1,0-1,3% С и 9-15% Мп.
Медлительно охлажденные сплавы этого состава складываются из карбидной фазы и аустенита переменного состава (Fe, Мп)3С. Аустенит представляет собой верный раствор замещения марганца в железе, в котором угле-поппНаХ0ДИТСЯ между узлами кристаллической решетки. Отливки одвергают закалке (нагрев до 1050-1100° С и охлаждение в хо-
Неповторимым свойством стали есть высокое сопротивление износу при работе в условиях ударных либо высоких статических нагрузок, в то время, когда сталь наклёвывается и твердость ее возрастает до НВ 500-600. Упрочнение стали при наклепе вызывается разделением зерна аустенита на небольшие блоки, выпадением дисперсных карбидов, а кроме этого превращением по плоскости сдвигов аустенита в мартенсит. Склонность к наклепу делает эту сталь труднообрабатываемой.
Своеобразные особенности стали 110П3Л выяснили практическую область ее применения. Из данной стали в главном изготовляют отливки сердечников стрелочных крестовин и переводов ЖД (в основном, трамвайных) дорог, сменных подробностей щековых и конусных дробилок, экскаваторов и многих вторых автомобилей.
Повышение кремния, желательное для увеличения износостойкости, приводит к образованию трещин. сера и Фосфор отрицательно воздействуют на эксплуатационные и технологические особенности, исходя из этого их содержание должно быть минимальным.
Выплавку стали 110П3Л возможно осуществлять в дуговых и мартеновских печах, конвертерах с боковым либо верхним дутьем. В зависимости от конкретных условий производства (наличие плавильных агрегатов, шихтовых материалов) и требований, предъявляемых к качеству отливок, высокомарганцовистую сталь возможно взять: 1) из свежих материалов в главных электродуговых либо мартеновских печах; 2) переплавом в тех же печах лома и отходов производства данной стали; 3) заливкой низкоуглеродистой перегретой стали в ковш с разогретым кусковым ферромарганцем; 4) смешением в ковше низкоуглеродистой стали с расплавленным (в вагранке либо втором агрегате) ферромарганцем.
Процесс плавки состоит как бы из двух этапов:
1) получения низкоуглеродистой стали (0,10-0,15% С) и
2) легирования данной стали марганцем.
По окончании расплавления при обычном содержании углерода (не ниже 0,4%) выполняют кипение металла при помощи металлической руды либо газообразного кислорода.
При применения низкоуглеродистой шихты, в то время, когда в ванне по окончании расплавления содержание углерода не превышает 0,15%, а фосфора 0,035%, передельный чугун не додают, кипение не выполняют. По окончании разогрева ванны удаляют окислительный шлак и реализовывают раскисление. Но такая сталь (без окисления) менее качественна и возможно использована лишь для неответственных отливок.
По окончании удаления окислительного шлака выполняют предварительное раскисление силикомарганцем либо ферросилицием и ферромарганцем. После этого загружают флюсы для образования белого шлака (известь, плавиковый шпат, молотый дроблёный ферросилиций и кокс) и перемешивают ванну. Ферромарганец для легирования вводят в 3-4 приема.
В печи под белым шлаком протекает диффузионное раскисление: сталь очищается от закиси марганца,отрицательно воздействующей на ее эксплуатационные и технологические особенности. Окончательное раскисление стали выполняют на желобе печи алюминием (0,8-1,0 кг алюминия на 1 т металла).
В больших сталелитейных цехах, специализирующихся на выпуске отливок из стали 110П3Л, а кроме этого приобретающих металлический лом данной марки, довольно часто используют способ переплава. В этом случае шихту составляют на 90-100% из лома и отходов производства и лишь до 10% -из низкоуглеродистой стали (додают для корректировки содержания углерода в готовой стали). В качестве шлакообразующего материала применяют известь, вводя ее при завалке и в период расплавления.
По окончании расплавления выполняют предварительное раскисление ванны кусковым ферросилицием. После этого в печь вводят смесь извести, плавикового шпата, дробленого ферросилиция, в предстоящем вместо ферросилиция применяют молотый кокс. Сталь до заданного состава по марганцу доводят за 10-15 мин до выпуска стали.
Длительность выдержки под белым шлаком и требования к шлаку остаются теми же, что и при выплавке стали из свежих материалов.
Особенности технологического процесса получения отливок из стали 110П3Л определяются своеобразными особенностями этого сплава. Поверхностное натяжение данной стали ниже, чем углеродистой в 1,5 раза. Высокомарганцовистая сталь если сравнивать с углеродистой характеризуется громадным коэффициентом термического сжатия (в 2 раза) и меньшей (в 2 раза) теплопроводностью.
Низкая теплопроводность стали делает неосуществимой сквозную закалку стенок отливок толще 120-150 мм. Также, в толстом сечении металл имеет пониженные особенности благодаря сильной транскристаллизации и ликвации углерода, фосфора, серы. Исходя из этого толщину стенок отливки рекомендуется назначать до 120 мм.
Принимая к сведенью повышенную литейную усадку стали, в состав формовочных смесей довольно часто вводят опилки, используют оболочковые стержни, т.е. делают все возможное для повышения податливости формы. Учитывая возможность химического сотрудничества окиси марганца с кремнием, кварцевый песок в составе облицовочных смесей время от времени заменяют молотым магнезитом.
Высокомарганцовистая сталь из-за присутствия закиси марганца агрессивна и по отношению к шамотной футеровке сифонного устройства и ковша. Исходя из этого для обеспечения разливки нужно использовать магнезитовые либо стаканчики и графитовые пробки. Не обращая внимания на высокую жидкотекучесть стали 110П3Л, разливку ее по формам нужно проводить с громадной скоростью, дабы исключить большое окисление.
Заливка с громадной скоростью повышает пластические особенности стали, трещино-устойчивость, сокращает пригар. Большая усадка, интенсивное развитие ее в промежутке, близком к температуре кристаллизации, пластичность и низкая прочность при больших температурах обусловливают громадную склонность стали 110П3Л к трещинообразованию.
Для борьбы с тёплыми трещинами, не считая повышения податливости формы, целесообразно снижать до минимума содержание кремния, серы и фосфора, уменьшать окисленность металла, осуществлять упрочнение не сильный мест холодильниками, усадочными ребрами. Из-за высокого коэффициента и низкой теплопроводности термического сжатия в отливках появляются громадные термические напряжения, каковые вместе с повышенной хрупкостью (в литом состоянии благодаря присутствию карбидов) довольно часто являются обстоятельством образования холодных трещин. Для борьбы с холодными трещинами применяют разные методы выравнивания скоростей охлаждения разных узлов отливки.
Для получения высоких пластических, прочностных особенностей все отливки подвергают закалке в холодной проточной воде. Качественное проведение закалки снабжает получение одно-казной аустенитной структуры. Исправление недостатков заваркой поизводится по окончании закалки отливки, в нагретом состоянии.
Заваренная отливка подвергается повторной закалке.
Корозионностойкие отливки изготовляют из высоколегированных хромистых, хромоникелевых и никельхромистых сталей. Довольно часто для улучшения особенностей этих сталей их дополнительно легируют Mo V, Mn, Си, Ti, N, В, W. Химические особенности металлов зависятот их сродства к кислороду и от свойства пассивироваться (образовывать на поверхности плотную, прочную пленку окислов, разобщающую главный металл от агрессивной среды).
В высоколегированных сталях хром информирует им свойство пассивироваться в окислительных средах. Увеличение коррозионной стойкости стали при легировании хромом происходит скачкообразно при концентрации хрома в феррите, равной V8 моля. Предстоящее заметное увеличение коррозионной стойкости отмечается при содержании в феррите 2/8, 3/8 и т. д. моля хрома (что соответствует 11,7; 23,4; 35,1 вес. %).
При таких концентрациях хрома электродный потенциал увеличивается скачкообразно, быстро изменяются химические особенности сплава и на поверхности стали вместо рыхлого слоя окислов железа появляется плотная узкая пленка окислов хрома. Эта пленка и снабжает высокую коррозионную стойкость хромсодержащих сталей в окислительных средах.
Никель имеет более большой электродный потенциал, т.е. меньшее сродство к кислороду, чем железо. При сплавлении никеля с железом кислотостойкость передается сплаву.
Стали ферритного класса (15Х25ТЛ, 75Х28Л, 185Х34Л) являются кислотостойкими и одновременно жаростойкими, предназначаются для того чтобы химического машиностроения, не подвергающихся громадным механическим нагрузкам. Низкие механические особенности обусловлены крупнозернистым строением, а увеличение концентрации хрома в феррите снижает его пластичность.
Стали аустенитного класса (10XI8Н9ТЛ, 10XI8Н9Л, 5XI8Н9Л, 15Х25Н19СЛ, 45XI7ПЗНЗЮЛ, 55XI8П4СТЛ и др.) владеют большой коррозионной стойкостью. Чисто аусте-нитная структура в стали, содержащей 18% Сг, получается при введении не меньше 8% Ni (время от времени часть никеля возможно заменена вторыми, менее дефицитными аустенитизирующими элементами, к примеру азотом, марганцем). Предельное равновесное количество углерода, растворимое в аустените данной стали, образовывает 0,02- 0,03%.
Избыточный углерод возможно переведен в жёсткий раствор закалкой от 1000-1050° С. Для предотвращения выделения карбидов хрома сталь «стабилизируют» сильными карбидообра-зующими элементами (Ti, Та либо Nb). Хром в этом случае всецело остается в жёстком растворе, в результате возрастает стойкость против межкристаллитной коррозии. Аустенитная хромо-никелевая сталь есть кислотостойкой и используется для изготовления разной арматуры химической индустрии, коллекторов выхлопных совокупностей, печной арматуры, трудящейся в среде агрессивных газов, подробностей паровых и газовых турбин и т. д.
Стали аустенитно-мартенситного класса используются как кор-розионностойкие (5XI4Н7МЛ) для подробностей, действующий при обычных и низких температурах, и как кислотостойкий (10XI8НГЛ), рекомендуемые в целях экономии никеля для замены стали 10XI8Н9Л.
Стали аустенитно-ферритного класса (10Х25Н5ТМФЛ, 25Х23Н7СЛ, 30Х24Н12СЛ). Структура, складывающаяся из зерен феррита, окаймленного аустенитом, обусловливает высокие прочностные особенности, удовлетворительную пластичность по окончании соответствующей термической обработки. Эти стали, владеющие в один момент кислотостойкостью и жаростойкостью при температурах до 600-1000° С, употребляются для того чтобы подробностей химического оборудования, оборудования нефтеперегонных фабрик, других деталей и лопаток компрессоров, действующий при давлении и высоких температурах.
Выплавка высоколегированных хромистых, хромоникелевых и никелехромистых сталей проводится в главных мартеновских и электродуговых печах. При изготовлении маленьких отливок очень важного назначения стали выплавляют в индукционных вакуумных печах. В качестве шихты применяют как свежие материалы, так и отходы высоколегированных сталей литейных цехов машиностроительных, металлургических фабрик, металлический высоколегированный лом.
Предупреждение чрезмерного угара хрома, получение в стали низкого содержания углерода (0,10- 0,12%) и допустимой газонасыщенности приводят к при переплаве высокохромистых, хромоникелевых, хромоникель-молибденовых и вторых сплавов.
молибден и Никель не окисляются на протяжении плавки, а титан (если он присутствует в шихте) выгорает всецело.
При переплаве хромсодержащих отходов в главной мартеновской печи науглероживание вероятно за счет сажистого углерода. Главные положения разработки переплава хромсодержащих ходов в главных мартеновских печах по опыту завода «Серп молот», заключаются в следующем. 2 П Реплав разрешается лишь при тёплом ходе печи. воздГНИчМгГ Все вероятные меры к понижению подсоса в печь приема3V ПР°ИВ°ДЯТ тщательную завалку-укладку шихты в три (на подину — легкую, после этого тяжелую и опять легкую)
с прогревом каждой части в течение 10-15 мин. 4. Процесс плавления ведут форсированно, с применением всей тепловой мощности печи. 5. К. финишу плавления продувают жидкий металл сжатым воздухом либо кислородом, каковые вводят под шлак. Продувку выполняют до получения в стали углерода на 0,01-0,02% ниже верхнего предела. В один момент окисляется и хром. Содержание Сг203 в шлаке к финишу продувки образовывает 30-45%.
6. Шлак раскисляют молотым 75%-ным ферросилицием. Оставшееся количество Сг203 в шлаке не должно быть больше 3-6%. 7. Сталь перегревают, вводят нужное количество хрома в виде ферросплавов (ФХ001, ФХ002).
8. Раскисление металла создают 45%-ным ферросилицием на желобе и в ковше алюминием. Кроме этого в ковш вводят ферротитан с учетом угара 50% титана.
Угар хрома при переплаве хромсодержащих отходов в главной мартеновской печи по обрисованной выше технологии образовывает 25-20%. В фасонно-сталелитейных цехах, изготовляющих отливки из коррозионностойких, жаростойких и жаропрочных сталей, в качестве плавильных агрегатов довольно часто используют главные дуговые электропечи.
Шихту для плавок без окисления, согласно данным Ф. П. Еднерала, составляют из 70-80% легированных стали и 30-20% отходов с низким содержание углерода. Состав шихты рассчитывают на получение по окончании расплавления завалки содержания углерода не выше нижнего предела, установленного для стали данной марки. За время плавления металл науглероживается на 0,03%. С целью уменьшения науглероживания за счет электродов рекомендуется применять лишь графитизированные электроды высшего качества.
Легирующие добавки загружают в печь совместно со всей шихтой. Во время плавления загружают прокаленный известняк (-4% от массы садки).
Отсутствие кипения в плавках без окисления заставляет предъявлять очень высокие требования к качеству шихтовых материалов. В случае если по окончании расплавления состав металла близок к расчетному, то приступают к раскислению шлака молотым коксом, древесным углем, алюминием и ферросилицием в зависимости от кремния и содержания углерода. Легирующие элементы восстанавливаются и переходят в металл.
Данный процесс выполняют под белым либо карбидным шлаком.
На практике используют действенную выплавку стали из высокохромистых отходов с окислением углерода кислородом. В этом случае шихту составляют из 70-80% отходов стали 10XI8Н9ТЛ или других отходов кремнистых либо хромокремни-стых сталей (должно быть 1,0-1,3% Si для защиты от окисления хрома и марганца), железной руды и никеля (35 кг1т). Оптимальное содержание углерода по окончании расплавления 0,2%.
Продувку ванны кислородом начинают по окончании расплавления 3/4 завалки и продолжают до полного расплавления. Расплавление заканчивается и перегрев ванны осуществляется за счет тепла окисле
ия кремния, железа и хрома. Предстоящую продувку ванны кислородом выполняют с целью понижения содержания углерода до q 07-0,10%. В один момент окисляется оставшееся количество кремния, содержание хрома в металле значительно уменьшается на 5-6%. Часть окислов хрома восстанавливается при обработке шлака силикокальцием, ферросилицием либо силикохромом.
Недостающее количество хрома вводится в ванну безуглеродистым феррохромом. Ферротитан вводят либо в струю металла при выпуске либо в ванну по окончании скачивания шлака.
Высоколегированные хромистые и хромоникелевые (корро-зионностойкие, жаростойкие и жаропрочные) стали разных марок слабо отличается друг от друга по литейным особенностям. В связи с этим технологические процессы изготовления отливок очень схожи. Жидкотекучесть хромистых и хромоникелевых высоколегированных сталей выше, чем углеродистых с соответствующим содержанием углерода.
Повышение жидкотекучести связано с более низкими значениями у легированных сталей температуры солидуса (на 50-20°) и ликвидуса (на 70-30°) если сравнивать с углеродистыми сталями.
Но, не обращая внимания на хорошую жидкотекучесть, формы нужно заливать сталью с громадным перегревом и скоро. скорости заливки и Увеличение температуры позвано склонностью сталей данной группы к пленообразованию. Наличие плен, состоящих в основном из окислов железа и хрома, не лишь ухудшает условия заполнения полости формы, но возможно обстоятельством падения качества отливки из-за нарушения ее повышенной склонности и сплошности к пригару.
Дабы предотвратить получение плен и включений в отливках со средней толщиной стенок, сталь разливают скоро при 1580-1600° С. Конструкция литниковой формы и системы, выбор способа и места подвода металла должны снабжать плавное перемещение металла, не допускать образования встречных потоков.
С целью уменьшения окисления в период пригара и заливки целесообразно формы окрашивать красками, создающими восстановительную воздух, использовать облицовочные смеси на базе хромистого железняка, циркония и хромомагнезита. Повышенная температура заливки приводит к формированию неотёсанной первичной структуры, которую довольно часто нереально поменять термической обработкой благодаря отсутствия у последовательности сталей фазовых превращений. Измельчение первичного зерна достигается модифицированием стали и дополнительным легированием (Mg, N, В, Ti, Zr).
Высокая температура заливаемой стали, пониженная ее теплопроводность, стремительное заполнение формы содействуют образованию громадных (если сравнивать с углеродистой сталью) усадочных раковин, что требует повышения размеров доходов. При производстве отливок из высоколегированных хромистых и хромо-икелевых сталей особенно действенны все меры по уменьшению расхода жидкого металла (дополнительный разогрев металла в прибыли, применение повышенного воздушного и газового давления и др.) — Громадная растворимость газов и трудность их удаления из затвердевающей отливки благодаря повышенной вязкости стали довольно часто являются обстоятельством образования в отливках газовых раковин.
Линейная усадка кислотостойкий, жаростойких и жаропрочных сталей изменяется в широких пределах в зависимости от их структуры. Большую усадку имеют стали аустенитного класса, а минимальную — стали мартенситного класса.
Низкая теплопроводность, крупнозернистое строение, прочность и недостаточная пластичность при больших температурах приводят к повышенной склонности высоколегированных никелем и хромом сталей к образованию тёплых трещин, исходя из этого литейная форма обязана владеть максимально достижимой податливостью. Хромистые стали практически всех классов (по структуре) склонны к образованию холодных трещин. Обстоятельством этого есть повышенная хрупкость из-за наличия карбидов, с-фазы.
Намного меньше опасность образования холодных трещин в сталях аустенитного класса, в основном, из-за низкого предела упругости и относительно хорошей пластичности. Многие отливки подвергаются разным сложным видам термической обработки, режим которых определяется назначением отливки и химическим составом стали.