Пайка миниатюрных изделий
Одним из самый распространенных способов создания неразъемных соединений миниатюрных изделий, присоединения узких контактных лепестков, микропроводов, разных микроэлементов есть пайка. Широкое использование пайки обусловливается надёжностью и прочностью создаваемых соединений, стойкостью к вибрационному и коррозионному действию.
Пайка миниатюрных изделий характеризуется рядом своеобразных изюминок. Ввиду малых размеров имеет место большая опасность пережога и перегрева изделий, приводящие к браку. Исходя из этого количество подводимого тепла должно быть строго дозировано.
Ввиду малых размеров поверхностей соприкосновения поток подводимого тепла должен быть локализованным, что требует применения особых малогабаритных паяльных устройств.
Время теплового действия ограничено, что приводит к необходимости применения импульсного подвода тепла и пайки с регулируемыми режимами. Используемые припои должны быть низкотемпературными, а флюсы не приводить к.
Малые размеры изделий обусловливают использование особых приёмов и способов пайки. Так, к примеру, на соединяемые поверхности предварительно наносят слой припоя либо паяльной пасты. При соединении данный Слой расплавляется посредством электрически нагреваемого электрода, потоком тёплого воздуха либо пучком света, сконцентрированным в место пайки.
Данный метод используют для присоединения малых по размеру элементов к узким (в пара микрон) напыленным пленкам, к примеру при пайке гибридных интегральных схем. Он довольно легко подается автоматизации, а количество подводимого тепла возможно дозировать.
В качестве соединяющих материалов при пайке миниатюрных изделий применяют низкотемпературные припои на базе олова и других химических элементов, смеси на базе галлия, токопроводящие пасты на базе полимерных смол с добавками тонкодисперсных порошков металлов, легкоплавкое стекло. Любой из этих соединительных материалов имеет собственную область применения.
При современном уровне разработки пайки уровень качества соединений возможно обеспечено при условии планирования качества на каждой операции. Наряду с этим должна быть обеспечена технологичность конструкции соединения, осуществлен верный выбор флюса и припоя, включая опробования на паяемость отдельных элементов, рациональность температурного режима и поддержание состава расплавленной ванны. При проведении подготовки к работам по пайке микроэлементов нужно особенное внимание уделять исполнению требований технологичности.
направляться обращать внимание на технологичность крепления микроэлементов к паяемому изделию. Так, соединения, полученные пайкой низкотемпературным припоем, в зоне спая не должны трудиться на растяжение либо срез. Пайка низкотемпературным припоем обязана помогать только для улучшения электро-и теплопроводности, для уплотнения соединения.
Наровне с преимуществами пайки имеет последовательность недочётов, в особенности проявляющихся при соединении узких и миниатюрных изделий. К ним относятся коррозия припоя в местах соединения, ведущая к утрата контактирования либо повышению сопротивления между контактами; образование в местах спаев структурных переходов, вызывающих утраты командных импульсов; попадание остатков флюса на контактные поверхности, ведущие к утрата контактирования.
Флюсы. К флюсам для пайки микроэлементов предъявляют ряд условий. Так, флюс обязан владеть активностью, снабжать хорошую растворяемость поверхностных окислов, соединяемых припоя и элементов; диапазон температур раскисления флюса должен быть в пределах 90—150 °С, а температура плавление припоя выше рабочей температуры флюса на 20—40 °С; остатки флюса не должны приводить к и изменять электрического сопротивления соединения.
В громаднейшей степени удовлетворяют этим специфическим особенностям и требованиям флюсы КЭ и ФПП, использующиеся для пайки микроэлементов; флюс КЭ складывается из 10—40% этилового спирта 90—60% и канифоли, а флюс ФПП включает полиэфирную смолу марки ПН-5 — 30% и метилэтилкетон либо этила-цетат — 80%. Преимуществом этих флюсов есть отсутствие корродирующего действия, а остатки флюсов не воздействуют на величину сопротивления изоляции. Недочётом их есть не сильный активность, которая увеличивается при температуре выше 220 °С, что требует применения припоев с температурой плавления более чем 140 °С.
Активность флюсов на базе канифоли возможно повысить методом добавления хлора, что вводится в виде галлоидных органических соединений.
Использование кислотных флюсов для пайки микроэлементов как правило исключается, поскольку удаление их остатков требует пассивирования и промывки, что довольно часто недопустимо по техническим условиям.
Для изготовление краски сначала растворяют канифоль в этиловом спирте. Раздельно подготавливается раствор полиэфирной смолы в метилэтилкетоне и водный раствор метилцеллюлозы, что нужно выдержать в течение нескольких часов при комнатной температуре. Затем смешивают метилцеллюлозы и растворы канифоли и в смесь додают раствор полиэфирной смолы, после этого смесь шепетильно перемешивают.
Флюсующая краска легко смывается водой, нагретой до 70—80 °С.
Для нанесения жидкого флюса помогает приспособление, схема которого продемонстрирована на рис. 1, а. Приспособление является резервуаром , в нижнем финише которого предусмотрено выпускное отверстие, являющееся седлом выпускного клапана. Верхнее отверстие помогает для заливки флюса. В пробке предусмотрено седло дополнительного клапана.
Пробка соединена без движений с командной кнопкой и ввинчена в резервуар.
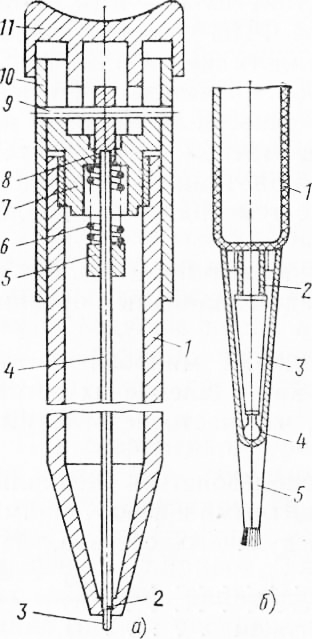
Рис. 1. Приспособления для нанесения флюса
Высота дополнительного клапанов и сёдел выходного однообразна. Соединены клапаны между собой штоком, в верхней части которого предусмотрено кольцо для опоры пружины. Выпускной клапан имеет упор, выступающий из выпускного отверстия. Диаметр упора меньше диаметра выпускного отверстия, а протяженность его больше высоты седла клапана.
Дополнительный клапан при помощи штифта, проходящего через пазы кнопки, соединен с гильзой, имеющей движение на протяжении резервуара, равный длине упора. Для заполнения приспособления жидким флюсом отвинчивают пробку, резервуар ставят выпускным отверстием на мягкую резину и создают заливку флюса. После этого пробку при открытых дополнительном и выходном клапанах завинчивают в резервуар, по окончании чего приспособление снимают с резины.
Наряду с этим подпружиненный шток перекрывает оба клапана. Нанесение флюса на место спая создают двумя приемами:
а) приспособление берут за резервуар и упором устанавливают на место спая, а после этого создают легкое нажатие в направлении продольной оси , пока упор не утопится до среза выпускного отверстия;
б) приспособление берут за гильзу, которая при нажатии на кнопку перемещается на протяжении корпуса и при помощи штифта, соединенного с штоком и клапаном, втягивает упор до среза выпускного отверстия. В следствии и в том и другом случае выпускной и дополнительный клапаны и соединяющий их шток с закрепленным на нем кольцом перемещаются в сторону кнопки. В один момент сжимается пружина, оба клапана раскрываются, а из выпускного отверстия через образующийся радиальный зазор вытекает флюс.
По окончании снятия нагрузки пружина, разжимаясь, возвращает шток в исходное положение. Флюс может выпускаться любыми порциями впредь до постоянного истечения.
Для нанесения жидкого флюса на место пайки при ручном монтаже целесообразно использование приспособления, воображающее собой полиэтиленовый баллон, в горловине которого при колпачка и помощи детали укреплена игла.
На иглу надета кисть. При надавливании на баллон флюс смачивает кисть и поступает на место пайки.
Припои. Выбор припоев для пайки микроэлементов зависит от температурных черт используемых флюсов. Припои должны удовлетворять следующим требованиям:
— иметь температуру пайки, снабжающую сохранность параметров термочувствительных микроэлементов;
— не растворять покрытия микроэлементов, поскольку в другом случае происходит нарушение электрических и механических соединений микросхем;
— снабжать достаточную надежность соединения и его коррозионную стойкость.
Припои ПОС-61 +3% Аи; ПОСК-50; ПОСК-47; ПОСИС-1; ПОС-61 +3% Ag, т. е. припои, не которые содержат висмута, используют для пайки микроэлементов к платам с печатным монтажом. Для пайки напыленных контактных схем возможно использовать припои на индиевой базе типа ПОСИС-1, ПОС-61 + 3% Др и Аи. Для пайки микропроводов используют припой ПК-70.
На данный момент имеется последовательность низкотемпературных припоев, содержащих индий, кадмий и висмут с температурой плавления 80— 150 °С.
Рис. 2. Форма мениска при опробованиях на паяемость
Для пайки микроэлементов из его сплавов и алюминия используют легкоплавкие припои П150А, П200А, П250А, П200Г. На практике применяют кроме этого припой следующего состава: магний-1 — 10%, кремний-3 — 12%; медь-5 — 10%, алюминий-5 — 10% и цинк — другое. Для коррозионной стойкости и повышения прочности соединений в приведенный состав додают серебро.
Для бесфлюсовой пайки изделий из разных материалов используют припой на базе меди, складывающийся из германия-7 — 10%, меди-1 — 2% и никеля (другое). Для получения качественных соединений рекомендуется проводить периодические регламентированные опробования элементов на паяемость, каковые делают на изделиях-примерах представителях перед их соединением. Эти опробования заключаются в окунании образцов 1 в припой и оценке расположения и величины мениска (рис. 139).
Паяемость сквозных отверстий возможно оценена визуально. Отверстия 2 диаметром до 1,4 мм при хорошей паяемости должны заполняться припоем 3, как это продемонстрировано на рис. 139, а, отверстия диаметром более 1,4 мм — как на рис. 139, б. На рис.
139, в изображен вид мениска при удовлетворительной паяемости, а на рис. 139, г, д — неудовлетворительной.
Для оценки паяемости узких проводов используют капельный способ. Имеются и другие способы опробований.
Пайка микроэлементов печатных плат. Печатные платы содержат много разных микроэлементов (проводов, контактных площадок, лепестков, выводов), соединение которых осуществляется пайкой. Исходя из этого разглядим процесс пайки микроэлементов, присоединяемых к печатной плате.
Технологический процесс складывается из следующих операций.
1. Подготовка печатной платы и микроэлементов к пайке содержится в том, что перед пайкой плату шепетильно обезжиривают растворителем и сушат на воздухе в течение 2—3 мин. Поверхности выводов микроэлементов зачищают с целью удаления окис-ной изоляционного лака и плёнки, попавшего на вывод при герметизации корпуса. Для зачистки возможно использовать пинцет, на рабочей поверхности губок которого укреплена мелкозернистая наждачная бумага либо узкий личной надфиль.
Потом выводы обезжиривают окунанием в сосуд с растворителем.
2. Лужение выводов микроэлементов создают последовательным окунанием их во флюс и в тигель с расплавленным припоем. После этого выводы вторично окунают во флюс с целью предохранения их от окисления. Операция лужения есть одновременно и контрольной для определения качества поверхности выводов.
Отверстия платы под микроэлементы запаивают так, дабы припой состоялся в отверстие до отметки противоположной плоскости, не растекаясь по ней. В один момент лудят узким ровным слоем контактные площадки отверстий. Температура жала паяльника 220—230° С. Время пайки не более 3 с. Температуру паяльника осуществляют контроль термопарой и микроамперметром.
3. Удаление остатков флюса создают методом промывки в воде. Перед пайкой и монтажом микроэлементов создают удаление припоя из медненных отверстий, подлежащих пайке. Припой удаляют методом отсоса его посредством особого приспособления. Припой из отверстий платы отсасывают при одновременном прогреве паяльником, нагретым до температуры 180— 190 °С.
Время прогрева не более 2 с. После этого создают повторное лужение контактных площадок. Перед пайкой выводы микроэлементов изгибают, и их вольно, без натяга, вводят в отверстия платы. Для удобства работы при пайке микросоединений помогают особые рабочие подставки, на которых располагают пластмассовые емкости для обезжиривающей смеси, флюса, бобины и припоя для ленточного припоя.
4. Пайку создают с тыльной стороны платы. Количество наносимого флюса должно быть минимальным. Он не должен растекаться за пределы территории пайки. Наносят флюс посредством обрисованных выше устройств, и капельницы, пипетки, заостренной палочки либо кисточки.
Температуру жала паяльника устанавливают в зависимости от материала присоединяемых припоя и элементов. Время пайки 1—2 с. Для предохранения от перегрева при пайке используют теплоотводы либо обдув воздухом.
При пайке пленочных микроэлементов и схем выводы последних с опаской изгибают и устанавливают на контактные площадки посредством пинцета, что при пайке в один момент делает и роль теплоотвода. Температура жала паяльника не превышает 200° С, пайки и время лужения не более 1 с.
Во многих случаях используют рабочие подставки с комплектом инструмента для монтажных работ (пинцет, скальпель, кисточка, наждачная бумага, надфили). Для удобства работы на подставке укреплены тумблеры для включения требуемого напряжения питания. Тут же находятся и переменные сопротивления для трансформации температуры нагрева паяльника.
При необходимости пайку ведут с применением лупы.
Рис. 3. Оснастка для пайки
При лужении расплавленным припоем выводов миниатюрных изделий появляется опасность их повреждения и перегрева. Для исключения этого используют приспособление, складывающееся из цангового держателя, и устройства для смачивания паяемых элементов флюсом и расплавленным припоем.
Теплоотводящие зажимы (рис. 140, а) цангового держателя удерживают изделие в ходе лужения и снабжают отвод тепла, исключающие передачу его в тело изделия. Для установки изделия в цанговый зажим нажимают на кнопку. Наряду с этим шток своим клинообразным финишем вдвигается между зажимами, закрепленными на плоских пружинах.
По окончании ориентирования изделия в нужном положении кнопку 5 отпускают, шток под действием пружины возвращается в исходное положение. Изделие наряду с этим надежно зажимается теплоотводами.
Устройство для смачивания изделий флюсом и расплавленным припоем складывается из основания, установленного на амортизаторах, на котором закреплена плита из асбоцемента. В данной плите расположены тигель с припоем и стакан для флюса. Тигель нагревается от нагревательного элемента, приобретающего питание от источника тока пониженного напряжения.
Глубину погружения выводов во припой и флюс устанавливают методом регулировки высоты упоров. Краткосрочным погружением выводов в расплавленный припой создают их лужение. Посредством зажимов цанги реализовывают отвод тепла.
Это предохраняет изделие от повреждения и перегрева.
С целью увеличения производительности для лужения используют групповой теплоотвод. В него вставляют сходу много изделий, выводы которых нужно облу-дить. Он складывается из двух параллельных теплоотводящих пластин, между которыми помещены прижимные планки, на осях. К планкам прикреплен эластичный элемент. Теплоотводящие пластины складываются из внутренней железной части, имеющей высокую теплопроводность, и наружной — из материала не смачиваемого припоем.
В теплоотводящих пластинах выполнен последовательность пазов. При лужении планки отводят назад и изделия вставляют между пластинами так, дабы их выводы вошли в пазы. По окончании комплекта изделий планки сближаются. Наряду с этим эластичный элемент, влияя на корпуса изделий, хорошо прижимает выводы к теплоотводящим пластинам.
Затем выводы погружают в расплавленный припой.
Изделия, предварительно покрытые узким слоем припоя, паяют на машине МТТ-02, предназначенной для термокомпрессионной сварки миниатюрных изделий.
В качестве покрытия применяют серебро и оловянистые припои. Для получения удовлетворительного качества соединений достаточно покрытие одного из соединяемых изделий припоем слоем толщиной до 0,01 мм. Соединение имеет лучшее уровень качества при покрытии его серебром.
Пайку бронзовых лепестков толщиной 0,05 мм, шириной 1 —1,5 мм с бронзовыми проводами диаметром 0,03—0,2 мм создают при токе 600 А, упрочнении прижатия 0,5 кГс; время пайки 0,1 с. Пайку реализовывают в простых условиях, без удаления и обезжиривания окисной пленки. Пайку проводов на сварочной машине возможно создавать без снятия изоляции.
Пайка микропроводов. Технологический процесс пайки микропроводов в эмалевой изоляции включает операции: снятие изоляции, обезжиривание, пайку, удаление остатков контроль и флюса. Для снятия изоляции используют механический, химический и термический способы.
Широкое распространение взял механический способ удаления изоляции методом зачистки финишей проводов наждачной шкуркой. Снятие механической зачисткой эмалевой изоляции с бронзовых проводов диаметром 0,015 мм и более создают на приспособлении, складывающемся из ролика и плиты. Финиши проводов кладут на плиту и на длине 2—3 мм, с опаской нажимая на ролик, прокатывают его по проводу.
Для снятия эмалевой изоляции с проводов диаметром 0,06— 0,12 мм используют приспособление, складывающееся из основания, на котором укреплен скоростной (7—12 тыс. об/мин) электродвигатель и соединенный посредством муфты с ведущей щеткой, которая вращается.
Вращение ведомой щетки, закрепленной в подвижных опорах, осуществляется за счет сцепления с ведущей щеткой. Щетки смогут быть изготовлены из константановой проволоки марки МНМ-40 диаметром 0,1—0,15 мм и прошлифованы по наружному диаметру, равному 20—25 мм.
Степень обоюдного прижатия щеток регулируют поворотом подвижных опор около оси предусмотренных фиксирующих винтов. Для зачистки финиш привода помещают между вращающимися щетками. При зачистке проводов другого сечения соответственно изменяется степень обоюдного прижатия щеток.
Снятие изоляции при пайке с некоторых типов проводов не нужно. Так, полиуретановая изоляция проводов ПЭВТЛ-1, ПЭВТЛ-2 и др. владеет флюсующими особенностями при температурах 320—350 °С. Кроме этого не нужно снятие стеклянной изоляции с проводов диаметром 0,005—0,05 мм.
Пайку же проводов со стеклянной изоляцией диаметром более 0,05 мм создают по окончании ее снятия. Для этого финиш провода кладут на протяжении губок пинцета и легким нажатием разрушают стеклянную изоляцию, но наряду с этим не повреждая провод.
Но направляться иметь в виду, что снятие изоляции методом механической зачистки снижает прочностные характеристики проводов, исходя из этого такую зачистку рекомендуется проводить для проводов диаметром более чем 0,1—0,2 мм.
Удаление изоляции создают кроме этого химическим методом. Химический метод удаления изоляции венифлексового лака методом погружения провода в муравьиную кислоту, нагретую до температуры 80—90 °С, требует наличия удлиненных выводных финишей ввиду ее токсичности.
Изоляция под действием кислоты набухает, размягчается и отслаивается от железной жилы. Для защиты расположенных выше участков изоляции в ванну сверху кислоты наливают защитный слой касторового масла. По окончании снятия изоляции провод подвергают нейтрализации.
Муравьиная кислота — неустойчивое соединение при температурах 110—120 °С и в ходе последующей сушки разлагается и улетучивается.
Винифлексовую изоляцию с проводов удаляют в растворе хлористого цинка. Состав раствора: 50% хлористого цинка и 50% воды. Раствор нагревают до температуры 120 °С и в него опускают в виде жгута провода. Время выдержки 4—6 мин.
Изоляция набухает и отслаивается от железной жилы. Остатки изоляции смывают сильной струей воды, а при необходимости их счищают щетками. Время выдержки проводов в растворе возможно пара сократить за счет применения более концентрированного раствора.
Химический метод действен при снятии изоляции с громадного количества проводов. Исходя из этого наровне с химическим способом взял распространение термический метод.
Рис. 4. Схема установки для обжига изоляции
Термический метод сводится к обжигу изоляции посредством электрической спирали. Но при обжиге изоляции в воздушной среде вероятны пережоги, что ведет к образованию на проводе окисных пленок и к трансформации структуры провода. Для исключения этого обжиг проводов диаметром 0,02—0,07 мм создают в защитной среде — аргоне.
Устройство для обжига изоляции проводов в аргоне включает нихромовый нагреватель, что навивают около одного финиша кварцевой трубки. Питание производится от регулируемого трансформатора. Внутренняя полость трубки соединена через редуктор и ротаметр с баллоном аргона.
Для измерения температуры предусмотрена термопара. Провод, подвергаемый обжигу, вводится в торцовое отверстие кварцевой трубки.
Разогретый газ разрушает изоляцию провода, не подвергая его окислению. Обжиг создают при температуре 500—600 °С. Время обжига 3—5 с. Обуглившаяся часть изоляции удаляется протиркой провода суконным тампоном, намоченным спиртом.
Во многих случаях для снятия изоляции с проводов диаметром 0,05 мм и более используют метод обжига в расплаве солей. Соль, к примеру хлористый калий, засыпают в особый тигель муфельной печи и расплавляют, нагревая до температуры 760 °С, и поддерживают эту температуру. Перед снятием изоляции провода скручивают и опускают сперва в соляную, а после этого в ванну с охлаждающей жидкостью и протирают.
Остатки соли, покрывающие провод, защищают его от окисления.
Снятие эмалевой изоляции с проводов типа ПЭВ, ПЭЛ, ПЭЛШО создают методом погружения в глицерин, нагретый до 260 °С. Наряду с этим происходит восстановление и отслаивание изоляции окисной бронзовой пленки.
Пайку бронзовых проводов создают низкотемпературными припоем ПОСК-50 с применением растворимого флюса Ф-55. Удаление остатков флюса возможно создавать тампоном из замши либо другого мягкого материала, намотанного на губки пинцета и намоченного сначала в воде, а позже в растворителе. Провода марки ПЭВТЛ рекомендуется предварительно лудить припоем ПК-70 при температуре 300—400 °С.
Пайку проводов диаметром от 0,005 до 0,05 мм в стеклянной изоляции ведут без ее зачистки. В качестве припоев используют ПСр-40, ПСр-70 и ПСр-25Ф, каковые предварительно измельчают в порошок. При пайке припоем ПСр-25Ф использование флюсов не нужно.
При пайке припоями ПСр-40 и ПСр-70 используют флюс № 209.
Пайка алмазов. В производственной практике время от времени требуется осуществить присоединение к бриллианту микропроводов, контактных лепестков, площадок и т. д. Для этого на поверхность бриллианта наносят слой титана. В зазор между соединенными поверхностями помещают припой и создают нагрев до расплавления припоя.
С целью исключения образования окисной пленки титана его нагревают в вакууме либо атмосфере инертного газа.
Возможно пайку создавать кроме этого методом предварительного нанесения на бриллиант пленки титана толщиной порядка 500 А, а после этого слоя меди толщиной 0,01 мм. Эти металлы осаждают термическим методом в вакууме. Затем омедненный кристалл бриллианта соединяют с металлами простой пайкой.
Контроль паяных соединений. Контроль качества паяных микросоединений создают визуально с применением луп, микроскопов (к примеру, МБС-1, МБС-2) и других оптических устройств. Он сводится к осмотру соединений, оценке прочности соединения, установлению наличия остатков флюса, следов коррозии, непропаянных других дефектов и контактов.
Но при контроле и приеме ОТК изделий, монтаж которых закончен, использовать микроскопы время от времени не редкость нереально ввиду малого расстояния и высокой плотности соединений h между нижними плоскостями и базовой поверхностью элементов. В этих обстоятельствах используют оптические приспособления.
Приспособление складывается из лупы и осветителя с миниатюрным зеркалом. Осветитель содержит световод, изготовленный из полосы (толщиной 0,5 мм) органического стекла, две низковольтные лампочки накаливания, эбонитовый корпус, являющийся в один момент державкой, и выводы к источнику тока. Торцовые грани световода должны быть полированными.
При включении лампочек свет распространяется на протяжении световода и излучается из его торца.
Рис. 5. Приспособление для контроля паяных соединений
Для контроля качества паяных соединений корпус оптического приспособления располагают так, дабы световод разместился в зазоре между впаянным базовой поверхностью и изделием. С противоположной стороны световода размещают лупу с зеркальцем и фокусирующим винтом. Свет, проходя через световод, пространство под впаянным элементом, падает на зеркальце и попадает на лупу, через которую видны рельеф и выводы паяного соединения.