Подготовка основы
Уровень качества фанерования и отделки мебели листовыми материалами сильно зависит от того, как подготовлена поверхность базы. Неосторожно подготовленная база может привести к браку.
Подготовка базы под фанерование
Базу под фанерование подготавливают с целью получения ровной фанеруемой поверхности, и удаления сучков, смолы, жировых пятен и вырывов волокон. В тех случаях, в то время, когда разнотолщинность заготовок не разрешает фанеровать их без выравнивания, заготовки калибруют (сглаживают) по толщине.
Подготовленная поверхность должна быть равномерно матовой и не иметь, царапин, задиров, вырывов, потеков клея и других недостатков. Ее шероховатость обязана пребывать в пределах6—9-го классов (ГОСТ 7016—68), что достигается шлифованием либо фрезерованием подробностей.
Процесс подготовки под фанерование зависит от материалов, используемых в качестве базы.
Подготовка щитов и плит содержится по большей части в калибровании их по толщине, оформлении кромок и шлифовании поверхностей.
Поставляемые мебельным фирмам некалибро-ванные и нешлифованные древесностружечные плиты имеют разнотолщинность +1—3 мм и более. В таком виде плиты негодны для фанерования, их калибруют и шлифуют.
Поверхность столярных плит не редкость волнистой из-за коробления их базы при хранении плит, перед фанерованием их шлифуют либо калибруют и шлифуют.
Точность изготовляемых мебельными фабриками щитов и плит в большинстве случаев высокая, подготовка их к фанерованию сводится значительно чаще лишь к шлифованию поверхностей.
При щитов кромки и необходимости плит оформляют вставками либо раскладками из древесины (рис. 1). Раскладки приклеивают с припуском 0,5—1 мм на сторону и по окончании снятия свесов пласти щитов шлифуют.
Совсем кромки обрабатывают на строгальных станках.
В случае если на подготавливаемых под фанерование плоскостях имеются заколы, вырывы волокон, их заделывают замазкой. Для изготовление замазки берут клей, которым будут пользоваться при фанеровании, додают в него 20—30% древесной муки либо измельченного березового угля и перемешивают состав до получения однородной массы. Приготовляют замазку по мере ее потребления маленькими порциями.
Замазку наносят шпателем. В случае если по окончании подсыхания она дает усадку, то места проседания вторично шпатлюют.
Рис. 1. Методы оформления кромок древесностружечных и столярных плит перед фанерованием: а — вставной рейкой, б — раскладкой на ровную фугу, в — раскладкой в гребень и шпунт
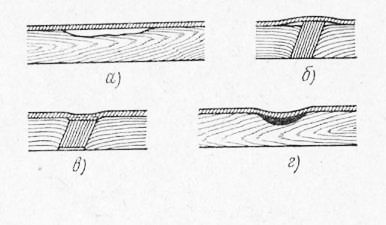
Рис. 2. Недостатки фанерования: а — воздушный пузырь «чиж», б — выпучивание шпона сучком при усыхании базы, в — проседание шпона на сучке при разбухании базы, г — проседание шпона
Замазка обязана прекрасно сцепляться с древесиной, иметь малого усадку и допускать обработку инструментами без стремительного их затупления при обычных режимах работы. Шпатлюют поверхности перед шлифованием.
Подготовка под фанерование подробностей из массива древесины содержится в удалении с их поверхности сучков, не допускаемых по техническим условиям под фанерование, жировых пятен, а также в ее выравнивании. Незаделанные на базе вмятины, сучки, заколы являются обстоятельством появления недостатков фанерования (рис. 2).
сучок и Основа владеют различной величиной усушки. При уменьшении влажности сучок, отличающийся поперечным к базе направлением волокон, будет усыхать меньше и выступать над поверхностью подробности. Напротив, при повышении влажности база разбухает больше и торцовая поверхность сучка втягивается в нее, образуя впадину.
Исходя из этого сучки в обязательном порядке высверливают, а после этого эти места заделывают пробками, направление волокон которых должно совпадать с направлением волокон базы в местах заделок.
Рис. 3. Методы заделки торцов и стыков перед фаиерованием: а — брусками, б — планками со скошенными кромками, в —долевыми наклейками, г — косынкой, д — вставками
гниль и Смолу кроме этого нужно удалять, поскольку над ними шпон будет отслаиваться.
Последней операцией подготовки подробностей из массива древесины под фанерование есть шлифование поверхностей либо цинубление. Цинублением достигают разрыхления поверхностного слоя древесины, для чего наносят на базу сетку рисок, направленных параллельно ее волокнам либо под некоторым углом к ним. В будущем под давлением запрессовки за счет снятия и уплотнения этих выступающих участков толщина и поверхность основы клеевого слоя выравниваются.
Подготовка под фанерование узлов (коробок, рамок) связана с технологическими трудностями, исходя из этого тут преобладает еще ручной труд. Выходящие на фанеруемую поверхность стыки и торцы связанных шиповыми соединениями брусков заделывают древесиной (рис. 3).
Связанные шиповым соединением узлы коробок срезают в полуторец и наклеивают на них долевые бруски либо планки со скошенными кромками. Торцы заготовок из щитов кроме этого заделывают долевыми наклейками.
Стыки брусков разных соединений заделывают наклейками разных формили накладками из шпона. По окончании заделки шиповых соединений и и торцов узлы фрезеруют, после этого шлифуют либо цинубят.
Подготовка базы под облицовывание пластиками и плёнками
Базу под облицовывание пластиками и плёнками подготавливают с целью получения ровной и равномерно матовой поверхности. На подготовленной поверхности не допускаются царапины, забои, вырывы волокон, следы от ножей и резцов, прошлифовка слоя шпона. Шероховатость подготовленной поверхности древесины под облицовывание пленками должна быть не ниже 10-го класса по ГОСТ 7016—68, а необлицованных древесностружечных плит — не ниже 8-го класса.
Под облицовывание пластиками шероховатость поверхности должна быть не ниже 6-го класса.
Процесс подготовки заготовок под облицовывание пленками складывается из пороза и операций шлифования-полнения облицовываемых поверхностей, под облицовывание пластиками — из операции шлифования. В случае если поверхности, облицовываемые пластиками, имеют заколы и вырывы, их заделывают замазкой.
В любых ситуациях нефанерованные заготовки из древесностружечных плит калибруют, в случае если разнотолщинность плит превышает нормы, установленные для них ГОСТ 10632—70.
Для порозаполнения используют мочевино-формаль-дегидные смолы либо мочевино-меламино-формальдегид-ную смолу ММФ, хлористый аммоний, латекс полиме-тилметакрилата ПММА и наполнители — каолин либо трепел.
Для изготовление порозаполнителя в чистую клее-мешалку с водяной охлаждающей рубахой заливают одну из указанных смол и при постоянном перемешивании вводят хлористый аммоний. По окончании получения однородной веса додают латекс ПММА и наполнитель. Смесь перемешивают в течение 15—20 мин.
Рецепты изготовление порозаполнителя приведены в табл. 5. Жизнеспособность порозаполнителя при температуре 18—20 °С не более 8 ч.
инструменты и Оборудование, используемые для подготовки базы
Нефанерованные древесностружечные плиты калибруют и шлифуют на фрезерно-шлифовальных станках, предназначенных для одностороннего калибрования заготовок из древесностружечных плит по толщине с последующим их шлифованием.
Калибрование заготовок из древесностружечных плит (рис. 20) на фрезерно-шлифовальных станках осуществляется четырьмя фрезами, расположенными в шахматном порядке, так что при перемещении щита фрезеруется вся его поверхность. Любая фреза имеет четыре ножа, оснащенных пластинками из жёсткого сплава.
Плиты шлифуют шлифовальной шкуркой, намотанной на обре-зиненные шлифовальные цилиндры.
Стол станка представляет собой твёрдую литую станину, на которой крепят металлические плиты, образующие стол для обрабатываемых заготовок. Между плитами установлены поддерживающие вальцы, образующие которых подняты над поверхностью стола на 0,25—0,3 мм.
Заготовки древесностружечных плит при шлифовании и калибровании подают обрезиненными вальцами. Плиты при калибровании прижимаются к плите станка задними прижимами и передними, при шлифовании — задними вальцами, каковые имеют пружины, установленные в опорах вальцов. Пыль с плит по окончании шлифования удаляют щеткой. Разнотолщинность плит
Рис. 4. Схема обработки заготовки на фрезерно-шлифовальном станке: 1 — вальцы, поддерживающие заготовку, 2 — подающие вальцы, 3 — щетки для удаления пыли, 4 — шлифовальные цилиндры, 5 — станина, 6 — прижимы, 7, 10 и 11— плиты станка, 8 — фрезы, 9 — ножи фрез, 12 — обрабатываемая заготовка
по окончании шлифования и калибрования должна быть в пределах от ±0,15—0,3 мм.
При калибровании заготовок из древесностружечных плит серьёзное значение имеют меры, дающие предупреждение их коробление.
В древесностружечной плите действуют остаточные внутренние напряжения, появляющиеся в ходе ее изготовления. В некалиброванной плите эти напряжения взаимно уравновешиваются, действуют симметрично по обе стороны плиты. При одностороннем калибровании плит равновесие напряжений нарушается, что ведет к их короблению.
Исходя из этого древесностружечные плиты рекомендуется калибровать с обеих сторон, сохраняя тем самым симметричность конструкции плиты.
При отсутствии фрезерно-шлифовальных станков подготовку под фанерование заготовок из древесностружечных плит возможно создавать калиброванием на рейсмусовых станках с последующим шлифованием на шлифовальных станках. Но калибрование на рейсмусовых станках непроизводительно и требует нередкой замены и переточки ножей.
Нефанерованные заготовки из столярных плит, массива древесины и мебельных щитов калибруют и шлифуют на трехцилиндровых шлифовальных станках с гусеничной либо вальцовой подачей.
Рис. 5. Схемы шлифования заготовок на трехцилиндровых шлифовальных станках: а — с вальцовой подачей, б — с гусеничной подачей; 1 — заготовка, 2 — подающие валики, 3— прижимные валики, 4— щеточный барабан для очистки подробностей от пыли, 5 — шлифовальные цилиндры, 6 — гусеничная цепь
Станки с гусеничной подачей снабжают лишь шлифование фанеруемых поверхностей. Исходя из этого их используют в тех случаях, в то время, когда шлифуемые заготовки не нужно калибровать по толщине. На станках с вальцовой подачей, не считая шлифования, возможно делать и калибрование заготовок.
В случае если разнотолщинность подготовляемых под фанерование заготовок велика и трехцилиндровый шлифовальный станок с вальцовой подачей неимеетвозможности обеспечить выравнивания заготовок по толщине за один проход, их перед шлифованием калибруют на рейсмусовых станках.
Заготовки шлифуют шкуркой, намотанной на шлифовальные цилиндры 5. Заготовки в станках с вальцовой подачей подают валиками, а в станках с гусеничной подачей — гусеничной цепью.
Для получения требуемой шероховатости при шлифовании на фрезерно-шлифовальных и трехцилиндровых шлифовальных станках на цилиндры станков наматывают шкурки различных номеров.
Уровень качества шлифования сильно зависит от верного оптимального номеров рабочего и выбора шкурки давления цилиндров на шлифуемую заготовку, подачи заготовок и скоростей шлифования. В табл. 6 приведены режимы шлифования заготовок, предназначенных под фанерование.
Скорость шлифования на фрезерно-шлифовальных станках образовывает 23,2 м/сек, на трехцилиндровых — 25—30 м/сек. Скорость подачи заготовок устанавливают экспериментально в зависимости от площади шлифуемых поверхностей. Она находится в пределах от 3 до 16 м/мин.
Шлифование заготовок из массива древесины под фанерование возможно заменено фрезерованием на строгальных станках.
В случае если строгальные станки не смогут обеспечить упомянутой в таблице шероховатости поверхности, то заготовки шлифуют либо цинубят простым методом.
Шлифование фанерованных заготовок под -отделку пленками возможно кроме этого создавать на ленточных шлифовальных станках с подвижным столом и бара-банно-ленточных.
При шлифовании на станках с подвижным столом заготовка, закрепленная на столе, перемещаемом по направляющим, шлифуется нескончаемой шлифовальной лентой, натянутой натяжным шкивом на ведущий шкив. Лента к шлифуемой заготовке вручную прижимается утюжком.
При шлифовании на барабанно-ленточных станках заготовка, перемещаемая при помощи нескончаемой прорезиненной ленты, шлифуется нескончаемой шлифовальной лентой, натянутой натяжным шкивом на ведущий шкив. Шлифовальная лента к шлифуемой заготовке прижимается колодкой, давление которой создается при помощи пружинного либо пневматического механизма.
Для получения нужной шероховатости поверхность заготовки шлифуют за три прохода шкурками разных номеров. По окончании второго прохода поверхность смачивают для поднятия ворса и просушивают в условиях цеха.
Высверливание сучков и заделку отверстий создают на полуавтоматических сверлильных станках. Станок имеет два рабочих шпинделя, из которых один помогает для высверливания сучков, а второй для запрессовки и высверливания пробки. Станок имеет кроме этого приспособление для впрыскивания клея в заделываемое механизм и отверстие для подачи древесной планки, из которой выпиливают пробку.
Рис. 6. Схема шлифования заготовок на ленточных шлифовальных станках: а — с подвижным столом, б — на барабанно-ленточных; 1 — ведущий шкив, 2 — шлифовальная лента, 3— натяжные шкивы, 4— утюжок, 5 — стол, 6 — шлифуемая заготовка, 7 — направляющие стола, 8 — прижимная колодка, 9 — подающая лента
Для высверливания заделки и сучка отверстия подготавливаемую под фанерование заготовку укладывают на стол с таким расчетом, дабы сучок был под шпинделем сверла. После этого заготовку прижимают к столу 8 и сверлом 3 высверливают сучок. По окончании операции суппорт со шпинделями машинально перемещается вперед.
В данный же момент клей из особого приспособлениявпрыскивается в просверленное отверстие. При предстоящем продвижении суппорта вперед второй шпиндель останавливается против отверстия и опускается. Наряду с этим сверло-про-бойник высверливает из древесной планки пробку, которая после этого подается в державку и запрессовывается в высверленное отверстие.
Для приклеивания пробок пользуются казеиновым либо синтетическим клеем.
Обрабатываемые на станке изделия должны быть однообразными по толщине с допуском ± 0,5 мм.
Ручное цинубление делают рубанком-цинублем. На лицевой стороне железки цинубеля сделана небольшая насечка, благодаря чему лезвие его получается зубчатым. Железка поставлена под углом 80— 85°,
На мебельных фирмах цинубление заменяют шлифованием крупнозернистыми шкурками.
Порозаполнение заготовок под облицовывание пленками создают прессованием в прессах с обогреваемыми плитами. Для прессования используют дюралюминиевые прокладки толщиной 1,5—2 мм. Чистота поверхности прокладок должна быть не ниже 8-го класса по ГОСТ 2789—59.
Технологический процесс порозаполнения осуществляется следующим образом. На рабочем столе у пресса формируют пакеты по схеме: дюралюминиевая прокладка, заготовка с нанесенным на клеенаносящем станке порозаполнителем, дюралюминиевая прокладка. Темпеоатуоа прокладок не выше 30 °С впемя от момента нанесения на заготовку порозаполнителя до начала формирования пакета не меньше 10 мин.
Организованные пакеты загружают в пресс и прессуют в течение 3— 4 мин при удельном давлении 12—15 кгс/см2, температуре плит пресса 115—120 С. По окончании выгрузки из пресса заготовки выдерживают в стопе в условиях цеха не меньше 12 ч.
Рис. 7. Схема обработки заготовок на полуавтоматических станках для высверливания сучков и заделки отверстий: 1 — обрабатываемая заготовка, 2 — прижимный механизм, 3 — сверло, 4 — шпиндель сверла, 5 — приспособление для впрыскивания клея, 6 — рабочий суппорт станка, 7 — шпиндель для высверливания и з.апрессовки пробок, 8 — стол станка
Рис. 8. Цинубель: а — неспециализированный вид, б — железка