Отделочная подготовка под прозрачные покрытия
Удаление ворса
При столярной подготовке, в особенности при циклевании и шлифовании поверхности древесины, часть перерезанных и оборванных узких древесных волокон приглаживается и вдавливается в поры.
При сушке и нанесении лакокрасочных материалов эти волокна (ворс) приподнимаются. Ворс портит прозрачное покрытие, исходя из этого его нужно удалить до нанесения и крашения лака.
Для удаления ворс нужно поднять, а после этого удалить. Для поднятия ворса поверхность древесины увлажняют тампоном либо губкой, намоченными в теплом (20± ±2°С) 3—5%-ном растворе глютинового клея (оптимальнееосветленного костного). По окончании увлажнения поверхность сушат, наряду с этим вставший ворс получает некую жесткость и легко сошлифовывается.
Сушить увлажненные поверхности нужно на этажерках, других устройствах и стеллажах так, дабы они были полностью открыты для доступа воздуха. Сушить в плотных штабелях и в штабелях с прокладками не допускается. Увлажненные поверхности сушат в цехе при температуре 18—20 °С и в особых сушильных устройствах при температуре не более 50 °С. В зависимости от температуры рекомендуются следующие сроки сушки:
Ворс удаляют методом шлифования поверхности шкуркой № 8—6.
В некоторых случаях удаления ворса и операции увлажнения заменяют термической обработкой поверхности. Она может выполняться различными методами. В карандашном производстве ее делают методом протягивания карандашей через нагретое до температуры 200—250°С металлическое полированное кольцо «фильеру» с размером в свету пара меньшим, че-м сечение карандаша. При протягивании через нагретое кольцо поверхностный слой уплотняется.
Прошедшая лишь термическую обработку поверхность древесины не стабильна. При увлажнении она набухает и делается шероховатой и ворсистой. В производстве карандашей данный недочёт устраняется наличием в древесине карандаша парафина, что придает ей гидрофоб-ность.
Для придания уплотненному поверхностному слою стабильности на поверхность подробности перед протягиванием наносят пленкообразующие вещества (олифу, масляный лак, мочевино-формальдегидные смолы).
Для термической обработки поверхностей плоских и изогнутых подробностей используются особые термопрокатные станки, в которых поверхности подробности прокатывают под нагретыми вальцами. Перед прокатыванием на поверхность подробностей наносят слой мочевино-формаль-дегидного клея. Обработанные так подробности имеют ровную и легко блестящую поверхность, смогут использоваться в качестве внутренних элементов изделий (полки, перегородки) без. дополнительного нанесения лаковых или других покрытий.
Обессмоливание
оптимальнеесмолу удалять, обрабатывая поверхности обессмоливающими составами, каковые по их действию разделяются на растворяющие и омыляющие.
К растворяющим составам относятся ацетон, спирт, бензол и другие органические растворители, прекрасно растворяющие живицу и еловую серку.
Довольно большая цена, огнеопасность спирта и ацетона и высокая токсичность бензола ограничивают их использование для данной цели. Исходя из этого чаще применяют для обессмоливания омыляющие средства. При обработке поверхности древесины растворами щелочей последние образуют со смолой растворимые мыла, легко смываемые после этого водой.
Для обессмоливания поверхность древесины натирают горячим (60 °С) 5—6%-ным раствором углекислого либо 4—5%-ным раствором едкого натра. Омыленную тёплой щелочью смолу смывают после этого горячей водой (25 °С) либо 2—3%-ным раствором соды.
От действия щелочи древесина пара темнеет, исходя из этого при прозрачной отделке древесины хвойных пород таковой метод обессмоливания возможно использовать только при окрашивания поверхности в довольно чёрные тона.
Отбеливание
Отбеливание как правило создают вручную методом нанесения составов тампонами. Для отбеливания используют перекись водорода разной концентрации с нашатырным спиртом. ВПКТИМом рекомендован следующий раствор для отбеливания подробностей, облицованных строганым шпоном из берёзы единиц и древесины: 10 ясеня количества 20%-ного раствора перекиси водорода и 1 единица количества 20%-ного водного раствора аммиака.
При отбеливании поверхность обрабатывают на плоскополировальном станке ПП-3 либо вручную тампоном. По окончании отбеливания поверхности сушат при температуре 45—50 °С —1 ч, 18—23 °С — 3 ч; выдерживают их по окончании сушки при температуре 45—50 °С — 24 ч, 18—23 °С —48 ч.
При применении щавелевой кислоты процесс отбеливания протекает более скоро. Щавелевая кислота требует осмотрительного обращения, и нейтрализации поверхности 2%-ным раствором буры.
Крашение
Крашение используют для усиления естественного цвета древесины, придания ей новой окраски либо однообразного цветового тона подробности либо изделию. При подготовке изделий под прозрачную отделку крашение может осуществляться протравами, пигментами и красителями.
Существуют разные методы крашения этими материалами: вручную (кистью и тампоном), пневматическое распыление, окунание, распыление при повышенном давлении («сухое»), крашение посредством вальцов, крашение на корню, крашение под давлением, в горяче-холодных ваннах.
По глубине проникания красящих растворов в древесину крашение (прямое и протравное) возможно поверхностным и глубоким.
Поверхностное крашение производится краткосрочным действием красящего состава на поверхность; наряду с этим он попадает лишь в верхний слой древесины (на глубину до 0,5 мм).
При глубоком крашении красящий состав воздействует на древесину более долгое время. Он попадает глубоко либо полностью в древесину при выдерживании ее в красящем растворе, нагнетании его в поры древесины либо при всасывании раствора деревом (крашение «на корню»).
Для крашения древесины чаще используют готовые водные растворы и кислотные красители красителей. При необходимости стремительной сушки окрашенной поверхности либо для придания большей яркости тона окраски применяют спиртовые красители.
При подборе того либо иного тона и цвета окраски древесины появляется необходимость в приготовлении смеси красителей на месте. Для этого сперва готовят растворы исходных красителей, после этого их смешивают и пробным окрашиванием образцов из древесины, подлежащей окрашиванию, подбирают необходимое соотношение красителей в смеси.
Для изготовление красящих растворов используют мягкую воду. Твёрдую воду смягчают кипячением либо додают к ней 0,1—0,5% кальцинированной соды.
Краситель растворяют в тёплой воде. Для этого отвешенное по расчету количество красителя растирают
в маленьком количестве тёплой воды до получения однородной кашицы, без комков. После этого додают другую воду (по рецепту). По окончании полного растворения красителя раствор фильтруют через два слоя марли и охлаждают до комнатной температуры.
При приготовлении гуминового красителя раствор отстаивают в течение не меньше 24 ч, по окончании чего его с опаской сливают, дабы не взмутить появившийся на дне осадок.
Растворы протрав готовят методом размешивания солей металлов в чистой мягкой тёплой воде с разбавлением и последующим фильтрованием водой до нужной концентрации. В зависимости от желаемого тона приготовляют 0,5—5%-ные растворы протрав. Все растворы протрав и красителей готовят и хранят в чистой нержавеющей посуде.
Грунтование
Грунтовочные составы наносят кистью, тампоном, пневматическим распылением, на вальцовых станках, обливом, окунанием.
тампоном и Кистью составы наносят при проведении ремонта изделий из древесины, на небольших фирмах и в мастерских.
Пневматическим распылением грунтовки наносят в основном на подробности и изделия решетчатой формы (стулья, кресла), изделия, декорируемые в собранном виде (футляры часов, радио- и телеприемников, устройств), изделия с фасонными поверхностями (лыжи, профильные элементы изделий мебели). Данный метод может использоваться и при грунтовании плоских элементов — щитов. Для пневматического распыления грунтовок применяют пневматические распылители.
Форма струи в зависимости от вида грунтуемых поверхностей возможно круглая — для маленьких подробностей, кромок; плоская вертикальная — для громадных поверхностей, расположенных вертикально.
Грунтовочные составы наносят перекрестным методом узким слоем. Количество покрытий по большей части одно. К недочётам этого метода относятся: повышенный расход грунтовочных составов, маленькая производительность, недостаточно хорошие санитарно-гигиенические условия труда.
Грунтование на клеенамазывающих станках высокопроизводительно и экономично. Для нанесения грунтовочных составов по этому способу используют нестандартные клеенамазывающие станки, станки КВ-9, KB-14,
KB-18, KB-28 с дозирующими устройствами (валиками) для нанесения клея и другие грунтовочные автомобили. Такие станки владеют высокой производительностью. На них вероятно одновременное грунтование двух сторон плоских подробностей.
Скорости подачи на этих станках смогут быть до тридцати метров/мин.
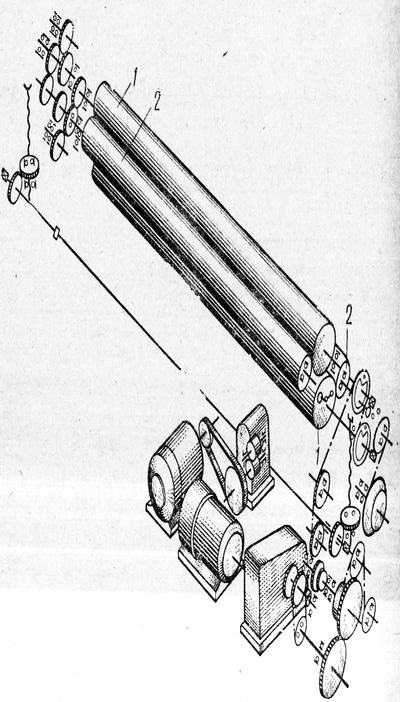
Рис. 1. Кинематическая схема клеенамазывающего станка для двустороннего нанесения грунтовки:
1 — наносящий валик, 2 — дозирующий валец
Клеенамазывающие станки имеют обрезиневные наносящие и железные хромированные дозирующие вальцы.
Схема клеенамазывающего станка для двустороннего нанесения грунтовки приведена на рис. 1.
Подробность подают между наносящими вальцами, благодаря которым грунтовка наносится на верхнюю и нижнюю поверхности подробности. Дозирующими вальцами регулируют количество грунтовки, нужное для нанесения на подробность.
Грунтование способом облива имеет широкое распространение при отделке щитовых подробностей. Для грунтования применяют лакообливные автомобили МН-1, ЛМ-3 и нестандартные.
Грунтование щитовых подробностей грунтовкой на базе карбамидных смол в прессах с обогреваемыми плитами содержится в следующем. На поверхность щитов наносят грунтовку на базе карбамидных смол МФ-17, МФ, М-60. После этого щиты устанавливают на ребро в стеллажи либо тележки и выдерживают 30—45 мин при температуре цеха.
Затем щиты помещают в многоэтажные гидравлические прессы с обогреваемыми плитами. Под действием тепла и давления грунтовочный слой полимеризуется. Для получения ровной и ровной поверхности щиты загружают в пресс между железными прокладками, шероховатость поверхности которых должна быть не ниже 8-го класса (ГОСТ 2789—73).
Между металлическими прокладками и плитами пресса крепят страницы термостойкой резины.
Чтобы не было прилипания грунтовочного слоя к металлическим прокладкам их через 10 запрессовок смазывают смесью, складывающейся из 85% минерального масла «Фригус» и 157о полибутоксилоксана, либо олеиновой кислотой перед каждой запрессовкой.
Для ускорения сушки лаковой пленки за счет аккумулирования тепла выгруженные из пресса щиты возможно лакировать сходу, без выдержки.
Вероятна кроме этого полимеризация грунтовочного слоя на проходных термопрокатных станках, каковые имеют обогреваемые валы-цилиндры.
Принцип работы термопрокатного станка содержится в следующем. Щитовые подробности, на поверхность которых предварительно нанесен и подсушен слой грунта (смола МФ-17, М-70), пропускают через станок, оснащенный шестью (по три на каждую пласть) обогреваемыми электрическим током рабочими валами, имеющими полированную поверхность. При пропуске деталей через станок слой грунта полимеризуется, получая ровную, ровную поверхность.
Порозаполнение
Порозаполнение возможно создавать при получении прозрачных покрытий нитроцеллюлозными, мочевино-формальдегиднымн, полиэфирными и другими лаками. По большей части же порозаполнению подлежат поверхности, декорируемые нитроцеллюлозными лаками с получением высококачественной поверхности .
Порозаполнители наносят на поверхности вручную кистью либо тампоном, на клеенамазывающих, вальцово-ракельных, тампонных полировальных, глянцевальных станках ГЛП.
Ручное порозаполнение используют, в основном, при обработке фасонных изделий и деталей в собранном виде. Порозаполнитель наносят тампоном, а после этого этим же тампоном втирают порозаполнитель сперва на протяжении, а после этого поперек волокон. По окончании втирания порозаполнителя поверхность нужно шепетильно протереть фланелевой тканью.
При механизированном порозаполнении порозаполнитель наносят на поверхность вручную тампоном либо кистью, а втирают его в поры древесины тампонами либо дисками полировальных и глянцевальных станков с механизированной подачей подробности либо суппортов с дис-нами. По окончании механизированного втирания порозаполни-теля поверхность вручную протирают фланелевой тканью.
Для порозаполнения постоянным методом создано специальное оборудование: клеенамазывающие и вальцово-ракельные станки. На вальцово-ракельных станках производится механизированное нанесение поро-заполнителя на поверхность, его выравнивание и втирание поверхности.
На рис. 2 продемонстрирована схема вальцово-ра-кельного станка постоянного действия для заполнения пор, принцип работы которого содержится в следующем. Щит подается вальцами в станок. На нижнюю сторону щита валиком наносится порозаполнитель из ванны. Дозирующим вальцом 4 регулируется количество порозапол-нителя, наносимого на поверхность. Втирание порозапол-нителя в поры осуществляется ракелем с прекрасно выверенной заоваленной кромкой.
Второй по ходу перемещения подробности ракель с острой кромкой снимает избыток поро-заполнителя с поверхности. Ракелем 8 выполняется окончательное втирание.
Существуют и другие схемы вальцово-ракельных станков для порозаполнения, а также станки, у которых порозаполнитель втирается не только ракелями, но и особыми колодками, двигающимися поперек волокон, а совсем поверхность протирается вальцами.
На рис. 3 продемонстрирован станок ПЗЩ постоянного действия для порозаполнения щитов. Деталь подается в станок роликами. На верхнюю сторону подробности вальцовым механизмом наносится порозаполнитель.
Порозаполнитель в поры втирается механизмом.
Рис. 2. Схема вальцово-ракельного станка для заполнения пор:
1 — щит, 2 — подающие вальцы. 3 — ванна, 4 — дозирующей валец, 5 — наносящий валик, 6 — втирающий ракель, 7 —ракели для снятия излишков гюрозаполнителя, 8 — ракель для окончательного втирания
Большие размеры обрабатываемых подробностей 1800Х X800X60 мм.
Эффективность порозаполнения (процент заполнения пор) должна быть для порозаполнителей КФ-1, ЛК-3, ЛК-4, ЛК-5 не ниже 65%; для порозаполнителей КФ-2, КФ-3, КФ-4, ТБМ-1, ТБМ-3, ТБМ-4 — не ниже 70%.
Грунты и порозаполнители сушат при комнатной температуре (18—20 °С), при повышенной температуре — в конвективных и терморадиационных сушильных камерах. Для неестественной сушки загрунтованных и порозаполненных поверхностей используют сушильные камеры, применяемые для сушки лаков.
Рис. 3. Станок П31Д для порозаполнения щитов:
1 — станина, 2— ролики подачи, 3 — механизм втирания, 4 — втирания и механизм нанесения порозаполнителя
Загрунтованные и порозаполненные поверхности по окончании сушки шлифуют для снятия вставшего ворса, отдельных неровностей, в следствии чего получается ровная ровная поверхность, готовая к последующей отделке.
Для шлифования используют ленточно-шлифовальные, вибрационные и щеточные станки. Шлифование грунта производится шкуркой № 6—5, а порозаполнителя — № 4—3. Не хватает загрунтованные и порозаполненные места подправляют вручную посредством тампона.