Порошковая металлургия
Способ получения разных деталей и материалов из железных порошков методом их последующего спекания и прессования, минуя стадию литья и плавления металла, именуется порошковой металлургией.
Разработка изготовления подробностей способами порошковой металлургии напоминает разработку керамического производства, исходя из этого продукцию порошковой металлургии часто именуют металлокерамикой.
Порошковая металлургия есть одним из самые перспективных способов получения изделий, владеющих особенными особенностями — пористостью, высокой твердостью, тугоплавкостью и т. д. Данный способ имеет громадные преимущества по сравнению с другими классическими методами изготовления изделий, такими как литье, штамповка, механическая обработка и др., так как разрешает приобретать совсем готовые изделия или подробности с малыми технологическими припусками.
Высокие технико-экономические преимущества способа порошковой металлургии перед вторыми методами производства (экономия металла, возможность замены цветных и дефицитных металлов менее дефицитными и более недорогими без ущерба для особенностей изделий, увеличение производительности труда, получение материалов со особыми особенностями и т. п.) создали предпосылки для широкого применения порошковых материалов в разных областях техники, непрерывного выпуска расширения и роста деталей их номенклатуры.
На данный момент металлокерамические изделия активно используются в виде антифрикционных, фрикционных и конструкционных подробностей, а также в виде фильтров, магнитов, электроконтактов, подробностей особой техники и т. д.
Утраты металла при изготовлении этих подробностей способами порошковой металлургии составляют 3—7%, в то время как при простом литье отходы материала время от времени достигают 80%.
Главными технологическими операциями процесса изготовления металлокерамических изделий и материалов являются:
а) приготовление порошковой шихты;
б) прессование — формование заготовки;
в) спекание;
г) контроль качества готовой продукции.
Для увеличения механических особенностей подробностей, и для придания им некоторых особых особенностей дополнительно смогут использоваться: допрессовка с повторным спеканием; калибровка; пропитка более легкоплавкими металлами, маслом и пластмассами; мехаиияеская, термическая и химико-техническая обработка.
Для получения шихты в качестве исходных материалов используются порошки чистых металлов, их сплавов либо смеси порошков тех либо иных металлов с легирующими и технологическими добавками.
Под приготовлением шихты подразумевается комплекс операций, снабжающих получение изделий с заданными особенностями.
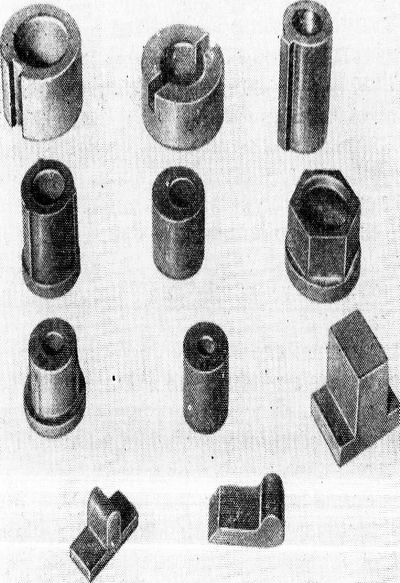
Рис. 1. Металлокерамические подробности
Все операции, которые связаны с приготовлением шихты, нужно делать шепетильно, поскольку от качества их проведения сильно зависят свойства готовых изделий.
Под формованием (прессованием) железных порошков и их смесей понимается операция, из-за которой под действием приложенных сил из бесформенного сыпучего порошка получаются довольно прочные заготовки с учетом допусков на усадку при спекании, и припусков, которые связаны с какой-либо нужной обработкой.
Прессование может осуществляться в закрытых и открытых пресс-формах, способом мундштучного и гидростатического прессования, и прокаткой вольно насыпанного порошка и порошка, заключенного в эластичные оболочки.
Прессование может производиться при простых температур pax — холодное прессование и прн повышенных температурах — горячее прессование. На практике широкое использование находит способ холодного прессования в закрытых пресс-формах. Он есть наиболее простым, легко поддается автоматизации и разрешает приобретать изделия разных размеров и форм.
Холодное прессование в закрытых пресс-формах содержится в засыпке и дозировке шихты в пресс-формы, выталкивании и прессовании прессовок из пресс-форм.
Назначение дозировки — обеспечение подачи совершенно верно нужной порции порошка в пресс-формы. Осуществляется дозировка или весовым, или объемным способом. самый точным способом дозировки есть весовая дозировка, но в связи с малой производительностью она используется лишь при необходимости получения изделий с совершенно верно заданной плотностью.
При массовом производстве, в особенности при автоматическом прессовании, по большей части используется объемная дозировка. Выполняется она при помощи свободного заполнения совершенно верно вычисленной полости пресс-формы. Недочётом этого способа есть возможность получения изделия неодинаковой плотности за счет трансформации технологических черт порошковой шихты.
Существует два способа прессования: одностороннее и двустороннее.
Недочётом одностороннего прессования есть твёрдости и неравномерность плотности по количеству изделия. Вследствие этого оно по большей части используется для того чтобы несложной конфигурации (цилиндры, втулки, контакты и т. д.) и малой высоты, отношение которой к диаметру не более двух, а к толщине стены не более трех.
Для изготовления изделий с равномерными твёрдостью и плотностью используется двустороннее прессование, которое может осуществляться или методом приложения давления прессования к верхнему и нижнему пуансонам, или за счет приложения упрочнений прессования лишь к одному верхнему пуансону, но с принудительным опусканием («плаванием») матрицы.
На рис. 2 продемонстрирована схема таковой пресс-формы. Порошок засыпают в матрицу, закрепленную в плавающей плите. При включении пресса верхний пуансон идет вниз, осуществляя прессование порошка, наряду с этим матрица не мешает уплотнению порошка, поскольку может скользить по колонкам.
Для выталкивания изделия на матрицу устанавливают стакан, надавливая на что, опускают матрицу, и изделие вольно снимают с нижнего пуансона.
Двустороннее прессование используют, в случае если высота меньше пяти диаметров и двадцати толщин стены.
Групповые способы получения металлокерамики. В случаях изготовления маленьких партий подробностей целесообразно использовать групповые блоки со сменными элементами.
Разглядим последовательность конструкции групповых блоков, применяемых на некоторых фабриках для того чтобы мелкосерийного и серийного производств.
Рис. 2. Схема двустороннего прессования
Групповой блок помогает для закрепления на гидропрессе группы сменных разногабаритных пресс-форм, предназначенных для прессования подробностей из железных пресс-порошков.
Рис. 3. Групповой блок для металлокерамики
Верхняя плита блока соединена с нижней плитой при помощи двух колонок и двух втулок, расположенных в блоке консольно. Благодаря такому размещению колонок обеспечивается вольный подход в зону прессования, существенно увеличивается удобство загрузки пресс-порошка в загрузочную камеру пресс-форм и создается условие механизированного удаления отпрессовок в конце цикла прессования.
Подвижная часть пресс-форм прикрепляется к верхней плите, а неподвижная часть — к нижней плите. Закрепление производится при помощи прихватов, болтов, сферических шайб и сферических гаек. Опорная часть прихватов имеет радиусную поверхность, которая содействует закреплению плит пресс-форм с разными высотами.
Наряду с этим изменение горизонтального положения прихватов не ухудшает надежности закрепления, поскольку болты сохраняют неизменно собственный вертикальное положение благодаря наличию в шайбе и гайке сферической поверхности.
Рис. 4. Групповой блок для металлокерамики
Наконечник резьбовой частью крепится к выталкивающему устройству пресс-форм и при помощи Т-образного паза, расположенного в нижней части наконечника, соединяется с хвостовиком. Благодаря таковой хвостовика и конструкции наконечника достигается эргономичное и свободное крепление этих подробностей к пресс-нижнему штоку и формам гидропресса.
наконечник и Хвостовик принимают силовое действие от штока и передают его выталкивающему устройству пресс-форм, снабжающему механическое выталкивание отпрессованных подробностей из формообразующей части пресс-форм.
Использование опорных подкладных плит и плит, упрощает разработку изготовления верхней и нижней частей блока.
Крепление указанных подробностей к верхней и нижней плитам блока осуществляется винтами.
Групповой блок, изображенный на рис. 4, устанавливается на механический пресс с нижним гидравлическим выталкивателем.
Плита крепится к верхнему ползуну пресса, и в ней при помощи гайки закрепляется верхний прессующий пуансон.
Главным преимуществом есть то, что матрица блока плавающая и плотность подробности при большой ее высоте регулируется машинально в ходе прессования за счет уто-пания матрицы на пружинах.
Матрица вкладыша крепится в гнезде плиты. При помощи гаек регулируется количество загрузочной камеры для засыпки порошка. Гайки 6 при работе на простых плоских подробностях опускаются вниз и в работе не участвуют.
Рис. 5. Формовкладыш к групповому блоку
В случае если же подробность ступенчатая, то для ее получения применяют гайки, умелым методом подбирая необходимый зазор. На рис. 1.38 продемонстрирована конструкция сменного элемента.
Рис. 6. Групповой блок для прессования
Групповой блок устанавливается на пресс-автомат 1501. Блок складывается из двух главных частей — верхней и нижней.
Верхняя часть содержит обойму с хвостовиком, в которой крепится планками верхний прессующий пуансон вкладыша.
Нижняя часть блока складывается из двух взаимно перемещающихся на протяжении оси частей: неподвижного основания и скрепленных между собой при помощи четырех обоймы и колонок плиты, каковые смогут перемещаться относительно основания на протяжении оси пресса. В основании крепится нижний прессующий пуансон-толкатель вкладыша в гнезде, образуемом двумя планками, и подкладкой. Матрица вкладыша устанавливается в обойму и крепится накладкой.
К плите двумя планками крепится стержень вкладыша, оформляющий внутреннее отверстие подробности, в случае если это требуется. В данной плите закреплен кроме этого стержень , что есть двигающим элементом блока. Он соединен с нижним рабочим штоком автомобили при шайб и помощи гаек.
Перемещением верхнего пуансона, входящего в матрицу на 4—10 мм, происходит маленькая подпрессовка и по большей части запирание камеры прессования, по окончании чего начинается одновременное перемещение вниз верхнего пуансона и нижнего штока вместе с матрицей и внутренним пуансоном.
Этим перемещением и совершается главное прессование подробности, т. е. матрица, закрытая сверху пуансоном, как бы надвигается на без движений стоящий нижний пуансон — толкатель.
По окончании процесса прессования верхн-ий пуансон отходит, а длящееся перемещение матрицы вниз есть уже перемещением выталкивания прессовки из матрицы.
Надвигающийся бункер пресса сталкивает прессовку в тару и создаёт засыпку новой дозы порошка в полость вкладыша, поскольку нижний пуансон — толкатель — к этому времени снова займет собственный нижнее исходное положение.
Для изготовления достаточно прочных заготовок при холодном прессовании в закрытых пресс-формах используются большие удельные давления, каковые в зависимости от свойств и необходимой пористости исходных компонентов шихты колеблются в пределах от 200 до 1000 кПа.
При прессовании в закрытых пресс-формах смогут быть использованы как механические, так и гидравлические прессы особого назначения, и прессы, используемые для прессования пластмасс, оснащенные особыми приспособлениями.
На данный момент этим способом изготовляется много подробностей массой до 2,5 кг.
Недочётами способа прессования в закрытых пресс-формах являются ограниченность размеров изготовляемых изделий по весу и размерам (большая масса изделий при прессовании в пресс-формах достигает не более 20— 30 кг), и необходимость применения прессов громадной мощности.
На данный момент создан последовательность способов, снабжающих получение заготовок громадной больших объёмов и длины. При изготовлении изделий громадной длины (труб, прутков, лент и т. п.) используются: прокатка железных порошков, мундштучное прессование, шликерное литье, гидростатическое прессование.
Кроме этих способов на данный момент создан ряд других: прессование взрывом, центробежное и вибропрессование н т. д., каковые расширяют возможности порошковой металлургии. Во всех этих случаях необходимо предусматривать возможность применения технологической оснастки со сменными элементами, что разрешает рационально применять данный прогрессивный способ в условиях мелкосерийного производства.
Частенько при изготовлении изделий со особыми особенностями применяется способ тёплого прессования, при котором совмещается процесс прессования с процессом спекания.
Заготовки, полученные по окончании прессования, в большинстве случаев, владеют низкими механическими особенностями, а также в ряде случаев не имеют нужных химико-физических особенностей. Вследствие этого полученные по окончании прессования «сырые» заготовки подвергают спеканию. Спекание производится при температуре, составляющей 0,7—0,9 от температуры плавления металла порошка однокомпонентной порошковой шихты либо температуры плавления главного компонента в многокомпонентной порошковой смеси.
В ходе спекания за счет качественного и количественного трансформации контактов, связанного с громадной подвижностью
атомов при повышенных температурах, возрастает поверхность сцепления частиц, увеличиваются прочность и плотность изделия, и достигаются нужные химико-физические особенности.
Спекание производится в вакууме либо в контролируемой воздухе (восстановительной либо нейтральной).
Продолжительность выдержки при температуре спекания в зависимости от размеров изделий и состава шихты может составить от нескольких десятков мин. до нескольких часов.
Для увеличения плотности используют повторное спекание, которое усиливает механические особенности подробностей.
Двукратному спеканию и прессованию подвергаются кроме этого магнитномягкие материалы, магнитная проницаемость которых быстро падает с повышением пористости.
Размеры металлокерамических подробностей по окончании спекания получаются с точностью до 12—14-го квалитетов и шероховатость поверхности до Rn = 10 мкм. Калибрование в особых пресс-формах при удельном давлении до 1000 мПа повышает точность до 8—11-го квалитетов при шероховатости поверхности до Ra = 1,25 -ь 2,5 мкм.
По окончании калибрования на поверхность подробности возможно наносить каждые гальванические покрытия.
Способ порошковой металлургии имеет собственные, ограничивающие его использование изюминки. Порошковая масса не в состоянии заполнить углы формы. Прессование происходит в вертикальном направлении, исходя из этого нереально верно отформовать углубления, резьбы и другие элементы подробности, расположенные под прямыми углами к направлению прессования.
Так как порошок под давлением фактически не перемещается в боковых направлениях в контейнере, достаточное количество порошка должно быть размещено совершенно верно в том месте, где это нужно, чтобы обеспечить равномерную плотность металла изделий. Это условие особенно принципиально важно при прессовании подробностей с узкими стенками либо переменного сечения.
Неравномерная плотность приводит к большим напряжениям в подробностях на протяжении их изготовления, в особенности при спекании, при котором появляются неравномерные усадки, коробление а также трещины.
направляться избегать таких не сильный частей подробности, как узкие стены, узкие шпоночные канавки, острые углы и т. п., по причине того, что они довольно часто разрушаются в конце хода выталкивания. приливы и Различные выемки необходимо располагать как возможно ближе к верхнему краю контейнера и, в случае если быть может, делать их конусообразными для облегчения выталкивания. Конусность стенок подробностей должна быть в пределах 5—10’.
Круговые канавки, обратная конусность и резьба в большинстве случаев выполняются механической обработкой по окончании спекания.
Исполнение отверстий в направлении прессования не воображает затруднений, и получаются они посредством сердечников любой формы. Но, в случае если отверстия малы, необходимы узкие сердечники, каковые скоро изнашиваются и изгибаются под действием порошка, перемещаемого при прессовании.
Для выталкивания цилиндрических отверстий используются относительно простые и недорогие инструменты. Вследствие этого вместо прямоугольных, квадратных и других форм отверстий, где это возможно, направляться делать цилиндрические.
Бытует вывод, что способ порошковой металлургии из-за большой стоимости технологической оснастки экономичен по большей части в условиях изготовления многочисленных партий подробностей. До появления группового способа изготовления подробностей такое же вывод существовало и довольно вероятного применения литья под давлением, штамповки жидкого металла, изготовления подробностей из пластмасс и т. д. Но, как уже указывалось выше, классификация подробностей, использование технологической оснастки со сменными элементами, создание специального технологического оборудования открывают много возможностей применения способа порошковой металлургии в условиях не только серийного, но и мелкосерийного производства.
Автоматизация производства металлокерамики. При изготовлении способом порошковой металлургии подробностей типа втулок, дисков, валов и планок используются автоматические технологические комплексы. Эти комплексы складываются из весового устройства для дозировки порошка, формовочного пресса К-8130 с промышленными роботами типа «Гном» для загрузки форм, их установки и разгрузки отформованной заготовки на разгрузочное устройство в особую графитовую тару; печи спекания, оснащенной средствами автоматики и безокислительной средой; пресса калибровочного, обслуживаемого промышленным роботом для загрузки, управления и разгрузки прессом; контрольного устройства с промышленным роботом для вторичного спекания по окончании калибровки.
Схема технологического комплекса изготовления подробностей способом порошковой металлургии приведена на рис. 7.
Данный комплекс рекомендован для того чтобы типа втулок, валов, дисков, планок из порошка в автоматическом режиме. В комплексе осуществляются следующие операции: подача, дозирование, засыпка порошка в форму, фйрмовка, спекание, калибровка, повторное спекание, контроль.
Рис. 7. Непроизвольный комплекс изготовления металлокерамических подробностей:
1 — тара с порошком; 2 — промышленный робот типа МРЛ-90-901; 3 — весовое устройство; 4 — пресс формовочный; 5 — разгрузочное устройство; 6 — графитовые лодочки для отпрессованных подробностей; 7 — конвейер; 8 — печь спекания; 9 — пресс калибровочный; 10 — контрольное устройство
Управление комплексом осуществляется от мини-ЭВМ «Электроника-60», имеющей вход сигналов с высшего управления. В условиях серийного производства нужно использовать групповые формы со сменными вкладышами. До применения форм, конструкция которых обеспечит автоматическую замену сменного вкладыша, эта работа может производиться рабочим-оператором.