Роль серы в процессах обработки металлов
Значение ее соединений и серы в процессах резания металлов, обработки и полирования давлением все более подтверждается рядом новейших работ многих авторов. Интерес к выяснению действия серы особенно возрос за последние годы.
Роль серы неоднозначная. С одной стороны, сера, сероводород и другие сернистые соединения как коррозийные агенты способны привести к серьёзным разрушениям металлов. Такое разрушение подробностей оборудования замечают в нефтехимической индустрии, а также в разных отраслях химической и газовой индустрии. Земля, природные воды, газ и кое-какие сорта нефти, которые содержат серу, являются коррозийными агентами.
Газ, содержащий до 12 частей H2S на каждые 3500 куб. м газа, при насыщении сероводорода влагой приводит к интенсивному разрушению сталей.
Кое-какие сорта нефти восточных районов СССР содержат большое количество ее соединений и серы (4—6%). При получении жидкого горючего из таковой нефти в него переходит (в зависимости от метода очистки) от десятых долей до 2—3% серы. Изучения продемонстрировали, что коррозия металлических и чугунных деталей двигателей (цилиндров и поршневых колец), трудящихся на жидком горючем, возрастает пропорционально содержанию в нем серы.
При сгорании горючего которые содержат серу продукты преобразовываются в сернистый газ. Последний, соединяясь с парами воды, кроме этого образующимися при сгорании горючего, переходит в сернистую кислоту, а при сотрудничестве с кислородом воздуха — в серную кислоту. Обе кислоты являются очень агрессивными реагентами.
Изучение износа поршневых колец при помощи радиоактивных изотопов продемонстрировало, что при эксплуатации дизеля износ подробностей обусловливается в основном наличием серной кислоты, образующейся при сгорании сернистого горючего.
Изучение износа двигателя в зависимости от влияния сернистого и серного ангидрида, вводимого неестественным методом, говорит о том, что в случае если топливно-воздушная смесь содержит больше ‘/з серного ангидрида (S03), то износ поршневых колец двигателя ускоряется в 40 раз по сравнению с работой на горючем, свободном от серы.
Известно огромное значение примесей серы в железных сплавах. Одна сотая процента примесей серы быстро снижает (до 50%) жаропрочность сплавов на никелевой базе.
Такое влияние примесей стало понятным в следствии изучения сплавов с радиоактивным изотопом серы. Оно продемонстрировало, что сера по большей части находится на поверхности зерен металла. Так, кроме того при очень малом содержании примеси (десятые, сотые доли процента) сера, концентрируясь в виде легкоплавкого сернистого никеля в узком пограничном слое, быстро понижает жаропрочность стали.
Разрушение металла в производственных условиях довольно часто происходит, как мы показывали, в следствии совместного абразивного процессов изнашивания и действия коррозии, в противном случае говоря, химико-механического процесса. В случае если в чистом азоте скорость абразивного изнашивания образовывает 4 мг/час на пример, то при введении в абразивный поток 0,7% сернистого ангидрида вместе с парами воды эта скорость возрастает в 4,5—5,5 раза, а при введения лишь паров воды (числом 20%) — в 2 раза.
На рис. 1 приведена зависимость износа углеродистой стали от содержания сернистого ангидрида в абразивной среде. Как видно, тут с повышением концентрации сернистого ангидрида с 0,005 до 0,7% скорость изнашивания стали возрастает по логарифмической кривой.
Предстоящее повышение концентрации сернистого ангидрида уже не оказывает влияния на интенсивность изнашивания.
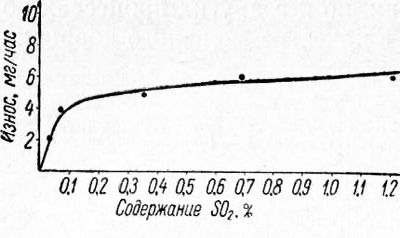
Рис. 1. Зависимость износа углеродистой стали от содержания сероводорода в абразивной среде
Подобная зависимость взята и при изучении изнашивания стали в той же среде, но содержащей еще и 20% паров воды.
Разрушения, найденные в трубопроводах, отстойниках конденсаторов, нагнетательных патрубках, других деталях и коллекторах компрессоров, результат эрозии и совместного воздействия коррозии.
Возможно привести значительно большее число аналогичных примеров, показывающих огромную разрушительную силу коррозийных процессов с участием серы.
Но в случае если при эксплуатации автомобилей коррозийные процессы являются, без сомнений, вредными, то при обработке металлов условия самоё интенсивного коррозийного разрушения смогут быть очень нужны.
При резании осерненные эмульсии в любых ситуациях оказывают самоё благоприятное воздействие. Так, к примеру, лучшей смазочно-охлаждающей жидкостью при операции развертывания отверстий, изготовленных из титаного сплава, есть масло с добавкой хлора и серы.
При нарезании наружной резьбы диаметром 18—28 мм на подробностях из сталей марок Х18Н12МЗТ и Х18Н9Т с применением в качестве смазочно-охлаждающей жидкости смеси сульфофрезола и олеиновой кислоты стойкость набора резцов из трех штук достаточна для работы в течение одной смены. Нарезание резьбы метчиками с применением неразбавленного минерального масла затруднено благодаря сильного налипания металла на метчик; с повышением содержания серы в минеральном масле до 1,5% налипание значительно уменьшается, а коэффициент трения понижается на 10% и более.
Проверка эффективности действия разных жидкостей по трансформации сил резания при протягивании сплава ЭИ437 продемонстрировала, что олеиновая кислота понижает силу резания на 7,5% и усиливает чистоту поверхности; 10%-ная эмульсия осерненного эмульсола понижает силу резания на 16%.
При шлифовании температуры и высокие давления содействуют установлению целого контакта между абразивным зерном и обрабатываемым металлом. Использование масла с добавлением 10% активной серы снижает потребную мощность шлифования.
На Коломенском тепловозостроительном заводе им. В. В. Куйбышева проводилось изучение эффективности смазочно-охлаждающих жидкостей, складывающихся из сульфофрезола, керосина, олеиновой кислоты и три-этаноламина. В ходе изучения определялось влияние отдельных составляющих на стойкость инструмента при обработке нержавеющих сталей. Согласно данным завода, самый действен состав, в который входит 24% сульфофрезола, 30% олеиновой кислоты, 1% три-этаноламина и 45% керосина.
Смазывающе-охлаждающая жидкость указанного состава внедрена на операциях нарезания резьб, протягивания, зубофрезерования и развертывания отверстий.
Стружкоотделение возможно существенно улучшено еще и введением в обрабатываемый сплав серы.
В хромоникелевую нержавеющую сталь марки Х18Н9 в связи с повышенным содержанием в ней марганца выяснилось нужным добавление 0,2—0,4% серы, и селена; в ферритную сталь с содержанием 13%: хрома додают 0,4—0,7% серы и 0,05—0,25% циркония. Эти компоненты играются хорошую роль при растачивании и сверлении: они мешают образованию нароста, разрешают повышать скорость резания без ухудшения шероховатости обрабатываемой поверхности и приближают ее обрабатываемость к соответствующим показателям для углеродистых сталей.
Такое же влияние оказывает сера при введении ее много в автоматные стали, каковые составляют большую часть всего пруткового материала.
Опробования говорят о том, что при резании автоматных сталей стойкость резца с повышением содержания серы увеличивается от 0,03 до 0,37%. В один момент улучшается шероховатость поверхности при малых скоростях резания.
Сера влияет и на процессы полирования. С целью ускорения полирования были совершены испытания с разными химически активными препаратами: серой, красной кровяной солью, йодом, сернистым мышьяком, многосернистым кальцием, сернистым натрием, сернистым барием, сероуглеродом с серой, хлористой серой и др. Эти реактивы вводились или конкретно в полирующие вещества, или, в случае если это были водные либо спиртовые растворы, наносились на полировальник.
Заметное ускорение процесса полирования отмечается при введении в пасту серы, растворенной в сероуглероде при 22 °С (в 100 весовых частях сероуглерода удается растворить до 46 весовых частей серы), и при введении хлористой серы (S2C12), взятой при пропускании хлора через расплавленную серу. Введение серы в состав пасты содействует повышению съема оло-вянистой латуни на 15—17%.
Кое-какие из сернистых препаратов (к примеру, натрия и кальция) в начальный момент ускоряют процесс полирования, но благодаря их стремительного разложения на воздухе в присутствии воды процесс нарушается.
При добавлении в пасту «сухих» сернистых препаратов (сернистой сурьмы, фосфора красного, гипосульфита, кислого сернокислого калия) ускорения процесса не наблюдалось. В присутствии в один момент влаги и кислорода гипосульфит, сульфит и кислый сернокислый калий смогут выделять активные атомы серы, вступающие в химическое сотрудничество с железной поверхностью. Это разъясняется, по-видимому, свойством серы к аллотропическим метаморфозам с образованием молекул разной величины, где сера возможно как окисляющейся (дисульфидной и сульфидной), так и неокисляющейся (сульфатной).
Роль серы при износе и трении
самый сильным причиной, предотвращающим схватывание при трении, есть наличие на трущихся поверхностях пленок. Эти пленки владеют свойством скоро образовываться на поверхности металла и скоро восстанавливаться на тех участках, где они были по той либо другой причине нарушены.
соединения и Элементарная сера с активной серой первенствовалиприсадками к смазочным маслам для уменьшения трения. Начало их применения относится к прошлому столетию. Известно, к примеру, что для смазки подшипников вагонов и паровозов первых железных дорог в Российской Федерации использовалась смазка с присадкой серы, которая, по выражению экспертов того времени, «лучше охлаждала трущиеся части».
Использовалась черенковая сера прежде и в смазке не легко нагруженных подшипников прокатных станов для предотвращения от заедания трущихся поверхностей.
Но использование серы в таком виде было скоро покинуто благодаря коррозии цветных повышенного износа и сплавов стали.
В наше время к данному вопросу снова появился громадный интерес, вызванный следующим событием. Прежде требования к смазочным маслам для всех передач двигателей, аппаратов и механизмов удовлетворялись маслами, приобретаемыми из нефти.
В современных передачах достигнуты такие высокие удельные давления (30—50 т/см2) и скорости скольжения (100 м/сек), что в этих условиях обычная эксплуатация многих различных механизмов и современных двигателей уже не может быть обеспечена кроме того самыми лучшими смазочными маслами, приобретаемыми из нефти. Смазывающая свойство их выясняется довольно часто неэффективной: масла при большой температуре образуют большое количество нагара, скоро испаряются, дают повышенные износ и трение, приводят к опасности заедания и в следствии выясняются негодными для смазки.
Для удовлетворительных смазочных материалов для современных автомобилей потребовалось улучшить отдельные качества нефтяных масел добавками особых химических присадок, а во многих случаях изготовить смазывающие вещества методом синтеза разных химических соединений.
Обзор составов смазок за последние годы говорит о том, что все большее использование находят смазки с разными химически активными присадками (хлор, фосфор, сера), владеющими противозадирными особенностями. В качестве таких противозадирных присадок самоё широкое использование взяли соединения серы. При трении железных поверхностей в следствии сотрудничества с химическими веществами появляются соединения, уменьшающие повреждение и трение трущихся поверхностей.
Работами многих исследователей доказано, что в ходе реакции образуются фосфиды, соединения в виде хлоридов и сульфидные пленки, каковые достаточно действенно предотвращают яркий схватывание поверхностей и металлический контакт, сохраняя собственные противозадирные особенности до высоких температур. ‘Гак, сульфид железа (FeS) имеет температуру плавления 1193°, что снабжает противозадирное либо противосварочное воздействие его пленки до скоростей скольжения и высоких нагрузок. Хлорид железа (FeCh) имеет температуру плавления 670°. Хлорсодер-жащие присадки снижают коэффициент трения, но одновременно с этим владеют меньшей противозадирной эффективностью, чем серосодержащие присадки, в особенности полисульфиды и дисульфиды.
При сочетании серо- и хлорсодержащих присадок громаднейшая эффективность достигается, в случае если первая присадка, образуя сульфиды, реагирует с поверхностью железа стремительнее второй.
Вопрос о влиянии узкой сульфидной пленки, образующейся на металле, изучался еще в 1939 г. А. К. Зайцевым, применившим осерненные масла для предохранения трущихся поверхностей от вырывания и задиров, наряду с этим на поверхности мгновенно образовывалась узкая пленка сульфида железа, предохраняющая поверхность от задиров.
П. Е. Дьяченко установил хорошее воздействие образующихся на поверхности трения сернистых образований. Эти неметаллические образования в виде пленок, мешая сцеплению железных поверхностей, предотвращают заедание и делают вероятным скольжение при большой температуре.
Неуклонно расширяется использование противозадирных смазок, либо, как их именуют, смазок для очень больших давлений. Соответственно совершенствуются методы и составы смазок их опробования, создаются нужные установки. Еще в 1937 г. были испытаны 182 смазки. Из выдержавших опробования смазок 90% содержали химически активную серу.
Все рекомендуемые составы смазок в зависимости от содержащихся в них присадок смогут быть поделены на две группы: сернохлорные и серные. Эти смазки содержат серу в химически активной форме и предохраняют от заедания и задиров не легко нагруженные передачи разных типов. Свойство смазки для очень больших давлений выдерживать громадные нагрузки разъясняется образованием разъединяющей пленки, которая состоит не из масла, а из сульфида железа, образующегося конкретно на поверхности стали.
Осерненные смазки ускоряют износ трущихся поверхностей, но вместе с тем они повышают нагрузку заедания. На участках контактов при повышенных температурах в следствии химической реакции молекул серы либо хлора образуются узкие пленки сульфидов либо хлоридов, каковые и предохраняют поверхность металлов от яркого соприкосновения.
В данной связи смазки возможно поделить на две группы:
1) химического действия, предохраняющие от заедания, и 2) адсорбционного действия, увеличивающие маслянистость и действенные при относительно малых скоростях скольжения.
Смазки химического действия по собственной природе являются коррозийно активными, причем продукты коррозии владеют противосварочными особенностями, т. е. имеют высокую точку плавления и не образуют каких-либо легкоплавких соединений с металлом.
Так, выясняется, что химически активные вещества прекрасно предохраняют от износа, но не смогут надежно обезопасисть от заедания, и напротив, вещества, предотвращающие заедание, не уменьшают износа.
Так как в работе при повышенных температурах исключается использование смазочных масел, то появилась идея об применении в качестве жёстких смазок дисульфида молибдена (MoS2). Дисульфид молибдена в смазках понижает коэффициент трения (0,05—0,09) и износ металла благодаря изюминок его молекулярного строения. MoS2 имеет пластинчатую структуру, в которой его слои соединены между собой атомами серы. Молибден с серой связан весьма прочно, а связь между атомами серы не сильный.
Именно поэтому перемещение слоев дисульфида молибдена относительно друг друга осуществляется при не сильный упрочнениях сдвига, исходя из этого MoS2 есть самоё ценным смазочным материалом среди известных, среди них и графита.
Высокая адсорбция серы на поверхности металла п громадная прочность связи молибдена с серой разрешают при больших удельных давлениях частицам дисульфида молибдена не выжиматься из пар трения. Грузоподъемность узла трения при применении MoS2 находится в пределах 6000—20 000 кг/см2. Такая прочность смазочной пленки на поверхности металла обусловливается в основном громадными ядерными силами, действующими между атомами металла и серы.
Дисульфид молибдена владеет термической стойкостью в температурном промежутке от —70 до + 400° С и высокой химической стойкостью — он подвергается действию лишь кипящих соляной и азотной кислот, хлора и царской водки. Дисульфид молибдена не владеет магнитными свойствами и электропроводностью. Это разрешает применять его для защиты от коррозии, поскольку, образуя пленку на железной поверхности, он тем самым защищает металлы от электрохимических процессов, каковые в большинстве случаев происходят на границе металл — окружающяя среда.
За последние годы громадной интерес в отечественной индустрии и за границей приводит к новому процессу — сульфидирование, заключающийся в насыщении поверхностных слоев металла серой. Последовательность отечественных и зарубежных исследователей показывает на очень высокую эффективность сульфидирования как способа увеличения противозадирных особенностей и направляться металла. Имеется последовательность сообщений об успешном внедрении нового процесса в производство.
Но одновременно с этим во многих случаях взяты отрицательные результаты при опробованиях на изнашивание сульфидированных подробностей разных автомобилей и инструмента. Подобная противоречивость есть следствием недостаточной изученности свойств и нового процесса сульфидированного металла.
Процесс сульфидирования технологически несложен, не требует дорогого либо дефицитного оборудования и в полной мере доступен для применения на фабриках.
При существующем многообразии технологических способов сульфидирования конечно, что обработка в разных составах дает как следует разные результаты. Обработка в некоторых составах приводит только к образованию окислов на поверхности металла.
Последовательность составов дает промежуточные результаты, в то время, когда на металле образуются сульфиды и окислы. Необходимо признать, что структура сульфидных слоев на данный момент изучена еще не хватает.
Но можно считать установленным, что улучшение противозадирных особенностей связано по большей части с образованием сульфидов.
Сульфидирование, без сомнений, есть действенным способом увеличения противозадирных чугуна и свойств стали.
Покрытию смазкой MoS2 подвергают развёртки и сверла диаметром более 10 мм из быстрорежущих сталей. Твердосплавные резцы покрывать данной смазкой не нужно, поскольку это не дает заметного результата.
В вырубных и вытяжных штампах смазкой MoS2 покрываются вертикальные поверхности матриц и пуансонов. Не считая них целесообразно подвергать покрытию направляющие элементы вырубных штампов, каковые при монтаже смазывают молибдендисульфидной пастой либо 20%-ной суспензией MoS2 в масле. У вытяжных штампов смазкой MoS2 покрывают места скругления и все те поверхности, по которым скользит вытягиваемая подробность.
Использование MoS2 для вытяжных штампов исключает заедание подробностей и как правило снабжает безукоризненную обработку трудновытягиваемых материалов.
Вместо сульфидирования советуют более несложный метод приработки подробностей со смазкой, содержащей от 5 до 20% дисперсных частиц серы. Как утверждают авторы опытов, данный метод разрешает сократить время приработки подробностей еще более существенно, чем использование вышеуказанного сульфидирования поверхностей трения, наряду с этим время приработки значительно уменьшается с увеличением содержания серы в смазке.
Сера (при содержании ее в смазке числом до 0,4%) спустя пару часов работы всецело растворяется либо вступает со смазкой в химическую реакцию.
Увеличение содержания серы (более 0,4%) содействует сохранению ее частиц в смазке во взвешенном состоянии, что быстро уменьшает время приработки.
В работе А. В. Кривулина приведены результаты опробований на машине «МИ» несульфидированных и сульфидированных чугунных роликов при трении по закаленному металлическому упору в течение 600 оборотов при нагрузке 150 кг без смазки. В этих условиях износ несульфидированного ролика составил 21 г, а ванна и (износ МАЗ) —0,005 г. Разумеется, что в течение 3 мин., за каковые на машине «МИ» ролик делает 600 оборотов, слой сульфидов предотвращал появление задира на сульфидированном примере, в то время как на несульфидированном примере задиры появились на протяжении первых оборотов, а режим трения его был очень похож на трение об абразивный круг. Так, результаты этого опыта свидетельствуют только об улучшении, противозадирных особенностей, прекрасно сохраняющихся в течение 3 мин. сухого трения.
Одновременно с этим при проведении более долгих опробований сульфидированных образцов на автомобилях трения и особенно при натурных опробованиях серонасыщенных подробностей разных автомобилей увеличение .износостойкости довольно часто было более скромным.
институтами и Нашими заводами созданы разные способы сульфидирования: в жёстких смесях, в расплавах солей и в газовых средах. Для каждого из этих способов предложено много составов рабочих сред, включающих самые разные компоненты. Количество разных составов для жидкостного сульфидирования лишь согласно данным, размещённым в отечественной печати и за границей, превышает сто.
Опробования продемонстрировали, что для долгого увеличения износостойкости в следствии сульфидирования нужным есть наличие под слоем сульфидов, играющих роль жёсткой смазки, слоя металла с повышенным содержанием углерода и азота. Слой серосодержащих соединений на поверхности подробностей активизирует приработку трущейся пары, усиливает адсорбцию масла и предотвращает задиры и схватывание, в то время как нижележащий жёсткий слой карбонитридных нитридов и фаз снабжает долгое сохранение высокой износостойкости прекрасно приработавшихся поверхностей.
Вследствие этого предложен вания и-процесс. Поверхностные слои металла, обработанного в ванне для сульфоцианирования, насыщают азотом, серой и углеродом. Повышенное содержание серы в слое достаточно легко устанавливается методом снятия отпечатков по Бауману, и способом послойного химического анализа.
направляться подчернуть, что серосодержащие слои на шлифе простыми травителями выявляются не хорошо. Но, в случае если подвергнуть сульфоцианированные образцы нагреву при 280—300 °С в течение часа, то благодаря выделению нитридов из жёсткого раствора структура всего слоя светло видна по окончании травления простым 4%-ным раствором азотной кислоты.
Под белым серосодержащим слоем, толщина которого достигает 20—30 мк, расположен чёрный слой карбонитридных фаз толщиной 40—60 мк, и вдобавок ниже— достаточно широкая диффузионная территория металла с повышенным содержанием азота, выделившегося при нагреве при 280 °С в виде игл нитридов. Толщина территории перлита и азотного феррита достигает 0,4—0,6 мм.
Характерно, что при обработке низкоуглеродистой стали в ванне для сульфоцианирования белой территории в микроструктуре не наблюдалось. Конечно, что отпечаток по Бауману не продемонстрировал повышенного содержания серы в поверхностном слое обработанных так образцов.
Сульфоцианирование может производиться в жёстких солях, в газовых средах и в расплавах солей.
Это подтверждает тот факт, что в любых ситуациях, в то время, когда сульфоцианирование вышло из стадии опытов и было вправду внедрено в производство, оно было внедрено только в виде обработки в расплавленных солях.
Обрабатываемые подробности оптимальнеезагружать в ванну на проволочных либо другого типа подвесках, но возможно кроме этого пользоваться железной сеткой, в которую помещают эти подробности. Последний метод эргономичен, в то время, когда приходится обрабатывать много небольших подробностей.
Приготовление ванны создают в такой последовательности. Сначала загружают в нагретый до 550° С тигель прекрасно перемешанную смесь желтой кровяной соли и едкого натра. По окончании расплавления смеси в ванну загружают небольшими порциями серосодержащие соли, перемешивая расплав.
направляться подчернуть, что серосодержащие соли перед их загрузкой в ванну должны быть обезвожены. Загрузка кристаллогидратов Na2S03-7H20 либо Na2S203-5H20 особенно большими порциями ведет к испарению и мгновенному выделению кристаллизационной воды и выбросу жидких солей из ванны.
Температура расплава солей в ванне обязана поддерживаться в пределах 560—580 °С. Подробности выдерживаются в ванне при данной температуре 2—3 часа, после этого их выгружают, подстуживают на воздухе до 100— 150 °С и промывают тёплой водой от налипших солей. Отмытые подробности направляться загрузить в горячее масло (120—130 °С) на 20 мин. для улучшения антикоррозийных особенностей металла.
Промасленные подробности протирают и подвергают обдуву сжатым воздухом.
Сульфидированию и сульфоцианированию, в большинстве случаев, подвергают углеродистые и низколегированные стали. Для аустенитных сталей создан способ сульфоселенирования. Поверхность наряду с этим насыщается в один момент селеном и серой, в следствии чего существенно понижается заедание в резьбовых соединениях кроме того при сверхкритическом давлении (3000 атм) и температуре 650 °С.
Процесс насыщения поверхности серой происходит медлительно. Его возможно ускорить электронно-химическим методом. С целью этого электрод электроимпульсной установки изготовляют из сернистого железа и контактируют его с поверхностью обрабатываемой подробности, которая перемещается над электродом, наряду с этим сера попадает на глубину 0,1 мм в десятки раз стремительнее, чем в ванне, насыщенной сернистыми препаратами.