Значение коррозийных явлений при обработке металлов
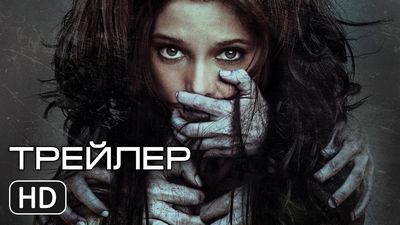
Разрушительная сила и скорость коррозийных процессов, вызванных химическим либо электрохимическим действием, бывают так велики, что появляется вопрос: запрещено ли разумно применять это явление при обработке металлов?
Разглядим коррозию металлов как раз с этих позиций.
Все технические сплавы неоднородны. На поверхности их одни участки играют роль анода, а другие (к примеру, разного рода структурные составляющие, включения) — катода. В следствии на поверхности сплавов образуется много микрогальванических пар, и чем больше неоднородность металла, тем больше скорость его разрушения. Коррозийное разрушение, которое связано с происхождением электрического тока, именуют электрохимической коррозией.
Она появляется не только тогда, в то время, когда металлы соприкасаются с растворами электролитов, но и в воздухе. Дело в том, что в воздухе постоянно содержится то либо иное количество воды в виде пара.
Особенно агрессивна воздух мокрого свежего морского ветра, где наровне с парами воды содержится много небольших частиц различных солей. Большое количество газов содержит воздух громадных городов и промышленных центров.
Разрушение металла в атмосферных условиях направляться разглядывать как следствие работы большого количества микроскопических гальванических элементов.
Еще более активна электрохимическая коррозия в намерено созданных условиях. В случае если влиять на чистый, без примесей цинк разбавленным раствором соляной кислоты, то он практически не будет растворяться в соляной кислоте. Но в присутствии меди цинк деятельно растворяется с выделением водорода.
В случае если соединить медь и цинк, загрузив их в раствор кислоты, то растворение цинка происходит под действием появившегося электрического тока.
Данный вид коррозии есть примером окислительно-восстановительной реакции. В раствор кислоты цинк интенсивно переходит в виде ионов. Избыток их переносится на медь.
Имеющиеся в растворе ионы водорода восстанавливаются на бронзовом электроде и, соединяясь с избыточными электронами, выделяются в виде газа.
В случае если осуществить обработку металла, например, шлифование в растворе электролита, то таким методом будут созданы условия коррозийно-абразивного разрушения, т. е. для того чтобы разрушения, с которым мы сталкиваемся в природе.
Коррозийно-абразивному изнашиванию подвергаются многие подробности газовых и паровых турбин, котлоагрегатов, химического и металлургического оборудования.
Испытания говорят о том, что из всего многообразия физико-химических явлений, происходящих при шлифовании в растворе электролитов, громаднейшее значение имеют коррозийные явления. Темперамент их зависит от состава металла и от особенностей среды, в которой осуществляется шлифование.
При изучении процессов шлифования в разных химически активных средах установлена прямая зависимость между коррозийной активностью и производительностью шлифования.
Другие растворы, как показывают испытания, воздействуют на производительность в меньшей степени.
Характерными являются экспериментальные эти производительности шлифования стали в растворах сернокислой меди и азотнокислой ртути: будет такой же, как и в растворе сернокислой меди.
Но это не подтвердилось: поверхность стали при шлифовании в растворе азотнокислой ртути равномерно амальгамируется и оказывается очень однородной. При шлифовании в азотнокислой ртути производительность в 6 раз меньше, чем в сернокислой меди. Данный же вывод подтверждается при шлифовании чугуна в растворе азотнокислой ртути.
По приведенным данным, при шлифовании чугуна производительность по сравнению со шлифованием стали возрастает в 15 раз. Этому содействует наличие свободного углерода (графита) в структуре чугуна. Чем больше структурная неоднородность, тем больше производительность шлифования в растворе электролита.
Графитовые включения, играя роль катодов, приводят к происхождению большого количества гальванических элементов микроскопических размеров (микрогальванических пар).
Коррозийное разрушение металла в растворах электролитов разъясняется деятельностью гальванических элементов на поверхности металла, что было подтверждено действующей моделью. Два различных металла (медь и железо) взаимно шлифовались суспензией абразивного порошка в электролите. Шлифуемые металлы, поделённые узким слоем суспензии, не имели между собой яркого контакта.
Толщина слоя между металлами определялась размерами зерен абразива. медь и Железо были замкнуты проводом. Так как в ходе шлифования суспензия и поверхность металла, разделяющая металлы, непрерывно обновлялись, то в воздействие включались все новые и новые микропары. Исходя из этого величина тока в замкнутой цепи была постоянной.
Измерялась скорость разрушения электроотрицательного металла цепи. При замыкании цепи производительность шлифования электроотрицательного металла увеличивалась в соответствии с током, развиваемым деятельностью микрогальванических пар. При поверхности 20 и2 шлифовании ток, вызванный действием микрогальванических пар, достигает 0,5 а.
При останове станка ток в цепи из-за поляризационных явлений скоро падает фактически до нуля. Следовательно, активное коррозийное разрушение сплава происходит лишь в ходе шлифования, в то время, когда обрабатываемая поверхность механически деполяризуется. Коррозийное разрушение в любой момент ограничено узким поверхностным слоем металла и не нарушает структуры более глубоких слоев.
Производительность шлифования зависит и от структуры, прочности и толщины пленки — продукта химической реакции. Очень значительным есть прочность сцепления пленки с главным металлом. С ее повышением производительность понижается. По данной причине кое-какие сплавы и металлы, не обращая внимания на высокую химическую активность, шлифуются с пониженной производительностью.
К числу их относятся хром, никель, алюминий, нержавеющие стали, что разъясняется образованием на их поверхности узких целых, прочно сцепляемых пленок.
Алюминий, относящийся к числу электроотрицательных металлов, легко пассивируется с образованием только плотной и прочной пленки окисла. Эта пленка помогает надежной защитой от разрушения. По данной причине шлифование алюминия в воде и в растворах сернокислой меди происходит фактически с однообразной производительностью.
В средах, где исключается образование защитных пленок (к примеру, едкого натра), производительность процесса шлифования возрастает больше чем в 2 раза, но поверхность выясняется более шероховатой.
При коррозийном разрушении на поверхности металла кроме защитного слоя большей либо меньшей прочности расположен узкий слой металла с пара нарушенной структурой. Механическая прочность этого Слоя меньше прочности глубинных слоев металла.
Исходя из этого в ходе шлифования происходит механическое разрушение не только поверхностного защитного слоя, но и лежащего под ним узкого слоя с ослабленной структурой.
Прямая зависимость между коррозийными явлениями и производительностью шлифования особенно четко устанавливается и при шлифовании таких структурно разнородных сплавов, как металлокерамические жёсткие сплавы. Поверхность жёсткого сплава в электрохимическом отношении особенно неоднородна. Зерна карбида вольфрама являются электроположительными, а участки кобальта — электроотрицательными- центрами поверхности.
Деятельность гальванических микропар ведет к коррозийному разрушению кобальтовой связки и к освобождению зерен карбида вольфрама.
Но данный процесс не заходит так глубоко, дабы зерна карбида вольфрама всецело освобождались благодаря коррозии. Частично это может происходить вследствие того что процесс разрушения кобальтовой связки, окружающей карбидное зерно, требует большого времени, частично и вследствие того что карбидные зерна в следствии спекания оказываются до некоей степени связанными между собой.
Поверхность жёсткого сплава, шлифуемая, к примеру, в растворе CuS04, выясняется покрытой целым узким слоем железной меди, играющим роль защитного слоя. Слой данный легко возможно удален методом краткосрочного шлифования поверхности абразивным порошком с водой. При шлифовании жёсткого сплава следуют приятель за втором процессы химического растворения кобальтовой механического удаления и связки бронзового слоя.
В разных электролитах образуются защитные пленки толщиной от долей микрона до нескольких десятков микронов, а в некоторых случаях кроме того много микронов. Пленка меди, образующаяся при шлифовании жёсткого сплава, видна невооруженным глазом. Процесс роста пленок носит затухающий темперамент, т. е. сперва толщина пленки скоро возрастает, после этого скорость ее роста понижается, поскольку металл оказывается отделенным от раствора электролита.
В разбавленном растворе сернокислой меди происходит стремительное осаждение меди на поверхность шлифуемого сплава, а в более концентрированном не сходу, а примерно через 10 сек., причем сперва медь покрывает сплав в некоторых точках (в большинстве случаев на протяжении краев), а после этого скоро распространяется по всей его поверхности.
Коррозийный процесс существенно ослабляет структуру поверхностного слоя сплава, что, со своей стороны, ведет к увеличению производительности шлифования. Темперамент коррозийных разрушений зависит от природы влияющего электролита. самые эффективными ускорителями являются соли электроположительных металлов (серебра, меди и ртути).
В этих электролитах железный кобальт, входящий в состав жёсткого сплава, вытесняет из раствора электроположительный металл, что покрывает всю поверхность жёсткого сплава узким слоем. В один момент с выделением электроположительного металла в раствор переходит эквивалентное количество кобальта.
Химический анализ абразивной суспензии говорит о том, что на протяжении шлифования непрерывно значительно уменьшается содержание соли электроположительного металла и возрастает содержание соли кобальта. Характерно, что производительность шлифования жёстких сплавов в растворе азотнокислой ртути, как и в других растворах солей электроположительных металлов, весьма велика.
Это разъясняется тем, что при шлифовании жёсткого сплава в азотнокислой ртути амальгамируется лишь кобальт, но не карбид вольфрама. По данной причине деятельность микропары на поверхности сплава в следствии амальгамирования не заканчивается, и при шлифовании происходит обычный процесс коррозийного разрушения. Помимо этого, амальгамирование участков кобальта содействует более легкому выкрашиванию зерен карбида вольфрама, что кроме этого повышает производительность процесса.
Производительность шлифования зависит от коррозийной стойкости жёстких сплавов. В азотной кислоте 10%-ной концентрации коррозийная стойкость сплава ВК8 образовывает 15 г/мм2 за день, в серной кислоте той же концентрации — 2,5 г/мм2. Подобная зависимость сохраняется и при шлифовании жёстких сплавов; в растворе азотнокислой ртути съем жёсткого сплава больше, чем в сернокислой меди. Ниже приводятся эти шлифования жёсткого сплава ВК8 микропорошком М20 в растворах электролитов (число оборотов бронзового шли-фовальника 74 об/мин.; давление 240 г/см2):
Влияние наложения тока. Как было продемонстрировано, коррозийное разрушение жёсткого сплава при шлифовании в растворах электролитов происходит по большей части за счет деятельности гальванических микропар на шлифуемой поверхности.
Подобные результаты получаются при шлифовании жёсткого сплава с одновременным анодным растворением. Шлифованная поверхность сплава в этом случае кроме этого имеет нарушенную коррозийным процессом структуру.
В целях сравнения было совершено изучение шлифования жёсткого сплава в растворах электролитов и при одновременном анодном растворении, в то время, когда во внешнюю цепь электрической схемы вводился источник постоянного тока.
Результаты опытов говорят о том, что шлифование жёсткого сплава с одновременным анодным растворением существенно усложняет условия шлифования. Требуются замечательные источники с регуляторами постоянного тока (200—5000 а), электронные устройства для сохранения постоянного межэлектродного зазора, насосы с баками емкостью в много, а время от времени и в тысячи литров, фильтрующие устройства, измерительные устройства и др. Но при обработке химически стойких сплавов, в то время, когда требуются громадные съемы, наложение тока не только нужно, но и экономически целесообразно.
Коррозийные процессы играются значительную роль не только при шлифовании, но и в других процессах обработки металлов. Тут в качестве активного коррозийного агента выступает сера.