Сборка столярных изделий
Сборка изделий — одна из последних стадий технологического процесса производства столярных изделий из древесины. Сборка будет последней стадией, в случае если отделка производится в сборочных единицах и деталях, и предпоследней, в случае если отделка производится в изделии.
Процесс сборки расчленяется на пара операций. В зависимости от сложности изделия число операций будет разным. Простые изделия (к примеру, разного вида полочки) смогут быть собраны за одну операцию из подробностей.
Изделия средней и повышенной сложности (окна, двери, предметы мебели, футляры радиоприемников) собирают за две-три и более операций: подробности собирают сперва в сборочные единицы, а после этого сборочные единицы — в изделие.
Расчленение процесса сборки изделия на последовательность несложных операций существенно упрощает его. Создаются условия для механизации отдельных операций, для введения промежуточной операции обработки сборочных единиц, что повышает уровень качества сборки, а следовательно, и уровень качества самого изделия. Пооперационный порядок сборки столярных изделий обязан предусматриваться при разработке конструкции изделий.
Сборка подробностей в сборочные единицы. Подробности в сборочные единицы собирают значительно чаще посредством столярных соединений и клея. Последовательность сборки подробностей следующая: нанесение клея на сопрягаемые поверхности; предварительная сборка методом вставки шипов в проушины и гнёзда; обжатие сборочной единицы для плотного соединения всех подробностей; выдержка до отверждения клея.
В случае если собираемая сборочная единица должна иметь дополнительно крепление в виде винтов, железных скреп, болтов, то их ставят по окончании обжатия сборочной единицы.
Клей наносят на обе склеиваемые поверхности. В шиповом соединении намазывают клеем проушины и шипы. В большинстве случаев эта операция выполняется вручную методом окунания шипов в ванну с клеем; в проушины гнезда клей возможно впрыскивать форсунками.
Предварительная сборка как операция может отсутствовать, в случае если обжатие сборочных единиц осуществляется в сборочных станках с многосторонним действием.
Качественную и правильную массовую сборку сборочных единиц возможно обеспечить лишь при условии правильного изготовления деталей на станках. Подробности должны быть взаимозаменяемыми. Для этого их изготовляют по совокупности посадок и допусков. В случае если это условие не соблюдено, то сборка потребует дополнительной ручной подгонки подробностей.
Операция подгонки довольно часто оказывается более трудоемкой, чем целый процесс сборки сборочной единицы.
Оборудование для сборочных работ. Сборочные единицы для плотного соединения всех подробностей обжимают на сборочных станках. Сборочные станки складываются из приспособления для фиксации собираемых подробностей и из обжимного механизма, приводимого в воздействие электродвигателем, сжатым воздухом либо вручную.
Громаднейшее распространение в столярно-мебельном производстве взяли сборочные станки с пневматическим обжимным механизмом. В зависимости от конструкции сборочные единицы требуют обжатия в одном либо двух взаимно перпендикулярных направлениях либо в двух направлениях по диагонали (при сборке рамок соединениями на «ус»).
На станках трудятся следующим образом. Подробности кладут на платформу станка в определенном порядке. Наряду с этим сопрягаемые поверхности располагают одну наоборот второй на некоем расстоянии. Включают привод пневмоцилиндра, и рамка обжимается.
На станке с двусторонним обжимом цилиндры включаются поочередно. Сначала включают цилиндр 8 для соединения продольного средника с поперечным, а после этого пневмоцилиндры 6 для обжима всей рамки.
Точность изготовления сборочных единиц. Собранные единицы должны удовлетворять , следующим главным техническим требованиям: размеры должны соответствовать заданным по чертежу; они должны иметь верную геометрическую ф’орму, без перекосов; шиповые соединения должны быть плотными и прочными.
Исполнение этих требований зависит от точности изготовления собираемых подробностей, от положения фиксаторов и направляющих в сборочном станке и от давления прижима.
Точность размеров собранной единицы определяется точностью размеров подробностей. Величина вероятных отклонений для различных измерений будет разной. Внутренние размеры рамки будут иметь меньшие отклонения, чем наружные.
Разъясняется это тем, что отклонения внутренних размеров рамки определяются лишь отклонением в расстоянии между заплечиками шипов на брусках,, тогда как отклонения наружного размера рамки складываются из отклонений отклонений и внутреннего размера ширины продольных брусков рамки.
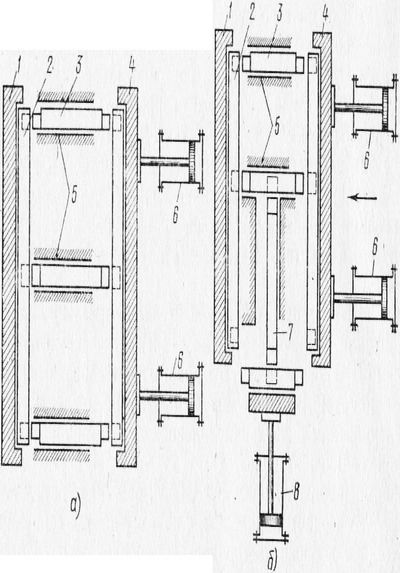
Рис. 1. Схемы сборочных станков: а — с односторонним обжимом, б— с двусторонним обжимом; 1 — неподвижный упор, 2— продольные бруски рамки, 3 — поперечные бруски, 4 — подвижный упор, 5 — направляющие, 6,8 — пневмоцилиндры, 7 — продольный средник
Размеры собранных единиц смогут колебаться кроме этого от неравномерного обжима либо от неравномерной усадки древесины ввиду различной твердости. Отклонения от верной формы (перекосы) смогут быть следствием неточной обработки подробностей либо неравномерного обжима сборочной единицы в различных частях.
В то время, когда к точности внутренних размеров рамки либо коробки предъявляются твёрдые требования, при обжиме рамки нужно в просвет ее вставлять твёрдый железный шаблон, что будет помогать собственного рода калибром. Для контроля формы сборочных единиц пользуются угольниками и шаблонами.
Выдержка сборочных единиц по окончании сборки. Сборочные единицы, собранные на клею, перед последующей обработкой должны пройти выдержку для отверждения клеевых швов. В случае если сборочные единицы направить сразу после сборки на предстоящую обработку, клеевой шов может разрушиться, сборочная единица утратит прочность и форму.
Длительность выдержки зависит от вида клея, температурных условий, конструкции сборочной характера и единицы последующей обработки. Время выдержки без подогрева для сборочных единиц, собранных шиповыми соединениями, должно составлять 24 ч.
Длительность выдержки возможно существенно сократить, в случае если сборочные единицы подогревать, в особенности при склеивании смоляными клеями, для чего помещают их в камеры с подогретым воздухом (65. ..70 °С). Время выдержки сократится до 30. ..45 мин.
Самым эффектным способом подогрева есть подогрев токами высокой частоты.-Время выдержки возможно увеличено до 1.. .2 мин.
Механическая обработка сборочных единиц. При сборке, как было сообщено, тяжело добиться формы и абсолютной точности размеров сборочных единиц. Перед окончательной неспециализированной сборкой сборочных единиц в изделия они проходят механическую обработку, которая содержится в снятии провесов на плоскостях щитов и в углах рамок и коробок, в сверления отверстий под шканты и петли и т. д.
При обработке щитов, рамок и низких коробок делают следующие операции: – сездание базовой поверхности — выверка пластей на фуговальном и одностороннем рейсмусовом станках, на двустороннем рейсмусовом либо шлифовальном станках; – придание заданных формы и размеров. Эта операция производится в два этапа. Сперва обрабатывается одна кромка как базисная на фрезерном станке.
После этого обрабатываются остальные три кромки (стороны) на любом из следующих станков: фрезерном, шипорезном, торцовочном с кареткой, двухпильном концеравнителе. При обработке рамок и щитов на станках используют шаблоны, направляющие линейки, упорные кольца; – дополнительная обработка, нужная для соединения сборочных единиц в изделие: выборка гнезд под петли на фрезерном и особых станках; выборка гнезд под замки на сверлильном либо цепнодолбежном станке; выборка гнёзд и отверстий под шканты на сверлильно-присадочных станках; – дополнительная зачистка поверхности, приклеивание обкладок и т. п.
При обработке высоких коробок (коробок) делают следующие операции: – придание заданных размеров по высоте обработкой одной стороны на фуговальном станке, второй — на рейсмусовом либо фрезерном станке круглыми пилами; – придание заданных размеров по длине и ширине, снятие провесов. Делают эту операцию значительно чаще на фрезерном станке с ножевой головкой. Коробку ставят на шаблон и усиливают внутренним распором.
Незначительные провесы в шиповых соединениях на углах коробок снимают на шлифовальных дисковых либо ленточных станках; – дополнительная обработка — углубление отверстий и гнёзд под петли и шканты, фрезерование закруглений, зачистка поверхностей шлифованием и циклеванием.
Механическая обработка сборочных единиц все чаще производится на полуавтоматических и автоматических линиях, в которых последовательно установлен последовательность станков, соединенных конвейерами, загрузочными устройствами и перекладчиками.
На рис. 2 приведена схема автоматической линии для первичной обработки створок. Створки поступают с линии сборки и подаются в станок для снятия провесов.
На этом станке под углом к направлению подачи установлены нижний и верхний ножевые валы. Створка обрабатывается с двух сторон на протяжении ее перемещения.
По окончании выверки плоскостей створка поступает на продольно-фрезерный станок, где останавливается и фиксируется верхними прижимами. После этого включается механизм подачи двух вертикальных ножевых головок, каковые, двигаясь в особых направляющих, обрабатывают продольные бруски створки. Потом створка поступает на станок, где ее поперечные бруски обрабатываются двумя вертикальными ножевыми головками.
После этого она идет на разгрузочное устройство.
Рис. 2. Схема автоматической линии для первичной обработки створок: 1 — станок для снятия провесов, 2 — станок для обработки продольных брусков створки, 3 — станок для обработки поперечных брусков створки. 4 — разгрузочное устройство, 5 — пульт управления
Неспециализированная сборка сборочных единиц в изделия. Перед сборкой детали и сборочные единицы комплектуют. Различают сборку последовательно-расчлененную и параллельно-расчлененную.
Последовательно-расчлененная сборка представляет собой таковой порядок работы, в то время, когда все изделие собирают из подробностей последовательно, начиная от каркаса. Никаких промежуточных сборочных единиц не собирают.
Параллельно-расчлененная сборка характеризуется тем, что сначала подробности собирают в отдельные сборочные единицы, а после этого уже из них собирают все изделие.
Технологический процесс сборки изделия возможно поделить на следующие последовательно делаемые операции: сборка каркаса либо корпуса изделия; закрепление и постановка неподвижных сборочных единиц либо подробностей, усиливающих главную конструкцию; установка подвижных частей изделия, закрепляемых в направляющих либо на шарнирах; крепление второстепенных подробностей (раскладок, штапиков).
Каркас либо корпус изделия планирует из главных деталей и сборочных единиц, несущих основную нагрузку. К примеру, каркас шкафа для белья и платья собирают из боковых стенок, верхней и нижней коробок.
Неспециализированную сборку создают посредством шиповых соединений (значительно чаще на круглых вставных шипах), клея, болтов, винтов, железных скреп и разного рода стяжек.
Неспециализированная сборка, как и сборка сборочных единиц, требует обжима собираемого фиксации и изделия собираемых частей в определенном положении в момент соединения. Для данной цели используют сборочные станки (ваймы, стапеля) и разные приспособления.
Те сборочные станки либо приспособления, в которых не считая обжатия каркаса изделия производятся и другие сборочные операции, именуются стапелями.
На стапелях при обжатом состоянии каркаса на него крепят неподвижные части, усиливающие жесткость каркаса (бобышки, раскосы, обшивку, задние стены корпусной мебели и другие элементы). Подвижные и декоративные части крепят к каркасу изделия по окончании освобождения его из обжима.
Вероятны случаи, в то время, когда неспециализированная сборка изделий не производится на предприятии. При соблюдении всех технических и технологических требований производства кое-какие изделия, к примеру корпусную мебель разборной конструкции, возможно производить наборами отдельных сборочных деталей и единиц и собирать в магазине либо у потребителя. На предприятии создают контрольную сборку части наборов из каждой партии изделий.
Организация неспециализированной сборки. Различают стапельную и конвейерную сборку изделий. При стапельной сборке изделие собирают от начала до конца на одном рабочем месте в сборочном станке либо приспособлении, при конвейерной сборке — на последовательности рабочих мест, расположенных последовательно одно за вторым.
За каждым рабочим местом закрепляется определенная сборочная операция.
Для движения собираемого изделия при конвейерной сборке используют особые конвейеры, каковые смогут быть распределительными и рабочими. Распределительный конвейер рекомендован лишь для транспортирования собираемых элементов изделия. сборочные станки и Рабочие места находятся последовательно на протяжении конвейера с одной либо с двух сторон.
Рабочий конвейер — это таковой вид поточного производства, при котором сборка изделий производится на самом транспортном устройстве без съема с него изделий.
Сборка на рабочем конвейере есть более идеальным процессом по сравнению со сборкой на распределительном конвейере. Работа на рабочем конвейере протекает по единому ритму, т. е. любая отдельная операция выполняется приблизительно за одно да и то же время. Следовательно, ритм конвейера — это временной отрезок между выходом с конвейера идущих приятель за втором изделий.
Рабочие сборочные конвейеры имеют пульсирующее либо периодическое перемещение. На время исполнения операции конвейер останавливается, по окончании операции он продвигается на длину рабочего места.