Снижение энергопотребления и использование отходящего тепла
Расход энергии в доменном производстве образовывает — 70% от расхода первичных источников энергии на заводе с полным циклом, исходя из этого понижение энергопотребления при выплавке чугуна есть одной из актуальных задач. Главным энергоносителем в доменной плавке есть горючее. Одновременно с этим большие затраты энергии связаны с высокой электровооруженностью производства, и расходом электричества на производство технологического кислорода и доменного дутья.
В ряде государств использование кислорода в доменной плаве сдерживается из-за повышения энергопотребления и большой ценой его получения. На данный момент экономии энергии на выплавку чугуна достигают двумя дорогами; изысканием возможностей большого понижения расхода горючего и более полного применения вторичных энергоносителей.
В соответствии с выполненным в последннее время тепловым балансам по теплотехнической схеме, из общего числа поступающего в печь тепла — 50% расходуется на протекание металлургических процессов, другое тепло теряется в виде внешних утрат (охлаждение, излучение и др.) и перешедшего в чугун углерода, а большинство его уносится с колошниковым газом.
Из приведенных данных видно, что нужный расход тепла на испарение влаги и диссоциацию оксидов, и на нагрев шлака и чугуна образовывает 49,8%. Более одной трети всего тепла (39,1%) уносится с колошниковым газом. Большая часть тепла теряетсяяз-за науглероживания чугуна (8,4%).
направляться отменить, что нужным есть расход тепла на физический нагрев продуктов плавки лишь с позиций обеспечения нужной жидкотекучести. По окончании выпуска из доменной печи данный запас физического тепла нужно разглядывать как потенциальную энергию, которую необходиммо применять для уменьшения энергопотребления при производстве чугуна. Так, лишь добрая половина всего тепла затрачивается безвозвратно (на диссоциацию оксидов, испарение жидкости, науглероживание чугуна и внешние потери) . Другое тепло может утилизироваться и возвращаться в тепловой баланс доменном плавки.
В понижении расхода горючего в последнее десятилетие достигнуты заметные удачи. На последовательности больших печей Японии, Франции, ФРГ, Италии суммарный расход кокса и вдуваемого заменителя составил 448-465 кг/т чугуна. На некоторых доменных печах Японии в отдельные месяцы достигнуто большое понижение расхода горючего.
Так, на доменной печи № 4 завода в Муро-Ране (сентябрь 1980 г.), на печи № 3 завода в Кимицу (ноябрь 1980 г.), на печи № 3 завода в Фукуяме (ноябрь 1981 г.) расход горючего составил 408, 406 и 396 кг/т i чугуна соответственно. Отмечается, что последнее значение расхода горючего близко к теоретически нижнему пределу для данных условий плавки. Воображают другие показатели и интерес работы печи в это время (табл.2.).
Из приведенных данных видно, что низкий расход достигнут по большей части за счет увеличения температуры дутья (1353 ° С), выплавки чугуна с довольно низким физическим прогревом (1481 ° С) и низким содержанием кремния в чугуне при высокой концентрации серы (соответственно 0,27 и 0,045%), проплавки богатой шихты (выход шлака 274 кг/т чугуна) и, в основном, благодаря высокой степени применения химической и тепловой энергии газового потока (степень применения СО 54,8%, температура колошникового газа 73 °С).
Из теплового баланса направляться, что возможности понижения расхода горючего пребывают в сокращении затрат тепла на диссоциацию оксидов (либо каких-либо вторых соединений), нагрев и испарение влаги продуктов плавки, степени температуры использования и повышение дутья газового потока, уменьшении науглероживания чугуна и внешних теплопотерь. Разглядывая статьи теплового баланса, нужно подчернуть, что они в значительной степени неравноценны.
К примеру, за счет понижения энтальпии чугуна нереально взять какой-либо большой эффект, потому, что физическое тепло чугуна нужно для предстоящего передела металла и дает в том месте заметный эффект по понижению энергозатрат. По-видимому, незначителен эффект и от степени энтальпии науглероживания и понижения шлака чугуна, и уменьшения внешних теплопотерь. Затраты тепла на испарение жидкости на данный момент фактически отсутствуют, поскольку в современной доменной плавке, в большинстве случаев, применяют подготовленное железорудное сырье (окатыши и агломерат ) и кокс сухого тушения.
Большой эффект по понижению расхода горючего возможно взять за счет совершенствования подготовки доменного сырья, увеличения температуры дутья, улучшения применения химической и тепловой энергии выплавки чугуна и газового потока с низким содержанием кремния. Уровень качества шихтовых материалов во многом определяет структуру теплового баланса и проявляется фактически во всех статьях.
К примеру, металлизация железорудного сырьяуменьшает затраты тепла на диссоциацию оксидов, а исключение из гидратов и доменной шихты карбонатов – расход тепла на них разложение. Соответственно понижается и расход горючего.
На данный момент доменная шихта фактически не содержит карбонатов и гидратов, т.е. данный источник экономии горючего фактически исчерпан. Попытки металлизовать агломерат на стандартных агломерационных автомобилях и применять его в шихте доменной печи не дали хороших результатов. Опытныё плавки на ЧерМК продемонстрировали, что полученный эффект в доменной плавке не перекрыл допол-нитльных затрат в агломерационном производстве.
При степени металлизации агломерата 32,1% производительность агломерационной ленты снизилась практически в два раза, расход жёсткого горючего на спекание составил 22-25%,быстро ухудшилась десульфурация шихты. Из-за повышения прихода серы с доменной шихтой вынуждены были повысить негрев чугуна и основность шлака. Поданным работы применение металлизованных окатышей в доменном производстве кроме этого экономически невыгодно, исходя из этого это направление в экономии горючего в доменной плавке не взяло развития.
Увеличение достатка шихты снижает расход тепла на нагрев шлака. При работе на 100% оливинсодержащих окатышей выход шлака уменьшился до 170-190 кг/т чугуна при ровной и стабильной работе печи. Компания ЛКАБ (Швеция) приступила к производству оли-винводержащих окатышей с содержанием до 68% Fe.
Но кроме того при понижении выхода шлака в 2 раза структура теплового балакса изменится не существенно, поскольку затраты тепла на нагрев шлака составляют всего 4%.
Значительные трансформации в тепловом балансе смогут случиться при улучшении таких черт железорудных метериалов, как прочность в горячем состоянии и холодном, восстановимость, показатели вязкопластического состояния в высокотемпературной территории печи. Эти особенности проявятся в основном в сокращении статей неиспользованного в доменной плавке тепла.
Главным источником экономии кокса в этом случае есть более действенное протекание восстановительных и теплообменных процессов в печи, увеличение применения химической и тепловой энергии газового потока. Как следствие, быстро уменьшается энергия, уносимая с колошниковым газом. Улучшение высокотемпературных особенностей шихтовых материалов ведет к меньшему науглероживанию чугуна и сокращению теплопотерь с углеродом, перходящим в чугун.
Увеличение металлургических особенностей железорудного сырья предоставляет возможность вести процесс более интенсивно, с большей подгрузкой материалами периферии, более равномерным их распределением по сечению шахты доменной печи. Наряду с этим наровне с повышением применения газа и понижением его температуры, уменьшаются внешние удельные теплопотери с охлаждающей водой.
Так, тепловой баланс доменной плавки возможно существенно улучшен за счет более идеальной подготовки шихтовых материалов. Второй действенный путь экономии горючего на выплавку чугуна – увеличение нагрева доменного дутья. Благодаря повышению конструкции свойств и совершенствованию воздухонагревателей огнеупоров для их футеровки удалось достигнуть на данный момент уровень нагрева дутья до 1300-1400 °С.
стаж работы воздухонагревателей в СССР, Японии, ФРГ продемонстрировал, что для нагрева дутья до 1300 °С и выше (температура купола 1400-1550 4 С) целесообразно строить аппараты с выносной камерой горения. Но цена сооружения блока таких воздухонагревателей на 30-40% – выше затрат на постройку блока воздухонагревателей с внутренней камерой горения. Уверены в том, что высокотемпературные воздухонагреватели с выносной камерой горения целесообразно строить на доменных печах количеством 2000 м3 и более.
Увеличению температуры дутья содействовало кроме этого оборудование выносных камер горения керамическими горелками. Такие горелки улучшают условия работы огнеупоров, снабжают растянутый факел. В следствии значительно уменьшается разрушение кладки из-за ползучести огнеупоров, и увеличивается равномерность нагрева кладки по периметру и понижается возможность образования трещин. За границей такие горелки стали широко распространены в высокотемпературных воздухонагревателях.
В СССР ими оборудовано около 20 воздухонагревателей, а также блок воздухонагревателей доменной печи количеством 5500 м3 ЧерМК.
На данный момент в высокотемпературных территориях насадки воздухонагревателей по большей части применяют малоразрыхляющийся динас либо высокоглиноземистые огнеупоры. Динас имее минимальную деформацию под действием нагрузок в условиях больших температур и владеет достаточной стойкостью при температуре купола 1550 °С.
Предстоящее увеличение температуры дутья связано с конструктивными трансформациями воздухонагревателей (к примеру, применением насыпных насадок и сжигание газа в подкупольном пространстве), применение новых огнеупоров, и применением более калорийной смеси газов для их обогрева, что не всегда действенно. Характерно, что наряду с этим увеличатся и затраты на постройку воздухонагревателей.
В работе приведена оценка эффективности увеличения температуры доменного дутья и сделан вывод о том, что нагрев дктья до 1400 °С экономически действен во всех районах страны. Повышение нагрева дутья до 1400 до 1700 ° С менее элективно, но экономически оправдано для всех экономических районов страны,не считая Западной Сибири,где цена кокса ниже,чем в остальных районах.
направляться также подчернуть, что экономия кокса от увеличения температуры на каждые 100 ° С в диапазоне от 1000 до 1400 ° С значительно уменьшается практически в 2 раза. Выполненная оценка эффективности нагрева дутья относительна и в каждом конкретном случае может оказаться и вторая величина экономически целесообразной тампературы дутья. Сейчас с целью экономии горючего все больше внимания уделяют улучшению применения газового потока в доменной печи за счет оптимального распределения шихтовых материалов, что произошло благодаря применению засыпных аппаратов и регулирующих устройств с широким диапазоном перераспределения материалов по созданию и сечению колошника технологических моделей для оптимизации процесса на базе сведений, приобретаемых посредством новейшей измерительной аппаратуры. ‘
Одним из направлений понижения расхода горючего за границей есть выплавка чугуна с низким содержанием кремния. Так, во время с мая по июнь 1984 г. среднемесячное содержание кремния в чугуне на доменной печи № 3 завода компании “Ниппон кокан” в Фукуляме (Япония) составило 0,19%, а на доменной печи № 2 завода компании “Кавасаки сэйтэцу” в Мидзусиме – 0,16%. В этом случае улучшается тепловой баланс за счет сокращения расхода нужного тепла на восстановление кремния.
Приведенные в табл.2 информацию о работе доменной печи № 3 завода в Фукуяма (Япония) иллюстрируют возможности экономии горючего, расход которого практически на 100 кг/т чугуна ниже, чем в простой доменной практике. На данной печи реализовано большая часть из рассмотренных выше направлений понижения на выплавку чугуна. Особенного внимания заслуживает достигнутая на печи высокая степень применения газового потока.
Наровне с экономией горючего в связи с недостатком отдельных его видов и постоянным трансформацией цен на горючее совершенствуется его структура. В доменной печи главным энергоносителем, регенератором и источником газа-восстановителя есть кокс. Он кроме этого является опорным каркасом и науглероживателем. В связи с возрастающим недостатком коксующихся углей во всемирной практике цена кокса за последние три десятилетия быстро возросла.
Так, в ФРГ к 1985 г. цена кокса возросла практически в 8 раз если сравнивать с 1950 г. Предпринимают попытки частично заменить дорогостоящий кокс более недорогими видами горючего, каковые вдувают в печь через фурмы.
На данный момент на отдельных доменных печах достигли расхода кокса 330-340 кг/т чугуна. Так, при вдувании порошкообразного угля 135 кг/т на доменной печи № 4 компании “Тиссен” (ФРГ) среднемесячный расход кокса составил 338 кг/т, а на доменной печи № 2 компании “Юзинор” в Дюнкирхене (Франция) – 333 кг/т чугуна при расходе угля 143 кг/т.
Одновременно с этим можно подчернуть, что расход заменителей кокса неимеетвозможности возрастать беспредельно, потому, что при недостаточном его количестве он не сможет делать функции опорного каркаса. Выбор эквивалентного горючего при ответе технических и технологических вопросов есть экономической проблемой и определяется соотношением цен на его заменители и кокс.
Так, поданным, начиная со второго нефтяного кризиса 1979 -1980 гг., экономичность доменного процесса за границей определяется в значительной степени динамикой роста цен на жидкое горючее, кокс и природный газ. В случае если до 1979 г. цена на природный газ и жидкое топливо была ниже кокса, то в последующий период она быстро возросла и существенно превысила цену кокса. Вследствие этого использование жидкого горючего в доменной плавке быстро сократилось, отказались кроме этого от применения высококалорийного газа в доменных воздухонагревателях, что стало причиной увеличению температуры расхода и понижению дутья кокса.
Соотношение цен на горючее в государствах ЕЭС на данный момент сложилось так, что жидкое горючее, ни газ ( природный либо коксовый) с высокой теплотой сгорания при сбалансированном энергопотреблении на металлургическом предприятии смогут соперничать с коксом и на ближайшую возможность экономичным остается лишь использование пылеугольного горючего.
В работе отмечается, что вдувание угля приобретает развитие не только в Европе. В Китае на отдельных доменных печах расход угля достигает 150 кг/т чугуна. В Японии ~ 37% дуйствующих печей оборудованы совокупностями угля. В Западной Европе на 13 доменных печах используют пылевидный уголь, числом ~ 150 кг/т чугуна.
На последовательности фабрик за границей в доменные печи вдувают смеси. На заводе в Торонто компании “Италсидер” (Италия) для вдувания применяют смеси угля с мазутом и дёгтем, и вдувают водно-угольные суспензии. Но, поданным японских экспертов, вдувание угольной пыли экономически более выгодно, чем таких смесей, как уголь – мазут, деготь – уголь, водно-угольная суспензия.
В СССР при сложившемся уровне цен на горючее в качестве заменителей кокса используют природный и коксовый газы, пылеугольное топливо и мазут. Большое распространение взял газ как более эргономичный с позиций эксплуатации и минимальных капитальных затрат на постройку совокупностей подачи его в доменные печи. Потому, что в СССР большая часть доменных печей трудятся с обогащением дутья кислородом, то использование газа действенно.
В работе продемонстрировано, что величина дополнительной экономии кокса от увеличения нагрева дутья при вдувании газа образовывает 60-100% главной, а прирост производительности от дополнительного увеличения температуры дутья либо обогащения его кислородом – 12-20% по отношению к производительности в исходном режиме. Соответствующие показатели для мазута и измельченного газового угля практически в два раза меньше, а для измельченного угля – меньше в 3,5 раза.
Большого результата возможно достигнуть при одновременном увеличении расхода и нагрева дутья газа. В СССР вдувание угля в доменные печи не взяло до тех пор пока широкого рапространения. Это связано в первую очередь с громадными капитальными вложениями по подаче и подготовке угля в печь, конструктивными недоработками отдельных узлов (в частности, по регулированию распределения и расхода угля по фурмам), высокими эксплуатацион: ными издержками, и приемлемым с экономической точки зрения уровнем цен на газ.
Вопрос о применении восстановительных газов в качестве других видов горючего не выходит до сих пор из стадии умело-промышленных изучений. В работе установлено, что наиболее удобным для реализации есть вариант работы с вдуванием в горн печи тёплых восстановительных газов чистого холодного кислорода. Наряду с этим для подачи газа возможно использован существующий тракт тёплого дутья, а для подачи кислорода – существующий тракт газа.
Но и в этом случае кроме получения чистого от С02 и Н20 высстановительного газа и его нагрева, громадные трудности появляются с организацией подачи восстановительного газа и кислорода в доменный очаг, созданием устойчивых, достаточных по размерам (особенно в направлении к оси печи) окислительных территорий. Так, на ближайшую возможность другими видами горючего как заменителей кокса в СССР смогут быть природный либо пылевидный уголь и коксовый газ; за границей – по большей части пылеугольное горючее, а в отдельных государствах, где имеются громадные его ресурсы, – газ (Южная Америка , страны Среднего востока и др.). Наровне со рвением максимально снизить расход горючего и поисками эквивалентных более недорогих его видов, сейчас прина-мают меры по применению энергии ртходящих газов.
Из теплового баланса видно, что большая его часть уносится из печи с колошниковым газом. На данный момент фактически вся энергия колошникового газа утилизируется. Доменные печи, трудящиеся с повышенным давлением газа на колошнике, оборудуют газовыми утилизационными бескомпрессорными турбинами (ГУБТ) для производства электричества. Наряду с этим принимают меры по увеличению эффективности применения большого давления колошникового газа методом его сухой очистки.
Колошниковый газ применяют для обогрева воздухонагревателей, и его тепло снова возвращается в доменную печь через нагрев дутья, а также в других агрегатах в качестве горючего.
Широкое распространение взяло применение тепла отходящих газов вохдухо-нагревателей для подогрева вохдуха горючего и горения газа в разных теплообменниках. Выбор типа теплообменников определяется технологическими параметрами теплоносителя и нагреваемой среды.
При средней температуре продуктов сгорания 250-300 ° С вероятен подогрев одного воздуха горения до 200-240 ° С, а совместный подгрев доменного газа и воздуха горения – до 140 – 150 ° С. Второй вариант имеет преимущество, поскольку снабжает более полную утилизацию тепла и меньшие габариты теплообменников. На данный момент в Японии84% воздухонагревателей оборудовано такими теплообменниками. Работы по утилизации тепла отходящих продуктов сгорания ведут в ФРГ, Франции,, Австрии и других государствах.
Помимо этого, уделяют громадное внимание уменьшению утрат от недожога в керамических горелках воздухонагревателей, поскольку из-за понижения теплоты сгорания свойство доменного газа к зажиганию и горения ухудшилась. Так, Университетом промвшленных изучений в ФРГ выполнено тщательное изучение степени догорания доменного газа в воздухонагревателях.
Установленно, что смешения и характер течения на выходе из горелки воздуха и газа оказывает большое влияние на ход процесса горения и появившаяся потоков распределения и неравномерность температур в камере горения самопроизвольно не устраняется, как в большинстве случаев принималось. Университетом созданы новые конструкции горелок, снабжающих полное оптимальное использование и сгорание топлива энергии горючего газа. Подогрев воздуха горения и доменного газа, наровне с совершенствованием конструкции керамических горелок воздухонагревателей и оптимизацией процесса горения, разрешает обеспечить температуру дутья ~ 1200-1250 °С ,без применения горючего с большой теплотой сгорания.
Все больше внимание уделяют применению физического тепла продуктов плавки. В СССР созданы и применяют на ЧерМК замечательные 600-т миксеровозы для транспортировки жидкого чугуна, теплопотери наряду с этим если сравнивать с транспортировкой в ковшах сократились более чем в 2 раза. В Японии наметился переход от стадии умелых разработок к промышленной утилизации физического тепла жидких доменных шлаков.
Установка воздушной грануляции доменного и конвертерного шлаков с утилизацией их тепла (рис. 1) открыта на заводе компании “Ниппон кокан” в Фукуяме (Япония). Шлак из ковша по желобу поступает в закрытую грануляционную камеру, где он дробится струей воздуха, подаваемого под давлением.
В грануляционной камере тепла шлак утилизируется на выработку нагрев и пара воздуха, идушего во вращающуюся сушилку, где употребляется для осушения прокатной окалины. Наряду с этим утилизируется 80% тепла шлака. Использование энергосберегающих разработок разрешит существенно повысить экономичность доменного процесса.
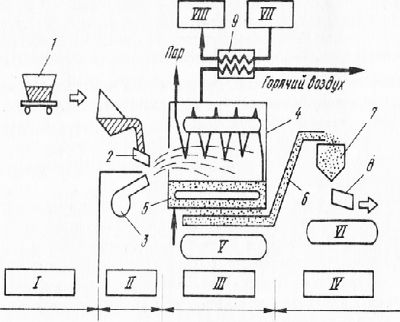
Рис.1. Технологическая схема установки воздушной грануляции шлака с утилизацией тепла: I – предварительная обработка жидкого шлака; II – воздушная грануляция шлака; III отделение утилизации тепла; IV обработка гранулированного шлака; V – транспортирование и разгрузка шлака; VI – отсев; VII и VIII – мокрая и сухая окалина соответственно; 1 – шлаковая чаша; 2 – желоб; 3 – вентилятор; 4 – грануляционная камера; 5 -гранулированный шлак; 6 – конвейер; 7 – бункер для сбора гранулированного шлака; 8 – грохот; 9 – вращающая сушилка для сушки прокатной окалины