Свойства при испытании на твердость
Твердость есть одной из значительных черт механических особенностей материала.
Вместе с тем определение твердости если сравнивать с опробованиями на растяжение есть весьма несложным.
Как уже отмечалось, твердостью именуется свойство материала противостоять пластическим деформациям при внедрении в него постороннего тела, которое само наряду с этим пластически не деформируется.
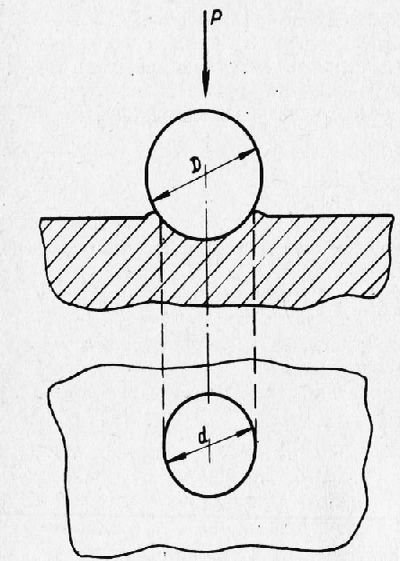
Рис. 1. Схема опробований на твердость по Бринеллю
Большая часть способов определения твердости основано на внедрении в испытуемые материалы тел разной формы — шара, конуса, пирамиды. Главными методами опробований материалов на твердость являются способы Бринелля, Роквелла, Виккерса, и способ измерения микротвердости и другие.
Способ Бринелля есть одним из самый распространенных способов определения твердости. Опробование по этому способу состоит во вдавливании в металл под определенной нагрузкой Р кг (рис. 1) закаленного металлического шарика стандартного размера диаметром D мм, выдержке под нагрузкой, в измерении диаметра d мм сферического отпечатка (лунки) и определении числа твердости НВ кг/мм2 по расчетной формуле либо по таблице (возможно без указания размерности).
Предел применению способа кладет твердость, характеризуемая 450 единицами по Бринеллю. Более высокие твердости требуют применения алмазных либо твердосплавных наконечников.
Способ Роквелла. При измерении твердости по способу Роквелла в качестве наконечника, внедряемого в исследуемый материал, используют:
1) алмазный конус в металлической оправе (шкала С) либо 2) мелкий металлический шарик (шкала В). Твердость наряду с этим характеризуется условно некоторым числом, уменьшающимся с повышением глубины вдавливания наконечника.
Рис. 2. Схема опробований на твердость по Роквеллу посредством алмазного конуса (а) и металлического шарика (б)
В зависимости от используемого наконечника при опробовании по Роквеллу различают:
а) твердость по шкале С, HRC, приобретаемую при опробовании алмазным конусом с углом при вершине 120°. Нагрузка наряду с этим как правило образовывает 150 кг. Показание твердости тем выше, чем меньше величина hc, являющаяся глубиной проникновения конуса в исследуемый материал;
б) твердость по шкале В, HRB, приобретаемую при опробовании металлическим шариком, имеющим диаметр 1,59 мм. Нагрузка наряду с этим образовывает 100 кг. Показание твердости тем выше, чем меньше величина hb, являющаяся глубиной проникновения шарика в материал.
Значение твердости по Роквеллу отсчитывается в условных единицах конкретно по шкале индикатора прибора. Наряду с этим никаких дополнительных расчетов не производится.
Способ Виккерса. При опробованиях на твердость по Виккерсу в качестве внедряемого в материал наконечника употребляется азмазная пирамидка, нагружаемая силой Р кг.
Наконечник образует при вдавливании отпечаток в форме квадрата. Протяженность диагонали отпечатка определяется посредством особого измерительного микроскопа. Твердость по Виккер-су HV возможно подсчитана как функция длины диагонали отпечатка d и величины нагрузки Р. Твердость по Виккерсу HV выражается в кГ/мм2 (возможно без указания размерности).
Рис. 2. Схема опробований на твердость по Виккерсу. Дополнительно даны: а — вид алмазной пирамидки; б — форма отпечатка
Способ микротвердости. Микротвердостью именуется твердость, определяемая в пределах микрообъемов металла.
При опробовании на микротвердость используют такую же алмазную пирамидку, как и при опробовании по Виккерсу. Нагрузки наряду с этим выбирают маленькие, в пределах до 200 г.
Одним из идеальных и современных микротвердомеров есть прибор отечественной конструкции марки ПМТ-3.
Подсчет величины микротвердости производится по формуле, используемой для определения твердости по Виккерсу (в большинстве случаев с указанием размерности).
Для измерений микротвердости разных материалов с Целью получения аналогичных по величине отпечатков, лежащих как и другие ударные пробы, способны распознать в материале такие недостатки, каковые при определении других механических особенностей не обнаруживаются. К таким недостаткам относятся, например, отпускная хрупкость, крупнозернистость и другие.
Усталостная прочность. В связи с развитием машиностроения со второй половины прошлого века показалась необходимость в изготовлении подробностей, каковые в ходе эксплуатации автомобили испытывают повторные нагружения.
Рис. 4. Схема маятникового копра: 1 — пример; 2 — опоры копра; 3 — боек маятника
Поломки, наблюдавшиеся в таких подробностях при работе, были очень необычными. Кроме того у самых пластичных материалов они не имели внешних показателей пластической деформации. Было увидено кроме этого, что они происходят при напряжениях, намного меньших предела прочности а также предела текучести.
Это необъяснимое, на первый взгляд, поведение металла при многократном повторении нагружения было приписано нераскрытому еще свойству так называемой усталости металла и названо усталостным разрушением. Более поздние изучения, и особенно работы последних десятилетий, во многом разъяснили явления усталости металлов.
Усталостные разрушения происходят неспешно в следствии многократного приложения переменных напряжений. Число циклов этих напряжений может составлять от нескольких тысяч до многих миллионов.
Наряду с этим в одном либо нескольких самые слабых кристаллитах появляется местная пластическая деформация, вызывающая упрочнение и наклёп и сопровождающаяся постепенным развитием повреждений.
Под действием переменных напряжений происходит постепенное накопление местных разрыхлений и искажений кристаллической решетки, являющихся очагом зарождения микротрещин. Кое-какие из этих микротрещин приобретают преимущественное развитие, распространяются на соседние зерна, сливаясь, преобразовываются в макротрещины и приводят к постепенному уменьшению трудящегося сечения подробности. Это приводит, наконец, к такому ослаблению изделия, в то время, когда делается достаточным однократного приложения нагрузки, дабы привести к окончательному разрушению.
Вид усталостного излома есть в большинстве случаев очень характерным; по нему отличают поломки, случившиеся благодаря усталости, от вторых видов разрушений. Обычный излом усталости, вид которого представлен на рис. 5, складывается из двух участков.
Первый участок включает наружную территорию излома и характеризует постепенное разрушение, в ходе которого происходит образование усталостной микротрещины и развитие ее в макротрещину. Поверхность этого участка блестящая, поскольку при многократных изгибах примера в ходе опробования она подвергалась действию второй половины его и наряду с этим как бы сглаживалась.
Наблюдения продемонстрировали, что макротрещина начинается весьма медлительно. Время от момента ее появления до окончательного разрушения может быть около 30% всей длительности опробования.
Второй участок включает внутреннюю территорию излома и характеризует стремительное окончательное разрушение по ослабленному усталостной трещиной сечению. Он имеет обычное зернистое строение без следов смятия.
Свойство металла сопротивляться усталости, либо усталостному разрушению именуется выносливостью. Выносливость, либо усталостная прочность характеризуется величиной предела выносливости.
Для определения предела выносливости выполняют особые опробования. Серия однотипных образцов для таких опробовании обязана содержать не меньше 6—8 штук. Из солидного числа используемых на практике способов самый распространенными являются опробования на переменный изгиб с вращением.
Рис. 5. Основной вид усталостного излома: 1 — территория постепенного разрушения; 2 — территория стремительного разрушения
При этих опробованиях любой пример нагружают по консольной либо по какой-либо второй схеме и информируют ему вращение. В каждой точке сечения примера в ходе вращения напряжения за один оборот изменяются по синусоиде от больших растягивающих до больших сжимающих и обратно. Таковой цикл напряжений именуется симметричным: в нем большие растягивающие и большие сжимающие напряжения равны по полной величине.
Рис. 6. Консольная схема нагружения (а), снабжающая симметричный цикл напряжений (Ь) при опробованиях на усталость
Первый пример серии испытывается при напряжении, составляющем приблизительно 3/4 от предела прочности. В следствии опробования устанавливается число циклов, т. е. число оборотов под нагрузкой, которое выдерживает пример до разрушения.
Второй и последующие образцы испытываются при неспешно уменьшаемых напряжениях.
В следствии опробования всех образцов строится кривая выносливости (рис. 7), по которой определяется предел выносливости, либо предел усталости, воображающий собой большое напряжение, выдерживаемое материалом без поломки при повторном нагружении в течение солидного числа циклов, условно принимаемого за неограниченное. Это число довольно часто именуют базой опробования на выносливость.
Рис. 7. Кривая выносливости
Неограниченным числом циклов принято вычислять для стали 10 млн изменений напряжений, а для цветных металлов 100 млн. Опыт говорит, что металлический пример, проработавший 10 млн циклов, трудится и дальше, не разрушаясь. Вид кривой выносливости, имеющей в правой собственной части практически горизонтальный участок, кроме этого подтверждает изложенное.
Все это относится и к примерам из цветных сплавов, но лишь не при 10, а при 100 млн циклов.
Рассмотренным тут способом опробования при симметричном цикле нагружения определяется в лабораторных условиях предел выносливости на гладкополированных стандартных примерах разных диаметров.
Бессчётными изучениями установлено, что предел выносливости стали образовывает приблизительно 0,4—0,6 от предела прочности. Эти соотношения честны лишь при опробований гладкополированных образцов маленького диаметра. Настоящие подробности, как мы знаем, не отвечают этим условиям.
Имеющиеся на них надрезы-концентраторы напряжений отрицательно сказываются на усталостной прочности.
Надрезы на настоящих подробностях смогут иметь вид резьбы, шлицев, шпоночных канавок, отверстий и т. д. Галтели, сопрягающие количества металла с разными поперечными сечениями, кроме этого являются концентраторами напряжений. Надрезами являются всевозможные царапины, риски, забоины, клейма и т. п. повреждения, появляющиеся в ходе производства подробностей и названные технологических надрезов.
Рис. 8. Простая (а) и высокотемпературная (б) кривые выносливости
Вредное влияние надрезов на усталостную прочность возможно уменьшено при помощи поверхностного упрочнения подробностей. В качестве способов поверхностного упрочнения, используемых на данный момент для данной цели, возможно назвать цементацию, азотирование, цианирование, поверхностную индукционную закалку, поверхностный наклеп металлической дробью либо обкатной роликами и другие. Наряду с этим увеличение усталостной прочности достигается за счет увеличения твердости и прочности поверхностного слоя, и благодаря происхождению в нем благоприятных остаточных напряжений сжатия.
С целью определения предела выносливости при больших температурах используют подобную методику опробования с той только отличием, что для поддержания и нагрева образца его в течение всего периода опробования при заданной температуре применяют в большинстве случаев электрическую нагревательную печь.
В следствии опробований строят кривую выносливости, которая имеет принципиальное отличие от кривой, взятой в ходе опробований при простых температурах. Сравнение этих кривых (рис. 8) говорит о том, что при больших температурах горизонтальный участок отсутствует и предела выносливости как большого напряжения, которое может выдержать материал при неограниченном числе циклов, не существует.
Для оценки усталостной прочности при больших температурах пользуются так называемым условным пределом выносливости, воображающим собой напряжение, под действием которого материал разрушается за определенное заблаговременно заданное число циклов. Так, к примеру, условный предел выносливости (рис. 8) является напряжением , которое приводит к разрушению примера за число циклов, равное N.
Железные материалы, подвергшиеся действию коррозии, довольно часто кроме этого не выявляют подлинного предела выносливости. Для них кроме этого приходится определять условный предел выносливости, поскольку нисходящая усталостная кривая с повышением числа циклов не обнаруживает горизонтального участка.