Техника, технический прогресс, стандартизация
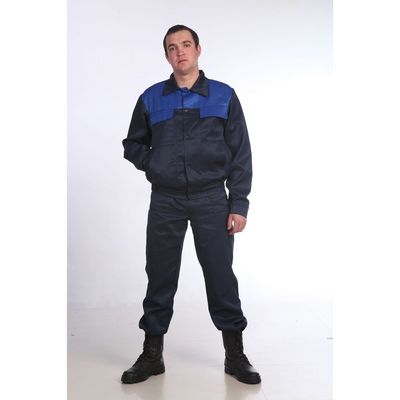
Материальная база техники, ее элементы, функции и структура находятся в закономерной связи между собой. учёт и Раскрытие этих закономерностей имеют очень ответственное значение как при проектировании техники, так и при организации ее производства. Очевидно, каждое техническое устройство имеет собственные своеобразные законы.
Уже в структуре этого устройства находят собственный выражение законы связи и внутренней своеобразной организации данной совокупности. Но особенный интерес при изучении статики техники воображают неспециализированные закономерности ее функционирования и внутренней организации, познание которых методологически вооружает инженеров, трудящихся в области технической подготовки производства.
Любая эра выдвигает свои требования и свои задачи к прогрессу техники. Вместе с тем любая эра формирует для технического прогресса возможности и определённые условия. Исходя из этого задачи совершенствования технической подготовки производства необходимо разглядывать с учетом конкретной исторической обстановки, в которой осуществляется прогресс техники.
В работе приведены следующие три самые существенные тенденции закономерного развития техники, которые связаны с трансформацией ее элементов, функций и структуры:
1) исторически углубляющися процесс дифференциации и их средств элементов и специализации труда;
2) последовательный, проходящий через последовательность этапов, интеграции и процесс усложнения техники;
3) неспециализированное перемещение на протяжении технического прогресса к автоматизации. Действительно, в работе Д. Бернал, отмечает, что в данное время производительность труда, которую может дать автоматизация, существует лишь в принципе, по причине того, что она находится только на первом этапе собственного развития и употребляется лишь на некоторых фабриках самые привилегированных индустрии. Это обусловлено многими факторами: уровнем развития стандартизации, материальными возможностями общества, надежностью автоматических устройств и др.
специализации и процесса Объективные предпосылки дифференциации в развитии техники коренятся в росте публичных потребностей, каковые вызывают к судьбе все новые формы деятельности, а вместе с ними и соответствующие средства труда. Данный процесс, как показывает создатель работы [34], обусловлен кроме этого внутренней логикой развития самой техники.
Суть разделения техники пребывает в том, что по мере ее развития создаются новые средства труда, разные по принципу действия и своей конструкции, с учетом исполнения ими операций и определённых функций, т. е. с учетом их особого назначения. Все это относится не только к сложным средствам труда, но и к их элементам.
Так же закономерным есть процесс их средств элементов и специализации труда, в котором активную роль играется структура, метод связи элементов. Автомобили, будучи сложными образованиями, являются не просто скоплением либо группой разрозненных элементов, а являются целым, владеющим интегративными особенностями и имеющим собственный своеобразное назначение. Но для этого нужна внутренняя организация, связь и определённое взаимодействие между элементами.
Иными словами, нужно наличие структуры, которая «имеется метод связи элементов, совокупность их взаимоотношений между собой».
В случае если элементы автомобилей делают относительно ограниченные по собственному яркому назначению функции, и относительно независимые если сравнивать с назначением и функциями целого, то со структурой дело обстоит в противном случае. Структура, соединяя элементы в суммарное образование, разрешает на данной базе делать функции, отвечающие назначению средства труда в целом.
Все это находит собственный отражение в современной технике, где многие подробности, предназначенные для соединения, установки, передачи перемещения и т. д., мало зависят от назначения всей автомобили. У них однообразное для всех автомобилей яркое назначение, они должны отвечать техническим требованиям, каковые в плане исполняемых ими функций являются неспециализированными для всех автомобилей.
Исходя из этого такие подробности, как шарикоподшипники, болты, гайки, кольца, винты, шестеренки, шкивы, подробности соединений трубопроводов и другие, с успехом смогут быть применены в самых разных автомобилях. То же самое относится и к целым узлам, блокам, механизмам.
Значение стандартизации этих подробностей (узлов, механизмов) тяжело переоценить. Из стандартизованных элементов (элементов в широком понимании), беря их в разном сочетании и дополняя нужным числом узкоспециализированных элементов, возможно создавать последовательность автомобилей разного назначения, а при трансформации целей трудового процесса относительно легко и скоро перестраивать их для исполнения новых операций. На этом принципе выстроено агрегатирование, которое активно используется в станкостроении, а сейчас и в тех отраслях машиностроения, до самого последнего времени автомобили планировали из разоренных подробностей.
Характерен в этом отношении пример конструирования и ооизводства прядильных автомобилей для химических волокон. Последние проектировались с таким расчетом, дабы их собирали из деталей и отдельных узлов. Для перевозки автомобилей на фабрики (по окончании стендовой сборки) требовалась их разборка на детали и отдельные узлы без технологической (в функциональном смысле) связи последних.
Это приводило к дополнительной загрузке сборочных цехов, затратам времени на упаковку и комплектацию подробностей по окончании окраски, повышению расхода леса и пиломатериалов, повреждению подробностей при дополнительной межцеховой перевозке (со сборочных участков в упаковочный цех), громадному количеству упаковочной документации, неточностям в комплектации при упаковке, утратам небольших подробностей при расконсервации и распаковке у клиента (особенно в условиях новостроек). Наряду с этим усложнялся монтаж, возрастали сроки его проведения, увеличивались требования к квалификации монтажников, понижалось уровень качества их надёжность и машин.
Секционный способ проектирования, монтажа и сборки разрешил избежать указанных недочётов. Так, 18-местная машина ПП-1000-ИМ была поделена на девять однообразных двухместных секций, воображающих собой твёрдую металлоконструкцию, на которых устанавливаются рабочие механизмы кроме этого блочной конструкции с личными приводами (галеты, фрикционные цилиндры, бабинодержатели, раскладчики). Конструкции блоков типовые, а кое-какие из них — стандартизованные.
В каждую секцию вмонтированы трубы препарации, валы привода замасливающих шайб, электрооборудование (включая разводку) и другие элементы конструкций. Уникальными являются головная и хвостовая секции, оформленные в виде независимых шкафов, в одном из которых монтируется пульт управления, в другом — бачки препарации. Секции (блоки) автомобили стыкуются между собой несложным соединением нескольких подробностей.
Электропроводка осуществляется лишь протягиванием проводов на протяжении автомобили. Переход на секционную и блочную конструкцию разрешил сэкономить 9,5 т чугуна на каждую машину, снизить трудоемкость изготовления автомобили на 3756 нормо-ч, сократить число коробок на упаковку с 255 до 160, уменьшить длительность монтажа автомобили на комбинате на 20%.
Секции и блоки позволили организовать производство на современном уровне, шире использовать поточную узловую сборку, а на стенде собирать машину не из отдельных подробностей, а из собранных и обкатанных в блоки узлов. Блоки разрешают быстро расширить ремонтоспособность автомобили, что особенно принципиально важно для самый нагруженных и механизмов и ответственных узлов, каковые заменяются блоками,
При переходе на секционную сборку уменьшается кроме этого расход лакокрасочных консервационной смазки и материалов. К примеру, все привалочные платики и т. д., находящиеся в сопряженном виде, не консервируют.
Так, создание разных автомобилей из стандартизованных и унифицированных элементов показывает громадную роль их внутренней организации, структуры.
Наровне с процессом специализации и дифференциации средств труда, технических их элементов и систем в технике отмечается кроме этого и усложнения и процесс интеграции. При усложнении техники происходит повышение числа элементов, входящих в совокупность, и изменение ее внутренней организации, структуры.
С усложнением связана интеграция, суть которой пребывает в создании целостных совокупностей, объединяющих обособленные элементы в единое образование, основанное на их согласованном тесном взаимодействии и функционировании [34]. Попытка управления этим процессом через стандартизацию во многих случаях наталкивается на значительные трудности.
Разъясняется это тем, что на данный момент, как мы показывали, еще мало теоретических и методических разработок в. области национальной и, в особенности, отраслевой и заводской стандартизации, определяющих ее связи с организацией производства и технической подготовкой. Так, практически отсутствуют исследования рациональных способов классификации функциональных блоков автомобилей. В это же время, как показывают изучения [21 ], эта классификация имеет собственную специфику (она значительно отличается от методики классификации общемашиностроительных подробностей) и есть базой для рациональной унификации как самих функциональных блоков, так и их подробностей, и типизации технологических
leccoB их изготовления. Отсутствуют кроме этого теоретические ПР°!едования и методические разработки в области установления ‘”^стандартизации связей конструктивных субординации деталей (структур и элементов состава конструктивных эле-ентов). Все это отрицательно отражается на практической деятельности фирм в области стандартизации.
В простой практике заводской и отраслевой стандартизации разные конструктивные элементы подробностей (диаметры, поля допусков, резьбы, проточки, канавки) рассматриваются и стандартизуются раздельно, без обоюдной связи между собой. Но эти элементы подробностей, кроме того будучи стандартизованными, выступая в стандартах изолированно, при проектировании смогут давать нескончаемое множество структурных образований.
При постоянном усложнении техники такая раздельная стандартизация конструктивных элементов очень затрудняет управление процессами проектирования автомобилей и технологической подготовки производства. В это же время логическая и функциональная связи между этими элементами объективно существуют и смогут быть распознаны и стандартизованы. Стандартизация таких связей элементов повышает уровень взаимозаменяемости подробностей и благоприятно воздействует на повышение универсальности и сокращение номенклатуры технологической инструмента и оснастки, что особенно принципиально важно для мелкосерийного многономенклатурного машиностроительного производства.
В один момент с процессами интеграции и дифференциации в технике действует обусловленный развитием науки и техники процесс широкого применения новых видов и марок материалов, каковые требуют установления оптимальных режимов и методов обработки. К примеру, развитие таковой относительно новой отрасли машиностроения, как производство автомобилей для изготовления синтетических и неестественных волокон, потребовало применения новых, устойчивых к агрессивным средствам материалов, во многом поменявших разработку производства автомобилей. Это потребовало режимов новых обработки и применения методов де~ лей.
Так, в связи с техническим прогрессом усложняются конструкции автомобилей, приборов и оборудования, начинается автоматизация, активно используются новые марки и виды железных и неметаллических материалов, увеличиваются требования к качеству продукции. Развитие этих тенденций без определенных ограничений, с позиций установления взаимосвязанных оптимальных требований и параметров через совокупность стандартизации, может привести к стихийному — неуправляемому процессу в области производства и проектирования, что, как показывает опыт, приводит не только к долгим срокам освоения новой техники, вместе с тем к громадным утратам в народном хозяйстве.
Управление же процессом технической подготовки производства на машиностроительных фабриках в условиях все ускоряющегося процесса современной научно-технической революции, как показывают изучения, может осуществляться только через совокупность стандартизации, в базу которой положены практический опыт и научные знания.
Одна из основных трудностей содержится в построении очень «эластичной» совокупности стандартизации. Эта совокупность обязана снабжать возможность максимально применять при создании техники все новое, передовое, что дает в ее распоряжение наука. К тому же, она обязана содействовать стремительному освоению новой техники в производстве при минимальных затратах и высоком ее качестве.
Иначе говоря в плане проектирования техники нужно предусмотреть избыточность «степеней свободы» для разнообразных, идеальных автомобилей и механизмов (исходя из требований народного хозяйства), а в производстве такую избыточность степеней свободы нужно сократить. При несоблюдении этих условий стандартизация будет мешать техническому прогрессу и потеряет собственную ведущую роль.
Это нужно учитывать и в связи с тем, что при развитии науки и техники неуклонно уменьшается промежуток между новыми научными их использованием и открытиями в производстве. В случае если раньше открытия новых явлений в естествознании приобретали собственный отражение в технике только через десятилетия а также столетия, то сейчас, в большинстве случаев, это происходит в течение нескольких лет.
Так, стандартизация в собственном развитии обязана в некотором роде опережать технический прогресс (опережающая стандартизация) и становиться причиной управления.
В каком же соотношении должно пребывать это опережение по отношению к служебным функциям стандартизации как в области проектирования автомобилей,.так и в области их производства и в состоянии ли стандартизация примирить между собой требования потребителей требования и машин фабрик-изготовителей?
На данный момент еще нет методики, обширно и комплексно хватывающей неприятности развития стандартизации в целом и это приводит к известным трудностям. Но при стандартизации пешать разглядываемые ею неприятности нужно с позиций «системного подхода». Дело в том, что окружающий нас мир состоит не из отдельных изолированных друг от друга предметов н явлений, а из совокупности взаимосвязанных и взаимодействующих объектов, определенного рода целостных образований.
Исходя из этого на данный момент стоит задача — изучить эти совокупности как сами по себе, так и в связи с другими совокупностями.
Стандартизация, как и каждая организованная (а тем более управляющая) совокупность, способна существовать с громаднейшей эффективностью лишь тогда, в то время, когда она предусматривает возможность эластичной (но не единообразной) связи отдельных элементов производства и техники. Так, к примеру, стандартизация обязана исходить из того, что связи между частями технических устройств и систем не смогут быть полностью устойчивыми, а строгая определенность одних частей не должна исключать возможность трансформации каких-то вторых.
Конечно, что трансформации эти при разных случаях будут разными. При данной организации производства, материальных возможностях, людских резервах, развитии науки и техники и т. д. они должны соответствовать понятию «разумный суть».
В соответствии с одной из главных концепций системного подхода — концепцией об трансформациях — в связи с тем, что коль не так долго осталось ждать трансформации в совокупности имеют место неизменно, а появляются и проявляются в первую очередь в более революционных составляющих совокупности — в ее элементах, то не следует стремиться делать данную совокупность окончательно идеальной. Она должна быть достаточно хорошей для исполнения поставленных целей на тот срок, на что эти цели нужны.
Помимо этого, совокупность необходимо строить так, дабы при внесении в нее трансформаций была бы возможность сводить до минимума утраты в сфере обслуживания и в производстве. Главное внимание должно быть обращено на разработку успешного принципа построения совокупности, что допускал бы ее совершенствование и действенно снабжал получение желаемого результата [57].
Изучения говорят о том, что сроки действия стандартов из-за стремительного темпа развития техники и широкого внедрения в производство новых материалов с высокоэффективными показателями фактически сократились, т. е. что стандарты скоро устаревают и нуждаются в пересмотре. Исходя из этого нужен систематический пересмотр стандартов, содействующий тому, дабы стандартизованные изделия постоянно отвечали требованиям потребителей.
Но нередкий пересмотр стандартов имеет и собственные недочёты: это связано с нарушением снабжения производства сырьем, моральным старением технологической оснастки и т. п. Замена одного стандарта вторым может привести к исчезновению какого-либо изделия на рынке из-за прекращения его отсутствия и производства не-’ обходимых условий для организации производства изделий, отвечающих требованиям новых стандартов. направляться учитывать кроме этого, что изделия, сооружения и механизмы становятся все более сложными.
Они складываются из громадного количества элементов, замена которых требует сохранения уже существующих размеров и основных параметров как этих элементов, так и узлов, в каковые они входят. Эти и другие технические, а в значительной мере и экономические факторы современного производства требуют создания таковой совокупности стандартизации, которая максимально удлиняла бы срок действия стандартов, не замедляя наряду с этим технического прогресса.
Чтобы стандарты определяли развитие изделий на более долгий период, совокупность стандартизации должна быть достаточно «эластичной», т. е. каждые накопленные трансформации в элементах (системах), подпадающих под управление данного стандарта, не должны привести к трансформации всей совокупности.
распределения энергии и Электроэнергетическая система передачи может служить примером, в то время, когда частоты параметров сети и стандартизация напряжения на шинах потребителя, выполненная на ранних стадиях развития данной совокупности, не настойчиво попросила значительных трансформаций в совокупности, не обращая внимания на то, что потребление энергии за прошедший 60-летний период удваивалось практически каждые 10 лет [57]. Совершенно верно кроме этого стандарты на обычные допуски и линейные размеры, стандарты на классы точности и основные размеры резьбы и другие явились базой для развития взаимозаменяемости в машиностроении.
В работе приводятся результаты исследований, свидетельствующие о том, что-в СССР за 1950—1966 гг. отношение в первый раз принятых стандартов к неспециализированному числу каждый год утверждаемых (по нарастающему итогу) колебалось в пределах 52,9—37,5% при среднем значении 41,1% (изучение проводилось по стандартам раздела «Д» классификатора национальных стандартов). Это указывает, что за 17 лет в СССР в среднем 58,9% каждый год „утверждаемых стандартов оказалось в следствии пересмотра ранее действовавших.
Создатель работы отмечает, что рост удельного веса производимых перерасмотрение стандартов в общем числе снова утверждаемых стандартов результат ускорения научного прогресса, приводящего к понижению стабильности стандартов в целом. Вместе с тем создатель правомерно ставит вопрос о необходимости обнаружить пути увеличения стабильности стандартов при
пяющихся темпах научного прогресса. Одним из УсК°Р пре0доления указанного несоответствия он справедливо “уТтает построение и дифференцированное изучение стандарта ° ндартов так, дабы любой из них содержал эле-СТнты однообразной стабильности. В данной же работе приводится имер изучений стабильности элементов стандартов, проченных К. Колоц. Разглядев более чем 1000 национальных
ндартов ГДР с позиций их стабильности по отношению ^научно-техническому прогрессу, К. Колоц пришла к выводу существовании четырех главных групп элементов стандартов. ° Эти изучения продемонстрировали, что не все элементы стандартов одинаково стабильны. Так, для элементов группы а стабильность превышает среднестатистическую продолжительность действия стан-партов в два’ раза, для элементов группы Ь она колеблется от восьми до 16 лет, для элементов группы с — от четырех до восьми лет и для элементов группы d — от одного до четырех лет. При полного стандарта (к примеру, стандарта полной характеристики), в состав которого входят элементы всех четырех групп, при первом трансформации элементов группы а элементы группы b изменяются от одного до двух раз, элементы группы с — от двух до четырех раз и элементы группы d — больше, чем четыре раза.
Не обращая внимания на то что эти исследований нуждаются в будущем уточнении и не смогут быть признаны исчерпывающими, в общем виде они дают верное представление о структуре элементов стандарта (с позиций их стабильности). Помимо этого, они подтверждают необходимость распространения правил системного подхода на заводскую, отраслевую и национальную стандартизацию и, например, распространения на них концепции системного подхода об трансформациях.
Так, к примеру, нормалями машиностроения МН14—61 — МН19—61 были установлены конструкции, главные и технические требования и вспомогательные размеры на прижимные крышки подшипников узлов. Последовательность машиностроительных фирм страны начал изготовлять прижимные крышки по указанным нормалям, оснастив их производство железными моделями, кондукторами, режущим и измерительным инструментом.
В 1967 г. в соответствии с замыслом национальной стандартизации нормали машиностроения МН14—61 — МН19—61 были заменены национальными стандартами ГОСТ 13219.1—67—ГОСТ 13219.16—67 «Крышки торцовые корпусов подшипников качения». Этими ГОСТами вводятся конструкции крышек, существенно отличающиеся от предусмотренных нормалями машиностроения. Помимо этого, подверглись трансформации присоединительные размеры крышек, чем была нарушена из взаимозаменяемость.
Так как машиностроительные фирмы изготовляют крышки подшипниковых узлов для призводимого ими оборудования собственными силами, то такое изменение конструкции крышек и их присоединительных размеров (не улучшив функциональные особенности подробностей) стало причиной дополнительным затратам в производстве (замена всей модельной и станочной оснастки) и усложнению взаимоотношения фирм со сферой эксплуатации (нарушение взаимозаменяемости). Лучшим ответом при стандартизации прижимных крышек было бы установление последовательностей присоединительных и габаритных основных требований и размеров, снабжающих требуемые функциональные особенности подробностей.
Это дало бы возможность долгое время сохранять госстандарт в качестве базы. В этом случае весьма логичным смотрелся бы строгий контроль за соблюдением и внедрением стандарта, потому, что его внедрение снабжало бы базу для специальных производств в рамках отраслей либо экономических районов. При отсутствии же последних стандарт давал бы возможность фирмам избирательно, т. е. в зависимости от конкретных условий (но в рамках свойств и показателей, определенных госстандартом), самые экономичным методом осуществлять изготовление подробностей.
Либо второй пример. Анализ говорит о том, что за последние 15 лет стандарт на болты с обычной шестигранной головкой (ГОСТ 7798—70) был переутвержден четыре раза (в 1955, 1957, 1962, 1970 гг.). Наряду с этим размерные элементы, снабжающие взаимозаменяемость, оставались фактически без трансформаций, но, как и размеры и основные параметры.
Но обозначение болтов с каждым новым переутверждением стандарта изменялось.
Из сообщённого направляться, что установление в национальных стандартах всех свойств и показателей изделий, способов их опробований, упаковки, хранения и транспортирования (стандарты полной характеристики) ведет к созданию совокупности, действующей по принципу твёрдой детерминации. Такая совокупность неимеетвозможности трудиться действенно, в случае если системы, подпадающие под управление данных стандартов, вынуждены функционировать избирательно, т. е. исходя из конкретных условий, в которых они находятся.
Это и конечно, потому, что при разработке для того чтобы стандарта нереально учесть все факторы, объективно существующие в рамках действующих во многих отраслях машиностроения совокупностей проектирования, эксплуатации и производства, и факторы, каковые смогут появиться в будущем. Недоучет же этих факторов ведет к накапливанию противоречий между производством и стандартизуемым объектом, либо в сфере сбыта, эксплуатации и т. д. Накопившиеся несоответствия смогут достигнуть столь громадных размеров, что потребуют трансформации самой базы — стандарта. В этих условиях стандарт делается не базой развития, а источником противоречий.
Но довольно часто как раз так строится совокупность стандартизации изделий машиностроения в стране. Отрицательное влияние для того чтобы принципа построения совокупности улучшается тем, что по различным обстоятельствам в один момент с введением стандарта, в большинстве случаев, не осуществляются мероприятия по централизации изготовления стандартизуемых изделий и по централизованной поставке их фирмам всех индустрии, переходящим на новый стандарт. Тяжесть перехода на новый стандарт в этих условиях полностью несут машиностроительные фирмы, изготовляющие конкретные виды оборудования и не специальные на изготовлении данного единичного продукта — стандартизованного изделия (подробности).
Так, регламентация национальными стандартами только главных (определяющих) показателей, свойств и параметров сохраняя базу для функциональной взаимозаменяемости в межотраслевом замысле, позволяет при разработке отраслевы (заводских) стандартов наилучшим образом учитывать особен ности производства и проектирования, свойственные данной конкре ной отрасли машиностроения. Она формирует предпосылки для раз вития отраслевой специализации, основанной на прогрессивно технологии и современных способах организации производства Все остальные требования и параметры, исходя из «собственных целей, изготовители смогут уточнять в пределах показателей г особенностей, регламентированных национальными стандартами.
Те самым подтверждается вывод о том, что на данный момент особенное значение получает отраслевая стандартизация и стандарти зация, в рамках производственных объединений, каковые должн выполнить главную работу по разработке и особенно внедрению стандартов. Как раз отрасли в соответствии с задачами народного хозяйства и развития отрасли в целом, вы раженными в национальных замыслах и национальных нор мативно-технических документах, смогут самый действенно проводить стандартизацию, выбирая самые эффективные дороги внедрения национальных стандартов.