Технологические схемы производства древесно-волокнистых плит
Схема производства жёстких и полутвердых плит
Схема производства жёстких и полутвердых древесно-волокнистых плит включает следующие процессы.
Древесное сырье в виде дров либо отходов подается транспортером с биржи сырья в древорубочный цех. При наличии рубильных автомобилей, приспособленных для рубки длинника, возможно обойтись без распиловки, т. е. подавать балансы конкретно в патрон рубильной автомобили. В этом случае значительно уменьшается количество отходов древесины на опилки при поперечной распиловке (0,3%).
В иных случаях длинник распиливают на 2—2,5-метро-вы’е отрезки при помощи поперечных одиночных выпивал либо, при громадной производительности предприятия, на многопильных станках — слешерах. На рубильной машине древесина преобразовывается в щепу, которая содержит, не считая щепы обычного размера, кроме этого крупные щепки и мелочь. Последние подвергают дополнительному измельчению на дезинтеграторах и возвращают затем на повторное сортирование.
Однородность щепы снабжает обычные условия работы размалывающих аппаратов. Однородная щепа равномернее прогревается при пропарке, лучше держит «пробку» в загрузочной камере дефибраторов, усиливает уровень качества древесно-волокнистой массы. Упорядоченная щепа транспортируется в бункеры, причем при проходе через магнитные сепараторы от нее отделяются случайные железные включения. Удаление железных частиц предотвращает поломку размалывающих дисков и самого аппарата.
Из бункера шепа при помощи вибрационного либо дискового питателя равномерно поступает на распределительный (в большинстве случаев скребковый) транспортер, подающий ее к малым бункерам дефибраторов. Обратной ветвью транспортера излишек щепы возвращается в бункер при помощи дополнительных транспортеров (нории и т- п.).
Из малых бункеров при помощи вибрационных механических питателей щепа подается равномерно и непрерывно в загрузочную камеру дефибратора либо быстроходного рафинера, подвергается размолу и, по окончании разбавления водой, поступает в бассейн несортированной массы. Из бассейна масса насосом подается на одноступенчатое сортирование.
Большая масса, не прошедшая через сортирующие сита, подвергается рафинированию и возвращается на дополнительное сортирование, а обычная масса поступает на сгуститель с целью Уменьшения количества бассейнов для ее экономии и хранения энергии на перекачку. Сгущенная масса поступает в бассейн, что снабжает бесперебойную работу отливного отдела завода.
Излишек воды из сгустителей поступает в бассейн оборотной оды, откуда она расходуется для разбавления массы по окончании размола’ и перед сортированием. Эта вода содержит волокно и не должна сбрасываться в сток; она употребляется в качестве «оборотной». Часть воды возможно использована для разбавления массы.
Из бассейна сгущенная масса подается в регулятор концентрации. Для хранения регулированной массы возможно не иметь отдельного бассейна, в случае если используется постоянная проклейка. При периодической проклейке приходится иметь два бассейна регулированной массы, каковые поочередно служат в качестве мешального и машинного бассейнов. В мешальном проводится процесс проклейки плит, по окончании чего он переключается на машину и проклейка начинается во втором бассейне.
При постоянной проклейке масса с отрегулированной концентрацией подается в бак для постоянной проклейки, куда в один момент через дозаторы поступают приготовленные растворы парафиновой эмульсии и глинозема. Проклеенная масса подается насосом в смесительный бачок, где она смешивается с кислой оборотной водой, поступающей из бака кислых оборотных вод, и после этого переливается в напорный коробку отливной автомобили.
Для производства жёстких плит по схеме компании «Дефибратор» используются автомобили с плоской сеткой. Пройдя регистровую часть, сформованная плита частично обезвоживается на сетке и потом поступает на сосуны. На них происходит предстоящее обезвоживание волокнистой плиты, а сосунная вода перекачивается в ловушку.
Эта вода более бедна по содержанию в ней волокна в сравнении с регистровой водой, исходя из этого ее не нужно применять в качестве оборотной. Пройдя ловушку, эта вода идет в сток. Разделение оборотных вод на кислые и нейтральные нужно чтобы не было нарушения режима проклейки. Волокнистая плита, пройдя сосунную часть автомобили, поступает на форпрессы и потом на гауч-прессы.
Отжимаемая с прессов вода идет на ловушку, а волокнистая плита подвергается предварительной продольной поперечной распиловке и обрезке. Получающиеся наряду с этим обрезки поступают в мешалку, а из нее возвращаются в неспециализированный поток через бассейн несортированной массы. Поперечная распиловка мокрого полотна на отдельные плиты нужна ввиду того, что сушильные устройства приспособлены для отдельных плит, а не для постоянного полотна, которое получается на отливной машине.
Распиленные влаж-ньге плиты поступают на дифференциальный транспортер, имеющий пешком половинах разные скорости.
Схема производства пористых плит
Схема технологического процесса производства пористых плит имеет следующие отличия от обрисованной схемы.
Для производства пористых плит используется двуступенчатый размол щепы. Размалывающая аппаратура второй ступени устанавливается или по окончании сортирования главного потока, или до сортирования массы, прошедшей через первую ступень размола. Отливные автомобили для пористых плит по схеме компании «Дефиб-ратор» используются кроме этого с плоской сеткой, а по американской схеме — крулосеточные. Сушка пористых плит, в отличие от жёстких, производится в роликовых сушилках постоянного действия.
Из охладительной камеры роликовой сушилки пористые плиты подаются к форматным обрезным станкам, обрезаются, упаковываются и направляются на склад.
Схема производства ультрапористых плит
При отливе на непрерывно движущейся плоской либо круглой сетке (с целью ускорения процесса обезвоживания древесно-во-локнистого полотна) используется обезвоживание Давлением и вакуумом. Получение в этих условиях древесно-волокнистых плит с объемным весом, намного меньшим 100 кг/м3, фактически нереально из-за уплотнения волокнистой массы.
В это же время использование весьма легких (меньше 100 кг/м3) и толстых плит для тепло- и звукоизоляции имеет множество плюсов если сравнивать с применением для этих целей простых пористых плит, объемный Вес которых находится в пределах 250—300 кг/м3. Теплоизоляционные особенности плит определяются тремя главными показателями: толщиной, коэффициентом их теплопроводности и гигроскопичностью. Влияние толщины плиты на ее теплоизолирующую свойство подчиняется уравнению Фурье, в соответствии с которому теплопроводность обратно пропорциональна толщине стены (в этом случае плиты).
Применяя более легкие ультрапористые плиты, имеющие при объемном весе 70 кг/м3 коэффициент теплопроводности всего лишь 0,035, вероятно взять при однообразных затратах сырья намного больший эффект теплоизоляции. Сообщённое иллюстрируется диаграммой (рис. 1) зависимости коэффициента теплопроводности плит от их объемного веса, взятой для воздушно-сухих плит.
Как было уже указано, при поглощении изоплитами паров воды коэффициент их теплопроводности возрастает, но для передачи тепла принципиально важно поглощение жидкости теплоизоля-тором в процентах не от его веса, а от количества. Следовательно, и в этом случае более легкий материал, содержащий меньшее количество волокна в единице количества, будет поглощать воды по количеству меньше, чем плита равного количества, но более тяжелая. На рис.
2 продемонстрирована зависимость объемного веса изоплит от градуса размола древесной (дефибрерной) массы: Из диаграммы видно, что при свободном стекании вероятно взять из массы с градусом помола 13° по ШР объемный вес плит 80—81 кг/м3. С повышением градуса размола объемный вес скоро растет. В это же время как мы знаем, что для получения хороших механических особенностей древесно-волокнистых плит нужно степень помола увеличивать тем больше, чем более рыхлые плиты изготавливаются.
Пэтому мы вычисляем целесообразным использование для ультрапористых плит повышенного градуса размола если сравнивать с пористыми, а для пористой структуры — флотацию массы.
Выбор флотореагента определяется условиями начальной периода стадии и продолжительности стекания сушки, в то время, когда стека-ние еще может длиться.
В следствии поставленных особых опытов стало известно, что период коалесценции флотированных волокон должен быть не меньше 60 мин.. Для этих условий подходят поверхностноак-тивные вещества типа полуколлоидов (мыло), владеющие не только громадной поверхностной активностью, но и громадной поверхностной прочностью, с периодом разрушения пены до 24 часов и более. Устойчивость пены олеата натрия во многом зависит от активной кислотности среды.
При рН = 7,65 она падает до нуля, а при рН = 11 образовывает около 60 мин. (при концентрации 0,025%). Для древесно-волокнистой массы жирностью 37° по ШР (дефибрерная масса) нами была взята следующая зависимость объемного веса изоплит от рН среды (рис. 3).
Как видно из данной диаграммы, для древесной массы жирностью 37° по ШР, дающей при обезвоживании свободным стеканием изоплиты с объемным весом 185—190 кг/м3 методом флотации с 2,5% от веса волокна олеата натрия, возможно снизить объемный вес до 80 кг/м3, подщелачивая среду до рН = 9,6; для этого требуется добавить к волокнистой суспензии 2% едкого натра от веса волокна. У взятой плиты — крупноячеистая структура, но достаточно ровная и сомкнутая поверхность.
Обрисованным способом возможно взять плиту с объемным весом до 37 кг/м3, в случае если понизить жирность волокнистой массы до 13°. В качестве вспенивателя возможно применить кроме этого сульфатное мыло числом 5—10% от веса волокна.
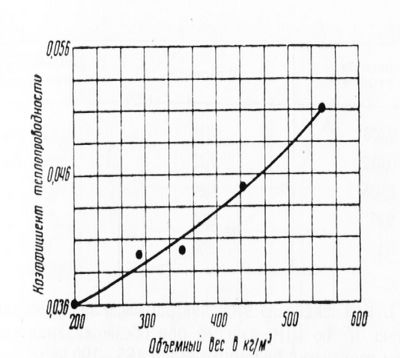
Рис. 1. Зависимость коэффициента теплопро водности от объемного веса плит
Рис. 2. Зависимость объемного веса изоляционных плит от степени размола
Рис. 3. Зависимость объемного веса изоляционных плит от рН среды
Указанные флотореагенты очень сильно увеличивают впитывающую свойство сухих плит, что возможно нужно для некоторых особых типов плит (впитывающая опалубка цементных сооружений), но как правило нежелательно. Исходя из этого воображают интерес флотореагенты, не повышающие впитывающей способности плит.
В качестве для того чтобы флотореагента возможно разглядывать изученную нами смесь 1 : 1 меламиновой и растворимой фенольной смолы С-1 (при концентрации каждой 0,025%), которая владеет хорошей вспенивающей свойством (рис. 4).
Водопоглощение плит, обработанных указанным числом смол, составляло около 40% от водопоглощения исходных плит. При применении для флотации сульфатного мыла водопоглощение плит возрастает в 8—10 раз. В соответствии с изложенным схема технологического процесса производства ультрапористых древесно-волокнистых плит Строится следующим образом.
Щепа, как видно из рис. 5, из древорубочного отделения поступает к загрузочной воронке рафинера первой ступени, куда подается кроме этого тёплая вода. Выходящая из этих рафинеров масса с градусом размола 12—14° по ШР распределяется шнеком на рафинеры второй ступени, где доводится до жирности 25—28° по ШР, разбавляется водой, по окончании чего спускается в метальный бассейн.
Из последнего, по окончании разбавления водой Д° 0,2%-ной концентрации, масса поступает на сортирующие сита и оттуда на сгуститель; отходы возвращаются на распределительный шнек, находящийся перед рафинерами второй ступени сгущенная масса спускается в метальный бассейн, откуда насосом через регулятор концентрации подается во флотационный аппарат. В том же направлении подается отмеренное количество флото-реагента.
По окончании вспенивания флотированная масса перекачивается насосом, как видно из прилагаемой схемы отливочно-сушильного отдела (рис. 6), в мерник, что будет над рольгангом; по последнему движутся отливочные формы со скоротью 1 м/мин. По окончании 30-минутного свободного стенания воды из Р°°сЫ рамка формы снимается тельфером с рольганга и переносится на его обратную ветвь, по которой движутся поддоны хороших форм.
Таким методом форма планирует и снова готова для Впцема массы. Вода, вытекающая из форм, планирует в сборный у для подсеточной воды, а поддон с мокрой массой (сухость q—10%) проходит под горизонтальной ленточной пилой для снятия части массы с поверхности с целью ее выравнивания.
Рис. 4. Вспенивающая свойство смол С-1 и меламиновой при их совмещении
Рис. 5. Схема размольно-плит и очистного отдела завода
Рис. 6. Схема отливочно-сушильного отдела завода ультрапористых плит
Снятая часть массы разбавляется подсеточной водой и постук пает в ментальный бассейн. Плита на поддоне транспортируется в роликовую либо другой конструкции сушилку. Сушка длится 15—16 час. (при толщине плит 80 мм), по окончании чего плиты разгружаются на рольганг.
На нем они снизу смачиваются водой для облегчения отделения от поддонов и проходят через особенный шабер, машинально отъединяющий поддоны от плит. После этого поддон идет на очистку и промывку, а плиты дополнительно подсушиваются до кондиционной влажности в роликовой сушилке.
Потом следуют операции продольной и поперечной обрезки плит на простых в древоплитном производстве обрезных станках и снятия неровного, обычно подгоревшего верхнего слоя плиты при помощи горизонтальной ленточной пилы. Затем, в случае если требуется, производится резка толстых плит при помощи той же пилы на более узкие размеры. Обрезанные плиты поступают на упаковку и в склад готовой продукции, а обрезки распускаются в гидропульпере и идут в мешальный бассейн.