Технологий изготовления литейных форм
Изготовляемые на данный момент отливки характеризуются громадным разнообразием, что приводит к необходимости применения разных литейных материалов и форм.
1. Классификация литейных форм
Литейные формы классифицируются в зависимости от материала, из которого они изготовлены, и состояния при заливке.
Разовые формы помогают для формообразования лишь одной отливки, по окончании чего они разрушаются. Формы изготовляются из песчано-глинистых, песчано-смоляных и других смесей.
Разовые формы смогут быть сырыми (формовка по сырому), сухими (формовка по сухому), подсушиваемыми, химически отверж-дающимися и собираемыми из сухих либо отвержденных стержней.
Сырые формы благодаря их низкой стоимости, быстроте и простоте изготовления, отсутствию процесса сушки имеют громаднейшее использование. Они употребляются для отливок несложной и средней сложности из чугуна, сплавов и стали цветных металлов массой до 1500 кг.
Сухие формы предназначены для того чтобы изготовить средние и с громадным количеством механической обработки. Прекрасно просушенная прочная форма, покрытая противопригарной краской, снабжает получение отличных отливок. Но долгий цикл сушки (6—36 ч и более), большой расход горючего, повышенная трудоемкость выбивки отливок из форм делают их неэкономичными.
Они заменяются поверхностно подсушиваемыми и химически отверждаемыми формами.
Подсушиваемые формы изготовляют из формовочных смесей, в состав которых вводят связующие СП, СБ, КТ. Эти формы используют для важных отливок из стали и чугуна массой от 1000 до 8000 кг. Продолжительность сушки таких форм на порядок меньше, чем простых сухих форм.
Химически отверждаемые формы предназначены для того чтобы из стали, сплавов и чугуна цветных металлов массой 100 т и более. Существуют две разновидности таких форм: одни отверждаются при продувке либо обдувке их углекислым газом, а вторые —самоотверждающиеся — при краткосрочной выдержке в воздухе цеха.
В последнее десятилетие широкое распространение взял процесс химического упрочнения формы, основанный на применении жидких самоотверждающихся формовочных смесей (ЖСС), содержащих в качестве связующего ускоритель и жидкое стекло его твердения (катализатор) — шлак феррохромового производства.
Многократно применяемые (полупостоянные) формы помогают для того чтобы изготовить средние и несложной конфигурации массой до 15 т. Эти формы делают из высокоогнеупорной смеси, состоящей преимущественно из шамота, кварцевого песка и формовочной глины. По окончании соответствующей тепловой обработки стойкость форм достигает 25—40 съемов.
К многократно применяемым формам относятся кроме этого железные формы-кокили для отливок из разных сплавов несложной и средней сложности, небольших и средних по размерам и массе (в серийном и массовом производстве).
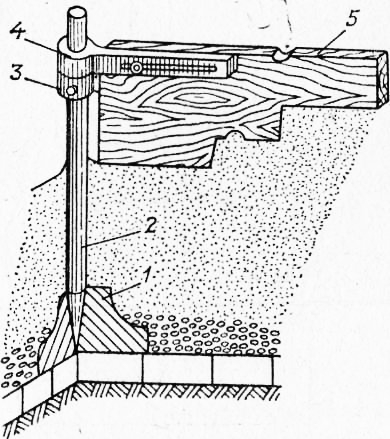
Рис. 1. Приспособление для шаблонной формовки.
2. приспособления и Формовочный инструмент
При изготовлении стержней и форм используют разные инструменты, приспособления и опоки.
Инструмент. самый полный комплект инструмента употребляется при формовке вручную. Технические условия на инструмент регламентированы ГОСТ 11775—74 — 11801—74.
Для засеивания модели облицовочной смесью предназначены прямоугольные сита с железной сеткой с ячейками 2—6 мм. Прямоугольными совковыми лопатами наполняют смесью опоки, а лопатами с заостренным финишем выкапывают ямы при формовке в земле.
Смесь в опоках уплотняют разными трамбовками:
— при работе на верстаках— маленькой трамбовкой (длиной 300 мм). Рукоятка таковой трамбовки выполнена из алюминиевого сплава, а клиновидный и плоский ботинки — из Ст. 40 или из маслобензо-стойкой резины марки А повышенной твердости;
— при уплотнении смеси в крупных опоках и средних самая производительной есть пневматическая трамбовка. Ботинки ее делают из чугуна марки СЧ18-36 либо, что предпочтитель-нее, из маслобензостойкой резины марки А повышенной твердости.
Трамбовка приводится в перемещение сжатым воздухом давлением 5—6 кгс/см2.
Гладилки помогают для заглаживания форм. В недоступных для гладилок местах для этих целей используют ланцеты. Отделку вогнутых углублений и поверхностей создают двухконечными ложечками.
Выглаживание поверхностных цилиндрических поверхностей, углов галтелей и других криволинейных поверхностей реализовывают фасонными гладилками/ Оставшиеся частицы смеси из глубоких полостей удаляют крючками.
Песок с поверхностей и модели форм сметают волосяной щеткой-косматкой, которая предназначена кроме этого для замывки и окраски больших форм. Лучшее уровень качества окраски получается при пользовании пульверизатором.
Вентилирование форм создают посредством душников — игл различных диаметров.
Рис. 10.2. Типы опок. делей в форме осущест
Большие модели расталкивают железным молотком, наряду с этим в модель должны быть врезаны особые металлические пластинки, дабы предохранить ее от порчи. Из полуформ модели вынимают посредством остроконечных и винтовых подъемов.
При формовке по шаблону с вертикальной осью вращения используют приспособление, изображенное на рис. 10.1. Оно складывается из подпятника-башмака, шпинделя, рукава и стопорного кольца, на котором закрепляют шаблон.
Опоки должны владеть большой прочностью, минимальной массой и жёсткостью. Они изготовляются из чугуна марок не ниже СЧ15-32, низкоуглеродистой стали 20Л — ЗОЛ-1, алюминиевых и магниевых сплавов.
Опоки бывают цельнолитыми и сварными. По конфигурации различают прямоугольные, фасонные и круглые опоки.
В зависимости от массы они делятся на ручные, комбинированные и крановые. Ручные опоки без смеси имеют массу до тридцати килограмм, а со смесью — не более 60 кг; комбинированные без смеси — от 31 до 60 кг, а со смесью — более 60 кг; крановые как без смеси, так и со смесью — более чем 60 кг.
Для правильной сборки полуформ используют штыри, изготовляемые из стали марок 40—45 с последующим шлифованием и закалкой. Различают съемные и постоянные штыри. Последние усиливают в ушках нижней опоки, а в больших опоках — в полках продольных стенок.
Съемные штыри имеют громаднейшее использование при машинной формовке.
Для взаимозаменяемости опок центрирующие отверстия в их ушках сверлят по кондуктору. В эти отверстия запрессовывают металлические каленые втулки, что позволяет заменить их при износе и тем самым обеспечить точность спаривания опок.
При выборе размеров опок направляться исходить из мельчайших допустимых толщин формовочной смеси на разных участках формы.
3. Изготовление форм вручную
При формовке вручную литейные формы изготовляют по древесным цельным и разъемным моделям, модельным плитам, шаблонам и скелетным моделям.
4. Формовка в земле
При формовке в земле самая ответственной операцией есть подготовка нижней части формы — постели. Различают два вида постели: мягкую и жёсткую.
Мягкая постель. При изготовлении единичных небольших отливок для каждой из них подготавливают постель в земле. При производстве серии однотипных отливок в полу литейного цеха вырывают яму глубиной на 100—125 мм больше высоты модели и габаритами, превышающими габариты модели на 200—250 мм на сторону.
На дне ямы оставляют четыре кучки смеси; на две из них укладывают древесную рейку, а на другие две — рейку.
На эти рейки кладут линейку и уровнем-ватерпасом контролируют горизонтальность их положения. После этого рейки окучивают смесью, уплотняют ее и снова контролируют горизонтальность их положения. Затем пространство между рейками засыпают отработанной формовочной смесью, сглаживают ее, а излишек сгребают линейкой.
На рейки укладывают бруски высотой 10—12 мм, а на слой отработанной смеси наносят слой просеянной облицовочной смеси.
Сняв бруски, уплотняют ее следующим образом: первый формовщик прижимает линейку к рейке, а второй, приподнимая и опуская второй финиш линейки, уплотняет смесь на участке в 300—400 мм. Затем второй формовщик прижимает линейку к рейке, а первый создаёт уплотнение смеси.
удаление борозд и Окончательное выравнивание поверхности достигается при перемещении линейки на протяжении реек. Выровненную поверхность засеивают узким слоем облицовочной смеси. На взятую постель лицевой стороной укладывают модель и ударами молотка либо трамбовки осаживают ее через промежуточную прокладку.
Жёсткую постель используют при изготовлении форм для крупных отливок и средних. В полу цеха выкапывают яму глубиной на 300—400 мм больше высоты модели. Дно ямы хорошо утрамбовывают, насыпают на него слой просеянной гари либо битого кирпича толщиной 150—200 мм, легко утрамбовывают его и сглаживают небольшой гарью.
Рис. 3. Схема изготовления мягкой постели.
Рис. 4. Схема изготовления жёсткой постели: 1 — слой гари; 2— вентиляционные каналы; 3— облицовочный слой смеси; 4 — вентиляционные трубы.
Поверхность слоя сглаживают линейкой и после этого душником диаметром 9 мм накалывают вентиляционные каналы до гаревой постели.
Приготовленную так постель засеивают слоем (в 40—50 мм) облицовочной смеси. По окончании уплотнения в нем кроме этого накалывают вентиляционные каналы душником диаметром 3—4 мм.
5. Формовка в парных опоках
Громаднейшая точность размеров отливок достигается при формовке в опоках. Широкое распространение взяла формовка в парных опоках. Формовку сложных по конфигурации отливок реализовывают в трех, четырех и более опоках.
Пример изготовления отливки тройника в парных опоках приведен на рис. 5.
Процесс формовки начинают с изготовления нижней полуформы. На подмодельный щиток укладывают нижнюю половину модели и два питателя, а на модель наносят слой облицовочной смеси и обжимают ее руками. В опоку засыпают наполнительную смесь и уплотняют ее.
Счистив излишнюю смесь, душником накалывают вентиляционные каналы.
Взятую полуформу скрепляют с подмодельным щитком и кантуют на 180°, устанавливают на разрыхленную площадку формовочного плаца, легко притирают, по окончании чего открепляют и снимают щиток. После этого проглаживают лад, посыпают его сухим кварцевым песком и сдувают песок с модели. Наложив шлакоуловитель и верхнюю половину модели, устанавливают модели стояка и выпоров.
Рис. 5. Формовка в парных опоках: 1 — нижняя полуформа; 2 — верхняя полуформа; 3 — стержень.
Затем в такой же последовательности изготовляют верхнюю полуформу.
Уплотнение ее должно быть равномерным, без местных слабин и переуплотнений. Степень уплотнения смеси контролируют твердомером. Она зависит от высоты и массы отливки.
Для увеличения прочности верхней половины формы ее усиливают металлическими крючками либо древесными колышками — «солдатиками», предварительно намоченными жидкой глиной.
Вынув модели стояка и выпоров, возможно раскрыть форму. При формовке небольших моделей по окончании уплотнения смеси половины модели удерживаются в полуформе и не требуют дополнительного крепления. При формовке средних и больших тяжелых моделей трение между моделью и формовочной смесью не хватает для удержания ее в верхней полуформе и нужно дополнительное упрочнение ее.
Закрепив модель подъемом к верхней опоке, раскрывают форму, удаляют половины моделей и декорируют верхнюю и нижнюю полуформы, после этого устанавливают стержень и собирают форму.
6. Формовка по модельным плитам
Наряду с этим методе формовки нижнюю и верхнюю полуформы изготовляют раздельно по двум модельным плитам.
Формовку по плитам целесообразно осуществлять в мелкосерийном производстве. На многих ленинградских фирмах — в объединениях имени Карла Маркса, имени Я. М. Свердлова, «Невский завод» имени В. И. Ленина и др. — она удачно используется при мелкосерийном производстве относительно крупногабаритных отливок (длиной более трех метров и массой до 3 т).
Раздельная формовка по плитам снабжает:
— увеличение точности отливок;
— повышение производительности труда на 15—20% за счет сокращения отделочных операций;
— возможность изготовления моделей из отдельных частей с последующей сборкой их на модельной плите;
— увеличение съема отливок с формовочной площади в 1,5 раза за счет установки форм в 2—3 этажа со сдвижкой.
При мелкосерийном производстве используют плиты из особо прочного древесного щита, а при серийном — чугунные строганые. Модельные плиты-могут употребляться многократно.
Набор модельных плит для того чтобы корпуса текстильной автомобили средних размеров (920X420X400 мм) продемонстрирован на рис. 6.
Формовочные работы осуществляются бригадой из двух формовщиков. Для уменьшения утомляемости рабочих модельные плиты устанавливают на низкие козлы.
Рис. 6. Набор модельных плит для формовки корпуса: а — плита для нижней полуформы; б — плита для верхней полуформы; 1 — плита; 2 — центрирующие втулки; 3— модель.
Работа ведется в следующей последовательности:
— плиты и очистка модели и нанесение разделительного состава;
— установка на верха опок и плиты низа;
— нанесение на модели облицовочной смеси, установка крючков (в верхней полуформе) и обжатие смеси;
— заполнение опок наполнительной смесью, уплотнение ее, удаление излишков и накол вентиляционных каналов;
— скрепление модельных плит с опоками и их кантовка; установка нижней полуформы на подготовленный плац, открепление модельной плиты, съем ее и отделка (при необходимости)
— полуформы;
— установка стержней;
— съём и открепление верхней плиты, отделка (при необходимости) полуформы;
— сборка формы.
На собранную полуформу укладывают чугунную плиту (время от времени древесную), на которую устанавливают вторую форму со сдвижкой для установки литниковой чаши.
7. Химически отверждающиеся и большие оболочковые формы
При изготовлении форм по С02-процессу в формовочную смесь в качестве связующего вводят жидкое стекло. Облицовочный слой жидкостекольной смеси наносят на модель слоем в 20—40 мм, а другой количество опоки заполняют наполнительной смесью. Все операции изготовления формы делают в той же последовательности, как и при формовке с применением песчано-глинистых смесей. По окончании отделки формы и удаления модели ее продувают углекислым газом, наряду с этим она скоро отверждается.
После этого форму собирают.
Химически отверждающиеся смеси употребляются и при изготовлении больших оболочковых форм, каковые используют при производстве крупных отливок и средних. Форма для металлической отливки подушки прокатного стана массой 10 т продемонстрирована на рис. 7.
Оболочки изготовляют по шепетильно обработанной разъемной древесной модели, натертой графитом.
Процесс складывается из следующих операций:
— на строганый подмодельный щиток укладывают нижнюю половину модели;
— на него же устанавливают разборный древесный жакет, в стенках которого высверлены отверстия диаметром 9—10 мм. Расстояние между стенками модели и жакета должно составлять приблизительно 120—150 мм;
— в зазор между жакетом и моделью устанавливают сварной каркас для упрочнения оболочки;
— слоями высотой 80—100 мм засыпают жидкостекольную смесь, уплотняют ее, между отдельными слоями смеси закладывают металлические прутки диаметром 8 мм для образования продувочных каналов, каковые не должны доходить до модели на 20—25 мм; – с горизонтальной поверхности счищают излишки смеси, и накалывают продувочные каналы;
— удаляют металлические прутки и через продувочные каналы продувают взятую оболочку углекислым газом;
— отвержденнуго оболочку вместе с жакетом и моделью кантуют на 180°;
— извлекают модель, раскрывают древесный жакет и удаляют его.
В такой же последовательности изготовляют верхнюю оболочку.
Сборку полуформ создают в рамке, складывающейся из двух опок без ребер. Нижнюю опоку укладывают на выровненную площадку и засеивают наполнительной смесью, которую после этого уплотняют. На взятую постель устанавливают зазоры и нижнюю оболочку между опокой и ней засыпают сухой смесью.
В символы оболочки устанавливают оболочковый стержень, накладывают вторую опоку и верхнюю оболочку и засыпают ее сухой смесью слоем в 150 мм.
Рис. 7. Комбинированная форма с оболочковыми вставками: а — нижняя оболочка; б — верхняя оболочка; в — оболочковый стержень; г — собранная форма; д — отливка.
Другую часть опоки заполняют железными шарами диаметром 40 мм. Перед заливкой форму дополнительно нагружают грузами.
Использование оболочковых форм, отвержденных до извлечения из них моделей, позволяет приобретать оболочки с размерами рабочих поверхностей, соответствующих размерам модели. Помимо этого, модели таких форм делают разборными, что разрешает ликвидировать на них формовочные уклоны, требующие дополнительного расхода металла.
8. Формовка по шаблону
Формовка по шаблону осуществляется при производстве единичных средних и больших отливок, имеющих наружную форму тел вращения несложной конфигурации (чаши, маховики, патрубки, трубы с фланцами в т. п.),
Различают следующие виды шаблонной формовки: с вертикальным шпинделем, с горизонтальным шпинделем и по протяжка блонам Громаднейшее распространение взяла формовка вертикальным шпинделем. Разглядим ее на примере формообразования отливки чаши размалывающих бегунов.
Дня шаблонной формовки чаши (рис. 8, а) требуются: станок с вертикальной осью, шаблонная мерка (рис. 8, б), шаблоны для заточки дурака с телом (рис. 8, в) и дурака чаши (рис. 8, г), модели ребер (рис. 8, д) и ступицы с центровым отверстием (рис. 8, е).
Формовка производится в земле (с жёсткой постелью) под верхней опокой.
Рис. 8. Приспособления для шаблонной формовки чаши бегунов.
Процесс складывается из последовательности этапов. На первом затачивают дурак с телом, что будет являться моделью для изготовления верхней полуформы; на втором реализовывают операции по изготовлению верхней полуформы; на третьем затачивают нижнюю полуформу; на четвертом декорируют и собирают форму; на пятом нагружают форму, заливают и выбивают отливки.
9. Формовка по скелетной модели
При единичном производстве больших отливок с целью понижения затрат на изготовление моделей используют скелетные модели, толщина ребер которых принимается равной толщине стенок отливки.
Скелетная модель для того чтобы большой ванны продемонстрирована на рис. 9, а, а схема формовки — на рис. 9, б. Модель заформовывают в опоке либо в земле. Внутреннюю полость заглаживают на уровне брусков и взятую поверхность обкла дывают бумагой.
После этого изготовляют верхнюю полуформу с дураком. По окончании разъема верхнюю полуформу декорируют, а в нижней снимают разделительную бумагу, уплотненную между ребрами смесь легко разрыхляют и шаблоном-сгребалкой снимают слой смеси на толщину ребер. Затем модель извлекают, и изготовление формы заканчивают простым методом.
Рис. 9. Схема формовки по скелетной модели.
10. Формовка в глине по кирпичу
Формовку в глине по кирпичу реализовывают при производстве таких больших отливок, как изложницы, ковши, котлы, трубы громадных диаметров и т. а Формовку ведут по модели, каркасной модели либо по шаблону.
Последовательность стержня и изготовления формы для отливки большого патрубка приведена на рис. 10. В жёсткой постели устанавливают подпятник, рукав и шпиндель, на котором усиливают шаблон.
Правильность установки шпинделя контролируют ватерпасом. На чугунный поддон наносят слой глины и выкладывают первый ряд кладки из красного кирпича. На него наносят слой глины толщиной 15—20 мм и выкладывают второй последовательность с перекрытием швов в первом ряду.
Для увеличения газопроницаемости между последовательностями кирпичей прокладывают небольшую гарь, гранулированный ваграночный шлак, пучки соломы и душником делают вентиляционные каналы в подсохшей глине. Для повышения прочности кладки через каждые 5—6 последовательностей укладывают чугунные плиты, соединяемые с нижним поддоном и между собой стяжками.
Правильность кладки контролируют шаблоном. Между поверхностью кладки и рабочей кромкой шаблона должен быть зазор в 20—25 мм. Внутреннюю поверхность кладки облицовывают шаблоном и глиной затачивают рабочую поверхность. По окончании краткосрочного провяливания на воздухе удаляют шпиндель и шаблон и сушат форму переносным сушилом.
После этого заделывают трещины форму окрашивают и сушат вторично.
Рис. 10. Изготовление кирпичной стержня и формы по шаблону: а — изготовление формы; б — изготовление стержня; в — собранная форма; г—отливка; 1 — подпятник; 2— шпиндель; 3— поддон; 4 — опоры; 5 — кирпичная кладка; 6 —- шаблон для заточки формы; 7 — литниковая совокупность; 8 — облицовочная глина.
Процесс изготовления стержня подобен процессу исполнения формы. Сушат стержень в сушиле.
Кирпичную кладку делают в особых кессонах либо опоках с заполнением промежутков между стенкой опоки и кладкой формовочной смесью. Такие формы смогут употребляться многократно при маленьких промежуточных ремонтах.
Современные методы изготовления больших форм вручную
Постоянный рост производства больших отливок требует совершенствования технологических условий и процессов труда понижения трудоемкости изготовления отливок при ручной формовке разглядим кое-какие рациональные процессы формообразования отливок, созданные литейщиками ленинградских объединений имени Я. М. Свердлова, «Невский завод» имени В И других предприятий и Ленина.
Железные постели. При формовке больших отливок используют жёсткие песчано-глинистые постели, а при изготовлении очень больших отливок постель делают кирпичной кладкой. При извлечении отливки из формы постель частично разрушается, и перед каждой формовкой приходится затрачивать большое количество времени на ее ремонт.
Рис. 11. Схема изготовление жёсткой железной постели: 1 — слой гари; 2 — железная плита; 3 — газоотводные трубы; 4 — кессон; 5 —верхняя полуформа.
Форма с железной постелью, выполненная в кессоне, продемонстрирована на рис. 11. Зазоры между моделью и стенками кессона определяются удобством набивки формы.
Дно кессона покрывают ровным слоем гари, поверх которого кладут чугунную плиту, образующую железную твёрдую постель.
Замена верхней полуформы стержнями
Чтобы не было протечки металла при заливке в большинстве случаев приме няют прокладочную глину, в следствии чего на отливке образуются заливы, на удаление которых затрачивается труд обрубщиков и бесцельно расходуется металл. При замене верхней полуформы перекрывающими стержнями вместо прокладочной глины стали использовать песчаные подушки. Для этого в горизонтальных символах стержней, через каковые выводятся газы, выполнены углубления в 20—25 мм, заполняемые сырым песком с некоторым завышением.
При установке перекрывающих стержней песок уплотняется, наряду с этим создаются надежная изоляция вентиляционных каналов и плотный контакт между стержнями, исключающий возможность образования заливов.
Рис. 12. Разработка изготовления больших форм: а — ветхая разработка; б — новая разработка: 1 — нижние почвенные полуформы; 2— верхняя полуформа; 3 — прокладочная глина; 4 — пригрузочная плита; 5 — стержень, заменяющий верхнюю опочную полуформу; 6 — вентиляционные стояки; 7 — песчаные подушки.
В следствии внедрения новой разработке повысилась размерная точность отливок, сократился расход металла, ликвидированы потребность и парк опок в сушке громоздких полуформ, уменьшилась трудоемкость обрубных работ. Формовка по блок-модели. При изготовлении небольших крупных отливок и серии средних целесообразно объединение в один блок двух однотипных моделей, связанных между собой разделительным стержнем.
Изготовление форм из жидких самоотверждающихся смесей. Чти смеси активно применяются при изготовлении больших стержней Так в литейных цехах объединения имени Я. М. Свердлова все стержни для отливок массой более 3 т делают из ЖСС.
Практика продемонстрировала, что эти смеси смогут удачно использоваться и при изготовлении форм для больших отливок. Схема формовки в ЖСС представлена на рис. 14. Модель устанавливают на кирпичи либо на укрепленные на ней особые упоры или фиксируют в кессоне посредством планок. Между стенками и моделью кессона должен быть зазор в 100—150 мм.
В модели имеются люки для заливки ЖСС. Для улучшения заполняемости формы смесь выдавливают из люков толкателями. По окончании заполнения смесью пространства под моделью ее заливают по периметру кессона в зазоры между его моделью и стенками.
Через 35-40 мин по окончании заливки ЖСС модель возможно извлечь и приступить к отделке формы.
Рабочая поверхность формы имеет большую пористость. Для ее устранения на поверхность наносят особую краску и просушивают- горелкой в течение 2—4 ч при температуре 200— 220 °С.
Разработка изготовления сложной формы для отливки чугунной модели лопасти массой 35 т приведена на рис. 15. Эта модель предназначена для формообразования больших отливок металлических лопастей. Формовка ведется по древесной модели, снабженной упорами, по которым модель устанавливают на постель, в кессоне. На модели размещают съемную раму, оформляющую контуры дурака.
Чтобы не было всплывания рама и модель нагружаются.
Заливку ЖСС реализовывают через люки, имеющиеся в съёмной раме и модели, и в зазоры между стенками съёмной рамы и кессона. После этого создают подпрессовку смеси толкателями. По окончании краткосрочной выдержки извлекают съемную раму, удаляют смесь из люков, подрезают ее около модели, поверхность полуформы покрывают разделительной бумагой и закрепляют ее шпильками, по окончании чего переходят к оформлению верхней полуформы (дурака-стержня).
Рис. 13. Разработка изготовления форм по блок-модели а — почвенная форма; б — стержневая форма.
Рис. 14. Схема изготовления формы из ЖСС.
Рис. 15. Разработка изготовления большой формы с применением
12. Машинная формовка
Механизированное извлечен И модели без предварительной расколотки снабжает получени высококачественных форм , повышает точность отливок и снижает брак. Внедрение координатных и наборных плит-рамок делает табельным использование машинной формовки не только при серий” ном и массовом, но и при мелкосерийном и единичном производстве.
В большинстве случаев литейную форму изготовляют на двух автомобилях: одной — нижнюю полуформу, а на другой — верхнюю. При массовом и серийном производстве элементы и металлические модели литниковой совокупности монтируют на односторонних чугунных плитах, а при мелкосерийном и единичном древесные модели
усиливают на координатных плитах либо в наборных плитах-рамках. Замену модели на координатной плите и в плите-рамке создают на рабочем месте в течение 20—30 мин.
По методу уплотнения смеси в опоке различают прессовые автомобили с нижним и верхним прессованием, встряхивающие автомобили, встряхивающие с подпрессовкой и пескометные.
Уплотнение смеси на автомобилях с нижним прессованием. Схема работы таковой автомобили приведена на рис. 17. На прессовом поршне, помещенном в цилиндре, закреплен стол. На нем расположена модельная плита, перемещающаяся в неподвижной раме. Опоку устанавливают на штыри неподвижной рамы и заполняют смесью, разравнивая ее по всей Поверхности, Затем опоку со смесью помещают под неподвижную траверсу.
При подаче в цилиндр сжатого воздуха прессовый поршень поднимается вверх, модель внедряется в смесь и уплотняет ее. В то время, когда поступление воздуха заканчивается, поршень опускается, и производится извлечение модели.
При нижнем прессовании громаднейшая плотность смеси создается у модели и понижается к верху,опоки, пара возрастая у траверсы, что есть преимуществом этого метода.
Громадный расход мощности на преодоление силы трения смеси о стены опоки ограничивает область применения этих автомобилей. Они смогут употребляться при опоках с размерами в свету до 1100X800 мм и высотой до 150 мм.
Уплотнение смеси на автомобилях с верхним прессованием. Схема работы данной автомобили продемонстрирована на рис. 18.
На прессовом поршне, помещенном в цилиндре, закреплен стол, на котором расположена плита с моделью. По окончании установки опоки с наполнительной рамкой и заполнения их формовочной смесью в цилиндр подают сжатый воздушное пространство под давлением 6 кгс/см2. Под действием воздуха поршень совместно со столом и смонтированной на нем модельной оснасткой поднимается вверх, наряду с этим прессовая колодка, закрепленная на траверсе, внедряется в наполнительную рамку и уплотняет смесь в опоке.
По окончании прекращения поступления в цилиндр сжатого воздуха стол опускается под действием собственной тяжести.
Уплотнение смеси на встряхивающих автомобилях. Данный метод уплотнения смеси, не обращая внимания на кое-какие свойственные ему недостат ки, — самый популярный, поскольку позволяет изготовлять формы для сложных больших отливок в опоках, с размерами в свету 3000 X 2000 мм при высоте до 750 мм.
Рис. 16. Типы модельных плит: а — односторонняя; б — координатная: в —наборная плита-рамка; 1 — главная плита; г — вкладная модельная плита; 3 — модель, 4 — шлакоуловитель; 5 — стояк; 6 — упорные винты.
Рис. 17. Схема работы автомобили с нижним прессованием.
На рис. 19 продемонстрирована схема работы встряхивающей автомобили с подпрессовкой. Она имеет два цилиндра: прессовый и встряхивающий, причем последний является поршнем для первого В цилиндра имеется встряхивающий поршень, на котором укреплен стол.
На столе монтируется модельная плита с моделью.
По штырям на модельную плиту устанавливают опоку с рамкой . По окончании рамки и заполнения опоки смесью в полость встряхивающего цилиндра подают сжатый воздушное пространство, под давлением которого встряхивающий поршень поднимается вверх. Наряду с этим впускное отверстие перекрывается боковой поверхностью поршня, а выхлопное раскрывается, и воздушное пространство выходит в воздух.
Стол с опокой и модельной плитой под действием собственной силы тяжести падает на торец цилиндра, исходя из этого при ударе формовочная смесь в опоке уплотняется. При опускании поршня впускное отверстие снова раскрывается, и цикл повторяется. В большинстве случаев стол поднимается на высоту 30—80 мм и совершает 30—120 ударов в 60 секунд.
Для уплотнения смеси хватает 20—40 ударов.
По окончании окончания процесса встряхивания сжатый воздушное пространство поступает в полость прессового цилиндра, а оснастка и модельная плита приходят в контакт с прессовой колодкой, закрепленной на траверсе. Колодка входит в полость наполнительной рамки и создаёт доугоготнение верхних слоев смеси (рис. 19, г и д).
Уплотнение смеси многоплунжерной головкой. При уплотнении смеси твёрдой прессовой колодкой (рис. 19), особенно в формах больших габаритов, тяжело достигнуть равномерности уплотнения. В таких случаях рекомендуется использовать многоплунжерную головку (рис.
20), наряду с этим формовочная смесь прессуется громадным числом прессующих башмаков, снабженных поршневыми гидравлическими приводами. Любой башмак под действием масла на поршень прессует находящийся под ним участок формы независимо от соседних участков.
Уплотнение смеси пескометами активно используется для уплотнения смеси и механизации наполнения в стержневых ящиках и крупных опоках. Производительность пескометов — от 12 Д° 80 м3/ч уплотненной смеси.
Главным рабочим органом пескомета есть головка (рис. 21). В металлическом кожухе вращается ротор, на котором посредством муфты закреплена лопатка-ковш.
Через окно в кожухе ленточный транспортер непрерывно подает формовочную смесь, которая при стремительном вращении ротора захватывается лопаткой, пара уплотняется и в виде маленьких пакетов выбрасывается в опоку через окно. При громадной скорости истечени смеси из окна и постоянном перемещении головки пескомета л площади опоки создается равномерное уплотнение всех слоев смес независимо от высоты опоки.
Извлечение модели из формы
Рис. 18. Схема работы автомобили с верхним прессованием.
Рис. 19. Схема работы встряхивающей автомобили
Рис. 20. Схема процесса уплотнения смеси в опоке многоплунжерной головкой: 1 — модель; 2 —опока; 3 — наполнительная рамка; 4— прессующая многопл-унжерная головка; 5 — поршни; 6 — прессующие ботинки.
Рис. 21. Схема работы пескометной головки: 1 — рукоятка; 2 — направляющая дуга; 3 — лопатка-ковш; 4 — окно; 5 —кожух; 6 — ротор; 7 — вал электродвигателя; 8 — окно.
Рис. 22. Схемы извлечения моделей при машинной
Автоматизированные формовочные линии. На данный момент в СССР удачно эксплуатируются автоматизированные формовочные линии как отечественного производства — конструкции ВНИИлит-маш, НИИтракторсельхозмаш, Гипросантехпром и др., так и зарубежных компаний.
Процесс формовки, выбивки и сборки на этих линиях всецело автоматизирован, рабочий-оператор наряду с этим лишь, руководит механизмами посредством кнопок.
Вручную выполняются операции заливки и установки стержней, а на некоторых линиях процесс заливки кроме этого автоматизирован.
На рис. 23 продемонстрирована схема автоматизированной линии компании «Гизаг» (ГДР). Она складывается из двух прессовых формообразующих полуавтоматов для изготовления нижней (поз. IV) и верхней (поз. II) литейного конвейера и полуформ (поз.
VII). Собранная на поз X форма поступает на поз. XI — к грузовому конвейеру, где она нагружается, и на поз. XII, где заливается металлом. При предстоящем перемещении залитая форма поступает в охладительную камеру (поз. XIII), снабженную замечательной вентиляционной совокупностью. На поз.
XIV с охлажденной формы снимается груз.
Верхняя опока протяжным устройством стягивается на поз. I и передается на машину для изготовления верхних полуформ (поз. II).
Нижняя полуформа с комом и отливкой смеси продвигается к поз. III, где нижняя опока протягивается, кантуется и передается на машину для изготовления нижних полуформ (поз. IV).
При подходе к толкателю ком смеси с отливкой передается на поз. V— охладительную решетку (накопитель). По окончании краткосрочного охлаждения он поступает на поз.
VI — выбивную решетку, где разрушается и освобождает отливку.
Формообразующая машина имеет два пресса, между которыми расположены дозатор смеси и подъёмный механизм. При поступлении опоки она спаривается с модельной плитой и поджимается к бункеру-дозатору, наряду с этим в опоку выдается определенная порция смеси. После этого опока передается под левый либо правый пресс, имеющий многоплунжерную головку.
По окончании процесса прессования ниясняя полуформа возвращается на среднюю позицию, где по окончании протяжки модели она выталкивается поступающей опокой и передается на поз. VIII. Тут нижняя полуформа кантуется и устанавливается на платформу конвейера. На поз.
IX в эту полуформу устанавливаются стержни.
При подходе к поз. X нижняя полуформа накрывается верхней, и форма поступает на заливку. Верхняя полуформа изготовляется подобно нижней.
Производительность линии в зависимости от типа размеров опок и формовочного автомата образовывает 200—280 форм в час.
Рис. 23. Схема автоматизированной формовочной линии.