Технология изготовления типичных отливок
Литые подробности паровых турбин СВК-150
Литые подробности паровых турбин СВК-150 предназначены для работы в среде пара при температуре 600° и давлении 130 aт.
В набор литых подробностей цилиндра большого давления турбин СВК-150, отливаемых из стали аустенитных марок, входят следующие:
1) внутренний цилиндр большого давления — верхняя добрая половина;
2) внутренний цилиндр большого давления — нижняя добрая половина;
3) верхняя паровая коробка;
4) коробка паровая боковая (правая и левая);
5) коробка сопловая верхняя (правая и левая);
6) коробка сопловая нижняя (правая и левая).
Первый набор перечисленных подробностей был изготовлен на ЭЗТМ по разработке НЗ им. Ленина, использовавшейся при изготовлении сходного по размерам и конфигурации перлитного литья для турбостроения. В изготовленных по данной технологии подробностях было найдено большое количество литейных пороков, недопустимых для данного вида продукции.
Изучения по окончании разрезки умелых отливок продемонстрировали, что влияние наружных холодильников на ускорение процессов кристаллизации, в отличие от перлитного литья, выяснилось намного менее действенным. Прибыли же конфигурации и обычных размеров кроме этого не снабжали нужного питания отливок. Направленного затвердевания в подробностях данных конструкций из стали ЛА1 не получилось и в большинстве отливок выявилось большое количество пороков усадочного происхождения.
Качественными отливками из перечисленной номенклатуры были лишь менее габаритные подробности несложной конфигурации: коробка верхняя паровая и сопловые коробки (верхняя и нижняя), и внутренний цилиндр большого давления (нижняя добрая половина). Громаднейшее количество литейных пороков имело место в отливках внутреннего цилиндра большого давления (верхняя и нижняя половины) и особенно в отливках боковой паровой коробки. Ниже приводится описание литейных технологических процессов самые характерных аустенитных отливок паровой турбины СВК-150.
Коробка паровая верхняя (правая и левая), тёмный вес 1290 кг, вес доходов 1410 кг (рис. 1). Модель разъемная из.двух половин, заливку и формовку создают в горизонтальном положении.
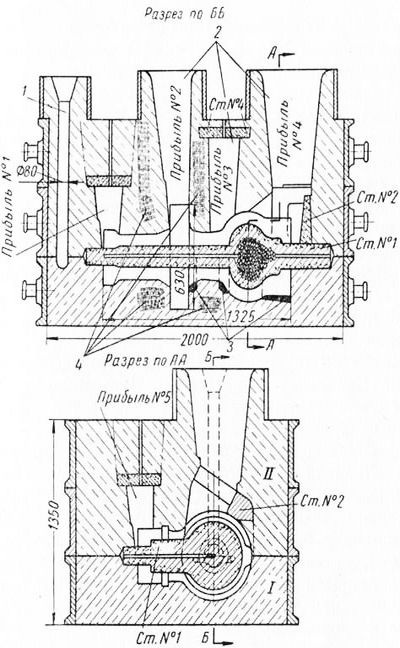
Рис. 1. Технологическая схема отливки коробки паровой верхней (правая и левая): 1 — литниковый стояк; 2 — прибыли; 3 — холодильники; 4 — опи-лочный состав для податливости формы.
Подвод металла осуществляется сбоку в нижнюю часть формы через два питателя со стороны патрубка меньшего диаметра. В нижней части формы в самые массивных участках ее проставлены холодильники, достигающие собственными торцами плоскости разъема формы. С левой стороны среднего фланца холодильник не проставлен, поскольку потоки металла, идущие с данной же стороны, будут омывать его и излишне охлаждаться.
Прибыли для питания отливки устанавливали над всеми самые массивными частями формы II, как Указано на рис. 1. Прибыли № 1, 3 и 5 закрытого типа, а прибыли открытого. Относительно простая конфигурация и небольшая высота отливки разрешили наряду с этим количестве доходов обеспечить удовлетворительное питание металлом всех ее сечений.
Наличие некоего количества окисных плен, найденных все же при изучении данной отливки, разъясняется медленным заполнением формы металлом при пониженной температуре (1490 — 1510°).
Формы заливали из стопорного ковша емкостью 3 т через стояк до заполнения прибыли № 4 на высоту 200 мм над отливкой, после этого ковш переводили на прибыль № 2 и, недоливая ее на 100—150 мм, продолжали разливку через прибыль № 4 до полного заполнения формы металлом. Так как доходы имели весьма громадную высоту, то перемешивания кристаллизующегося металла в теле отливки наряду с этим, по-видимому, не происходило.
Особенное внимание обращали на изготовление стержней, поскольку недопустимо использование жеребеек. Центральный стержень № 1 изготовляли по половинкам и спаривали в сухом состоянии. Каждую половину стержня изготовляли на очень прочном каркасе, складывающемся из пяти металлических прутков диаметром 15 и 35 мм, сваренных между собой.
Рядом с каркасами прокладывали металлические трубки диаметром 20 мм с отверстиями в стенке для вывода газов. Для увеличения податливости стержня каркас обматывали паклей.
По окончании спаривания двух половин стержня каркасы каждой половины стержня сваривали между собой. Швы стержня расчищали, промазывали клеем и шпаклевали стержневой смесью. Все остальные операции проводились простым порядком.
Коробка сопловая верхняя (правая и левая), тёмный вес 570 кг, вес прибыли 570 кг (рис. 2). Модель разъемная из двух половин. заливку и Формовку создавали в горизонтальном положении. Металл подводили сифоном в нижнюю часть формы через два питателя со стороны патрубка.
В нижней части формы в самые массивных участках ее, и у боковых приливов проставляли холодильники 4. Три доходы устанавливали над самые массивными частями отливки, как указано на рис. 2. По данной технологии отливали все сопловые коробки из трехтонного стопорного ковша при температуре металла 1500—1510°.
По окончании окончания заливки прибыли засыпали золой для уменьшения теплоотдачи. Указанные отливки благодаря применению и незначительным размерам массивных доходов, перекрывающих практически всю поверхность отливки, прекрасно питались металлом и во всех сечениях имели плотное строение. Пара малых заворотов и окисных плен на поверхности отдельных отливок наблюдалось благодаря заливки их металлом пониженной температуры.
Указанный технологический процесс возможно рекомендован для широкого применения при изготовлении подобных отливок из любых аустенитных и перлитных марок стали. Требуется только корректировка в каждом отдельном случае температуры металла при заливке.
Предстоящими умелыми работами установлено, что использование наружных холодильников для стали аустенитных марок типа ЛA1 намного менее действенно, чем для перлитных сталей, исходя из этого
данных отливках нужную плотность металла направляться достигать методом соответствующего размещения массивных доходов. 1Л самоё значительное количество литейных пороков было отливках внутреннего цилиндра большого давления (верхняя добрая половина) и паровой боковой коробки. Немного меньше пороков найдено в отливке внутреннего цилиндра большого давления (нижняя добрая половина).
Рис. 2. Технологическая схема отливки коробки сопловой верхней (правая и левая): 1 — литниковый стояк; 2 — прибыли; 3 — опилочный состав для податливости формы; 4 — наружные холодильники.
Коробка паровая боковая (правая и левая), тёмный вес 1700 кг, вес доходов 1500 кг (рис. 27). Модель разъемная, складывается из двух половин для формовки в горизонтальном и заливки в вертикальном положениях, как указано на рис.
27.
Металл подводят сифоном в нижнюю часть формы, в один из фланцев, на котором установлена прибыль № 3. На горловине коробки Установлена прибыль № 1. Обе прибыли закрытого типа и для выхода газа снабжены вентиляционными каналами. На самом массивном боковом фланце отливки размещена прибыль № 2 открытого типа, через которую проходит один из знаков стержня № 1. Прибыль № 2 в первых отливках делали открытой для доливки металла с целью подогрева прибыли, но в будущем, в то время, когда выявилось вредное влияние доливки металла в прибыли, выражавшееся в перемешивании начавшего кристаллизоваться металла в теле отливки с снова доливаемым металлом, прибыль № 2 стали выполнять закрытой, как и прибыли № 1 и 3. По аналогии с отливками верхней паровой и сопловыми коробками в нижней форме боковой паровой коробки проставляли наружные холодильники, доходящие до разъема формы.
Рис. 3. Технологическая схема отливки паровой боковой коробки: 1 — прибыли; 2 — литниковая совокупность; 3 — опилочный состав для податливости формы; 1 — наружные холодильники.
Как уже отмечалось выше, эта отливка относится к числу очень нетехнологичных. Отсутствие достаточного опыта в производстве аустенитного литья усугубляло последствия данной нетехнологичности и приводило к образованию большого количества литейных пороков в виде раковин и рыхлот усадочного происхождения, и окисных плен, которые связаны с низкой температурой металла, при заливке и недостаточной скоростью подъема металла в форме. Произведенная потом корректировка конструкции данной отливки, и увеличение температуры металла при заливке разрешили ликвидировать в последующих отливках литейные пороки и обеспечили получение высококачественных отливок .
Рис. 4. Технологическая схема отливки внутреннего цилиндра большого давления (верхняя добрая половина):
1 — литниковая совокупность 1-го яруса; 2 — литниковая совокупность 2-го яруса; 3 — наружные холодильники; 4 — опилочный состав для податливости формы; 5 — внутренние холодильники; 6 — прибыли.
Внутренний цилиндр большого давления (верхняя добрая половина), тёмный вес 3690 кг, вес доходов 4830 кг (рис. 4). Модель неразъемна» предназначается для заливки и формовки подробности в горизонтальном положении. Форму заливают из стопорного ковша емкостью 10 т при температуре металла 1420—1430°. Металл в форму на первом этапе заливки подводят сифоном к двум нижним патрубкам и оттого же стояка к торцовой части цилиндра примерно посередине его высоты.
Заливка через эту литниковую совокупность длится до появления металла в доходах на высоте 200 мм над телом отливки, по окончании чего заливку заканчивают через второй стояк, подводящий металл при помощи питателей, во все шесть доходов.
Конструкция данной отливки в ее первом варианте кроме этого не отвечала требованиям технологичности и отливка не получалась качественной. По окончании уточнения конструкции и изменения отливки температурного режима заливки отливки цилиндра значительных недостатков не имели.
Арматура для паропроводов
Литые подробности арматуры, предназначенные для паровых турбин очень высоких параметров, долгое время трудятся в среде пара при температуре 580—600° и давлении 130 ат. Исходя из этого металл отливок арматуры обязан владеть хорошей свариваемостью и высокой жаропрочностью, а металл швов и околошовных территорий по механическим особенностям не должен уступать металлу отливок.
В литых подробностях арматуры не должно быть пороков в виде трещин, рыхлости и усадочных раковин, окисных плен и заворотов металла, и вторых пороков, способные привести к преждевременному разрушению подробности в ходе эксплуатации и привести к аварии.
Металл отливок при комнатной температуре должен иметь следующие механические особенности: предел текучести не менее двадцати килограмм/мм2-, предел прочности при растяжении (аь) не менее сорока килограмм/мм2; удлинение (б) не меньше 15% и ударная вязкость (ak) не меньше 3,5 кгм/см2; предел ползучести при 600° (сгп) 8,0 кг!мм2 и предел долгой прочности при данной же температуре 12,0 кг/мм2. Данный металл обязан владеть стабильностью особенностей и по окончании старения при 600—750° длительностью 3000 час.
В набор литых подробностей арматуры паропровода важного назначения входит шесть наименований: 1) средняя часть корпуса; 2) два патрубка; 3) главная часть корпуса редукторно-охладитель-ной установки; 4) коробка; 5) корпус и 6) крышка.
Перечисленные подробности в начальном конструктивном и технологическом выполнении имели большое количество недостатков, обусловливаемых нетехнологичностью конструкции литых подробностей арматуры и технологическими свойствами и неудовлетворительными литейными используемой для отливок аустенитной стали марки ЛАЗ и, например, повышенной склонностью данной стали к образованию трещин и нехорошей свариваемостью.
Вследствие этого перед ЦНИИТМАШем’ была поставлена задача изыскать методы резкого улучшения качества литых повышения и деталей арматуры эксплуатационной стойкости их.
Ответ поставленной задачи осуществлялось в трех направлениях:
1) созданием новой, более технологичной, чем ЛАЗ, литой жаропрочной стали для работы при 600°, не склонной к образованию трещин и владеющей удовлетворительной свариваемостью;
2) улучшением технологичности конструкции литых подробностей арматуры; _
3) освоением и разработкой в промышленных условиях более рациональных литейных технологических процессов применительно к подробностям арматуры с учетом внесенных в их конструкцию трансформаций.
В качестве нового, более технологичного материала отливок арматуры была предложена аустенитно-ферритная сталь марки 1Х20Н12Т-Л.
Сталь данного состава всецело соответствует требованиям технических условий; она не склонна к образованию тёплых межкристаллитных надрывов и трещин и снабжает хорошую свариваемость металла отливок.
В уточненных конструкциях литых подробностей арматуры предусматриваются геометрические уклоны, утолщения и напуски, ликвидирующие тепловые узлы и содействующие направленному затвердеванию жидкого металла в литейной форме.
Использование рациональных литейных технологических процессов в сочетании с более технологичной конструкцией и новой прекрасно свариваемой литой сталью марки 1Х20Н12Т-Л обеспечили достаточно высокий уровень качества отливок арматуры.
Создание технологичных конструкций подробностей арматуры, отливаемых из стали аустенитных и аустенитно-ферритных марок, разрешает использовать более рациональные литейные технологические процессы, в базу которых закладывается принцип направленного затвердевания жидкого металла в литейной форме.
У подробностей, входящих в набор арматуры, за исключением крышки, самые массивными частями являются фланцы, составляющие около 50% от веса отливки. Для улучшения питания отливок их формуют фланцами кверху и доходы устанавливаются на громаднейшие по площади горизонтальные части фланцев. Такое размещение отливок разрешает более рационально применять большие веса металла не только доходов, но и фланцев для значительного улучшения питания как отдельных самые массивных узлов, так и всей отливки в целом.
Сообщённое положение подробностей арматуры при заливке снабжает создание хорошего температурного градиента методом плавного повышения толщин, стенок отливок от низа вверх по направлению к прибылям и фланцам.
Ниже приводится описание отработанных и оправдавших себя рациональных литейных и конструкций технологических процессов изготовления подробностей арматуры применительно к отливке из аусте-нито-ферритной стали 1Х20Н12Т-Л, и аустенитной стали ЛАЗ.