Термическая обработка
Литые хромоникелевые стали аустенитных марок характеризуются в основном большой степенью и крупнокристаллическим строением неоднородности состава в микрообъемах.
В ходе долгой эксплуатации литых изделий, при большой температуре, происходит выпадение карбидов из жёсткого раствора в виде мелкодисперсной фазы, которая после этого коагулирует.
Выделение карбидов хрома по границам зерен, вызываемое распадом жёсткого раствора, есть основной обстоятельством нестабильности стали и приводит к понижению пластичности, и увеличение склонности стали к межкристаллитной коррозии. Исходя из этого нужна стабилизация структуры литой стали аустенитных марок маленькими карбидообразующими добавками титана либо ниобия. Эти элементы быстро уменьшают количество карбидов хрома, выделяемых по границам зерен, и, следовательно, мешают обеднению главного жёсткого раствора хромом.
Не считая карбидов хрома, в литой хромоникелевой стали аустенитных марок время от времени обнаруживается в малых количествах хрупкая составляющая —сигма-фаза, которая, так же как и карбиды хрома, повышает склонность сплава к межкристаллитной коррозии и разупрочнению.
Для уменьшения склонности к межкристаллитной коррозии аустенитных сталей рекомендуется понижение содержания углерода и, как уже ранее отмечалось, введение в сталь сильных карбидо-ниобия элементов и образующих титана в количествах, нужных для полного связывания имеющегося в стали углерода в стойкие карбиды (TiC, NbC) либо карбонитриды. Наряду с этим неспециализированное содержание углерода в стали должно быть понижено до 0,08—Ю,11%.
В сталях, содержащих титан, принято иметь примерно пятикратное отношение титана к углероду, а в сталях, содержащих ниобий, восьми — десятикратное отношение ниобия к углероду.
Сталь для того чтобы состава фактически не склонна к межкристаллитной коррозии в электролите. Механические и жаропрочные особенности ее при комнатной и повышенных температурах существенно
превышают свойства стали с простым меньшим содержанием и содержанием углерода титана. Уменьшение содержания углерода до 0,06% в стали с ниобием ведет к появлению сигма-фазы.
В отдельных случаях, и при более высоких содержаниях углерода, не считая карбидов хрома, в литой хромоникелевой стали аустенитных марок время от времени по границам зерен возможно замечать образование сигма-фазы, что связано с наличием в стали ферритообразующих элементов в избыточном количестве. Ввиду того, что наличие сигма-фазы в стали очень нежелательно, такие элементы направляться додавать совершенно верно в заданных количествах.
В ходе эксплуатации при больших температурах, наровне с явлением распада жёсткого раствора в металле происходит пластическая деформация. Воздействие пластической деформации неоднозначное: с одной стороны увеличивается жесткость металла (явление наклепа), причем под действием температуры наклеп будет неспешно сниматься, с другой —пластическая деформация содействует ускорению процесса выпадания фаз из пересыщенного жёсткого раствора (интерметаллические соединения и карбиды).
Все эти процессы происходят в металле весьма медлительно, но так как срок работы подробностей исчисляется несколькими десятками тысяч часов, то за это время в структуре металла, а следовательно, и в особенностях его происходят громадные трансформации. Перечисленные явления обнаруживаются опробованиями на ползучесть, долгую прочность, релаксацию, старение, усталость при больших температурах.
Для увеличения механических особенностей металла необходимо, дабы легирующие элементы, в особенности карбидообразующие, переводились в жёсткий раствор. Для более полного растворения углерода в аусте-ните и уменьшения выделенияшвторичных фаз отливки из стали таких марок направляться подвергать закалке с последующеи стаоилизацией. Сигма-фаза, находящаяся в металле по окончании отжига и закалки отливок, преобразовывается в феррит.
Нужно кроме этого учитывать, что теплопроводность стали аустенитных марок примерно в 3 раза меньше теплопроводности углеродистой стали, что дополнительно содействует локализации тепла в отдельных «термических» узлах отливки. Коэффициент же расширения стали таких марок больше углеродистых на 50%, исходя из этого нужно иметь в виду более высокие повышенное коробление и остаточные напряжения отливок.
Термическая обработка особенно серьёзна для аустенитных отливок сложной конфигурации, у которых имеются особенно громадные внутренние напряжения, быстро понижающие эксплуатационные особенности подробностей турбин.
Очень незначительное увеличение механических особенностей при комнатной температуре, замечаемое в стали аустенитных марок, по окончании применения соответствующего режима термической обработки не есть постоянным, поскольку происходящие при эксплуатации либо при неестественном старении процессы неспешно приводят сталь в более равновесное для данных температурных, условий состояние.
В структуре литых подробностей турбин из аустенитной стали по границам зерен частенько видятся микро- и макротрещины. Большая часть исследователей склонны происхождение этих трещин отнести за счет термических напряжений. В отдельных литературных источниках наличие внутрикристаллических трещин разъясняется действием коррозионной тепловых ударов и среды в ходе термической обработки.
Появление тёплых трещин возможно растолковано кроме этого низкой температурой плавления эвтектики, в состав которой входит карбид ниобия, владеющий меньшей пластичностью в толстостенных отливках.
Изучения структуры умелых и промышленных отливок из стали аустенитных марок ЛА1, ЛАЗ, ЛА4, 1Х20Н12Т-Л и др. говорят о том, что в узких сечениях (40—80 мм) отмечается в основном большое столбчатое строение с направлением кристаллов от поверхности к центру, а в более толстостенных отливках (80— 180 мм) наровне со столбчатым строением в центре наблюдаются территории более небольших дезориентированных кристаллов.
Освещаемые на страницах отечественной и зарубежной литературы взоры по вопросам, связанным с определением оптимального размера зерна литого изделия из стали аустенитного класса, очень разноречивы. К примеру, кое-какие советские исследователи утверждают, что в условиях больших температур крупнозернистое строение значительно влияет на жаропрочные особенности аустенитной стали в сторону понижения этих особенностей.
В работах отдельных зарубежных исследователей отмечается значительное влияние разных режимов термической обработки на величину зерна кованой стали. К примеру, долгая прочность сплава 18-8 практически совсем не зависит от величины зерна, в то время как уменьшение величины зерна с № 2—5 до № 8 содействует значительному увеличению удлинения при долгом разрыве. Свойства сплавов 25-20 и 25-12 кроме этого значительно меняются с трансформацией величины зерна.
С уменьшением величины зерна предел долгой прочности указанных сплавов понижается. Отмечается, что роль величины зерна тем меньше, чем выше температура опробования, к примеру, при температуре 870° величина зерна не оказывает фактически никакого влияния.
Громаднейшее падение предела долгой прочности при уменьшении величины зерна с № 2/4 до № 8 замечаете для сплава 25-20 при температуре 538°. Соответственно понижается удлинение при опробовании на долгий разрыв. Особенно заметно воздействует величина зерна сплава 25-20 на предел ползучести. Уменьшение величины зерна с № 2/4 до № 8 при температуре 538° содействует понижению предела ползучести с 11 до 3,5 кг/мм2, т. е. примерно в 3 раза.
С увеличением температуры опробования сплава 25-20 влияние величины зерна на предел ползучести неспешно заканчивается.
Отдельными работами подтверждается, что на процессы ползучести воздействуют не только свойства фактически кристаллов, но и свойства вещества межкристаллитных прослоек. Отношение количества, занимаемого межкристаллитной прослойкой, к количеству фактически кристаллов зависит от размера кристаллов. Это отношение при мелкозернистых сплавов больше, чем при крупнозернистых, поскольку количество межкристаллитного вещества при мелкозернистом строении громаднейший.
Потому, что при низких температурах границы кристаллов более прочные, чем фактически кристаллы, возможно высказать предположение, что при больших температурах крупнозернистый металл обязан владеть более высоким сопротивлением ползучести, чем мелкозернистый. При низких же температурах должно наблюдаться обратное явление: уменьшение размера зерен стали аустенитных марок существенно повышает пластические особенности ее.
Термическая обработка отливок из стали
Режим термической обработки для отливок из аустенитной стали ЛА1 создан работниками ЦНИИТМАШа под управлением чл.-корр. АН СССР И. А. Одинга.
Сталь ЛА1 владеет четко выраженной дендритной кристаллизацией, слабо поддающейся действию термической обработки.
Благодаря отсутствия фазовых превращений в аустенитных сталях возможно лишь незначительно оказать влияние на устранение транскристаллизации и дендритного строения отливки. Исходя из этого термической обработкой преследуются очень ограниченные цели — гомогенизация жёсткого раствора с частичным растворением карбидов сложного состава (WC, Сг23С6, МоС, TiC, NbC). Наровне с растворением карбидов в зерен аустенита, гомогенизация литых аустенитных сталей содействует кроме этого некоему выравниванию состава в микрообъемах стали.
На основании бессчётных литературных данных для стали ЛА1 рекомендуется термическая обработка, складывающаяся из аусте-низации (закалки) и последующей стабилизации (большого отпуска). С целью более полного перевода в жёсткий раствор карбидов хрома температура закалки увеличивается до 1175—1180°. Указанный режим термической обработки находит ширкое использование при производстве отливок из стали аустенитных марок типа ЛА1 для паровых и газовых турбин высоких параметров.
Двойной режим термической обработки складывается из двух стадий: аустенизации, используемой по окончании прибылей отливок и отрезки литников, и последующей стабилизации, создаваемой по окончании выборки литейных пороков, заварки и обдирки выбранных участков.
АУСТЕНИЗАЦИЯ
1) Посадка в печь при температуре не выше 200°.
2) Нагрев до 600° по 50° в час.
3) Выдержка при температуре 600° + 5° в течение 3 час.
4) Нагрев до температуры 800° по 40° в час в течение 5 час!.
5) Выдержка при температуре 800—850° в течение 3 час.
6) Нагрев до температуры 1150° по 60° в час в течение 5 час.
7) Выравнивание при температуре 1150° в течение 3 час.
8) Выдержка при температуре 1150—1170° в течение 4 час..
9) Охлаждение до 400° на воздухе с обдувкой шлангами.
Предстоящее охлаждение на спокойном воздухе.
СТАБИЛИЗАЦИЯ
1) Посадка в печь при температуре не выше 200°.
2) Нагрев до температуры 650° со скоростью 30° в час.
3) Выравнивание при 650° в течение 3 час.
4) Нагрев до температуры 770° + 10° по 30° в час.
5) Выравнивание при 770° + 10° в течение 6 час.
6) Выдержка при температуре 770° + 10° в течение 10 час.
7) Охлаждение до 440° по 25 + 5° в час.
8) Охлаждение от 440° до 250° по 50° в час.
9) Предстоящее охлаждение на воздухе.
Особенный интерес воображает изучение влияния разных режимов термической обработки на уровень качества отливок. Для данной цели был использован металл умелой отливки — внутренней части газовпуска по окончании аустенизации при 1150—1170°. Перед термической обработкой исследуемая часть отливки со всех сторон была зачищена и подвергнута керосиновой пробе для устранения и выявления литейных пороков.
Для изучения влияния сварочных напряжений в указанной отливке была произведена особая выборка глубиной до 60 мм* которая после этого была заварена, зачищена и протравлена.
Подготовленная так отливка была разрезана на части, подвергнута термической обработке по трем разным режимам термической обработки А, Б и” В.
РЕЖИМ А — СТАБИЛИЗАЦИЯ По окончании ЗАВАРКИ
1) Посадка в печь при температуре не выше 200°.
2) Нагрев до температуры 650° со скоростью 30° в час.
3) Выравнивание температуры при 650° в течение 3 час.
4) Нагрев до температуры 700 + 10° по 30° в час.
5) Выравнивание при температуре 770 + 10° в течение 6 час.
6) Выдержка при температуре 770 + 10° в течение 10 час.
7) Охлаждение до 440° со скоростью 25° в час.
8) Охлаждение от 440° до 250° со скоростью 50° в час.
9) Предстоящее охлаждение на воздухе.
РЕЖИМ Б —АУСТЕНИЗАЦИЯ
1) Посадка в печь при температуре не выше 200°.
2) Нагрев до температуры 550—560° со скоростью 50° в час.
3) Выдержка при температуре 550—560° в течение 5 час.
4) Нагрев до температуры 1050—1070° со скоростью 100—120^ в час.
5) выдержка и Выравнивание температуры при 1050 — 1070е’ в течение 4 час.
6) Охлаждение до температуры 550—560° методом углубления из обдувки и печи воздухом из переноса и шланга в низкотемпературную печь, нагретую до 550—560°.
7) Посадка в низкотемпературную печь при температуре 550— 560°, выдержка и выравнивание при указанной температуре в течение 4 час.
8) Медленное охлаждение с печью со скоростью 25° в час до температуры 200°.
9) Предстоящее охлаждение на воздухе.
РЕЖИМ В — СТАБИЛИЗАЦИЯ По окончании АУСТЕНИЗАЦИИ ПО РЕЖИМУ Б
1) Посадка в печь при температуре не выше 200° С.
2) Нагрев до температуры 550—560° со скоростью 100° в часх
3) выдержка и Выравнивание температуры при 550—560° в течение 3 час.
4) Нагрев до температуры 730—750° со скоростью 100° в час„
5) выдержка и Выравнивание температуры при 730—750° в течение 12 час.
6) Охлаждение до температуры 550—560° со скоростью 25—40° в час.
7) Охлаждение до температуры 250° со скоростью 50° в час.
8) Предстоящее охлаждение на спокойном воздухе.
По окончании термической обработки по всем вышеприведенным режимам каких-либо новых пороков на поверхности отливки не было, найдено.
Исследование не разрешило установить обстоятельства появления интеркристаллитных трещин в ходе заварки и последующей стабилизации, поскольку разрезка исследуемых частей отливки на небольшие темплеты, по-видимому, сняла имеющиеся напряжения. Заварка же и термическая обработка небольших частей отливки вряд ли имела возможность оказать влияние на происхождение напряжений, талантливых позвать, трещины и надрывы.
Широкое изучение режимов термической обработки и влияние их на особенности металла было произведено ЦНИИТМАШем и НЗ им. Ленина на умело-промышленной отливке из аустенитной стали ЛА4 (модификация стали ЛА1 с пара повышенным содержанием титана).
В качестве объекта для изучения служила отливка сопловой коробки паровой турбины СВК-150. Макроструктура металла данной отливки характеризуется темплетом, представленным на рис. 1, Наружная территория небольшой кристаллизации развита слабо и занимает малого площадь. Территория же столбчатой кристаллизации распространяется на солидную часть площади сечения данного участка отливки.
Внутренняя территория отливки с равноосной кристаллизацией металла занимает довольно маленькую площадь темплета.
Микроструктура стали в разных участках отливки пара разна. Но в большинстве участков она. по большей части, складывается из крупнозернистой базы с маленьким числом выделений состоящих в основном из карбидов и карбонитридов титана каковые достаточно равномерно находятся в виде включений как в аустенитных зерен, так и в виде цепочек по их границам (рис. 2).
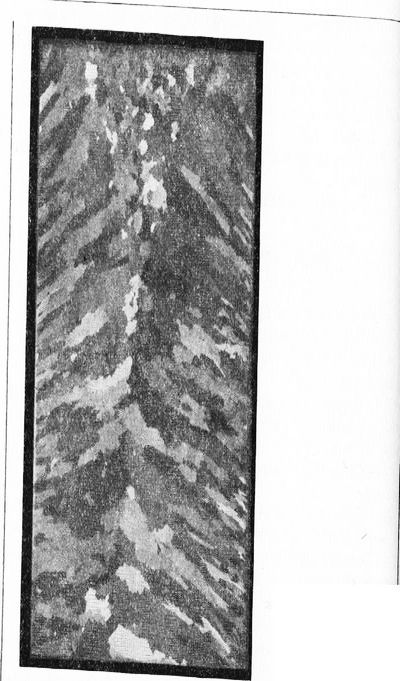
Рис. 1. Макроструктура отливки сопловой коробки паровой турбины CBK-I50 из стали ЛA4.
Рис. 2. Микроструктура металла отливки сопловой коробки паровой турбины СВК-150 из стали ЛА4.
Для изучения влияния температуры нагрева при закалке на структуру стали ЛA4 литые заготовки малых размеров в лабораторных условиях подвергались нагреву в соляной ванне в течение около 20 мин. при восьми разных температурах от 950 до 1300° с промежутком 50 °С*. Значительных трансформаций в характере структуры стали ЛА4 в зависимости от температуры указанных краткосрочных нагревов не было распознано. Не нашли кроме этого показателей трансформации величины зерен стали кроме того при нагреве до самая высокой температуры 1300°, не смотря на то, что количество небольших выделений вторичных фаз в этом случае выяснилось значительно меньше, чем их было у стали в исходном состоянии.
технологические свойства и Структура стали ЛА4 проверялись на более больших промышленных отливках по окончании нижеприведенных режимов термической обработки:
I. Термическая обработка при 950° в течение 4 час.
II. Термическая обработка при 1050—1070° в течение 4 час.
III. Термическая обработка при 1150° в течение 4 час.
IV. Термическая обработка, складывающаяся из аустенизации и стабилизации.
Первые три режима термической обработки различаются лишь температурой большого нагрева отливок. Все остальные условия термической охлаждения (скорости и обработки нагрева, продолжительность выдержек) однообразные.
Результаты механических опробований образцов по окончании разных режимов термической обработки не показывают преимущества того либо иного режима термической обработки.
Прочностные и пластические особенности стали ЛА4 при 650° в следствии старения в час 2300 и 3000 течение. фактически не изменяются, что говорит о малой чувствительности ее к трансформациям режимов термической обработки.
При изучении структуры стали в зависимости от термической обработки для устранения влияния фактора массы образцы отбирали из однообразных смежных участков отливки. При рассмотрении структуры отливок установить какую-либо зависимость ее от термической обработки не представилось вероятным. Заметного роста зерен У стали ЛА4 не наблюдалось кроме того при высоких температурах (1250 и 1300° при краткосрочных нагревах).
При этих нагревах, по-видимому, вероятны лишь незначительные трансформации в структуре отдельных зерен, поскольку способом оптической металлографии (кроме электронную микроскопию) они не выявляются.
Рис. 3. График режима термической обработки (первый вариант).
Рис. 4. График режима термической обработки (второй вариант).
Рис. 5. График режима термической обработки (третий вариант).
При термической обработке с разными нагревами до температур 950, 1050 и 1150° количество выделенных вторичных фаз и темперамент их распределения в любых ситуациях остаются приблизительно однообразными. Более заметное изменение структуры стали ЛА4 отмечается по окончании долгого старения при 700°.
При сопоставлении исходной и конечной структуры стали по окончании долгой выдержки при 700° замечается повышение количества небольших выделений вторичных фаз, концентрирующихся в основном около границ аустенитных зерен. Выделение субмикроскопических вторичных фаз подтверждается увеличением травимости микрошлифов при долгом старении.
Рис. 6. График режима термической обработки (четвертый вариант): а — аустенизация; б — стабилизация.
Дилатометрические опробования с увеличением температуры термической обработки дают охлаждения кривых и сближение нагрева, и размеров образцов до и по окончании термической обработки.
Исследования говорят о том, что более высокая температура (1150°) термической обработки стали JIA4 увеличивает стабильность ее при последующих нагревах.
В зависимости от используемого режима термической обработки показатели долгой прочности изменяются следующим образом. Образцы, вырезанные из отливки по окончании термической обработки по режиму: посадка в печь при температуре 20—250°, нагрев до 500° со скоростью 30—50° в час, выдержка при 500° 3 часа, нагрев до 950° со скоростью 90—120° в час, нагрев до 1070° со скоростью 50° в час, выдержка 3—4 часа, охлаждение с печью до 850°, охлаждение до 250° со скоростью 25—30° в час, предстоящее охлаждение на воздухе, имели при 650° предел долгой прочности, равный 8,5 кг/мм2. Металл данной же отливки по окончании закалки со стабилизацией по режиму: закалка с 1150° по окончании двухчасовой выдержки и последующая стабилизация при 800° в течение 10 час. —имеет предел долгой прочности (ст-105) при 650° — 10 кг!мм2 вместо 8,5 кг!мм2.
Вышеприведенные эксперименты и ряд других работ по изучению режимов термической обработки говорят о том, что для аустенитной стали ЛА4 и ей аналогичных совмещенный режим термической обработки с большой температурой нагрева 1050° в отношении долгой прочности был менее рациональным, чем двойной режим термической обработки, складывающейся из закалки при 1150° и последующей стабилизации при 800°. Но возможно сделать предположение, что при тщательном подборе оптимальных выдержек и параметров нагрева при совмещенном режиме термической обработки возможно будет обеспечить более высокие жаропрочные особенности стали.
Для данной цели потребуется проведение особых исследовательских работ. Возможно кроме этого ожидать, что в ходе долгой эксплуатации при больших температурах может случиться упрочнение стали и в конечном итоге провалится сквозь землю преимущество двойного режима термической обработки перед совмещенным. Сокращенный режим термической обработки разрешит сократить неспециализированный цикл обработки, исходя из этого изучения в этом направлении направляться признать желательными, поскольку фактор сокращения длительности режимов термической обработки, в особенности в условиях фабрик, изготовляющих турбины, имеет громадное значение.
Подвергавшаяся изучению литая сталь марки ЛА4 была выплавлена на свежих шихтовых материалах. В связи с необходимостью применения в качестве шихтовых материалов —50% отходов производства в виде доходов, продувки и литников жидкой ванны кислородом появляется необходимость дополнительной проверки режима термической обработки для отливок из таковой стали.
Рис. 7. охлаждения стали и Дилатометрические кривые нагрева ЛA4: 1 — обработанной при 950”; 2 — обработанной при 1050°; 3 — обработанной при 1150° С.
Данные исследований стали ЛA4, выплавленной с применением 50% отходов в шихте, подтвердили целесообразность применения следующего режима термической обработки.
1. Аустенизация. Посадка в печь при 200°, нагрев до 600°— 8 час., выдержка при 600°—3 часа, нагрев до 950° — 5 час., выдержка при 950° —2 часа, нагрев до 1050° —2 часа, выдержка
2. Стабилизация. Посадка в печь при 140°, нагрев от 200 до 650°— 9 час., выдержка при 650—660° —3 часа, нагрев от 660° до 760°— 3 часа, выравнивание при 760—770° —3 часа, выдержка при 770— 780° — Ю час. и охлаждение с печью до 400°.
Рис. 8. Макроструктура отливки обоймы уплотнения газовой турбины ГТ-12-3 из стали ЛA4.
При 1050 —1080° —2 часа, нагрев до 1160°— 3 часа, выдержка при 1160 —1180°—4 часа и охлаждение на воздухе.
Вышеуказанный режим термической обработки был проверен на отливке обоймы уплотнения газовой турбины (плавка № 24214) и Дал хорошие результаты.
Макроструктура темплетов, вырезанных из различных частей отливки обоймы, характеризуется плотным строением и большими столбчатыми кристаллами.
—
При изготовлении сварных узлов авиационных конструкций ответственное место занимает термическая обработка. В большинстве случаев термической обработке подвергаются подробности и узлы из сталей, тёмных сплавов, титановых сплавов и некоторых вторых материалов. Узлы из легких сплавов, в большинстве случаев, свариваются из предварительно закаленных и состаренных элементов и последующей термической обработке не подвергаются.
При изготовлении сварных узлов из чёрных сплавов и сталей смогут быть два варианта исходного состояния подробностей перед сваркой. В первом случае подробности термически обрабатываются лишь до сварки. По второму варианту узлы изготовляются из отожженных либо нормализованных элементов с термической обработкой всей конструкции по окончании сварки.
Заготовки и узлы в соответствии с технологическим процессом их изготовления смогут много раз подвергаться разным операциям термической обработки. Вследствие этого по занимаемому назначению и месту в технологическом ходе все операции термической обработки возможно разбить на три группы: а) подготовительную б) промежуточную и в) окончательную.
Подготовительная термическая обработка имеет целью в большинстве случаев подготовить материал, поступающий с металлургических фабрик, к механической обработке, обработке давлением и сварке.
В качестве операций подготовительной обработки для сталей, например, возможно назвать:
1. Низкий отжиг для сталей типа ЗОХГСА и ЗОХГСНА с целью снятия внутренних напряжений перед заготовительными работами
2. Неполный отжиг, при котором происходит частичное изменение особенностей металла. Неполный отжиг в большинстве случаев используется для металлических заготовок из высокопрочных сталей с целью снятия внутренних улучшения и напряжений обрабатываемости резанием.
3. Полный отжиг для подробностей из сталей типа ЗОХГСА и ЗОХГСНА и нормализация для малоуглеродистых сталей, подвергающихся штамповке и глубокой вытяжке. Довольно часто употребляется изотермический отжиг. По итогам трансформации физико-механических особенностей он подобен полному отжигу, но менее продолжителен.
4. отпуск и Закалка подробностей из конструкционных сталей, не подвергающихся термической обработке по окончании сварки.
5. Закалка заготовок из сплавов и аустенитных сталей, подвергающихся штамповке и глубокой вытяжке.
Промежуточная термическая обработка чаще используется для конструкций и узлов, подвергающихся по окончании сварки большой правке либо механической обработке.
В качестве промежуточной термической обработки довольно часто употребляются:
1. Низкий отжиг для узлов из сталей типа ЗОХГСА и ЗОХГСНА, подвергающихся по окончании сварки правке.
2. Неполный отжиг для узлов из сталей того же типа, проходящих механическую обработку.
3. Закалка для сплавов и аустенитных сталей с целью снятия напряжений, повышения пластичности и выравнивания структуры.
К промежуточной термической обработке возможно отнести и предварительный подогрев подробностей перед сваркой и сопутствующий нагрев сварных соединений при сварке, снимающий внутренние напряжения для предотвращения трещин.
Окончательная термическая обработка ставит перед собой цель придание сварному узлу механических особенностей, обусловленных чертежом и техническими условиями, и снятие внутренних напряжений в изделии, показавшихся в следствии прошлых операций.
К операциям окончательной термической обработки относятся:
1. Закалка с последующим отпуском изделий из высокопрочных сталей типа ЗОХГСА и ЗОХГСНА.
2. Нормализация самые ответственных узлов из малоуглеродистых сталей.
3. Закалка узлов из сплавов и аустенитных сталей.
4. Особые виды обработки, используемые для некоторых сплавов и высоколегированных сталей.
Термообработку узлов по окончании сварки стремятся проводить при минимальных припусках на последующую механическую обработку, а довольно часто и при окончательных размерах. Но для больших узлов со сложной конфигурацией простые способы термической обработки довольно часто сопровождаются происхождением громадных короблений. Особенно это характерно для операции закалки.
Правка же закаленных на большую прочность узлов не всегда желательна ввиду возможности образования трещин. Решения данной неприятности довольно часто, в случае если разрешают габариты и форма изделия, возможно достигнуть за счет применения изотермической обработки, разрешающей существенно уменьшить коробление узлов.
К тому же изотермическая обработка, снижая деформации, содействует тем самым уменьшению припусков на механическую доработку.
Выдержка при охлаждении производится в селитровых ваннах при температуре 260 — 270 °С. Громадное внимание нужно кроме этого уделять верному конструированию приспособлений для поддержания изделий при нагреве в закалочной печи, и удобству и быстроте захвата узлов при выгрузке их из печи и переносе в селитровую ванну либо закалочную ванну.
Громадное значение имеет кроме этого выбор верного размещения изделия в печи в зависимости от его конфигурации. Наряду с этим главным требованием есть устранение возможности деформации узла за счет провисания его под собственной тяжестью. Охлажденные на воздухе по окончании обработки в селитровой ванне узлы должны быть срочно и шепетильно промыты в тёплой воде чтобы не было разъедания металла, в особенности на поверхностях с окончательными размерами.
Для подробностей из титаного сплава и его сплавов в большинстве случаев используются подготовительная и окончательная термическая обработка.
В большинстве случаев подробности по окончании заготовительно-штамповочных работ, которые связаны с нагартовкой материала, подвергаются отжигу для снятия имеющихся напряжений с последующим травлением для снятия поверхностных окислов.
Подробности из титановых сплавов, подвергаемые сварке плавлением, и сварочную проволоку нужно отжигать в вакууме с целью понижения содержания водорода и, как следствие, увеличения их пластичности. Отжиг производится при температуре 700 — 800° С и вакууме 10~3 — 10~4 мм рт. .ст. в течение 1 — 2 час.
В качестве окончательной термической обработки кроме этого в большинстве случаев употребляется отжиг. Отжиг титановых сплавов, в большинстве случаев, не воздействует на механические особенности сварных соединений (для сплавов типа ВТ-1, ВТ-4, 0Т4 и др.), но снижает внутренние напряжения, появляющиеся в изделии при сварке. Целесообразно отжиг создавать в приспособлениях, не допускающих короблений узлов.
В некоторых случаях допускается создавать местный отжиг сварных соединений посредством газовой горелки. Местный отжиг производится в приспособлении и сразу же по окончании сварки. Сварные соединения, выполненные автоматической сваркой, смогут отжигу не подвергаться.
Операции термической обработки употребляются кроме этого для многих вторых сплавов и материалов. В зависимости от типа материала и поставленных целей назначаются и режимы обработки и соответствующие виды. Эти вопросы излагаются в особой литературе.