Тугоплавкие сплавы
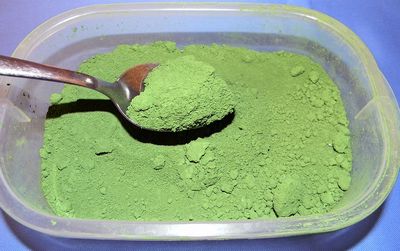
Общепринятой границы по температуре плавления, которая бы четко отделяла тугоплавкие элементы от других, еще нет. В одних случаях такой температурой считают 1600 °С, а в других 1875 °С (температура плавления хрома).
Если принять температуру 1600 °С за величину нижнего предела температур плавления тугоплавких металлов, то к числу тугоплавких можно отнести металлы: V, W, Hf, Ir, Lu, Mo, Nb Os, Pt, Re, Rh, Та, Те, Th, Ti, Tc, Cr, Zr.
По температуре плавления перечисленные 18 металлов можно разделить на три подгруппы (по элементу, наиболее характерно представляющему тугоплавкость).
1. Подгруппа хрома (температура плавления от 1600 до 2000 °С) — Ti, V, Cr, Zr, Rh, Lu, Pt, Th.
2. Подгруппа молибдена (температура плавления от 2500 до 3000° С) — Мо, Тс, Та, Os.
3. Подгруппа вольфрама (температура плавления более 3000° С) — W, Re.
По плотности тугоплавкие металлы можно разделить на металлы:
1) легкие (до 5 г!см3) — Ti;
2) тяжелые (5-10 г/см3) — V, Cr, Zr, Nb, Lu;
3) очень тяжелые — Mo, Тс, Rh, Hf, Та, W, Os, Ir, Rt, Th.
Хром и ванадий по сравнению с другими тугоплавкими элементами имеют меньшую температуру плавления, однако из-за определенных недостатков (например, хром при температуре ниже 350 °С очень хрупок) их редко применяют в качестве основы тугоплавких сплавов.
При испытании растяжением гладких ненадрезанных образцов температура перехода вязкого разрушения в хрупкое составляет для ниобия 200 °С; тантала 196 °С; молибдена 0 °С; вольфрама 300 °С; хрома 350 °С. При иномхарактере испытаний и наличии примесей температура перехода из вязкого состояния в хрупкое может измениться, однако общая тенденция сохраняется, что должно учитываться при выборе металла для соответствующих условий и в качестве основы сплава.
Сплавы на основе титана. Титан обладает низкой теплопроводностью (в 13 раз меньшей, чем у алюминия), низким модулем нормальной упругости (11 250 кгс/мм2), высоким электросопротивлением и значительной анизотропией некоторых физических свойств, обусловленной его гексагональной структурой.
Технический титан благодаря высокому сопротивлению коррозии является прекрасным материалом для химического машиностроения и приборостроения, а также для судостроения. Он используется для изготовления деталей насосов, применяемых для перекачки агрессивных жидкостей, теплообменников, работающих в условиях химически агрессивных сред и т. д.
Титан является основой новой группы сплавов с малой плотностью, высокой общей и удельной прочностью. Предел прочности при растяжении некоторых титановых сплавов превышает 150 кгс/мм2. С учетом низкой плотности сплавы с такой прочностью эквивалентны стали с пределом прочности при растяжении 255 кгс/мм2.
Изделия из титановых сплавов хорошо работают при значительных отрицательных температурах, вплоть до температуры жидкого азота.
Литье титановых сплавов вызывает большие технологические ‘РУДности, обусловленные активным взаимодействием жидкого расплава со всеми используемыми в настоящее время для изготовления Литейных форм материалами.
В промышленности используют простые и сложные титановые сплавы. Разнообразие структур и свойств титановых сплавов объясняется полиморфизмом самого титана, хорошей растворимостью многих элементов в нем, его способностью сравнительно легко вступать в химические соединения с другими элементами, которые, в свою очередь, обладают способностью растворяться в титане.
Химические элементы, образующие с титаном сплавы, делят на три группы.
К первой группе относят элементы, повышающие стабильность осфазы, их называют а-стабилизаторами. Основным элементом этой группы сплавов является алюминий.
Система титан-алюминий для титановых сплавов по значимости аналогична системе железо-углерод в сплавах на основе железа.
Вторую группу составляют элементы, стабилизирующие р-фазу, их называют стабилизаторами. Они делятся на две подгруппы. В сплавах титана с элементами первой подгруппы при достаточно низкой температуре происходит эвтектоидный распад Р-фазы. В эту подгруппу входят Сг, Мп, Fe, Си, Ni, Be, W, Co.
С элементами второй подгруппы при достаточно высокой их концентрации р-твердый раствор сохраняется до комнатной температуры без эвтектоидного распада, р-стабилизаторы второй подгруппы (V, Мо, Nb, Та) иногда называют изоморфными стабилизаторами.
К. третьей группе относят легирующие элементы — нейтральные упрочнители, не оказывающие существенного влияния на устойчивость а- и р -фаз (Sn, Zr, Ge, Hf, Th).
В зависимости от того, какая структура преобладает в титановых сплавах после термической обработки, их делят на ос-, (а + р) — и р-классы.
Сплавы, применяемые в промышленности, делят на следующие подгруппы:
1) двойные сплавы титан-алюминий;
2) сложные сплавы, легированные, кроме алюминия, другими (нейтральными) упрочнителями;
3) сложные сплавы мартенситного типа, в состав которых помимо алюминия, введены р-стабилизаторы в таком количестве, которое еще не вызывает появления в структуре при комнатной температуре Р-фазы; о 1
4) сложные сплавы, содержащие, кроме алюминия, цирконий, ниобий и тантал;
5) сплавы, в структуре которых, кроме а-фазы содержатся интерметаллиды (например, сплавы системы Ti-A1-Sn-Cu).
Термодинамически устойчивую р-фазу можно получить на основе систем, в которых легирующие элементы имеют объемно-центрированную кубическую решетку при комнатной температуре и дают с P-Ti непрерывный ряд твердых растворов. К числу таких элементов относятся ванадий, хром, молибден, ниобий и тантал.
Представителем этой группы сплавов является сплав, содержащий 90% Ti и 10% Сг. После закалки и старения его предел прочности при растяжении достигает 160- 170 кгс/мм2 при относительном удлинении 2-6%.
Состав и свойства. Химический состав некоторых титановых сплавов, используемых главным образом для литья слитков и последующей обработки давлением, приведен в табл. 35.
Сплавы ВТ5, ВТ5-1, ВТ4, ОТ4, ВТ10 являются типичными представителями а-титановых сплавов. Сплавы ВТЗ, ВТЗ-1, ВТ6, ВТ8, ВТ14 представляют собой а + (i-титановые сплавы.
В литом состоянии в большинстве случаев прочность и вязкость титана и его сплавов ниже соответствующих показателей образцов из тех же сплавов после обработки давлением.
Наиболее благоприятным сочетанием свойств обладают титановые сплавы, содержащие одновременно а- и р-фазы. Эти сплавы содержат алюминий, фиксирующий а-фазу, а также молибден, ванадий и марганец.
За рубежом для изготовления фасонных отливок успешно применяют сплавы типа Ti-Fe-V, содержащие 1,2% Fe и 0,8% V.
В отличие от других сплавов плавка титана и его сплавов сопряжена с большими трудностями. Титан при высоких температурах активно взаимодействует с азотом и кислородом. Реакция образования нитрида титана в этих условиях протекает так же активно, как горение некоторых веществ в среде кислорода.
Расплавленный титан активно взаимодействует и с кислородом. Поэтому плавку титановых сплавов проводят в условиях, исключающих возможность его контакта с этими газами. Расплавленный титан также активно взаимодействует со всеми обычными огнеупорными материалами, из которых выполнена рабочая часть плавильного агрегата.
Из всех известных^высокоогнеупоров менее интенсивно с титаном взаимодействует плотный графит, но и он во многих случаях не может быть использован, так как в титановых сплавах содержание углерода строго ограничено.
Наиболее совершенным плавильным агрегатом для выплавки титана и его сплавов является вакуумная дуговая печь с расходуемым электродом. В таких печах могут быть выплавлены различные порции жидкого металла — от долей килограмма до нескольких тонн.
Литье. Песчано-глинистые формы для изготовления фасонных отливок из титана и его сплавов по отмеченным выше причинам малопригодны.
Отливки с наиболее чистой поверхностью изготовляют в массивных медных формах или тонкостенных медных водоохлаждае-мых формах. Применение медных форм ограничено их высокой стоимостью и невозможностью получения в них отливок сложной конфигурации. Удовлетворительным материалом для изготовления форм является плотный графит. Формы из него обычно получают с помощью механической обработки. Графитовые формы можно использовать несколько раз.
Но и их стоимость достаточно высока.
Более дешевыми являются оболочковые формы, изготовленные из смеси высокоогнеупорных нейтральных окислов с применением в качестве связующего феноло-формальдегидной смолы. Оболочковые формы могут быть изготовлены, например, из графитового порошка на смоляной связке.
Во всех случаях применения литейных форм из высокоогнеупорных материалов поверхность отливок оказывается на ту или иную величину загрязненной продуктами взаимодействия титана с материалом формы. При использовании для изготовления форм плотного графита отливки загрязняются на глубине около 1% толщины стенки. Заливка в оболочковые формы из крупнозернистого графитового порошка и феноло-формальдегидной смолы позволяет получать отливки толщиной до 50 мм, поверхность которых может быть загрязнена на глубину приблизительно до 1,5 мм.
Мелкие сложные тонкостенные отливки из титановых сплавов можно получать в формах, изготовленных по выплавляемым моделям. В качестве материала для форм используют кремнезем, циркон, двуокись циркония, силлиманит, а в качестве связующего — этилсиликат, фосфорнокислый аммоний, нитрат циркония.
Для получения доброкачественных отливок литниковопитаю-Щая система должна обеспечивать быстрое заполнение формы и надежное питание толстых сечений.
Современная техника позволяет получать отливки из титановых сплавов с минимальной толщиной стенки 1,5 мм при ширине или высоте отливки 25 мм.
Сплавы на основе ванадия. Ванадий в качестве основы литейных сплавов применяется сравнительно недавно. По этой причине ведения о применении и свойствах ванадиевых литейных сплавов ограничены.
Ванадиевые сплавы используют при температуре до 650-675° С. анадий одновременно имеет хорошую теплопроводность и коррозионную стойкость.
Из ванадия изготовляют трубы центробежным способом в графитовых формах, например трубы диаметром 355 мм и массой около 27 кг.
Установлено, что свойства ванадия улучшаются при сплавлении его с титаном, цирконием, ниобием и некоторыми другими элементами. Сплавы ванадия с 50% Ti, а также с 3% Zr обладают значительно большей пластичностью, чем чистый ванадий.
Легирование ванадия ниобием способствует получению более высокой прочности и увеличению сопротивляемости окислению.
Сплав ванадия с 50% Ti и 2% Si обладает следующими свойствами: предел прочности при растяжении 105 кгс/мм2, относительное удлинение 12,5%; относительное сужение 17,5%.
Сплав ванадия с 50% Ti и 5% А1 имеет более высокую прочность, чем сплавы на основе никеля, кобальта и железа. Длительная прочность его при 300° С соизмерима с прочностью титановых сплавов.
Сплавы на основе хрома. Фасонные отливки из хрома и его сплавов применяют ограниченно. К числу положительных свойств хрома и его сплавов следует отнести сравнительно высокую жаропрочность, а также повышенную стойкость в окислительных и эрозионных средах при высоких температурах.
Вместе с тем, для хрома характерны низкая пластичность при нормальной температуре, высокое значение порога хрупкости и большая склонность его к ухудшению свойств под влиянием незначительного количества многих примесей и в первую очередь газов.
Используемые для литья хромовые сплавы предназначаются для работы при температурах 980-1200 °С.
Чистый хром при 900 °С и напряжении 4,8 кгс/мм2 имеет высокую ползучесть. Многие элементы, вплавляемые с хромом (Со, Ni, Pd, Al, Si и Ti), повышают ползучесть, а 9,5-15% Fe понижают ползучесть. Сплав хрома с 10% Fe и 5-10% Та имеет наименьшую ползучесть при 800° С и напряжении 14,5 кгс/мм2.
Общая деформация такого сплава за 100 ч составляет около 0,25%.
Предел прочности при растяжении сплавов хрома с 40-50% Ni после термической обработки составляет 92-113 кгс/мм2, а относительное удлинение 0-12%.
Введение молибдена в сплав хрома с железом (15% Fe и 25% Мо) обеспечивает получение длительной прочности (около 1000 ч) при температуре 870° С и напряжении 14 кгс/мм2; удлинение образцов в этих условиях составляет 8-10%. Введение в сплавы подобного типа никеля (10% Fe, 5% Мо, 45% Ni) делает их при нормальной температуре пластичными.
Сплав из 60% Сг и 30% Fe с Мо, Ti, Al при хорошей термической стойкости имеет длительную прочность 100 ч при 815 °С и напряжении 19,6 кгс/мма.
Характерной особенностью многих композиций сплавов является отсутствие пластических свойств при нормальных температурах.
Сплавы на основе хрома по жаропрочности превосходят все известные жаропрочные сплавы на основе железа, никеля и кобальта.
Отливки из хрома и его сплавов можно изготовлять только с использованием специальных способов литья.
Сплавы на основе ниобия. Фасонные отливки из ниобия и его сплавов используют при высоких температурах. Известно применение ниобиевых сплавов для деталей турбин, работающих при 1100-1400° С. Высокая жаропрочность и жаростойкость ниобия и его сплавов, несмотря на большие технологические трудности, делают их перспективными для изготовления изделий, работающих в особенно тяжелых условиях.
Применение ниобиевых сплавов позволит повысить температуру газа при входе в турбину с 925 до 1370 °С.
Чистый ниобий обладает очень высокой пластичностью при нормальной температуре, коррозионной стойкостью, хорошими эмиссионными свойствами и хорошо сваривается.
При температуре белого каления прочность ниобия выше, чем любого другого конструкционного материала.
Известны патенты на двойные, тройные и многокомпонентные сплавы ниобия с железом, углеродом, хромом, титаном, алюминием, кобальтом, молибденом, никелем, кремнием, и другими элементами.