Зарубежные литейные цехи
Двухэтажный литейный цех компании «Рено» (Франция) для того чтобы из стали и ковкого чугуна автотракторной индустрии приведен на рис. 1. В торце цеха расположен раздельно стоящий склад формовочных материалов и шихты.
На втором этаже сосредоточены установки и процессы более чистые и менее шумные, и конторы и бытовые устройства. В нижнем этаже расположены смесеприготовительные отделения, выбивка, дробеметная очистка, термическая обработка и разные
помещения и вспомогательные установки, бытовые помещения. Конечный пролет одноэтажный, рекомендован для производства единичных отливок, обслуживается краном.
В плавильном отделении установлены индукционные печи. Восемь печей емкостью 4 т предназначены для стали и плавки чугуна, две печи емкостью 1,5 т — для плавки особых марок стали.
Крупносерийные отливки формуются на двух автоматических линиях, оборудованных четырехпозиционными автоматами, небольшие серии — на встряхивающих формовочных автомобилях с программным управлением. Любая формовочная линия при двухсменной работе цеха производит 70 т отливок в день, обслуживается собственной смесеприготовительной совокупностью с автоматическим контролем качества смеси.
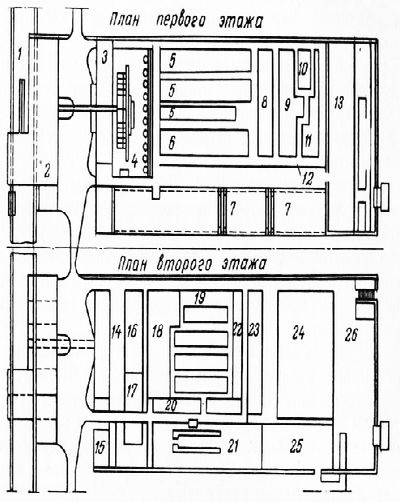
Рис. 1. Двухэтажный цех ковкого и металлического литья компании «Рено» (Франция): 1 — склад свежего песка; 2 — шихтовый двор; 3 — плавильное отделение; 4 — плавильные печи; 5 — изготовление форм для отливок из ковкого чугуна; 6 — изготовление форм для металлического литья; 7 — мостовые краны; 8 — стержневое отделение; 9 — обрубка; 10 — исправление литья; 11 — промежуточный склад литья; 12 — окрасочный конвейер; 13 — бытовые помещения; 14 — ремонтная мастерская; 15 — лаборатория формовочных материалов; 16 — печи для особых сталей; 17 — генераторы; 18 — компрессорная и котельная; 19 — смесеприготовительное отделение; 20 — склад древесных моделей; 21 — формовка единичных отливок; 22 — выбивка; 23 — дробеметная очистка; 24 — печи для термообработки; 25 — обрезка литников; 26 — экспедиция
Отжиг отливок производится в термических печах с газовым нагревом защитной атмосферой и радиационными трубами из азота. Цех запланирован на выпуск 70 т/дни отливок при двухсменной работе.
Новый чугунолитейный цех компании «General Motors Корпорейшн» (США) представлен на рис. 2. Цех выстроен и запущен в эксплуатацию в 1966 г., он занимает площадь 41 340 м2 и рекомендован для производства коленчатых валов из перлитного чугуна с шаровидным графитом, подробностей передачи из перлитного ряда деталей и ковкого чугуна из ферритного чугуна с шаровидным графитом. Цех трудится в две смены, но запроектирован на трехсменный параллельный режим работы.
В третью смену предусмотрена работа лишь плавильного и формовочного отделений с частичной их остановкой для планово-предупредительного ремонта.
Мощность цеха 200 000 т/год, общее число трудящихся 1000 человек, выпуск отливок на 1 м2 площади цеха 5 т/год, а на одного трудящегося — 200 т.
В плавильном отделении установлены одна водоохлаждаемая вагранка с подогревом дутья до 540°С производительностью 55 т/ч с канальным миксером емкостью 60 т и четыре тигельные печи промышленной частоты на 33 т металла любая, предусмотрена установка пятой такой же печи. Вагранка диаметром 2900 мм с водоох-лаждаемыми бронзовыми фурмами трудится непрерывно на протяжении семи дней на производство перлитного чугуна с шаровидным графитом.
Ферритный чугун с шаровидным графитом и перлитный ковкий чугун выплавляются в тигельных печах. Модифицирование магнием производится в трехтонных ковшах. Загрузкой плавильных агрегатов, плавкой и разливкой металла руководит оператор с пульта.
В отделение шихтовки железная шихта для вагранки подается на автодрезине, а личные возвраты — подвесным транспортом. Шихтовые материалы загружаются в пятитонную бадью магнитной шайбой мостового крана грузоподъемностью 10 тс в количествах, заблаговременно заданных на особом щите. Шихта для индукционных печей подается в бадьях по монорельсу к пяти пунктам, на каждом из которых установлены автоматические весы с электронными датчиками.
Лом, переплавляемый в индукционных печах, предварительно сушат. В плавильном отделении предусмотрена аварийная совокупность при прекращения подачи электричества либо охлаждающей воды для плавильных агрегатов.
Формовочное отделение оборудовано двумя литейными тележеч-ными конвейерами длиной по 375 м. На каждом конвейере установлены по две безударные встряхивающие формовочные автомобили с гидравлическим прессованием до 16 кГс/см2. Производительность каждого конвейера 270 форм/ч. Формовочные автоматы заключены в изолированные кабины с отсосом запыленного воздуха и поглощением шума.
сборка форм и Простановка стержней производится на конвейере. Период охлаждения залитых форм строго контролируется. Эти по каждой форме поступают в счетно-решающее устройство, которое учитывает результаты лабораторного анализа металла, условия охлаждения форм и дает соответствующие сигналы на выбивной участок. Тут в зависимости от сигнала формы с годными отливками поступают на основную выбивную решетку, а забракованные — на запасного.
Выбивные участки заключены в звуко- и пы-леизолирующие кабины. Выбитые отливки подвесным конвейером доставляются в очистные отделения. Отработанная смесь ленточными транспортерами подается в смесеприготовительное отделение.
В цехе употребляются лишь стержни, полученные по горячим коробкам, и оболочковые. Формовочные материалы, а также кварцевый песок, глина, бентонит, молотый другие добавки и уголь, поставляются по железной дороге и сохраняются в восьми бетонных силосах. К смесеприготовительным установкам формовочные материалы доставляются совокупностью ленточных транспортеров, элеваторов и пневмотранспортом.
Любой литейный конвейер обслуживает отдельная смесеприготовительная установка производительностью 250 т смеси в час, оборудованная смесителем барабанного типа.
В термоочистное отделение отливки доставляются охладительными подвесными конвейерами толкающего типа в особых контейнерах с раскрывающимся дном.
Отжиг на ковкий чугун производится в двух печах постоянного действия с контролируемой воздухом и машинально регулируемой температурой отдельных территорий от 650 до 1000 °С, протяженность печей 38 м. Закалка отливок производится в туннеле с регулируемым воздушным дутьем. Для отдыха отливок из ковкого чугуна установлены две конвейерные печи постоянного действия.
Особенное внимание уделено вентиляции: неспециализированная протяженность труб вентиляционной совокупности цеха образовывает около десяти километров. Естественная аэрация отсутствует, цех выполнен без фонарей, открытых проёмов и окон. Приточная совокупность снабжает восьмикратный обмен воздуха в час.
Наружный воздушное пространство предварительно пропускается через 23 промывателя, где он очищается от пыли и охлаждается и лишь позже распределяется по цеху. Зимой наружный воздушное пространство подогревается. Вытяжная совокупность вентиляции снабжает отсос запыленного воздуха от всего пылеобразующего оборудования в цехе. Отсасываемый запыленный воздушное пространство очищается от пыли в 14 мокрых пылеуловителях на крыше цеха.
Очищенный воздушное пространство, выбрасываемый в воздух, содержит пыли менее 1,25 г/и3. Ваграночные газы отсасываются ниже завалочного окна, дожигаются, очищаются в мокром скруббере и выбрасываются в воздух с содержанием пыли ниже 2 г/м3.
Цех освещается более чем 10 000 ртутных и люминесцентных ламп, снабжающих освещенность на уровне дневного света. Потолки и стенки всего строения окрашены в белый цвет и лишь нижняя часть стен на уровне 2 м от пола — в коричневый. трубопроводы и Оборудование окрашены в различные цвета.
Самый большой в мире литейный цех по производству отливок из чугуна с шаровидным графитом выстроила американская компания «Шевроле» (рис. 8.9). Мощность цеха 350 000 т/год при двухсменной восьмичасовой работе с пятидневной рабочей неделей. Цех неспециализированной площадью 93 000 м2 размещен на промышленной площадке 80 га, по которой проложено 4,3 км ЖД дорог и 3,3 км цементных дорог.
При проектной мощности цеха общее число трудящихся образовывает 1750 человек.
В плавильном отделении установлены четыре водоохлаждаемых вагранки тёплого дутья диаметром 2600 мм, производительностью любая 40 т/ч, две электродуговые печи емкостью по 22 т и две индукционные печи нужной емкостью 40 т. Плавка ведется дуплекс-процессом вагранка+электропечь. Одна пара вагранок трудится с двумя дуговыми печами, производительность которых при перегреве жидкого чугуна образовывает по 40 т/ч. Металл в дуговые печи подается по желобу, шлак отбирается на желобе.
Вторая пара вагранок трудится совместно с канальными индукционными печами.
Рис. 3. Замысел чугунолитейного цеха компании «Шевроле» (США): 1 — емкости для связующих; 2 — емкости для угля; 3 — силосы для формовочных материалов; 4 — стержневое отделение; 5 — ремонтная мастерская № 3; 8 — формовочно-заливочное отделение; 7 — площадь для пятой формовочной линии; 8 — плавильное отделение; 9 — склад шихтовых материалов; 10 — ремонтная мастерская N° 2; 11 — печь для термообработки отливок; 12 — очистное отделение; 13 — участок контроля качества отливок; 14 — материальный склад; 15 — модельная мастерская; 16 — главная ремонтная мастерская № 1; 17 — гараж; 18 — контора
Любая индукционная установка складывается из двух печных корпусов, питаемых от одного источника энергии. Неспециализированная производительность плавильных агрегатов 610 000 т/год при выходе годного 0,55%. Остановка вагранок с целью проведения ремонтных работ производится один раз в неделю.
Шихтовые материалы размещаются в крытом складе, расположенном между плавильным и очистным отделениями, оснащенным закромами емкостью 2250 т, снабжающими двухсменную работу плавильного отделения. загрузка и Шихтовка вагранок автоматическая.
Химический анализ металла контролируется по 17 элементам скоростным способом посредством вакуум-спектрометра. Результаты анализа сообщаются в цех через электронно-счётные автомобили.
Формовочное отделение запроектировано на выпуск 1080 форм/ч к оборудовано четырьмя формовочными линиями, любая с независимым транспортными системами и технологическим оборудованием, аналогичными по производительности, размерам, последовательности и оборудованию операций. На линиях все операции выполняются по автоматическому циклу за исключением простановки стержней, удаления литников и заливки форм, осуществляемыми вручную.
Такая линия производительностью 270 форм/ч продемонстрирована на рис. 4. Любая линия снабжена тележечным конвейером длиной 504 м из 275 тележек, перекрытых плитами для опок 1270Х X 810X375/300 мм. Вес залитой формы 3,6 т.
Рис. 4. Формовочно-заливочно-выбивная линия цеха компании «Шевроле»: 1 — ленточный транспортер распределения отработанной смеси; 2 — элеватор отработанной смеси; 3 — магнитный сепаратор на ленте возврата отработанной смеси и барабанное сито; 4 — бункер над формовочными автомобилями; 5 — формовочный агрегат нижних полуформ; 6 — устройство для установки нижних полуформ на конвейере; 7 — участок простановки стержней; 8 — наклонный желоб излишней формовочной смеси; 9 — формовочный агрегат верхних полуформ; 10 —. устройство для сборки форм; II — тележечный литейный конвейер; 12 — заливочный ковш; 13 — заливочная территория; 14 — территория охлаждения форм; 15 — агрегат выбивки верхних полуформ; 16 — ленточные транспортеры просыпи формовочной смеси; 17 — выбивная решетка; 18 — вибрационный конвейер для тёплых отливок; 19 — ленточные транспортеры формовочной смеси; 20 — бегуны; 21 — охладители отработанной смеси; 22 — питатели, подающие смесь в охладители; 23 — бункер отработанной смеси
Охладительная территория конвейера проходит в подвальном помещении в два яруса, что уменьшает площади цеха на 19%. На линии стоят два прессовых автомата с безударным встряхиванием для верхних и нижних полуформ.
Формы заливаются из ковшей емкостью 1600 кг, скорость перемещения которых на протяжении заливки синхронизирована со скоростью перемещения литейного конвейера. Через 8 мин по окончании заливки, достаточных для затвердевания металла, формы транспортируются литейным конвейером в подвальное помещение, где они охлаждаются. Время охлаждения 52 мин, но при необходимости его возможно расширить.
Из подвала литейный конвейер выходит на первый этаж и доставляет остывшие формы на участки выбивки верхних и после этого нижних полуформ. Верхние опоки снимаются с форм, смесь из них выдавливается, а опоки возвращаются к соответствующей формовочной машине. Нижние опоки кантуются, отливки из них вываливаются на решетку, оставшаяся смесь выдавливается, опоки снова кантуются и направляются к собственной машине.
Охлажденные литники в бадьях подвесным конвейером отправляются в закрома шихтового склада. Отливки из выбивной являлось вибрационным лотковым питателем выдаются в бадьи подвесного охладительного транспортера с приводными и неприводными участками. Время охлаждения отливок в бадьях 40—170 мин.
Мощность стержневого отделения 20 т стержней/ч, а также 45% по весу составляют оболочковые стержни, 45 — цельные стержни, изготовляемые в тёплых коробках, и 10% —песчано-масляные. Отделение оборудовано пятью стержневыми машинами 45 и смесителями.
Стержневые автомобили размещены в шесть последовательностей по ширине отделения. Любой последовательность обслуживается уборочным транспортером. Готовые стержни ставят, снимают и комплектуют на подвесных конвейерах с приводными и неприводными участками. Любая подвеска на конвейере закодирована и возможно направлена на склад либо к формовочной линии.
При необходимости каждая подвеска конвейерного участка возможно машинально позвана на любую формовочную линию.
Свежие пески поступают в ЖД гондолах, разгружаются в бункера и сохраняются в силосах. За две смены цех потребляет в среднем 145 т свежих песков. По окончании охлаждения отливки последовательно подвергаются дробеметной очистке, обрубке, контролю и зачистке.
В очистном отделении установлены четыре дробе-метных агрегата постоянного действия.
Контроль качества отливок выстроен на принципе ответственности каждого отделения за уровень качества делаемой им работы. Одновременно с этим любой элемент технологического процесса производства отливок контролируется инспекцией по качеству. Неспециализированный штат приёмки контроля отливок и службы качества в двух сменах образовывает около 50 человек.
Строение литейного цеха одноэтажное, без окон, выстроено из металлических конструкций с наружным заполнением из готовых цементных панелей и из гофрированного металлического страницы. Приточно-вы-тяжная вентиляция снабжает в производственных отделениях 32-кратный обмен воздуха в час, наряду с этим подача свежего воздуха достигает 13 млн. м3/ч. Запыленные места имеют местный отсос.
Воздушное пространство, выбрасываемый в воздух, очищается. Из всей площади цеха производственная занимает 56 тыс. м2.
Современные литейные цехи являются специальные фирмы с высокомеханизированным и автоматизированным оборудованием, технологическими процессами, выделяющие пыль, газы и тепло. Труд рабочих в таких цехах усложняется, часть умственного труда увеличивается и, как следствие, психологическая нагрузка на трудящихся возрастает.
Исходя из этого при проектировании литейных цехов очень ответственное место занимают вопросы увеличения условий труда рабочих.
Вследствие этого воображает интерес решение проблем вентиляции, борьбы и освещения с шумом в зарубежных литейных цехах и в первую очередь в новых цехах США.
В литейных цехах США создается маленькое хорошее давление. Приточная вентиляция подает в цех больше воздуха, чем отсасывает вытяжная. Это превышение, к примеру, во снова строящемся литейном цехе компании «Форд» образовывает около 14%.
Свежий воздушное пространство очищается и в зависимости от времени года подогревается либо охлаждается.
Согласно точки зрения американских экспертов, ликвидация окон в современных литейных цехах вытекает из необходимости улучшения контроля чистоты внешней среды в цехе, позволяет осуществлять контроль воздушный поток и стабилизировать требуемое давление в цехе и тем самым содействует улучшению санитарно-ги-гиенических условий труда. Кроме этого, отсутствие фонарей разрешает действенно располагать на крыше бессчётные вентиляционные установки.
Ликвидация окон не оказывает ощутимого влияния на увеличение цены освещения цехов. Считается, что окна с позиций естественного освещения цехов не имеют значительного значения. Освещенность главных производственных отделений в современных литейных цехах США находится на уровне освещения административных помещений и образовывает 1100 лк. На снова строящемся литейном заводе Форда освещенность главных производственных пролетов цеха запроектирована в 1400 лк.
Такая освещенность не может быть по большому счету обеспечена за счет лишь естественного освещения. Помимо этого, в больших литейных цехах с шириной строения 240 м и более без световых фонарей, где работа организована в две, а время от времени и в три смены, эффект естественного освещения по существу сводится на нет.
Не обращая внимания на довольно высокие начальные затраты, в современных литейных цехах США предпочтение отдают лампам с натриевым кварцем, с ртутными парами, ртутным лампам с регулировкой цвета освещения. В большинстве случаев, предусматривается аварийное, время от времени двойное аварийное освещение. К примеру, в литейном цехе компании «Крайслер» главное освещение обеспечивается ртутными лампами, а двойное аварийное освещение — люминесцентными с едой от батарей.
Борьба с шумом в литейных цехах ведется двумя направлениями: методом создания бесшумного оборудования и изоляцией его. Оборудование с большим уровнем шума размещается на отдельных участках, каковые шепетильно изолируют звукозадерживающими преградами. В Соединенных Штатах в 1969 г. издан особый закон, что запрещает трудиться в помещении более 8 ч при уровне шума 90 дб.
Уровень шума на рабочих местах при умственной деятельности не должен быть больше 50 дб, при простой конторской работе — 70 дб.
Распределение капитальных вложений на строительный комплекс строений литейных цехов говорит о том, что затраты на освещение и вентиляцию в Соединенных Штатах составляют 50% всех капитальных вложений строительного комплекса, а остальные 50% идут на архитектурно-фундаменты и строительную часть под оборудование.