Отечественные литейные цехи
Проектирование литейного цеха — трудоемкий процесс. Введение в строй новых заводов литейных и мощностей цехов, и реконструкция существующих требуют громадного количества проектной документации в сжатые сроки.
Для ускорения исполнения проектных работ, и унификации проектных ответов, специальных сооружений и нестандартного оборудования создан «размерные ряды и Типаж производственных участков чугуно- и сталелитейных цехов машиностроительных фабрик», на основании которого созданы типовые проекты плавильных, смесеприготовительных, стержневых, формовочно-зали-вочно-выбивных, обрубных и грунтовочных участков с набором оборудования, организацией производства и типовой технологией. При разработке типовых проектов производственных участков учитывались материалы утвержденных типовых заводов литейных и проектов цехов, проектов снова строящихся, и реконструируемых цехов, отвечающих современному уровню проектирования, и материалы обследования передовых заводов и цехов.
Номенклатура материалов по литейному производству создана и издана рядом проектных организаций. Она вошла в «Общемашиностроительные типовые и руководящие материалы в организации производства и области технологии» (ОМТРМ).
При проектировании применяют утвержденные типовые проекты литейных цехов и созданные типовые участки. Это разрешает существенно сократить сроки проектирования, неточности в проектах и тем самым снизить цена проектных работ. Методом подбора соответствующих типовых производственных участков возможно частично или полностью применять проектную документацию для компоновки литейного цеха.
Компоновки некоторых отечественных и зарубежных литейных цехов в одноэтажном и двухэтажном выполнении приведены ниже. На рис.
1 продемонстрирован сталелитейный цех Уральского автомобильного завода мощностью 30 000 т/год отливок, запущенный в работу в 1967 г. Цех одноэтажный, находится в одном корпусе прямоугольной формы размером 120X 144 м и складывается из двух поперечных пролетов высотой 12,6 м до запятки ферм и пяти продольных пролетов высотой 9 м, сетка колонн по всему корпусу—24 X 12 м, ход колонн по наружным осям — 6 м. Кровля цеха плоская, мягкая, бесфонарная. Корпус имеет развитое подземное хозяйство, где размещены постоянный технологический транспорт, оборудование, работа которого сопровождается шумом, и др.
Площадь застройки корпуса 17 280 м2. К торцу цеха пристроен бытовой корпус.
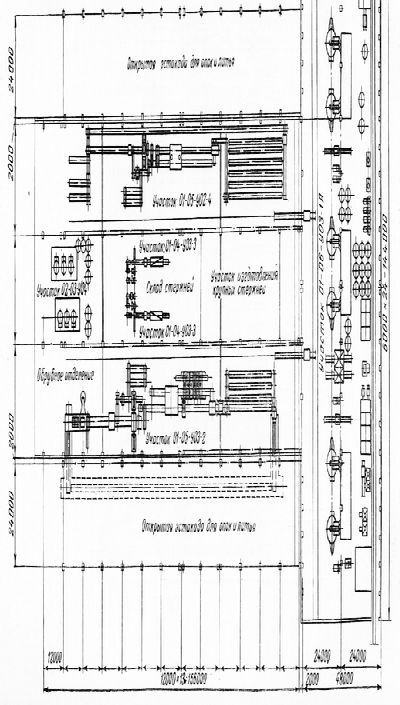
Рис. 1. Сталелитейный цех Уральского автомобильного завода мощностью 30 000 т/год
Цех спроектирован с учетом достижений современной техники отечественного и зарубежного сталеплавильного производства и укомплектован прогрессивным оборудованием, современными автоматикой и транспортными средствами. В корпусе осуществляется комплексный технологический цикл поточного производства.
Громадное внимание уделено эстетике: подбору и качественной окраске оборудования, коммуникаций и оснастки, отделке помещений, улучшению и созданию интерьеров культурно-бытового обслуживания рабочих.
В двух поперечных пролетах корпуса размещены склад формовочных материалов и шихты, плавильное отделение, а в пяти продольных — формовочно-заливочно-выбивное, стержневое, термообрубное и окрасочное отделения. Автоматизированные смесеприготовитель-ные отделения находятся в торцах пролетов соответствующих отделений.
В плавильном отделении установлено пять электродуговых печей типа ДС5МТ производительностью 2,5 т/ч. Жидкий металл на заливку подается в ковшах на подвесном транспортере. В цехе используется процесс грануляции электропечного шлака, в первый раз созданный у нас, что разрешает сократить утраты металла со шлаком на 260 т/год.
В формовочном отделении установлены два конвейера, оснащенные формовочными автомобилями мод. 2М265, для опок размером 950 X X 650?350/350 мм.
Стержневое отделение оснащено пескодувными и пескострельны-ми полуавтоматами мод. 310 для стержней весом 12 кг и мод. 400 для стержней весом 8—12 кг; производительность стержней 70 и 85 автоматов/ч.
Стержни весом 3,5—4 кг изготовляются в тёплых коробках на агрегате мод. 700 (80—90 съемов/ч).
Выбивка отливок производится на конвейере, а очистка — в галтовочных барабанах постоянного действия, установленных в подвальном помещении. Для сокращения длины охладительных конвейеров в первый раз в сталелитейном производстве применено двукратное водяное душирование отливок. Поступление всецело охлажденных отливок в галтовочные барабаны обеспечило удаление литников и прибылей в барабане и полностью ликвидировало операцию газовой отрезки доходов.
Отливки подвергаются нормализации в толкательных печах площадью пода 20 м2 с газовым обогревом, производительностью 2000 кг/ч. Отливки грунтуются окунанием.
Технико-экономические показатели цеха: съем с 1 м2 площади образовывает 2 т/год, брак— 1,75%, что практически втрое меньше, чем в среднем по сталелитейным цехам отрасли.
В цехе применена высокоэффективная вентиляция с очисткой воздуха. Вентиляцию снабжают 172 приточные и вытяжные совокупности. Приточные камеры размещены на антресолях и имеют секции для очистки, охлаждения либо подогрева воздуха.
Неспециализированный приток воздуха образовывает 1,4 млн. м3/ч, кратность воздухообмена в корпусе повышена до 6,5 раза в час. Удаляется воздушное пространство местными вентиляторами и вытяжными системами, установленными на кровле корпуса. Местная вытяжка установлена на заливке металла, выбивке, у дуговых печей и др.
Все ленточные конвейеры для удаления отработанной смеси оборудованы укрытиями с вытяжной вентиляцией, в местах пересылок с конвейера на конвейер предусмотрен отсос пыли.
Высокая освещенность цеха достигнута совмещением неспециализированного освещения ртутными лампами большого давления ДРЛ-400, ДРЛ-700 и местного — комфортно расположенными лампами накаливания.
На рис. 2, 3 продемонстрированы проектные ответы цехов массового производства отливок машин из стали и серого чугуна. Цехи— двухэтажные, шириной 72 м и длиной 300 м, без фонарей с расчетом на неестественную вентиляцию.
Выплавка серого чугуна производится в вагранках закрытого типа. В сталелитейном цехе для выплавки стали установлены элект-родугокые печи. В цехах предусмотрена автоматизация и комплексная механизация всех производственных и транспортных процессов.
Специализация мелкосерийного производства разрешает организовать поточное производство отливок, во многом схожее с крупносерийным. Современные специальные цехи с мелкосерийным характером производства отличаются от крупносерийных в основном большими площадями для подготовки и хранения модельной и стержневой оснастки.
Двухэтажный типовой чугунолитейный цех мелкосерийного производства отливок весом до 1000 кг продемонстрирован на рис. 4.
На втором этаже размещены по большей части производственные отделения. На первом — бытовые помещения, склады оснастки, грунтовки охлаждения и участки отливок, печи для сушки стержней, вентиляционные установки, экспедиция.
Плавильное отделение оборудовано вагранками. Для легирования и жидкого модифицирования рядом с вагранками установлены индукционные печи.
Изготовление отливок производится на двух поточных линиях. В обеих линиях употребляются пульсирующие вертикально замкнутые конвейеры. На первой линии изготовляются отливки весом до 500 кг в опоках размером 1500X1000 мм, на второй — отливки весом 500—1000 кг размером опок 2000Х 1600 мм.
Небольшие отливки формуются на шестипозиционных полуавтоматических линиях скользящей оснастки, где осуществляются в один момент все операции формовки. Для серийных отливок предусмотрены автомобили 846. Громадные отливки изготовляются на линии скользящей оснастки, оборудованной двумя пескомётом 236 и машинами. Модельная оснастка наборами подается с первого этажа.
Сборка форм производится на пульсирующих конвейерах-спутниках посредством кранов-балок и кранов. Для средних отливок предусматривается поверхностное упрочнение форм.
Рис. 2. Двухэтажный литейный цех массового производства отливок машин мощностью 65 000 т/год: замысел первого этажа: 1 — мастерская по ремонту оборудования, моделей, опок; 2 — склад моделей; 3 — склад стержневых коробок; 4 — грунтовочное отделение; 5 — склад отливок; 6 — бытовые и конторские помещения; замысел второго этажа: 1 — открытая эстакада для хранения чушкового чугуна; 2 — склад шихты; 3 — плавильное отделение; 4 — заливочное отделение; 5 — формовочное отделение; 6 — выбивно» отделение; 7 — смесеприготовительное отделение для форм; 8 — стержневое отделение; 9 — участок изготовления оболочковых стержней; 10 — смесеприготовительное отделение для стержней; 11 — очистное отделение
Рис. 3. Двухэтажный фасонно-сталелитейный цех массового производства отливок машин мощностью 65 000 т/год: 1 — ЖД путь; 2 — склад шихты; 3 — плавильное отделение; 4 — заливочный участок; 5 — формовочное отделение- 6 — выбивной участок; 7 — смесеприготовительное отделение для форм; 8 — стержневое отделение; 9 — смесеприготовительное отделение для стержней; 10 — участок первичной очистки отливок; 11 — термические печи; 12 — участок вторичной очистки отливок; 13 — участок изготовления оболочковых форм
Рис. 4. Двухэтажный типовой чугунолитейный цех мелкосерийного производства станочных подробностей весом до 1000 кг мощностью 35 000 т/год: 1 — отделение навески шихты; 2 — плавильное отделение; 3 — стержневое отделение; 4 — формовочное отделение для отливок весом до 500— 1000 кг- 5—формовочное отделение для отливок весом до 500 кг; 6 — смесеприготовительное отделение; 7 — очистки отливок и участок обрубки весом 500—100 кг; 8 — очистки отливок и участок обрубки весом до 500 кг; 9 — бытовые помещения; 10 — участок подготовки модельной оснастки для громадных отливок; И — участок подготовки стержневой оснастки; 12 — участок подготовки модельной оснастки для малых отливок; 13 — вентиляционные дыры; 14 — участок грунтовки отливок; 15 — участок охлаждения отливок; 16 — участок грунтовки отливок весом до 20—500 кг
Рис. 5. Двухэтажный типовой чугунолитейный цех мелкосерийного производства станочных больших отливок мощностью 25 000 т/год: 1 — отделение навески шихты; 2 — плавильное отделение; 3 — формовочное отделение конвейерного литья; 4 — формовочное отделение плацевого и кессонного литья; 5 — участок подготовки модельной оснастки; 6 — участок подготовки стержневой оснастки; 7 — смесеприготовительное отделение; 8 — обрубное отделение для конвейерного литья; 9 — обрубное отделение для плацевого и кессонного литья; 10 — отделение грунтовки; 11 — бытовые помещения; 12 — эстакада для отливок и опок с козловым краном; 13 — стержневое отделение
Залитые формы охлаждаются на двух линиях, расположенных одна над второй на первом этаже. Время остывания в форме отливок весом 500—1000 кг образовывает 8—16 ч.
Формы выбиваются на автоматических установках, приспособленных для опок с крестовинами. Выбитые отливки охлаждаются на конвейере с несколькими ветвями, проходящими по первому этажу поперек строения. По окончании охлаждения отливки тележкой конвейера поднимаются на второй этаж, где проходят выбивку стержней в гидрокамере и очистку.
Дальше отливки подвергаются дробеметной очистке,, зачистке наждаками и опускаются лифтом в отделение грунтовки, откуда передаются на склад.
На рис. 5 продемонстрирован частично двухэтажный типовой цех мелкосерийного производства больших отливок. Плавильное отделение оборудовано индукционными печами и вагранками для легирования и модифицирования чугуна.
У вагранок предусмотрен участок для заливки каркасов.
Формы для отливок весом 1000—2000 кг формуются пескометами на горизонтально замкнутой линии скользящей оснастки с кантователем. На линии изготовляются нижние и верхние полуформы. Модельная оснастка подается со склада, расположенного на первом этаже под стержневым отделением. Формы проходят подсушку.
заливка и Сборка производится на пульсирующем тележечном горизонтально замкнутом конвейере.
Охладительная ветвь конвейера проходит в галерее и запланирована на остывание отливок в форме в течение 24 ч. Выбитые отливки охлаждаются на особом конвейере пульсирующего типа.
Отливки весом более 2000 кг изготовляются на плацевом участке в кессонах и опоках. Набивка кессонов и форм осуществляется консольными пескометами. Сушка форм производится в камерных сушилах.
Залитые формы охлаждаются в камере предварительного остывания, установленной в обрубном отделении. Отливки проходят очистку в гидрокамерах и по окончании окончательной зачистки грунтуются и передаются на склад.
Стержневое отделение расположено на втором этаже. Стержни изготовляются посредством пескометов и пескодувных автомобилей, встроенных в линии скользящей оснастки, и из жидких самотвердеющих смесей. Тут же производится комплектовка стержней.
Цех запланирован на ступенчатый режим работы.