Зубчатые передачи
Зубчатые передачи имеются практически во всех сборочных единицах промышленного оборудования. С их помощью изменяют по направлению и величине скорости движущихся частей станков, передают от одного вала к второму упрочнения и крутящие моменты.
В зубчатой передаче перемещение передается посредством пары шестеренок. В практике меньшее зубчатое колесо принято именовать шестерней, а большее — колесом. Термин «зубчатое колесо» относится как к шестерне, так и к колесу.
Зубчатое колесо, сидящее на ведущем валу, именуют ведущим, а сидящее на ведомом валу — ведомым. Число зубьев зубчатого колеса обозначается буквой z.
В зависимости от обоюдного размещения геометрических осей валов зубчатые передачи бывают: цилиндрические, конические и винтовые. Шестеренки для промышленного оборудования изготовляют с прямыми, косыми и угловыми (шевронными) зубьями.
По профилю зубьев зубчатые передачи различают: эволь-вентные и циклоидальные. Кроме зубчатых передач с эволь-вентным зацеплением в редукторах используют передачу Новикова с круговым профилем зубьев. Передача Новикова разрешает использовать колеса с малым числом зубьев, соответственно, имеет солидное передаточное число и может передавать большие мощности.
Циклоидальное зацепление употребляется в часах и приборах.
Цилиндрические шестеренки с прямым зубом проходят службу в передачах с параллельно расположенными осями валов и монтируются на последних без движений либо подвижно.
Шестеренки с косым зубом используют для передачи перемещения между валами, оси которых пересекаются в пространстве, а во многих случаях и между параллельными валами, к примеру, в то время, когда в передаче должны сочетаться повышенная бесшумность и окружная скорость колёс их работы при громадных передаточных отношениях до 15:1.
Косозубые колеса монтируют на валах лишь без движений.
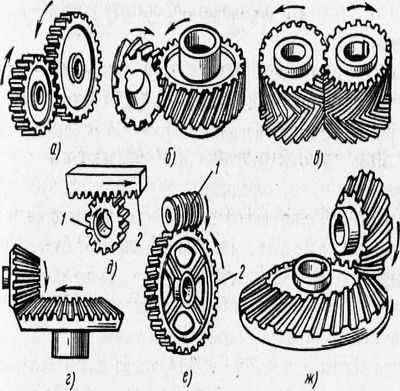
Рис. 1. Зубчатые зацепления: а — цилиндрическое с прямым зубом, б — то же, с косым зубом, в — с шевронным зубом, г — коническое, д — колесо — рейка, е — червячное, ж — с круговым зубом
Работа косозубых колес сопровождается осевым давлением. Осевое давление возможно устранить, соединив два косозубых колеса с однообразными, но направленными в различные стороны зубьями. Так приобретают шевронное колесо (рис.
1, в), которое монтируют, обращая вершину угла зубьев в сторону вращения колеса. На особых станках шевронные колеса изготовляют целыми из одной заготовки.
Конические зубчатые передачи различают по форме зубьев: прямозубые, косозубые и круговые.
На рис. 1, г продемонстрированы конические прямозубые, а на рис. 1, ж – круговые шестеренки. Их назначение – передача вращения между валами, оси которых пересекаются. Для пересекающихся осей используют кроме этого червячные передачи (рис.
1, е). Конические шестеренки с круговым зубом используются в передачах, где требуется бесшумность движения и особая плавность.
На рис. 1, д изображены рейка и зубчатое колесо. В данной передаче вращательное перемещение колеса преобразуется в прямолинейное перемещение рейки.
Элементы зубчатого колеса. В каждом зубчатом колесе (рис. 2) различают три окружности (делительную, окружность выступов, окружность впадин) и, следовательно, три соответствующих им диаметра.
Делительная, либо начальная, окружность дробит 3Уб по высоте на две неравные части: верхнюю, именуемую головкой зуба, и нижнюю, именуемую ножкой зуба. Высоту головки зуба принято обозначать ha, высоту ножки — hf, а диаметр окружности — d.
Окружность выступов – это окружность, ограничивающая сверху профили зубьев колеса. Обозначают ее da.
Окружность впадин проходит по основанию впадин зубьев. Диаметр данной окружности обозначают df.
Расстояние между серединами двух соседних зубьев, измеренное по дуге делительной окружности, именуется шагом зубчатогозацепления. Ход обозначают буквой Р. В случае если ход, выраженный в миллиметрах, поделить на число л = 3,14, то возьмём величину, именуемую модулем. Модуль высказывают в миллиметрах и обозначают буквой т.
Дуга делительной окружности в пределах зуба именуется толщиной зуба, дуга S1 — шириной впадины. В большинстве случаев, S = = Sx. Размер b зуба по линии, параллельной оси колес, именуется длиной зуба.
Радиальный зазор — малейшее расстояние между основанием впадины и вершиной зуба сопряженного колеса.
Боковой зазор — малейшее расстояние между нерабочими профильными поверхностями смежных зубьев, в то время, когда их рабочие поверхности находятся в контакте.
С модулем связаны все элементы зубчатого колеса: высота головки зуба ha = т, высота ножки зуба hf= 1,2т, высота всего зуба h = 2,2 т.
Зная число зубьев z, посредством модуля возможно выяснить диаметр делительной окружности зубчатого колеса d = zm.
Рис. 2. Схема зацепления в передачах цилиндрическими зубчатыми колесами
Формулы, благодаря которым возможно выяснить параметры цилиндрических шестеренок в зависимости от числа и модуля зубьев, приведены в табл. 5.
Тихоходные шестеренки изготовляют из чугуна либо углеродистой стали, быстроходные — из легированной стали. По окончании нарезания зубьев на зуборезных станках шестеренки подвергают термической обработке, дабы расширить их прочность и повысить стойкость против износа. У колес из углеро-
диетой CTa.‘irf поверхность зубьев улучшают химико-термическим методом — цементацией и позже закалкой. Зубья быстроходных колес по окончании термической обработки шлифуют либо притирают, Используется кроме этого поверхностная закалка токами высокой частоты.
Дабы зацепление было плавным и бесшумным, одно из двух колес в зубчатых парах в отдельных случаях, в то время, когда это разрешает нагрузка, делают из текстолита, древеснослои-стого пластика ДСП-Г либо капрона. Для облегчения зацепления шестеренок при включении при помощи перемещения по валу торцы зубьев со стороны включения закругляют.
Зубчатые передачи бывают открытые и закрытые. Открытые передачи, в большинстве случаев, тихоходные. Они не имеют корпуса для масляной ванны и иногда смазываются густой смазкой.
Закрытые передачи заключены в корпуса. Шестеренки закрытых передач смазываются либо в масляной ванне, либо струйной смазкой под давлением.
По быстроходности зубчатые передачи разделяются на следующие виды (м/с): очень тихоходные — v0,5, тихоходные — 0,5v3, среднескоростные — 3v15, скоростные — 15v40.
сборка изготовления передач и Точность колёс должны соответствовать госстандарту. Для цилиндрических, конических и червячных зубчатых передач установлено 12 степеней точности, обозначаемых в порядке убывания точности степенями 1 —12.
самые точные 1-я и 2-я степени являются резервными, поскольку современные возможности контроля и производства не смогут обеспечить изготовление правильных колес. 12-я степень кроме этого резервная, поскольку в соответствии с действующим ГОСТам шестеренки пока не выполняются неотёсаннее 12-й степени точности.
Громадное использование имеют зубчатые передачи 6, 7, 8 и 9-й степеней точности. Краткие характеристики самый распространенных зубчатых и червячных передач (6-й — 9-й степеней точности) приведены в табл. 6. Любая степень точности зубчатой передачи соответствует нормали кинематической точности, установленной ГОСТом, и контакта работы зубьев и плавности колеса.
Посадка шестеренок на валы ничем не отличается от посадки шкивов, исходя из этого ниже обрисована лишь проверка, регулирование зубчатых и червячных передач.
Главными техническими требованиями к зубчатым сборочным единицам являются следующие:
1. Зубья колес при проверке на краску должны иметь территорию касания не меньше 0,3 длины зуба, а по профилю — от 0,6 до 0,7 высоты зуба.
2. Радиальное торцовое биение колес не должно выходить за пределы, установленные техническими требованиями.
3. Оси валов сцепляющихся оси и колёс гнезд корпусов должны лежать в одной плоскости и быть между собой параллельными. Допускаемые отклонения указаны в технических условиях.
4. Между зубьями сцепляющихся колес нужен зазор, величина которого зависит от степени точности передачи и определяется по таблице.
5. Собранная сборочная единица испытывается на холостом ходу либо под нагрузкой. Она обязана снабжать соответствующую прочность для передачи мощности, умеренный нагрев и плавность хода подшипниковых опор (не более чем 323 К, либо 50 °С).
6. Передача обязана трудиться медлено и практически очень тихо.
Ниже обрисован порядок сборки некоторых сборочных единиц составных шестеренок.
Зубчатый венец устанавливают на центрирующий бурт А ступицы и предварительно закрепляют тремя-четырьмя временными болтами, имеющими меньший диаметр. Сборочную единицу контролируют на оправке на радиальное биение и венец закрепляют временными болтами.
Оставшиеся отверстия под болты в венце и ступице посредством кондуктора совместно развертывают и зенкуют, а после этого в эти отверстия вставляют обычные болты, а временные болты снимают и освободившиеся отверстия обрабатывают равно как и первые. По окончании установки обычных болтов во все отверстия зубчатое колесо совсем контролируют на биение. В тяжелонагруженных передачах затягивать болты целесообразно динамометрическим ключом, дабы на плоскостях фланцев создать силу трения, момент которой превосходил бы крутящий момент, передаваемый зубчатым колесом.
Зубчатый венец напрессовывают на диск ступицы с натя-том. Дабы уменьшить операцию и избежать вероятных перекосов, венец предварительно нагревают в масляной ванне либо особом индукторе т. в. ч. до 393-423 К (120-150 °С). После этого сверлят отверстия под стопоры.
Вместо стопоров часто крепление реализовывают заклепками. В этом случае отверстия сверлят полностью, устанавливают в них заклепки и расклепывают на прессах.
При установке зубчатых сборочных единиц на валах чаще всего видятся следующие погрешности: качание зубчатого колеса на шейке вала, радиальное биение по окружности выступов, неплотное прилегание и торцовое биение к упорному буртику вала.
На качание сборочную единицу контролируют обстукиванием напрессованного зубчатого колеса молотком из мягкого металла.
Диагностику на радиальное и торцовое биение сборочной единицы — зубчатое колесо с валом создают на призмах либо в центрах.
Рис. 3. Монтаж составных шестеренок и проверка на биение: а — составное зубчатое колесо, закрепленное болтами, б — закрепленное стопорами, в — схема проверка сборочной единицы вал — зубчатое колесо на радиальное и торцовое биение
Для этого вал укладывают на призмы, регулируют положение седла призмы винтами и устанавливают вал параллельно поверочной плите по индикатору. Во впадину колеса укладывают цилиндрический калибр, диаметр которого обязан составлять 1,68 модуля зацепления колеса. Стойку с индикатором устанавливают так, дабы ножка его вошла в соприкосновение с калибром и с натягом на один-два оборота стрелки.
Наряду с этим подмечают показание индикатора, после этого, перекладывая калибр через 2-3 зуба и поворачивая колесо, подводят калибр к ножке индикатора. Отмечают показание стрелки и определяют величину диаметрального биения. Допустимое биение диаметра и торца венца зубчатого колеса зависит от степени точности колеса по ГОСТу.
Торцовое биение контролируют индикатором.
Верное зацепление зубьев происходит при параллельности осей колес, отсутствии их скрещивания и сохранении расстояния между осями валов, равного расчетной величине. Параллельность размещения осей подшипников корпуса зубчатой передачи (рис. 4) контролируют штихмассом, индикатором и штангенциркулем.
Расстояние между осями подшипников контролируют контрольными оправками, устанавливаемыми в корпус. Расстояние измеряет либо между оправками, либо по их наружной поверхности.
Рис. 4. перпендикулярности проверки осей и Схема параллельности отверстий и валов контрольным валом и универсальным измерительным инструментом
Выяснив размеры либо на обеих сторонах, устанавливают непараллельность осей отверстий подшипников. Дабы добиться требуемого параллельности и межосевого расстояния, смещают корпуса подшипников. Непараллельность в вертикальной плоскости возможно выяснена при наложении уровня на любой из валов. Величина непараллельности в этом случае будет равна разности показаний уровня в угловых делениях.
В большинстве случаев цена деления уровней дается в долях миллиметра на 1 мм и для перевода показаний уровня в угловые секунды цену деления необходимо умножить на число 200.
К примеру, цена деления уровня 0,1 мм на 1 м соответствует 20 угловым секундам (0,1-200/1 =20”).
От передач точности и степени колёс устанавливают нормы бокового зазора. Главными являются нормы обычного гарантированного зазора (обозначаемого буквой X), компенсирующего уменьшение бокового зазора от нагрева передачи.
На рис. 5, а продемонстрирована проверка бокового зазора, которую в цилиндрических зубчатых колесах делают щупом либо индикатором. На валу одного из шестеренок крепят поводок, финиш которого упирают в ножку индикатора, установленного на корпусе сборочной единицы. Второе зубчатое колесо удерживают от проворачивания фиксатором. После этого поводок вместе с валом и колесом легко поворачивают то в одну, то в другую сторону, а это возможно сделать лишь на величину зазора в зубьях.
По показанию индикатора определяют боковой зазор. Мельчайший боковой зазор С„ показывают в технических условиях на сборку сборочной единицы. При межосевом расстоянии 320 — 500 мм для передач средней точности зазор данный должен быть не меньше 0,26 мм. Самый совершенно верно боковые зазоры измеряют посредством индикаторных приспособлений так называемым выносным способом.
Приспособления разрешают создавать замеры зазора в глухих передачах.
На рис. 5,б продемонстрировано одно из таких приспособлений. Оно складывается из крестовины, закрепленной на валу редуктора рукоятками, и стойки с индикатором. Стойку с индикатором ввертывают в хомут, закрепляют винтом к крышке редуктора.
При покачивании вала рукой до соприкосновения плоскости крестовины с ножкой индикатора, закрепленного на неподвижной крышке редуктора, определяют боковой зазор между зубьями. Малое колесо передачи должно быть неподвижным.
Рис. 5. Схема проверки бокового зазора индикатором: а — открытым методом, б — выносным
Замеренный зазор направляться отнести к диаметру начальной окружности зубчатого колеса, на валу которого закреплена крестовина.
Таким же образом контролируют боковой зазор и для других пяти положений крестовины, при повороте ее вместе с валом на угол 60°. По итогам замеров определяют колебание величины боковых зазоров и делают выводы о качестве собранной передачи. В зависимости от точности и модуля зубчатой передачи допустимая разность боковых зазоров образовывает 0,08—0,15 мм.
Рис. 6. Размещение пятен контакта при проверке на краску:
а — размеры контакта для оценки, б — одностороннее размещение пятна (перекос колеса на зуборезном станке либо перекос отверстий в корпусе редуктора, в – громадный зазор по всему венцу (мало либо громадно межосевое расстояние), г — недостаточный зазор по всему венцу (излишняя либо недостаточная толщина зуба одного либо обоих колес)
Неправильное неправильное место и пятно касания размещения на зубьях являются следствием погрешностей, появившихся при сборке и обработке колес, валов, корпусов редукторов, подшипников. На рис. 6,б отпечаток краски расположен односторонне.
Обстоятельством неправильного пятна контакта возможно перекос колеса на зуборезном станке либо перекос отверстий в корпусе редуктора.
В случае если зуб колеса утоплен со стороны торца и при поворачивании на 180° положение не изменяется, то, следовательно, перекошена ось отверстия в корпусе. Эту погрешность ликвидируют запрессовкой новой втулки и растачиванием ее либо перепрессовкой пальца зубчатого колеса, если оно посажено на палец.
На рис. 6, в продемонстрирован через чур большой зазор по всему венцу. Вероятные обстоятельства: межосевое расстояние в корпусе недостаточное либо через чур большое. Ликвидируют погрешность
перепрессовкой втулок в корпусе и их повторным растачиванием.
Недостаточный зазор по всему венцу продемонстрирован на рис. 6, г. Вероятные обстоятельства малой величины зазора: излишняя либо недостаточная толщина зуба у одного либо у обоих колес. В этом случае заменяют колеса либо применяют корпус с другим межосевым расстоянием.