Cпециальные способы изготовления отливок
В современном литейном производстве активно используются прогрессивные особые методы литья: в оболочковые формы, по выплавляемым моделям, в железные формы (кокили), центробежное литье, литье под давлением. Главным преимуществом их если сравнивать с литьем в песчаные формы есть то, что они позволяют приобретать отливки более правильные по конфигурации и размерам, с меньшей шероховатостью поверхностей, в следствии чего значительно уменьшается, а в некоторых случаях всецело исключается их механическая обработка. Помимо этого, эти методы разрешают максимально механизировать и автоматизировать технологические процессы и тем самым повысить производительность труда.
1. Литье в оболочковые формы
Данный прогрессивный метод изготовления отливок был в первый раз внедрен в 1953 г. на Кировском заводе, а после этого и на многих вторых фирмах Ленинграда. На данный момент в специальном цехе Тихвинских производств объединения «Кировский завод» более 40 наименований подробностей из чугуна и стали для трактора «Кировец» изготовляются методом литья в оболочковые формы.
Солидный вклад в развитие этого прогрессивного метода получения отливок, в его механизацию внес ленинградский проектно-технологический университет ВПТИэлектро.
области применения и Сущность процесса. Литьем в оболочковые формы изготовляют разные детали двигателей, насосов, вентиляторов, текстильных автомобилей, коленчатые валы и др. Большие габаритные размеры отливок — до 1 м, масса — до 200 кг.
Сущность процесса основана на свойстве термореактивных смол, входящих в состав песчано-смоляных смесей, скоро и необратимо отверждаться под действием тепла нагретой до температуры 200—250 °С модельной оснастки.
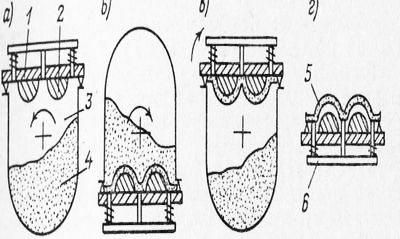
Рис. 1. Схема изготовления оболочковых полуформ.
По окончании соответствующей выдержки (в течение 20 с либо пара более, в зависимости от требуемой толщины оболочки) термореактивная смола плавится и связывает отдельные зерна песка, образуя на плите и моделях полу-отвержденную оболочку. По окончании возвращения бункера в исходное положение не успевшая прогреться смесь ссыпается в бункер (рис. 1, в).
Модельная плита открепляется и вместе с появившейся оболочкой на 1—2 мин помещается в электрическую печь, нагретую до температуры 325—375 °С, для окончательного отверждения оболочки.
Остывшая оболочка посредством толкателей снимается с модельной плиты и спаривается со второй оболочковой полуформой, изготовленной подобным методом. Оболочковые полуформы скрепляются скобами, струбцинами либо — при массовом производстве — склеиваются разными клеями на особом оборудовании. Собранные формы устанавливают в железный короб, для упрочнения их засыпают железной дробью и подают на заливку.
Материалы для оболочек. Для изготовления оболочковых форм используют пески, термореактивные смолы, увлажнители, растворители, разделительные составы, различные добавки и клеи.
Пески. В большинстве случаев употребляются обогащенные либо природные кварцевые пески классов 061 К, 062К, ОбЗК и 1К зернистостью 02А (Б), 016А(Б) либо 01А(Б). Для важных отливок используют кроме этого цирконовые пески.
Рис. 2. Схема установки под заливку собранных полуформ в железных коробах.
Термореактивные смолы. Связующими материалами являются фенолформальдегидные смолы: ПК-Ю4 — в виде порошка, СФ-010 и СФ-015— в виде чешуек. Порошок ПК-104 самый универсален.
Он употребляется в песчано-смоляных смесях механического смешения при тёплом плакировании и холодном. Смолы СФ-010 и СФ-015 используются лишь при тёплом плакировании.
Плакирование —покрытие зерен песка узкой пленкой связующего — реализовывают с целью его улучшения и экономии качества смесей, и для возможности их применения при пескодувных и пескострельных процессах.
Увлажнители помогают для предотвращения расслоения смеси, и ее пыления в ходе применения. В большинстве случаев это керосин либо веретенное масло, которое вводят в смесь числом 0,3—0,5% от ее массы.
Разделительные составы используют для устранения прилипания отвержденных оболочек к поверхности модельной оснастки. На поверхность оснастки их наносят кисточкой либо пульверизатором.
Песчано-смоляные смеси смогут быть механическими и плакированными. Первые складываются из песка, увлажнителя и порошкообразной смолы. Все составляющие смеси перемешиваются в лопастных смесителях либо бегунах.
Плакированные смеси готовятся несколькими методами: холодным, теплым и горячим. При холодном плакировании сухой песок смешивают со растворителем и смолой в один момент, после этого вводят добавки и продувкой холодным воздухом удаляют растворитель. Теплое плакирование отличается от холодного тем, что песок предварительно подогревают до температуры 80 °С либо смесь продувают не холодным, а нагретым до 70—80 °С воздухом.
При тёплом плакировании предварительно нагретый до температуры.
Использование оболочковых форм действенно лишь при автоматизации и комплексной механизации технологического процесса.
2. Литье по выплавляемым моделям
Литье в формы, приобретаемые по выплавляемым моделям, — один из самый древних способов изготовления отливок. Он использовался для отливки скульптур, монументов, украшений, предметов орудий труда и домашнего обихода. В индустрии данный метод начал употребляться в сороковые годы для того чтобы из сплавов, не поддающихся обработке резанием и давлением.
На данный момент — это высокомеханизированный и автоматизированный процесс, обширно используемый в разных отраслях индустрии, среди них и на ленинградских фирмах.
На заводе турбинных лопаток в первый раз в стране был налажен выпуск литых лопаток для паровых и газовых турбин. Прогрессивный метод внедрен в объединении имени Карла Маркса, на заводе имени Воскова и последовательности вторых фирм. Этим методом изготовляют отливки массой от 10 г до 100 кг с минимальной толщиной стенок 0,7—1 мм.
Точность размеров литых заготовок соответствует 5—6-му классам, а шероховатость поверхности — 4 6-му классам, что разрешает отливать заготовки с минимальными припусками (0,2—0,7 мм) под полировку и шлифовку.
Сущность процесса содержится в следующем. По разъемным пресс-формам из легкоплавких модельных составов, в большинстве случаев складывающихся из парафина, стеарина, буроугольного и торфяного других компонентов и восков, делают литниковые системы и разовые модели. По окончании затвердения и полного застывания их извлекают из пресс-формы и собирают в модельные блоки. На рис. XII 1.3, а продемонстрирован таковой блок, собранный на железном стояке из отдельных модельных звеньев, с литниковой воронкой.
Нижнюю часть стояка закрывают колпаком (из того же состава), припаиваемого к нижней модели звена.
При серийном и мелкосерийном производстве метод сборки модельных наборов другой. питатель и Литниковую чашу-шлакоуловитель изготовляют по пресс-форме в основном из возврата модельного состава. На моделях зачищаются посадочные торцы и швы. Нагретый паяльный ноле (узкую железную пластинку) накладывают на питатель, а поверх ножа устанавливают модель.
По окончании оплавления участка на питателе и посадочном торце модели нож удаляют и модель припаивают к питателю.
Рис. 3. Схема собранного модельного блока.
На собранные так модельные блоки наносят пара (три-четыре) слоев огнеупорного покрытия, любой из которых складывается из слоя огнеупорной суспензии, обсыпанной кварцевым песком. Огнеупорная суспензия состоит приблизительно из 35% (по массе) гидролизованного этилсиликата и 65% пылевидных огнеупорных материалов. Этилсиликат — эфир ортокремниевой кислоты (C2H50)4Si — играет роль связующего благодаря свойству в присутствии воды выделять гель — кремнезем в виде студенистого осадка, обволакивающего и скрепляющего зерна кварца в монолитную массу.
В зависимости от материала модели удаляют из оболочки тёплой воде, посредством пара либо нагретого воздуха.
Главные материалы для того чтобы изготовить модели и формы. В зависимости от требований, предъявляемых к точности размеров отливок и к шероховатости поверхностей, их изготовляют из разных модельных составов: легкоплавких — на базе восков, тугоплавких — на базе смол и солевых — на базе карбамида (технической мочевины).
отливки и Крупные отливки высокой точности, какими являются, к примеру, турбинные лопатки, делают из модельного состава КС 80-20, а менее важные при механизированном ходе — из составов ПС 50-50, Р-3 и др.
Для образования керамической формы, владеющей термической стойкостью при заливке и прокалке, используют следующие формовочные материалы:
— для того чтобы — пылевидные материалы — неестественный и плавленый кварц, микропорошки электрокорунда и др.;
— для обсыпки блоков по окончании окунания в суспензию — кварцевые пески, электрокорунд, циркон, силлиманит и др.
Наполнителем помогают кварцевый песок, шамотная крошка и др.
При приготовлении суспензии в качестве связующих применяют этилсиликат марок 32 и 40 с содержанием Si02 соответственно 32 и 40%, а в качестве растворителя при его гидролизе — этиловый и гидролизный спирт.
Модели изготовляют по железным пресс-формам (из алюминиевых сплавов и стали), у которых рабочие поверхности имеют высокую низкую шероховатость и размерную точность.
Сейчас процессы литья по выплавляемым моделям механизированы и автоматизированы. Так, автоматизированы операции изготовления моделей, нанесения покрытий, выплавки моделей из оболочек, сушки, формовки, прокалки.
3. Литье в железные формы-кокили
Литье в железные формы — прогрессивный метод получения небольших и средних отливок из алюминиевых и магниевых сплавов, чугуна, стали в серийном и массовом производстве.
Если сравнивать с литьем в песчаные формы он имеет последовательность преимуществ: трудовые затраты на изготовление отливок уменьшаются более чем в 2 раза, их себестоимость понижается на 15—25%, съем отливок с формовочных площадей возрастает более чем в 2 раза, брак уменьшается многократно.
Сущность процесса. Для получения фасонных отливок сплав заливают в железные (преимущественно из стали и чугуна) формы, каковые выдерживают от нескольких сотен до нескольких десятков тысяч заливок.
экономичность процесса и Качество отливок сильно зависят от технологичности их конструкции, которая должна иметь несложную конфигурацию, что облегчает изготовление железной формы без резких переходов от толстых стенок к узким, без выступающих частей, кромок и острых – углов, углублений и поднутрений, мешающих удалению и усадке отливки из форм; иметь нужную толщину стены, снабжающую возможность заполнения формы.
Типы железных форм. В зависимости от конструкции литых подробностей, принятой технологии и материала изготовления отливок железные формы смогут, быть: неразъемными (вытряхными), разъемными —с горизонтальным разъемом, с несколькими разъемами, с вертикальным разъемом, со сложной плоскостью разъема.
Заготовки железных форм значительно чаще делают из серого чугуна СЧ18-36, высокопрочного — марки ВЧ50-2, и ц3 стали марок 25Л и 35Л.
Цапфы, ручки и шайбы изготовляют из углеродистых сталей стержни — из углеродистой марок У7 — У10, а теплоотводящие вставки — из меди марки М-1.
Рис. 4. Типы литейных железных форм.
В зависимости от требований к шероховатости рабочих и точности размеров поверхностей формы они смогут быть взяты литьем либо механической обработкой. Последняя обходится существенно дороже и осуществляется при литье из цветных сплавов.
Для повышения стойкости форм на их рабочие поверхности наносят защитные покрытия, каковые кроме этого уменьшают отбел отливок из серого чугуна. При изготовлении чугунных и металлических отливок на рабочие поверхности наносят облицовочный слой и после этого окрашивают их; при отливках из легких сплавов достаточно одной окраски.
Для увеличения стойкости форм их подогревают до температуры 200 °С при отливках из бронзовых и алюминиевых сплавов, до 250 °С — из магниевых и до 300 °С — чугунных. По окончании нанесения и подогрева форм на них защитных покрытий приступают к их заливке и сборке.
Для автоматизации и механизации процессов изготовления отливок в железных формах обширно используют станки с ручным и механическим приводами, личные полуавтоматические автомобили, автоматизированные линии и карусельные станки
4. Центробежное литье
При центробежном литье заливка жидкого сплава производится в быстровращающиеся железные формы, наряду с этим сплав под действием центробежных сил оттесняется к стенкам формы. Наружная поверхность отливки оформляется стенками формы-изложницы, а внутренняя образуется под действием центробежных сил и сил тяжести.
Рис. 5. Схемы центробежного литья.
Появляющиеся при вращении жидкого сплава в изложницах центробежные силы содействуют хорошему заполнению форм сплавом, уплотняют ее структуру и в один момент перемещают на внутреннюю поверхность более легкие составляющие — шлаковые и газовые включения.
Автомобили для центробежного литья строятся с горизонтальной, вертикальной, а время от времени с наклонной осями вращенйя.
В автомобилях с горизонтальной осью вращения железная форма заполняется жидким сплавом из ковша по желобу. Сплав затвердевает в виде полой цилиндрической заготовки.
На автомобилях с вертикальной осью вращения (рис. 5, б) приобретают пустотелые заготовки в виде кольца. Их внутренняя поверхность не имеет строго цилиндрической формы, поскольку под влиянием сил тяжести толщина стенок внизу получается пара большей, чем вверху, исходя из этого высота литых заготовок ограничена.
Фасонные отливки с полостями изготовляются посредством стержней, установленных в формы.
Центробежный метод литья имеет последовательность преимуществ: возрастает выход годного благодаря отсутствию необходимости в литниковой совокупности, среди них и прибылях, увеличивается уровень качества отливок, снижатся брак и т. п.
Рекомендуемая частота вращения формы при производстве отливок втулок, труб и т. п.
Центробежный метод литья во многих случаях ведет к резкому сокращению брака отливок. Так, на ленинградском заводе турбинных лопаток рабочее колесо турбонаддува диаметром 400 мм и массой 19 кг, воображающее собой ступицу с 26-ю лопатками, ранее изготовляли по выплавляемым моделям, наряду с этим узкие кромки лопаток сплавом не заполнялись, в следствии чего брак Достигал недопустимых пределов, При новой технологии, сохранив
На ленинградских фирмах имеется опыт отливки этим методом толстостенных втулок из бронзовых сплавов диаметром до 1 м, длиной до 3,5 м и массой до 7,5 т, и больших маслот из легированной стали.
5. Литье под давлением
Данный самый прогрессивный метод получения литых заготовок по производительности, точности размеров отливок, шероховатости поверхности существенно превосходит все другие. Его используют для того чтобы из цветных сплавов на базе цинка, алюминия, меди и магния. Обширно употребляется он в при-боро- и автомобилестроении, правильном машиностроении, в оптико-механической индустрии и последовательности вторых отраслей при серийном и массовом производстве.
Наличие на данный момент богатого выбора автомобилей для литья под давлением, усовершенствованных пресс-форм, вентилирования подвода и методов сплава пресс-форм позволяет изготовлять сложные заготовки с точностью размеров по 3—5-му классам и шероховатостью поверхностей по 5—8-му классам. Заготовки возможно приобретать с готовыми отверстиями, резьбой, накаткой, надписями и цифрами. Мельчайшая толщина стенок литых заготовок образовывает 0,6 мм.
Сущность процесса содержится в том, что жидкий сплав поступает в железную пресс-форму под давлением, которое осуществляется на особых автомобилях с горизонтальной и вертикальной камерами прессования.
В полость цилиндра ложкой заливается сплав, что поршнем запрессовывается в рабочую полость пресс-формы через литниковый канал. По окончании затвердевания сплава подвижная полуформа вместе с отливкой
Я литниковым остатком отходит и перемещается , пока упор не встретит на своем пути ограничитель хода. Посредством особых толкателей отливка удаляется нз пресс-формы. Неподвижная полуформа с плитой остается наряду с этим на месте. По окончании окончания рабочего цикла прессующий поршень возвращается в исходное положение
Технологические изюминки процесса. Для процесса литья под давлением свойственны высокая скорость прессования и громадное удельное давление на сплав в пресс-форме. На уровень качества отливки влияют марка сплава, конструкция заготовки, качество и конструкция поверхности пресс-формы, и самой пресс и температура сплава-формы в момент заливки.
Рис. 6. Схема процесса литья под давлением.
Сплавы. При литье под давлением к сплавам предъявляют следующие главные требования: жидкотекучесть при маленьком перегреве (на 15—20 °С выше температуры плавления); минимальная усадка; достаточная прочность к моменту удаления заготовки из пресс-формы. Этим требованиям отвечают сплавы на базе совокупностей: алюминий — кремний марок АЛ2, АЛ9 и др.; алюминий — кремний — медь марок АЛЗ, АЛ5 и др.; алюминий — магний марок АЛ8, АЛ 13, АЛ27 и др.
Наилучшими литейными особенностями владеют цинковые сплавы. К ним относятся сплавы на базе цинка, меди и алюминия. Из магниевых сплавов самый удовлетворяют требованиям литья под давлением сплавы марок МЛ5 и МЛ6. Для предохранения магниевого сплава от контакта с воздухом и создания окисной пленки используется присадка бериллия числом до 0,01%.
Из бронзовых сплавов громаднейшее распространение взяли сплавы меди с цинком — бронзы марок ЛК80-ЗЛ и ЛС59-1ЛД.
Автомобили для литья под давлением. Для литья сплавов с низкой температурой плавления на базе цинка, свинца и олова используют автомобили с тёплой камерой прессования, а для литья всех сплавов — автомобили с холодной горизонтальной либо вертикальной камерой прессования. Горизонтальная камера прессования более эргономична, разрешает упростить ее эксплуатацию и конструкцию машины.