Cушка, отделка и сборка форм
В сырых формах изготовляют в основном тонкостенные отливки. При применении отличных формовочных достаточной квалификации и материалов формовщика в сырые формы возможно отливать большие подробности: чугунные — массой до 1500 кг и металлические — до 800 кг.
Стержни, находящиеся на протяжении заливки в более тяжелых условиях,‘чем формы, в большинстве случаев, подвергают сушке. Помимо этого, стержни из смесей на органических связующих должны быть подвергнуты тепловой обработке для полимеризации связующего.
При изготовлении больших отливок большой высоты либо сложной конфигурации с выступающими частями сырая форма не в состоянии противостоять давлению громадного количества заливаемого сплава. Прочность ее в этом случае недостаточна, а газопроницаемость мелка, что не разрешает вовремя удалить образующиеся на протяжении заливки газы и водяные пары. Высушенные стержни и формы имеют высокие прочностные особенности, они способны выдерживать без деформации большие гидростатические давления сплава и не разрушаться при механических действиях (толчках при транспортировке, ударах сплава при заливке).
1. Сущность процесса сушки
Главная цель сушки — улучшить прочностные особенности стержней и форм и повысить их газопроницаемость.
Формы, подлежащие сушке, в зависимости от их состава и назначения содержат 6—9% жидкости. Для удаления жидкости из стержней и форм нужно подвести к ним тепло от какого-либо источника (к примеру, газ). Под действием тепла с стержней и поверхности форм начинает испаряться влага.
По мере ее испарения из внутренних слоев к гаружным поступают новые порции жидкости, и без того практически До полного ее испарения.
Для полной и стремительной сушки формы и стержни должны омываться газами равномерно со всех сторон. Удаление жидкости в форме происходит в основном через ее верхний разъем и частично через низ. Железные стены опок не пропускают газы. Дабы уменьшить и ускорить сушку, стены опок делают с отверстиями.
С данной же целью полуформы устанавливают на прокладках. По образующимся зазорам газы смогут циркулировать и обогревать низ формы. В негативных условиях находится низ стержней, каковые сушатся на плитах, исходя из этого плиты должны иметь отверстия.
2. Сушка форм
Главным связующим для формовочных смесей чугунного и металлического литья есть глина. Будучи намочена водой, глина делается пластичной и благодаря связующей свойству придает нужную прочность сырой форме. При сушке до температуры 450—500 °С глина не теряет связующих особенностей и увеличивает прочность высушенной формы.
Для газопроницаемости формы и увеличения податливости в кое-какие формовочные смеси вводят органические вещества — древесные опилки и др. На протяжении сушки из них испаряется влага и удаляются летучие вещества, а образующиеся поры повышают газопроницаемость формы.
Перед сушкой формы покрывают противопригарной краской, наносимой пульверизатором либо кистью.
продолжительность и Температура сушки форм зависят от вида и размеров отливок.
3. Сушка стержней
Стержневые смеси в зависимости от назначения, размеров рожней, требуемой прочности и газопроницаемости содержат Сязличны’е связующие. продолжительность и Температура сушки по различному воздействуют на особенности смеси. Исходя из этого для каждого вида связующего нужно выбрать собственный режим сушки.
Типы сушил
По принципу работы различают сушила периодического и не-рерывного действия. К первым относят камерные стационарные Ушильные^ установки и переносные сушила, ко вторым — различ-е конвейерные и туннельные сушильные печи.
Переносные сушила. применение и Разработка быстросохну-формовочных смесей позволили не только сократить подолжительность цикла изготовления формы за счет уменьшения времени сушки, но и отказаться от применения камерных сушильных печей.
Литейные формы из быстросохнущих формовочных смесей не нуждаются в сквозной сушке. Для получения годной отливки достаточно просушить только поверхностный слой формы — на глубину 20—50 мм.
направляться стремиться к максимально допустимой температуре, снабжающей кратковременность процесса подсушки без повреждения формы.
При изготовлении форм для средних и больших чугунных отливок массой 8 т и более в состав облицовочной смеси вводят связующие СБ либо СП. Перед подсушкой поверхность формы покрывают краской на графитовой базе. При температуре 260—290 °С глубина подсушенного слоя через 30 мин образовывает 10 мм, а через 60—90 мин —30 мм.
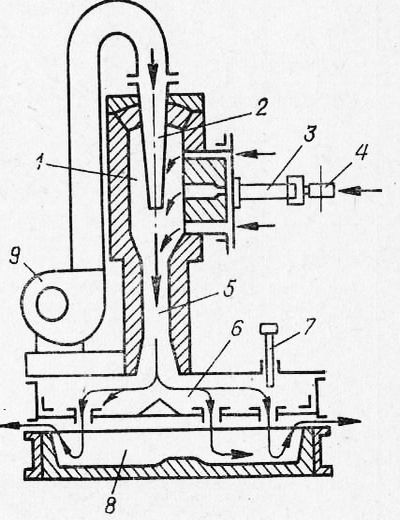
Рис. 1. Схема газового переносного сушила.
При изготовлении форм для металлических отливок используют быстросохнущую смесь на базе жидкого стекла. До подсушки поверхность формы покрывают краской на базе маршалита. При температуре 270—300 °С через 45—70 мин толщина подсушенного слоя образовывает около 25 мм.
самый рациональным видом горючего для переносных сушил есть газ. Он позволяет уменьшить габариты установки, упростить ее эксплуатацию. Схема переносного сушила, трудящегося на газообразном горючем, продемонстрирована на рис. 1.
На форму, предназначенную для подсушки, устанавливается короб распределительной камеры. В верхней части короба смонтирован газовый смеситель, в котором находится топка.
Рис. 2. Установка для сушки инфракрасными лучами: 1 — форма; 2 — лампа; 3 — патрон; 4 — ограничитель продвижения форм; 5 — рефлектор; 5 —рама сушильной установки; 7 — механизм подъема рамы.
Рис. 3. Схема горизонтального конвейерного сушила.
Использование переносных коксовых сушильных печей должно быть ограничено, поскольку при их работе в воздух цеха выделяются газообразные продукты горения, ухудшающие санитарно-гигиенические условия труда.
Сушка инфракрасными лучами. Некое распространение взяла подсушка форм инфракрасными лучами от зеркальных ламп мощностью 250—500 Вт. Лампы являются стеклянную колбу параболической формы, внутренняя поверхность которой покрыта узким слоем серебра и является отражателем.
В фокусе зеркала закреплена вольфрамовая нить, температура накала которой достигает 2200 °С.
Формы устанавливают на рольганг и перемещают под раму сушильной установки. Рама выполнена в виде древесной решетки, на которой смонтированы патроны типа «Голиаф» для ламп мощностью 500 Вт. опускание и Подъём рамы осуществляются по стойкам особым механизмом.
На таковой установке создают поверхностную подсушку форм размером 1200X1000 мм и высотой до 600 мм. Подсушка поверхностного слоя на глубину 15—20 мм продолжается приблизительно 40—50 мин.
Рис. 4. Схема вертикального конвейерного сушила.
Сушка форм может производиться в любом месте цеха конкретно на плацу — установка легко переносится и без особенных приспособлений может включаться в сеть цеха.
Сушила постоянного действия подразделяются на горизонтальные и вертикальные. Они предназначены для сушки стержней в крупносерийном и массовом производстве.
Горизонтальные конвейерные сушила (рис. 3). Рабочая камера сушила выполнена в виде коридора, где с определенной расчетной скоростью движется подвесной цепной конвейер, на котором подвешены сушильные этажерки с полками для установки стержней. Сушило делится на три территории: I — подогрев, IIсушка и III — охлаждение. Температура сушки устанавливается в зависимости от связующего и колеблется от 220 до 240 °С.
Установка имеет вентиляционную совокупность, снабжающую рециркуляцию отработанных газов и перемешивание их с тёплыми газами в смесительной камере.
Вертикальные конвейерные сушила. В литейных цехах серийного и массового производства для сушки небольших стержней используют вертикальные конвейерные сушила (рис. 4).
Сушило выполнено в виде каркаса, покрытого металлическими панелями, заполненными теплоизоляционным материалом. Внутреннюю сторону панелей покрывают жаростойким, а наружную — алюминиевым лаком. На валах закреплены звездочки, через каковые перекинуты нескончаемые цепи, несущие полки со стержнями.
Полки связаны посредством шарниров и вольно покачиваются, а под влиянием нагрузки постоянно находятся в вертикальном положении. Нижний вал звездочек приводится в перемещение через редуктор электродвигателем. В зависимости от режима сушки скорость перемещения цепи может регулироваться в широких пределах.
В большинстве случаев она образовывает 0,25—0,5 м/мин.
Газы из топки, поднимаясь вверх, прижимаются к разделительной перегородке и, перейдя в левую сторону сушила, отсасываются в дымовую трубу.
Загрузка стержней, размещенных на особом сушителе, производится через окно, где температура не превышает 35— 40 °С. По мере подъема вверх стержни последовательно поступают в области более больших температур. Под сводом камеры и в верхней части левой стороны сушила температура достигает 230— 250 °С, а у окна, через которое производится выгрузка стержней, она понижается до 65 °С.
5. Химическое отверждение стержней и форм
Формовочные и стержневые смеси на жидком стекле владеют свойством скоро отверждаться при продувке либо обдувке их углекислым газом. Процесс химического отверждения смеси протекает за счет действия газа на силикат натрия, являющегося базой жидкого стекла, по реакции:
Из данной реакции видно, что при введении в жидкостекольную смесь углекислого газа происходит образование геля и углекислого натрия кремниевой кислоты. Пленки геля равно как и связующего, равномерно обволакивают зерна песка, связывая их в прочную сухую массу. Рабочий слой формы либо стержня наряду с этим получает достаточную прочность, дабы выдержать давление заливаемого сплава.
Рис. 5. Схемы продувки форм углекислым газом.
Небольшие стержни в большинстве случаев продувают углекислым газом партиями под зонтом. Для этого под зонт 2 раза подают углекислый газ в течение 20—30 с с перерывом в 2—3 мин. крупные стержни и Средние продувают конкретно в стержневых коробках, благодаря чему исключается возможность их деформации.
Схемы продувки форм углекислым газом продемонстрированы на рис. 5. Самый распространенной есть схема, приведенная на рис. 5, а. Продувка формы тут осуществляется по окончании удаления модели. Но при необходимости обеспечить более правильные размеры отливки продувку создают до удаления модели.
Данный метод, при котором подвод углекислого газа в форму осуществляется через совокупность резиновых трубок (рис. 5, б), шланг и коллектор, создан литейщиками объединения «Невский завод» имени В. И. Ленина.
Длительность продувки форм зависит от их площади. Новые методы стержней и отверждения форм в оснастке без тепловой обработки и продувки были рассмотрены выше.
6. сборка и Отделка форм
Сборка форм складывается из следующих операций: подготовки площадки для сборки, окончательной отделки форм, покрытия их противопригарными красками, устройства вентиляционных каналов, крепления и установки стержней, контрольного и окончательного накрывания форм, установки литниковых, выпорных и прибыльных их оформления и чаш, крепления форм.
Подготовка площадки для сборки. Для установки нижней половины формы площадку шепетильно разрыхляют, а при больших формах в ней делают поперечные борозды для свободного удаления газов. По окончании установки полуформу шепетильно притирают к поверхности площадки.
Отделка. При формовке по сырому все поврежденные участки формы исправляют методом отделки и нанесения смеси формовочным инструментом и прошпиливают. Запрещено допускать переуплотнения участков, поскольку это может позвать вскипы.
Для этого в знаковой части формы гладилкой вырезают углубления и устанавливают толщину просушенного слоя. Умелые формовщики контролируют уровень качества просушки простукиванием формы. Затем переходят к установке предварительно подготовленных стержней. В случае если символы не снабжают устойчивого положения стержня, то для его дополнительного крепления используют жеребейки.
При единичном и мелкосерийном “производстве размеры формы осуществляют контроль в ходе сборки древесными шаблонами, линейками и вторым несложным инструментом. При серийном и массовом производстве контроль осуществляется шаблонами и кондукторами.
При больших и сложных формах создают контрольное перекрытие. По разъему формы прокладывают глиняный валик диаметром 3—5 мм, а на контролируемые места стержней укладывают комки глины (мушки). Такие же комки располагают в местах, каковые при установке стержней не смогут быть проверены инструментом. По окончании установки всех стержней полости закрывают паклей и полуформу накрывают.
Под действием массы верхней стержней и полуформы комки и валики из глины сдавливаются и при удалении стержней и раскрытии формы возможно делать выводы о высоте жеребеек и толщине стенок для дополнительного крепления стержней. Затем форму шепетильно очищают, при необходимости устанавливают жеребейки и заканчивают сборку.
При формовке по сырому в плоскости разъема нижней полуформы гладилкой делают около полости формы риску, наряду с этим смесь приподнимается, образуя гребешок, что при накрытии верхней полуформы сдавливается, заграждая проход сплава по разъему. При формовке по сухому около полости формы прокладывают глиняный валик либо асбестовый шнур, сдавливаемый верхней полуформой.
Последние операции сборки — исполнение литниковых чаш и наростков для выпоров. При применении сухих готовых литниковых чаш, оформленных в обечайке, они устанавливаются на подсыпку и хорошо соединяются с поверхностью формы. Чаша для выпора должна быть на одном уровне с литниковой чашей. При исполнении чаш конкретно при сборке в литниковые и выпорные отверстия опускают стояки, зазоры заделывают паклей, устанавливают обечайки на подсыпку и формуют чаши.
Дабы предохранить поверхность верхней формы от обгррания, все выпоры закрывают глиняными лепешками.
По окончании крепления либо нагружения форма готова к заливке.