Формирование физико-механических свойств доменного сырья для печей большого объема
Этому вопросу до недавнего времени не уделялось достаточного внимания. Но с вводом замечательных доменных печей и интенсифика-цей выплавки чугуна требования к физико-механическим особенностям шихтовых материалов возросли и изучения в этом направлении расширились. На данный момент оптимизация металлургических особенностей доменного сырья по прочности и крупности есть одним из определяющих факторов в технологии выплавки чугуна на всех современных доменных печах.
Выполненные ранее изучения по разработке требований к насыпной массе шихты базировались, в большинстве случаев, на физико-механических особенностях ее компонентов в холодном состоянии, не учитывая их поведения при больших температурах под действием газовой среды. Помимо этого, недостаточная роль отводилась стабилизации прочностных черт доменного сырья в ходе его подготовки к доменной плавке.
Замечательные доменные печи оборудованы транспортерными совокупностями подачи сырья и часть операций по формированию нужных шихтовых материалов может выполняться на конвейерном тракте. Вследствие этого в базу разработки подготовки сырья для замечательных доменных печей должен быть положен принципиально новый подход, учитывающий поведение материалов в ходе транспортировки, загрузки, опускания в доменной печи, в особенности при повышенных температурах.
С целью этого на ЧерМК совместно с ЛПИ им.Калинина и ИЧМ (г. Днепропетровск) выполнили комплекс работ по оценке физико-механических особенностей кокса и железорудных материалов в холодном и нагретом состоянии, и изучению трансформаций наиболее значимых окатышей и характеристик агломерата при восстановительно-тепловой обработке в высокотемпературных территориях доменной печи.
Кокс
Изучили кокс, полеченный из печорских (85%) и кузнецких (15%) углей. Печорские угли представлены марками Ж10, Ж18 и К14, кузнецкие – марками ОС и СС + Кг. Оценка физико-механических особенностей проводилась для кокса сухого тушения, взятого в узкокамерных батареях № 7 и 8 (ширина камеры 410 мм) с нижним подводом тепла, и мокрого тушения из ширококамерных батарей № 5 и 6 (ширина камеры 450 мм) с боковым подводом тепла.
При оценке отдельных классов кокса и выборе оптимальной его крупности крайне важно установить оценочные параметры, исходя из роли кокса в доменной плавке. Выбор оптимальной крупности кокса ранее обосновывался исходной прочностью его отдельных фракций и соотношением размеров кусков железорудных материалов и кокса, определяющих газопроницаемость их смеси.
Таковой подход неправомерен, поскольку наряду с этим не учитывается, что в нижней части доменной печи железорудные материалы в жёстком виде по большому счету отсутствуют, а крупность его прочность и кокса изменяются под действием возрастающих окислительной среды и температур. Из этого следует, что роль кокса в доменной печи в значительной степени независима.
С повышением количества доменных интенсивности и печей плавки нагрузка на кокс возрастает и определяющими становятся характеристики кокса, снабжающие наилучшие аэродинамические условия в нижней части печи и дренажную свойство коксовой насадки. Последние и являются оценочными параметрами физико-механических особенностей насыпной массы кокса.
Для определения оптимальной крупности кокса выполнен комплекс изучений физико-механических особенностей отдельных фракций кокса сухого и мокрого тушения, включая определение дробимо-сти и истираемости классов кокса в холодном состоянии и при высоких
температурах в окислительной среде, изучение пористой структуры способом ртутной порометрии и микроструктуры посредством рентгено-структурного анализа, и промышленные изучения трансформации физико-механических особенностей фракций кокса на тракте подачи к доменным печам. Сопоставлены свойства кокса однообразной крупности в исходном состоянии и взятого при разрушении разных классов.
Эти опробований кокса разной крупности в холодном состоянии приведены на рис. 1 и 2. Не обращая внимания на разное уровень качества кокса, поведение отдельных его фракций в ходе опробований было по большей части однообразным. самые прочными были частицы фракцией 40-25 мм, а наименее прочными80 мм.
Но по окончании действия истирающих и дробящих нагрузок в барабане (моделирующих нагрузки на кокс при опускании в печи) громаднейшее количество не хорошо газопроницаемой фракции 25-0 мм образуется по окончании 400 оборотов из обеих этих фракций кокса, причем количество образующейся мелочи для класса кокса 25-40 мм кроме того превосходит данный показатель для класса более 80 мм. направляться также подчеркнуть повышенное содержание в большом коксе по окончании опробований самая мелкой фракции 10-0 мм.
Характерно, что различие в особенностях отдельных частиц кокса мокрого тушения более низкого качества меньше, чем у кокса сухого тушения с более высокими физико-механическими чертями. Так, отличие в выходе фракции 25-0 мм по окончании 400 оборотов барабана из отдельных фракций кокса мокрого и сухого тушения составила ~4 и 9% соответственно. Так, с улучшением условий получений кокса свойства отдельных его фракций не выравниваются.
Исходя из этого и для кокса повышенного качества выбор оптимальной крупности кусков для доменной плавки остается актуальным. Оценка прочности отдельных классов кокса при больших температурах в окислительной среде произведена на установках ЛПИ. Нагрев кокса в потоке диоксида углерода ведет к его разупрочнению при действии и ударных, и особенно истирающих нагрузок, что связано с внутренним механизмом окисления углерода.
Если бы кокс окислялся лишь с наружной поверхности кусков, то действие диоксида углерода не воздействовало бы на сопротивление кокса ударным нагрузкам.
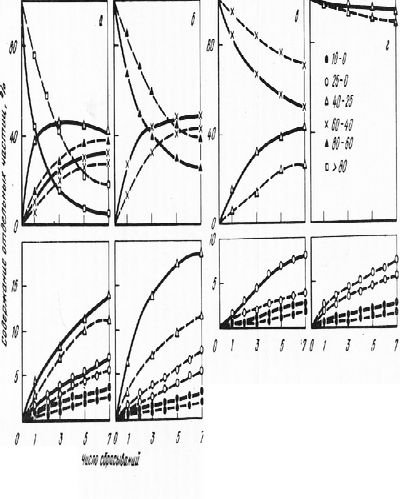
Рис.1. Разрушение при ударных нагрузках кокса сухою (пунктирные линии) и мокрого (целые линии) тушения разной фракции: а –80 мм; б -80-60 мм; в – 60-40 мм; г – 40-25 мм
Рис. 2. Разрушение при обработке в барабане кокса разных классов крупности
Подобная картина отмечается для всех частиц кокса сухого и мокрого тушения.
Как и при комнатнойТёмпературе, прочность на удар и истирание в окислительной воздухе при больших температурах у больших частиц ниже, чем у небольших, не обращая внимания на то, что испытывались частицы однообразной фракции, выделенные из различных классов. Так, большие частицы кокса имеют пониженную прочность не только из-за изюминок их формирования в ходе коксования, вместе с тем и благодаря меньшей прочности пористого материала кокса,
С целью выяснения механизма таковой связи изучены рациональная способность и пористая структура разных фракций кокса. Пористую структуру изучали способом ртутной порометрии на установках ЛПИ. Результаты изучения приведены в табл. 5. Из приведенных данных видно, что особенности формирования при
совании кусков разной фракции проявляются и в их пористой структуре. Кокс фракцией 25-40 и 40-60 мм имеет близкую структуру. Колее большой кокс имеет повышенную пористость, самоё резкое озрастание количества пор отмечается для фракции80 мм. Повышенная пористость больших классов кокса образована по большей части за счет пор радиусом600 мкм. Пористость кокса мокрого тушения выше, чем кокса сухого тушения. Эта отличие в пористой структуре намного больше для больших фракций кокса.
Отмеченные изюминки пористой .структуры больших классов кокса находятся в соответствии с их пониженной прочностью при действии ударных и истирающих нагрузок.
Результаты определений говорят о том, что реакционная свойство кокса мокрого тушения ширококамерных батарей № 5 и 6 в 1,2 и 1,4 раза больше, чем у соответствующих фракций кокса сухого тушения узкокаМерных батарей № 7 и 8. Эта закономерность обусловлена повышенной микропористостью кокса мокрого тушения.
Для кокса фракцией 40-25 мм изучили влияние его крупности на скорость окисления углерода. Установлено, что с уменьшением крупности кусков кокса в диапазоне от 25 до 0,5 мм скорость окисления
Таковой темперамент трансформации скорости реагирования углерода с окислителем при измельчении кокса связан с внутридиффузионным режимом процесса. Наряду с этим режиме окисление_происходит на
большой части внутренней поверхности, площадь которой во большое количество сотен раз превышает величину наружной поверхности кусков. Исходя из этого скорость окисления возрастает с уменьшением диаметра кусков не в следствии повышения площади их наружной поверхности, а благодаря увеличения эффективности применения в реакции внутренней поверхности благодаря ускорению диффузионного обмена в порах частиц малого диаметра.
Не считая пористой структуры, на прочность материала кокса большое влияние оказывает прочность тела кокса. Оценка узкой структуры кокса произведена с применением рентгеноструктурного анализа в лаборатории ЧерМК . Установлено, что дифракционные . спектры кокса очень чувствительны к факторам действия на его свойства и исходя из этого попытка дифференцировать свойства и структуру кокса по дифракционным показателям оправдана и перспективна.
Рен-ггеноструктурный анализ разрешает уточнить представления о узкой структуре металлургического кокса и установить связи структуры с физико-механическими особенностями. Ниже приведены результаты рентгеноструктурного изучения разных фракций кокса сухого и мокрого тушения. Благодаря неоднородности макроструктуры кусков кокса пробы от них для рентгенографирования отбирались по визуальной оценке от самые характерных для данного куска участков.
Рис.3. Дифрактограмма кокса
Одновременно с этим благодаря наложения максимумов выяснить степень графитизации кокса по соотношению интенсивности линии в Moспектре кроме этого не представляется вероятным. Помимо этого, максимум при таком методе получения дифрактограммы обусловлен не одним личным рефлексом и является суперпозициейотражений от различных состояний углерода. Дифрак-тограмма кокса, полученная в РеКд-излучении (рис.
4), является суперпозициеймаксимумов отражения от трех физически различных структурных состояний углерода: кристаллического (графита), аморфного и без того именуемого блочного углерода, дающего на дифрактограмме симметричный диффузный максимум.
Рис.4. Участок дифрактограммы
Рис.5. Дифрактограммы древесного угля (в) и кристаллического графита (б), снятые в FeAa-излучении
Дифрактограмма графита из чугуна (рис. 5,б) характеризуется интенсивным максимумом кристаллического графита в окрестностях рефлекса и отсутствием резких аномалий в фоне во всем диапазоне углов дифракции. На ней четко разрешены другие максимумы графита, дополнительные отражения обусловлены присутствием в графите фаз на базе кремния, оказывающего большое влияние на графитизацию.
Для оценки влияния метода тушения на структуру кокса отобрали его пробы с батарей, кокс с которых тушится как сухим, так и мокрым методом. Из приведенных данных видно, что кокс сухого тушения больше содержит кристаллического углерода, определяющего прочность. Сопоставляя дифракционные характеристики кокса различных батарей, возможно оценить его уровень качества.
К примеру, кокс сухого тушения батарей предпочтительнее кокса батарей № 3 и 4, так как содержит больше кристаллической фазы углеродистого вещества.
На рис. 6 приведены зависимости дифракционных черт от фракционного состава кокса сухого тушения батарей. Из приведенных данных видно, что с повышением размера фракции содержание кристаллического углерода в коксе меньшается, а блочного углерода растет, причем темп трансформации их содержания в коксе с повышением крупности кусков возрастает. Фактически линейно значительно уменьшается аморфная фаза кокса.
Это свидетельствует не только о меньшей прочности больших классов кокса, но и ухудшении горючести, что отрицательно отражается на дренажной свойстве горна при повышенной истираемости этих фракций. Изучение узкой структуры кокса разрешило дать более полное объяснение различия его прочностных черт. С повышением доли кристаллического углерода изменяется пористая структура куска кокса с увеличением его плотности и возрастает прочность тела кокса.
С целью оценки влияния исходной крупности кокса на условия фильтрации и газодинамический режим жидких продуктов плавки в нижней части печи произведена оценка трансформации размеров отдельных фракций кокса под действием механических нагрузок в холодном состоянии, а также в процессе окисления и нагрева.
На рис. 7 по итогам опробований отдельных частиц кокса в холодном состоянии приведено изменение среднего диаметра кусков кокса при истирающих и ударных нагрузках.
При действии лишь ударных нагрузок фракция 40-25 мм остается минимальной из всех классов кокса при любом числе сбрасываний. Недочёты небольшого кокса дополнительно проявляются в окислительной среде. Увеличение степени окисления углерода (рис.
8) проводит к резкому разупрочнению кокса и любой последующий процент окисления вызывает все больше разупрочнение, исходя из этого при больших температурах соотношение прочности разных фракций кокса в зависимости от их окисления возможно иным, чем при опробовании на холоду.
Рис.6. Зависимости дифракционных характерстик от фракционного состава кокса
Риc. 7. Влияние дробящих (а) и истирающих (б) : нагрузок на трансформацию среднего диаметра кусков кокса разных классов крупности (цифры у условных обозначений – вер, мм), батарей 7 и 8 (С) и 5 и 6 (М)
Как было продемонстрировано выше, с уменьшением фракции кокса скорость окисления углерода возрастает, а следовательно, в большей мере понижается прочность небольшого кокса. Значительное различие фракций кокса классов 40-25, 60-40, 80-60 мм сохраняется и в зоне сотрудничества углерода кокса с диоксидом углерода. При поступлении кокса в зону, где проявляется его реакционная свойство, он подвергается нагрузкам, в большинстве случаев, не более 50 оборотов барабана и различие в крупности кусков кокса отдельных классов остается большим.
Рис.8. Влияние степени окисления углерода на сопротивляемость истирающим нагрузкам кокса сухого тушения разных классов крупности (цифры у кривых – мм)
Так, фракция кокса 60-40 и 80-60 мм по окончании 50 оборотов барабана превышает фракцию кокса 40-25 мм приблизительно 1,4 раза, а следовательно, куски кокса, полученные из фракции 40-25 мм будут окисляться в 1,2 раза больше, чем из фракции 60-40 мм. В случае если степень окисления углерода для фракции 60-40 мм равна 7%, а для фракции 80-60 мм – 7,5% (с учетом однообразного размера этих частиц при нагрузке, равной 50 оборотам барабана и более высокой реакционной способности большой фракции), то куски кокса из фракции 40-25 мм окисляется на 8,4%.
По данным рис.28, при истирании кокса фракцией 40-25, 60-40 и 80-60 мм при степенях окисления углерода соответственно 8,4; 7,0 и 7,5% образуется 24, 18 и 21,5% мелочи класса 3-0 мм. Из этого следует, что в окислительной среде при степени окисления углерода кокса 7,0% и более фракции 40-25 мм будут разрушаться в большей мере, чем кокс классов 60-40 и 80-60 мм.
Кокс больше 80 мм, несмотря,на большое различие в крупности если сравнивать с классом 40-25 мм по окончании наложения нагрузок, равных 50 оборотам барабана, в следствии более высокой собственной реакционной способности окислится приблизительно одинаково с кусками кокса из фракции 40-25 мм, а благодаря более низкой прочности вещества кокса (см.рис.28) будет разрушаться в большей мере. В отдельных случаях нижний предел крупности кокса на доменных печах понижается до 15-20 мм. Это в большинстве случаев обосновано большей прочностью небольшого кокса, что подтверждено и настоящими изучениями в разнообразных условиях опробований.
Из теории доменной плавки хорошо как мы знаем, что аэродинамические условия в доменной печи и особенно в нижней ее части, где жидкие продукты плавки фильтруются через коксовую насадку, ухудшаются при уменьшении диаметра кусков кокса. Вследствие этого понижение нижнего предела фракции кокса было бы оправданным, если бы небольшой кокс повышенной прочности при перемещении в доменной печи оставался бы более большим если сравнивать с коксом повышенной исходной крупности.
Из рис. 7 видно, что такое явление вероятно лишь для фракций кокса80 мм, потому, что средний диаметр его кусков по окончании 200 оборотов барабана делается минимальным из всех классов кокса, а с учетом повышенной реакционной свойстве большого кокса разрушение начнется при меньших нагрузках. Помимо этого, кокс фракцией80 мм легче подвергается истиранию по сравнению с другими классами кокса.
Отрицательная роль небольших частиц кокса в горне общеизвестна.
Из изложенного направляться, что кокс фракцией80 мм мало пригоден для доменной плавки. Кокс фракцией 40-25 мм уступает по своим физико-механическим особенностям коксу фракцией 60-40 и 80-60 мм, но предпочтительнее кокса фракцией80 мм.
С целью оптимизации физико-механических особенностей улучшения и кокса подготовки его особенно для замечательных доменных печей на ЧерМК изучили стабилизации и процесс разрушения отдельных классов кокса на тракте его подачи от коксосортировки до загрузки в печь. Темперамент трансформации физико-механических особенностей кокса мокрого тушения изучали на тракте его подачи от коксосортировки батарей № 5 и 6 до загрузки в доменную печь 2700 м3, трудящейся на этом коксе, а кокса сухого тушения – от коксосортировки батарей № 1-4 до загрузки в доменную печь 2000 м3, которая трудится на смеси кокса сухого и мокрого тушения.
Рис. 9. Схема транспортировки кокса мокрого тушения коксовых батарей 5 и 6 ЧерМК до загрузки в доменную печь количеством 2700 м3: I – коксосортировка; II – бункер; III – грохот; IV -весовая воронка; К-19, K-21, K-22, КД-4 – транспортеры с перегрузками; 1-6 – места отбора проб кокса
Из приведенных данных видно, что кокс в ходе транспортировки испытывает большие нагрузки и отмечается его стабилизация с улучшением физико-механических особенностей. Особенно существенно увеличивается уровень качества кокса по окончании прохождения через бункер: показатель Мю понижается с 7,6 до 6,2%, а М25 возрастает с 88,4 до 90,5%; показатели П и Г возрастают соотвественно с 9,0 до 11,3 кг об/дм2 и с 275 до 292 ед.
Подобные результаты взяли и в изучениях при транспортировке кокса сухого тушения. самоё значительное улучшение качества кокса кроме этого замечали по окончании прохождения бункера: показатель Mjо понизился с 7,4-7,8 до 6,9%, показатели П и Г возросли соответственно с 9,1 до 10,2 кг об/дм2 и с 277 до 282 ед.
Изучения продемонстрировали, что в ходе транспортировки до бункеров доменного цеха кокс по большей части подвергается дробящим упрочнениям: прочность кокса возрастает незначительно, а истираемость его остается на прошлом уровне. В следствии реализации трещин при перегрузках образуются новые поверхности кусков кокса, а потому, что кокс на тракте испытывает незначительные истирающие действия, то при обработке в барабане, не обращая внимания на кое-какие улучшения его прочностных особенностей в ходе транспортировки, количество образующейся мелочи не значительно уменьшается.
Только по окончании прохождения через бункер, где кокс в один момент с дробящими действиями подвергается большим истирающим нагрузкам, имитируя собственный поведение в доменной печи, его уровень качества заметно улучшается. Для получения дополнительных сведений о влиянии предварительной обработке кокса на его прочность испытали в барабане куски кокса сухого тушения батарей № 7 и 8, полученные из более больших фракций методом пятикратного сбрасывания пробы на чугунную плиту с высоты 2 м. Прочность кокса оценивали по трансформации эквивалентного диаметра кусков dcр и показателя П согласно данным работы.
Установлено (рис. 10), что прочность частиц каждой фракции кокса, неразрушившихся по окончании пяти сбрасываний, выше прочности исходного кокса таковой крупности до приложения ударных нагрузок. В любых ситуациях прочность кусков однообразных размеров выяснялись тем меньше, чем больше были частицы, из которых они появились. Особенно быстро различались прочность всех кусков, взятых из самая крупной фракции ( 80 мм).
В меньшей мере эта закономерность проявляется для кусков кокса 40-25 мм, взятых из частиц фракцией 60-40 и 80-60 мм; их прочность была близкой к прочности исходной фракции (40-25 мм).
Рис. 10. Изменение показателя прочности и диаметра кусков при обработке в барабане разных частиц исходного (0) и стабилизированного кокса, взятого из частиц фракциями80 (а); 80-60 (б) и 60-40 (в), 40-25 (г) мм
Для всех классов кокса выяснили влияние предварительной стабилизации на прочность при высокотемпературном нагреве в окислительной среде, сравнивая прочность однообразных классов исходного кокса и оставшихся неразрушенными по окончании двух и пяти сбрасываний. Стабилизация улучшила сопротивление кокса действию истирающих и ударных нагрузок. Так, стабилизация кокса усиливает его свойства как в холодном, так и тёплом состоянии в окислительной среде.
Наряду с этим под действием ударных нагрузок прочностные характеристики кокса увеличиваются в намного меньшей мере, чем при истирающих нагрузках.
Низкая прочность кусков кокса, образующихся при разрушении фракции80 мм, если сравнивать с кусками однообразных размеров вторых классов, говорит о целесообразности выделения данной фракции из насыпной массы доменного кокса. Одновременно с этим, как продемонстрировали результаты опробований, механическая обработка данной фракции с преобладанием истирающих нагрузок разрешает приблизить ее прочностные особенности к уровню вторых классов кокса, т.е. большая фракция кокса по окончании дополнительной механической обработки кроме этого может употребляться в доменной плавке, заметно не ухудшая свойства насыпной массы кокса.
Изучения продемонстрировали, что предельное число мелочи (0-25 мм) на единицу затраченной энергии образуется в начальной стадии механической обработки кокса. Кокс наряду с этим существенно упрочняется.
В будущем темп роста образующейся мелочи фактически остается неизменным, т.е. не обращая внимания на более глубокую механическую обработку в доменной печи будет образовываться такое же количество небольших частиц кокса при уменьшении крупности его массы, что отрицательно отразится на аэродинамических условиях нижней части доменной печи. Из этого следует, что чрезмерная степень механической обработки кбкса может оказаться не только экономически нецелесообразной, но и привести к ухудшению показателей доменной плавки.
Предельный уровень механической обработки кокса, при превышении которого уровень качества кокса не улучшается, определяется достижением фактически неизменного темпа роста образующейся мелочи. Целесообразный уровень механической обработки кокса обязан определятся в каждых конкретных условиях, исходя из экономических параметров с учетом соответствия качества кокса условиям доменной плавки. Изложенное относится к коксу, взятому с простой скоростью коксования.
При повышенных ее значениях, в то время, когда упрочняется пористая структура кокса, но возрастает ее трещинова-тость, часть дробящих нагрузок для реализации трещин должна быть увеличена.
Предложены разные методы улучшения физико-механических особенностей кокса: разделение больших кусков в зубчатых и валковых дробилках; механическая обработка в барабанных аппаратах; разные конструкции перегрузочных устройств, разрешающие изменять соотношение дробящих и истирающих нагрузок; механическая обработка больших кусков без выделения их из потока свободным ударом, и регламентированным давлением с одновременной классификацией; замена вибрационных либо механических грохотов для отсева коксовой мелочи перед загрузкой кокса в доменную печь барабанными классификаторами и др. Все эти методы механического действия на кокс улучшают в большей либо меньшей мере его отдельные особенности, но в целом не отражают целый комплекс нагрузок, которым подвергается кокс в доменной печи.
Более рациональным и идеальным методом улучшения физико-механических особенностей кокса есть пропускание его через емкость вертикального типа с заданным уровнем и регулируемой выдачей заполнения с последующей классификацией на грохоте. В этом случае в намного большей мере постоянно совершенствуются прочностные характеристики кокса. Степень механической обработки кокса возможно регулировать его уровнем в емкости, что поддерживают заданным регулируемой выдачей кокса на грохот.
При таком методе механической обработки кокс испытывает фактически все виды ок, которым подвергается в доменной печи.
Такой же эффект замечали и при прохождении кокса через камеры установок при сухом тушении. В связи с интенсификацией доменного процесса и повышением количества доменных печей, с одной стороны, и ухудшением угольной сырьевой базы для коксания, с другой, все актуальнее делается вопрос о соответствии физико-механических особенностей кокса усг ловиям доменной плавки и, как следствие, первоочередности осуществления мероприятий по улучшению его качества.
Критерием степени для того чтобы соответствия может являться полная величина количественных соотношений между удельным показателями (расходом и основными производительностью кокса) доменной плавки и прочностными чертями кокса. Чем больше влияние особенностей кокса на работу доменной печи, тем в большей мере его количество не соответствует условиям доменной плавки.
Количественная оценка этого влияния может изменяться в широком диапазоне не только для разных фабрик, но и для отдельных доменных печей одного предприятия и обязана проводиться для конкретных условий работы доменной печи. В зависимости от того, в какой мере прочностные особенности кокса лимитируют работу печи, может оказаться, что одно да и то же мероприятие в одних условиях более действенно, а в других менее.
Чем больше несоответствие качества кокса условиям доменной плавки, тем выше эффективность мероприятий, направленных на улучшение его особенностей. Степень влияния качества KQKca на работу доменной печи может определяться активным опытом либо статистическим методом. Выяснить это влияние в лабораторных условиях моделированием доменного процесса либо аналитическим методом из-за недостаточной изученности процесса не представляется вероятным.
направляться кроме этого иметь в виду, что маленькая величина взятых количественных соотношений не всегда говорит о соответствии качества кокса условиям работы доменной печи, поскольку при наличии больших помех в коксодоменном производстве это влияние обычно установить не удается. Отсутствие связи говорит о “загрязнённости” опыта, поскольку в наше время доменной плавки физико-механические особенности кокса в значительной степени определяют работу доменных печей.
Так, на печи 2700 м3 (период I) установлена зависимость показателей качества кокса как с производительностью печи, так и удельным расходом кокса, а на печи 1007 м3 (период II) – лишь с производительностью. Полученные результаты говорят о большом влиянии качества кокса на работу доменной печи 2700 м3, т.е. уровень качества кокса в большей мере лимитирует ее эффективность и работу мероприятий по его улучшению в этих условиях будет выше.
Изучения продемонстрировали, что целесообразность мероприятий по улучшению качества кокса нельзя установить в отрыве от конкретных условий доменной плавки: одно да и то же мероприятие (к примеру, механическая обработка кокса) в одних условиях может принести большой эффект, а в других будет неэкономичным. Обнаружение закономерности формирования особенностей доменного кокса вне камер коксования и их влияние на работу доменных печей разрешают сформулировать следующие теоретические положения, имеющие прикладное значение.
1. Роль Кокса в доменной плавке в значительной степени независима и проявляется по большей части внизу печи, где жидкие продукты плавки фильтруются через коксовую насадку. Отсюда вытекают и требования к коксу, каковые должны отражать его свойства не только в холодном, на и тёплом состоянии под действием окислительной среды.
2. Прочность кокса быстро снижается в окислительной среде, наряду с этим любой последующий процент окисления вызывает все большее разупрочнение. С уменьшением фракции кокса скорость окисления углерода возрастает обратно пропорционально диаметру частиц в степени —0,5. Таковой темперамент трансформации скорости реагирования углерода с окислителем при измельчении кокса связан с внутридиффузионным режимом окисления.
3. С улучшением условий получения кокса физико-механические особенности отдельных его фракций не выравниваются. Фундаментальные закономерности трансформации особенностей кокса в зависимости от его фракции сохраняются в широком диапазоне его качества.
4. Требования к качеству кокса и особенно его прочности возрастают с повышением количества доменных интенсивности и печей плавки из-за увеличения нагрузок при перемещении в печи и повышения количества жидких продуктов плавки на единицу площади горна. По комплексу физико-механических особенностей самый пригоден для доменной плавки кокс фракцией 80-40 мм. Таким коксом целесообразно снабжать прежде всего замечательные печи среднего и доменные печи количества, трудящиеся с высокой интенсивностью.
При недостатке доменного кокса печи меньшего количества смогут трудиться на коксе фракцией 80-25 мм, наряду с этим особенно шепетильно обязан обеспечиваться отсев коксовой мелочи 25-0 мм, быстро ухудшающей газопроницаемость кокса. Кокс фракцией80 мм целесообразно отправлять потребителям как литейный кокс либо подвергать дополнительной механической обработке.
5. Прочность кокса определяют структурным состоянием углерода. Повышение доли кристаллического углерода повышает его прочностные характеристики. Определение структурного состояния углерода в коксе по его дифрактограммам’, взятым СиКа- н Fe/Qj-излуче-ниях, с их количественной оценкой и расшифровкой структурных составляющих разрешает увеличить возможности улучшения особенностей .доменного кокса, поскольку существующие способы не полностью отражают их настоящие трансформации.
6. Свойства кокса, взятого при простых скоростях коксования, постоянно совершенствуются в громаднейшей степени при совместном действии давящих и истирающих нагрузок. Разделение кокса под действием ударных нагрузок повышает прочность кусков кокса в следствии реализации трещин, но фактически не сокращает его склонности к истиранию, наряду с этим прочностные характеристики постоянно совершенствуются в меньшей мере, чем при комплексном действии вышеперечисленных нагрузок.
7. Стабилизация кокса под действием нагрузок повышает его прочность, но в любых ситуациях прочность кусков однообразного размера оказывается тем меньшей, чем больше были частицы, из которых они образовывались, направляться.е. чем больше кокс, тем громадным механическим действиям он должен быть подвергнут для сглаживая черт.
8. Большое упрочнение кокса на единицу затраченной энергии происходит в начальной стадии механической обработки, наряду с этим образуется и предельное число мелочи, быстро ухудшающей газодинамические характеристики насыпной массы кокса. В будущем темп роста образующей мелочи фактически остается неизменным, т.е. не обращая внимания на более глубокую механическую обработку, в доменной печи будет образовываться столько же небольших частиц кокса при уменьшении его крупности, что отрицательно отразится на аэродинамических условиях в нижней части доменной печи.
Существует предельный уровень механической обработки кокса, превышение которого может привести кроме того к ухудшению показателей доменной плавки. Наряду с этим предельный уровень механической обработки невсегда есть оптимальным.
9. Целенаправленное формирование особенностей доменного кокса вне камер коксования должно осуществляться с учетом их соответствия условиям доменной плавки. Критерием степени для того чтобы соответствия может являться полная величина количественных соотношений между главными показателями доменной плавки и физико-механическими особенностями кокса.
Чем больше влияние черт кокса на работу доменной печи, тем в большей мере его уровень качества не соответствует условиям ее работы и выше эффект от мероприятий по улучшению подготовки кокса. Целесообразность таких мероприятий нельзя рассматривать в отрыве от условий доменной плавки. Определение степени соответствия особенностей кокса условиям работы доменных печей разрешает установить не только целесообразность, но и очередность осуществления мероприятий по улучшению качества кокса.
Изучили отдельные классы агломерата ЧерМК и частично офлюсованных окатышей КостГОКа. Пробы агломерата отобрали по окончании сортировки на аглофабрике и перед загрузкой в доменную печь (стабилизированный в ходе транспортировки агломерат).
окатышей характеристик и Зависимости агломерата от их фракции приведены на рис. 11. Форму отдельных окатышей и кусков агломерата оценивали по степени ее приближения к шару.
Насыпную плотность определяли до и по окончании уминки, а их порозность – лишь по окончании уминки при первом и повторном заполнении водой (способы I и II соответственно). Установлено, что темперамент зависимостей порозно-сти материалов от их фракции при однократном и двухкратном заполнении водой аналогичен, а значения порозности различаются только по полной величине (рис. 11).
Для обнаружения закономерности трансформации порозности с повышением крупности материалов достаточно применять первый способ, что существенно уменьшает количество опробований. С повышением размера кусков агломерата угол естественного откоса возрастает. Для окатышей отмечается противоположная зависимость, что разъясняется в основном формой кусков по большей части – шаровидная и их размером.
Рис. 11. Зависимость окатышей и характеристик агломерата от их крупности: 1-3 – скиповый агломерат (1-е умин-кой, метрдика I; 2 – с уминкой, методика П; 3 – без уминки); 4 -стабилизированный агломерат (с уминкой, методика I); 5-7 – окатыши (5 – с уминкой, методика I; 6 – с уминкой, медика II; 7 – без уминки)
Большие частицы агломерата по большей части из-за неправильной формы, цепляясь приятель за приятеля, формируют конусный штабель с острым углом. Мелкозернистые фракции с формой кусков более близкой к шаровидной легко скатывается к подножию штабеля. У шаровидных окатышей угол естественного откоса определяется в основном размером кусков, а правильнее – их массой. Чем больше размер окатышей (а следовательно, и их масса), тем легче они скатываются к подножию и образуют штабель с менее острым углом.
Для окатышей фракцией5 мм естественный угол откоса меньше, чем у агломерата. Из этого и склонность окатышей при большой их доле в шихте и близком с агломератом насыпном весе скатываться в осевую территорию доменной печи.
структура кусков упаковки и Форма материалов определяют газопроницаемость и порозность их слоя. Как мы знаем, что порозность шарообразных тел не зависит от диаметра частиц, а определяется только структурой формы упаковок. Порозность кубической упаковки самая большая (47,6%), но эта упаковка и самая неустойчивая. самая устойчивая упаковка – пирамидальная, для нее порозность минимальна (25,9%). Порозность шаровидных окатышей фракцией5 мм образовывает ~35% (рис.
11, кривая б), что соответствует куби-ческо-тетраэдальной упаковке. Оценку порозности материалов создавали лишь для плотной упаковки, поскольку газопроницаемость в верхней части печи определяет сформировавшийся слой материалов. Коэффициент уминки для небольшой фракции ( 5 мм) обоих материалов примерно однообразный. Из рис.
31 видно, что самый быстро порозность материалов понижается с уменьшением фракции куска5 мм.
Для окатышей5 мм с повышением размера порозность возрастает незначительно, т.е. их фракция мало воздействует на максимальный размер и газопроницаемость окатышей их обязан определяться вторыми металлургическими особенностями (в первую очередь прочностью). С повышением размера кусков агломерата фракцией5 мм порозность возрастает , но в намного меньшей мере, чем возрастала при переходе от небольших частиц к большим. Наряду с этим кроме этого направляться иметь в виду, что повышение порозности в этом случае неоднозначно увеличению газопроницаемости агломерата, поскольку чем больше агломерат, тем больше больших пор, увеличивающих количество межкусковых вакуумов и в один момент повышающих сопротивление проходу газа из-за образования каналов с изменяющимся направлением и более шероховатой их поверхностью.
насыпная плотность и Порозность отдельных частиц агломерата оптимальнееописываются степенной функцией (рис. 11 )типае = еоdn, d – размер данной фракции;^ – порозность самая мелкой фракции; п – коэффициент, характеризующий склонность кусков и форму материала его к уплотнению.
Как видно из приведенных на рис. 11 результатов опробований, причиной, самый быстро воздействующим на газопроницаемость железорудных материалов и определяющим газодинамический режим в верхней части печи есть содержание частиц небольшой фракции (5 мм). Вследствие этого в качестве главного оценочного критерия металлургической сокровище отдельных окатышей и частиц агломерата выбрали их склонность к образованию мелочи при действии механических нагрузок.
Исходя из установленного критерия оценки физико-механических особенностей разных частиц железорудных материалов, возможно сформулировать требования к их крупности. Крупность окатышей и агломерата должна быть таковой, дабы при загрузке их в доменную печь по окончании грохочения как возможно меньше образовывалось частиц небольшой фракции (5-0 мм).
Рис. 12. Влияние истирающих нагрузок на разрушение исходного (а) и скипового (б) агломерата разной фракции (цифры условных обозначении)
самая прочной являются частицы фракцией 10-5 мм, но по окончании обработки в барабане выход мелочи из данной фракции больше, чем из фракций 25-15, 15-10 и 40-25 мм. Предельное число мелочи образуется при первых 25 оборотах барабана (—12%), после этого темп роста небольших частиц понижается и делается фактически постоянным. Прочность отдельных частиц скипового агломерата выше, чем у исходного (рис. 12). Намного меньше образуется и мелочи при предстоящих перегрузках.
Это говорит о целесообразности механической обработки агломерата.
При обработке в барабане стабилизированного агломерата предельное число мелочи образуется у частиц фракцией 15-10,10-5 и 25-15 мм. Темп роста мелочи особенно при первых оборотах барабана существенно ниже, чем у исходного. Темперамент разрушения отдельных частиц агломерата под действием ударных нагрузок подобен (рис.
13). Но имеются и особенности. Так, темп роста при обработке исходного агломерата на начальной и последующих стадиях различается не столь быстро. Предельное число мелочи образуется у частиц фракцией 10-5 мм. У остальных частиц количество образующейся мелочи различается незначительно (рис.
13,а). Не обращая внимания на то, что степень разрушения агломерата фракцией 10-5 мм минимальна, в силу изюминок формирования куска (постепенное откалывание маленьких частиц), мелочи у данной фракции образуется громаднейшее количество. С данной точки зрения целесообразно увеличивать нижний предел крупности исходного агломерата.
Окатыши кроме этого подвергали действию дробящих и истирающих нагрузок. При истирании на удар методом неоднократного сбрасывания на железную плиту окатыши крупностью 15-5 мм фактически не разрушались. Меньшей прочностью владеют окатыши фракцией 25-15 мм.
При обработке в барабане под действием преобладающих истирающих нагрузок мелочи образуется больше (рис. 14). Особенно существенно разрушаются частицы фракции 25-15 мм.
самая прочной у окатышей являются частицы фракцией 15-10 мм.
Характерным для окатышей есть фактически линейное нарастание в них мелочи под действием истирающих нагрузок. Исключение составляют только частицы фракцией 10-5 мм, у которых отмечается стабилизация особенностей. В отличие от агломерата, механическая обработка окатышей фактически не усиливает их свойства и необходимость в ней отпадает.
Так, путь улучшения физико-механических особенностей окатышей – это совершенствование разработки их получения. С позиций фракционного состава окатышей предпочтение направляться дать частицам фракцией 15-10 мм. Сопоставляя полученные результаты опробований отдельных
частиц агломерата с данными о характере разрушения разных классов кокса, возможно сделать вывод о специфике подготовки агломерата к доменной плавке.
Приведенные на рис. 12 и 13 зависимости свидетельствует, в отличие от кокса, о возможности переизмельчения агломерата при больших нагрузках, в особенности истирающих. В случае если у разных частиц классов кокса при величине нагрузок равной 200 оборотам барабана образуется мелочи (25-0 мм) до 20%, то у агломерата небольших частиц (5-0 мм) – до 30-37%. Степени измельчения Ыо/(1Ср) сопоставимы только у самых больших частиц кокса и агломерата ( 80 мм) – соответственно 4,5 и 6,2 (при 200 оборотах барабана).
Для остальных частиц разрушаемость агломерата многократно больше, чем кокса. Так, для фракции 40-25 мм степень измельчения агломерата выше в 2 раза (соответственно 3,0 и 1,5).
Это говорит о большей склонности агломерата к разрушению благодаря изюминок формирования структуры куска (наличие более больших пор с узкими стенками). Вследствие этого вторым должен быть и подход к подготовке агломерата.
В случае если для кокса глубокая механическая обработка (с преобладанием истирающих нагрузок) возможно действенным средством улучшения его особенностей, то для агломерата подобная механическая обработка может привести не только к громадным утратам годного агломерата, но и ухудшению особенностей его насыпной массы по окончании загрузки в печь. Чрезмерная механическая обработка агломерата с преобладанием истирающих нагрузок ведет к резкому уменьшению среднего диаметра кусков агломерата (см.рис.
14) с громадной долей частиц фракцией 10-5 мм, при загрузке которой в печь, под действием ударных нагрузок образуется много мелочи 5-0 (рис. 13).
Рис.14. Влияние истирающих нагрузок на разрушаемость частиц окатышей
Одновременно с этим понижение фракции агломерата до определенного предела есть действенным средством улучшения прочностных черт его насыпной массы. Опробования продемонстрировали (рис. 15), что при предстоящих перегрузках у исходного агломерата предельное число мелочи (5-0) образуется из частиц фракцией 10-15 и 15-25 мм (рис.
15, а, в). Наряду с этим в зависимости от вида нагрузок, которым подвергается агломерат при загрузке в печь, оптимальная его крупность различается. Так, при преобладании истирающих нагрузок предельное число мелочи.у скипового агломерата образуется йз частиц фракцией 15-10,10-5 и 25-15 мм, а при ударных нагрузках – из частиц фракцией 15-10 и 25-15 мм (рис. 15, б, г).
В современных конструкциях загрузочных устройств часть перегрузок с дробящими действиями велика, исходя из этого предпочтение направляться дать фракции агломерата 10-25 мм. Разрушаемость для того чтобы агломерата в печи при восстановительно-тепловой обработке кроме этого минимальная.
На замечательных доменных печах при загрузке в печь агломерат испытывает большие нагрузки. Для таких печей целесообразно повышать предел крупности агломерата с 5 до 6-7 мм, что разрешит сократить образование наименее газопроницаемой фракции (5-0 мм). С целью более экономического расходования агломерата частиц небольшой фракции (3-6 мм) возможно загружать в доменную печь раздельно от главной массы, перераспределяя по сечению для регулирования газораспределения.
Опробования продемонстрировали, что при однообразной степени измельчения агломерата меньше мелочи 5-0 мм образуется при ударных нагрузках, т.е. предпочтительнее уменьшать его фракцию (до определенного предела) методом разделения на дробилках аглофабрик. Но при большом понижении фракции быстро увеличиваются затраты на разделение. Помимо этого, при ударных нагрузках стабилизация агломерата фактически не отмечается.
Это говорит о необходимости использования и операций рационального сочетания дробления разрушающих нагрузок при транспортировке.
Наличие на тракте подачи агломерата перегрузочных узлов с определенной долей истирающих нагрузок и организацией отсева мелочи разрешит стабилизировать агломерат, улучшить его физико-механи-.ческие свойства. Наряду с этим понижаются требования к разделению агломерата на аглофабриках и верхнему пределу его крупности.
Величина дробящих и истирающих нагрузок на всем тракте (включая узел разделения агломерата на аглофабрнке, охлаждение и сортировку) обязана снабжать понижение верхнего предела крупности агломерата на выходе из бункеров доменного цеха до 25-40 мм. Отсев мелочи на тракте разрешает снизить ее содержание в бункерном агломерате, повысить эффективность его грохочения и обеспечить предельное число небольших частиц как в грохоченном агломерате, так и загружаемом конкретно в печь по окончании прохождения загрузочного устройства.
Рис. 15. Выход частиц небольшой фракции из разных классов исходного (а, в) и скипового (б, г) агломерата под действием истирающих (а, б; цифры у кривых – число оборотов барабана) и дробящих (в, г) (цифры у кривых – число сбрасываний) нагрузок
Изучения продемонстрировали кроме этого целесообразность окатышей и смешения агломерата перед загрузкой в доменную печь. В этом случае в меньшей мере окатыши спонтанно скатываются в осевую территорию и более равномерно распределяются по сечению колошника. В смеси расплав начинает стекать через коксовую насадку в диапазоне температур между началом фильтрации расплава из окатышей и агломерата и вытекает лучше, чем отдельные составляющие наряду с этим на слое кокса меньше остается шлаковых соединений.
Меньше возможность и слипания окатышей при их оплавлении.
Изученные закономерности разрешили сформулировать требования к качеству железорудного сырья и выяснить пути формирования его оптимальных особенностей.
1. Лучшие особенности агломерата обеспечиваются при понижении верхнего предела крупности до 25-40 мм с максимальным отсевом частиц небольшой фракции (5-0 мм).
2. Стабилизация агломерата под действием истирающих нагрузок повышает прочность его насыпной массы. При ударных нагрузках стабилизация агломерата фактически не отмечается.
3. Для улучшения особенностей агломерата при конвейерной подаче к доменным печам целесообразно наровне с разделением тёплого спека агломерата проводить его стабилизацию в ходе транспортировки с действием истирающих нагрузок на перегрузках. Наряду с этим суммарная величина механических действий не должна быть больше критических значений, при превышении которых происходит переизмельчение агломерата, сопровождающееся большим уменьшением выхода годного, и резким повышением доли частиц фракцией 10-5 мм, при загрузке которой в печь образуется много мелочи (5-0 мм).
4. Создание высокоэффективных грохотов и сооружение трактов с отсевом частиц небольшой фракции на перегрузках разрешит обеспечить оптимальную крупность агломерата и существенно улучшить его свойства.
5. самая прочной у окатышей являются частицы фракцией 15-10 мм. В отличие от агломерата механическая обработка окатышей фактически не усиливает их особенностей (за исключением трансформации формы). Повышение доли лучшей фракции достигается отсевом частиц и технологическими приёмами небольшой фракции.
6. Смешение окатышей и агломерата перед загрузкой в доменную печь усиливает распределение последних по сечению колошника и их поведение в высокотемпературных территориях.
Формирование особенностей доменного сырья, снабжающих рациональное распределение шихтовых материалов в печи, лучшую газопроницаемость и фильтрующую свойство, формирует условия для оптимизации технологических интенсификации и режимов процессов выплавки чугуна в замечательных доменных печах.